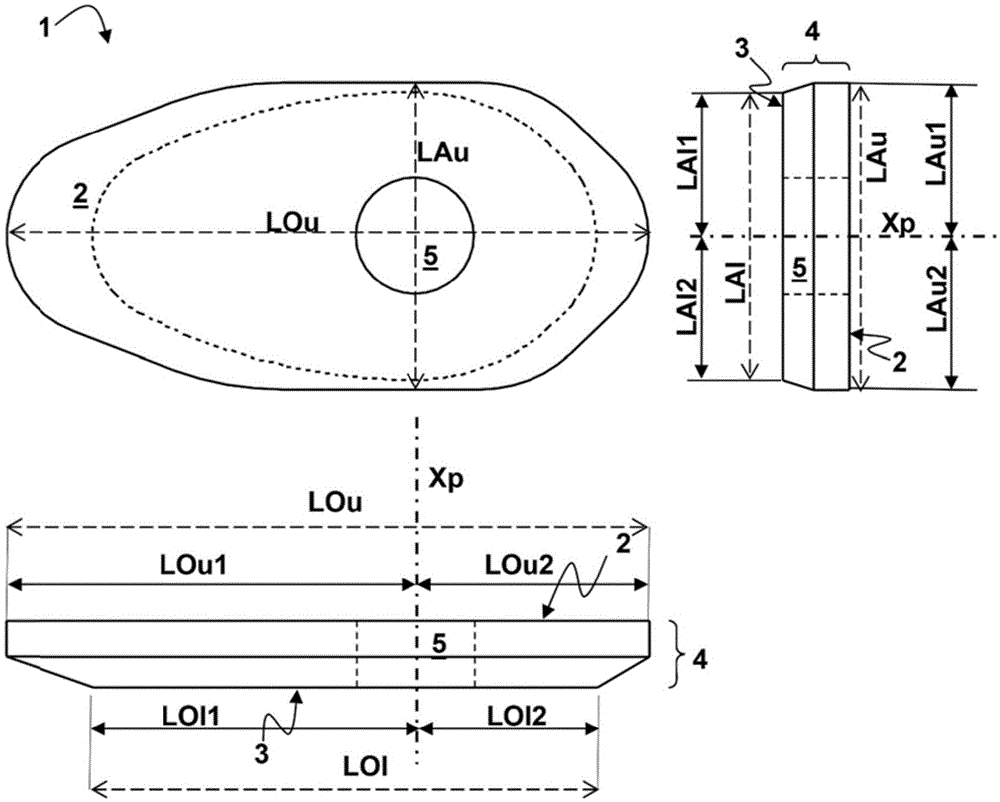
本发明涉及用于熔融金属滑动闸阀的耐火滑动闸阀板。在熔融金属的铸造过程中,滑动闸阀用于控制从上游冶金容器浇注至下游容器的熔融金属的流动。例如,从熔炉到钢水包,从钢水包到中间包或者从中间包到铸锭模具。滑动闸阀包括至少两个相对于彼此滑动的耐火滑动闸阀板。板的滑动移动可以是线性的(其中滑动闸阀沿直线方向移动)或旋转的(其中板相对于彼此旋转)。在下面的描述中,将参考熔融钢的连续铸造,但应当理解,本发明可以用于其中使用了耐火滑动闸阀板的用于调节任何熔融材料流(玻璃、金属等)的滑动闸。
背景技术:
:自1883年以来,滑动闸阀就已为人所知。例如us-a-0311902或us-a-0506328公开了布置在浇注包的底部下方的滑动闸阀,其中设置有浇注口的一对耐火滑动闸阀板相对于彼此滑动。当浇注口对齐或部分重叠时,熔融金属可以流过滑动闸阀,而当浇注口之间没有重叠时,熔融金属流动完全停止。浇注口的部分重叠允许通过使熔融金属流节流来调节熔融金属流动。在20世纪60年代末,第一个滑动闸阀板在德国实现了工业规模的使用。这项技术多年来有了显著的改进并且如今已被广泛使用。自滑动闸阀的创始时代开始,人们就注意到操作者的安全性和安装的安全性、气密性、滑动闸阀板的破裂、板的腐蚀等。可以参考例如提出使用板的两个面以及防止将板以错误的取向插入滑动闸阀的外壳中的安全概念的us-a-5893492,或者参考提出减少滑动闸阀板中裂纹萌生以及防止裂纹扩展(如果形成裂纹)的解决方案的us-b2-6814268。尽管自第一个滑动闸阀开始已取得相当大的进步,但仍有改进的空间。具体地讲,本发明人已经观察到,对于现有的滑动闸阀板,在使用期间可能发生耐火板弯曲或翘曲。据推测,该现象是由板中存在的巨大温度梯度引起的热应力(靠近浇注口的区域被穿过浇注口的熔融钢升高到1500℃以上的温度,而只有几厘米远的板周边处于约300至400℃的温度)结合为了保持板紧密接触而施加的不均匀推力引起的机械应力引起的。继而,板的此类弯曲或翘曲可以将两块板之间的有效接触面积减小到低至38%的值。在本发明的观念中,有效接触面积是板之间的实际接触面积与假定完美接触下两个板之间的理论接触面积的比率(以%表示),在两种情况下两个板完美对齐。实际接触面积和理论接触面积可以通过有限元分析来计算。这样低的有效接触面积与足够的气密性不兼容,并且可能导致空气通过板之间的接头进入通过板浇注的熔融钢。空气进入对浇注的熔融钢的质量和耐火板的预期寿命不利。具体地讲,空气氧化了用于粘合板的耐火元件的碳材料。在现有技术中已经开发了限制空气进入的影响的解决方案,例如向熔融钢浴中添加氧气清除剂(铝、钙、硅等)与氧气反应。继而,这些清除剂与氧气的反应产物会在滑动闸阀的下游产生其他问题(由于氧化铝沉积而堵塞)。还有人提出利用惰性气体(例如,氩气)保护浇注口,惰性气体在板之间的接合处的凹槽中循环或者在围绕整个滑动闸阀的密封箱中循环。除了这些解决方案的不切实际的方面之外,惰性气体价格昂贵并且对操作者具有危险性。除了空气进入问题之外,板之间的低有效接触面积也会导致翅片化,其中熔融金属的小膜(称为“翅片”)渗透两个板之间的接头。在凝固时,金属翅片刮擦两个板的表面并严重损坏它们的接触表面。此外,金属翅片充当伸展板的楔形件以促进进一步翅片化,最终导致熔融钢渗漏。本发明人尚未发现现有技术中通过修改板几何形状来解决这些问题的任何尝试。此外,本发明人还强调,由于这种不均匀地向板施加推力,局部可以观察到极高的压力峰值(高达12mpa)。如此高的压力峰值会导致磨损并显著减少耐火板的预期寿命。本发明的目的在于在解决这些问题的同时(增加操作者和安装的安全性,提高钢的质量,延长耐火板的寿命),将操作条件保持为与当前条件相当类似(板的重量、手工作业等)。