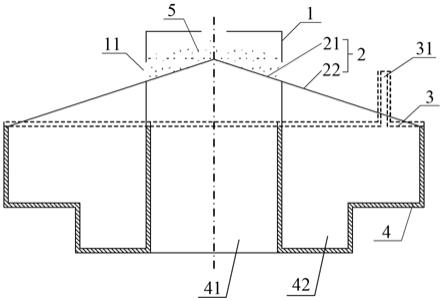
1.本发明属于航空发动机涡轮盘制造技术领域,具体涉及一种晶粒连续变化的双性能粉末涡轮盘制备方法及装置。
背景技术:2.航空发动机涡轮盘在工作时因其不同部位承受的温度与应力状态不同,具体如盘毂(涡轮盘中部)处于高应力状态,应力沿着其盘径向外逐渐降低,而盘缘(涡轮盘外部)处于高温度状态,温度沿盘径向内逐渐降低。因此,高性能的涡轮盘其盘毂部位应具有优异的屈服强度和低周疲劳性能,而盘缘部位应具有优异的高温持久强度和蠕变强度。众所周知,从微观组织状态研究,粗晶(粒度大的金属粉末)有利于提高材料的蠕变和持久性能,而细晶(粒度小的金属粉末)有利于增强材料的塑性、疲劳性能和屈服强度等。因而,双性能粉末涡轮盘应运而生,其盘毂部位是细晶组织,盘缘部位是粗晶组织,是一种具有双重组织的高性能粉末涡轮盘。
3.目前,双性能粉末涡轮盘的制造较为成熟的工艺主要有以下三种:第一种工艺首先是通过热等静压制备得到金属粉末坯体,然后通过等温锻造制得均匀细晶的涡轮盘,最后对均匀细晶的涡轮盘进行梯度热处理得到双性能粉末涡轮盘。这种工艺在进行梯度热处理时,要求涡轮盘的盘毂和盘缘之间的温度差高达300~600℃,因此需要在特制的热处理炉进行,工艺要求较高,不但制造成本较高,且制造过程比较复杂,与此同时,由于涡轮盘自身的热传导效应,要长时间保持涡轮盘的盘毂和盘缘之间较大的温度差很困难,对专用设备的要求极高,以致最终得到的双性能粉末涡轮盘的性能不高,品质不是很理想。
4.第二种工艺首先制备得到细晶金属粉末坯体,然后对细晶金属粉末坯的盘毂部位与辐板部位进行热锻,对盘缘部位只加热不锻造。此种工艺中,由于盘缘部位只加热不锻造,因此盘缘部位在制造过程中不变形,容易存在大量疏松空隙等缺陷,导致产品质量很差,不能满足双性能粉末涡轮盘的使用性能,且合格率较低,成本也较高。
5.最后一种获得双性能粉末涡轮盘的方法是,先用两种不同的材料分别锻造(或铸造或金属粉末压实)出环坯和饼坯,然后通过热等静压扩散连接或电子束焊接加等温模锻而成双性能粉末涡轮盘。然而此种工艺由于其粗晶环坯和细晶饼坯的连接界面存在突然的变化,此工艺制备的技术难点在于如何解决两种材料(即环坯和饼坯)结合区的“弱连接”问题,因为“弱连接”部位极易形成双性能粉末涡轮盘的裂纹源,对于高度强调安全性的航空发动机来说,这是个致命隐患。
6.有鉴于此,本发明人提出一种晶粒连续变化的双性能粉末涡轮盘制备方法及装置,以克服现有技术的缺陷。
技术实现要素:7.本发明的目的在于克服上述现有技术的缺点,提供一种晶粒连续变化的双性能粉末涡轮盘制备方法及装置,采用该制备方法及装置解决了现有技术制备双性能粉末涡轮盘
时过程复杂、成本高以及“弱连接”等原因引起的质量差的问题。
8.本发明的目的是通过以下技术方案来解决的:一种晶粒连续变化的双性能粉末涡轮盘的制备装置,包括包套体,所述包套体上方开口处安装有锥形筛,所述锥形筛的上方设置有储粉器;其中,所述包套体中部预留有通孔,所述通孔的孔壁与包套体的内壁共同构成用于放置金属粉末的包套腔室,所述包套腔室的形状与预要制备的双性能粉末涡轮盘外轮廓相同,所述包套腔室顶部开口;所述锥形筛的锥形面由内圈锥面和外圈锥面两部分组成,所述内圈锥面的最大外径与通孔孔壁的外径相同,所述外圈锥面沿周向均匀布设有若干个筛缝,每个所述筛缝的宽度由内向外随着锥形筛直径的增加线性增大,所述储粉器底部开设有下粉口,所述下粉口位于内圈锥面的正上方,当下粉口打开时,储粉器内盛放的不同粒度的金属粉末先经内圈锥面均匀向下流动、再流入到外圈锥面上开设的筛缝中进行筛选,使落入包套腔室内的金属粉末粒度由小到大、沿包套腔室由内向外径向连续分布。
