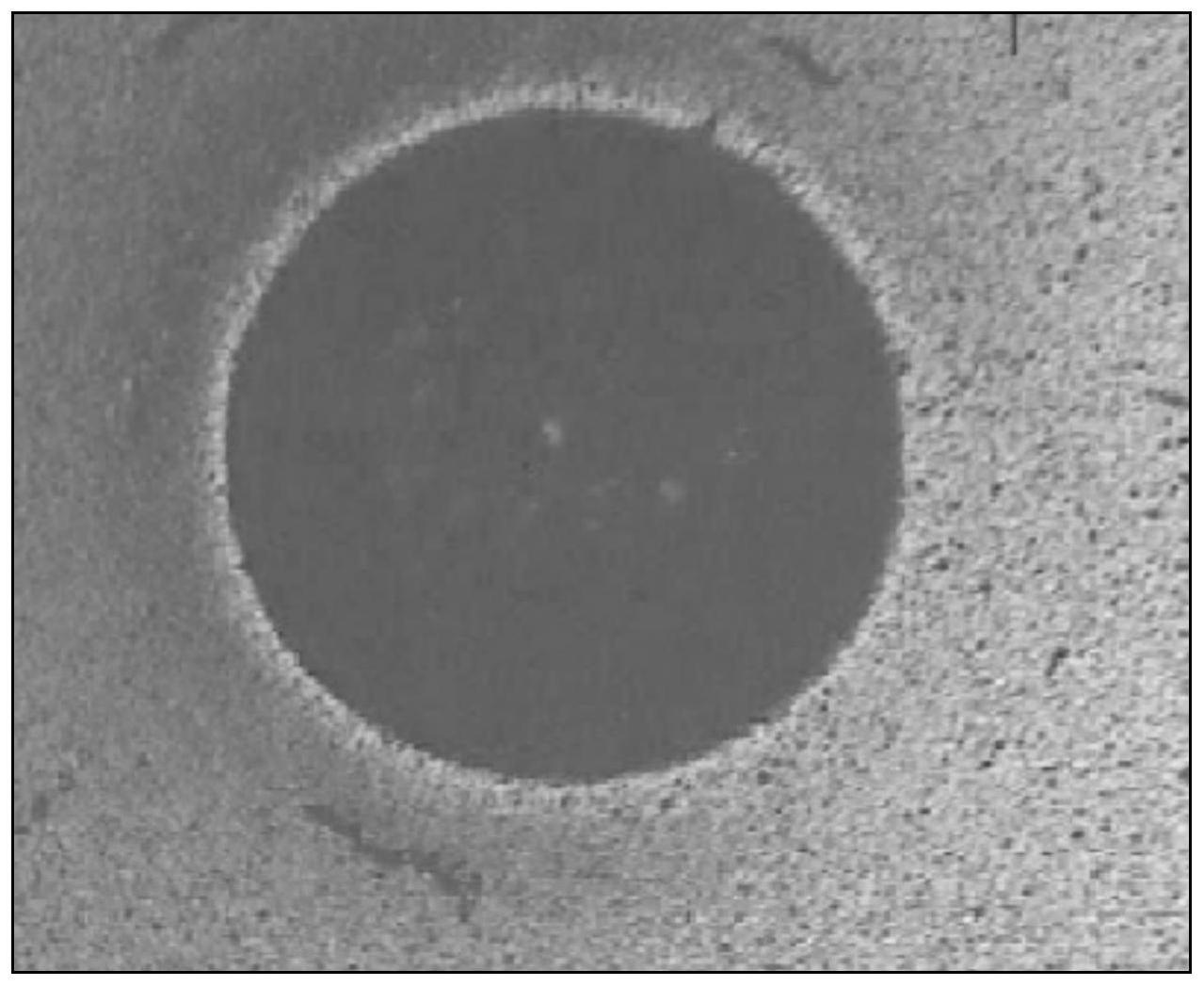
1.本技术涉及硬质涂层领域,更具体地说,它涉及一种高附着力纳米刀具涂层及其制备方法。
背景技术:2.一般而言,在硬质涂层体系中,涂层与基体材料各不相同,在涂层的沉积过程中,涂层材料一般通过化学键、分子间作用力、机械咬合等方式沉积在基体表面。层
‑
基材料的相互作用表现为附着,将层
‑
基剥离所需要的力或者能量被称为结合力或者结合强度。由于涂层和基体之间的层
‑
基界面是涂层与基体连接的纽带,不仅起到传递涂层受到的外界载荷的作用,还要承受涂层内部的应力应变。所以层
‑
基界面结合的质量对涂层的质量和寿命影响较大。
3.现有技术可参考公开号为cn102517539a的中国发明专利,公开了一种提高硬质涂层(薄膜)与基体界面结合强度的方法,该方法将硬质涂层/基体复合体系于
‑
50℃
‑‑
273℃的低温或超低温下处理5
‑
48小时实现。硬质涂层包括tin、crn、tialn、tisin、craltin、bn等氮化物涂层、金刚石、类金刚石等c涂层及tic、wc等碳化物涂层。应用本发明方法,可使涂层/基体界面结合强度提高10%
‑
50%,还可避免采用传统的高温退火方法时,基体或涂层本身性能的劣化;同时,低温或超低温处理成本低,适用的涂层/基体复合体系种类广泛。
4.针对上述中的相关技术,申请人认为现有的刀具的硬质涂层基体表面结构性能不佳,难以形成连续的覆盖层,不仅影响涂层的力学性能,也会影响涂层的结合强度,从而降低了纳米刀具涂层的抗脱落性能。
技术实现要素:5.为了克服现有纳米刀具涂层与基体之间结合强度不佳的缺陷,本技术提供了一种高附着力纳米刀具涂层及其制备方法,采用如下的技术方案:第一方面,本技术提供一种高附着力纳米刀具涂层,所述高附着力纳米刀具涂层包括从内向外依次包覆在经基体改性后刀具表面的crn界面层、altin中间层、altin/tisin连接层和tisin包覆层,所述crn界面层、altin中间层、altin/tisin连接层和tisin包覆层均采用沉积包覆的方案进行制备。
6.通过采用上述技术方案,由于本技术采用了多层硬质包覆层依次沉积的技术方案,通过多层包覆的设置,一方面,能通过多层包覆的结构,满足硬质涂层设置的多种需要,同时,多层结构的硬质涂层,相对于单层结构的硬质涂层来说,能有效改善硬质涂层结构强度,在此基础上,本技术优化了刀具材料的表面结构,通过对其表面结构进行改性处理,能有效对基体表面去除粉尘颗粒的同时,降低其粗糙度,从而提高涂层与基体的勾连嵌合作用,促进粒子成核、提高膜层质量增强其结合强度,从而有效提高了硬质涂层在刀具表面的附着性能和抗脱落性能。
7.进一步地,所述基体改性包括打砂前处理和抛光后处理,所述基体改性步骤包括:
(1)打砂前处理:取需处理的刀具材料,洗净后打砂处理,调整打砂粒度为#600;(2)抛光后处理:待打磨完成后,再对其抛光处理,控制抛光压力为10~20kpa,抛光浆料流速为125ml/min,待抛光完成后,即可完成所述基体改性。
8.通过采用上述技术方案,由于本技术采用打砂前处理和抛光后处理的方案,对刀具表面进行表面处理,其中,打砂前处理的操作步骤,通过砂粒磨料对刀具表面的冲击和切削作用使得工件表面获得一定的清洁度,改善了工件表面的机械性能,增加了工件表面和涂层之间的附着力,提升硬质涂层的耐久性,在此基础上,再进行抛光处理,由于打砂前处理形成的涂层虽然降低了粗糙度,但是形成细微的粗糙表面的结构是不规律的,本技术技术方案采用抛光处理,降低表面结构的粗糙度的同时,重点改善刀具的表面结构,从而有效提高了硬质涂层在刀具表面的附着性能和抗脱落性能。
9.进一步地,所述打砂处理为,在打砂压力0.4mpa~0.6mpa,打砂距离100~120mm,打砂角度25
°
~35
°
下打砂处理。
10.通过采用上述技术方案,由于本技术优化了打砂的压力和角度,使打砂处理后的刀具表面的氧化层和杂质有效去除,同时经过打砂后的刀具表面的活性进一步提高,改善了刀具表面的压应力,从而有效提高了硬质涂层在刀具表面的附着性能和抗脱落性能。
11.进一步地,所述打砂处理采用的打砂沙粒包括白刚玉、棕刚玉以及锆刚玉中的一种或多种的混合物。
12.通过采用上述技术方案,由于本技术优化了打砂的材料,通过选用上述材料或者多种材料的混合物,来对不同组分的刀具能的不同需求进行调整,其目的最终还是通过打砂改善刀具表面的粗糙度,从而进一步提高了硬质涂层在刀具表面的附着性能和抗脱落性能。
13.进一步地,步骤(2)所述抛光浆料包括下列重量份物质组成:50~60份水、10~15份纳米硅溶胶和6~8份氧化铝颗粒。
14.通过采用上述技术方案,由于本技术优化了抛光浆料的组成成分的同时,调整了各组分的配比,通过硅溶胶作分散介质的抛光浆料,提高了抛光处理过程中对刀具表面的抛光均匀性能,同时由于分散介质中的硅溶胶也具有良好的结构性能,改善抛光浆液的稳定性能,从而进一步提高了硬质涂层在刀具表面的附着性能和抗脱落性能。
15.进一步地,所述抛光浆液还包括3~5重量份的质量分数1%氢氧化钠溶液。
16.通过采用上述技术方案,由于本技术对抛光浆液的组成进一步限定,通过优化抛光浆液的组成,改变其ph值,由于在碱性条件下,ph值能有效改善抛光液中氧化铝颗粒的zeta电位,从而改善了抛光浆液的稳定性能,使其在实际使用中,提高了抛光处理过程中对刀具表面的抛光均匀性能,从而进一步提高了硬质涂层在刀具表面的附着性能和抗脱落性能。
17.进一步地,所述tisin包覆层按原子质量比,包括6~8%的si、37~39%的ti和52~58%的n。
18.通过采用上述技术方案,由于本技术在涂层结构中添加si元素,而si元素的添加能显著提高涂层材料的硬度和抗高温性能,从而在实际使用过程中,改善刀具涂层的耐高温性能和强度。
