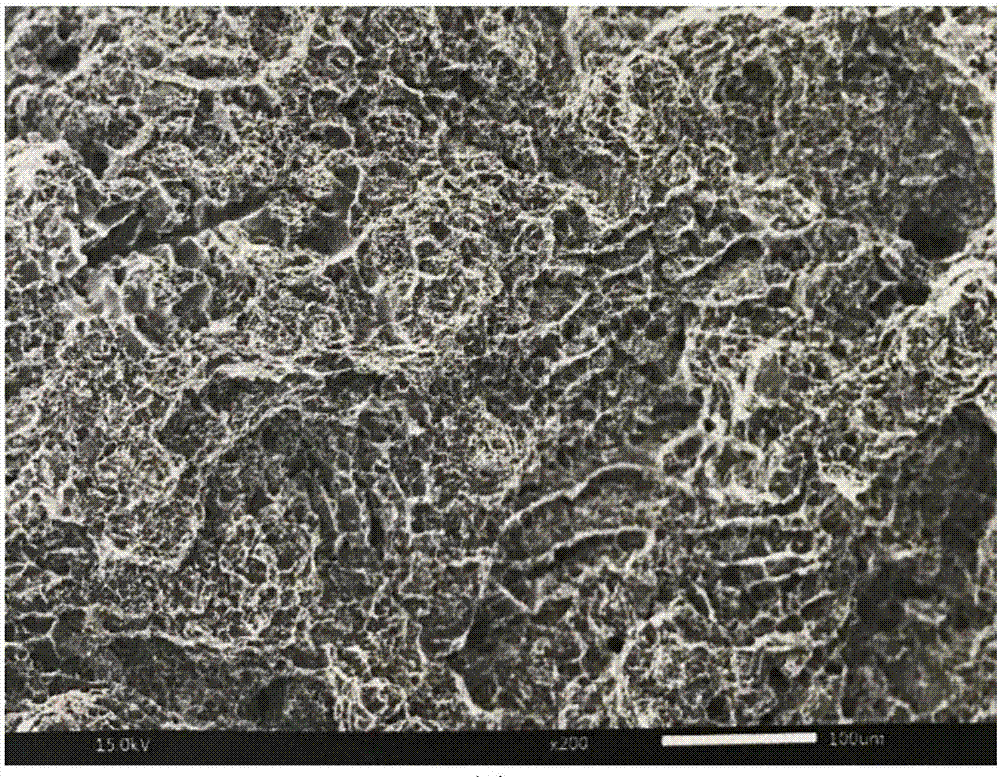
本发明涉及合金材料领域,尤其涉及一种高强韧耐腐蚀铝合金材料,还涉及该铝合金材料的制备方法。
背景技术:
:al-si-cu系铸造铝合金是当前在工业中应用最多的铸造铝合金材料,如国内yl102(alsi12)、yl112(alsi8.5cu3.5)和yl113(alsi811cu3),日本adc12(alsi11cu3)、adc10(alsi8.5cu3.5)以及美国a380(alsi8.5cu3.5)等,这些合金具有优异的铸造性能、高的强度和较好的抗腐蚀性,在扶梯电梯、汽车关键零部件(减速器壳体、控制臂)等众多领域广泛应用,但其韧性、塑性较低,如:y112合金(gb/t15115-94)的强度为240mpa,延伸率仅为1%。如能进一步提高其塑性无疑将提高产品的可靠性和轻量化水平。迄今为止,国内外对铸造成型好、强韧性高、耐腐蚀性好的铸造铝合金材料都进行了大量研究,但冲击韧性≥34.3j/cm2,抗拉强度≥208mpa,断后延伸率≥6.5%,在3.5%nacl水溶液中浸泡93h的腐蚀速率≤0.049mm/y的铸造铝合金材料尚未见报道。如中国专利cn101798649a公开了一种锆和锶微合金化的6013型铝合金,主要由铝、1.22~1.52%的镁、0.90~1.15%的硅、0.804~1.04%的铜、0.451~0.661%的锰、0.311~0.135%的锌、0.0915~0.135%的锆和0.0157~0.0391%的锶组成;该合金的制备方法是:将纯al融化后加入al-cu中间合金、al-si中间合金、al-mn中间合金、al-zr中间合金、al-sr中间合金、纯mg、纯zn,待其融化后加入六氯乙烷精炼,静置保温5~10min后去渣并浇铸成锭。该发明合金硬度为156.0~159.1hv,抗晶间腐蚀性能处于四级,抗剥落腐蚀性能不低于pb级。该发明提供的微合金化铝合金的制备方法为本发明提供了一定的指导思路,但是,相比于本发明,该发明制备的铝合金在强韧性和可塑性方面远不如本发明制备的铝合金。又如中国专利cn103572111a公开了一种高强韧铸造用铝合金,其成分按重量百分比为:si:6.5~7.50%、mg:0.3~0.45%、sr:0.1~0.2%、cu≤0.1%、cr:0.02%、ti≤0.2%、mn≤0.5%、zn≤0.05%、fe≤0.12%,余量为al。其制造方法包括以下步骤:首先熔炼铝材,去掉废渣;将温度升至780℃,加入sr;铝液温度调整至740℃除气30分钟;将温度降至浇铸温度690℃;倒入模具进行浇铸;将铝合金铸件经人工时效处理。该发明提供的高强韧铸造铝合金抗拉强度为250mpa,伸长率为5%,布氏硬度80hbw。而本发明提供的高强韧耐腐蚀铝合金材料,其伸长率明显优于该发明。技术实现要素:为克服现有技术中存在的铸造铝合金材料韧性和塑性低、耐腐蚀性不高的问题,本发明提供了一种高强韧耐腐蚀铝合金材料及其制备方法。