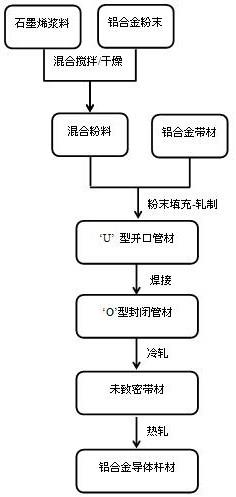
1.本发明涉及输电线缆制造技术领域,具体涉及一种架空线缆用石墨烯复合铝导体杆材及其制备工艺。
背景技术:2.架空输电线缆作为主要的电力输送载体,在电线线路中占有极为重要的地位。金属铝作为轻质金属材料,具有良好的导电性,在线缆领域的应用前景十分广阔。铝合金的导电性和强度是一对相互矛盾性能,金属铝在合金化过程中,强度会显著提高,但同时会造成导电率明显降低。为保证线缆导电性,市场所用架空线缆导体一般为工业纯铝,但受限于纯铝本身强度,现阶段所采用的线缆一般以高强度钢丝作为承力芯,承力芯的重量已经超过线缆导体本身重量。
3.无论是新线路建设,还是旧线路改造,都需要一种轻质量、高模量、高强度的新型线缆。伴随着社会经济的高速发展,土地资源的日趋紧张,架空输电线路新通道的审批和新建成为电网建设的突出难题。提高线缆导体本体强度,降低承力芯在线缆中所占比例是新型线缆发展路线之一。
4.石墨烯是迄今为止实验室发现的最坚韧、导电性和导热性最好的材料,其抗拉强度最高可达到130 gpa,理论拉伸模量高达1000 gpa。此外,石墨烯在受力时特有的褶皱舒展再断裂过程,因此石墨烯具有良好的韧性和塑性。受益于石墨烯上述的优点,将石墨烯加入铝合金中,有望显著实现铝合金良好力学性能与高导电性的结合。但现有技术中将石墨烯应用于制作线缆的技术还不够成熟,导致线缆的质量没有达到理想的性能。
技术实现要素:5.本发明要解决的技术问题是针对现有技术的缺陷,提供一种可实现铝导体杆材轻质化,且导电性无显著降低,同时显著提高铝杆材的弹性模量和抗拉强度,大幅度提高导体杆材耐用性和实用性的架空线缆用定向石墨烯复合铝导体杆材及其制备工艺。
6.为解决上述技术问题,本发明采用如下技术方案:一种架空线缆用定向石墨烯复合铝导体杆材,包括有铝合金外壳和芯材,铝合金外壳包覆在芯材外部形成壳芯结构,其特征在于:所述芯材采用取向石墨烯强化的铝合金复合材料制成,芯材的截面积占整个杆材总截面积的10~70%,其中石墨烯为强化相,其占芯材的重量百分比为0.1~3%,其余为铝合金;石墨烯的片层与铝合金外壳平行,形成同心取向,同时与长度方向平行。
7.用于制作芯材的铝合金成分如下:fe:≤0.25%,si:0.02
‑
0.20%,mn:≤0.15%,cu:≤0.04%,re:0.001
‑
0.006%,be:0.001
‑
0.002%,zr:0.06
‑
0.10%,sc:0.004
‑
0.006%,zn:≤0.04%,余量为铝,当然,还可能包括有一些不可避免的杂质。
8.所述石墨烯同批次内石墨烯厚度分布波动和粒径分布波动小于5 %的石墨烯,石墨烯为单层石墨烯或多层石墨烯,其最大厚度≤10nm;石墨烯的平均片层数量为3
‑
5层,更优为最大厚度≤7nm。
9.所述铝合金外壳为添加有锰和镁的铝合金,其中镁的含量为4.0~5.4%,锰的含量为0.5~1.0%;铝合金外壳的外径为3~15mm,厚度为0.3~5mm。
10.一种基于前述架空线缆用定向石墨烯复合铝导体杆材的制备工艺,其特征在于:采用连续产线,线速度为0.1~5m/s,按以下步骤进行,步骤s1:用于制作芯材的复合材料采用粉末冶金方法制备,经配料、混料、真空干燥处理后获得铝/石墨烯均匀混合的粉料;步骤s2:采用分批次填充多道次轧制工艺,消除混合粉末之间孔隙,同时促进石墨烯片层取向;将步骤s1制得的铝/石墨烯混合粉料经喂料系统某一喂料口按照设定的喂料速率匀速投放至铝合金带材,采用宽度略小于铝合金带材宽度的模具进行冷轧以提高混合粉料的致密度,与此同时,铝合金带材同步产生变形;在下一喂料口继续投放重复上述步骤,直至铝合金带材完全转变为u型开口铝合金管且其内部被铝/石墨烯混合粉料填充;该轧制工艺完