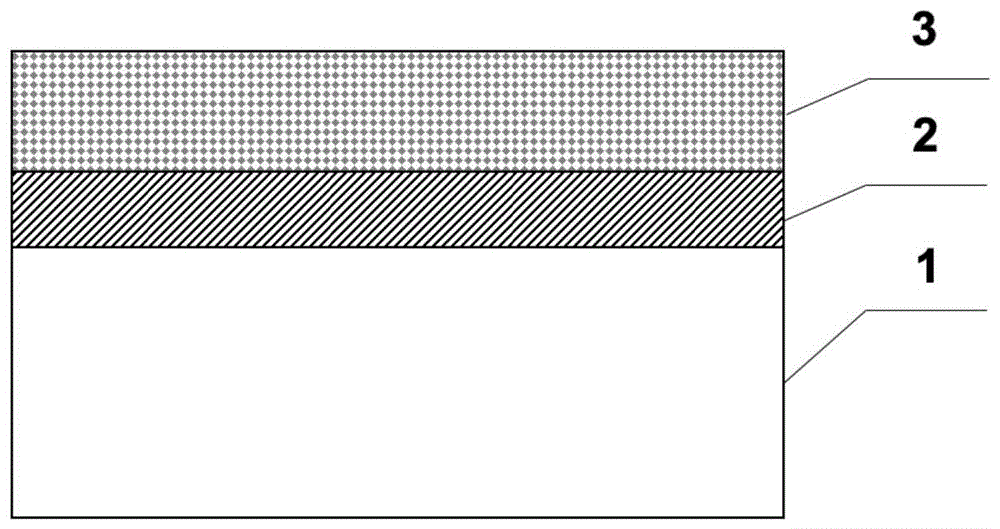
本发明涉及硬质薄膜
技术领域:
,具体涉及一种导电耐磨自润滑碳基薄膜及其制备方法。
背景技术:
:非晶碳基薄膜(amorphouscarbon,a-c)是一类由石墨结构sp2杂化键碳原子和金刚石结构sp3杂化键碳原子相互混杂组成的亚稳态非晶物质,因其硬度高,摩擦系数低,承载能力强和在大气、水等环境中具有良好的自适应减摩耐磨特性,被认为是一种理想的耐磨自润滑薄膜材料,在航空航天、电子机械、现代轨道交通系统等领域具有广阔的应用前景。随着科技的发展,越来越多的机械关键核心部件如电力电子系统集电环、电磁轨道炮的导轨、mems等,需要在滑动电接触摩擦条件下运行,由于电因素的引入,电接触载流摩擦磨损需要在传统机械摩擦磨损的基础上考虑电场、电流甚至电弧对滑动摩擦副的影响。作为面向载流摩擦磨损应用的表面防护涂层,碳基薄膜不仅需要具有良好的力学性能,较低的接触电阻,还必须具有优良的减摩耐磨和热稳定性。因此,如何实现高导电、高耐磨和自润滑碳基薄膜的可控制备对发展高可靠性关键摩擦副零部件表面防护具有十分积极的意义。掺杂异质元素通过在碳基薄膜中引入异质原子形成纳米复合结构,不仅能够有效地降低薄膜残余应力,提高薄膜与基体之间的结合力,增强薄膜的韧性,还可以在较大范围内调节薄膜的力学与电学性能。g.schultes等团队在2018年报道了采用pvd/cvd复合技术制备ni元素掺杂的非晶碳基薄膜的技术,该制备产品碳基网络中的fcc-ni和ni3c纳米晶被碳原子网络紧紧包裹着形成“核壳结构”,由于电子在不同纳米晶颗粒间可以通过“隧道效应”传输迁移运动,使所制备的薄膜表现出一定的电学性能。然而,这类产品包裹纳米晶粒的非晶碳基网络呈无序排布状态以及大量氢原子会阻碍电子的传输运动,使得薄膜的导电能力存在较大的局限性。氮元素掺杂不仅能够能提高薄膜载流子浓度,改变薄膜中的sp3和sp2杂化碳原子相对比例,高浓度氮掺杂还会诱导碳原子以六角圆环形式排布而形成sp2杂化键,形成独特的纳米二维层状结构。此外,氮源丰富无毒性,使得氮元素掺杂成为提高非晶碳薄膜导电性能最常用的措施之一。石墨烯中碳原子独特的纳米二维层状结构使其具有极高的力学性能、导电和导热性能。技术实现要素:基于现有技术存在的缺陷,本发明的目的在于提供了一种导电耐磨自润滑碳基薄膜的制备方法,所述方法采用高功率脉冲磁控溅射技术,利用ni和n二元元素掺杂改性并调控工艺,在高温下将纳米二维层状碳网络结构引入至非晶碳基薄膜中,充分发挥复合元素间的协同作用,不仅使其获得优异的导电性能,同时产品内部的应力充分缓解,有效提高所得薄膜的减摩耐磨性。为了达到上述目的,本发明采取的技术方案为:一种导电耐磨自润滑碳基薄膜的制备方法,包括以下步骤:(1)基体预处理:将处理干净后的基体置于真空环境中,随后通入氩气并在基体上施加负偏压,通过辉光放电产生等离子体对基体表面进行离子蚀刻;(2)沉积梯度过渡层:通入氮气并调节cr靶功率至500~600w,在离子蚀刻后的基体表面沉积金属crn层,随后开启高纯石墨靶高功率脉冲电源并梯度提升功率至30kw,同时降低cr靶功率,在沉积的金属crn层上继续沉积金属碳化物crcxny层;(3)沉积功能碳基薄膜:将步骤(2)沉积梯度过渡层后的基体加热并控制负偏压,开启镶嵌有金属ni的高纯石墨靶高功率脉冲电源,通入氮气并在步骤(2)所述crcxny层上方沉积功能碳基薄膜层,即得所述导电耐磨自润滑碳基薄膜。