技术实现要素:本发明的目的已经通过用于熔融金属闸阀的耐火滑动闸阀板实现,该耐火滑动闸阀板具有:-上表面,-下表面,该下表面通过滑动闸阀板的厚度与上表面分开,所述上表面和下表面是平坦的并且彼此平行,-将上表面连接到下表面的连接外表面以及-将上表面(2)流体连接到下表面(3)的浇注通道,所述浇注通道具有对称浇注轴线(xp),-上表面和下表面分别具有彼此平行的上部纵向范围和下部纵向范围(lou,lol)并且在垂直于上部纵向范围和下部纵向范围(lou,lol)的方向上分别具有上部横向范围和下部横向范围(lau,lal),其中上部纵向范围(lou)是连接上表面的周长的两个点并与对称浇注轴线(xp)相交的最长节段,-纵向范围(lou,lol)被分成在对称浇注轴线(xp)的水平面处连接的两个节段(分别为lou1和lou2以及lol1和lol2),并且其中节段lou1和lol1在对称浇注轴线的第一侧上,并且节段lou2和lol2在对称浇注轴线的第二侧上;-横向范围(lau,lal)被分成在对称浇注轴线(xp)的水平面处连接的两个节段(分别为lau1和lau2以及lal1和lal2),并且其中节段lau1和lal1在对称浇注轴线的第一侧上,并且节段lau2和lal2在对称浇注轴线的第二侧上;-其中以下比率定义为:r1=lol1/lou1,包括在50和95%之间,优选地在57和92%之间,更优选地在62.5和90%之间,r2=lol2/lou2,包括在50和95%之间,优选地在57和92%之间,更优选地在62.5和90%之间,r3=lal1/lau1,大于或等于75%,优选地大于或等于90%,更优选地大于或等于95%,r4=lal2/lau2,大于或等于75%,优选地大于或等于90%,更优选地大于或等于95%。在本发明的观念中,耐火滑动闸阀板应被理解为诸如插入到滑动闸阀中的板。即,“裸露的”耐火板、罐装板(即,耐火体、砂浆或粘固剂和围绕周边和表面的一部分的金属包层的组合)或带状板(即,耐火板和围绕耐火板的带的组合)。在罐装或带状板的情况下,上表面被定义为从罐/带突出的耐火平坦表面。在罐装板的情况下,下表面被定义为围绕浇注通道的平坦表面。在本发明的观念中,浇注通道的对称浇注轴线xp是具有通道几何形状的最高对称度的轴线。例如,在圆柱形浇注通道中,对称轴线xp是圆柱形通道的旋转轴线。在通道具有椭圆形横截面的情况下,对称浇注轴线是经过通道的椭圆形横截面的长轴和短轴的交点的轴线。从更一般的意义上来讲,在浇注通道完全没有对称性的不太可能的情况下,对称浇注轴线xp是垂直于上表面并且在上表面的水平面上经过通道横截面的形心的轴线。该定义适用于任何浇注通道几何形状,即时是示出高度对称性的几何形状,诸如圆柱形浇注通道。板的对称浇注轴线xp对应于相邻铸造装置的耐火元件(即,内部喷嘴或收集器喷嘴)的对称浇注轴线。在本发明的观念中,上表面被定义为“由形成所述平坦表面的周长的闭合线限定并且包括浇注通道开口的最大平坦表面”。在滑动闸阀中,第一滑动闸阀板的上表面与第二(通常不一定)相同的滑动闸阀板的上表面接触并沿其滑动。当然,为了定义上部纵向和横向范围及其相应的长度,浇注通道入口被忽略。下表面被定义为“由形成所述平坦表面的周长的闭合线限定并且包括浇注通道开口的第二大平坦表面”。该表面的所有点均包括在与上表面的平面平行的平面中。在用于包括保持在固定位置的第二滑动闸阀板的滑动闸阀时,第一滑动闸阀板的下表面是所述第一滑动闸阀板与框架和滑动机构的动态接收站的推动装置之间的接触表面,该框架保持滑动闸阀板滑动接触,并且该滑动机构控制第一滑动闸阀板和第二滑动闸阀板的浇注通道的相对位置,从而控制滑动闸阀的打开。当然,为了定义下部纵向和横向范围及其相应的长度,浇注通道入口被忽略。类似地,在罐装板(即,利用金属罐装饰的板)中,围绕浇注口用于接收收集器喷嘴或内部喷嘴的开口以及用于减轻重量或有助于夹持板的切口(如us-b1-6415967所公开的)也被忽略。在本发明的观念中,表面的纵向范围被定义为连接该表面的周长的两个点且与对称浇注轴线xp相交的最长节段,而横向范围是同一平面中沿垂直于纵向范围的方向并且与对称浇注轴线xp相交的板的范围。每个上表面和下表面的纵向范围分别被分成两个节段(lou1和lou2)以及(lol1和lol2),每个节段从对应表面的周长的一个点延伸到对称浇注轴线xp。