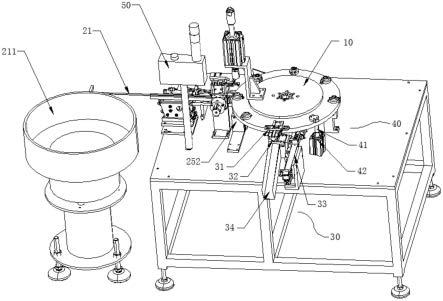
1.本实用新型涉及模型加工技术领域,尤其是涉及一种轮子自动压轴设备。
背景技术:2.如今,汽车模型已成为了一种新的时尚,汽车模型在车身烤漆、发动机、变速箱、车轮、车灯、后视镜等的制作都跟真车相仿。请参阅图1,在汽车模型轮子的装配中,轮子的轮芯有i面和o面,i面是朝汽车模型内侧的面,o面试朝汽车模型外侧的面,轮子的压轴是将车轴b装入轮芯a的i面的车轴孔。由于目前大多轮子的压轴是靠手工组装的,而手工组装加工效率低且劳动力有限,随着汽车模型的市场需求的增加,手工组装已不足以满足生产量的需求,而增加人工将耗费人工成本。
技术实现要素:3.本实用新型的目的在于克服现有技术的缺点与不足,提供一种轮子自动压轴设备,其结构设计巧妙,能够实现轮子自动压轴,提高加工效率和加工量,降低人工成本。
4.本实用新型是通过以下技术方案实现的:一种轮子自动压轴设备,其特征在于:包括压轴单元,所述压轴单元包括车轴定位装置、压轴装置和顶轴装置;所述压轴装置包括压轴杆和压轴动力源,所述压轴动力源驱动所述压轴杆移动,所述车轴定位装置夹持轮子的车轴,所述压轴杆将所述车轴定位装置夹持的车轴压入轮子的轮芯;所述顶轴装置包括顶轴杆和顶轴动力源,所述顶轴杆的端部与所述压轴杆的端部相对,所述顶轴动力源驱动所述顶轴杆移动,所述压轴杆将所述车轴压入所述轮芯时所述车轴与所述顶轴杆的端部相抵。
5.相对于现有技术,本实用新型提供一种轮子自动压轴设备,通过机械结构模拟手工组装中将车轴压入轮芯的过程,实现了轮子的压轴的自动安装,可替代人工的手工组装从而降低人工成本。并且,顶轴装置在压轴的同时限制车轴的压入位置,防止了车轴压入轮芯时超出安装位置,提高了加工质量。
6.进一步地,所述压轴单元还包括车轴供料装置和车轴搬料装置,所述车轴供料装置包括车轴振动盘、车轴振动输送槽、第一检测模块和第二检测模块,所述车轴振动盘发生振动将所述车轴传输至所述车轴振动输送槽,所述车轴振动输送槽发生振动将所述车轴从入料端传输至出料端,所述第一检测模块检测所述车轴振动输送槽中是否有料,所述第二检测模块检测所述车轴振动输送槽的出料端是否有料;所述车轴搬料装置将所述车轴从车轴振动输送槽的出料端移动至所述车轴定位装置。通过该方案,实现了轮胎和轮芯的自动供料,进一步实现自动化。
7.进一步地,所述车轴搬料装置包括车轴夹具和车轴搬料动力源,所述车轴夹具设有车轴夹孔;所述车轴搬料动力源驱动所述车轴夹具转动,所述车轴夹孔夹持的车轴的移动路径经过所述车轴振动输送槽的出料端;所述车轴定位装置包括车轴定位抓取部、第一定位动力源和第二定位动力源,所述第一定位动力源和所述第二定位动力源驱动所述车轴
定位抓取部移动,所述车轴定位抓取部夹持所述车轴夹孔中的车轴。
8.进一步地,还包括回转装置和配件台,所述回转装置驱动所述配件台转动;所述配件台上设有多个配件工位,所述配件工位设有用于放置配件夹具的配件夹具槽,所述配件夹具装夹所述轮胎或轮芯或轮子;所述压轴杆将车轴压入所述配件工位上的轮芯。
9.进一步地,还包括多个承力模块,所述承力模块包括轴承和支撑所述轴承的固定块,所述轴承的轴向与所述配件台的转动方向垂直并与所述配件台底面接触。通过该方案,防止了压芯和打轴过程中对配件台产生的压力使配件台受损。
10.进一步地,还包括下料单元,所述下料单元包括下料抓取部、第一下料动力源和第二下料动力源,所述第一下料动力源和所述第二下料动力源驱动所述下料抓取部移动,所述下料抓取部夹持所述配件工位上的轮子,并将所述轮子搬离所述配件工位。通过该方案,实现了将完成装配的轮子搬离配件台,进一步实现了自动化。
11.进一步地,还包括清理单元,所述清理单元包括顶出杆和轮子顶出动力源,所述顶出杆位于所述配件台下方,所述轮子顶出动力源驱动所述顶出杆移动,所述顶出杆的移动路径穿过所述配件夹具槽。通过该方案,防止了错过下料的轮子再次进入加工程序导致设备损坏。
附图说明
12.图1为轮芯和车轴的结构示意图。
13.图2为实施例中轮子自动压轴设备的结构示意图。
14.图3为实施例中轮子自动压轴设备的装配台的结构示意图。
15.图4为实施例中轮子自动压轴设备的压轴单元的结构示意图。
16.下面结合附图,对本实用新型的技术方案进行详细的描述。
具体实施方式
