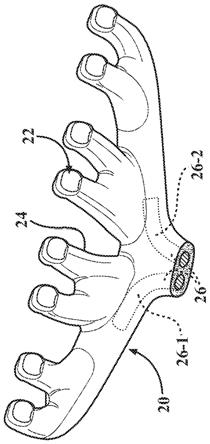
1.本公开涉及一种用于制造铸造部件的混合型芯。
背景技术:2.铸造是一种制造工艺,其中液体材料通常被浇注到包含期望形状的中空型腔的模具中,且然后被允许凝固。凝固的零件也被称为铸件,其从模具被弹出或破裂出来以完成工艺。铸造通常被用于制造以其它方式难以或无法经济地制造的复杂形状。砂型铸造(又被称为砂型模具铸造)是以使用砂子作为模具材料为特征的金属铸造工艺。术语“砂型铸件”也可以指通过砂型铸造工艺生产的物体。
3.某些笨重的设备,如机床床身、船舶推进器、内燃发动机部件(诸如缸盖、发动机缸体和排气歧管)等,可能更容易铸造成所需的大小,而不是通过联结几个小件来制造。通常通过在模型(称为模样(pattern))周围压实砂子、通过直接在砂子上雕刻或通过3d打印来产生模具型腔和浇口系统。模具包括流道和冒口,其通过充当贮存器来馈给铸件凝固时的收缩,从而使得熔融金属能够填充模具型腔。在铸造工艺期间,金属首先被加热直到其变成液体,且然后在经过一定的熔体处理(诸如脱气、添加晶粒细化剂和调整合金元素含量)之后被浇注到模具中。在从液体金属吸热之后,模具逐渐升温。因此,熔融金属被持续冷却,直到其凝固。在凝固零件(铸件)被取出模具且随后落砂之后,去除铸件(诸如流道和冒口)中的过量材料。
4.型芯通常被用于具有内部型腔和凹角(即内角大于180度)的砂型铸造部件。例如,型芯被用于限定发动机缸体、缸盖和排气歧管中的多个通道。型芯通常是由诸如砂子、粘土、煤和树脂的材料构成的一次性物品。型芯材料通常具有:足够的强度以便在生料状态下被搬运,且尤其是在压缩状态下被搬运,以便承受铸件的力,例如材料重量;足够的渗透性以允许气体逸出;良好的耐火性以承受铸造温度。因为型芯在从凝固铸件移除之后通常被毁坏,所以型芯材料通常被选择成允许型芯在落砂期间被破坏。型芯材料通常被回收。
技术实现要素:5.一种用于制造铸造部件的混合型芯,混合型芯包括砂芯部分,该砂芯部分具有外部形状,该外部形状配置成限定铸造部件的内部特征件。混合型芯还包括嵌入在砂芯部分内的金属冷却元件(metal chill element)。金属冷却元件配置成在铸造部件的冷却和其凝固期间从铸造部件局部地吸收热能。金属冷却元件被构造和布置在砂芯部分内,以在铸造部件凝固之后在落砂期间从铸造部件移除。
6.金属冷却元件可以具有实心横截面。
7.替代性地,金属冷却元件可以具有中空横截面,或者具有变化的横截面,其中一个截面是中空的,而另一个是实心的。
8.金属冷却元件可以具有整体式构造或单件式构造。
9.替代性地,金属冷却元件可以包括多件式构造,该多件式构造配置成促进在落砂
期间从铸造部件移除金属冷却元件。
10.具有多件式构造的金属冷却元件可以包括与金属冷却元件的第二件互连的金属冷却元件的第一件。
11.金属冷却元件可以通过外部表面限定。在这种实施例中,金属冷却元件可以包括在外部表面上的涂层,该涂层定位成接触铸造部件,并且配置成使金属冷却元件对铸造部件的内部特征件的粘附最小化。涂层旨在不限制从铸造部件到金属元件的热传递。
12.涂层可以包括陶瓷、氮化物、硅和钛中的至少一种。
13.涂层可以具有在50纳米至5微米的范围内的厚度。
14.金属冷却元件可以具有外部形状,该外部形状配置成遵循铸造部件的内部特征件的形状或几何结构。
15.还公开了一种系统和一种方法,用于使用这种混合型芯制造铸造部件。