类似地,每个上表面和下表面的横向范围分别被分成两个节段(lau1和lau2)以及(lal1和lal2),每个节段从对应表面的周长的一个点延伸到对称浇注轴线xp。根据惯例,lou1和lau1是对应的纵向范围和横向范围中最长的节段,而lou2、lau2是它们最短的节段。下表面中的节段lol1和lol2以及lal1和lal2以与上表面中相同的顺序进行编号。如果上表面给定范围的两个节段具有相同的长度,则它是下表面对应的下部范围的最长节段,其确定上表面和下表面的哪些节段标记为“1”。如果对应的下部范围也被分成具有相同长度的两个节段,则可以自由指定编号1或2,只要它们在上下表面中以相同顺序使用即可。上表面和下表面的周长是闭合的,并且优选地不包括凹度变化,其中部分周长从形成凸曲线到形成凹曲线。周长优选地是平滑的,没有切线不连续的奇点。在实际周长的限定平坦表面的一部分包括形成平坦表面的凹陷或突出舌状部的单个凹陷部或突起的情况下,纵向和横向范围被确定为忽略所述单个突起或凹陷部,并且考虑利用直线连接实际周长的两个边界点形成所述单个凹陷部或突起的边界来代替理论周长(参见图2(b))。边界点被定义为出现奇点位置处的点,曲率符号的改变或曲线的切线的不连续性。在所有情况下,应考虑理论周长而非实际周长来确定纵向和横向范围,其中两个边界点彼此分开的距离小于总理论周长长度的10%。本发明还涉及用于修整耐火元件并由此形成如上所述的滑动闸阀板的金属罐。金属罐包括:-底部表面,该底部表面由周长限定并且包括具有形心点(xp)的开口,使得对称浇注轴线(xp)是垂直于底部表面并且经过形心点(xp)的轴线;-周向表面,该周向表面从所述底部表面的周长横向于底部表面延伸到限定金属罐的边缘的自由端部,-所述周向表面和底部表面限定配合耐火元件的几何形状的几何形状的内腔,该耐火元件借助于粘固剂附着到金属罐,并且其中:-金属罐具有上部纵向直径(lcu),该上部纵向直径被定义为连接金属罐的边缘的两个点并且与对称浇注轴线(xp)相交的最长节段,并且具有上部横向直径(ldu),该上部横向直径连接金属罐的边缘的两个点,并且垂直地与上部纵向直径(lcu)和对称浇注轴线(xp)相交,-底部表面具有平行于上部纵向直径(lcu)的下部纵向直径(lcl)并且具有平行于下部纵向直径(ldu)的下部横向直径(ldl),下部纵向直径和下部横向直径两者与对称浇注轴线相交于形心点(xp)处;上部纵向直径和下部纵向直径(lcu,lcl)被分成在对称浇注轴线(xp)的水平面处连接的两个节段(分别为lcu1和lcu2以及lcl1和lcl2),并且其中节段lcu1和lcl1在对称浇注轴线的第一侧上,并且节段lou2和lol2在对称浇注轴线的第二侧上;上部横向直径和下部横向直径(ldu,ldl)被分成在对称浇注轴线(xp)的水平面处连接的两个节段(分别为ldu1和ldu2以及ldl1和ldl2),并且其中节段lau1和lal1在对称浇注轴线的第一侧上,并且节段ldu2和ldl2在对称浇注轴线的第二侧上;其中定义以下比率rc1=lcl1/lcu1,包括在50和95%之间,优选地在57和92%之间,更优选地在62.5和90%之间,rc2=lcl2/lcu2,包括在50和95%之间,优选地在57和92%之间,更优选地在62.5和90%之间,rc3=ldl1/ldu1,大于或等于75%,优选地大于或等于90%,更优选地大于或等于95%,rc4=ldl2/ldu2,大于或等于75%,优选地大于或等于90%,更优选地大于或等于95%。当使用金属罐时,它形成第一滑动闸板的下表面。当安装在滑动闸阀框架中时,力被施加到金属罐的底部表面上以将所述第一滑动闸阀板的上表面压靠静止地安装在所述框架中的第二滑动闸阀板的上表面。