17.请参阅图2,其为本实用新型的轮子自动压轴设备示意图。该轮子自动压轴设备包括装配台10、压轴单元20、下料单元30、清理单元40和电控单元50,其中装配台10可以自动回转以实现装配流水线的传输;压轴单元20将车轴装入轮芯;下料单元30将所述压轴单元20安装完成的轮子搬离装配台10;清理单元40将经过所述下料单元30而未被搬离的轮子清除出装配台10;所述电控单元50控制所述装配台10、压轴单元20、下料单元30和清理单元40工作。
18.具体地,请参阅图3,其为实施例中轮子自动压轴设备的装配台的结构示意图。所述装配台10包括装置台11、配件台12、回转装置13和承力模块14,其中,装置台11用于放置所述压轴单元20中的装配装置。配件台12与所述装置台11平行同轴设置,所述配件台12设有多个沿所述装置台11外围设置的配件工位121,每一配件工位121上设有用于放置配件夹具的配件夹具槽,配件夹具用于固定配件,可根据不同尺寸的配件更换不同的配件夹具。所述回转装置13使所述配件台12与所述装置台11同轴相对转动,在本实施例中,所述回转装置13为一凸轮分割器,凸轮分割器通过不动法兰连接于所述装置台11轴心使所述装置台11固定;凸轮分割器同时通过动法兰连接于所述配件台12轴心,并通过电控单元50控制一马达驱动所述配件台12相对于所述装置台11同轴转动。在本实施例中,配件台12转动时每一
配件工位121将循环经过三个装配工位,为便于说明以下将装配工位分别命名为第一工位、第二工位和第三工位。承力模块14包括一轴承和支撑轴承的固定块,所述轴承的轴向与配件台12的转动方向垂直并与配件台12底面接触,以抵住入轮打轴过程中配件台12所承受的压力,在本实施例中,所述承力模块14设置为3个且等间隔设置在配件台12下方。
19.请同时参阅图4,其为实施例中轮子自动压轴设备的压轴单元的结构示意图。所述压轴单元20包括车轴供料装置21、车轴搬料装置22、车轴定位装置23、压轴装置24和顶轴装置25,其中,车轴供料装置21实现车轴的逐个供给;车轴搬料装置22将所述车轴供料装置21供给的车轴逐个搬运至车轴定位装置23;压轴装置24将所述车轴定位装置23上定位的车轴压入轮芯的车轴孔中;顶轴装置25用于防止所述压轴装置24压轴时使车轴穿出轮芯的o面。
20.更具体地,车轴供料装置21包括车轴振动盘211、车轴振动输送槽212、第一检测模块(图未示)和第二检测模块(图未示),其中,所述车轴振动盘211是一可振动的带有螺旋轨道的料斗,通过振动使车轴自动有序排列沿螺旋轨道向上移动至螺旋轨道末端。所述车轴振动输送槽212包括一输送槽和使输送槽振动的振动机,通过振动使车轴从输送槽的入料端输送到输送槽的出料端,所述车轴振动输送槽212的入料端与所述车轴振动盘211的螺旋轨道末端对接。所述第一检测模块通过感应器检测所述车轴振动输送槽212中是否有料并发送有无料信息至电控单元50,当检测得无料时电控单元50控制车轴振动盘211开始振动;当检测得有料时,电控单元50控制所述所述车轴振动盘211停止振动。具体实施中,第一检测模块可选设置在所述车轴振动输送槽212的入料端或中段位置。第二检测模块设置在所述车轴振动输送槽212的出料端,通过感应器检测所述车轴振动输送槽212的出料端是否有料并发送有无料信息至电控单元50,当检测到车轴振动输送槽212的出料端无料时,电控单元50控制车轴振动输送槽212开始振动;当检测到车轴振动输送槽212的出料端有料时,电控单元50控制车轴振动输送槽212停止振动。
21.车轴搬料装置22包括车轴夹具221和车轴搬料动力源222,其中,车轴夹具221上设有一用于夹持车轴的车轴夹孔;车轴搬料动力源222驱动所述车轴夹具221在所述车轴夹孔对准所述车轴振动输送槽212出料端的方向和所述车轴夹孔竖直朝上的方向之间转动。
22.车轴定位装置23包括车轴定位抓取部231、第一定位动力源232、滑轨233和第二定位动力源234,其中,车轴定位抓取部231用于抓取车轴,在具体实施中可选用手指气缸。第一定位动力源232驱动所述车轴定位抓取部231竖直上下移动,第二定位动力源234驱动所述第一定位动力源232在所述滑轨233上水平移动,以使所述车轴定位抓取部231在所述车轴夹具221上方和第一工位上方之间水平移动,从而可将车轴从车轴夹具221移动至第一工位并定位于第一工位上方。
