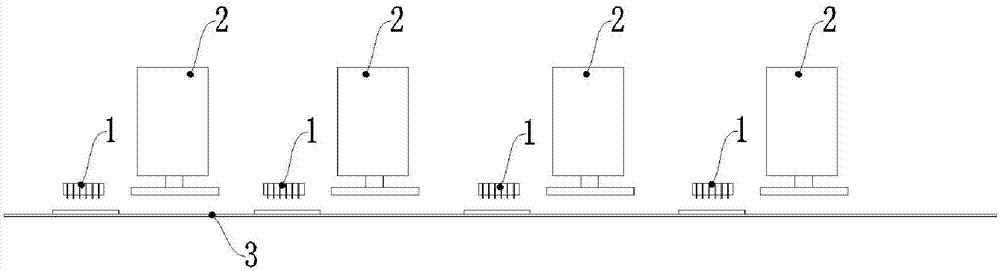
本发明涉及建筑陶瓷生产
技术领域:
,尤其涉及一种改善抛釉砖表面毛细孔的方法。
背景技术:
抛釉类产品由于表面都要淋一层低温透明釉形成玻璃相釉层从而提高釉面透感,但由于后期釉料温度的波动、窑炉温度的波动等因素导致釉层在高温煅烧时坯釉中的有机物氧化释放气体,如果釉在熔化之前气体还没充分时排除干净,从而使得釉层表面有大量细小气泡浮在釉层上层,抛光磨块切削打磨砖面后,砖面上浮气泡被磨穿,通过打蜡后,蜡水填进了气泡孔洞中,从而导致砖面形成密集白点气孔现象,影响产品美观、产品质量。一般可通过调整窑炉烧成曲线或提高釉的高温黏度解决气孔问题,但是仍难以避免出现不合格品。专利200610123726.x公开了一种纳米防污抛光砖生产工艺,将无机硅化合物液态纳米材料渗入未打蜡的抛光砖坯中,然后烧制实现两者的结合,进而实现防污效果,但是该纳米需要多次导入,每次导入都要进行一次烧制,这种工艺操作复杂、成本高,不利于广泛应用。技术实现要素:本发明的目的在于提出一种改善抛釉砖表面毛细孔的方法,具有成本低、提高产品合格率的特点。为达此目的,本发明采用以下技术方案:一种改善抛釉砖表面毛细孔的方法,包括以下步骤:静置:将出窑的有气孔瓷砖静置完全释放热应力;抛切:对有气孔瓷砖的表面进行抛切,抛切量为0.07~0.1mm;滴墨:采用滴管以滴定的方式将陶瓷墨水滴入抛切后有气孔瓷砖上的破口孔洞中,根据抛切后有气孔瓷砖上的破口孔洞数量和大小确定陶瓷墨水的摄入量;固化:以抛光磨盘加压加热的方式,使陶瓷墨水充分填充破口孔洞,加压压力为1~4kg/m2,加热温度为40~60℃;打蜡抛光,得抛釉砖成品。通过设定对有孔瓷砖的抛切量,既能保证将绝大部分的上浮气泡抛切形成开口,又能保证气泡抛破后的孔洞直径不过大,减少陶瓷墨水的填充量,节约成本。使陶瓷墨水填充由于气泡上浮产生的孔洞,不仅能够保证产品图案色彩的一致性,提高产品的合格率,还能提高产品的防污效果。进一步的,滴墨步骤中,针对同一生产批次随机选取4~6块有气孔瓷砖,确定每块砖的陶瓷墨水摄入量,选用陶瓷墨水的最大摄入量作为该生产批次有气孔瓷砖的陶瓷墨水填充量。通过对陶瓷填充量的设定,实现对陶瓷墨水施用量的定量,使本改善抛釉砖表面毛小孔的方法实现自动化应用,提高生产效率。进一步的,有气孔瓷砖的釉面有多种颜色时,将瓷砖釉面根据颜色的不同分割为多个色块,每个色块分别对应有滴注对应颜色的滴管,每个色块对应的滴管数量以及滴管的位置根据该色块的形状及大小进行设置。针对不同色块滴注不同颜色的墨水,保证的抛釉砖图案色彩的一致性,使得处理过后的产品与未处理产品有同等的装饰效果。多个色块的划分,陶瓷墨水的滴注位置更容易控制,降低工艺难度。进一步的,有气孔瓷砖的釉面有多种颜色时,首先对相间隔的色块进行滴墨和固化步骤,然后对其他未填充的间隔色块进行滴墨和固化步骤,如此重复,直至所有色块全部填充完毕。这种分布填充陶瓷墨水的方法能有效防止相邻色块的陶瓷墨水融合发生干扰,尤其是相邻色块的颜色差异很大时,两种陶瓷墨水发生干扰严重影响抛釉砖的图案装饰效果。进一步的,滴墨和固化步骤中,所述有气孔瓷砖放置在输送带上,所述抛光磨盘的具有线性排列的多组,相邻两组抛光磨盘之间以及固化起始抛光磨盘上游均设置有滴管,所述滴管连接有升降装置,当滴管在有气孔瓷砖滴注陶瓷墨水时,所述滴管的最低端与有气孔瓷砖的间距为1~3cm。滴墨和固化步骤采用这种流水线生产方式,在很大程度上提高了生产的效率。