一种高强韧耐腐蚀铝合金材料,包含主合金化元素铝、硅和铜,微合金化元素锰、镁和锌,同时添加微量锆和锶元素进行复合微合金化,其特征在于:所述主合金化元素中硅含量为7.93~8.92wt%,铜含量为1.98~2.11wt%;所述微合金化元素中锰含量为0.001~0.02wt%,镁含量为0.001~0.02wt%,锌含量为0.005~0.23wt%,锆含量为0.182~0.62wt%,锶含量为0.0346~0.0391wt%或0.0391~0.04wt%,余量为铝。在一些实施方式中,所述主合金化元素中硅含量为8.21~8.92wt%,铜含量为1.98~2.08wt%;所述微合金化元素中锰含量为0.001~0.02wt%,镁含量为0.001~0.02wt%,锌含量为0.005~0.23wt%,锆含量为0.32~0.62wt%,锶含量为0.0346~0.0391wt%,余量为铝。在一些实施方式中,所述主合金化元素中硅含量为8.61~8.92wt%,铜含量为1.98~2.04wt%;所述微合金化元素中锰含量为0.001~0.02wt%、镁含量为0.001~0.02wt%、锌含量为0.005~0.23wt%,锆含量为0.55~0.62wt%,锶含量为0.0391~0.04wt%,余量为铝。在一些实施方式中,所述主合金化元素中硅含量为8.92wt%,铜含量为1.98wt%;所述微合金化元素中锰含量为0.001~0.02wt%,镁含量为0.001~0.02wt%,锌含量为0.005~0.23wt%,锆含量为0.62wt%,锶含量为0.04%,余量为铝。在一些实施方式中,所述高强韧耐腐蚀铝合金材料冲击韧性≥34.3j/cm2,抗拉强度≥208mpa,断后延伸率≥6.5%,在3.5%nacl水溶液中浸泡93h的腐蚀速率≤0.049mm/y,可应用在航天、汽车和自动扶梯的梯级上。一种高强韧耐腐蚀铝合金材料的制备方法,其特征在于:包括以下步骤:步骤一:高温融化,使铝融化成铝液;步骤二:加入合金化元素si、cu、zr、sr、mn、mg和zn,使其各元素最终含量满足配比要求;步骤三:去除废渣,降温排气;步骤四:浇铸成型。在一些实施方式中,所述步骤二中合金化元素的加入方法以铝基中间合金的方式加入,其中,al-si中间合金含量15.86~17.84wt%,si的质量百分比为50%;al-cu中间合金含量5.66~6.03wt%,cu的质量百分比为35%;al-zr中间合金含量1.86~6.33wt%,zr的质量百分比为9.8%;al-sr中间合金含量0.23~0.257wt%或0.257~0.263wt%,sr的质量百分比为15.2%;al-mg中间合金含量0.019~0.39wt%,mg的质量百分比为5.1%;al-mn中间合金含量0.016~0.33wt%,mn的质量百分比为6%;al-zn中间合金0.065~3.067wt%,zn的质量百分比为7.6%。在一些实施方式中,所述步骤一种高温融化温度为750~800℃,所述步骤三中降温排气温度为700~750℃,时间为20~30min。在一些实施方式中,所述步骤四种浇铸成型包括浇铸凝固和后处理加工,浇铸温度为680~740℃,凝固时间控制为1~3min;后处理加工为铝合金表面瑕疵的处理,依次包括退火和回火处理。