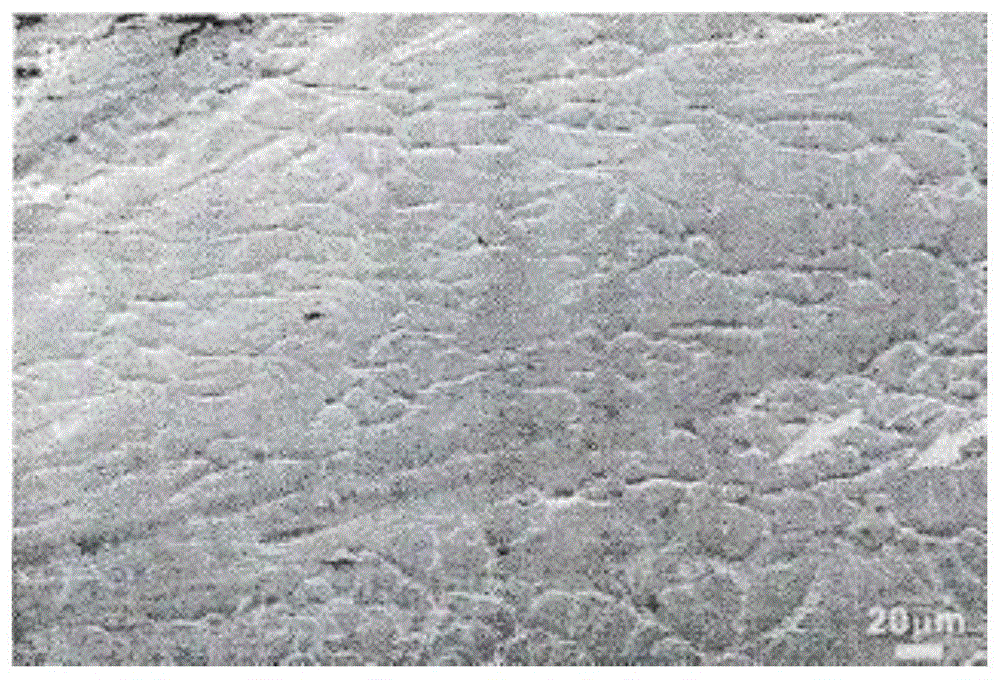
本发明属于铝合金材料领域,尤其涉及一种具有高综合性能的合金材料及其制备方法。
背景技术:
:按照原子排列的方式可以将物质分为晶体和非晶体两大类,当材料的原子排列方式呈规则有序时为晶体材料,反之原子排列方式无规则可寻则为非晶体。当固体合金的原子排列结构跟液态金属相类似,是一种长程无序的混乱状态时,称之为非晶合金。非晶态可以通过物质冷却过程中不发生结晶获得,也可以通过气相沉积、离子束混合等方法制备得到。非晶态合金与传统的氧化物玻璃不同,非晶合金中原子间是通过金属键相连而不是共价键,所以金属的很多优良特性在非晶态合金中得以保留而表现出优异的性能。作为一类先进的金属材料,非晶合金由于其无序的原子结构表现出极为优异的力学性能,如高强度、高硬度、大弹性极限(约2%)、较好的耐磨性以及在过冷液相区的超塑性成型能力等,在精密机械、海洋工程、航空航天和生物医疗等高新
技术领域:
具有广阔的应用前景,因而受到人们的广泛关注。但是块体非晶合金由于晶体缺陷(如位错,晶界等)的缺失,非晶合金失去了传递塑性应变的介质,导致其室温变形在屈服后迅速出现局域化,进而形成剪切带变形,并造成灾难性断裂,大多数块体非晶合金在宏观上表现出很有限的塑性应变,约为0%~2%,室温拉伸塑性更是几乎为零。虽然也有少量的块体非晶合金体系在压缩变形过程中显示出了极好的塑性变形能力,但其应力一应变曲线常显示出明显的加工软化特征,这一应变局域化过程严重地阻碍了非晶合金作为结构材料的实际应用。研究发现,块体非晶合金有限的宏观塑性变形性与高度局部化的变形过程相关,例如局部高度集中的剪切带的演变过程,其中大量塑性应变积聚在一个非常狭窄的区域,并表现出应变软化现象,虽然剪切带中的局部塑性应变非常高,但整体室温塑性却是非常差的。后来研究发现,解决应变局域化的有效途径之一就是在在块体非晶基体中引入具有不同长度尺度的第二相颗粒而制备出具有非均匀微观结构的非晶复合材料。非晶合金中引入第二相,可以影响剪切带的形成与扩展,并有效的缓解了应变集中,从而提高材料的整体宏观塑性。在一些非晶复合材料中,已发现第二晶体相能有效抑制变形时单个剪切带的快速失稳扩展,同时促进多重剪切带的生成,最终导致材料具有良好的压缩塑性。由此可见,通过引入第二相而制备非晶复合材料可以有效地改善块体非晶合金的易脆断性。铸造共晶铝硅合金拉伸试样端口存在明显的孔洞缺陷,此类缺陷是由于铝液在凝固过程中体积收缩而得不到铝液的补充或由于凝固过程气体的析出而形成的,而且在铸件中是难以避免的。这类缺陷的存在,一方面减少了受力的横截面积,另一方面在孔洞处容易造成应力集中,受力过程中导致裂纹产生和扩展。工业生产中,铸造合金在熔炉中反复熔炼,有可能保持较长时间,锶(sr)变质的长效性有重要的实际意义,可保证共晶硅在长时间熔炼中晶体变质效果稳定。试剂生产中常用al-sr作为长效变质剂,以克服na盐的有效变质时间短,使用工序复杂,效果不稳定的缺陷。中国专利cn201210142891.5涉及适用于航天产品的高性能铸造铝合金,以zl107铝合金材料为基础,通过进行铸造铝合金的化学成份优化,确定了一种化学成份配比合理并能满足技术指标的高性能铸造铝合金。