本发明还涉及滑动闸阀,该滑动闸阀包括安装在框架中的一组第一滑动闸阀板和第二滑动闸阀板,其中,-第一滑动闸阀板如上所述并且包括上表面,该上表面为平面并且具有由围绕浇注通道的入口的周长界定的上部区域au,并且包括下表面,该下表面为平面并且具有由围绕浇注通道(5l)的出口的周长界定的下部区域al,第一滑动闸阀板的平坦上表面和下表面彼此平行,-第二滑动闸阀板包括平坦的上表面,该上表面具有由围绕浇注通道的出口的周长界定的上部区域au并且具有与第一滑动闸阀板的上表面相同的几何形状,并且包括下表面,该下表面是平坦的并且由围绕浇注通道的入口的周长界定,第二滑动闸阀板的平坦的上表面和下表面彼此平行,其中所述第一滑动闸阀板和第二滑动闸阀板安装在框架中,其中它们各自的上表面彼此接触并彼此平行使得,-第二滑动闸阀板固定安装在框架中,-第一滑动闸阀板能够沿着平行于第一滑动阀板和第二滑动阀板的上表面的平面从浇注位置可换向地移动到闭合位置,在该浇注位置,第一滑动闸阀板的浇注通道与第二滑动闸阀板的浇注通道(5l)对齐,在该闭合位置,第一滑动闸阀板的浇注通道不与第二滑动闸阀板的浇注通道流体连通,所述滑动闸阀还包括若干推动器单元,所述多个推动器单元围绕第一滑动闸阀板的下表面分布并且将推力施加到其上以将第一滑动闸阀板的上表面压靠第二滑动闸阀板的上表面,第一滑动闸阀板垂直于第一滑动闸阀板的所述下表面取向,其特征在于,下表面的面积al与上表面的面积au的比率al/au包括在40和85%之间,其中忽略浇注通道对上部面积和下部面积(au,al)进行测量。根据本发明的另一方面,本发明涉及滑动闸阀,其被设计成使得由滑动闸阀传递到用于该滑动闸阀的滑动闸阀板的推力集中在浇注口周围。即,超过55%,优选地超过60%的接受推力的板的表面(由此的下表面)位于距离对称浇注轴线xp的小于或等于lal1的位置。在优选的实施方案中,第二滑动闸阀板也如上文那样定义。在另一个优选的实施方案中,第一滑动闸阀板与第二滑动闸阀板相同。在优选的实施方案中,第一滑动闸阀板由安装在滑动机构上的滑架支撑,使得第一滑动闸阀板的上表面能够在浇注位置与闭合位置之间滑动。滑架包括下表面,推动器单元将推力(f)施加到滑架的下表面上,以便将第一滑动闸阀板的上表面压靠第二滑动闸阀板的上表面,其中所述力(f)取向成垂直于滑架的下表面。在所述实施方案中,滑架包括优选地平行于第一滑动闸阀板的上表面并且从其中凹陷的上表面。下表面与推动器单元中的至少一些永久接触,并且优选地具有的几何形状使得推动器单元仅在纵向平面(xpl,lou)上的投影与第一滑动闸阀板的纵向平面上的投影相交的情况下才与滑架的下表面接触,纵向平面(xpl,lou)由对称浇注轴线(xpl)和力矢量的第一滑动阀板(1l)的上部纵向范围(lou)限定,该力矢量定义当与下表面接触时由所述推动器单元施加的力(f),所述几何形状优选地包括倒角部分。更优选的是,力矢量在纵向平面上的投影也与第二滑动闸阀板的所述纵向平面上的投影相交。本发明还涉及设计用于接收第一滑动闸阀板和第二滑动闸阀板的滑动闸阀的框架,其中至少第一滑动闸阀板如上文那样定义,并且可以移动使得其上表面沿着第二滑动闸阀板的上表面滑动。从下面的表格可以看出,有效接触面积已经显著增加(从现有技术板的38%到根据本发明的65%以上),并且最大压力峰值已经降低了高达50%。当r3=r4时,这些参数可以进一步改善。事实上,在这种情况下,接触更加对称并且避免了应力分布的不平衡。此外,由于上表面相对于纵向范围的不对称性似乎没有带来任何特别的优点,因此相对于纵向轴线的对称设计具有节省耐火材料的优点,因为在纵向范围的一侧上的上表面的半侧上的优化设计可以镜像地应用于上表面的另一半,而不必添加任何耐火材料。利用一对耐火滑动闸阀板测量了有效接触面积的增加值,其中r1和r2为80%±5%。同时利用根据本发明的耐火滑动闸阀测量了非常有利的特性,其中r3和r4包括在98和100%之间。当r1和r2为80%±5%并且其中r3和r4包括在98和100%之间时,可以获得更好的结果。外部连接表面可以具有任何可能的形状。例如,它可以是伪锥形表面,它可以具有圆柱形部分,它可以是纺锤或反向纺锤的形式并且它可以是单个表面或所有这些形状的组合。外部连接表面也可以具有围绕滑动闸阀板的周长变化的形状。有利的是,外表面包括多个表面部分。具体地讲,连接外表面可以包括至少圆柱形表面部分和一个或多个过渡表面部分。过渡表面部分被定义为减小平行于上表面和下表面的平面上的板表面横截面的表面。