与现有技术相比,本发明提供的一种高强韧耐腐蚀铝合金材料及其制备方法产生的有益效果是:一、本发明提供的一种高强韧耐腐蚀铝合金材料及其制备方法,在常规al-si-cu系铸造铝合金成分设计的基础上,通过调整硅含量至7.93~8.92wt%,铜含量至1.98~2.11wt%,同时添加0.182~0.62wt%的锆,0.0346~0.0391wt%或0.0391~0.04wt%的锶进行复合微合金化,在不降低铝合金铸造性能(流动性)的同时,高效细化了铝合金中的硅相,使硅尺寸集中在亚微米级,并且长径比集中在≤2,大幅提高了铝合金的韧性、塑性和耐腐蚀性,同时,合金的强度也得到提高,具有非常显著的性能效果。二、本发明提供的一种高强韧耐腐蚀铝合金材料及其制备方法,获得的铸造铝合金其性能突破了国际标准规范,经机械工业材料质量检测中心检测:其冲击韧性≥34.3j/cm2,抗拉强度≥208mpa,断后延伸率≥6.5%,在3.5%nacl水溶液中浸泡93h的腐蚀速率≤0.049mm/y,其中断后延伸率是其他材料不可比拟的,能显著提高铝合金材料的强韧性和可塑性。三、本发明提供的一种高强韧耐腐蚀铝合金材料及其制备方法,制备得到的高强韧耐腐蚀铝合金材料可制备得到更具轻量化的产品,可广泛应用于自动扶梯、汽车、航空等工业领域,以减轻扶梯、汽车、航天器的重量,从而降低扶梯、汽车、航天器的能耗,并提高其可靠性。四、本发明提供的一种高强韧耐腐蚀铝合金材料及其制备方法,通过理论分析、jmatpro材料设计软件计算和试验研究,研究主合金化元素(si、cu)、微合金化元素(zr、sr、mn、mg、zn)及其含量对高强韧耐腐蚀铝合金铸造性能(流动性)、组织、力学性能的影响规律,为制定实验方案提供了精确指导,为确保获得硅相细小、合金致密的优良铸态组织提供了有力的数据支持和性能保障。附图说明图1是本发明披露的高强韧耐腐蚀铝合金的微观组织;图2是本发明披露的高强韧耐腐蚀铝合金在冲击韧性时的断口形貌;图3是本发明披露的高强韧耐腐蚀铝合金在拉伸时的断口形貌。具体实施方式以下结合附图和实施例,对本发明进行进一步详细说明。应当理解,此处所描述的具体实施例仅用以解释本发明,并不用于限定本发明。本发明披露了一种高强韧耐腐蚀铝合金,包含主合金化元素铝、硅和铜,微合金化元素锰、镁和锌,同时添加微量锆和锶元素进行复合微合金化。作为本发明的一个发明点,所述主合金化元素中硅含量为7.93~8.92wt%,铜含量为1.98~2.11wt%;所述微合金化元素中锰含量为0.001~0.02wt%,镁含量为0.001~0.02wt%,锌含量为0.005~0.23wt%,锆含量为0.182~0.62wt%,锶含量为0.0346~0.0391wt%或0.0391~0.04wt%,余量为铝。本发明在常规al-si-cu系铸造铝合金成分设计的基础上,通过调整硅含量至7.93~8.92wt%,铜含量至1.98~2.11wt%,同时添加0.182~0.62wt%的锆,0.0346~0.0391wt%或0.0391~0.04wt%的锶进行复合微合金化,在不降低铝合金铸造性能(流动性)的同时,高效细化了铝合金中的硅相。