19.进一步地,所述altin/tisin连接层厚度为1~3μm。
20.通过采用上述技术方案,由于本技术优化了刀具涂层的尺寸和原料的组成,通过altin/tisin连接层填充在多层涂层的结构之间,形成良好的负载和支撑作用,使该涂层在外力作用下,能有效防止刀具表面与涂层之间的结合强度,改善了整体涂层的结构性能,从而进一步提高了硬质涂层在刀具表面的附着性能和抗脱落性能。
21.第二方面,本技术提供一种高附着力纳米刀具涂层的制备方法,所述高附着力纳米刀具涂层的制备步骤为:s1、取基体改性刀具并置于沉积真空室中,升温减压后,再在氮气气氛下,对基体改性刀具进行活化处理;s2、待刀具活化完成后,依次在刀具表面以cr为靶材、alti为靶材、tisi/alti为靶材和tisi为靶材,依次沉积包覆crn界面层、altin中间层、altin/tisin连接层和tisin包覆层,待沉积完成后,即可制备得所述高附着力纳米刀具涂层。
22.通过采用上述技术方案,由于本技术通过对刀具表面材料的改性处理,一方面改善了刀具表面材料与涂层之间的结合强度,提高了刀具表面材料的抗脱落性能,另一方面,本技术采用多层结构沉积的方案,有效改善涂层的组成结构,优化了涂层的配比,从而有效降低涂层结构应力,从而进一步提高了硬质涂层在刀具表面的附着性能和抗脱落性能。
23.综上所述,本技术包括以下至少一种有益技术效果:第一、本技术采用了多层硬质包覆层依次沉积的技术方案,通过多层包覆的设置,一方面,能通过多层包覆的结构,满足硬质涂层设置的多种需要,同时,多层结构的硬质涂层,相对于单层结构的硬质涂层来说,能有效改善硬质涂层结构强度,在此基础上,本技术优化了刀具材料的表面结构,通过对其表面结构进行改性处理,能有效对基体表面去除粉尘颗粒的同时,降低其粗糙度,从而提高涂层与基体的勾连嵌合作用,促进粒子成核、提高膜层质量增强其结合强度,从而有效提高了硬质涂层在刀具表面的附着性能和抗脱落性能。
24.第二、本技术采用打砂前处理和抛光后处理的方案,对刀具表面进行表面处理,其中,打砂前处理的操作步骤,通过砂粒磨料对刀具表面的冲击和切削作用使得工件表面获得一定的清洁度,改善了工件表面的机械性能,增加了工件表面和涂层之间的附着力,提升硬质涂层的耐久性,在此基础上,再进行抛光处理,由于打砂前处理形成的涂层虽然降低了粗糙度,但是形成细微的粗糙表面的结构是不规律的,本技术技术方案采用抛光处理,降低表面结构的粗糙度的同时,重点改善刀具的表面结构,从而有效提高了硬质涂层在刀具表面的附着性能和抗脱落性能。
25.第三、本技术优化了抛光浆料的组成成分的同时,调整了各组分的配比,通过硅溶胶作分散介质的抛光浆料,提高了抛光处理过程中对刀具表面的抛光均匀性能,同时由于分散介质中的硅溶胶也具有良好的结构性能,改善抛光浆液的稳定性能,从而进一步提高了硬质涂层在刀具表面的附着性能和抗脱落性能。