圆柱形表面允许在铸造操作期间利用保持耐火材料受压的材料(例如,金属箍或带)缠绕或绑扎板。在出现裂纹的情况下,压缩力将保持这些裂纹闭合并避免裂纹扩展。在这种情况下,更有利的是圆柱形表面将上表面连接到过渡表面,并且过渡表面将圆柱形表面连接到下表面。过渡表面不需要是唯一的并且可以由多个过渡表面组成。尽管这不是强制性的,但在最优选的情况下,根据本发明的滑动闸阀板包括具有上表面和浇注通道的耐火元件,该上表面和浇注通道分别对应于板的上表面和浇注通道;金属罐,该金属罐具有分别对应于板的下表面和浇注通道的下表面和浇注通道;以及将板粘合至罐的粘固剂。为了能够更好地理解本发明,现在将参考示出了本发明的具体实施方案的附图进行描述,但不以任何方式限制本发明。附图说明在这些附图中,图1描绘了以俯视图、侧正视图和前正视图表示的根据本发明的实施方案的板;图2和图3示出了同一块板的三维等轴视图;图4和图5示出了具有不同的r3和r4比率值的板的实施方案的侧视图;图6示出了定位成各自的上表面彼此滑动接触的两个板,如它们将定位在滑动闸阀中那样;图7示出了适用于修整根据图2和图3的板的金属罐的三维等轴视图。图8示出了滑动闸阀的优选实施方案的纵向平面(xpl,lou)上的各种投影,示出了推动器何时与滑架接触或不接触。具体实施方式图1至图3示出了用于具有上表面2和下表面3的熔融金属闸阀的耐火滑动闸阀板1。上表面和下表面平行,如通常在滑动闸阀中的情况那样,并且它们被滑动闸板的厚度彼此分开。在图1至图3中,滑动闸板被描绘为裸露的,即没有围绕或保护板的金属罐或带。在图4和图5中,描绘了罐装滑动闸阀板的横向范围。在图6中,根据本发明的两个相同的罐装板描绘在它们用于滑动闸阀的相应位置中:(a)在打开构型中,其中第一滑动闸阀板和第二滑动闸阀板的浇注通道对齐,并且(b)其中它们几乎未流体连通,从而显著降低了浇注金属熔体的流速。推动器单元将力f施加到第一滑动闸阀板的下表面上,使得其上表面压靠第二滑动闸阀板的上表面。图7示出了金属罐。滑动闸阀板的上表面和下表面2,3通过连接外表面4连接。在板1上还可见的是在内部将上表面2流体连接到下表面3的浇注通道5。还描绘了浇注通道5的对称浇注轴线xp。还示出了上表面和下表面2,3的上部纵向范围和下部纵向范围(lou,lol),并且在垂直于上部纵向范围和下部纵向范围(lou,lol)的方向上存在上表面横向范围和下表面横向范围(lau,lal)。上部纵向范围和下部纵向范围(lou,lol)被分成在对称浇注轴线(xp)的水平面处连接的两个节段(分别为lou1和lou2以及lol1和lol2)。类似地,上部横向范围和下部横向范围(lau,lal)被分成在对称浇注轴线(xp)的水平面处连接的两个节段(分别为lau1和lau2以及lal1和lal2)。定义以下比率:r1=lol1/lou1,r2=lol2/lou2,r3=lal1/lau1和r4=lal2/lau2。在图1至图3的实施方案中,r1为约80%(即,包括在65和90%之间),r2为约80%(即,包括在65和90%之间),r3=r4为约95%(即,大于或等于90%)。图4和图5示出了根据本发明的滑动闸阀板的两个实施方案,其中板1由耐火体、砂浆或粘固剂6以及围绕周边和耐火体的下表面的一部分的金属罐7的组合形成。在图4和图5中,由于板相对于纵向轴线对称地形成,因此r3和r4相等。在图4中,r3等于100%并且在图5中等于约95%。如在这些附图中可见的那样,滑动闸阀板的下表面由限定金属罐的平坦表面的周长的外边界限定,该金属罐修整陶瓷体。图7示出了根据本发明的用于修整耐火体以一起形成滑动闸阀板的金属罐的实施方案。金属罐可以包括底部表面(3m),该底部表面为平坦的并由周长限定并且包括具有形心点(xp)的开口(15),使得对称浇注轴线(xp)是垂直于底部表面的平面并且经过形心点(xp)的轴线。图7中用虚线在开口(15)内表示的虚拟圈表示当罐修整所述耐火体时,浇注通道(5)穿过耐火体的位置。