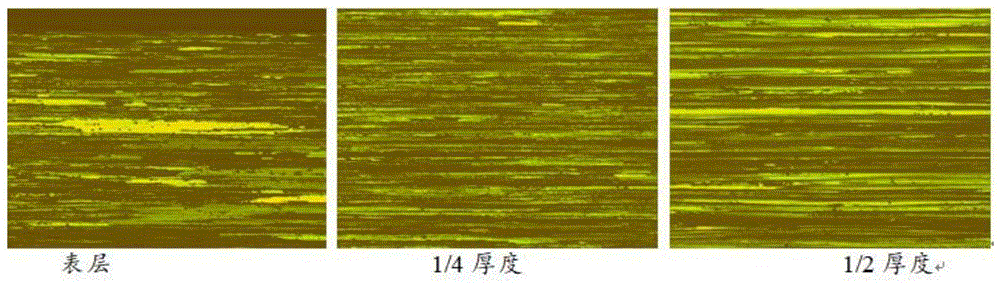
本发明属于7075合金
技术领域:
,尤其涉及一种提高7075合金厚板截面阳极氧化质量的方法。
背景技术:
:由于轧制工艺的不同,导致合金铸锭在轧制过程中晶粒变形程度、第二相破碎程度、材料变形存储能量能力等各个方面存在差异。因此,合金经后续热处理后,厚度截面容易出现不同的晶粒组织形貌,导致产品最终阳极氧化效果变差,出现色差、麻点、抛物线等缺陷。现行7075合金厚板轧制工艺窗口宽,终轧温度为390~420℃,单道次轧制变形量控制范围为5~45mm之间,乳液喷射时间及气嘴吹扫时间不定,导致产品过程控制不稳定,成品阳极氧化质量稳定性较差,无法满足用户需求。现有技术制备7075合金厚板终轧温度处于7075合金板材再结晶温度临界点;单道次轧制变形量控制范围宽,板材厚度截面变形储能分布不均匀;轧制速度快,板材冷却速度慢,乳液喷射时间不定,无法实现精确控制终轧温度的效果。技术实现要素:有鉴于此,本发明的目的在于提供一种提高7075合金厚板截面阳极氧化质量的方法,本发明提供的方法能够获得质量较好的阳极氧化效果。本发明提供了一种提高7075合金厚板截面阳极氧化质量的方法,包括:将7075合金铸锭轧制后进行固溶淬火、时效处理和阳极氧化;所述轧制过程中将终轧温度控制在≤360℃。优选的,所述终轧温度为320~360℃。优选的,所述轧制过程中的单道次轧制变形量控制范围为5~25mm。优选的,所述轧制过程中的轧制速度为70~80mm/min。优选的,所述轧制过程中全过程喷射乳液。优选的,所述轧制过程中最后2道次开启气嘴吹扫模式。优选的,所述阳极氧化的电解液为硫酸水溶液;所述阳极氧化的阳极为时效处理后的7075铝合金板材。优选的,所述阳极氧化的电流为15~25a;所述阳极氧化的电压为13~17v;所述阳极氧化的温度为18~22℃;所述阳极氧化的处理时间为21~30min。优选的,所述7075合金铸锭的成分为:0.04~0.1wt%的si;0.1~0.2wt%的fe;1.35~1.65wt%的cu;0.01~0.02wt%的mn;2.20~2.50wt%的mg;0.18~0.25wt%的cr;5.20~5.60wt%的zn;0.02~0.07wt%的ti;余量为al。优选的,所述轧制后得到的7075合金厚板的厚度≤40mm。本发明通过精确控制终轧温度及轧制工艺,使7075合金厚板成品截面获得均匀一致的晶粒组织形貌,改善产品最终的阳极氧化效果。本发明通过精确控制板材终轧温度、轧制变形量、轧制速度、轧制乳液喷射及气嘴的吹扫时机等轧制方法,获得厚度截面均匀一致的晶粒组织形貌,进而使板材最终阳极氧化效果好。本发明降低了轧制温度和轧制速度,并且有效控制了7075铝合金板材冷却时间,避免轧制温度处于再结晶温度临界点,进而避免混晶组织(再结晶组织与轧制变形组织混合)的出现,使板材最终阳极氧化效果变好。附图说明图1为本发明比较例1制备的板材成品的截面组织形貌图;图2为本发明实施例1制备的板材成品的截面组织形貌图;图3为本发明实施例2制备的板材成品的截面组织形貌图;图4为本发明实施例3制备的板材成品的截面组织形貌图;图5为本发明比较例1制备的板材成品阳极氧化的形貌图;图6为本发明实施例1制备的板材成品阳极氧化的形貌图;图7为本发明实施例2制备的板材成品阳极氧化的形貌图;图8为本发明实施例3制备的板材成品阳极氧化的形貌图;图9为本发明实施例及对比例制备的板材成品截面阳极氧化色差检测位置示意图。