附图说明
26.图1是本技术实施例1样品的一种高附着力纳米刀具涂层的压痕形貌图;图2是本技术对比例1样品的一种高附着力纳米刀具涂层的压痕形貌图;图3是本技术对比例2样品的一种高附着力纳米刀具涂层的压痕形貌图;图4是本技术对比例3样品的一种高附着力纳米刀具涂层的压痕形貌图;
图5是本技术对比例4样品的一种高附着力纳米刀具涂层的压痕形貌图;图6是本技术对比实施例1样品的一种高附着力纳米刀具涂层的压痕形貌图。
具体实施方式
27.以下结合实施例对本技术作进一步详细说明。
28.本技术实施例中,所用的仪器设备和原料辅料如下所示,但不以此为限:机器:hv
‑
1000 型显微硬度计、高倍扫描电镜、蔡司的smartzoom5三维数码显微镜。
29.制备例制备例1分别称量5kg水、1kg纳米硅溶胶、0.6kg氧化铝颗粒和0.3kg的质量分数1%氢氧化钠溶液,搅拌混合得抛光液1。
30.制备例2分别称量5.5kg水、1.25kg纳米硅溶胶、0.7kg氧化铝颗粒和0.4kg的质量分数1%氢氧化钠溶液,搅拌混合得抛光液2。
31.制备例3分别称量6kg水、1.5kg纳米硅溶胶、0.8kg氧化铝颗粒和0.5kg的质量分数1%氢氧化钠溶液,搅拌混合得抛光液3。
实施例
32.实施例1打砂前处理:取需处理的刀具材料,洗净后在打砂压力0.4mpampa,打砂距离100mm,打砂角度25
°
下打砂处理,调整打砂粒度为#600,打砂材料为白刚玉;抛光后处理:待打磨完成后,再对其抛光处理,控制抛光压力为10kpa,抛光浆料1流速为125ml/min,待抛光完成后,即可完成所述基体改性;活化处理:取基体改性刀具并置于沉积真空室中,升温减压后,再在氮气气氛下,对基体改性刀具进行活化处理;沉积包覆:待刀具活化完成后,依次在刀具表面选取cr靶材、alti靶材、tisi/alti靶材和靶材tisi,依次沉积包覆crn界面层、altin中间层、altin/tisin连接层和tisin包覆层,调节tisin包覆层为按原子质量比6%的si、37%的ti和52%的n,控制altin/tisin连接层厚度为1μm,待沉积完成后,即可制备得所述高附着力纳米刀具涂层。
33.实施例2打砂前处理:取需处理的刀具材料,洗净后在打砂压力0.5mpa,打砂距离110mm,打砂角度30
°
下打砂处理,调整打砂粒度为#600,打砂材料为白刚玉;抛光后处理:待打磨完成后,再对其抛光处理,控制抛光压力为15kpa,抛光浆料2流速为125ml/min,待抛光完成后,即可完成所述基体改性;活化处理:取基体改性刀具并置于沉积真空室中,升温减压后,再在氮气气氛下,对基体改性刀具进行活化处理;沉积包覆:待刀具活化完成后,依次在刀具表面选取cr靶材、alti靶材、tisi/alti