9.进一步地,所述外圈锥面上、任意相邻所述筛缝之间的连接面设置为圆弧状或者三角状的凸起,用于使不同粒度的金属粉末只能沿筛缝运动、并最终落入包套腔室内。
10.进一步地,所述制备装置还包括包套盖,所述包套盖扣合在包套腔室顶部、并与包套腔室密封连接。
11.进一步地,所述包套盖上安装有抽气管、且所述抽气管位于包套腔室顶部开口处,用于将包套腔室内部抽真空。
12.进一步地,所述筛缝最小宽度大于等于金属粉末最小粒度的直径,所述筛缝最大宽度大于金属粉末最大粒度的直径。
13.一种晶粒连续变化的双性能粉末涡轮盘的制备方法,该方法基于上述制备装置,具体包括以下步骤:步骤一、先将不同粒度的金属粉末分批次装入储粉器中;步骤二、打开储粉器底部的下粉口,金属粉末按照粒度大小依次落入包套腔室中相应位置;打开储粉器底部的下粉口,不同粒度的金属粉末先经过内圈锥面均匀向下流动、再通过外圈锥面的筛缝进行筛选,使粒度小的金属粉末从靠近包套体中心的小筛缝落入包套腔室中内圈位置,粒度偏大的金属粉末从相应较大筛缝落入包套腔室中外圈位置,即落入包套腔室内部的金属粉末按照粒度由小到大、沿包套腔室由内向外径向连续分布;步骤三、重复步骤一和步骤二直至整个包套腔室内部装满金属粉末,盖上包套盖并封焊;步骤四、对封焊好的包套腔室再进行抽真空、加热除气以及最后的焊接密封处理;步骤五、先对步骤四焊接密封后的包套腔室进行热等静压处理,再机加工去除包套体,然后对金属粉末进行相应的热处理,即得到晶粒尺寸从盘毂至盘缘连续变大的双性能粉末涡轮盘。
14.进一步地,所述步骤一中金属粉末采用粒度为15~250μm单合金金属粉末或双合金金属粉末。
15.进一步地,所述步骤四中,对包套腔室进行抽真空、加热除气处理时,真空度小于5
×
10
‑4pa,保温温度450℃,保温时间8h。
16.进一步地,所述步骤五中,对包套腔室进行热等静压处理时,热等静压温度设定为1200
±
10℃,压力150
±
10mpa,保温保压时间不少于5h;机加工去除包套体后、再对金属粉末进行固溶热处理:设定温度为1200
±
10℃,保温8h,风冷;一级时效:设定温度为910
±
10℃,保温3h,风冷;二级时效:设定温度为850
±
10℃,保温10h,风冷:三级时效:设定温度为800
±
10℃,保温18h,风冷。
17.与现有技术相比,本发明的有益效果:本发明一种晶粒连续变化的双性能粉末涡轮盘制备方法及装置,采用本发明制备的双性能粉末涡轮盘,能够从宏观上保证其从盘毂至盘缘晶粒尺寸从小到大呈连续变化,且无明显的突变现象,即盘毂部位是细晶(粒度小的金属粉末)组织,盘缘部位是粗晶(粒度大的金属粉末)组织,且晶粒尺寸连续线性变化。另外经过实际验证,相同热处理的条件下,采用本发明制备的双性能粉末涡轮盘其盘毂具有优异的屈服强度和低周疲劳性能,盘缘部位具有优异的高温持久强度和蠕变强度,其次本发明可制备单合金金属粉末或双合金金属粉末两种类型的双性能粉末涡轮盘,同时制造方法操作简便、制备装置成本低、无“弱连接”等引起的质量问题,有效的解决了现有技术难以制备高品质的双性能粉末涡轮盘,提高了生产效率的同时保证了产品的质量。