本发明所述导电耐磨自润滑碳基薄膜的制备方法创新地将纳米二维层状结构引入非晶碳基薄膜中,在碳基薄膜优良的耐磨自润滑特性基础上获得优异的导电性能。本发明所述方法采用高功率脉冲磁控溅射技术,通过工艺调控使非晶碳基薄膜中碳原子呈二维层状排列,同时在碳基薄膜中同时掺杂非金属元素n和金属元素ni,使薄膜形成纳米晶-非晶复合结构,充分发挥复合元素之间的协同作用,缓解薄膜内应力,提高薄膜导电性和减摩耐磨特性。优选地,所述基体包括铜合金、铝合金、钛合金、模具钢、不锈钢中的至少一种。优选地,步骤(1)所述真空环境的气压≤5×10-3pa。优选地,步骤(1)所述基体预处理过程中,通入氩气后的气压为1~1.5pa,在基体上施加负偏压≥800v,对基体表面进行离子蚀刻的时间为20~30min。所述条件下可保障等离子体的高纯度以及基体表面的离子清洗洁净程度,有利于清除基体表面的污染物,露出新鲜的原子面,便于后续沉积。优选地,步骤(2)所述基体表面沉积金属crn层时基体的负偏压为100~200v,氮气的通入流量为30~50sccm。通过步骤(2)在所述条件下引入的金属crn层以及金属碳化物crcxny层作为过渡层可增加后续沉积的功能碳基薄膜与基体间的结合强度。更优选地,所述金属crn层的沉积厚度为50~100nm,所述金属碳化物crcxny层的沉积厚度为100~200nm,所述金属crn层与金属碳化物crcxny层的总厚度为150~300nm。优选地,步骤(3)所述沉积功能碳基薄膜层时基体的负偏压为80~150v,加热的温度为300~350℃,氮气的通入流量为30~50sccm,沉积气压为0.35~0.5pa。通过所述环境条件下,基体表面可有效沉积功能碳基薄膜,所述沉积薄膜纯度高,质地均匀且沉积效率高。优选地,步骤(3)所述沉积功能碳基薄膜层时镶嵌有金属ni的高纯石墨靶高功率脉冲电源的功率为25~30kw,脉宽为100~200μs,频率为100~200hz。本发明所述镶嵌有金属ni的高纯石墨靶高功率脉冲电源可引入纳米ni掺杂碳基薄膜,所述使用条件可保障生成薄膜功率稳定,沉积薄膜质量高,所得产品具有优异的均匀性。优选地,步骤(3)所述功能碳基薄膜层的沉积厚度为500~5000nm。优选地,所述沉积过程采用闭场非平衡磁控溅射离子镀膜设备实施。本发明的另一目的还在于提供所述导电耐磨自润滑碳基薄膜的制备方法制备的导电耐磨自润滑碳基薄膜。本发明所制备的导电耐磨自润滑碳基薄膜内部结构中无氢原子存在,碳基薄膜的内部结构为纳米晶-非晶复合结构,其中部分碳原子呈类石墨烯片层状排列,n原子取代部分c原子与c原子组成化学键,这种特殊的结构使得碳基薄膜具有导电耐磨自润滑的功能特性,可用于电接触摩擦条件下服役的关键部件表面防护涂层应用于mems、电子控制等领域。