具体实施方式下面将对本发明实施例中的技术方案进行清楚、完整地描述,显然,所描述的实施例仅仅是本发明一部分实施例,而不是全部的实施例。基于本发明中的实施例,本领域普通技术人员经改进或润饰的所有其它实例,都属于本发明保护的范围。应理解,本发明实施例仅用于说明本发明的技术效果,而非用于限制本发明的保护范围。实施例中,所用方法如无特别说明,均为常规方法。本发明提供了一种提高7075合金厚板截面阳极氧化质量的方法,包括:将7075合金铸锭轧制后进行固溶淬火、时效处理和阳极氧化;所述轧制过程中将终轧温度控制在≤360℃。在本发明中,所述终轧温度优选为320~360℃,更优选为330~350℃,更优选为335~345℃,最优选为340℃。在本发明中,所述轧制过程中优选将单道次轧制变形量控制范围在5~25mm,更优选为20~25mm。在本发明中,所述轧制过程中优选控制轧制速度为70~80mm/min,更优选为72~78mm/min,更优选为74~76mm/min,最优选为75mm/min。在本发明中,所述轧制过程中优选全过程喷射乳液。在本发明中,所述乳液成分优选包括:基础油、抗氧化剂和乳化剂。本发明对所述乳液的来源没有特殊的限制,采用本领域技术人员熟知的轧制过程中使用的乳液即可,可由市场购买获得,如可采用奎克好富顿公司提供的6816型号的乳液产品。在本发明中,所述乳液的喷射量优选为4500~5500l/min,更优选为4800~5200l/min,最优选为5000l/min。在本发明中,所述轧制过程中优选在轧制最后2道次开启气嘴吹扫模式;所述气嘴吹扫过程中优选通过控制开关确定吹扫时机。在本发明中,所述轧制之前优选还包括:将7075合金铸锭进行加热。在本发明中,所述加热的温度优选为380~400℃,更优选为385~395℃,最优选为390℃。在本发明中,低温小变形轧制过程,由于轧制温度相对较低,导致7075合金更容易发生轧制变形,而不是动态回复或动态再结晶,此时更容易储存变形能,因此,在后续热处理(固溶淬火)过程中,变形储能释放,促进再结晶形核及长大,促进“完全”再结晶组织形成,获得单一组织。在本发明中,轧制变形量控制范围窄且相对固定(单道次控制范围5~25mm),有利于整个厚度截面的均匀变形,有利于获得均匀一致的晶粒组织形貌,因此,精确控制轧制方式,对获得均匀一致阳极氧化产品至关重要。在本发明中,轧制速度慢、乳液喷射时间长,板材冷却速度快,更好实现精确控制终轧温度的效果,获得单一组织。在本发明中,所述7075合金铸锭的成分优选为:0.04~0.1wt%的si;0.1~0.2wt%的fe;1.35~1.65wt%的cu;0.01~0.02wt%的mn;2.20~2.50wt%的mg;0.18~0.25wt%的cr;5.20~5.60wt%的zn;0.02~0.07wt%的ti;余量为al。在本发明中,所述si的质量含量优选为0.05~0.09%,更优选为0.06~0.08%,最优选为0.07%;所述fe的质量含量优选为0.12~0.18%,更优选为0.14~0.16%,最优选为0.15%;所述cu的质量含量优选为1.4~1.6%,更优选为1.5%;所述mn的质量含量优选为0.015~0.02%,更优选为0.02%;所述mg的质量含量优选为2.3~2.4%;所述cr的质量含量优选为0.2~0.23,更优选为0.21~0.22%;所述zn的质量含量优选为5.3~5.5%,更优选为5.4%;所述ti的质量含量优选为0.04~0.06%,更优选为0.05%。在本发明中,所述7075合金铸锭中的其它杂质单个优选≤0.05wt%;合计优选≤0.15wt%。