附图说明
18.此处的附图被并入说明书中并构成本说明书的一部分,与说明书一起用于解释本发明的原理。
19.为了更清楚地说明本发明实施例或现有技术中的技术方案,下面将对实施例或现有技术描述中所需要使用的附图作简单地介绍,显而易见地,对于本领域普通技术人员而言,在不付出创造性劳动性的前提下,还可以根据这些附图获得其他的附图。
20.图1是本发明制备装置的结构示意图;图2是本发明锥形筛的俯视结构示意图;图3是本发明制备方法的流程框图。
21.其中: 1为储粉器;2为锥形筛;3为包套盖;4为包套体;5为金属粉末;11为下粉口;21为内圈锥面;22为外圈锥面;31为抽气管;41为通孔;42为包套腔室;221为筛缝。
具体实施方式
22.这里将详细地对示例性实施例进行说明,其示例表示在附图中。下面的描述涉及附图时,除非另有表示,不同附图中的相同数字表示相同或相似的要素。以下示例性实施例中所描述的实施方式并不代表与本发明相一致的所有实施方式。相反,它们仅是与所附权利要求书中所详述的、本发明的一些方面相一致的装置的例子。
23.为了使本领域的技术人员更好地理解本发明的技术方案,下面结合附图及实施例对本发明作进一步详细描述。
24.参见图1~2所示,本发明一种晶粒连续变化的双性能粉末涡轮盘的制备装置,包括包套体4,所述包套体4上方开口处安装有锥形筛2,锥形筛2的上方设置有储粉器1,储粉器1内可以盛放不同粒度的金属粉末5;制备时,打开储粉器1,不同粒度的金属粉末5经过锥
形筛2筛选后,按照金属粉末5粒度大小依次落入包套体4内相应位置,再通过热处理工艺制备成晶粒尺寸(金属粉末粒度大小)连续变化的双性能粉末涡轮盘。
25.具体的,所述包套体4中部预留有通孔41,通孔41的孔壁与包套体4的内壁共同构成用于放置金属粉末5的包套腔室42,包套腔室42的形状可根据预要制备的双性能粉末涡轮盘的外轮廓对应设置,包套腔室42顶部开口;锥形筛2的锥形面由内圈锥面21和外圈锥面22两部分组成,所述内圈锥面21的最大外径与通孔41孔壁的外径相同,内圈锥面21一方面用于防止金属粉末5掉落至通孔41中,造成材料的浪费;另一方面保证金属粉末5沿内圈锥面21均匀向下流动;外圈锥面22沿周向均匀布设有若干个筛缝221,每个筛缝221的宽度由内向外随着锥形筛2直径的增加线性增大,即筛缝221的宽度尺寸从小到大呈连续变化,所述筛缝221最小宽度大于金属粉末5最小粒度的直径,筛缝221最大宽度大于金属粉末5最大粒度的直径,以确保所有的金属粉末5都能够顺利从筛缝221落入包套腔室42内,储粉器1底部开设有下粉口11,下粉口11位于内圈锥面21的正上方,当下粉口11打开时,储粉器1内盛放的不同粒度的金属粉末5先经内圈锥面21均匀向下流动、再流入到外圈锥面22上开设的筛缝221中进行筛选,使落入包套腔室42内的金属粉末5粒度由小到大、沿包套腔室42由内向外径向连续分布。
26.其中,所述外圈锥面22上、任意相邻筛缝221之间的连接面设置为圆弧状或者三角状的凸起(图中未显示),用于使不同粒度的金属粉末5只能沿筛缝221向下运动、并最终落入包套腔室42内,避免金属粉末5停留在相邻筛缝221之间。