滴管和有气孔瓷砖的间距设置进一步提高陶瓷墨水滴注的准确。进一步的,在滴墨步骤中,所述输送带的输送速度为1~3cm/s,所述滴管的滴液速度为2~5滴/s。输送带的速度和滴管的滴液速度相适应,在保证滴注准确性的前提下,提高整体滴注速度,提高生产效率。进一步的,陶瓷墨水由4~6种纯色墨水和溶剂通过摇墨装置混合均匀获得,所述摇墨装置与墨水容器相连通,所述墨水容器与滴管相连通,所述滴管上设置有流量调节件。进一步的,纯色墨水的颜料粒径为250~350nm,25℃下流速10~15s,固含量为40%。进一步的,还包括筛选步骤:烧成瓷砖由传送装置输送出窑,所述传送装置的尾端设置有筛选装置,所述筛选装置用筛选将出窑瓷砖中的有气孔瓷砖,所述筛选装置采用图像处理的方式识别有气孔瓷砖。有气孔瓷砖的筛选采用自动筛选的方式,相对于人工筛选,不仅可以提高筛选的准确性,还能提高筛选的速度。进一步的,陶瓷墨水采用超出使用有效期的陶瓷墨水。当陶瓷墨水超出有效期后,其烧制的发色效果变差,但在低温固化的情况下不会影响其发色效果,因此,本发明的方法可以采用超出使用有效期的陶瓷墨水,进一步降低生产成本。本发明的有益效果为:通过设定对有孔瓷砖的抛切量,既能保证将绝大部分的上浮气泡抛切形成开口,又能保证气泡抛破后的孔洞直径不过大,减少陶瓷墨水的填充量,节约成本。使陶瓷墨水填充由于气泡上浮产生的孔洞,不仅能够保证产品图案色彩的一致性,提高产品的合格率,还能提高产品的防污效果。本发明通过对具有多种色彩的有气孔瓷砖进行色块划分,分别对不同的色块进行滴注陶瓷墨水,不仅可以提高陶瓷墨水滴注的准确性,提高产品的图案色彩效果,还能够提高生产效率。附图说明图1是本发明一个实施例的滴管、抛切磨头和输送带的位置关系示意图;其中,滴管1、抛切磨头2、输送带3。具体实施方式下面结合附图及具体实施方式进一步说明本发明的技术方案。一种改善抛釉砖表面毛细孔的方法,包括以下步骤:静置:将出窑的有气孔瓷砖静置完全释放热应力;抛切:对有气孔瓷砖的表面进行抛切,抛切量为0.07~0.1mm;滴墨:采用滴管以滴定的方式将陶瓷墨水滴入抛切后有气孔瓷砖上的破口孔洞中,根据抛切后有气孔瓷砖上的破口孔洞数量和大小确定陶瓷墨水的摄入量;固化:以抛光磨盘加压加热的方式,使陶瓷墨水充分填充破口孔洞,加压压力为1~4kg/m2,加热温度为40~60℃;打蜡抛光,得抛釉砖成品。通过设定对有孔瓷砖的抛切量,既能保证将绝大部分的上浮气泡抛切形成开口,又能保证气泡抛破后的孔洞直径不过大,减少陶瓷墨水的填充量,节约成本。使陶瓷墨水填充由于气泡上浮产生的孔洞,不仅能够保证产品图案色彩的一致性,提高产品的合格率,还能提高产品的防污效果。优选的,滴墨步骤中,针对同一生产批次随机选取4~6块有气孔瓷砖,确定每块砖的陶瓷墨水摄入量,选用陶瓷墨水的最大摄入量作为该生产批次有气孔瓷砖的陶瓷墨水填充量。通过对陶瓷填充量的设定,实现对陶瓷墨水施用量的定量,使本改善抛釉砖表面毛小孔的方法实现自动化应用,提高生产效率。需要说明的是,在一些实施方式中,根据瓷砖的大小设定滴注陶瓷墨水的量,滴注量为1~2滴/m2。优选的,有气孔瓷砖的釉面有多种颜色时,将瓷砖釉面根据颜色的不同分割为多个色块,每个色块分别对应有滴注对应颜色的滴管,每个色块对应的滴管数量以及滴管的位置根据该色块的形状及大小进行设置。针对不同色块滴注不同颜色的墨水,保证的抛釉砖图案色彩的一致性,使得处理过后的产品与未处理产品有同等的装饰效果。多个色块的划分,陶瓷墨水的滴注位置更容易控制,降低工艺难度。