周向表面(4ma,4mb),该周向表面从所述底部表面的周长横向于底部表面延伸到限定金属罐的边缘(4r)的自由端部,从而与该底部表面形成配合耐火元件的几何形状的几何形状的腔,该耐火元件借助于粘固剂附着到金属罐。上部纵向直径(lcu)被定义为连接金属罐的边缘的两个点并且与对称浇注轴线(xp)相交的最长节段。上部横向直径(ldu)连接金属罐的边缘的两个点,并且垂直地与上部纵向直径(lcu)和对称浇注轴线(xp)相交。底部表面(3m)具有平行于所述上部纵向直径(lcu)的下部纵向直径(lcl)并且具有平行于所述下部纵向直径(ldu)的下部横向直径(ldl),所述下部纵向直径和所述下部横向直径两者与所述对称浇注轴线相交于所述形心点(xp)处。当联接到耐火体时,金属罐的底部表面限定滑动闸阀板的下表面。忽略开口(15),确定纵向直径和横向直径的长度。定义以下比率rc1=lcl1/lcu1,包括在50和95%之间,优选地在57和92%之间,更优选地在62.5和90%之间,rc2=lcl2/lcu2,包括在50和95%之间,优选地在57和92%之间,更优选地在62.5和90%之间,rc3=ldl1/ldu1,大于或等于75%,优选地大于或等于90%,更优选地大于或等于95%,rc4=ldl2/ldu2,大于或等于75%,优选地大于或等于90%,更优选地大于或等于95%。如图6所示,在使用中,根据本发明的第一滑动闸阀板(1l)安装在滑动闸阀框架中,其上表面(2l)平行于第二滑动闸阀板(1u)的上表面(2u)并与其接触,第二滑动闸阀板包括浇注通道(5u)。此类滑动闸阀框架包括用于将第二阀板(1u)保持在固定位置的静态接收站;当框架安装在包括出口的冶金容器(诸如钢水包)的底部时,第二滑动闸板被固定在使得浇注通道(5u)与冶金容器出口对齐的位置。框架还包括动态接收站,该动态接收站包括用于保持第一滑动阀板及其上表面(2l)以滑动关系平行面向第二滑动闸阀板的上表面(2u)并与其接触的滑架(10)。动态接收站还包括若干推动器单元(11),该推动器单元_被取向并分布成以便向滑架的下表面施加推力(f),该推力被传递到第一滑动闸阀板(1l)的下表面(3l)并且取向成垂直于第一滑动闸阀板的所述下表面(3l),以将第一滑动闸阀板的上表面压靠第二滑动闸阀板的上表面。推进器单元在滑架和第一滑动闸阀板的下表面上的分布已被发明人确认为对第一滑动闸阀板和第二滑动闸阀板的上表面之间实现的有效接触面积至关重要。针对具有如上所定义的比率r1至r4的第一滑动闸阀板的几何形状,令人惊讶的是,与现有技术的滑动闸板阀相比,可以提高有效接触面积并且可以极大降低板上测量的机械应力峰值(参见下面的表1至iii)。框架包括滑动机构,该滑动机构通过在第二滑动闸阀板(1u)的上表面(2u)上将第一滑动闸阀板(1l)的上表面(2l)从浇注位置滑动到闭合位置,在该浇注位置,第一滑动闸阀板(1u)的浇注通道(5u)与第二滑动闸阀板(1l)的浇注通道(5l)对齐,在该闭合位置,第一滑动闸阀板(1u)的浇注通道不与第二滑动闸阀板(1l)的所述浇注通道流体连通,从而使保持第一滑动闸阀板(1l)的滑架相对于第二滑动闸阀板(1u)移动。滑动机构通常是固定在滑动闸阀板(1l)的连接外表面(4)的一端的电动、气动或液压臂,并且能够在第二静态滑动闸阀板(1u)的上表面(2u)上推动、拉动或旋转第一滑动闸阀板。通过将第一滑动闸阀板安装在动态接收站的滑架中并且将第二滑动闸阀板安装在静态接收站中形成滑动闸。第一滑动板的下表面的面积al与第一滑动板的上表面的面积au的比率al/au包括在40和85%之间。优选地,第一滑动闸阀板是根据本发明的滑动闸阀板。更优选地,第二滑动闸阀板也是根据本发明的滑动闸阀板。第二滑动闸阀板可以与第一滑动闸阀板类似或甚至相同。滑动闸阀被设计成使得由滑动闸阀传递到用于该滑动闸阀的滑动闸阀板的推力集中在浇注口周围。即,超过55%,优选地超过60%的接受推力的板的表面(由此的下表面)位于距离对称浇注轴线xp的小于或等于lal1的位置。针对图1所示的板,接受推力的板的63%的表面(由此的下表面)位于距离对称浇注轴线xp的小于或等于lal1的位置。