27.实际制备时,所采用的金属粉末5均是球形粉末且经过加热除气处理,金属粉末5均相互独立存在,不会出现粘连现象,保证金属粉末5能够按照粒度大小依次通过筛缝221筛选后、落入包套腔室42内相应位置。
28.本发明制备装置还包括包套盖3,所述包套盖3扣合在包套腔室42顶部、并与包套腔室42密封连接;所述包套盖3上安装有抽气管31、且抽气管31位于包套腔室42顶部开口处,抽气管31用于配合抽真空装置将包套腔室42内部抽真空。
29.如图3所示,基于上述制备装置,本发明提供一种晶粒连续变化的双性能粉末涡轮盘的制备方法,其具体包括以下步骤:步骤一、先将不同粒度的金属粉末5分批次装入储粉器1中;本发明金属粉末5采用粒度为15~250μm单合金的金属粉末或双合金的金属粉末。其中,当金属粉末5为单合金时,金属粉末5粒度为15~53μm体积占比15%~20%,53~106μm体积占比15%~20%,106~150μm体积占比30%~35%,150~250μm体积占比30%~35%。
30.步骤二、打开储粉器1底部的下粉口11,金属粉末5按照粒度大小依次落入包套腔室42中相应位置;具体的,打开储粉器1底部的下粉口11,不同粒度的金属粉末5先经过内圈锥面21均匀向下流动、再通过外圈锥面22的筛缝221进行筛选,使粒度小的金属粉末5从靠近包套体4中心的小筛缝221落入包套腔室42中内圈位置,粒度偏大的金属粉末5从相应较大筛缝221落入包套腔室42中外圈位置,即落入包套腔室42内部的金属粉末5按照粒度由小到大、沿包套腔室42由内向外径向连续分布。实际操作时,可以旋转锥形筛2的角度,以便落入包套腔室42内的金属粉末5能够均匀分布。
31.其中,当金属粉末5粒度与筛缝221的尺寸十分接近时,金属粉末5可能落入包套腔室42内的位置会出现一些偏差,本发明允许这种偏差存在,这是因为本方法并不是要保证每一个金属粉末5一定是按照粒度从小到大由内向外连续变化,因为这几乎不可能实现,原因是金属粉末5落入包套腔室42内部的轨迹并不是唯一确定的,且金属粉末5落入包套腔室42后也会向周围滚动。但是由于本发明所采用的金属粉末5是微米级别,不同与宏观世界中的球体,金属粉末5的滚动距离微乎其微,即使滚动也是在允许误差的范围内,宏观上不会影响晶粒的连续分布,本方法从宏观上保证了靠近包套腔室42内圈是细粉(粒度小的金属粉末),包套腔室42越靠外圈金属粉末5的粒度越来越大,且分布呈连续变化,从而在宏观上保证了最终制备的双性能粉末涡轮盘中的金属粉末5粒度从盘毂至盘缘呈连续变化状态;另外本发明金属粉末5在锥形筛2上流动时,对锥形筛2施加高频超声振动,以确保金属粉末5不会堵塞筛缝221。
32.步骤三、重复步骤一和二直至整个包套腔室42内部装满金属粉末5,盖上包套盖3并封焊;步骤四、对封焊好的包套腔室42再进行抽真空、加热除气以及最后的焊接密封处理;对包套腔室42进行抽真空、加热除气处理时,设定真空度小于5
×
10
‑4pa,保温温度450℃,保温时间8h。
33.步骤五、先对步骤四焊接密封后的包套腔室42进行热等静压处理,再机加工去除包套体4,然后对金属粉末5进行相应的热处理,即得到晶粒尺寸从盘毂至盘缘连续变大的双性能粉末涡轮盘;具体的,对包套腔室42进行热等静压处理时,热等静压温度设定为1200