对上述实施方式所得到的高强韧耐腐蚀铝合金进行性能表征和测试,具体如下:通过光学电镜,观察所得高强韧耐腐蚀铝合金的表面微观组织,结果如图1所示,由图1可知,硅相尺寸集中在亚微米级,并且长径比集中在≤2。通过扫面电镜,观察所得高强韧耐腐蚀铝合金在冲击韧性时的断口形貌,结果如图2所示,由图2可知,高强韧耐腐蚀铝合金材料在冲击韧性时的断口呈韧窝特征的典型韧性断裂形貌;观察所得高强韧耐腐蚀铝合金在拉伸时的断口形貌,结果如图3所示,由图3可知,高强韧耐腐蚀铝合金材料在拉伸时的断口也呈韧窝特征的典型韧性断裂形貌;对高强韧耐腐蚀铝合金进行腐蚀试验:将试样放入温度为(37±2)℃的3.5%氯化钠溶液中进行93小时浸泡试验后观察,发现试样表面有白色腐蚀物,去除腐蚀物后称重,得出试样的均匀腐蚀速率为0.049mm/y。对高强韧耐腐蚀铝合金进行拉伸性能测试,测试方法参照gb/t228.1-2010,测试结果如表1所示,由表1可知,其抗拉强度≥208mpa,断后延伸率≥6.5%,规定塑性延伸强度≥88mpa。对高强韧耐腐蚀铝合金进行冲击性能测试,测试方法参照gb/t229-2007,测试结果如表2所示,由表2可知,其冲击韧性≥34.3j/cm2。表1高强韧耐腐蚀铝合金拉伸性能测试检测项目1#2#3#4#5#抗拉强度(mpa)208208211208209断后延伸率(%)6.76.57.17.86.6规定塑性延伸强度(mpa)8889909388表2高强韧耐腐蚀铝合金冲击性能测试综上所述,本发明制备所得的高强韧耐腐蚀铝合金材料大幅提高了铝合金的韧性、塑性和耐腐蚀性,具体而言,该高强韧耐腐蚀铝合金材料冲击韧性≥34.3j/cm2,抗拉强度≥208mpa,断后延伸率≥6.5%,在3.5%nacl水溶液中浸泡93h的腐蚀速率≤0.049mm/y,其中断后延伸率是其他材料不可比拟的,能显著提高铝合金材料的强韧性和可塑性,获得的高强韧耐腐蚀铝合金其性能突破了国际标准规范。在上述实施方式的基础之上,以下通过实施例1-3三个对比实施例具体阐述该高强韧耐腐蚀铝合金各元素含量对材料性能的影响。实施例1:所述主合金化元素中硅含量为8.21~8.92wt%,铜含量为1.98~2.08wt%;所述微合金化元素中锰含量为0.001~0.02wt%,镁含量为0.001~0.02wt%,锌含量为0.005~0.23wt%,锆含量为0.32~0.62wt%,锶含量为0.0346~0.0391wt%,余量为铝。该实施方式获得的高强韧耐腐蚀铝合金材料冲击韧性≥38.4j/cm2,抗拉强度≥210mpa,断后延伸率≥6.8%,在3.5%nacl水溶液中浸泡93h的腐蚀速率≤0.047mm/y。实施例2:所述主合金化元素中硅含量为8.61~8.92wt%,铜含量为1.98~2.04wt%;所述微合金化元素中锰含量为0.001~0.02wt%、镁含量为0.001~0.02wt%、锌含量为0.005~0.23wt%,锆含量为0.55~0.62wt%,锶含量为0.0391~0.04wt%,余量为铝。该实施方式获得的高强韧耐腐蚀铝合金材料冲击韧性≥39.1j/cm2,抗拉强度≥209mpa,断后延伸率≥7.1%,在3.5%nacl水溶液中浸泡93h的腐蚀速率≤0.045mm/y。