在本发明中,所述轧制后得到的7075合金厚板的厚度优选≤40mm,更优选为15~40mm,更优选为20~35mm,最优选为25~30mm。在本发明中,优选将轧制后的板材冷却至室温再进行固溶淬火;所述室温的温度优选为20~30℃,更优选为25℃。在本发明中,所述固溶淬火优选在辊底炉中进行。在本发明中,所述固溶淬火的方法优选包括:将轧制后的板材加热到高温单相区恒温保持,使过剩相充分溶解到固溶体中再快速冷却,得到过饱和固溶体。在本发明中,所述固溶淬火过程中固溶的定温温度优选为470~480℃,更优选为472~478℃,更优选为474~476℃,最优选为475℃;所述固溶淬火过程中的加热系数优选为41~50,更优选为41.25~47.5,更优选为42.14~45.6,更优选为42.5~45,最优选为43.5~43.75;所述固溶淬火过程中的加热时间优选为16~66min,更优选为19~59min,更优选为22~51min,更优选为27~44min,最优选为35min;所述固溶淬火过程中的保温时间优选为31~64min,更优选为33~56min,更优选为34~48min,更优选为35~42min,最优选为38min;所述固溶淬火过程总固溶处理的总时间优选为47~130min,更优选为52~115min,更优选为56~99min,更优选为62~86min,最优选为73min。在本发明中,优选根据轧制后的板材的不同厚度采用不同的固溶淬火过程中固溶处理的工艺参数,优选按照下表进行固溶处理:在本发明中,所述固溶淬火过程中淬火处理的方式可以为软淬火处理也可以为硬淬火处理;所述淬火处理过程中的出炉淬火辊道速度优选为300~550mm/s,更优选为325~525mm/s,更优选为350~500mm/s,更优选为375~450mm/s,最优选为400mm/s;所述淬火处理过程中淬火区水刀一区优选为6~8.8l/s,更优选为7.5~8.5l/s,最优选为8l/s;二区优选为7~11l/s,更优选为10l/s;所述淬火处理过程中的喷嘴流量硬淬火时的喷嘴流量一区优选为100~110l/s,二区优选为160~180l/s,三区优选为100~110l/s,四区优选为160~180l/s;软淬火喷嘴流量一区优选为60~80l/s,更优选为70l/s,二区优选为80~100l/s,更优选为90l/s;所述淬火处理过程中的后冷却摆动时间优选为15~40s,更优选为20~35s,最优选为25~30s;所述淬火处理过程中的后冷却喷嘴流量一区优选为0.8~20l/s,更优选为15l/s,二区优选为0.8~1.2l/s,三区优选为0.8~1l/s,四区优选为0.8~1.2l/s。在本发明中,优选根据轧制后的板材的不同厚度采用不同的固溶淬火过程中淬火处理的工艺参数,优选按照下表进行淬火处理:在本发明中,所述时效处理优选在时效炉中进行;所述时效炉优选为50吨。在本发明中,所述时效处理的方法优选包括:将固溶淬火后的板材加热后保温然后出炉空冷,使过饱和固溶体分解,使基体组织稳定。在本发明中,所述加热过程中的温度优选为120~125℃;所述保温温度优选为120~130℃,更优选为122~128℃,更优选为124~126℃,最优选为125℃;所述保温时间优选为850~950min,更优选为880~920min,最优选为900min;所述时效处理过程中的金属温度优选为120~130℃,更优选为122~128℃,更优选为124~126℃,最优选为125℃。在本发明中,所述空冷优选为空冷至室温,所述室温的温度优选为20~30℃,更优选为22~28℃,更优选为24~26℃,最优选为25℃。