本发明的有益效果在于,本发明提供了一种导电耐磨自润滑碳基薄膜的制备方法,该方法创新地将纳米二维层状结构引入非晶碳基薄膜中,在碳基薄膜优良的耐磨自润滑特性基础上获得优异的导电性能。本发明所述方法采用高功率脉冲磁控溅射技术,通过工艺调控使非晶碳基薄膜中碳原子呈二维层状排列,同时在碳基薄膜中同时掺杂非金属元素n和金属元素ni,使薄膜形成纳米晶-非晶复合结构,充分发挥复合元素之间的协同作用,缓解薄膜内应力,提高薄膜导电性和减摩耐磨特性。此外,所述方法无需制备产品无需后处理工序,制备流程简单可控,可实现工业化大规模生产。本发明还提供了所述方法制备的导电耐磨自润滑碳基薄膜。附图说明图1为本发明所述导电耐磨自润滑碳基薄膜的结构示意图,其中1为基体,2为梯度过渡层,3为功能碳基薄膜层;图2为本发明所述导电耐磨自润滑碳基薄膜的扫描电镜横截面结构图;图3为本发明所述导电耐磨自润滑碳基薄膜的摩擦系数曲线图。具体实施方式为了更好地说明本发明的目的、技术方案和优点,下面将结合具体实施例及对比例对本发明作进一步说明,其目的在于详细地理解本发明的内容,而不是对本发明的限制。本领域普通技术人员在没有做出创造性劳动前提下所获得的所有其他实施例,都属于本发明的保护范围。本发明实施所设计的实验试剂及仪器,除非特别说明,均为常用的普通试剂及仪器。实施例1本发明所述所述导电耐磨自润滑碳基薄膜的制备方法的一种实施例,包括以下步骤:(1)基体预处理:将除油清洗干净后的基体置于真空环境中的真空室工作架上,抽真空至气压为5×10-3pa,随后通过流量自动控制系统通入氩气至气压为1pa并在基体上施加800v负偏压,通过辉光放电产生等离子体对基体表面进行离子蚀刻20min;(2)沉积梯度过渡层:将基体负偏压降至100v,通入30sccm氮气并调节cr靶功率至500w,在离子蚀刻后的基体表面50nm厚度的沉积金属crn层,随后开启高纯石墨靶高功率脉冲电源并梯度提升功率至30kw,同时降低cr靶功率,在沉积的金属crn层上继续100nm厚度的沉积金属碳化物crcxny层;(3)沉积功能碳基薄膜:将步骤(2)沉积梯度过渡层后的基体加热至300℃并控制负偏压至80v,开启镶嵌有金属ni的高纯石墨靶高功率脉冲电源,通入30sccm氮气,保持气压为0.35pa并在步骤(2)所述crcxny层上方沉积功能碳基薄膜层30min至厚度为500nm,即得所述导电耐磨自润滑碳基薄膜;所述电源的功率为25kw,脉宽100μs,频率为100hz。本实施例所述导电耐磨自润滑碳基薄膜经沉积后理论的结构示意图如图1所示,而经过扫描电镜对本实施例产品进行观察后发现其与理论预期一致,如图2所示,所述沉积层具有纳米二维层状结构。将所得产品在大气环境下进行摩擦系数测试,采用ms-t3001型球盘式摩擦磨损试验仪,所述产品的对磨对象为氮化硅球,结果如图3所示,所制备的导电耐磨自润滑碳基薄膜的摩擦系数始终在0.1~0.15左右,说明产品具有优异的减摩自润滑性能。