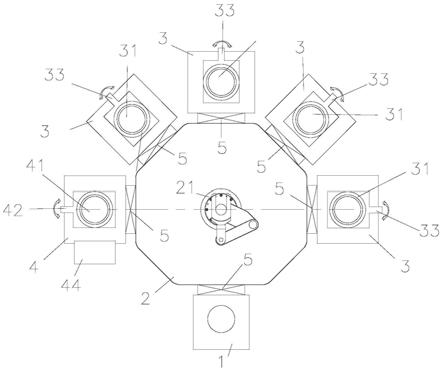
1.本发明涉及一种离子束镀膜设备及及其镀膜方法。
背景技术:2.离子束溅射镀膜技术是各类镀膜技术中最重要技术之一,广泛应用于光学元件、航空发动机、微电子器件和材料表面处理领域中。
3.基片金属化及钝化/绝缘层工艺,要求薄膜与基片粘附性好,以及基片沉积过程中保持低温且沉膜均匀区大,因而在镀膜之前需要先去除基片表面的杂质材料,然而,现有镀膜设备中清洗和镀膜是在两个不同设备中完成的,存在以下缺陷:(1)仅能实现对单个基片的镀膜,不能同时对多个基片进行镀膜,也不能实现对不同类型薄膜的同时制备,无法批量生产;(2)不具备独立装卸片室功能,且每次清洗、镀膜完成需要打开工艺腔室,建立真空时间长,有效工作时间短,镀膜效率低;(3)现有离子束镀膜设备大都是为小尺寸衬底、手动型科研型设备,不具备清洗角度和镀膜角度的自动调节功能,也不具备镀膜膜层的在线监控功能;(4)无温控装置和降温装置,无法确保在较低温度条件下对红外器件进行清洗和镀膜,容易造成红外器件损失,这是因为红外器件基片材料碲镉汞具有特殊性,受等离子体轰击升温到一定温度后汞原子很容易逸出,从而会导致芯片损伤。另外,现有离子束镀膜设备通常采用多面靶台进行多层薄膜制备,存在交叉污染现象,同时工件台不具备角度调节功能,难以满足不同晶向材料对基片沉积角度的需求。上述缺陷的存在,使得现有离子束镀膜设备难以满足基片(如红外器件)对大尺寸、高均匀性、低损伤、低温镀膜工艺的要求。
技术实现要素:4.本发明要解决的技术问题是克服现有技术的不足,提供一种结构简单、膜层纯度高、薄膜与基片附着力好的离子束镀膜设备及及其镀膜方法。
5.为解决上述技术问题,本发明采用以下技术方案:
6.一种离子束镀膜设备,包括装卸片腔室、用传送基片的传送腔室、至少一个用于基片镀膜的镀膜腔室和清洗腔室;所述装卸片腔室、镀膜腔室和清洗腔室分别连接在传送腔室上;所述装卸片腔室与传送腔室之间设有隔离阀;所述传送腔室与镀膜腔室之间设有隔离阀;所述传送腔室与清洗腔室之间设有隔离阀;所述传送腔室内设有用于传送基片的转运机构。
7.作为上述技术方案的进一步改进:
8.所述传送腔室为球体,所述装卸片腔室、镀膜腔室和清洗腔室分布在传送腔室的周围;或,所述传送腔室为多面体,所述装卸片腔室、镀膜腔室和清洗腔室分布在传送腔室的各个面上。
9.所述转运机构为真空机械手;所述装卸片腔室的数量为1个~2个;所述镀膜腔室的数量为1个~5个;所述清洗腔室的数量为1个~2个。
10.每个所述镀膜腔室内设有用于放置基片的第一可旋转基片工件台、用于调节第一
可旋转基片工件台摆动角度的第一调控装置、用于放置靶材的可摆动靶材工件台和溅射离子源;所述第一可旋转基片工件台上连接有用于调节基片温度的第一控温装置和用于监控基片镀膜程度的第一监控装置;所述第一控温装置包括冷却管和在冷却管内循环的冷却液,所述冷却管设置在第一可旋转基片工件台的内部或表面;所述冷却液为硅油;所述硅油的温度为
‑
40℃~150℃;所述第一可旋转基片工件台的前侧依次设有第一可旋转基片挡板机构和可移动束流修正板;所述可摆动靶材工件台的前侧设有可旋转靶材挡板机构;