其合金元素成份及配比(重量百分比)如下:si:5.5~7.5,mn:0.05~0.35,cu:3.5~4.5,cd:0.05~0.2,余量为al。本发明中允许杂质存在,当使用金属型铸造时,杂质总和≤0.4,其中,fe≤0.2;当使用砂型铸造时,杂质总和≤0.3,其中,fe≤0.2。本发明铸造铝合金通过以上合金元素成份配比熔炼而成,进行t5状态热处理后,在力学性能方面达到:抗拉强度σb≥300mpa,伸长率δ≥1.5%,硬度hb≥110。上述专利原料配比简单,未添加pd、ho等稀有元素以强化合金材料的综合性能,且铸造后的铝合金材料为晶型合金材料,不具备非晶型材料的优异的力学性能。且仅采用铸造工艺制备铝合金材料,无法克服偏析、夹渣、气孔、凹陷等铸造缺陷。技术实现要素:本发明所要解决的技术问题:针对目前铸造铝硅合金的缺点,本发明提供一种具有高综合性能的合金材料,在高强度和硬度的同时满足塑性良好,不易断裂的韧性需求。为解决上述技术问题,本发明提供以下的技术方案:一种具有高综合性能的合金材料,由如下重量百分含量的成分组成:9-12%si,0.4-0.7%fe,1-3%cu,0.004-0.006%au,0.6-0.8%mg,0.4-0.7%pd,0.5-0.8%ni,2-6%zn,1-4%sr,0.2-0.5%ho,余量为al;所述fe、cu、au、pd、ho、al均以纯物质作为制备原料,纯度均大于99.9%;sr以铝锶合金形式作为制备原料,其中sr的重量百分含量为10%,其余为铝;ni以铝镍合金合金形式作为制备原料,其中ni的重量百分含量为15%,其余为铝;si、mg、zn以铝镁锌合金形式作为制备原料,其中si的含量为24~30wt%;zn的含量为4~20wt%;mg的含量为1.6~2.0wt%,其余为铝。优选地,所述au、pd、ho、fe纯物质原料为粉末状,平均粒径100~200目;所述铝镁锌合金、铜原料为合金锭,所述铝镍合金、铝锶合金均为颗粒状,平均粒径1~3mm。一种上述具有高综合性能的合金材料的制备方法,包含如下具体步骤:(1)根据配料表称取fe、cu、au、pd、ho、al金属单质及铝锶合金、铝镍合金、铝镁锌合金作为原料,精确到0.0001g;(2)将铝镁锌合金和al、cu、fe、au单质用超声波清洗后烘干放入高真空电弧熔炼炉中的坩埚中,用机械泵抽至炉内气压为5pa后用分子泵抽空气至气压为0.0001pa,然后向熔炼炉内充入氩气作为保护气体至气压为0.05~0.5mpa,关闭阀门于1300~1800℃进行熔炼,反复熔炼5次,在第二次熔炼时加入铝镍合金和铝锶合金;(3)待合金成分熔炼均匀后打开阀门利用压力将合金浆料压入水冷铜模中,并吸铸成厚度为1.6~3.3mm的非晶板材,冷却速率为800~1000k/s;(4)将pd、ho粉末均匀平铺于非晶板材上表面,粉末层厚度0.05~0.2mm,采用功率为580±120w的中功率真空电子束焊机在真空度为1×10-5~10-7pa的区域熔炼室内进行电弧区域熔炼;中功率真空电子束焊机的钨极位于非晶板材上方,钨极与非晶板材上表面间的距离1~4mm;(5)采用400kgf空气锤对熔炼后的板材进行