用于将第一板保持在动态接收站中的滑架(10)包括下表面和上表面。上表面优选地平行于安装在其中的第一滑动闸阀板的上表面并且从其中凹陷。当滑架平行且相对于第二滑动闸阀板的上表面移动时,其也相对于推动器单元(11)移动。在现有技术的滑架中,无论滑架相对于推动器单元的位置如何,推动器单元总是与滑架的下表面接触。由于滑架的上表面相对于第一滑动闸阀板的上表面凹陷,所以在滑架处于第一滑动闸阀板不面向推动器单元的位置的情况下;所述推动器单元的力将在动态接收站上施加悬臂上的弯曲应力。这会在滑动闸阀板的边缘形成应力集中,从而加速磨损。它还会释放浇注通道周围的压力,从而降低滑动闸阀的密封性。已经发现,这个问题可以通过设计滑架的底部表面来解决,使得它始终与至少一个推动器单元接触,并且使得推动器单元仅在纵向平面(xpl,lou)上的投影与第一滑动闸阀板的纵向平面上的投影相交的情况下才与滑架的下表面接触,纵向平面(xpl,lou)由对称浇注轴线(xpl)和力矢量的第一滑动阀板(1l)的上部纵向范围(lou)限定,该力矢量定义当与下表面接触时由所述推动器单元施加的力(f)。优选地,推动器单元将力施加到滑架的下表面上也需要力矢量在纵向平面上的投影与第二滑动闸阀板的纵向平面上的投影相交。由于滑动闸阀中的推动器单元和第二滑动闸阀板都是静止的,因此该条件的实现与第一滑动闸阀板相对于推动器单元的位置无关。如果所述投影的力矢量实际上穿过投影的滑动闸阀板,或者落在沿着纵向平面测量的推动器单元的一半宽度的公差内,则认为投影的力矢量与投影的滑动闸阀板相交。例如,如果推动器单元包括螺旋弹簧,则公差将是所述螺旋弹簧中最靠近滑架的最后一个线圈的直径的一半。如有疑问,公差无论如何都在20mm以内,优选地在投影的力矢量与投影的滑动闸阀板之间的实际交点的10mm以内。如沿着图8的纵向平面的剖视图所示,所述几何形状可包括倒角部分。可以看出,图8的滑动闸阀被设计成使得推动器单元面向第二滑动闸阀板。由于两者都是静止的,因此无论第一滑动闸阀板的位置如何都将保持这种情况。在图8(a)中,第一滑动闸阀板处于浇注位置,其中上部浇注通道和下部浇注通道形成单个连续通道。可以看出,在所示的五个推动器单元(11)中,其中仅四个面向第一滑动闸阀板(1l)。这四个接触的推动器单元也与滑架的下表面接触,并在其上施加垂直力,传递到第一滑动闸阀板。图8(a)左手边的第五个推动器单元不面向第一滑动闸阀板并且也不与滑架的下表面接触(或者不对其施加实质力),滑架的下表面在所述部分被倒角。这样,第五个推动器单元不会将弯曲力施加到滑架上,倾向于减小滑架的上表面与第二滑动闸阀板之间的距离。在图8(b)中,滑动闸阀处于第一闭合位置,其中上部浇注通道和下部浇注通道未流体连通,但彼此之间仅分开较短的距离。因此,滑动闸阀的密封性取决于分别集中在上部浇注通道和下部浇注通道周围的最大压缩力。在这个位置,图8(b)所示的所有五个推动器单元均与滑架的下表面接触,施加集中在浇注通道周围的高压缩压力。在图8(c)中,滑动闸通道处于闭合位置,其中上部浇注通道与下部浇注通道之间存在很大的距离。图8(c)右-手边所示的推动器单元不面向第一滑动闸阀板并且也不与滑架的下表面接触(或者不对其施加实质力),滑架的下表面在所述部分被倒角。这样,如参考图8(a)所讨论的那样,右-手边的推动器单元不会将弯曲力施加到滑架上,倾向于减小滑架的上表面与第二滑动闸阀板之间的距离。如上文参考图8所述的滑架(10)可有利地与任何类型的滑动闸阀板一起使用,因为它延长了滑动闸阀板的使用寿命。然而,更有利的是与根据本发明的第一滑动闸阀板一起使用并且优选地与根据本发明的第二滑动闸阀板一起使用,因为与滑架的下表面接触的推动器单元施加的力更均匀地分布在第一滑动闸阀板和第二滑动闸阀板的上表面的较大区域上,所述区域围绕浇注通道延伸。压力在更大区域上更好地分布具有两个优点。首先,它防止了对滑动闸阀板的完整性不利的压力峰值,从而延长其使用寿命。其次,它防止了当压力峰值存在时不可避免的较低压力区域,从而增加了滑动闸阀的密封性。这对于减少第一滑动闸阀板与第二滑动闸阀板之间的氧气进入和熔融金属进入至关重要。