成后,石墨烯片层在u型开口铝合金管内呈同心状分布;步骤s3:将步骤s2制得的充满铝/石墨烯混合粉料的u型开口铝合金管进行初步轧制,经初步轧制后u型开口缩小至完全封闭,使u型开口铝合金管成为完整的管状结构铝合金外壳,如o型;步骤s4:对步骤s3制得的铝合金外壳的缝隙进行焊接,得到完全封闭、但芯材尚未完全致密的铝合金导体杆材;步骤s5:将步骤s4制得的铝合金导体杆材进行多道次冷轧,排除粉末与粉末、粉末与铝合金外壳之间的孔隙,提高芯材的致密度,并在每一步轧制完成后进行退火处理,以调节铝合金导体杆材的内应力;通过硬度检测监控内应力残留,并与挤压前相比使硬度增加值不超过70%;步骤s6:将步骤s5制得的铝合金导体杆材进行热轧,以进一步提高其致密度,同时促使粉末与粉末、粉末与铝合金外壳形成稳定有效的冶金连接;步骤s7:将步骤s6制得的铝合金导体杆材收卷放入热处理炉内进行处理,升温至270
‑
350℃之间,保温2
‑
3h,完成导体最终性能调控。
11.在步骤s1中,所述配料,即按照所需计量的石墨烯浆料、铝合金粉及有机溶剂进行配料,其中石墨烯的含量为0.01
‑
3%;所述混料,包括以下步骤:1)将铝合金粉加入石墨烯浆料中,得到铝/石墨烯混合浆料,根据混合浆的料粘度加入有机溶剂,使混合浆料粘度适当,有机溶剂为乙醇、二氯甲烷、氯仿中的至少一种;2)将混合浆料进行充分研磨混合,得到铝/石墨烯坯体;研磨混合采用高能球磨混合或高速分散,以制备均匀复合浆料;所述真空干燥,是将铝/石墨烯浆料放入真空干燥箱内,进行真空干燥,去除铝/石墨烯浆料中的有机溶剂,最终得到铝/石墨烯混合粉末;其烘干温度为50
‑
80℃,保温时间≥48h,真空度≤0.03mpa。
12.在步骤s2中,铝合金带材经轧制、焊接工艺后形成铝合金外壳,其宽度与外径为5
‑
20mm的圆的周长相同,厚度为1
‑
5mm,填充铝/石墨烯粉料以轧制后形成的u型开口的宽度为1
‑
18mm;所述喂料系统包含若干个线性分布的喂料口,任意一个喂料口的喂料速率 均可
单独调节,且喂料系统保持静止,铝合金带材以恒定速度经过喂料系统;喂料速率及铝合金带材移动速度均可根据铝合金带材宽度尺寸d及开口尺寸进行调整,以保证铝/石墨烯粉料完全铺满铝合金带材;分批次填充工艺是根据铝合金带材的尺寸将所需混合粉料由单个喂料口一次填充完成或由多个喂料口分批次填充;而多道次轧制工艺是在任意一个喂料口填料后均进行冷轧,冷轧次数与混合粉料填充次数保持一致;在任意一喂料口填充混合粉料,经轧制后其厚度≤1.5mm,致密度≥60%,铝合金带材变形量≤6%;更优为其厚度应在0.3
‑
1mm之间,致密度≥70%;石墨烯片层择优取向是在轧制力驱动下,石墨烯片层经多道次冷轧后,与铝合金外壳呈同心结构。
13.在步骤s4中,对于铝合金外壳的缝隙采用压力焊接或熔化焊接工艺。
14.在步骤s5中,单道次冷轧变形率≤9%,总变形量为50%以上;轧制速度范围为130
‑
170mm/s;冷轧后的铝合金导体杆材,其芯部混料致密度≥75%,更优为致密度≥85%;在冷轧过程中,由于轧制力和粉末流动的共同作用,使同心状的石墨烯片层沿平行于铝合金导体杆材长度方向进行二次定向分布,石墨烯片层与铝合金导体杆材的长度方向夹角≤5度。
15.在步骤s6中,热轧过程的温度为300
‑
570℃,轧制压力为70
‑
300mpa,所得铝合金导体杆材芯部的致密度≥99%。
16.本发明首先通过采用定向石墨烯强化铝合金导体杆材,在不显著降低铝合金导体导电性前提下,导体杆材抗拉强度强度相比于纯铝抗拉强度提升90%以上,弹性模量提升10%以上,同时铝合金导体杆材在圆周方向的性能一致;其次,采用冷轧等工艺制备铝合金导体杆材,在生产过程中细化晶粒,与此同时,促进石墨烯片层二次取向,进一步提高铝导体杆材强度;第三,通过控制铝合金导体杆材制备过程的工艺条件,有效抑制有害相al4c3生成。这是因为al4c3在高温(≥500 ℃)条件下,或者熔融铝(熔点670℃)中将与碳材快速反应生成。本发明采用热轧工艺,可促进铝材和碳材形成冶金连接,降低两者接触时温度,缩短其接触时间,有助于抑制al4c3的生成;第四,采用壳芯结构,在石墨烯