实施例3:所述主合金化元素中硅含量为8.92wt%,铜含量为1.98wt%;所述微合金化元素中锰含量为0.001~0.02wt%,镁含量为0.001~0.02wt%,锌含量为0.005~0.23wt%,锆含量为0.62wt%,锶含量为0.04%,余量为铝。该实施方式获得的高强韧耐腐蚀铝合金材料冲击韧性≥40.1j/cm2,抗拉强度≥211mpa,断后延伸率≥7.8%,在3.5%nacl水溶液中浸泡93h的腐蚀速率≤0.042mm/y。以上三种实施方式,对主合金化元素硅和铜的含量进行进一步的优化,同时对微合金化元素锆和锶的含量也进行进一步的优化,经过一系列检测,得到了高强韧耐腐蚀铝合金材料的冲击韧性、抗拉强度、断后延伸率以及在3.5%nacl水溶液中浸泡93h的腐蚀速率。由测试结果发现,当主合金化元素中硅含量为8.92wt%,铜含量为1.98wt%;微合金化元素中锰含量为0.001~0.02wt%,镁含量为0.001~0.02wt%,锌含量为0.005~0.23wt%,锆含量为0.62wt%,锶含量为0.04%时,所得的高强韧耐腐蚀铝合金材料击韧性≥40.1j/cm2,抗拉强度≥211mpa,断后延伸率≥7.8%,在3.5%nacl水溶液中浸泡93h的腐蚀速率≤0.042mm/y,相比于之前的实施例,具有最佳的实施效果。在实际生产应用中,本发明提供的实施方式:主合金化元素中硅含量为7.93~8.92wt%,铜含量为1.98~2.11wt%;微合金化元素中锰含量为0.001~0.02wt%,镁含量为0.001~0.02wt%,锌含量为0.005~0.23wt%,锆含量为0.182~0.62wt%,锶含量为0.0346~0.0391wt%或0.0391~0.04wt%已能满足目标产品需求,但是,为了具备更优化的实施效果,可选择实施例1-3所述的实施方式或在此范围内的其他实施方式,尤其可选择实施例3所述的实施方式。另外,在理想状态下,所述高强韧耐腐蚀铝合金中杂质含量可为0,但是,在实际生产中,为了避免一些不可控的因素,本发明提供的高强韧耐腐蚀铝合金材料中不可避免的杂志含量控制在≤0.05wt%的范围内即可达到生产需求。作为进一步优选的,在本发明的此实施方式中,通过理论分析、jmatpro材料设计软件计算和试验研究,研究主合金化元素(si、cu)、微合金化元素(zr、sr、mn、mg、zn)及其含量对高强韧耐腐蚀铝合金铸造性能(流动性)、组织、力学性能的影响规律。具体的,包括以下研究内容:(1)高强韧耐腐蚀铝合金材料铸造性能的研究:通过流动性试验,研究主合金化元素、微合金化元素及其含量对合金液态流动性能的影响规律。(2)高强韧耐腐蚀铝合金材料铸态组织的研究:通过光学显微镜和扫面电镜,研究确立主合金化元素、微合金化元素、熔铸工艺等因素与合金铸态组织之间内在联系。(3)高强韧耐腐蚀铝合金材料铸态冲击韧性和多冲疲劳性能的研究:通过摆锤冲击韧性试验、多冲疲劳试验,研究高强韧耐腐蚀铝合金材料铸态韧性和多冲疲劳性能及其关键影响因素(化学成分、熔铸工艺、组织等)。(4)高强韧耐腐蚀铝合金材料铸态强度、塑性的研究:通过拉伸试验,研究合金的化学成分、熔铸工艺、微观组织等关键因素对高强韧耐腐蚀铝合金材料的强度、延伸率的影响并进行检测。