锻造,开坯温度850~1000℃,保温1~3h,随后三墩三拔,每次变形量55~85%,空冷至室温,再500~700℃精锻为直径90~120mm,长度200~300mm的棒材;(6)将棒材在箱式电阻炉中加热到变形温度,在液压机上按照最佳挤压比、应变速率进行挤压变形,一火成形,工件轮廓清晰,变形充分,然后空冷;(7)350~450℃固溶1.5~2h,升温至500~600℃,保温1~3h,水冷;(8)时效处理:将固溶后的合金升温至120~150℃预时效1~2h,水冷,升温至150~180℃,保温2~4h,空冷,再升温至85~115℃进行二级时效15~30h。优选地,所述步骤(4)中钨极直径为1~2mm,输入电流15~30a,输入电压70kv,熔炼区域直径2.0mm~4.6mm,熔炼水冷速率为800~900k/s。优选地,所述步骤(4)中钨极的移动方式为点扫描、线扫描或面扫描,扫描速度为2~5mm/s,直至熔炼区域覆盖全部非晶板材表面,所述钨极的电弧输入功率密度为5.2~7.6×107w/m2。优选地,所述最佳挤压比为合金挤压前后横截面积之比约为10~13:1;所述变形温度为500~550℃,所述应变速率为0.0015~0.0025s-1。本发明获得的有益效果:(1)本发明一种具有高综合性能的合金材料,具有良好的力学性能,同时具有良好的可塑性,综合性能优异,可广泛应用于机械零件制造领域等。(2)融入固溶体中的溶质原子造成晶格畸变,晶格畸变增大了位错运动的阻力,使滑移难以进行,从而使合金固溶体的强度与硬度增加。ni和al可以形成高熔点的化合物,弥散分布在基体中。强化相弥散强化的实质是利用弥散的超细微粒阻碍位错的运动,从而提高材料的力学性能。fe、au、cu及含硅铝镁锌合金熔炼后快速冷却形成非晶合金材料,并作为后续晶相沉积的中间材料,使本发明具备高强度、高硬度、大弹性极限的优点。通过sr实现细晶强化,即通过晶粒粒度的细化来提高金属的强度。(3)在非晶合金板材上添加pd、ho粉末进行区域熔炼,使得在非晶合金材料中产生pd-ho晶体沉积相,通过引入第二相提高合金材料的可塑性,解决晶体材料的易脆断性,为后续的锻造成型提供了塑性条件。通过控制区域熔炼技术参数,人为控制第二相的体积分数和空间分布状态,使得晶体相仅出现于非晶板材表面,并未贯穿板材,防止过度晶体化,降低合金材料的强度。(4)合金在后续锻造加工后能进一步改善其组织结构和力学性能。铸造组织经过锻造和热挤压变形后由于金属的变形和再结晶,使原来的粗大枝晶和柱状晶粒变为晶粒较细、大小均匀的等轴再结晶组织,使合金内原有的偏析、疏松、气孔、夹渣等压实和焊合,其组织变得更加紧密,提高了金属材料的塑性和力学性能。(5)恰当选择的固溶和时效温度与时间,可显著提高铝合金材料的硬度,避免时效和固溶温度过高及时效时间过长导致的合金韧性下降。附图说明图1对照实施例1中制备的非晶合金材料压缩断口sem图;图2实施例3中制备的合金材料压缩断口sem图。具体实施方式下面通过对实施例的描述,对本发明的具体实施方式作进一步详细的说明,以帮助本领域的技术人员对本发明的发明构思、技术方案有更完整、准确和深入的理解。