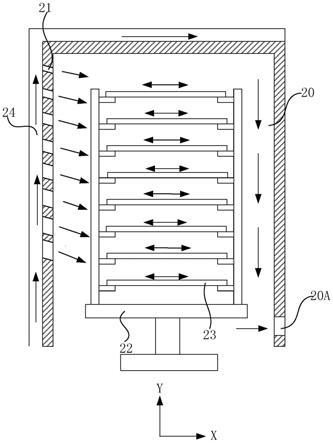
1.本发明涉及半导体制造领域,尤其涉及一种扩散炉。
背景技术:2.扩散炉是半导体生产线前工序的重要工艺设备之一,用于大规模集成电路、分立器件、电力电子、光电器件和光导纤维等行业的扩散、氧化、退火、合金及烧结等工艺。
3.图1是现有的扩散炉的示意图,请参阅图1,所述扩散炉具有一反应腔10,晶圆11放置在晶舟12上,置于所述反应腔10内。在进行工艺沉积时,反应气体自所述反应腔10顶部喷淋,并扩散到晶圆11表面(反应气体的扩散路线请参阅图1中箭头所示),进行沉积。现有的扩散炉的缺点在于,反应气体自所述反应腔10顶部喷淋,则在进行工艺沉积过程中,由于反应气体相对于晶圆是垂直喷射的,则顶部晶圆接触的反应气体较多,底部晶圆由于被阻挡,其接触的反应气体较少,使得同一批次晶圆膜厚不同,产品均匀性下降;而对底部被遮挡晶圆而言,反应气体自晶圆11的边缘向晶圆的中心扩散,使得晶圆11表面边缘的膜厚大于中心的膜厚,造成晶圆11表面膜厚不均匀,产品良率下降。
4.因此,如何提高晶圆表面沉积膜层的均匀性,成为目前亟需解决的技术问题。
技术实现要素:5.本发明所要解决的技术问题是,提供一种扩散炉,其能够提高晶圆表面沉积膜层的均匀性及稳定性。
6.为了解决上述问题,本发明提供了一种扩散炉,其包括:反应腔室,沿第一方向延伸,所述反应腔室具有排气端,多个晶圆能够沿第一方向依次设置,所述晶圆表面沿第二方向延伸,所述第二方向与所述第一方向垂直或呈一锐角;多个气体管道,贯通所述反应腔室的侧壁,以将外部反应气体引入所述反应腔室,所述气体通道自所述排气端沿所述第一方向分布,所述气体通道的轴心与所述第二方向具有一锐角夹角。
7.进一步,所述锐角夹角的范围为3~20度。
8.进一步,沿所述第一方向,自所述排气端起,所述气体通道的孔径逐渐减小。
9.进一步,每一所述气体管道由至少一子通道组成,所述子通道贯通所述反应腔室的侧壁,所述子通道在所述反应腔室的侧壁上沿所述第二方向依次排列。
10.进一步,同一所述气体管道中的子通道的孔径相同。
11.进一步,同一所述气体管道中的子通道的孔径按照与所述排气端的距离由远至近逐渐增大。
12.进一步,在所述第一方向上,所述气体通道被划分为多个通道组,同一所述通道组的气体通道的孔径相同。
13.进一步,所述气体通道的孔径以预设数值逐渐减小。
14.进一步,所述气体通道的出气口在第二方向上的投影位于相邻的两个晶圆之间。
15.进一步,所述气体通道突出于所述反应腔室的侧壁。
16.进一步,所述气体通道突出于所述反应腔室的侧壁部分的长度为1~5mm。
17.进一步,所述扩散炉还包括晶舟,用于在反应腔室内承载晶圆,所述晶舟能够旋转,以带动所述晶圆旋转。
18.进一步,所述扩散炉还包括进气管,所述进气管与所述气体通道连通,用于向所述气体通道输送反应气体。
19.进一步,所述进气管的进气端与所述反应腔室的所述排气端位于同一侧。
20.本发明的优点在于,在所述反应腔室的侧壁设置气体通道,相对于现有的在顶部设置气体通道而言,能够避免晶圆之间的相互遮挡而造成的晶圆之间反应气体浓度的差异,从而避免同一批次晶圆沉积膜层的厚度不均匀的情况发生,且能够改善单一晶圆表面沉积膜层厚度不均匀的问题;并通过气体通道的倾斜设计使得自所述气体通道喷出的反应气体能够直达晶圆的中心,从而解决了沉积过程中两边厚中间薄的问题,而由于排气端排气的作用,反应气体到达晶圆中间会向两边扩散,同时晶舟旋转加速气体的扩散,使得单片晶圆表面中心与边缘沉积的膜层的厚度更加均匀,提高产品良率。