±
10℃,压力150
±
10mpa,保温保压时间不少于5h;机加工去除包套体4,然后对金属粉末5进行固溶热处理:设定温度为1200
±
10℃,保温8h,风冷;一级时效:设定温度为910
±
10℃,保温3h,风冷;二级时效:设定温度为850
±
10℃,保温10h,风冷:三级时效:设定温度为800
±
10℃,保温18h,风冷。
34.为了进一步验证上述制备方法,发明人做了如下具体试验:实施例1:用于制备尺寸为φ500mm
×
60mm的双性能粉末涡轮盘,具体按照以下步骤实施:前期准备:制作用于装填金属粉末5的双性能粉末涡轮盘包套体42,所述包套体42采用不锈钢材质制作,再准备相应的金属粉末5,例如对金属粉末5进行选取以及加热除气处理等操作,最后搭建好制备装置。
35.步骤一:先将不同粒度的金属粉末5分批次装入储粉器1中;其中,金属粉末5为单合金,金属粉末5粒度为15~53μm,体积占比20%,粒度为53~106μm,体积占比20%,粒度为106~150μm,体积占比30%,粒度为150~250μm,体积占比30%。
36.步骤二、打开储粉器1底部的下粉口11,金属粉末5按照粒度大小依次落入包套腔室42中相应位置;步骤三、重复步骤一和二直至整个包套腔室42内部装满金属粉末5,盖上包套盖3并封焊;
步骤四、对封焊好的包套腔室42再进行抽真空、加热除气以及最后的焊接密封处理;对包套腔室42进行抽真空、加热除气处理时,设定真空度小于5
×
10
‑4pa,保温温度450℃,保温时间8h。
37.步骤五、先对步骤四焊接密封后的包套腔室42进行热等静压处理,再机加工去除包套体4,然后对金属粉末5进行相应的热处理,即得到晶粒尺寸从盘毂至盘缘连续变大的双性能粉末涡轮盘。
38.具体的,对包套腔室42进行热等静压处理时,热等静压温度设定为1200
±
10℃,压力150
±
10mpa,保温保压时间6h;机加工去除包套体4,然后对金属粉末5进行固溶热处理:设定温度为1200
±
10℃,保温8h,风冷;一级时效:设定温度为910
±
10℃,保温3h,风冷;二级时效:设定温度为850
±
10℃保温,10h,风冷:三级时效:设定温度为800
±
10℃,保温18h,风冷。
39.上述热处理完成后,对本实施例制备的双性能粉末涡轮盘样件进行检测,其各部位力学性能如下表1~3所示:表1:表2:表3:
通过上述检测数据说明,本发明制备的双性能粉末涡轮盘,其盘毂部位具有优异的抗拉强度、屈服强度和低周疲劳强度,盘缘部位具有优异的高温持久强度和蠕变强度,特别值得注意的是,本实施例制备的双性能粉末涡轮盘沿直径切开后,晶粒度等级沿盘毂
→
盘缘逐步下降,即盘毂部位是细晶组织,盘缘部位是粗晶组织,且晶粒尺寸从宏观上呈连续变化。
40.以上所述仅是本发明的具体实施方式,使本领域技术人员能够理解或实现本发明。对这些实施例的多种修改对本领域的技术人员来说将是显而易见的,本文中所定义的一般原理可以在不脱离本发明的精神或范围的情况下,在其它实施例中实现。
41.应当理解的是,本发明并不局限于上述已经描述的内容,并且可以在不脱离其范围进行各种修改和改变。本发明的范围仅由所附的权利要求来限制。