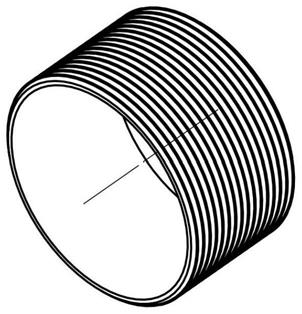
1.本发明属于激光熔覆修复技术领域,涉及一种飞机用滚筒槽尖磨损的激光直接沉积修复工艺方法。
背景技术:2.滚筒的材质为30crmnsia结构钢,其在飞机制造业中使用最广泛的一种调质钢,在淬火高温回火状态下具有较高的强度和足够的韧性。但在恶劣的服役环境中,槽尖与钢索接触式摩擦,表面cr层和基体极容易损伤、腐蚀,导致提前失效。而激光熔覆技术与传统的表面修复技术相比,具有精度高、结合强度高等优点,可实现一些局部区域的修复,与滚筒槽尖磨损区域的修复要求契合度高。但常规的滚筒槽尖修复方法因为修复前的路径规划、修复后的二次加工极易出现尺寸偏差,同时也容易出现熔覆层与基体结合强度不足导致满足不了滚筒使用要求。因此,市场亟需一种既能有效修复滚筒槽尖,又能满足尺寸和使用要求的修复工艺。
技术实现要素:3.为了解决所述的技术缺陷,本发明提供了一种飞机用滚筒槽尖磨损的激光直接沉积修复工艺方法,对待修复槽尖磨损表面进行预处理,通过光学三维扫描确认槽尖磨损尺寸与需恢复的最终尺寸,选择强度相当的高强钢粉末在磨损区域按算法轨迹激光熔覆修复改性形成具有加工余量的熔覆层,并通过逆向耦合机加修复区,形成满足尺寸要求和使用要求的滚筒槽尖。
4.为了实现上述目的,本发明的技术方案在于,提供一种飞机用滚筒槽尖磨损的激光直接沉积修复工艺方法,包括以下步骤:
5.s1,选择强度相当的高强钢粉末进行单道、多道多层激光熔覆实验,通过金相组织、拉伸性能、冲击性能评估结果,获得最终的修复工艺;
6.s2,滚筒槽尖待修复区域拍照记录,并进行修复区域的随形机械清理,去除表面氧化层及磨损处凹凸不平的位置,使之修复表面平滑且呈现光泽金属;
7.s3,通过光学三维扫描确认槽尖磨损尺寸与需恢复的最终尺寸,并采用游标卡尺对磨损区域进行测量;
8.s4,精确装夹滚筒零件,卡盘旋转时跳动控制在0.1mm以内,并计算修复区域的面积和厚度,设计扫描路径算法;
9.s5,采用激光熔覆方法修复磨损位置的尺寸,修复起始点位置左右端交替,控制工件温度以防止氧化,并留有0.3~0.5mm的加工余量;
10.s6,对修复区域进行局部去应力退火,升至190
±
10℃,保温2h,空冷;
11.s7,根据滚筒槽尖的形状、尺寸和表面粗糙度进行逆向耦合机械加工,可适当留0.1
‑
0.2mm余量,手工打磨并使用油石对手工打磨后的表面进行磨抛,提高修复区光滑度;
12.s8,机加磨抛后尺寸检验、荧光检验、外观检测,检测合格后镀铬层以完成修复。
13.进一步的,所述步骤s1中所述高强钢粉末为30crmnsia粉末,粉末使用前需置于100℃下真空烘干60min。
14.进一步的,所述步骤s1中修复改性形成熔覆层的工艺参数为激光功率700
‑
1100w,扫描速度6
‑
12mm/s,送粉量5g/min
‑
10g/min,光斑2mm
‑
4mm,送粉氦气流量为5l/min,保护氩气流量20l/min,熔覆层宽度为1.5~3.5mm,熔覆层厚度为0.2~0.8mm。
15.进一步的,所述步骤s1中为了获得熔覆层与母材的结合力,采用对接接头且熔覆填充的方式,拉伸试样取样、测试遵循gb/t228.1
‑
2010,冲击试样取样、测试遵循gb/t229.1
‑
2007,分别进行沉积态和退火态的试件的性能测试。
16.进一步的,所述步骤s4中滚筒装夹于两轴变位机,需保证滚筒表面的跳动在
±
0.1mm,同时扫描轨迹需要精准到0.1mm,采用轴向移动与转动结合的方式,实现轨迹的精确控制。
17.进一步的,所述步骤s4中根据滚筒直径裁剪2块0.5mm厚的防护板,用铁丝紧固于待修复区域两侧,中间留出一定距离露出待修复区。
18.进一步的,所述步骤s4中扫描路径算法为:局部修复区域速度:v
q
=j*k/(t*n*1000),其中k为常数360,t=3.14*d/v,d为滚筒直径,v为最优工艺参数对应的扫描速度,j为滚筒槽尖螺旋线角度,n为修复起始点圆心与结束点圆心的夹角。
19.与现有技术相比,本发明所具备的优点和有益效果:
20.1.本发明选择与滚筒材料强度相当的高强钢粉末,采用激光熔覆修复滚筒槽尖,能更好的控制槽尖的变形和熔覆层的质量,最终形成的修复后槽尖硬度高于基材,耐磨性和拉伸性能均有显著的提高。
21.2.本发明采用激光熔覆轨迹算法和逆向耦合机加方法能保证滚筒槽尖尺寸要求和熔覆层与基体的结合性能,工艺稳定,重复性好,可进行广泛推广。
22.3.本发明得到的修复工艺熔覆层与基材结合致密、微观缺陷少、结合性能高,在提高滚筒槽尖硬度、耐磨性、结合强度等方面具有广泛的应用前景。