在本发明中,所述阳极氧化的电解液优选为硫酸水溶液;所述硫酸水溶液的浓度优选为160~240g/l,更优选为180~220g/l,最优选为200g/l;所述氧化阳极过程中的阳极优选为时效处理后的7075铝合金板材;所述阳极氧化过程中的电流优选为15~25a,更优选为18~22a,最优选为20a;所述阳极氧化过程中的电压优选为13~17v,更优选为14~16v,最优选为15v;所述阳极氧化的温度优选为18~22℃,更优选为19~21℃,最优选为20℃;所述阳极氧化的处理时间优选为21~30min,更优选为22~28min,更优选为24~26min,最优选为25min;所述阳极氧化过程中的阳极规格纵向优选为20~30mm,更优选为22~28mm,更优选为24~26mm,最优选为25mm;横向优选为90~110mm,更优选为95~105mm,最优选为100mm。本发明通过控制7075合金终轧温度及轧制工艺,使板材在较低温度条件下均匀变形,此时板材厚度截面轧制变形储存的能量分布均匀,且在随后的固溶淬火过程中,由于变形储能的释放,使得板材整个厚度截面发生均匀静态再结晶转变,获得均匀一致的组织。本发明通过精确控制板材终轧温度、轧制变形量、轧制速度、轧制乳液喷射时机及气嘴的吹扫时机等轧制方法,获得厚度截面均匀一致的晶粒组织形貌,进而使板材最终阳极氧化效果好。本发明降低了轧制温度和轧制速度,并且有效控制了7075铝合金板材冷却时间,避免轧制温度处于再结晶温度临界点,进而避免混晶组织(再结晶组织与轧制变形组织混合)的出现,使板材最终阳极氧化效果变好。实施例1对加热温度为392℃的7075合金铸锭进行低温轧制,轧制过程中,单道次轧制变形量控制范围在5~20mm,轧制速度控制在2速(75mm/min),并且轧制全过程喷射乳液(奎克好富顿公司提供的6816型号的乳液产品),轧制最后2道次开启气嘴吹扫模式,吹干板材表面的乳液,同时测量板材表面的金属温度,板材终轧温度为342℃。轧制全过程采用低温、慢速轧制工艺,保证板材温度的均匀扩散。轧制后将板材冷却至室温,对冷却后的板材进行475℃/86min固溶淬火(按照上面固溶淬火两个表中设定厚度为25mm的工艺参数进行固溶淬火)、125℃/15h进行时效处理,得到厚度为25mm的铝合金板材。对铝合金板材进行阳极氧化,阳极氧化过程中的电解液为浓度为200g/l的硫酸水溶液,阳极为上述时效处理后的铝合金板材(横向为100mm,纵向为25mm,厚度为25mm),阳极氧化过程中的电流为20a,电压为15v,温度为21℃,阳极氧化的处理时间为25分钟。分别对时效态试样进行成分、金相组织、力学性能进行检测,对阳极氧化态试样形貌及板材全厚度截面色差进行检测。对本发明实施例1制备的板材(时效处理后的板材)进行成分检测,检测标准为gb/t20975《铝及铝合金化学分析方法》,本发明实施例1制备得到的板材的成分为:对本发明实施例1制备的板材(时效处理后的板材)进行截面金相组织检测,检测方法为gb/t3246.1《变形铝及铝合金制品组织检测方法第1部分:显微组织检测方法》,检测结果如图2所示,由图2可知,实施例1制备的7075合金截面不同厚度位置均呈现明显再结晶组织形貌,再结晶晶粒尺寸相差较小,分布均匀。对本发明实施例1制备的板材(时效处理后的板材)进行纵向力学性能检测,检测方法为gb/t228.1《金属材料拉伸试验第1部分:室温试验方法》,本发明实施例1制备得到的板材纵向力学性能为:屈服强度/mpa抗拉强度/mpa延伸率/%490-501560-56611.5-13.5对本发明实施例1制备的板材阳极氧化后采用目视观察法进行形貌检测,检测结果如图6所示,由图6可知,试样试验面氧化膜透明,无明显的条、点、带等发黑缺陷,且无明显的对比度及异常现象产生。