为了证明本发明的效果,发明人已经对安装在滑动闸阀中的两个滑动闸阀板的实际和理论接触面积执行了许多有限元分析计算。这些计算没有考虑热量的影响。在第一系列中,设计了对应于us-b2-6814268的滑动闸阀。该模型包括底板、承板、门、两个耐火滑动闸阀板以及钢水包包底。通过多个弹簧将推力施加在板上,以便保持板受压并增加两个板之间的接触面积。计算的第一个输出是最大接触压力(mpa),它是耐火滑动闸阀板之间的接触表面的最高压力峰值。当两个板的浇注通道完美对齐时,有效接触面积是通过有限元分析计算出的滑动闸阀板之间的实际接触面积(忽略周边的任何孔)与理论接触面积(假定完美接触)的比率(以%计)。例如,如果滑动闸阀板的理论接触面积等于1000mm2并且计算出的实际接触面积为250mm2。则有效接触面积(%)为250/1000=0.25=25%。利用us-b2-6814268中所述的板(现有技术:其中r1=r2=r3=r4=100%;为了比较)和根据本发明的板进行计算。结果列于下表i至iii。在这些实施例中,r4保持等于r3。在实际和理论接触面积之间观察到的(和计算出的)偏差一方面是由于熔融金属流过浇注通道所施加的机械应力,另一方面是由于在滑动闸阀板的体积内形成的显著热梯度。表i(r3(=r4)的影响)实施例现有技术1234r1100%80%80%80%80%r2100%80%80%80%80%r3100%95%97%99%100%有效接触面积(%)38.468.364.561.760.1最大接触压力(mpa)12.86.16.77.27.6如表i中所见,对于根据本发明的板,有效接触面积从现有技术板的38.4%提高到68.3%(实施例1)。同时,最大接触压力从12.8mpa降至6.1mpa。保持r1和r2恒定,将r3(和r4)从95%增加至100%,对有效接触面积(从68.3%降至60.1%)和最大接触压力(从6.1增加至7.6mpa)具有很小的负面影响。所有的测量值仍然可以接受,并且远远好于现有技术板所能观察到的值。表ii(r2的影响)实施例现有技术5678r1100%80%80%80%80%r2100%90%90%90%90%r3100%95%97%99%100%有效接触面积(%)38.460.957.153.952.2最大接触压力(mpa)12.87.17.78.28.8表ii基于类似于表i的实施例,其中r2变为90%(而非表i中的80%)。对于r3(和r4)的影响,可以观察到相同的趋势。此外,可以观察到,将r2从80%提高到90%对有效接触面积和最大接触压力都有负面影响(可以通过比较实施例对1-5、2-6、3-7、4-8得出结论)。因此,根据本发明,r2不应超过90%。表iii(r1的影响)实施例现有技术9101112r1100%90%90%90%90%r2100%80%80%80%80%r3100%95%97%99%100%有效接触面积(%)38.467.364.260.759.1最大接触压力(mpa)12.86.86.97.77.9表iii基于类似于表i的实施例,其中r1变为90%(而非表i中的80%)。对于r3(和r4)的影响,可以观察到相同的趋势。此外,可以观察到,将r1从80%提高到90%对有效接触面积和最大接触压力都有负面影响(可以通过比较实施例对1-9、2-10、3-11、4-12得出结论)。因此,根据本发明,r1不应超过90%。在第二系列有限元分析计算中,为了模拟热冲击,将模拟由流过板的浇注通道的熔融钢传输的热通量的边界条件在浇注通道壁的水平面处应用于系统。在上述现有技术板上,在根据本发明的裸露耐火滑动闸阀板上(r1=r2=80%,r3=r4=95%),在独立的罐装板上(即,耐火板、砂浆或粘固剂和围绕周边和表面的一部分的金属包层的组合;r1=r2=80%,r3=r4=95%)以及在滑动闸阀中的罐装板(相同板)上执行相同的分析。这些模型之间的比较允许量化热应力以及热机械应力。针对多个实施例重复进行计算,其中连接外表面不同。这些有限元分析计算确认在第一系列中观察到的趋势。当前第1页12