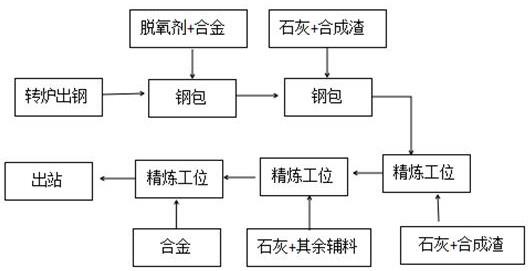
1.本发明属于合金钢技术领域,涉及低碳低硅含铝镇静钢生产工艺;具体为一种低碳低硅含铝镇静钢精炼快速成渣的方法。
背景技术:2.随着用户对钢材质量的要求越来越高,炉外精炼作为提升钢材质量的手段得到了迅速的发展。在炉外精炼过程中,通过合理地造渣可以达到脱硫、脱氧甚至脱氮的目的;可以吸收钢中的夹杂物;可以控制夹杂物的形态;可以形成泡沫渣淹没电弧提高热效率,减少耐火材料侵蚀。因此,在炉外精炼工艺中要特别重视造渣。
3.快速造白渣是 lf 炉精炼的关键。精炼工位起一个承上启下的作用,它不仅要细化钢水的成分、温度以及纯净度,同时还要保证连铸工位的连续性,所以在实际生产过程中精炼工艺需要在一定的时间内完成所有的任务。从而精炼过程中就必须在短时间内调制出白渣,为后续有充足的时间脱硫、微调成分和去除夹杂物创造好条件。为了缩短造白渣的时间,把部分渣料提前到转炉出钢过程中加入就提供了较好的条件,因为转炉出钢过程中钢水温度较高、钢包的底吹以及钢流的冲击作用具备了较好的热力学和动力学条件,对精炼早成渣和早脱氧能够提供较好的条件。但是出钢过程中的加入料需要有合适的量,石灰加多了容易结坨,不但影响化渣效果,更使得喂入的铝线无法进入钢水,大幅度降低铝的回收率,合成渣加多了容易造成渣稀效果影响大型夹杂物的排除效果;出钢过程中的加入料过少便无法及时化渣,延迟了精炼成渣时间。
技术实现要素:4.本发明克服了现有技术的不足,提出一种低碳低硅含铝镇静钢精炼快速成渣的方法,应用于钢种在lf精炼生产过程中,快速生成白渣的工艺控制。
5.为了达到上述目的,本发明是通过如下技术方案实现的:一种低碳低硅含铝镇静钢精炼快速成渣的方法,在转炉出钢过程中同时加入自身总量28
‑
35%的精炼合成渣和自身总量28
‑
35%的石灰渣料;精炼过程中加入剩余的精炼合成渣和石灰渣料;精炼合成渣和石灰渣料的总量比为1:5
‑
7;所述精炼合成渣的成分为重量百分比:20~50%的金属铝、35~60%的al2o3、10~20%的cao,所述金属铝的粒度<5mm。
6.优选的,在转炉出钢过程中同时加入自身总量1/3的精炼合成渣和自身总量1/3的石灰渣料。
7.优选的,所述的含铝镇静钢的钢种为ml08al。
8.优选的,所述快速成渣是精炼过程中在15分钟内实现白渣操作。
9.优选的,钢水进精炼的温度>1580℃。
10.优选的,精炼合成渣和石灰渣料的总量比为1:6。
11.通过以上方法最终形成的精炼炉渣的成分指标为:cao:45~55%,sio
2:
<7%,al2o
3:
25~35%,mgo:5~10%,feo:<0.7%,mno:<0.3%,r:>8。
12.精炼终渣成分中:feo+mno<1,钢中【o】≤20ppm。
13.本发明相对于现有技术所产生的有益效果为:合成精炼渣的组成成分直接影响精炼渣的冶金效果,通过调整精炼渣中的 cao 和 sio
2 的成分含量,可以精确控制精炼渣的碱度。高碱度精炼渣有利于降低钢水中平衡氧的含量,提高硫在渣、钢之间的分配比,有利于脱氧和脱硫,但碱度过高,精炼渣的粘度过大,流动性变差,则会降低精炼效果。精炼渣中的al2o3含量可以有效调节 cao
‑‑
sio2ꢀ‑‑
al2o3三元渣系的熔点,使精炼渣处于低熔点区域;在精炼渣中添加caco3、mgco3、baco3等成分,可以作为发泡剂,提高熔渣的泡沫化性能,为精炼过程提供足够的内生气源。
14.本发明是在生产低碳低硅含铝镇静钢时,加入特制的精炼合成渣,同时配以特定的加入方法,来实现快速成白渣的目的。本发明方法的精炼过程15分钟内实现白渣操作,造成的白渣不仅为精炼后期有充足的时间脱硫、去除夹杂物,同时可以降本增效。
附图说明
15.图1为本发明所述低碳低硅含铝镇静钢精炼快速成渣的生产工艺流程图。
具体实施方式
16.为了使本发明所要解决的技术问题、技术方案及有益效果更加清楚明白,结合实施例和附图,对本发明进行进一步详细说明。应当理解,此处所描述的具体实施例仅仅用以解释本发明,并不用于限定本发明。下面结合实施例和附图详细说明本发明的技术方案,但保护范围不被此限制。