实施例1:按如下方法制备高综合性能的合金材料:一、原料的准备:fe、cu、au、pd、ho、al均以纯物质作为制备原料,纯度均大于99.9%;sr以铝锶合金形式作为制备原料,其中sr的重量百分含量为10%,其余为铝;ni以铝镍合金合金形式作为制备原料,其中ni的重量百分含量为15%,其余为铝;si、mg、zn以铝镁锌合金形式作为制备原料,其中si的含量为30wt%;zn的含量为20wt%;mg的含量为2.0wt%,其余为铝。au、pd、ho、fe纯物质原料为粉末状,平均粒径100目;所述铝镁锌合金、铜原料为合金锭,所述铝镍合金、铝锶合金均为颗粒状,平均粒径1~3mm。二、高综合性能合金材料的制备:(1)按如下重量百分含量称取原料:0.4%fe,1%cu,0.004%au,30%铝镁锌合金,0.4%pd,3.33%铝镍合金,10%铝锶合金,0.2%ho,余量为al;精确到0.0001g;(2)将铝镁锌合金和al、cu、fe、au单质用超声波清洗后烘干放入高真空电弧熔炼炉中的坩埚中,用机械泵抽至炉内气压为5pa后用分子泵抽空气至气压为0.0001pa,然后向熔炼炉内充入氩气作为保护气体至气压为0.05mpa,关闭阀门于1300℃进行熔炼,反复熔炼5次,在第二次熔炼时加入铝镍合金和铝锶合金;(3)待合金成分熔炼均匀后打开阀门利用压力将合金浆料压入水冷铜模中,并吸铸成厚度为1.6mm的非晶板材,冷却速率为800k/s;(4)将pd、ho粉末均匀平铺于非晶板材上表面,粉末层厚度0.05mm,采用功率为460w的中功率真空电子束焊机在真空度为1×10-5pa的区域熔炼室内进行电弧区域熔炼;中功率真空电子束焊机的钨极位于非晶板材上方,钨极与非晶板材上表面间的距离1mm;钨极直径为1mm,输入电流15a,输入电压70kv,单个熔炼区域为圆形,直径2.0mm,熔炼水冷速率为800k/s。钨极的移动方式为点扫描,扫描速度为2mm/s,直至熔炼区域覆盖全部非晶板材表面,钨极的电弧输入功率密度为5.2×107w/m2。(5)采用400kgf空气锤对熔炼后的板材进行锻造,开坯温度850℃,保温1h,随后三墩三拔,每次变形量55%,空冷至室温,再500℃精锻为直径90mm,长度200mm的棒材;(6)将棒材在箱式电阻炉中加热后挤压变形,最佳挤压比(合金挤压前后横截面积之比)为约为10:1;变形温度为500℃,应变速率为0.0015s-1。一火成形,工件轮廓清晰,变形充分,然后空冷;(7)350℃固溶1.5h,升温至500℃,保温1h,水冷;(8)时效处理:将固溶后的合金升温至120℃预时效1h,水冷,升温至150℃,保温2h,空冷,再升温至85℃进行二级时效15h。实施例2:按如下方法制备高综合性能的合金材料:一、原料的准备:fe、cu、au、pd、ho、al均以纯物质作为制备原料,纯度均大于99.9%;sr以铝锶合金形式作为制备原料,其中sr的重量百分含量为10%,其余为铝;ni以铝镍合金合金形式作为制备原料,其中ni的重量百分含量为15%,其余为铝;si、mg、zn以铝镁锌合金形式作为制备原料,其中si的含量为24wt%;zn的含量为4wt%;mg的含量为1.6wt%,其余为铝。