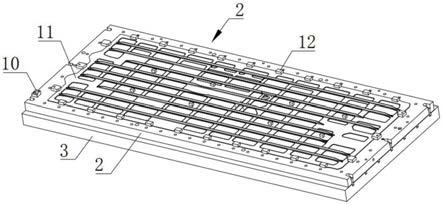
1.本发明涉及航空器零部件加工技术领域,特别涉及一种客舱底板薄壁铝件加工工艺及工装。
背景技术:2.飞机客舱地板为薄壁铝件结构,由于其特殊的薄壁结构,因此在加工时容易出现形变,形变后直接影响地板的平面度,最后导致所加工零件报废,增加生产成本。
技术实现要素:3.本发明的目的在于克服现有技术的不足,提供一种客舱底板薄壁铝件加工工艺及工装,通过对薄壁零件多点真空吸附固定,薄壁零件受力面积增大,加工时薄壁零件多点均匀受力抵消零件形变应力,避免零件发生形变,保证零件的加工质量;同时加工时零件与工装接触面积大、受力面积大,减少零件加工时的振颤,进而减小刀具与零件发生碰撞的概率,因此可避免在加工时发生弹刀、拉刀现象。
4.本发明的目的是通过以下技术方案来实现的:
5.一种客舱底板薄壁铝件加工工艺,包括如下步骤:
6.s10、检查零件尺寸:检查零件毛坯尺寸,零件上标记纤维方向并设置吊环孔,零件的侧面设置零件质量编号;
7.s20、第一次数铣:检查零件平面变形,零件变形小于2.5mm时,手工加工b面厚度至27
±
0.3mm,保证b面平面度0.1;b面朝下,x轴、y轴以四面分中,z轴以零件底面为0,加工基准孔和压板位;工装保证平面度0.05mm,以基准孔找正分中;零件以b面朝下设置在工装上,x轴、y轴以基准孔用插销定位,z轴以零件底面为0,工装通过真空吸附固定零件;使用程式9602c-0003、9602c-0004加工零件至平面厚度为22
±
0.2mm;其中,零件的长和宽组成的两个相对平面分别为a面和b面;其中:9602c-0001表示铣基准孔;9602c-0002表示铣压板位;9602c-0003表示粗铣平面;9602c-0004表示精铣平面,要求平面度0.1,厚度保证22
±
0.2mm;
8.s30、第二次数铣:检查零件变形,根据零件变形使零件凸起部分朝上放置零件;零件设置在工装上,x轴、y轴以基准孔用插销定位,z轴以零件底面为0,工装通过真空吸附多点固定零件;加工螺丝过孔,刻铣压板位;
9.s40、第三次数铣:零件设置在工装上,零件四周通过工艺台搭压板压紧;粗铣零件b面,单边留量2mm;检查零件尺寸,用卡尺检测肋高、肋宽,用百分表检测腹板厚度;
10.s50、时效处理:零件水平放置,自然时效48小时;
11.s60、第四次数铣:零件设置在工装上,x轴、y轴以基准孔用插销定位,z轴以零件底面抬高0.02mm为0,工装通过真空吸附多点固定零件,零件四周通过工艺台搭压板压紧;敲打零件底面检查吸附情况,保证零件与工装贴平;加工9602c-2501程式,加工完后敲打零件底面检查零件吸附情况;加工9602c-2504程式,加工完后检查零件接刀痕,保证接刀痕小于
0.03;检查后开始镗孔;镗孔后尺寸检测;腹板厚度检测后,换压板位置加工工艺台;工艺台加工完在零件表面记录零件信息;其中9602c-2501表示粗铣,单边留量0.5mm;9602c-2504表示精铣肋到数接刀痕小于0.03在线检测图示对应尺寸;
12.s70、去毛刺:去除外形预料和毛边;接平高于0.03的接刀痕;锐边倒圆r0.2;在所镗孔的孔口处0.5*45
°
倒角;
13.s80、检验:按设计要求检验;
14.s90、清洗:按标准清洗零件,保证零件表面无油污、灰尘及腐蚀斑,清洗后包装。
15.进一步地,所述工装的真空压力为-0.07pa-0.085pa。
16.进一步地,所述步骤s90中,使用防护泡沫进行包装防护。
17.一种用于客舱底板薄壁铝件加工工艺的工装,包括真空板,所述真空板设置在机床工作台上,所述真空板远离机床工作台的一面设有网站状分布的真空吸附槽,所述真空板内部设有真空通道,所述真空通道与所述真空吸附槽连通,所述真空通道通过气嘴连接有负压设备。其中负压设备可以是但不局限于真空发生器,具体结构及原理为公知常识,此处不做赘述。
18.进一步地,所述真空吸附槽其边缘形状与零件形状适配。
19.进一步地,所述真空板上设有用于密封零件上通孔的密封环槽。
20.进一步地,所述真空板通过圆柱销、衬套与所述机床工作台相连接。
21.进一步地,所述真空板远离机床工作台的一面通过螺钉连接有试刀块。
22.本发明的有益效果是:
23.本发明通过对薄壁零件多点真空吸附固定,薄壁零件受力面积增大,加工时薄壁零件多点均匀受力抵消零件形变应力,避免了零件发生形变,保证了零件的加工质量;同时加工时零件与工装接触面积大、受力面积大,减少零件加工时的振颤,进而减小刀具与零件发生碰撞的概率,因此可避免在加工时发生弹刀、拉刀现象。