11.每个所述清洗腔室内设有用于放置基片的第二可旋转基片工件台、用于调节第二可旋转基片工件台摆动角度的第二调控装置和清洗离子源;所述第二可旋转基片工件台上连接有用于调节基片温度的第二控温装置和用于监控基片清洗程度的第二监控装置;所述第二控温装置包括冷却管和在冷却管内循环的冷却液,所述冷却管设置在第二可旋转基片工件台的内部或表面;所述冷却液为硅油;所述硅油的温度为
‑
40℃~150℃;所述第二可旋转基片工件台的前侧设有第二可旋转基片挡板机构。
12.每个所述镀膜腔室上设有维护门,所述溅射离子源安装在维护门上;所述溅射离子源位于镀膜腔室内的一侧设有聚焦型或平行型的栅网;所述栅网上连接有用于发射电子、中和带正电离子束的中和器;
13.每个所述清洗腔室上设有维护门,所述清洗离子源安装在维护门上;所述清洗离子源位于清洗腔室内的一侧设有发散型或平行型的栅网;所述栅网上连接有用于发射电子、中和带正电离子束的中和器。
14.所述装卸片腔室中设有用于升降基片的升降机构;所述升降机构上设有至少两个用于放置基片的托盘;每个所述托盘上设有若干个用于固定基片的紧固孔;所述托盘的形状为椭圆形、圆形、三角形或多边方形。
15.还包括抽真空装置和电控装置;所述抽真空装置和电控装置分别连接在装卸片腔室、传送腔室、镀膜腔室和清洗腔室上。
16.作为一个总的技术构思,本发明还提供了一种镀膜方法,所述镀膜方法是上述的离子束镀膜设备对基片进行镀膜。
17.作为上述技术方案的进一步改进:
18.包括以下步骤:
19.s1、对基片进行预处理;
20.s2、将步骤s1中预处理后的基片置于装卸片腔室中,经传送腔室转运至清洗腔室中进行清洗处理;
21.s3、将步骤s2中清洗处理后的基片从清洗腔室中取出,经传送腔室转运至镀膜腔室中进行镀膜处理。
22.步骤s1中,所述清洗处理过程中,控制离子源能量为100ev~500ev,离子束束流为50ma~200ma,中和束束流为离子束束流的1~2倍;所述清洗过程中,基片的圆周旋转转速为5rpm~60rpm,左右摆动角度为
‑
35
°
~35
°
,温度为
‑
20℃~80℃;
23.步骤s2中,对基片进行镀膜处理之前还包括对靶材进行清洗处理;所述靶材的清洗处理过程中,控制离子源能量为300ev~1200ev,离子束束流为50ma~500ma,中和束束流为离子束束流的1~2倍;所述靶材的清洗处理过程中,靶材的左右摆动角度为
‑
35
°
~35
°
,温度为
‑
20℃~80℃;所述镀膜处理过程中,控制离子源能量为300ev~1200ev,离子束束流
为50ma~500ma,中和束束流为离子束束流的1~2倍;所述镀膜处理过程中,基片的圆周旋转转速为5rpm~60rpm,左右摆动角度为
‑
35
°
~35
°
,温度为
‑
20℃~80℃;所述镀膜过程中,在基片与第一可旋转基片工件台31之间涂覆硅脂或石墨层。
24.与现有技术相比,本发明的优点在于:
25.(1)本发明提供了一种离子束镀膜设备,包括装卸片腔室、用传送基片的传送腔室、至少一个用于基片镀膜的镀膜腔室和清洗腔室;装卸片腔室、镀膜腔室和清洗腔室分别连接在传送腔室上;装卸片腔室与传送腔室之间设有隔离阀;传送腔室与镀膜腔室之间设有隔离阀;传送腔室与清洗腔室之间设有隔离阀;传送腔室内设有用于传送基片的转运机构。本发明中,设置的装卸片腔室,用于存放不同类型的基片,一次装卸即可放入多种不同类型的基片,设置的传送腔室,实现基片在装卸片腔室、镀膜腔室和清洗腔室之间的转运,设置至少一个的镀膜腔室,可实现对多个基片进行同时镀膜,也可实现多种类型膜层的制备,设置的清洗腔室,可用于对基片进行清洗,去除基片表面的脏污及氧化物,极大的提高薄膜与基片之间的附着力。本发明中,通过传送腔室中设置的转运机构,将基片从装卸片腔室中转运至清洗腔室中进行清洗,进而将基片从清洗腔室中转运至镀膜腔室中进行镀膜,最后将镀膜后的基片从镀膜腔室中转运至装卸片腔室中,同时,在使用过程中,通过隔离阀实现装卸片腔室、传送腔室、镀膜腔室和清洗腔室的通断,隔离阀关闭时,装卸片腔室、传送腔室、镀膜腔室和清洗腔室均不会暴露在大气中,不仅能够保证在相同的真空条件下实现基片装卸,降低基片带入镀膜腔室中的水气量,而且不会破坏镀膜腔室和清洗腔室的真空度,可实现基片的连续清洗和连续镀膜,大大降低因腔体与基片污染造成的薄膜质量差等问题,可实现连续生产,提高生产效率,降低生产成本。本发明离子束镀膜设备,能够满足基片(如红外器件)对大尺寸、高均匀性、低损伤、低温镀膜工艺的要求,是一种结构简单、膜层纯度高、薄膜与基片附着力好的批产型离子束镀膜设备。
26.(2)本发明中,第一可旋转基片工件台、可摆动靶材工件台和溅射离子源相对设置,可利用第一调控装置的摆动调节作用,实现第一可旋转基片工件台的摆动,其中第一可旋转基片工件台的摆动角度为
‑
90
°
~65
°
,进而通过控制第一可旋转基片工件台的摆动角度改变基片、靶材和溅射离子源的相对角度,可用于镀膜工艺均匀性、镀膜区域以及镀膜速率的优化调整,有利于提高镀膜的均匀性和镀膜面积;同时,通过调节第一可旋转基片工件台的旋转转速和摆动角度,改善镀膜角度,使得镀膜角度能够满足不同晶向材料的镀膜需求,有利于提高膜层镀膜速率。
27.(3)本发明中,在第一可旋转基片工件台内部或表面设置第一控温装置,利用第一控温装置的温度调节作用,使第一可旋转基片工件台具备低温控制控制功能,可实现可旋转工件台的温度可调范围为
‑
40℃~150℃,能够满足红外器件基片如碲镉汞及带有光刻胶的基片对低温镀膜工艺要求。
28.(4)本发明中,通过在第一可旋转基片工件台上连接第一监控装置,使镀膜腔室具备镀膜厚度监控功能,可实现基片镀膜膜层厚度的在线精准监控,解决镀膜不均匀或者过度镀膜的问题。
29.(5)本发明中,第一可旋转基片挡板机构位于第一可旋转基片工件台的前侧,用于遮挡或开启第一可旋转基片工件台,可实现对第一可旋转基片工件台的遮挡或开启,当遮挡第一可旋转基片工件台时,第一可旋转基片挡板机构与第一可旋转基片工件台同心,保
护离子源初始放电时不稳定束流损伤基片,在镀膜过过程中,将第一可旋转基片挡板机构从第一可旋转基片工件台的前侧移开。
30.(6)本发明中,可移动束流修正板位于第一可旋转基片挡板机构的前侧,与溅射离子源之间的距离可调,可实现对离子源束流部分区域遮挡,具备镀膜形状调节功能,能够提高镀膜均匀性,最终实现大尺寸高均匀镀膜,适用于多种离子源束流的修正,可低成本解决基片镀膜不均匀问题。
附图说明
31.为使本发明实施例的目的、技术方案和优点更加清楚,下面将结合本发明实施例中的附图,对本发明实施例中的技术方案进行清楚、完整的描述。
32.图1为本发明离子束镀膜设备的布局示意图。
33.图2为本发明离子束镀膜设备中镀膜腔室的布局示意图。