au、pd、ho、fe纯物质原料为粉末状,平均粒径200目;所述铝镁锌合金、铜原料为合金锭,所述铝镍合金、铝锶合金均为颗粒状,平均粒径3mm。二、高综合性能合金材料的制备:(1)按如下重量百分含量称取原料:0.7%fe,3%cu,0.006%au,50%铝镁锌合金,0.7%pd,5.33%铝镍合金,40%铝锶合金,0.5%ho,余量为al;精确到0.0001g;(2)将铝镁锌合金和al、cu、fe、au单质用超声波清洗后烘干放入高真空电弧熔炼炉中的坩埚中,用机械泵抽至炉内气压为5pa后用分子泵抽空气至气压为0.0001pa,然后向熔炼炉内充入氩气作为保护气体至气压为0.5mpa,关闭阀门于1800℃进行熔炼,反复熔炼5次,在第二次熔炼时加入铝镍合金和铝锶合金;(3)待合金成分熔炼均匀后打开阀门利用压力将合金浆料压入水冷铜模中,并吸铸成厚度为3.3mm的非晶板材,冷却速率为1000k/s;(4)将pd、ho粉末均匀平铺于非晶板材上表面,粉末层厚度0.2mm,采用功率为700w的中功率真空电子束焊机在真空度为1×10-7pa的区域熔炼室内进行电弧区域熔炼;中功率真空电子束焊机的钨极位于非晶板材上方,钨极与非晶板材上表面间的距离4mm;钨极直径为2mm,输入电流30a,输入电压70kv,单个熔炼区域为圆形,直径4.6mm,熔炼水冷速率为900k/s。钨极的移动方式为线扫描,扫描速度为5mm/s,直至熔炼区域覆盖全部非晶板材表面,所述钨极的电弧输入功率密度为7.6×107w/m2。(5)采用400kgf空气锤对熔炼后的板材进行锻造,开坯温度1000℃,保温3h,随后三墩三拔,每次变形量85%,空冷至室温,再700℃精锻为直径120mm,长度300mm的棒材;(6)将棒材在箱式电阻炉中加热后挤压变形,最佳挤压比(合金挤压前后横截面积之比)为约为13:1;变形温度为550℃,应变速率为0.0025s-1。一火成形,工件轮廓清晰,变形充分,然后空冷;(7)450℃固溶2h,升温至600℃,保温3h,水冷;(8)时效处理:将固溶后的合金升温至150℃预时效2h,水冷,升温至180℃,保温4h,空冷,再升温至115℃进行二级时效30h。实施例3:按如下方法制备高综合性能的合金材料:一、原料的准备:fe、cu、au、pd、ho、al均以纯物质作为制备原料,纯度均大于99.9%;sr以铝锶合金形式作为制备原料,其中sr的重量百分含量为10%,其余为铝;ni以铝镍合金合金形式作为制备原料,其中ni的重量百分含量为15%,其余为铝;si、mg、zn以铝镁锌合金形式作为制备原料,其中si的含量为27wt%;zn的含量为12wt%;mg的含量为1.8wt%,其余为铝。au、pd、ho、fe纯物质原料为粉末状,平均粒径150目;所述铝镁锌合金、铜原料为合金锭,所述铝镍合金、铝锶合金均为颗粒状,平均粒径2mm。