靶材和靶材tisi,依次沉积包覆crn界面层、altin中间层、altin/tisin连接层和tisin包覆层,调节tisin包覆层为按原子质量比7%的si、38%的ti和55%的n,控制altin/tisin连接层厚度为2μm,待沉积完成后,即可制备得所述高附着力纳米刀具涂层。
34.实施例3打砂前处理:取需处理的刀具材料,洗净后在打砂压力0.6mpa,打砂距离120mm,打砂角度35
°
下打砂处理,调整打砂粒度为#600,打砂材料为白刚玉;抛光后处理:待打磨完成后,再对其抛光处理,控制抛光压力为20kpa,抛光浆料3流速为125ml/min,待抛光完成后,即可完成所述基体改性;活化处理:取基体改性刀具并置于沉积真空室中,升温减压后,再在氮气气氛下,对基体改性刀具进行活化处理;沉积包覆:待刀具活化完成后,依次在刀具表面选取cr靶材、alti靶材、tisi/alti靶材和靶材tisi,依次沉积包覆crn界面层、altin中间层、altin/tisin连接层和tisin包覆层,调节tisin包覆层为按原子质量比8%的si、39%的ti和58%的n,控制altin/tisin连接层厚度为3μm,待沉积完成后,即可制备得所述高附着力纳米刀具涂层。
35.对比例对比例1:一种高附着力纳米刀具涂层,与实施例1的区别在于,对比例1不对刀具表面进行改性处理,其余制备条件和组分配比均与实施例1相同。
36.对比例2:一种高附着力纳米刀具涂层,与实施例1的区别在于,对比例2对刀具表面进行改性处理时只采用打砂前处理的改性方案,其余制备条件和组分配比均与实施例1相同。
37.对比例3:一种高附着力纳米刀具涂层,与实施例1的区别在于,对比例3对刀具表面进行改性处理时只采用抛光后处理的改性方案,其余制备条件和组分配比均与实施例1相同。
38.对比例4:一种高附着力纳米刀具涂层,与实施例1的区别在于,对比例4中抛光浆料直接采用等质量的纳米氧化铝颗粒,其余制备条件和组分配比均与实施例1相同。
39.对比例5:一种高附着力纳米刀具涂层,与实施例1的区别在于,对比例5中抛光浆料直接采用等质量的硅溶胶,其余制备条件和组分配比均与实施例1相同。
40.对比实施例对比实施例1对比实施例1:一种高附着力纳米刀具涂层,与实施例1的区别在于,对比实施例1中抛光浆料中未添加氢氧化钠溶液,其余制备条件和组分配比均与实施例1相同。
41.性能检测试验分别对实施例1~3、对比例1~5和对比实施例1进行性能测试,分别测试其涂层的压痕形貌、涂层膜
‑
基结合力。
42.检测方法/试验方法(1)涂层膜
‑
基结合力:采用mft-4000多功能材料表面性能测试仪测定涂层-基体结合强度,划痕速度为6mm/min,加载速度为300n/min,终止载荷为 150n,对每组试样测3次并取平均值;(2)涂层压痕形貌:采用洛氏硬度仪在涂层及涂层表面加载,观察加载后形成的压
痕(如图1
‑
