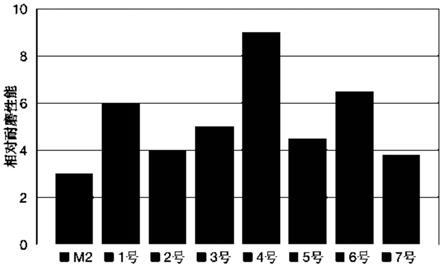
1.本发明涉及工具合金材料技术领域,特别涉及一种沉淀硬化合金。
背景技术:2.对于有色合金如ni基金属或奥氏体不锈钢类材质的车削加工,由于刃口位置高的应力及剧烈的摩擦,导致刃口局部范围产生极高的温度。目前广泛采用的一种方案是使用硬质合金刀具进行加工,但是使用过程需要操作非常严格,毕竟硬质合金是一种脆性非常大的金属,尤其是在高温高应力反复加载工况条件下,局部热疲劳微崩是主要的失效机制。
3.另外,硬质合金大量使用w、co等元素,价格高昂是其一个短板。相比于硬质合金,高速钢是另外一种通用的车削刀具材料,以fe为基体,韧性相对较好,价格相对低廉。
4.高速钢在一定温度条件下,马氏体基体中二次析出的极细小碳化物使高速钢的硬度和耐磨性能能够得到维持,但在前述ni基合金或不锈钢车削加工工况条件下,刃口局部温度甚至超过高速钢的高温回火温度,高速钢马氏体基体中合金元素加速析出,碳化物粗化,总体表现为高速钢的刃口软化,使用过程快速磨损,受限于此,传统以碳化物作为主要析出强化相的高速钢难以胜任该类合金的高效车削加工。
技术实现要素:5.有鉴于此,本发明旨在提出一种沉淀硬化合金,以使其具有优异的综合性能,尤其是高温硬度及耐磨性能。
6.为达到上述目的,本发明的技术方案是这样实现的:
7.一种沉淀硬化合金,所述沉淀硬化合金采用电渣工艺或粉末冶金工艺制备,且其化学组分按质量百分比计包括:(c+n):0.01%-1.2%;si:0.1%-1.0%;mn:0.1%-0.8%;(mo+0.5w):10%-32%,且mo:6%-30%;co:15%-35%;ti:0.01%-6%,余量为fe和杂质。
8.进一步的,(c+n):0.01%-0.6%;si:0.2%-1.0%;mn:0.2%-0.8%;(mo+0.5w):10%-30%,且mo:10%-30%;co:15%-30%;ti:0.01%-3%。
9.进一步的,所述合金包括w:≤20%。
10.进一步的,所述合金包括w:≤16%。
11.进一步的,所述杂质包括o,且o:≤0.03%。
12.进一步的,所述杂质包括s和p中至少其一,且s:≤0.3%,p:≤0.05%。
13.进一步的,所述沉淀硬化合金中金属间化合物的体积分数为4-30%。
14.进一步的,所述金属间化合物颗粒尺寸≤8μm。
15.进一步的,至少80%的所述金属间化合物颗粒尺寸≤5μm。
16.在本发明中,特定的化学成分及配比是实现其综合性能的必要条件,各化学组分作用及原理简述如下:
17.fe、co、mo化合反应以μ型沉淀硬化方式析出,可提升及维持基体硬度,co的合适的含量范围为:15%-35%,co优选范围为:15%-30%,mo的合适的含量范围为:6%-30%,mo
优选范围为:10%-30%。
18.w作为一种可选元素,可部分替换mo发挥类似作用,本发明中(mo+0.5w)的合适的含量范围10%-32%,同时w:≤20%,优选(mo+0.5w)的含量范围为10%-30%,同时w:≤16%。
19.ti提供高熔点析出细化晶粒作用,其可与c或n化合反应形成高熔点mx析出相,产生细化晶粒及提升耐磨性能作用,其中m为ti元素,x为c或n元素,c和n在一定范围内可互换,本发明中,ti的合适的含量范围为0.01%-6%,优选的含量范围为0.01%-3%,(c+n)的合适的含量范围为0.01%-1.2%,优选的(c+n)的合适的含量范围为0.01%-0.6%。
20.si作为一种脱氧剂和基体强化元素来使用,但过高的si导致基体脆性增加,因此本发明中,si的合适的含量范围为0.1%-1.0%,优选的合适的含量范围为0.2%-1.0%。
21.mn作为脱氧剂加入,可以弱化s的有害作用,但过高mn增加脆性风险,因此本发明中,mn的合适的含量范围为0.1%-0.8%,优选的合适的含量范围为0.2%-0.8%。
22.本发明的沉淀硬化合金,除了上述设定的化学组分,余量为fe基体,当然还包括一些不可避免的残余微量元素,包括o、s、p等,为了防止对合金力学性能产生不利影响,要求o的合适的含量范围为≤0.03%,s的合适的含量范围为≤0.3%,p的合适的含量范围为≤0.05%。