优选的,有气孔瓷砖的釉面有多种颜色时,首先对相间隔的色块进行滴墨和固化步骤,然后对其他未填充的间隔色块进行滴墨和固化步骤,如此重复,直至所有色块全部填充完毕。这种分布填充陶瓷墨水的方法能有效防止相邻色块的陶瓷墨水融合发生干扰,尤其是相邻色块的颜色差异很大时,两种陶瓷墨水发生干扰严重影响抛釉砖的图案装饰效果。优选的,滴墨和固化步骤中,有气孔瓷砖放置在输送带上,抛光磨盘的具有线性排列的多组,相邻两组抛光磨盘之间以及固化起始抛光磨盘上游均设置有滴管,滴管连接有升降装置,当滴管在有气孔瓷砖滴注陶瓷墨水时,滴管的最低端与有气孔瓷砖的间距为1~3cm。滴墨和固化步骤采用这种流水线生产方式,在很大程度上提高了生产的效率。滴管和有气孔瓷砖的间距设置进一步提高陶瓷墨水滴注的准确。优选的,在滴墨步骤中,输送带的输送速度为1~3cm/s,滴管的滴液速度为2~5滴/s。输送带的速度和滴管的滴液速度相适应,在保证滴注准确性的前提下,提高整体滴注速度,提高生产效率。优选的,陶瓷墨水由4~6种纯色墨水和溶剂通过摇墨装置混合均匀获得,摇墨装置与墨水容器相连通,墨水容器与滴管相连通,滴管上设置有流量调节件。4~6种纯色墨水和溶剂可以实现足够种类的颜色调配。优选的,纯色墨水的颜料粒径为250~350nm,25℃下流速10~15s,固含量为40%。这种墨水有良好的流动性和固化效果。本发明的纯色墨水和溶剂均是现有的,溶剂用于调浅墨水颜色,溶剂是与陶瓷墨水同配方体系的墨水清洗剂。优选的,还包括筛选步骤:烧成瓷砖由传送装置输送出窑,传送装置的尾端设置有筛选装置,筛选装置用筛选将出窑瓷砖中的有气孔瓷砖,筛选装置采用图像处理的方式识别有气孔瓷砖。当识别出有气孔瓷砖时,筛选装置的拨杆,将该瓷砖拨动至筛除传送带上,由筛除传送待将该有气孔瓷砖传送至静置区。有气孔瓷砖的筛选采用自动筛选的方式,相对于人工筛选,不仅可以提高筛选的准确性,还能提高筛选的速度。优选的,陶瓷墨水采用超出使用有效期的陶瓷墨水。当陶瓷墨水超出有效期后,其烧制的发色效果变差,但在低温固化的情况下不会影响其发色效果,因此,本发明的方法可以采用超出使用有效期的陶瓷墨水,进一步降低生产成本。实施方式1针对花纹图案均匀单一的抛釉砖本实施方式的一种改善抛釉砖表面毛细孔的方法,包括以下步骤(1)~(6):(1)筛选:烧成瓷砖由传送装置输送出窑,传送装置的尾端设置有筛选装置,筛选装置用筛选将出窑瓷砖中的有气孔瓷砖,筛选装置采用图像处理的方式识别有气孔瓷砖。(2)静置:将出窑的有气孔瓷砖静置完全释放热应力。(3)抛切:对有气孔瓷砖的表面进行抛切,抛切量为0.07~0.1mm。(4)滴墨:采用滴管以滴定的方式将陶瓷墨水滴入抛切后有气孔瓷砖上的破口孔洞中。根据抛切后有气孔瓷砖上的破口孔洞数量和大小确定陶瓷墨水的摄入量,陶瓷墨水滴注完成后,采用刮平装置,使陶瓷墨水均匀分布。针对同一生产批次随机选取4~6块有气孔瓷砖,确定每块砖的陶瓷墨水摄入量,选用陶瓷墨水的最大摄入量作为该生产批次有气孔瓷砖的陶瓷墨水填充量。或者根据瓷砖的大小设定滴注陶瓷墨水的量,滴注量为1~2滴/m2。滴管具有多个,多个滴管平均分布,平均1~2cm2对应一支滴管,保证滴注的平均性。(5)固化:以抛光磨盘加压加热的方式,使陶瓷墨水充分填充破口孔洞,加压压力为1~4kg/m2,加热温度为40~60℃。(6)打蜡抛光,得抛釉砖成品。实施方式2针对花纹色彩多样化的抛釉砖本实施方式的一种改善抛釉砖表面毛细孔的方法,包括以下步骤(1)~(6):(1)筛选:烧成瓷砖由传送装置输送出窑,传送装置的尾端设置有筛选装置,筛选装置用筛选将出窑瓷砖中的有气孔瓷砖,筛选装置采用图像处理的方式识别有气孔瓷砖。