对本发明实施例1制备的板材阳极氧化后进行厚度截面色差检测,检测方法为:采用ys3060高精度分光测色仪测试色差,包括明度l*以及彩度a*、b*值,色差计算公式为以截面中心为标样区域,分别检测上表面色差△e+1,中心区域色差△e0和近下表面色差△e-1,取不同区域色差的最大值△emax为样品的色差值,△emax值≤0.8为阳极氧化质量较好,△emax>0.8为阳极氧化质量较差。检测位置示意图如图9,检测结果如下:实施例2对加热温度为397℃的7075合金铸锭进行低温轧制,轧制过程中,单道次轧制变形量控制在范围在5~20mm,轧制速度控制在2速(75mm/min),并且轧制全过程喷射乳液(奎克好富顿公司提供的6816型号的乳液产品),轧制最后2道次开启气嘴吹扫模式,吹干板材表面的乳液,同时测量板材表面的金属温度,板材终轧温度为347℃。轧制全过程采用低温、慢速轧制工艺,保证板材温度的均匀扩散。轧制后将板材冷却至室温,对冷却后的板材进行475℃/86min固溶淬火(按照上面固溶淬火两个表中设定厚度为25mm的工艺参数进行固溶淬火)、125℃/15h时效处理,得到厚度为25mm的铝合金板材。按照实施例1的方法分别对时效态试样进行成分、金相组织、力学性能进行检测,对阳极氧化态试样形貌及板材全厚度截面色差检测。对铝合金板材进行阳极氧化,阳极氧化过程中的电解液为浓度为200g/l的硫酸水溶液,阳极为上述时效处理后的铝合金板材(横向为100mm,纵向为25mm,厚度为25mm),阳极氧化过程中的电流为19a,电压为15v,温度为20℃,阳极氧化的处理时间为25分钟。本发明实施例2制备得到的板材(时效处理后的板材)的成分为:对本发明实施例2制备的板材(时效处理后的板材)进行截面金相组织检测,检测结果如图3所示,由图3可知,7075合金截面不同厚度位置均呈现明显再结晶组织形貌,再结晶晶粒尺寸相差较小,分布均匀。本发明实施例2制备得到的板材(时效处理后的板材)纵向力学性能为:屈服强度/mpa抗拉强度/mpa延伸率/%488-497558-56311.0-13.5对本发明实施例2制备的板材阳极氧化后采用目视观察法进行形貌检测,检测结果如图7所示,由图7可知,试样试验面氧化膜透明,无明显的条、点、带等发黑缺陷,且无明显的对比度及异常现象产生。对本发明实施例2制备的板材阳极氧化后进行厚度截面色差检测,检测结果如下:实施例3对加热温度为395℃的7075合金铸锭进行低温轧制,轧制过程中,单道次轧制变形量控制在范围在5~20mm,轧制速度控制在2速(75mm/min),并且轧制全过程喷射乳液(奎克好富顿公司提供的6816型号的乳液产品),轧制最后2道次开启气嘴吹扫模式,吹干板材表面的乳液,同时测量板材表面的金属温度,板材终轧温度为350℃。轧制全过程采用低温、慢速轧制工艺,保证板材温度的均匀扩散。轧制后将板材冷却至室温,对冷却后的板材进行475℃/86min固溶淬火(按照上面固溶淬火两个表中设定厚度为25mm的工艺参数进行固溶淬火)、125℃/15h时效处理以及硫酸阳极氧化,得到厚度为25mm的铝合金板材。对铝合金板材进行阳极氧化,阳极氧化过程中的电解液为浓度为200g/l的硫酸水溶液,阳极为上述时效处理后的铝合金板材(横向为100mm,纵向为25mm,厚度为25mm),阳极氧化过程中的电流为23a,电压为15v,温度为20℃,阳极氧化的处理时间为25分钟。