23.除此以外,本发明的化学组分中,杂质还可包括zr、mg、al、cu、ni、sn和pb中的至少一种,且这些杂质的总量不大于1%。
24.相对于现有技术,本发明具有以下优势:
25.本发明所述的沉淀硬化合金,关键在于选定合适的化学组分及配比,使得第二相主要以沉淀硬化方式在基体中脱溶析出,形成μ型金属间化合物,金属间化合物主要组成合金元素包括fe、co、mo等,且金属间化合物以细小弥散方式分布于基体,具有高硬度、高热稳定性特点,可对基体产生强化作用。除此以外,其还具有优异的综合性能,包括高的红硬性、优异的抗高温软化特性、热处理变形小、耐磨损性能、耐腐蚀性能、抗高温氧化性能及韧性等。
26.另外,本发明所述沉淀硬化合金适用于刀具、模具以及特殊关键零部件的制造,如高速车削加工用的滚刀、车刀等,也可用于冷作加工,包括深冲、折弯、粉末压制等。基于其性能特点,也适用于各类关键部件的制作,如喷油嘴、螺杆、泵体滑片等。
附图说明
27.构成本发明的一部分的附图用来提供对本发明的进一步理解,本发明的示意性实施例及其说明用于解释本发明,并不构成对本发明的不当限定。在附图中:
28.图1为本发明所述的m2高速钢热处理后的微观组织示意图;
29.图2为本发明所述的实施例1的沉淀硬化合金微观组织示意图;
30.图3为本发明所述的实施例2的沉淀硬化合金微观组织示意图;
31.图4为本发明所述的沉淀硬化合金各实施例的相对耐磨性能对比的示意图。
具体实施方式
32.需要说明的是,在不冲突的情况下,本发明中的实施例及实施例中的特征可以相
互组合。
33.下面将参考附图并结合实施例来详细说明本发明。
34.本发明的沉淀硬化合金,尤其涉及一种基于沉淀硬化机理,具有高的红硬性、耐磨损性能、耐腐蚀性能、抗高温氧化特性合金。为了改善其综合性能,本发明限定了合适的化学组分及配比,根据本发明中特定的化学成分及配比,本发明所述的沉淀硬化合金可以采用传统电渣工艺制备锭材,同时也可采用粉末冶金工艺制备锭材。
35.传统电渣重熔工艺主要包括合金熔液冶炼,电渣重熔精炼等步骤。粉末冶金工艺主要包括气雾化制粉,热等静压等步骤。作为一种优选的可行的实施方案,本发明的沉淀硬化合金优选采用粉末冶金工艺制备。
36.在此需要说明的是,本发明所述的气雾化制粉工艺包括如下过程,采用一种高压惰性气体,如氮气或氩气,将具有本发明合金成分的熔融态合金液雾化喷射冷却,使合金熔液瞬间凝固成细小的近球形粉末颗粒。
37.本发明所述的热等静压工艺包括如下过程,将气雾化制粉工艺制备的合金粉末置于一个金属包套,对其抽真空后排出包套内气体后然后焊接密封,将装粉密封后的包套置于热等静压炉,在温度超过1000℃及压力超过100mpa条件下实现包套内粉末完全的致密化,从而成为锭材。
38.为了进一步改善力学性能或实现特定形状产品尺寸,当然还可对制备的锭材进行进一步的热变形加工。作为一种优选的可行的实施方案,热处理工艺包括固溶处理及时效处理两个步骤,高温固溶处理温度为1150℃-1240℃,保温时间30min-240min;时效处理温度为560℃-680℃,保温时间60min-300min。
39.现结合本发明的几个具体实施例来进行说明,具体可参照表1中所示。
40.表1:各实施例和对比例的化学组分
[0041][0042]
对比例为通用的商业牌号为m2的高速钢,其成分如表1中所示,该m2高速钢采用电渣重熔工艺制备,由电渣重熔锭热变形至直径50mm棒材。而后经过1160℃奥氏体化后淬火处理,随后620℃回火2小时。
[0043]
实施例1至实施例8所示。其采用粉末冶金工艺制备,也即先采用气雾化制粉工艺
制取粉末,然后对粉末进行热等静压致密化,而后制成直径120mm的锭坯,进一步热变形加工后得到直径50mm的棒材。
[0044]
所述雾化制粉工艺步骤及工艺参数如下:
[0045]
a.将本发明合金装入熔炼钢包,在保护气氛下供电加热;
[0046]
b.合金熔化后继续升温至1700℃,取样分析成分后调整至合格范围;
[0047]
c.预热雾化中间包坩埚,合金熔液雾化前中间包温度达到1200℃;
[0048]
d.合金熔液温度达到要求后开启高压雾化气体及排空风机,合金熔液经中间包底部陶瓷漏眼进入雾化系统,启动合金熔液雾化,合金熔液雾化流量控制在20kg/min;
[0049]
e.雾化粉末经气流输送至集粉罐体,冷却至50℃。