16.本发明还提供了以下方案:方案1.一种用于制造铸造部件的混合型芯,所述混合型芯包括:砂芯部分,所述砂芯部分具有外部形状,所述外部形状被配置为限定所述铸造部件的内部特征件;以及金属冷却元件,所述金属冷却元件嵌入在所述砂芯部分内,并且配置成在所述铸造部件的冷却和其凝固期间局部地吸收来自所述铸造部件的热能,并且所述金属冷却元件构造和布置在所述砂芯部分内,以在所述铸造部件凝固之后在落砂期间从所述铸造部件移除。
17.方案2.根据方案1所述的混合型芯,其中,所述金属冷却元件具有实心横截面。
18.方案3.根据方案1所述的混合型芯,其中,所述金属冷却元件具有中空横截面。
19.方案4.根据方案1所述的混合型芯,其中,所述金属冷却元件具有单件式构造。
20.方案5.根据方案1所述的混合型芯,其中,所述金属冷却元件包括多件式构造,所述多件式构造配置成促进在落砂期间从所述铸造部件移除所述金属冷却元件。
21.方案6.根据方案5所述的混合型芯,其中,具有所述多件式构造的所述金属冷却元件包括与所述金属冷却元件的第二件互连的所述金属冷却元件的第一件。
22.方案7.根据方案1所述的混合型芯,其中,所述金属冷却元件由外部表面限定,并且其中,所述金属冷却元件包括在所述外部表面上的涂层,所述涂层定位成接触所述铸造部件并且配置成使所述金属冷却元件对所述铸造部件的内部特征件的粘附最小化。
23.方案8.根据方案7所述的混合型芯,其中,所述涂层包括陶瓷、氮化物、硅和钛中的至少一种。
24.方案9.根据方案7所述的混合型芯,其中,所述涂层具有在50纳米至5微米的范围内的厚度。
25.方案10.根据方案1所述的混合型芯,其中,所述金属冷却元件具有外部形状,所述外部形状配置成遵循所述铸造部件的内部特征件的形状。
26.方案11.一种用于制造铸造部件的系统,所述系统包括:模具,所述模具具有第一半部和第二半部,所述第一半部和所述第二半部限定内部型腔,所述内部型腔配置成形成所述铸造部件的外部形状;混合型芯,所述混合型芯布置在所述模具的内部型腔内,并且配置成限定所述铸
造部件的内部特征件,所述混合型芯包括:砂芯部分,所述砂芯部分具有外部形状,所述外部形状被配置为限定所述铸造部件的内部特征件;以及金属冷却元件,所述金属冷却元件嵌入在所述砂芯部分内,并且配置成在所述铸造部件的冷却和其凝固期间局部地吸收来自所述铸造部件的热能,并且所述金属冷却元件构造和布置在所述砂芯部分内,以在所述铸造部件凝固之后在落砂期间从所述铸造部件移除;以及机构,所述机构用于将熔融材料引入到所述型腔中以形成所述铸造部件,使得所述熔融材料流动到所述型腔中并且围绕所述混合型芯以形成所述铸造部件的外部形状和内部特征件。
27.方案12.根据方案11所述的系统,其中,所述金属冷却元件具有实心横截面。
28.方案13.根据方案11所述的系统,其中,所述金属冷却元件具有中空横截面。
29.方案14.根据方案11所述的系统,其中,所述金属冷却元件具有单件式构造。
30.方案15.根据方案11所述的系统,其中,所述金属冷却元件包括多件式构造,所述多件式构造配置成促进在落砂期间从所述铸造部件移除所述金属冷却元件。
31.方案16、根据方案15所述的系统,其中,具有所述多件式构造的所述金属冷却元件包括与所述金属冷却元件的第二件互连的所述金属冷却元件的第一件。
32.方案17.根据方案11所述的系统,其中,所述金属冷却元件由外部表面限定,并且其中,所述金属冷却元件包括在所述外部表面上的涂层,所述涂层定位成接触所述铸造部件并且配置成使所述金属冷却元件对所述铸造部件的内部特征件的粘附最小化。
33.方案18.根据方案17所述的系统,其中,所述涂层包括陶瓷、氮化物、硅和钛中的至少一种。