34.图3为本发明离子束镀膜设备中清洗腔室的布局示意图。
35.图例说明:
36.1、装卸片腔室;2、传送腔室;21、转运机构;3、镀膜腔室;31、第一可旋转基片工件台;32、第一控温装置;33、第一调控装置;34、第一可旋转基片挡板机构;35、可摆动靶材工件台;36、可旋转靶材挡板机构;37、溅射离子源;4、清洗腔室;41、第二可旋转基片工件台;42、第二调控装置;43、第二可旋转基片挡板机构;44、清洗离子源;5、隔离阀。
具体实施方式
37.以下结合说明书附图和具体优选的实施例对本发明作进一步描述,但并不因此而限制本发明的保护范围。
38.实施例1
39.如图1、图2和图3所示,本实施例的离子束镀膜设备,包括装卸片腔室1、用传送基片的传送腔室2、至少一个用于基片镀膜的镀膜腔室3和清洗腔室4;装卸片腔室1、镀膜腔室3和清洗腔室4分别连接在传送腔室2上;装卸片腔室1与传送腔室2之间设有隔离阀5;传送腔室2与镀膜腔室3之间设有隔离阀5;传送腔室2与清洗腔室4之间设有隔离阀5;传送腔室2内设有用于传送基片的转运机构21。
40.本发明中,设置的装卸片腔室1,用于存放不同类型的基片,一次装卸即可放入多种不同类型的基片,设置的传送腔室2,实现基片在装卸片腔室1、镀膜腔室3和清洗腔室4之间的转运,设置至少一个的镀膜腔室3,可实现对多个基片进行同时镀膜,也可实现多种类型膜层的制备,设置的清洗腔室4,可用于对基片进行清洗,去除基片表面的脏污及氧化物,极大的提高薄膜与基片之间的附着力。本发明中,通过传送腔室2中设置的转运机构21,将基片从装卸片腔室1中转运至清洗腔室4中进行清洗,进而将基片从清洗腔室4中转运至镀膜腔室3中进行镀膜,最后将镀膜后的基片从镀膜腔室3中转运至装卸片腔室1中,同时,在使用过程中,通过隔离阀5实现装卸片腔室1、传送腔室2、镀膜腔室3和清洗腔室4的通断,隔离阀5关闭时,装卸片腔室1、传送腔室2、镀膜腔室3和清洗腔室4均不会暴露在大气中,不仅能够保证在相同的真空条件下实现基片装卸,降低基片带入镀膜腔室中的水气量,而且不会破坏镀膜腔室3和清洗腔室4的真空度,可实现基片的连续清洗和连续镀膜,大大降低因
腔体与基片污染造成的薄膜质量差等问题,可实现连续生产,提高生产效率,降低生产成本。本发明离子束镀膜设备,能够满足基片(如红外器件)对大尺寸、低损伤、低温镀膜工艺的要求。
41.本实施例中,传送腔室2为多面体,装卸片腔室1、镀膜腔室3和清洗腔室4分布在传送腔室2的各个面上,其中装卸片腔室1的数量为1个,位于传送腔室2的底部;镀膜腔室3的数量为4个,位于传送腔室2的四周和上部;清洗腔室4的的数量为1个,位于传送腔室2的四周。另外,本发明中,传送腔室2还可以为球体,其中装卸片腔室1、镀膜腔室3和清洗腔室4的布置方式可根据实际情况进行调整,如,装卸片腔室1、镀膜腔室3和清洗腔室4分布在传送腔室2的周围,包括底部、顶部和四周。
42.本实施例中,转运机构21为真空机械手。
43.本实施例中,每个镀膜腔室3内设有用于放置基片的第一可旋转基片工件台31、用于调节第一可旋转基片工件台31摆动角度的第一调控装置33、用于放置靶材的可摆动靶材工件台35和溅射离子源37;第一可旋转基片工件台31上连接有用于调节基片温度的第一控温装置32和用于监控基片镀膜程度的第一监控装置;第一控温装置32包括冷却管和在冷却管内循环的冷却液,冷却管设置在第一可旋转基片工件台31的内部或表面;冷却液为硅油;硅油的温度为