(5)高强韧耐腐蚀铝合金材料铸态耐腐蚀性能的研究:通过腐蚀试验,检测高强韧耐腐蚀铝合金材料的耐腐蚀性能,进一步优化合金的化学成分、熔铸工艺和微观组织。通过以上研究内容,高度细化了高强韧耐腐蚀铝合金制备过程中的实验数据,为制定实验方案提供了精确指导,同时也为确保获得硅相细小、合金致密的优良铸态铝合金组织提供了有力的数据支持和性能保障。在上述实施方式的基础之上,本发明还提供了这种高强韧耐腐蚀铝合金材料的制备方法,具体包括以下步骤:步骤一:将铝放入高温炉内进行高温融化,高温融化温度为750~800℃;步骤二:待融化成铝液后,依次加入合金化元素si、cu、zr、sr、mn、mg和zn,使其各元素最终含量满足配比要求;步骤三:待充分搅拌融化后,去除废渣,然后降温排气直至没有气体溢出,降温排气温度为700~750℃,时间为20~30min;步骤四:最后进行浇铸成型,具体包括浇铸凝固和后处理加工,浇铸温度为680~740℃,凝固时间控制为1~3min;后处理加工为铝合金表面瑕疵的处理,依次包括退火和回火处理。进一步优化的,所述步骤二中合金化元素的加入方法以铝基中间合金的方式加入,其中,al-si中间合金含量15.86-17.84wt%,si的质量百分比为50%;al-cu中间合金含量5.66~6.03wt%,cu的质量百分比为35%;al-zr中间合金含量1.86~6.33wt%,zr的质量百分比为9.8%;al-sr中间合金含量0.23~0.257wt%或0.257~0.263wt%,sr的质量百分比为15.2%;al-mg中间合金含量0.019~0.39wt%,mg的质量百分比为5.1%;al-mn中间合金含量0.016~0.33wt%,mn的质量百分比为6%;al-zn中间合金0.065~3.067wt%,zn的质量百分比为7.6%。此外,也可选用复合铝基中间合金,如以al-si-mg中间合金、al-cu-mn中间合金等中间合金的方式添加进入铝液中,在保证最终铝合金材料中各元素配比含量满足本发明要求的前提下可以以任意多种铝基组合中间合金的方式加入。不选用金属单质而使用铝基中间合金是为了减少烧损,所述中间合金可采用常规方法:如铝热法或溶化合成法,进行自行配置,也可根据配比在市场进行购买;中间合金的加入方式可以一次性加入也可待前一种中间合金融化后再加入另一种中间合金,优选后一种加入方式。本发明实现了高强韧耐腐蚀铝合金材料的研究,制备了铸造性能优,强韧性高、耐腐蚀性能好的铸造铝合金材料。通过该方法制备得到的高强韧耐腐蚀铝合金材料可制备得到更具轻量化的产品,可广泛应用于自动扶梯、汽车、航空等工业领域,以减轻扶梯、汽车、航天器的重量,从而降低扶梯、汽车、航天器的能耗,并提高其可靠性。上述说明示出并描述了本发明的优选实施例,如前所述,应当理解本发明并非局限于本文所披露的形式,不应看作是对其他实施例的排除,而可用于各种其他组合、修改和环境,并能够在本文所述发明构想范围内,通过上述教导或相关领域的技术或知识进行改动。而本领域人员所进行的改动和变化不脱离本发明的精神和范围,则都应在本发明所附权利要求的保护范围内。当前第1页12