23.压轴装置24包括压轴杆241和压轴动力源242,其中,压轴杆241的端部正对于第一工位;压轴动力源242驱动所述压轴杆241于所述车轴定位抓取部231上方竖直上下移动,压轴杆241下移时将车轴定位抓取部231上的车轴压入位于第一工位的配件工位121的轮芯中。
24.顶轴装置25包括顶轴杆(图未示)和顶轴动力源252,其中,顶轴杆的端部正对于所述压轴杆161并设置在配件台12下方;顶轴动力源252驱动所述顶轴杆竖直上下移动,所述顶轴杆上移时顶轴杆的端部穿过配件工位121的配件夹具槽与配件夹具上的轮芯接触。
25.请再次参阅图2,所述下料单元30包括下料抓取部31、第一下料动力源32、第二下
料动力源33和下料滑槽34,其中,下料抓取部31用于抓取完成加工的轮子,在具体实施中可选用手指气缸。第一下料动力源32驱动所述下料抓取部31竖直上下移动。第二下料动力源33驱动所述第一下料动力源32水平移动,以使所述下料抓取部31在第二工位的上方和下料滑槽34的上方之间水平移动,从而可将位于第二工位的配件工位121上的轮子移动至下料滑槽34。
26.所述清理单元40包括顶出杆41和顶出动力源42,其中,顶出杆41的端部正对于第三工位并设置在配件台12下方;顶出动力源42驱动所述顶出杆41竖直上下移动,所述顶出杆41上移时穿过位于第三工位的配件工位121的配件夹具槽,从而将该配件工位121上的轮子顶出配件夹具槽。
27.所述电控单元50包括处理模块和操作模块,处理模块控制所述压轴单元20、下料单元30和清理单元40工作;操作模块接收外部操作指令并发送至处理模块。在具体实施中,所述处理模块可以为微型电脑、微型处理器等可以实现电气控制的器件,操作模块可以为电子触摸屏、键盘、电子按钮等可以实现外部指令传输的器件。
28.在具体实施中,第一定位动力源232、第二定位动力源234、压轴动力源242、顶轴动力源252、第一下料动力源32、第二下料动力源33和轮子顶出动力源42可选用直线驱动气缸等可驱动物体直线运动的动力装置;反转动力源411、车轴搬料动力源222可选用旋转气缸等可驱动物体旋转的动力装置。
29.本实用新型对轮子的加工将经过压轴单元20执行打轴工序。首先,当车轴供料装置21的第二检测模块检测得车轴振动输送槽212的出料端有料时,电控单元50控制车轴搬料装置22的车轴搬料动力源222驱动车轴夹具221使其车轴夹孔转向车轴振动输送槽212出料端,以使车轴插入车轴夹孔,随后再次驱动车轴夹具221使其车轴夹孔中的车轴转向竖直上方;紧接着,电控单元50控制车轴定位装置23的第一定位动力源232和第二定位动力源234驱动车轴定位抓取部231移动至车轴夹具221抓取车轴,然后将车轴移动至第一工位上方和压轴杆241之间;紧接着,电控单元50控制压轴动力源242驱动压轴杆241竖直向下移动,从而将车轴压入位于第一工位的配件工位121上的轮芯的车轴孔中;在压轴杆241下压的同时,电控单元50控制顶轴装置25的顶轴动力源252驱动顶轴杆向上移动,抵住位于第一工位的配件工位121上的轮芯。此时,已完成轮子的入轴工序,接着电控单元50控制完成入轴的轮子所在的配件工位121转动至第二工位。
30.当配件工位121位于第二工位时,电控单元50控制下料单元30的第一下料动力源32和第二下料动力源33驱动下料抓取部31移动至配件工位121上方并抓取轮子,然后将轮子移动至下料滑槽34上方放下。
31.之后,电控单元50控制位于第二工位的配件工位121转动至第三工位,随后电控单元50控制清理单元40的顶出动力源42驱动顶出杆41竖直向上移动将位于第三工位的配件工位121上的轮子顶出配件工位121,以防止未下料的轮子再次进入其他装配工位而损坏设备。
32.相对于现有技术,本实用新型设置的车轴供料装置21、车轴搬料装置22、车轴定位装置23、压轴装置24的配合实现了轮子的自动打轴加工,提高了轮子加工的效率;设置的顶轴装置25在压轴时抵住车轴,提高了压轴加工的轮子的质量。
33.本实用新型并不局限于上述实施方式,如果对本实用新型的各种改动或变形不脱
离本实用新型的精神和范围,倘若这些改动和变形属于本实用新型的权利要求和等同技术范围之内,则本实用新型也意图包含这些改动和变形。