‑
40℃~150℃;第一可旋转基片工件台31的前侧依次设有第一可旋转基片挡板机构34和可移动束流修正板;可摆动靶材工件台35的前侧设有可旋转靶材挡板机构36。本发明中,第一可旋转基片工件台31、可摆动靶材工件台35和溅射离子源37相对设置,可利用第一调控装置33的摆动调节作用,实现第一可旋转基片工件台31的摆动,其中第一可旋转基片工件台31的摆动角度为
‑
90
°
~65
°
,进而通过控制第一可旋转基片工件台31的摆动角度改变基片、靶材和溅射离子源的相对角度,可用于镀膜工艺均匀性、镀膜区域以及镀膜速率的优化调整,有利于提高镀膜的均匀性和镀膜面积;同时,通过调节第一可旋转基片工件台31的旋转转速和摆动角度,改善镀膜角度,使得镀膜角度能够满足不同晶向材料的镀膜需求,有利于提高膜层镀膜速率。本发明中,在第一可旋转基片工件台31内部或表面设置第一控温装置32,利用第一控温装置32的温度调节作用,使第一可旋转基片工件台31具备低温控制控制功能,可实现可旋转工件台31的温度可调范围为
‑
40℃~150℃,能够满足红外器件基片如碲镉汞及带有光刻胶的基片对低温镀膜工艺要求。本发明中,通过在第一可旋转基片工件台31上连接第一监控装置,使镀膜腔室3具备镀膜厚度监控功能,可实现基片镀膜膜层厚度的在线精准监控,解决镀膜不均匀或者过度镀膜的问题。本发明中,第一可旋转基片挡板机构34位于第一可旋转基片工件台31的前侧,用于遮挡或开启第一可旋转基片工件台31,可实现对第一可旋转基片工件台31的遮挡或开启,当遮挡第一可旋转基片工件台31时,第一可旋转基片挡板机构34与第一可旋转基片工件台31同心,保护离子源初始放电时不稳定束流损伤基片,在镀膜过过程中,将第一可旋转基片挡板机构34从第一可旋转基片工件台31的前侧移开。本发明中,可移动束流修正板位于第一可旋转基片挡板机构34的前侧,与溅射离子源37之间的距离可调,可实现对离子源束流部分区域遮挡,具备镀膜形状调节功能,能够提高镀膜均匀性,最终实现大尺寸高均匀镀膜,适用于多种离子源束流的修正,可低成本解决基片镀膜不均匀问题。
44.每个清洗腔室4内设有用于放置基片的第二可旋转基片工件台41、用于调节第二可旋转基片工件台41摆动角度的第二调控装置42和清洗离子源44;第二可旋转基片工件台
41上连接有用于调节基片温度的第二控温装置和用于监控基片清洗程度的第二监控装置;第二控温装置包括冷却管和在冷却管内循环的冷却液,冷却管设置在第二可旋转基片工件台41的内部或表面;冷却液为硅油;硅油的温度为
‑
40℃~150℃;第二可旋转基片工件台41的前侧设有第二可旋转基片挡板机构43。本发明中,第二可旋转基片工件台41和清洗离子源44相对设置,可利用第二调控装置42的摆动调节作用,实现第二可旋转基片工件台41的摆动,其中第二可旋转基片工件台41的摆动角度为
‑
90
°
~65
°