附图说明
23.图1是实例中所述力学性能坡口设计加工试板示意图。
24.图2是实例中所述滚筒示意图。
25.图3是实例中所述逆向耦合机加原理示意图。
26.图4是实例中所述对接坡口填充区域截面组织金相图。
27.图中:1.工件几何体、2.毛坯几何体。
具体实施方式
28.以下结合附图,对本发明的较佳实施例作更详细的说明,具体的工艺步骤为:
29.s1,选择与滚筒基材强度相当的高强钢粉末30crmnsia粉末,粒度15~53μm。粉末使用前需置于100℃下真空烘干60min。
30.s2,进行30crmnsia粉末的单道激光熔覆试验,选取3组表面平整、成形良好的单道参数用于多道多层激光增材制造,通过对熔覆层显微组织优选最优参数。同时为了获得熔覆层与母材的结合力,采用对接接头且熔覆填充的方式(如图1)。拉伸试样取样和测试遵循
gb/t228.1
‑
2010,冲击试样取样、测试遵循gb/t229.1
‑
2007,进行退火态的试件的性能测试。
31.s3,确定失效的滚筒槽尖表面的待修复区域,并标记加以区分(滚筒示意图如图2);已标记的待修复区域拍照记录,再用打磨工具清理需要修复位置,去除表面氧化层及磨损处凹凸不平的位置,使之表面平滑且呈现光泽金属;通过光学三维扫描确认不同区域槽尖磨损尺寸与需恢复的最终尺寸。
32.s4,将滚筒装夹于两轴变位机上,同时需保证滚筒开始转动时表面的跳动在
±
0.1mm;根据滚筒直径裁剪2块0.5mm厚的防护板,用铁丝紧固于待修复区域两侧,中间留出一定距离露出待修复区。
33.s5,根据三维扫描确定的待修复区域尺寸,计算熔覆区域的面积和厚度,设计熔覆轨迹算法,道间填充路径为蛇形往复,在相邻层熔覆时起始点位置左右端交替,并留有0.3~0.5mm的机加工余量;局部修复区域速度:vq=j*k/(t*n*1000),其中k为常数360,t=3.14*d/v,d为滚筒直径,v为最优工艺参数对应的扫描速度,j为滚筒槽尖螺旋线角度,n为修复起始点圆心与结束点圆心的夹角,各个参数根据实测值在算法中定义。
34.s6,采用陶瓷加热带对激光修复后的局部滚筒槽尖进行去应力退火,以消除修复区域残余应力,热处理制度为:190℃
×
2h,空冷。过程中将测温偶端部放置零件与加热带之间,并用保温棉盖住加热带。
35.s7,选取完好的滚筒槽尖三维重构作为工件几何体1(图3),将修复后的区域定义为毛坯几何体2,选取球刀为加工刀头,根据毛坯几何体、工件几何体尺寸确定加工表面、加工角度、加工偏置轨迹的切削量(0.1mm),生成毛坯几何体加工算法,进行逆向耦合机械加工,可适当留0.1
‑
0.2mm余量,手工打磨并使用油石对手工打磨后的表面进行磨抛,提高修复区光滑度。
36.s8,机加磨抛后尺寸检验、荧光检验、外观检测,检测合格后镀铬层以完成修复。目视检测:采用目视检测的方法,对激光熔覆层进行检查,要求无裂纹、夹杂、气孔、和弧坑等缺陷。尺寸检测:修复后滚筒做三维光学扫描,并与修复前的滚筒扫描模型做对比,标记出各关键位置处的尺寸偏差,结果为实测值。当偏差值超过一定值时需要补焊修复。荧光检验:采用荧光渗透的方法,对修复后的零件检查,不允许有线性显示。
37.较佳的,所述s2和s5中激光熔覆设备主要包括:、kukakr90六轴机器人、trudisk6002碟片式激光器、medicoat振动送粉器、kuka dkp400变位机、spr480加工机床,保护气体为氩气,送粉气体为氦气,氦气和氩气都对熔池起保护作用,以防止熔覆过程中氧化。
38.较佳的,所述s2中激光熔覆最优工艺参数为:激光功率700w,扫描速度10mm/s,送粉量9g/min,光斑2.4mm,送粉氦气流量为5l/min,保护氩气流量20l/min。熔覆层宽度为1.8mm,熔覆层厚度为0.26mm。
39.较佳的,所述的对接坡口填充区域截面组织(如图4)主要由三层组成:熔覆层、热影响区和母材,无裂纹、未熔合等缺陷,组织致密、微观缺陷少。采用激光熔覆30crmnsia钢热影响区出现了硬化现象,淬硬区宽度约0.2mm,最高值达450hv0.5,热影响区宽约0.5mm。熔覆区硬度约380hv
0.5
高于母材区硬度360hv
0.5
。拉伸断裂于母材,冲击韧性远超过了锻件标准值。
40.以上实施例仅用以说明本发明的技术方案,而非对其限制,各实施例中的技术方案也可以经适当组合,形成本领域技术人员可以理解的其他实施方式。而这些属于本发明的精神所引伸出的显而易见的变化仍落入本发明的保护范围内。