附图说明
21.图1是现有的扩散炉的示意图;
22.图2是本发明第一实施例的扩散炉的结构示意图;
23.图3是本发明第一实施例的扩散炉的气体通道贯穿反应腔室侧壁的示意图;
24.图4是本发明第一实施例的扩散炉的气体通道在反应腔室侧壁的分布示意图;
25.图5是本发明第二实施例的扩散炉的气体通道在反应腔室侧壁的分布示意图;
26.图6是本发明第三实施例的扩散炉的气体通道在反应腔室侧壁的分布示意图;
27.图7是本发明第四实施例的扩散炉的气体通道在反应腔室侧壁的分布示意图;
28.图8是本发明第五实施例的扩散炉的气体通道贯穿反应腔室侧壁的示意图。
具体实施方式
29.下面结合附图对本发明提供的扩散炉的具体实施方式做详细说明。
30.图2是本发明第一实施例的扩散炉的结构示意图。请参阅图2,所述扩散炉包括反应腔室20及多个气体管道21。
31.所述反应腔室20作为进行反应的腔室,晶圆可置于所述反应腔室20内进行沉积膜层等工艺。进一步,所述扩散炉还包括晶舟22,所述晶舟22能够深入所述反应腔室20内,并承载晶圆23,以将所述晶圆23置于所述反应腔室20内。其中,所述晶舟22能够旋转,以带动所述晶圆23在反应腔室20内旋转,实现反应气体的均匀沉积。
32.所述反应腔室20沿第一方向延伸。如图2所示,所述反应腔室20沿y方向延伸。当进行工艺制程时,在所述反应腔室20内,多个所述晶圆23沿第一方向依次设置,所述晶圆23表面沿第二方向延伸。所述第二方向与所述第一方向垂直或呈一锐角。其中,在第一实施例中,所述第一方向为y方向,所述第二方向为x方向,所述第一方向与所述第二方向垂直,而在本发明其他实施例中,所述第二方向与所述第一方向呈一锐角。
33.所述反应腔室20具有排气端20a,所述排气端20a用于排出所述反应腔室20内的废气。在本实施例中,所述排气端20a设置所述反应腔室20的底部,而在本发明其他实施例中,
所述排气端20a也可设置在所述反应腔室20的顶部或者中部。
34.所述气体管道21贯通所述反应腔室20的侧壁,以将外部反应气体引入所述反应腔室20。所述气体管道21自所述反应腔室20外部贯穿所述反应腔室20的侧壁,以在所述反应腔室20与外部连通,进而使反应气体能够通入所述反应腔室20。
35.进一步,所述扩散炉还包括进气管24,所述进气管24与所述气体通道21连通,反应气源通过所述进气管24向所述气体通道21输送反应气体。在本实施例中,所述进气管24为一根总管,所有的所述气体通道21均与该进气管24连通。在本发明其他实施例中,所述进气管包括多根管路,每一管路可与一个或多个气体通道21连通,以分别向所述气体通道21输送反应气体,实现气体通道21的分批控制。
36.进一步,在本实施例中,所述进气管24的进气端与所述反应腔室20的所述排气端20a位于同一侧,例如,两者均位于所述反应腔室20的底部,而在本发明其他实施例中,所述进气管24的进气端与所述反应腔室20的所述排气端20a位于不同侧,例如,所述进气管24的进气端位于所述反应腔室20的顶端,所述排气端20a位于所述反应腔室20的底端,或者所述进气管24的进气端位于所述反应腔室20的底端,所述排气端20a位于所述反应腔室20的顶端,本发明对此不进行限定。