6所示);(3)涂层的显微硬度:选用hvs-1000维氏硬度仪检测基体硬度,加载力为5kgf,加载时间为10s,每组试样测量5次并取平均值,采用nanotest tm vantage纳米力学测试系统测量涂层硬度,为避免基体硬度对涂层硬度的影响,将压入深度控制在涂层厚度的10%之内,最大压入深度为150nm,压入载荷为10mn,加载和卸载速度为0.25mn/s,保压时间为10s,每组试样测量8次并取平均值;具体检测结果如下表表1和图1~6所示:表1 性能检测表参考表1和图1~6的性能检测对比可以发现:(1)参照表1和图1结合实施例1~3进行性能对比,由表1和图1可以看出,本技术实施例制备的涂层具有良好的显微硬度,涂膜和基层的结合强度优异,说明本技术技术方案采用了多层硬质包覆层依次沉积的技术方案,能有效改善硬质涂层结构强度,在此基础上,本技术优化了刀具材料的表面结构,通过对其表面结构进行改性处理,能有效对基体表面去除粉尘颗粒的同时,降低其粗糙度,从而提高涂层与基体的勾连嵌合作用,促进粒子成核、提高膜层质量增强其结合强度,从而有效提高了硬质涂层在刀具表面的附着性能和抗脱落性能。
43.(2)参照表1和图2~4结合对比例1~3进行性能对比,由表1和图2~4可以看出,本技术实施例制备的涂层的显微硬度和结合强度显著降低,这反映了本技术技术方案采用打砂前处理和抛光后处理的方案对刀具表面进行表面处理,改善了工件表面的机械性能,增加了工件表面和涂层之间的附着力,同时也降低表面结构的粗糙度的同时,重点改善刀具的表面结构,从而有效提高了硬质涂层在刀具表面的附着性能和抗脱落性能。
44.(3)参照表1和图5结合对比例4~5进行性能对比,由表1和图5可以看出,本技术实施例制备的涂层的显微硬度和结合强度显著降低,这反映了本技术技术方案优化了抛光浆料的组成成分的同时,调整了各组分的配比,通过硅溶胶作分散介质的抛光浆料,提高了抛光处理过程中对刀具表面的抛光均匀性能,同时由于分散介质中的硅溶胶也具有良好的结构性能,改善抛光浆液的稳定性能,从而进一步提高了硬质涂层在刀具表面的附着性能和抗脱落性能。
45.(4)参照表1和图6结合对比实施例1和实施例1~3进行性能对比,由表1和图6可以
看出,本技术实施例制备的涂层的显微硬度和结合强度略有降低,这反映了本技术技术方案对抛光浆液的组成进一步限定,通过优化抛光浆液的组成,改变其ph值,由于在碱性条件下,ph值能有效改善抛光液中氧化铝颗粒的zeta电位,从而改善了抛光浆液的稳定性能,使其在实际使用中,提高了抛光处理过程中对刀具表面的抛光均匀性能,从而进一步提高了硬质涂层在刀具表面的附着性能和抗脱落性能。
46.本具体实施例仅仅是对本技术的解释,其并不是对本技术的限制,本领域技术人员在阅读完本说明书后可以根据需要对本实施例做出没有创造性贡献的修改,但只要在本技术的权利要求范围内都受到专利法的保护。