二、高综合性能合金材料的制备:(1)按如下重量百分含量称取原料:0.55%fe,2%cu,0.005%au,40%铝镁锌合金,0.56%pd,0.65%铝镍合金,2.5%铝锶合金,0.33%ho,余量为al;精确到0.0001g;(2)将铝镁锌合金和al、cu、fe、au单质用超声波清洗后烘干放入高真空电弧熔炼炉中的坩埚中,用机械泵抽至炉内气压为5pa后用分子泵抽空气至气压为0.0001pa,然后向熔炼炉内充入氩气作为保护气体至气压为0.25mpa,关闭阀门于1500℃进行熔炼,反复熔炼5次,在第二次熔炼时加入铝镍合金和铝锶合金;(3)待合金成分熔炼均匀后打开阀门利用压力将合金浆料压入水冷铜模中,并吸铸成厚度为2.4mm的非晶板材,冷却速率为900k/s;(4)将pd、ho粉末均匀平铺于非晶板材上表面,粉末层厚度0.11mm,采用功率为580w的中功率真空电子束焊机在真空度为1×10-6pa的区域熔炼室内进行电弧区域熔炼;中功率真空电子束焊机的钨极位于非晶板材上方,钨极与非晶板材上表面间的距离2.5mm;钨极直径为1.5mm,输入电流22a,输入电压70kv,熔炼区域直径3.3mm,熔炼水冷速率为850k/s。钨极的移动方式为多个钨极平行面扫描,扫描速度为3mm/s,直至熔炼区域覆盖全部非晶板材表面,所述钨极的电弧输入功率密度为6.4×107w/m2。(5)采用200kgf空气锤对熔炼后的板材进行锻造,开坯温度900℃,保温2h,随后三墩三拔,每次变形量65%,空冷至室温,再550℃精锻为直径100mm,长度250mm的棒材;(6)将棒材在箱式电阻炉中加热后挤压变形,最佳挤压比(合金挤压前后横截面积之比)为约为11:1;变形温度为530℃,应变速率为0.002s-1。一火成形,工件轮廓清晰,变形充分,然后空冷;(7)400℃固溶1.7h,升温至550℃,保温2h,水冷;(8)时效处理:将固溶后的合金升温至120~150℃预时效1.5h,水冷,升温至165℃,保温3h,空冷,再升温至100℃进行二级时效23h。对照实施例1:按如下方法制备合金材料:本实施例其余均与实施例3相同,区别仅在无步骤(4)的区域熔炼步骤。pd和ho粉末的添加改为在步骤(2)第二次熔炼时与铝镍合金和铝锶合金一同加入,且无锻造和热挤压步骤。对照实施例2:按如下方法制备合金材料:本实施例其余均与实施例3相同,区别仅在固溶和时效工艺为:400℃固溶1h,空冷后100℃时效30h。对照实施例3:根据中国专利cn201210142891.5中实施例1公开的方法,制备高性能铸造铝合金,作为对照用于后续的性能测试。为了检测实施例1~3及对照实施例1~3制备的合金材料的各项性能进行如下试验:1、力学性能测试将得到的试样按gb6397-86,机加工成标准的8mm短拉伸试棒,在微电子控制万能试验机上进行拉伸试验,测其抗拉强度、硬度和伸长率,最终结果取4个试样的平均值。结果见表1。表1高强高韧材料的力学性能测试结果上述结果表明本发明制备的合金材料在力学性能上显著优于传统铸造共晶铝硅合金(对照实施例3)。由对照实施例1和实施例3的力学性能参数对比后可知,在非晶铸态合金铸造后引入第二相,且经过锻造和热挤压工艺后显著提升了合金的伸长率和抗拉强度,且相比实施例1~3在综合性能上更优。由对照实施例2和实施例3的力学性能对比后可知,固溶和时效等热处理工艺可以在保留塑性的同时显著提升合金的抗拉强度和硬度,使得综合性更优。