34.方案19.根据方案17所述的系统,其中,所述涂层具有在50纳米至5微米的范围内的厚度。
35.方案20.根据方案11所述的系统,其中,所述金属冷却元件具有外部形状,所述外部形状配置成遵循所述铸造部件的内部特征件的形状。
36.当结合附图和所附权利要求获得时,从用于执行所述公开的实施例和最佳模式的以下详细描述,本公开的上述特征和优点以及其它特征和优点将变得容易明白。
附图说明
37.图1是根据本公开的具有内部特征件的铸造部件的实施例的示意性局部视图,该内部特征件通常借助于铸造型芯形成。
38.图2是根据本公开的混合铸造型芯的实施例的示意性俯视立体局部剖视图,该混合铸造型芯具有嵌入在砂芯部分内用于制造图1中所示的铸造部件的内部特征件的金属冷却元件。
39.图3是根据本公开的混合铸造型芯的另一实施例的示意性俯视立体局部剖视图,该混合铸造型芯具有嵌入在砂芯部分内的金属冷却元件。
40.图4是图2中所示的混合型芯的示意性俯视立体局部图。
41.图5是根据本公开的具有涂层的金属冷却元件的实施例的示意性横截面正视图。
42.图6是根据本公开的金属冷却元件的另一实施例的示意性横截面正视图。
43.图7是根据本公开的金属冷却元件的另一实施例的示意性横截面纵向图。
44.图8是根据本公开的金属冷却元件的另一实施例的示意性横截面纵向图。
45.图9是根据本公开的金属冷却元件的互连多件式实施例的示意性横截面正视图。
46.图10是根据本公开的制备混合型芯的方法的流程图,该混合型芯在图2-9中所示,用于产生铸造部件。
47.图11是根据本公开的用于制造在图1中所示的铸造部件的系统的示意图,系统包括在图2-9中所示的混合型芯。
具体实施方式
48.诸如“上面”、“下面”、“向上”、“向下”、“顶部”、“底部”等等的术语在本公开中被用于描述附图并且不代表对由所附权利要求限定的本公开的范围的限制。
49.参考图1,描绘了铸造部件10。铸造部件10具体地是“砂型铸件”,也被称为砂型模具铸件。大体而言,砂型铸件是通过使用砂子作为模具材料产生的金属铸件。铸造部件10可以是具有集成排气歧管的缸盖(图1中所示),其诸如用于内燃汽油发动机或者柴油发动机(未示出)。铸造部件10的单独的实施例可以被配置成机器、工业设备等的另一零件。
50.如图1的每个中所示,铸造部件10包括内部特征件12,诸如内部型腔、凹角(大于180度的内角)或者在铸造工艺期间通过使用型芯形成的通道。在铸造部件10的具体缸盖实施例中,内部特征件12被具体描绘为会合到排气收集器中的集成排气歧管的排气通道或流道。大体而言,型芯是由具体选择成允许在其在模具中凝固后将主题型芯从铸造部件10移除的材料构成的一次性物品。在铸造工艺期间,熔融金属通常以一定速率凝固,该速率取决于模具的设计和型芯的导热性。
51.大体而言,凝固速率越快,则铸造材料微观结构越精细且铸件的机械性能越高。通常,砂芯具有低的导热性并且影响在完成的铸件中的粗糙的材料微观结构和低的材料性能。例如,当铸造部件(如缸盖)经受发动机耐久性测试或道路使用时,由于特定区域承受较高的热应力和机械应力,在使用砂芯的情况下的在排气歧管壁14周围的铸造部件10的凝固期间的低冷却速率会导致裂纹16(如图1中所示)。如下文具体描述的,可以想到各种配置的混合型芯以便增加液体金属的局部凝固速率并增强铸造部件10的局部材料性能。
52.通常通过将芯砂引入到被具体配置的芯箱(例如半芯箱、堆芯箱、分芯箱和成组芯箱)中来生产砂芯。可向芯砂添加粘合剂,以增强型芯强度。干的砂芯通常在堆芯箱中生产,其中砂子被装入箱中并且被刮平至与箱的顶部齐平。通常由木头或金属配置的板被放置在箱上方,并且之后在板就位的情况下箱被翻转,以致形成的型芯部段可以从芯箱掉出。形成的型芯部段之后被烘烤或以其它方式硬化。对于复杂形状型芯,多个型芯部段可以被热胶粘在一起或使用其它附接方法被联结。