,进而通过控制第二可旋转基片工件台41的摆动角度改变基片、靶材与清洗离子源的相对角度,可用于清洗工艺均匀性、清洗区域以及清洗速率的优化调整,有利于提高清洗的均匀性和清洗面积;同时,通过调节第二可旋转基片工件台41的旋转转速和摆动角度,改善清洗角度,使得清洗角度能够满足不同晶向材料的清洗需求,有利于提高清洗速率。本发明中,在第二可旋转基片工件台41内部或表面设置第二控温装置,利用第二控温装置的温度调节作用,使第二可旋转基片工件台41具备低温控制控制功能,可实现第二可旋转基片工件台41的温度可调范围为
‑
40℃~150℃,能够满足红外器件基片如碲镉汞及带有光刻胶的基片对低温清洗工艺要求。本发明中,通过在第二可旋转基片工件台41上连接第二监控装置,使清洗腔室4具备清洗情况监控功能,可实现基片清洗情况的在线精准监控,解决清洗不干净或者过清洗问题。本发明中,第二可旋转基片挡板机构43位于第二可旋转基片工件台41的前侧,用于遮挡或开启第二可旋转基片工件台41,可实现对第二可旋转基片工件台41的遮挡或开启,当遮挡第二可旋转基片工件台41时,第二可旋转基片挡板机构43与第二可旋转基片工件台41同心,保护离子源初始放电时不稳定束流损伤基片,在镀膜过过程中,将第二可旋转基片挡板机构43从第二可旋转基片工件台41的前侧移开。
45.本实施例中,每个镀膜腔室3上设有维护门,溅射离子源37安装在维护门上;溅射离子源37位于镀膜腔室3内的一侧设有聚焦型的栅网;栅网上连接有用于发射电子、中和带正电离子束的中和器。本发明中,溅射离子源37安装在镀膜腔室3的维护门上,可通过移动维护门来增大溅射离子源37的维护空间,不需要将溅射离子源37从腔室取出,大幅度缩短溅射离子源37的维护时间,提高生产效率。本发明中,溅射离子源37位于镀膜腔室3内的一侧设有的栅网还可以为平行型(也称为平面型)的栅网。
46.每个清洗腔室4上设有维护门,清洗离子源44安装在维护门上;清洗离子源44位于清洗腔室4内的一侧设有发散型的栅网;栅网上连接有用于发射电子、中和带正电离子束的中和器。本发明中,清洗离子源44安装在清洗腔室4的维护门上,可通过移动维护门来增大清洗离子源44的维护空间,不需要将清洗离子源44从腔室取出,大幅度缩短清洗离子源44的维护时间,提高生产效率。本发明中,清洗离子源44位于清洗腔室4内的一侧设有的栅网还可以为平行型(也称为平面型)的栅网。
47.本实施例中,装卸片腔室1中设有用于升降基片的升降机构;升降机构上设有至少两个用于放置基片的托盘;每个托盘上设有若干个用于固定基片的紧固孔;托盘的形状为圆形。本发明中,设置多个托盘,不仅可以将预镀膜基片和镀膜后的基片分开放置,提高清洗和镀膜效率,同时也能将不同类型的基片分开放置,一次装载实现多种不同类型基片的清洗、镀膜,具备多样性功能。本发明中,在托盘上设置若干个紧固孔,可实现不同规格基片的兼容装载,如可满足可兼容圆形、方形或异形等不同规则的基片。本发明中,托盘的形状还可以为椭圆形、三角形或多边方形。
48.本实施例中,还包括抽真空装置和电控装置;抽真空装置和电控装置分别连接在装卸片腔室1、传送腔室2、镀膜腔室3和清洗腔室4上。本发明中,通过抽真空装置的抽真空作用控制装卸片腔室1、传送腔室2、镀膜腔室3和清洗腔室4中清洗和镀膜时所需的真空度;同时,通过电控装置(如计算机以及plc)控制离子源、工件台、挡板机构、转运机构、升降机构、抽真空装置等工作,可以根据离子源参数自动跟踪调整离子束流大小,不需要人为干预,降低人力成本的同时提高工艺的可重复性。