‑
铝合金复合材料外层包覆一层耐腐蚀的铝合金外壳,既可增加铝导体杆材的导电容量,又可提高铝导体杆材的耐腐蚀性。
附图说明
17.图1
‑
图6为本发明铝合金导体杆材各种典型形状的横截面示意图;图7为本发明制备工艺流程图。
具体实施方式
18.下面结合附图及具体实施例对本发明做进一步说明。本实施例中,所有份、百分比在无特指时,均为重量百分比。所有原料均可由市场采购或属于行业常用的原材料。
19.本实施例以截面形状为圆形、等效截面积为50mm2的铝合金导体杆材为例进行说明。石墨烯的含量为1%,铝合金外壳的成分为:mg4.5
‑
5.0%,mn0.6
‑
1.0%,杂质元素少于
0.1%,其余为铝,厚度为1mm。具体制作过程步骤如下:s1:按石墨烯含量1%配置原材料。称取标称粒径为20μm铝合金粉末1.98kg;取浓度为4%、标称石墨烯片层厚度5nm的无水乙醇石墨烯浆料0.5kg;加入适量无水乙醇调节混合料粘度;将混合料以混合速度150rpm、混合时间90min进行混合,得到混合浆料;将混合浆料放入真空烘箱,烘干温度为68℃,保温时间为60h,真空度为0.03mpa,得到混合粉料;s2:选取铝合金带材,mg元素含量为4.5%,mn元素含量为0.8%,铝合金带材宽度为37.5mm,厚度1.5mm。根据铝合金带材尺寸,选择填料方式为多喂料口填充,同时需多次轧制压实。铝/石墨烯混合粉料的致密度为25%,铝合金带材以100mm/s靠近喂料系统,将混合粉料分别从6个喂料口以339ml/min匀速投放至铝合金带材;在每个喂料口后方,均采用宽度为35mm凸滚轮,将粉末冷轧提高致密度;单喂料口所投放铝合金粉末层经轧制后,转变为厚度为1mm、致密度为75%的混合料带材,且与铝合金包覆层呈同心圆结构;与此同时,铝合金带材在轧制力作用下,同步发生变形,其变形量在7%左右;经全部喂料口填充及轧制变形后,铝合金带材转变为u型铝合金半开口管,且内部由初步致密的同心圆状石墨烯片层和铝粉混合料;s3:将步骤s2中,完全充满混合料粉末铝合金管进行冷轧收口,轧制后u型铝合金半开口管转变为o型铝合金管,其外径约为12mm;s4:随后采用熔化焊
‑
冷金属过渡焊焊接,保证焊缝无咬边、未熔合等缺陷,保护气体为纯度99.999%以上的高纯氩气,气流量为25l/min;s5:焊接完成后,线缆升温至320 ℃,保温10 min进行去应力退火,冷却至室温后,开始进行冷轧,单道次变形量8%,轧制道次4次,最终冷轧结束后,铝合金导体杆材直径尺寸约为8.6mm;s6:在冷轧完成后,更换圆弧状热轧模具,更换完成后将模具预热至480 ℃,随后将冷轧铝合金导体杆材放入模具进行热轧,直至截面形状为圆形、等效直径为8mm的定向石墨烯复合铝导体杆材;步骤s7:将步骤s6制得的石墨烯复合铝导体杆材收卷放入热处理炉子内,升温至320 ℃,保温2h,完成铝合金导体杆材去应力退火,并提高铝合金导体杆材的强度;其性能测试结果如表1所示。由表1可以看出,本发明中添加石墨烯强化得到的铝合金导体杆材,对比纯铝导体杆材具有更高的力学强度和拉伸模量,但其电导率略微下降。抗拉性能及拉伸模量相对于纯铝分别提高111.2 %和14.1 %。
20.表1 1%石墨烯/铝合金性能测试结果以上已将本发明做一详细说明,以上所述,仅为本发明之较佳实施例而已,当不能限定本发明实施范围,即凡依本技术范围所作均等变化与修饰,皆应仍属本发明涵盖范围内。