17.实施例1一种低碳低硅含铝镇静钢精炼快速成渣的方法:本精炼模式设置为100t钢水/炉,精炼生产过程中严格规范渣料总量为1~1.3t/炉。其中石灰渣料用量控制在900kg左右,精炼合成渣的加入总量控制在150kg左右。
18.选用的低碳低硅含铝镇静钢钢种为ml08al;转炉终点钢水的成分包括重量百分比为c:0.06%,mn:0.10%,p:0.020%,s:0.025%,终点温度1620℃。
19.转炉出钢过程加入石灰渣料302kg,精炼合成渣50kg,其余按原工艺执行,此处的原工艺是指:出钢过程按顺序加入400kg中碳锰铁合金、60kg铝块、石灰,出钢后喂入300m铝线。
20.精炼进站温度为1588℃,精炼过程加入石灰渣料610kg,精炼合成渣100kg,其余按原工艺执行,此处的原工艺是指加入铝粒30k用以脱氧。其中,精炼合成渣的成分为重量百分比:金属铝:41%,al2o3:48%,cao:10.5%,金属铝的粒度<5mm。
21.最终的成渣时间14min,形成的精炼渣成分具体为:cao:51%,sio2:6%,al2o3:31%,mgo:10%,feo:0.5%,mno:0.1%,r:8。钢中全o:18ppm。在要求的时间内指标全部达标。
22.实施例2精炼模式与实施例1相同,钢种为ml08al,转炉终点钢水的成分包括重量百分比为:c:0.04%,mn:0.06%,p:0.016%,s:0.023%,终点温度1645℃。出钢过程加入石灰渣料303kg,精炼合成渣50kg,其余按原工艺执行。精炼进站温度为1605℃,精炼过程共计加入石灰650kg,精炼合成渣100kg,其余按原工艺执行。原工艺均与实施例1相同;其中,精炼合成
渣的成分为重量百分比:金属铝:50%,al2o3:35%,cao:15%,金属铝的粒度<5mm。
23.成渣时间13min,精炼渣成分具体为(重量百分比):cao:55%,sio2:6%,al2o3:29%,mgo:8%,feo:0.7%,mno:0.06%,r:9。钢中全o:20ppm。在要求的时间内指标全部达标。
24.对比例1精炼模式与实施例1相同,钢种为ml08al:转炉终点钢水成分包括(重量百分比):c:0.06%,mn:0.11%,p:0.023%,s:0.025%,终点温度1611℃。出钢过程加入石灰202kg,精炼合成渣0kg,按原工艺执行。精炼进站温度为1580℃,精炼过程共计加入石灰750kg,精炼合成渣150kg,其余按原工艺执行。原工艺均与实施例1相同。
25.成渣时间18min,精炼渣成分具体为:cao:49%,sio2:7%,al2o3:35%,mgo:7%,feo:0.8%,mno:0.22%,r:7。钢中全o:24ppm。该工艺没有执行炉后加精炼合成渣的方法,最终在要求的时间内没有完成指标,且氧化性指标(feo+mno、【o】)没有达标。
26.对比例2精炼模式与实施例1相同,钢种为ml08al:转炉终点钢水成分包括(重量百分比):c:0.05%,mn:0.07%,p:0.014%,s:0.020%,终点温度1631℃。出钢过程加入石灰320kg,精炼合成渣75kg,其余按原工艺执行。精炼进站温度为1598℃,精炼过程共计加入石灰610kg,精炼合成渣75kg,其余按原工艺执行。原工艺均与实施例1相同。
27.成渣时间20min,精炼渣成分具体为:cao:50%,sio2:7%,al2o3:32%,mgo:9%,feo:0.7%,mno:0.19%,r:7,钢中全o:19ppm。该工艺在炉后加入的精炼合成渣量达到了总加入量的50%,使得钢包进精炼炉时,表面渣过稀,最终没有在要求的时间内完成指标,影响了整个生产节奏。且渣样的碱度没有达标。
28.以上内容是结合具体的优选实施方式对本发明所做的进一步详细说明,不能认定本发明的具体实施方式仅限于此,对于本发明所属技术领域的普通技术人员来说,在不脱离本发明的前提下,还可以做出若干简单的推演或替换,都应当视为属于本发明由所提交的权利要求书确定专利保护范围。