附图说明
24.图1为本发明实施例中设置有吊环孔的零件结构示意图;
25.图2为本发明实施例中设置有基准孔、压板为的零件结构示意图;
26.图3为本发明实施例中零件与工装的安装结构示意图;
27.图4为本发明实施例中零件上螺丝过孔位置示意图;
28.图5为变形的零件与工装的位置关系示意图;
29.图6为第三次数铣时零件与工装的连接关系示意图;
30.图7为第四次数铣时零件与工装的连接关系示意图;
31.图8为本发明实施例中工装的立体图;
32.图9为本发明实施例中工装的剖视图;
33.图10为图9中局部a处的放大示意图;
34.图11为本发明实施例中真空板的俯视图;
35.图12为图11中b-b向剖视图;
36.图13为图11中c-c向剖视图;
37.图14为图11中d-d向剖视图;
38.图15为图11中e-e向剖视图;
39.图16为本发明实施例中零件设置在真空板上时的俯视图;
40.图17为本发明实施例中零件设置在真空板上时正视图;
41.图中,
42.1、工装;2、真空板;3、机床工作台;4、真空吸附槽;5、真空通道;6、气嘴;7、密封环槽;8、圆柱销;9、衬套;10、试刀块;11、零件;12、工艺台。
具体实施方式
43.下面将结合实施例,对本发明的技术方案进行清楚、完整地描述,显然,所描述的实施例仅仅是本发明一部分实施例,而不是全部的实施例。基于本发明中的实施例,本领域技术人员在没有付出创造性劳动的前提下所获得的所有其他实施例,都属于本发明保护的范围。
44.参阅图1-图17,本发明提供一种技术方案:
45.实施例1:
46.如图1-图17所示,一种客舱底板薄壁铝件加工工艺,包括如下步骤:
47.s10、检查零件尺寸:检查零件毛坯尺寸(本实施例中零件毛坯为2805
×
1040
×
30),零件上标记纤维方向(为零件毛坯的长度方向即长度尺寸2805方向,具体如图1示,其中图1中包含零件的俯视图和正视图)并设置吊环孔(4个m10吊环孔,),零件的侧面设置零件质量编号;
48.s20、第一次数铣:s21、检查零件平面变形,零件变形小于2.5mm时,手工加工b面厚度至27
±
0.3mm(零件最薄处),保证b面平面度0.1(刀具切削方向和零件纤维方向一致);s22、b面朝下,x轴、y轴以四面分中,z轴以零件底面为0,加工基准孔(2个φ12基准孔,具体位置如图2所示,)和压板位(该步骤加工基准孔和压板为的程式为9602c-0001,9602c-0002);s23、如图3所示,工装保证平面度0.05mm,以基准孔找正分中;s24、零件以b面朝下设置在工装上,x轴、y轴以基准孔用插销定位,z轴以零件底面为0,工装通过真空吸附固定零件,工装的真空压力为-0.07pa-0.085pa;s25、使用程式9602c-0003、9602c-0004加工零件至平面厚度为22
±
0.2mm;其中,零件的长和宽组成的两个相对平面分别为a面和b面;其中:9602c-0001表示铣基准孔;9602c-0002表示铣压板位;9602c-0003表示粗铣平面;9602c-0004表示精铣平面,要求平面度0.1,厚度保证22
±
0.2mm;其中x、y、z轴的方向如图2所示,图2中包含零件的正视图和俯视图。
49.具体程式参数如下表1;
50.[0051][0052]
表1
[0053]
s30、第二次数铣:检查零件变形,根据零件变形使零件凸起部分朝上放置零件(如图5所示);零件设置在工装上,x轴、y轴以基准孔用插销定位,z轴以零件底面为0,工装通过真空吸附多点固定零件,工装的真空压力为-0.07pa-0.085pa;使用程式9602c-0501加工m12螺丝过孔(如图4所示,),刻铣压板位(具体参数如表2);
[0054][0055]
表2
[0056]
s40、第三次数铣:如图6所示,零件设置在工装上,x轴、y轴以基准孔用插销定位,z轴以零件底面为0,工装通过真空吸附多点固定零件,零件四周通过工艺18处凸台搭压板压紧;使用程式9602c-1001粗铣零件b面(具体参数如表3),单边留量2mm;检查零件尺寸,用卡尺检测肋高、肋宽,用百分表检测腹板厚度,检查记录填写在过程控制卡上;
[0057][0058]
表3
[0059]
s50、时效处理:零件水平放置,自然时效48小时;