37.所述气体通道21自所述排气端20a沿所述第一方向分布,且所述气体通道21的轴心与所述第二方向具有一锐角夹角。具体地说,请参阅图3,其为本发明第一实施例的气体通道贯穿反应腔室侧壁的示意图,所述气体通道的轴心o与所述第二方向(x方向)并不平行,而是具有一锐角夹角
ɑ
,这使得所述自所述气体通道喷出的反应气体能够直达晶圆23的中心,从而解决了沉积过程中两边厚中间薄的问题,而由于排气端20a排气的作用,反应气体到达晶圆中间会向两边扩散,同时晶舟旋转加速气体的扩散,使得单片晶圆23表面中心与边缘沉积的膜层的厚度更加均匀。
38.进一步,所述锐角夹角
ɑ
的范围为3~20度,若该角度太小,会使得反应气体平行于晶圆喷出,若该角度太大,反应气体会喷洒在晶圆的边缘,而无法达到晶圆表面中心。优选地,所述锐角夹角
ɑ
为15度。
39.进一步,所述气体通道21的出气口在第二方向(x方向)上的投影位于相邻的两个晶圆23之间,以避免晶圆侧面阻挡反应气体的传输。
40.进一步,沿所述第一方向,自所述排气端30a起,所述气体通道21的孔径逐渐减小。具体地说,如图2及图3所示,所述气体通道21自所述排气端20a沿y方向分布,且所述气体通道21的孔径逐渐减小。也就是说,越靠近所述排气端20a,所述气体通道21的孔径越大。
41.由于反应腔室20内的废气自所述排气端20a排出,则在废气排出时,部分反应气体也会被带走,使得越靠近排气端20a的区域反应气体浓度越小,造成同一批次晶圆均匀性差。因此,本发明扩散炉通过气体通道21的孔径大小的设计对反应气体浓度小的区域进行补偿,使得越靠近所述排气端20a的区域反应气体流量大,以增大该区域的反应气体浓度,进而提高同一批次晶圆的均匀性,提高产品良率。
42.另外,本发明扩散炉在所述反应腔室的侧壁设置气体通道,相对于现有的在顶部设置气体通道而言,能够避免晶圆之间的相互遮挡而造成的晶圆之间反应气体浓度的差异,从而避免同一批次晶圆沉积膜层的厚度不均匀的情况发生。
43.进一步,图4是本发明第一实施例的气体通道在反应腔室侧壁的分布示意图。请参
阅图4,本实施例中,多个所述气体管道21自排气端20a沿第一方向(y方向)依次分布,且所述气体管道21的孔径以一预设数值逐渐减小。所述预设数值可根据实际工艺中反应腔室20的排气端20a与其他区域的反应气体的浓度差异而定。所述预设数值可为一恒定值,所述预设数值也可为一可变数值,例如,所述预设数值以递减的方式逐渐减小。
44.在本发明第一实施例中,所述气体通道21的孔径逐渐减小,而在本发明其他实施例中,在所述第一方向上,所述气体通道被划分为多个通道组,同一所述通道组的气体通道的孔径相同。具体地说,请参阅图5,其为本发明第二实施例的气体通道在反应腔室侧壁的分布示意图,其与第一实施例的区别在于,在所述第一方向(y方向)上,所述气体通道21被划分为多个通道组,在图5中示意性绘示了通道组a、b、c。同一所述通道组的气体通道21的孔径相同,不同通道组的气体通道21的孔径不同,且越靠近所述排气端20a,所述通道组的气体通道的孔径越大。
45.在所述气体通道21的数量很多的情况下,相邻的几个气体通道21所对应的反应腔室20区域的反应气体浓度受到排气端20a排气的影响程度可能相同,因此,为了避免由于气体通道21输入的气体流量不同而造成的反应气体浓度不同,可将该几个气体通道21划分为同一个通道组,该几个气体通道21的孔径相同,以使得反应腔室20内的气体浓度均一。