49.一种镀膜方法,该镀膜方法是采用上述离子束镀膜设备对基片进行镀膜,包括以下步骤:
50.s1、对基片(红外器件)进行预处理;
51.s2、将步骤s1中预处理后的基片置于装卸片腔室1中,经传送腔室2转运至清洗腔室4中进行清洗处理,具体为:
52.s2
‑
1、将步骤s1中预处理后的基片转运至清洗腔室4中:(a)将预处理后的基片放置于装卸片腔室1内的托盘中,用紧固孔固定;(b)利用抽真空装置对装卸片腔室1、传送腔室2、镀膜腔室3、清洗腔室4进行抽真空处理;(c)打开装卸片腔室1与传送腔室2之间的隔离阀5并通过升降机构将基片转运到真空条件下的传送腔室2内,随后关闭装卸片腔室1与传送腔室2之间的隔离阀5,并打开传送腔室2与清洗腔室4之间的隔离阀5,利用真空机械手将基片转运至清洗腔室4中,固定在第二可旋转基片工件台41上,关闭传送腔室2与清洗腔室4之间的隔离阀5。
53.s2
‑
2、对固定在清洗腔室4中的基片进行清洗处理,其中清洗处理过程中,控制离子源能量为100ev~500ev,离子束束流为50ma~200ma,中和束束流为离子束束流的1~2倍,基片的圆周旋转转速为5rpm~60rpm,左右摆动角度为
‑
35
°
~35
°
,温度为
‑
20℃~80℃。同时在清洗过程中利用第二监控装置监控基片表面的清洗,直至将基片表面的杂质材料有效去除即可。
54.s3、将步骤s2中清洗处理后的基片从清洗腔室4中取出,经传送腔室2转运至镀膜腔室3中进行镀膜处理,具体为:
55.s3
‑
1、将步骤s2中清洗处理后的基片转运至镀膜腔室3中:打开清洗腔室4与传送腔室2之间的隔离阀5并通过真空机械手将基片转运到真空条件下的镀膜腔室3内,并固定在第一可旋转基片工件台31上,在基片与第一可旋转基片工件台31之间设置硅脂,以提高基片与第一可旋转基片工件台31之间的导热能力,随后关闭清洗腔室4与传送腔室2之间的隔离阀5。
56.s3
‑
2、对固定在镀膜腔室3中的靶材进行清洗处理,其中靶材的清洗处理过程中,控制离子源能量为300ev~1200ev,离子束束流为50ma~500ma,中和束束流为离子束束流的1~2倍,靶材的左右摆动角度为
‑
35
°
~35
°
,温度为
‑
20℃~80℃。同时在清洗过程中监控靶材的清洗,直至将靶材表面的杂质材料有效去除即可。
57.s3
‑
3、利用步骤s2中清洗后的靶材对固定在镀膜腔室3中的基片进行镀膜处理,其中镀膜过程中控制离子源能量为300ev~1200ev,离子束束流为50ma~500ma,中和束束流为离子束束流的1~2倍;镀膜过程中,基片的圆周旋转转速为5rpm~60rpm,左右摆动角度为
‑
35
°
~35
°
,温度为
‑
20℃~80℃。同时在镀膜过程中利用第一监控装置监控基片镀膜程度,直至膜层厚度达到设定要求即可。
58.s4、重复步骤s3,在同一基片上沉积不同类型的薄膜。
59.s5、打开传送腔室2与镀膜腔室3之间的隔离阀5,利用真空机械手将基片转运至托盘中,通过装卸片腔室1将基片取出,完成对基片的镀膜。
60.以上实施例仅是本发明的优选实施方式,本发明的保护范围并不仅局限于上述实施例。凡属于本发明思路下的技术方案均属于本发明的保护范围。应该指出,对于本技术领域的普通技术人员来说,在不脱离本发明原理的前提下的改进和润饰,这些改进和润饰也应视为本发明的保护范围。