53.简单形状单件式砂芯也可以在分芯箱中被生产。典型的分芯箱由两个半部制成并且具有至少一个孔以用于引入用型芯的砂子。可以通使用专门配置的型芯生产挤出机来产生具有恒定横截面的型芯。之后得到的挤出件被切割成恰当的长度并被硬化。具有更复杂形状的单件式型芯可以以类似于注塑成型和压铸的方式被制造。在提取和组装(如有必要)型芯部段后,可以锉或打磨得到的型芯的表面上的粗糙点。最后,型芯被轻轻涂覆有石墨、
二氧化硅或云母,以赋予型芯更光滑的表面精整度和更好的耐热性。
54.在图2至图4中以各种配置示出的混合型芯20被配置成解决诸如在靠近壁14处的铸造部件10的与热应力有关的裂纹16。具体地,混合型芯20旨在根据需要提高局部凝固速率并增强完成的铸造部件10的局部材料性能。混合型芯20特别被配置成用于制造铸造部件10,并且更特别地用于形成内部特征件12。混合型芯20包括砂芯部分22。砂芯部分22具有外部形状24,该外部形状24配置成限定铸造部件10的内部特征件12。混合型芯20还包括嵌入在砂芯部分22内的金属冷却元件26。金属冷却元件26配置成在铸造部件10的冷却和其凝固期间从熔融金属局部吸收热能。可以通过使砂芯部分22围绕下文中公开的金属冷却元件26的实施例之一在芯箱中形成而产生混合型芯20。
55.通常,金属冷却元件26材料的熔化温度应当高于用于实际铸件的材料的熔化温度。例如,对于由铝制造的铸造部件,选择用于金属冷却元件26的材料可以是铜、青铜、铸铁或工具钢(不锈钢)。主要由于其高导热性和耐用性而采用这样的金属冷却元件材料。然而,对于铝铸件,当与陶瓷涂层一起使用时,铝(其熔点约为660摄氏度)也可用作金属冷却元件的材料。涂层的另一种选择是喷涂醇基石墨涂层。这种喷涂涂层可包括石墨片/颗粒(60%至70%)、有机膨润土(2-3%)、有机粘合剂(1-2%)、无机粘合剂(1.5-2.5%)、聚乙烯醇缩丁醛(pvb,0.2-0.5%)、添加剂(2-5%)和剩余的基于无水乙醇与其它醇溶剂的混合物。
56.金属冷却元件26成形为使得其可以完全嵌入砂芯部分22内并从而被其覆盖,或者部分嵌入砂芯部分内,因此被部分暴露。金属冷却元件26作为混合型芯20的一部分布置在模具内,以用于在铸造工艺期间冷却熔融金属并因此控制靠近内部特征件12的铸造部件10的凝固速率。通过从熔融金属吸收热能,金属冷却元件26旨在产生铸造材料的更精细的微观结构,并产生铸造部件10在操作中的改善的机械性能。这种改善的机械性能将继而使铸造部件10开裂的可能性最小化。例如,在制造铝铸件时,金属冷却元件26旨在增强铸件的局部冷却,且从而减小铸铝材料的枝晶臂间距(das),这将改善铸造部件10在内部特征件12周围的区域中的强度。
57.金属冷却元件26被附加成形,使得在铸造部件10凝固之后,可以在落砂期间从铸造部件10将金属冷却元件26移除。特别重要的是,在不损坏或以其它方式破坏所形成的铸造部件10的结构的情况下,移除混合型芯20,通过将金属冷却元件26布置在砂芯部分22内而促进这一点。具体地,砂芯部分22可首先在凝固的铸造部件10内破裂,这继而将允许在落砂期间将金属冷却元件26从铸造部件中拉出来。