46.进一步,本发明还提供一第三实施例,在第三实施例中,每一所述气体管道由至少一子通道组成,所述子通道贯通所述反应腔室的侧壁,所述子通道在所述反应腔室的侧壁上沿第二方向依次排列,所述第二方向与所述第一方向垂直或呈一锐角。
47.具体地说,请参阅图6,其为本发明第三实施例的气体通道在反应腔室侧壁的分布示意图,为了增加气体管道21的作用区域,每一所述气体管道21由多个子通道21a组成,在本实施例中,每一所述气体管道21由三个子通道21a组成,在本发明其他实施例中,所述子通道的数量可根据实际需求选择,例如,所述子通道的数量可根据反应气体的作用区域的宽度选择,若要求所述反应气体的作用区域宽,则可增加所述子通道的数量,若要求所述反应气体的作用区域窄,则可减少所述子通道的数量。
48.所述子通道21a贯通所述反应腔室20的侧壁,所述子通道21a彼此之间不连通。所述子通道21a在所述反应腔室20的侧壁上沿第二方向依次排列。如图5所示,所述第二方向为x方向。所述第二方向与所述第一方向垂直或呈一锐角。在本实施例中,所述第一方向为y方向,所述第二方向为x方向,两者相互垂直,在本发明其他实施例中,所述第一方向为y方向,所述第二方向与所述第一方向呈一锐角。
49.进一步,在本发明其他实施例中,也可参考第二实施例,将所述气体通道21分为多个通道组,同一通道组内的子通道21a的孔径均相同。
50.在第三实施例中,同一所述气体管道21中的子通道21a的孔径相同。而在本发明其他实施例中,同一所述气体管道中的子通道的孔径按照与所述排气端的距离由远至近逐渐增大。具体地说,请参阅图7,其为本发明第四实施例的气体通道在反应腔室侧壁的分布示意图,在本实施例中,所述排气端20a位于所述反应腔室20底部一侧,所述子通道21a所在的区域距离所述排气端20a的距离不同,这也导致排气端20a排气对该些区域的影响不同,因此,同一所述气体管道21中的子通道21a的孔径按照与所述排气端20a的距离由远至近逐渐增大,即距离所述排气端20a越近,所述子通道21a的孔径越大,以平衡排气端20a排气对反应气体浓度的影响。
51.在上述各个实施例中,所述气体通道21仅贯穿所述反应腔室20的侧壁。而在本发明其他实施例中,所述气体通道突出于所述反应腔室的侧壁。具体地说,请参阅图8,其为本发明第五实施例的气体通道贯穿反应腔室侧壁的示意图,在本实施例中,所述气体通道21突出于所述反应腔室20的侧壁,即所述气体通道21延伸至所述反应腔室20内,以使得反应气体能够喷洒至晶圆表面的中心区域,进一步提高单一晶圆表面沉积膜层厚度的均匀性。
52.进一步,所述气体通道突出于所述反应腔室的侧壁部分的长度为1~5mm,若所述气体通道突出于所述反应腔室的侧壁部分的长度太长,可能会影响晶圆在反应腔室内的移动。
53.本发明扩散炉能够改善单一晶圆表面沉积膜层厚度不均匀的问题,也能够改善排气端排气对反应腔室内反应气体浓度的影响,大大提高了同一批次晶圆的稳定性,提高了产品良率。
54.以上所述仅是本发明的优选实施方式,应当指出,对于本技术领域的普通技术人员,在不脱离本发明原理的前提下,还可以做出若干改进和润饰,这些改进和润饰也应视为本发明的保护范围。