按照实施例1的方法分别对时效态试样进行成分、金相组织、力学性能进行检测,对阳极氧化态试样形貌及板材全厚度截面色差检测。本发明实施例3制备得到的板材(时效处理后的板材)的成分为:对本发明实施例3制备的板材(时效处理后的板材)进行截面金相组织检测,检测结果如图4所示,由图4可知,7075合金截面不同厚度位置均呈现明显再结晶组织形貌,再结晶晶粒尺寸相差较小,分布均匀。本发明实施例3制备得到的板材(时效处理后的板材)纵向力学性能为:屈服强度/mpa抗拉强度/mpa延伸率/%484-494553-56311.5-12.5对本发明实施例3制备的板材阳极氧化后采用目视观察法进行形貌检测,检测结果如图8所示,由图8可知,试样试验面氧化膜透明,无明显的条、点、带等发黑缺陷,且无明显的对比度及异常现象产生。对本发明实施例3制备的板材阳极氧化后进行厚度截面色差检测,检测结果如下:比较例1对加热温度为393℃的7075合金铸锭进行正常温度轧制,轧制过程中,单道次轧制变形量控制在5~45mm,轧制速度控制在3速(120mm/min),轧制全过程采用边喷乳液(奎克好富顿公司提供的6816型号的乳液产品)边吹扫的模式,轧制结束时测量板材表面的金属温度,板材终轧温度为398℃。轧制后将板材冷却至室温,对冷却后的板材进行475℃/86min固溶淬火(按照上面固溶淬火两个表中设定厚度为25mm的工艺参数进行固溶淬火)、125℃/15h进行时效处理,得到厚度为25mm的铝合金板材。对铝合金板材进行阳极氧化,阳极氧化过程中的电解液为浓度为200g/l的硫酸水溶液,阳极为上述时效处理后的铝合金板材(横向为100mm,纵向为25mm,厚度为25mm),阳极氧化过程中的电流为23a,电压为15v,温度为22℃,阳极氧化的处理时间为25分钟。按照实施例1的方法分别对时效态试样进行成分、金相组织、力学性能进行检测,对阳极氧化态试样形貌及板材全厚度截面色差检测。本发明比较例1制备得到的板材(时效处理后的板材)的成分为:对本发明比较例1制备的板材(时效处理后的板材)进行截面金相组织检测,检测结果如图1所示,由图1可知,7075合金截面不同厚度位置均呈现明显再结晶组织与轧制变形组织混合现象,再结晶晶粒尺寸相差较大,且分布不均匀。本发明比较例1制备得到的板材(时效处理后的板材)纵向力学性能为:对本发明比较例1制备的板材阳极氧化后采用目视观察法进行形貌检测,检测结果如图5所示,由图5可知,试样试验面表层出现明显的黑色点状缺陷,整个厚度截面对比度较大,色差明显,阳极氧化效果差。对本发明比较例1制备的板材阳极氧化后进行厚度截面色差检测,检测结果如下:本发明比较例1和实施例1制备的板材成品截面组织形貌如图1和图2所示,由于实施例1中低温轧制工艺的精确控制,使板材整个厚度截面阳极氧化效果明显变好。同时,轧制工艺操作简单,成品低廉,无三废排放,有利于对环境的保护。本发明通过精确控制板材终轧温度、轧制变形量、轧制速度、轧制乳液喷射时机及气嘴的吹扫时机等轧制方法,获得厚度截面均匀一致的晶粒组织形貌,进而使板材最终阳极氧化效果好。本发明降低了轧制温度和轧制速度,并且有效控制了7075铝合金板材冷却时间,避免轧制温度处于再结晶温度临界点,进而避免混晶组织(再结晶组织与轧制变形组织混合)的出现,使板材最终阳极氧化效果变好。以上所述的仅是本发明的优选实施方式,应当指出,对于本
技术领域:
的普通技术人员来说,在不脱离本发明原理的前提下,还可以做出若干改进和润饰,这些改进和润饰也应视为本发明的保护范围。当前第1页12