58.如图5中以横截面图5-5所示,金属冷却元件26可具有实心横截面28a。替代性地,如图6中以横截面图6-6所示,金属冷却元件26可具有中空横截面28b。中空截面28b可以沿着金属冷却元件26的轴线x具有变化的厚度(如图7中以横截面图7-7所示)。附加地,金属冷却元件26可以具有组合或混合的配置。其中,一部分28a的横截面是实心的,并且另一部分28b的横截面是中空的(如在图8中以横截面图8-8所示)。如在图2和图4中所示,金属冷却元件26可以具有整体式构造或单件式构造。在图4中所示的金属冷却元件26的配置可以例如通过铸造或从实心件机械加工来产生。通常,金属冷却元件26可以通过机械加工、铸造、使用专门配置的型芯生产挤出机或经由3d打印工艺来产生。
59.替代性地,如在图3中所示,金属冷却元件26可包括多件式构造,例如,具有单独的、拆分的和非接触的相应的第一部段26-1和第二部段26-2。图3中所示的金属冷却元件26
具体地包括不接触的第一部段26-1和第二部段26-2,以促进在落砂期间从铸造部件10移除金属冷却元件。如图9中以横截面图9-9所示的,金属冷却元件26可以具有与第二部段26-2互连的第一部段26-1,即,两个件彼此接触。例如,第一部段26-1和第二部段26-2可以通过经由互补的凸部和凹部配合在一起而互连或互锁。当冷却元件位于砂芯部分22内时,金属冷却元件26的这种配置可以用于精确地建立和维持在相应单独的第一部段26-1和第二部段26-2之间的间距。
60.如在图4中所示,金属冷却元件26可以由外部表面30限定。金属冷却元件26的外部表面30通常可以形成为使得由此限定的外部形状30a配置成内部遵循砂芯部分22的外部形状22a,其用于形成由铸造部件10的内部特征件12限定的形状12a。然而,金属冷却元件26的一些部分可以突出超过砂芯部分22。在铸造工艺期间,金属冷却元件26的这种突出部分可以与内部特征件12或铸造部件10的其它区域直接接触。为了解决这种可能性,金属冷却元件26可以包括施加到其外部表面30的涂层32(如图5中以横截面图5-5所示)。
61.涂层32具体旨在在金属冷却元件与内部特征件12之间的直接接触区域中最小化金属冷却元件26对砂芯部分22的可能粘附,并最小化金属冷却元件26对铸造部件10的粘附。将附加选择涂层32以对热能从铸造部件10到金属冷却元件26的传递具有最小的影响,即不限制该传递。涂层32可以作为可喷涂的模具涂料施加。模具涂料的具体成分可以是:~30%的水、~10%的可溶性矿物油、~10%的煤油、~40%的二氧化硅粉以及~10%的陶瓷粉末。为了限制涂层32对热传递的影响,涂层的成分可以包括:陶瓷、氮化物、硅和钛中的至少一种,例如,根据非限制列表,陶瓷铝化物、氮化物-铝化物(nitride-aluminide)以及铝化钛、氮化硅、碳化硅、类金刚石涂层、氮化硼和氧化铈。为了进一步限制其对热传递的影响,取决于在涂料中使用的二氧化硅粉和陶瓷粉末的大小,涂层32的厚度的范围可以在50纳米(nm)至5微米(μm)的范围内。
62.在图10中示出并且在下文参考在图2-9中所示的混合型芯的结构描述了制备用于产生铸造部件10的混合型芯20方法100。方法100在框102中开始,其中通过上文中公开的方法之一来产生金属冷却元件26的实施例。在框102之后,该方法可以前进到框104。在框104中,该方法包括将涂层32施加到金属冷却元件26的外部表面30。在框102或框104之后,该方法将继续进行到框106。在框106中,该方法包括将所形成的金属冷却元件26布置在芯箱中。在框106中,如果适合于混合型芯20的具体实施例,则该方法可以具体地包括金属冷却元件26的单独的第一部段26-1和第二部段26-2的布置或组装。