[0050]
所述热等静压工艺过程如下:
[0051]
a、将气雾化制粉工艺制备的合金粉末置于一个金属包套,对其抽真空后排出包套内气体,然后焊接密封;
[0052]
b、将装粉密封后的包套置于热等静压炉,在温度1170℃及压力150mpa条件下实现包套内粉末完全致密化,成为热等静压锭材。
[0053]
在此需要说明的是,实施例8在气雾化制粉过程中,金属液容易发生雾化漏眼堵塞,难以稳定生产。
[0054]
接下来,对表1中实施例1至实施例7的合金从以下几个方面进行对比测试:(1)热处理后微观组织;(2)热处理硬度;(3)耐磨性能;(4)耐腐蚀性能。对比结果如下:
[0055]
(1)热处理后微观组织
[0056]
对实施例1至实施例7分析微观组织,结果如表2所示。
[0057]
表2:各实施例第二相含量及粒度对比
[0058]
实施例高温固溶处理时效处理第二相体积分数11190℃,1h600℃,4h11%21190℃,1h600℃,4h8%31190℃,1h600℃,4h10%41190℃,1h600℃,4h13%51190℃,1h600℃,4h9%61190℃,1h600℃,4h10%71190℃,1h600℃,4h5%
[0059]
对比例m2高速钢采用传统电渣重熔工艺制备,其热处理后的微观组织如图1所示,碳化物表现出不均匀分布现象,一方面碳化物比较粗大,其尺寸可达到20μm-30μm,同时延热变形方向呈条带状分布。
[0060]
对实施例1至实施例7的微观组织进行分析,其中实施例1和实施例2的合金的微观组织分别如图2和图3所示,微观组织均匀,第二相主要为沉淀析出金属间化合物及高熔点mx析出相,第二相颗粒均细小且分布均匀,其中金属间化合物颗粒尺寸≤8μm,至少80%颗粒尺寸≤5μm。
[0061]
实施例8由于没有高熔点mx析出相对晶粒生长的阻滞作用,其晶粒尺寸相比其它实施例有明显粗化。
[0062]
(2)热处理硬度
[0063]
对实施例1至实施例7沉淀硬化合金测试硬度,结果见下表。
[0064]
表3:对各实施例进行热处理后的硬度测试结果
[0065]
实施例高温固溶回火硬度/hrcm21160℃,0.5h600℃,4h5411190℃,1h600℃,4h6621190℃,1h600℃,4h6531190℃,1h600℃,4h6541190℃,1h600℃,4h6451190℃,1h600℃,4h6561190℃,1h600℃,4h6571190℃,1h600℃,4h64
[0066]
热处理的工艺参数如表3所示,参照gb/t 230.1-2018,并采用洛氏硬度计分别测定各实施例和对比例的合金热处理后的硬度,结果表明,实施例1至实施例7的沉淀硬化合金相比传统m2高速钢在高温回火后具有更优越的硬度保持性。
[0067]
(3)耐磨性能
[0068]
采用金属对磨试验测试合金的耐磨性能,摩擦副为45#钢,载荷50kg,转数200r/min。本实施例1至实施例7的合金热处理的工艺参数如表3中所示。为发挥m2高速钢最佳耐磨性能,采用1160℃淬火及540℃回火工艺进行热处理,热处理后硬度为65hrc。耐磨性能根据被测试材料失重进行计量,划分为10个耐磨性能等级,其中1为最差耐磨性能,10为最好耐磨性能。
[0069]
对比结果如图4中所示,实施例1至实施例7的合金均表现出更为优秀的耐磨性能,尤其是实施例4,在微观组织析出大量高硬度mx析出相的叠加作用下,表现出了最优异的耐磨性能。
[0070]
(4)耐腐蚀性能
[0071]
参照表3对实施例1-7进行热处理,采用1160℃淬火及540℃回火工艺对m2进行热处理,然后对比测试耐腐蚀性能,方法为采用5%硝酸乙醇溶液浸泡腐蚀,浸泡1小时后观察表面腐蚀状态,0代表无腐蚀点,10代表整个表面被腐蚀,对比结果如表4所示:
[0072]
表4:对合金的各实施例进行耐腐蚀性能对比
[0073]
序号腐蚀状态m210102030406070
[0074]
从表4可看出,本发明合金表现出非常优秀的耐腐蚀特性。
[0075]
在本说明书的描述中,给出了本发明的实施例,可以理解的是,上述实施例是示例性的,不能理解为对发明的限制,在不相互矛盾的情况下,本领域的普通技术人员可以将本
说明书中描述的不同实施例或示例的特征进行结合、组合、替换和变形。