2、区域熔炼中第二相的分布状态将实施例1~3中区域熔炼后的非晶板材剪切后抛光,用om观察并测量切口上第二相的出现深度,结果如下:表2pd-ho第二相在非晶板材中的出现深度组别第二相深度(μm)实施例1298实施例2853实施例3657表2结果表明通过控制区域熔炼技术参数,人为控制第二相的体积分数和空间分布状态,第二相的出现深度小于板材厚度,且仅出现于钨极扫描熔炼的一侧,使得第二相晶体相仅出现于非晶板材表面,并未贯穿板材。3、金相分析采用实施例3和对照实施例1作为金相试样,采用sem对样品进行微观形貌观察,样品需要进行镶嵌并且抛光处理,样品需表面粗抛光并进行超声清洗,采用纳米压痕仪和万能试验机测试样品的力学性能,压缩试样压缩样品需要利用慢走丝线切割机切成尺寸为1.5*1.1*3的小长方体,并且周边进行抛光处理以便后期的断口sem形貌观测。压缩实验后样品的断口形貌能够反映出压缩断裂过程中的某些特征,而这些特征依附于样品的塑性、强度、压缩速率以及断口模型等。通常来说,断口形貌为脉络状图样一般与断裂前样品出现软化以及样品粘度的降低有关。非晶基体区域的断口形貌一般为脉络状,也会有部分成支流状的形貌出现在脉络状的形貌区域中。图1可见,对照实施例1中制备的非晶合金,其压缩断口的边缘出现脉络状逐渐转变为支流状的形貌;图2可见实施例3制备的合金材料其断口形貌为以支流状为主,并掺杂着少量成泥沙状形貌,暗示出样品的微观组织结构在剪切带扩展过程中能够影响样品的软化。这表明第二相的出现影响了样品的微观组织形貌,从而在样品断口形貌中得到体现。综上所述,本发明一种具有高综合性能的合金材料,具有良好的力学性能,同时具有良好的可塑性,综合性能优异,可广泛应用于机械零件制造领域等。融入固溶体中的溶质原子造成晶格畸变,晶格畸变增大了位错运动的阻力,使滑移难以进行,从而使合金固溶体的强度与硬度增加。ni和al可以形成高熔点的化合物,弥散分布在基体中。强化相弥散强化的实质是利用弥散的超细微粒阻碍位错的运动,从而提高材料的力学性能。fe、au、cu及含硅铝镁锌合金熔炼后快速冷却形成非晶合金材料,并作为后续晶相沉积的中间材料,使本发明具备高强度、高硬度、大弹性极限的优点。通过sr实现细晶强化,即通过晶粒粒度的细化来提高金属的强度。在非晶合金板材上添加pd、ho粉末进行区域熔炼,使得在非晶合金材料中产生pd-ho晶体沉积相,通过引入第二相提高合金材料的可塑性,解决晶体材料的易脆断性,为后续的锻造成型提供了塑性条件。通过控制区域熔炼技术参数,人为控制第二相的体积分数和空间分布状态,使得晶体相仅出现于非晶板材表面,并未贯穿板材,防止过度晶体化,降低合金材料的强度。合金在后续锻造加工后能进一步改善其组织结构和力学性能。铸造组织经过锻造和热挤压变形后由于金属的变形和再结晶,使原来的粗大枝晶和柱状晶粒变为晶粒较细、大小均匀的等轴再结晶组织,使合金内原有的偏析、疏松、气孔、夹渣等压实和焊合,其组织变得更加紧密,提高了金属材料的塑性和力学性能。恰当选择的固溶和时效温度与时间,可显著提高铝合金材料的硬度,避免时效和固溶温度过高及时效时间过长导致的合金韧性下降。以上实施例仅为说明本发明的技术思想,不能以此限定本发明的保护范围,凡是按照本发明提出的技术思想,在技术方案基础上所做的任何改动,均落入本发明保护范围之内;本发明未涉及的技术均可通过现有技术加以实现。当前第1页12