63.该方法从框106继续进行至框108。在框108中,该方法包括将芯砂引入并压实到芯箱中,直到芯箱装满为止,例如,砂子与芯箱的顶部齐平。在框108之后,该方法继续至框110。在框110中,该方法包括从芯箱取出所形成的混合型芯20。在框110之后,该方法可以继续至框112。在框112中,该方法可以包括诸如通过在200至250摄氏度的范围内的温度下在炉中烘烤来硬化所形成的混合型芯20。替代性地,如果使用自硬化砂(其中通常将两种或更多种粘合剂成分与砂子混合),则砂子将在室温下固化并自硬化。
64.在框112之后,该方法可以前进到框114。在框114中,该方法包括组装单独的混合型芯20部段(如果适用于该型芯的具体实施例),以及平滑混合型芯的外部表面,例如锉或打磨。附加地,在框114中,该方法可包括利用合适的复合物,诸如石墨、二氧化硅或云母涂覆混合型芯20的外部表面,以赋予混合型芯更光滑的表面精整度和更好的耐热性。该方法
可以在框110-114中的一个之后的框116中结束,在框116中包装或存储混合型芯20以准备将其放置在模具中以用于随后产生铸造部件10。
65.在图11中示出并且参考在图10中所示的方法100和在图2-9中所示的混合型芯20的结构描述了用于制造铸造部件10的系统200。如出于示例性目的所示的,铸造部件10可以是铝缸盖,其限定了铸入式集成排气歧管。系统200具体地包括模具202以及浇注系统(未示出),该模具202具有第一或上半部202-1和第二或下半部202-2。模具202的第一半部202-1和第二半部202-2一起限定了内部型腔204。内部型腔204配置成形成铸造部件10的外部形状10a。可以通过在模样周围压实生砂或化学结合的砂、直接在砂中雕刻或通过3d打印来创建内部型腔204和浇口系统。
66.系统200还包括混合型芯20,如上文关于图2-9所描述地。混合型芯20被布置在内部型腔204内,并且配置成限定铸造部件10的内部特征件12,诸如集成排气歧管的排气通道。系统200还采用机构206,以用于将诸如铝的熔融金属208引入型腔204中,以由此形成铸造部件10。机构206可以包括流量阀210以及流道和冒口的系统(未示出),其中流量阀可操作地连接至模具202以用于供应熔融金属208。流量阀210的操作可以经由电子控制器(未示出)来调节。电子控制器可以被编程为以预定材料流动速率将具体量的熔融金属208分配到模具202中,以确保型腔204的适当填充。
67.当经由机构206引入时,熔融金属208流入型腔204中并围绕混合型芯20形成铸造部件10的外部形状10a和内部特征件12。混合型芯20以及具体地金属冷却元件26控制内部特征件12周围的熔融金属208的凝固,以增强所制造的铸造部件10在内部特征件周围的区域中的机械性能。允许熔融金属208冷却和凝固,之后,将铸造部件10从模具移除。如上文所述,在型芯落砂工艺期间,从凝固的铸造部件10移除混合型芯20。其中,砂芯部分22的破裂有助于从铸件取出金属冷却元件26。
68.具体描述和附图或图支持并描述本公开,但是本公开的范围仅由权利要求限定。虽然用于执行所要求保护的本公开的最佳模式中的一些和其它实施例已经被具体描述,不过存在各种替代性设计和实施例来实践所附权利要求中限定的本公开。此外,附图中所示的实施例或本说明书中提及的各种实施例的特征不一定被理解为彼此独立的实施例。而是,在实施例的示例中的一个中描述的每个特征可以与来自其它实施例的一个或多个其它期望特征组合,从而导致未以文字或通过参考附图描述的其它实施例。因此,这样的其它实施例落入所附权利要求的范围的框架内。