实施例2本发明所述所述导电耐磨自润滑碳基薄膜的制备方法的一种实施例,包括以下步骤:(1)基体预处理:将除油清洗干净后的基体置于真空环境中的真空室工作架上,抽真空至气压为4×10-3pa,随后通过流量自动控制系统通入氩气至气压为1.2pa并在基体上施加850v负偏压,通过辉光放电产生等离子体对基体表面进行离子蚀刻25min;(2)沉积梯度过渡层:将基体负偏压降至150v,通入40sccm氮气并调节cr靶功率至550w,在离子蚀刻后的基体表面75nm厚度的沉积金属crn层,随后开启高纯石墨靶高功率脉冲电源并梯度提升功率至30kw,同时降低cr靶功率,在沉积的金属crn层上继续150nm厚度的沉积金属碳化物crcxny层;(3)沉积功能碳基薄膜:将步骤(2)沉积梯度过渡层后的基体加热至330℃并控制负偏压至100v,开启镶嵌有金属ni的高纯石墨靶高功率脉冲电源,通入40sccm氮气,保持气压为0.4pa并在步骤(2)所述crcxny层上方沉积功能碳基薄膜层180min至厚度为3000nm,即得所述导电耐磨自润滑碳基薄膜;所述电源的功率为28kw,脉宽150μs,频率为150hz。实施例3本发明所述所述导电耐磨自润滑碳基薄膜的制备方法的一种实施例,包括以下步骤:(1)基体预处理:将除油清洗干净后的基体置于真空环境中的真空室工作架上,抽真空至气压为4.5×10-3pa,随后通过流量自动控制系统通入氩气至气压为1.5pa并在基体上施加900v负偏压,通过辉光放电产生等离子体对基体表面进行离子蚀刻30min;(2)沉积梯度过渡层:将基体负偏压降至200v,通入50sccm氮气并调节cr靶功率至600w,在离子蚀刻后的基体表面100nm厚度的沉积金属crn层,随后开启高纯石墨靶高功率脉冲电源并梯度提升功率至30kw,同时降低cr靶功率,在沉积的金属crn层上继续200nm厚度的沉积金属碳化物crcxny层;(3)沉积功能碳基薄膜:将步骤(2)沉积梯度过渡层后的基体加热至350℃并控制负偏压至150v,开启镶嵌有金属ni的高纯石墨靶高功率脉冲电源,通入50sccm氮气,保持气压为0.5pa并在步骤(2)所述crcxny层上方沉积功能碳基薄膜层300min至厚度为5000nm,即得所述导电耐磨自润滑碳基薄膜;所述电源的功率为30kw,脉宽200μs,频率为200hz。效果例1为验证本发明所述导电耐磨自润滑碳基薄膜的性能,对实施例1~3所得产品进行力学性能、导电性及耐磨性的测试,其中结合力评级采用din-vdi3198标准判定,硬度评价采用纳米压痕(antonparr,瑞士)样品测试仪测试,电阻率采用霍尔效应测试仪测试,平均摩擦系数测试同实施例1。测试结果如表1所示。表1项目结合力等级硬度(gpa)电阻率(ω.cm)平均摩擦系数实施例1hf113.53.6×10-50.15实施例2hf112.54.5×10-50.15实施例3hf114.16.5×10-50.12从表1可知,本发明实施例所制备的导电耐磨自润滑碳基薄膜具有优异的力学性能及导电性,所述材料中的二维层状结构充分缓解了薄膜内的应力,同时有效提高了产品的减摩耐磨性。最后所应当说明的是,以上实施例仅用以说明本发明的技术方案而非对本发明保护范围的限制,尽管参照较佳实施例对本发明作了详细说明,本领域的普通技术人员应当理解,可以对本发明的技术方案进行修改或者等同替换,而不脱离本发明技术方案的实质和范围。当前第1页12