(2)静置:将出窑的有气孔瓷砖静置完全释放热应力。(3)抛切:对有气孔瓷砖的表面进行抛切,抛切量为0.07~0.1mm。(4)滴墨:采用滴管以滴定的方式将陶瓷墨水滴入抛切后有气孔瓷砖上的破口孔洞中。根据抛切后有气孔瓷砖上的破口孔洞数量和大小确定陶瓷墨水的摄入量。针对同一生产批次随机选取4~6块有气孔瓷砖,确定每块砖的陶瓷墨水摄入量,选用陶瓷墨水的最大摄入量作为该生产批次有气孔瓷砖的陶瓷墨水填充量。(5)固化:以抛光磨盘加压加热的方式,使陶瓷墨水充分填充破口孔洞,加压压力为1~4kg/m2,加热温度为40~60℃。有气孔瓷砖的釉面有多种颜色时,将瓷砖釉面根据颜色的不同分割为多个色块,每个色块分别对应有滴注对应颜色的滴管,每个色块对应的滴管数量以及滴管的位置根据该色块的形状及大小进行设置。每个色块对应有一个或多个滴管,多个滴管平均分布,平均1~2cm2对应一支滴管,保证滴注的平均性。首先对相间隔的色块进行滴墨和固化步骤,然后对其他未填充的间隔色块进行滴墨和固化步骤,如此重复,直至所有色块全部填充完毕。如图1所示,有气孔瓷砖放置在输送带3上,抛光磨盘2的具有线性排列的多组,相邻两组抛光磨盘2之间以及固化起始抛光磨盘2上游均设置有滴管1,滴管1连接有升降装置,当滴管1在有气孔瓷砖滴注陶瓷墨水时,滴管1的最低端与有气孔瓷砖的间距为1~3cm。输送带3的输送速度为1~3cm/s,滴管1的滴液速度为2~5滴/s。(6)打蜡抛光,得抛釉砖成品。在实施方式1和2中,陶瓷墨水由4~6种纯色墨水和溶剂通过摇墨装置混合均匀获得,摇墨装置与墨水容器相连通,墨水容器与滴管相连通,滴管上设置有流量调节件。纯色墨水的颜料粒径为250~350nm,25℃下流速10~15s,固含量为40%。优选的,陶瓷墨水采用超出使用有效期的陶瓷墨水。当陶瓷墨水超出有效期后,其烧制的发色效果变差,但在低温固化的情况下不会影响其发色效果,因此,本发明的方法可以采用超出使用有效期的陶瓷墨水,进一步降低生产成本。实施方式1中的滴墨量设置方式、固化加压压力和加热温度有多种实施方式,具体按照下表来设置:序号滴墨量设置方式固化加压压力固化加热温度101随机选取瓷砖的最大滴墨量1kg/m260℃102随机选取瓷砖的最大滴墨量2kg/m255℃103随机选取瓷砖的最大滴墨量3kg/m250℃104滴注量为1~2滴/m23kg/m245℃105滴注量为1~2滴/m24kg/m240℃采用上述参数获得的抛釉砖的砖面效果如下表所示。序号抛釉砖的砖面效果101砖面偶有细小白点出现,填充陶瓷墨水色彩与原图案色彩稍有偏差102砖面无白点出现,填充陶瓷墨水色彩与原图案色彩相近,砖面平整光滑103砖面无白点出现,填充陶瓷墨水色彩与原图案色彩相近,砖面平整光滑104砖面无白点出现,填充陶瓷墨水色彩与原图案色彩相近,砖面平整光滑105砖面偶有细小白点出现,填充陶瓷墨水色彩与原图案色彩稍有偏差由以上对比实验数据可知,两中滴墨量的设置方式均能得到较好的效果;砖面偶有细小白点出现,填充陶瓷墨水色彩与原图案色彩稍有偏差的原因是固化加压压力和加热温度不足导致,可知,加压压力2~3kg/m2,固化加热温度45~55℃是最佳范围。以上结合具体实施例描述了本发明的技术原理。这些描述只是为了解释本发明的原理,而不能以任何方式解释为对本发明保护范围的限制。基于此处的解释,本领域的技术人员不需要付出创造性的劳动即可联想到本发明的其它具体实施方式,这些方式都将落入本发明的保护范围之内。当前第1页12