[0060]
s60、第四次数铣:s61、零件设置在工装上,x轴、y轴以基准孔用插销定位,z轴以零件底面抬高0.02mm为0,工装通过真空吸附多点固定零件,零件四周通过工艺台搭压板压紧(如图7所示);敲打零件底面检查吸附情况,保证零件与工装贴平;s62、依次加工9602c-2501、9602c-2502、9602c-2503程式,加工完后敲打零件底面检查零件吸附情况,该步骤中,若零件工装贴合不好需重新装夹工件;s63、加工9602c-25041、9602c-25042程式,加工完后检查零件接刀痕,保证接刀痕小于0.03;该步骤若接刀痕大于0.03则用9602c-2504a程式重新加工;s64、检查接刀痕后开始镗φ58孔;s65、镗孔后尺寸检测(尺寸检测为用卡尺检测肋高、肋宽,用百分表检测腹板厚度),并记录在过程控制卡上(其中步骤s64和s65加工过程包括依次加工9602c-2505~9602c-2515程式);s66、腹板厚度检测后,换压板位置加工工艺台;s67、工艺台加工完用黑色色笔在零件表面记录零件信息;其中9602c-2501表示粗铣,单边留量0.5mm;9602c-2504表示精铣肋到数接刀痕小于0.03在线检测图示对应尺寸;程式参数如下表4。
[0061][0062][0063]
表4
[0064]
s70、去毛刺:去除外形预料和毛边;接平高于0.03的接刀痕;锐边倒圆r0.2;在所镗孔的φ58孔口处0.5*45
°
倒角,并挂标牌;
[0065]
s80、检验:按设计要求(明胶板、蓝图及交接单)检验;
[0066]
s90、清洗:按标准清洗零件,保证零件表面无油污、灰尘及腐蚀斑,清洗后使用防护泡沫进行包装防护。
[0067]
本发明通过对薄壁零件多点真空吸附固定,薄壁零件受力面积增大,加工时薄壁零件多点均匀受力抵消零件形变应力,避免了零件发生形变,保证了零件的加工质量;同时加工时零件与工装接触面积大、受力面积大,减少零件加工时的振颤,进而减小刀具与零件发生碰撞的概率,因此可避免在加工时发生弹刀、拉刀现象。
[0068]
实施例2:
[0069]
如图8-图17所示,本实施例为一种用于实施例1中客舱底板薄壁铝件加工工艺的工装,包括真空板2,所述真空板2设置在机床工作台3上,所述真空板2远离机床工作台3的一面设有网站状分布的真空吸附槽4,所述真空板2内部设有真空通道5,所述真空通道5与所述真空吸附槽4连通,所述真空通道5通过气嘴6连接有负压设备。
[0070]
工作原理:零件11表面贴合在工装1上,零件11表面与工装1上表面之间形成密封的空间,零件11有工装1四周通过工艺台12和压板进行固定,避免零件11移动、振动等导致零件11与工装1之间产生缝隙影响密封。使用时,真空板2通过负压设备使真空吸附槽4产生负压,网格状分布的真空吸附槽4对零件11多点吸附,进而实现零件11的多点固定,保证零件11多点均匀受力,保证增加薄壁零件11的固定面积,保证零件11与真空板2充分接触,在加工时,薄壁零件11的变形应力由真空板2对零件11的多处吸力抵消,进而防止零件11发生形变;且零件11的多点固定还可在加工时避免弹刀、拉刀的现象。
[0071]
进一步地,如图8所示,所述真空吸附槽4其边缘形状与零件11形状适配。如此设置可保证真空吸附槽4面积最大化,保证零件11的固定效果。
[0072]
进一步地,如图11所示,所述真空板2上设有用于密封零件11上通孔的密封环槽7。密封环槽7内设置密封圈,密封环槽7独立于真空吸附槽4设置,具体如图所示,设置的密封环槽7用于对零件11上的孔位进行密封,避免零件11上的孔位导致真空板2与零件11之间的密封失效无法产生负压。
[0073]
进一步地,如图13所示,所述真空板2通过圆柱销8、衬套9与所述机床工作台3相连接。真空板2与机床工作台3通过圆柱销8与衬套9连接,连接结构简单,拆卸方便。
[0074]
进一步地,如图8和图14所示,所述真空板2远离机床工作台3的一面通过螺钉连接有试刀块10。设置的试刀块用于刀具使用前的试刀,保证铣削质量。
[0075]
以上所述仅是本发明的优选实施方式,应当理解本发明并非局限于本文所披露的形式,不应看作是对其他实施例的排除,而可用于各种其他组合、修改和环境,并能够在本文所述构想范围内,通过上述教导或相关领域的技术或知识进行改动。而本领域人员所进行的改动和变化不脱离本发明的精神和范围,则都应在本发明所附权利要求的保护范围内。