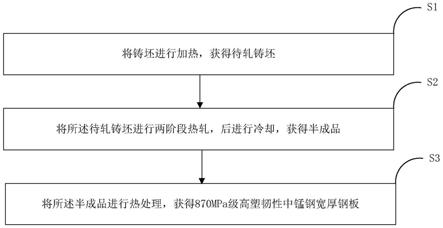
一种870mpa级高塑韧性中锰钢宽厚钢板及其制造方法
技术领域
1.本发明属于钢材制备技术领域,特别涉及一种870mpa级高塑韧性中锰钢宽厚钢板及其制造方法。
背景技术:2.近年来,以690mpa级为主的高强度宽厚钢板已大量应用于大型结构件制造中,其典型应用为海洋工程平台桩腿,起重机吊臂,水电压力管道等。为了进一步基于降低自重,减少生产成本,提高构件灵活性,高强度宽厚钢板强度等级正在朝着870mpa级迈进。同时,大型结构件的服役环境复杂多样,为提高材料在多重环境下的安全性,对高强度钢板同时提出高塑性和高韧性的要求。中锰钢以受载时发生trip效应(transformation induced plasticity)为特征,相比传统的高强钢,具有低屈强比和高塑韧性优势,但为保证钢板的综合力学性能,通常需添加大量的ni、mo、v等贵重合金元素,合金成本较高。在成分设计上以mn、nb、ti等低成本合金来替代贵重合金,同时具备高塑韧特性的870mpa级中锰钢高强度宽厚钢板,成为市场关注的重点。
3.目前的中锰钢宽厚板多以屈服强度690mpa级或以下等低强度级别为主,如中国发明专利申请cn110846577a、cn110983158a和cn104805378b。屈服强度达到800mpa以上的技术有:如中国发明专利申请cn109609848,最高屈服强度只达到855mpa,未达到870mpa级水平,且采用ni+cr+mo合金化成分设计,成本较高。少数屈服强度达到870mpa级或以上的技术有:如中国发明专利申请cn106119493b和cn111270160a,则采用冷轧+退火或热轧+卷曲的生产方式,但该生产方式并不适用于中厚板生产。因此870mpa级高塑韧性中锰钢宽厚钢板的制造技术尚属空白。
技术实现要素:4.本技术的目的在于提供一种870mpa级高塑韧性中锰钢宽厚钢板及其制造方法,以填补目前870mpa级高塑韧性中锰钢宽厚钢板的空白。
5.本发明实施例提供了一种870mpa级高塑韧性中锰钢宽厚钢板,所述钢板的化学成分以质量分数计包括:
6.c:0.05%-0.10%,si:0.20%-0.50%,mn:4.0%-8.0%,p:≤0.03%,s:≤0.04%,al:0.010%-0.020%,nb:0.035%-0.055%,ti:0.010%-0.020%,n:0.020%-0.050%,其余为fe和不可避免的杂质。
7.可选的,所述钢板的化学成分以质量分数计包括:
8.c:0.07%-0.09%,si:0.30%-0.40%,mn:5.0%-7.0%,p:≤0.03%,s:≤0.04%,al:0.013%-0.017%,nb:0.040%-0.050%,ti:0.013%-0.017%,n:0.030%-0.040%,其余为fe和不可避免的杂质。
9.可选的,所述钢的金相组织以体积分数计为:90%-96%的回火马氏体和4%-10%的奥氏体。
10.可选的,所述回火马氏体中含有nb/ti析出相,所述nb/ti析出相的尺寸<60nm。
11.基于同一发明构思,本发明实施例还提供了一种如上所述的870mpa级高塑韧性中锰钢宽厚钢板的制造方法,所述方法包括:
12.将铸坯进行加热,获得待轧铸坯;
13.将所述待轧铸坯进行两阶段热轧,后进行冷却,获得半成品;
14.将所述半成品进行热处理,获得870mpa级高塑韧性中锰钢宽厚钢板。
15.可选的,所述加热的温度为1050℃-1100℃,所述加热的时间为240min-360min。
16.可选的,所述两阶段热轧中,粗轧的结束温度为1050℃-1100℃,精轧的终轧温度为830℃-860℃。
17.可选的,所述冷却采用水冷,所述冷却的冷却速率≥5℃/s,所述冷却的终点温度为50℃-200℃。
18.可选的,所述热处理包括回火,所述回火的温度为550℃-600℃,所述回火的加热时间为40min-100min。
19.可选的,所述热处理的时机为所述两阶段热轧后的48小时内。
20.本发明实施例中的一个或多个技术方案,至少具有如下技术效果或优点:
21.本发明实施例提供的870mpa级高塑韧性中锰钢宽厚钢板,所述钢板的化学成分以质量分数计包括:c:0.05%-0.10%,si:0.20%-0.50%,mn:4.0%-8.0%,p:≤0.03%,s:≤0.04%,al:0.010%-0.020%,nb:0.035%-0.055%,ti:0.010%-0.020%,n:0.020%-0.050%,其余为fe和不可避免的杂质;通过低c添加nb/ti的成分设计,无需添加ni、cr、v、mo等合金,既能保证屈服强度在870mpa以上,还使延伸率≥20%,同时-60℃冲击功≥120j,钢板厚度≤30mm。
22.上述说明仅是本发明技术方案的概述,为了能够更清楚了解本发明的技术手段,而可依照说明书的内容予以实施,并且为了让本发明的上述和其它目的、特征和优点能够更明显易懂,以下特举本发明的具体实施方式。
附图说明
23.为了更清楚地说明本发明实施例中的技术方案,下面将对实施例描述中所需要使用的附图作一简单地介绍,显而易见地,下面描述中的附图是本发明的一些实施例,对于本领域普通技术人员来讲,在不付出创造性劳动的前提下,还可以根据这些附图获得其它的附图。
24.图1是本发明实施例提供的方法的流程图;
25.图2是本发明实施例1提供的钢板的金相组织图;
26.图3是本发明实施例1提供的钢板的投射电镜图。
具体实施方式
27.下文将结合具体实施方式和实施例,具体阐述本发明,本发明的优点和各种效果将由此更加清楚地呈现。本领域技术人员应理解,这些具体实施方式和实施例是用于说明本发明,而非限制本发明。
28.在整个说明书中,除非另有特别说明,本文使用的术语应理解为如本领域中通常
所使用的含义。因此,除非另有定义,本文使用的所有技术和科学术语具有与本发明所属领域技术人员的一般理解相同的含义。若存在矛盾,本说明书优先。本文中所使用的专业术语只是为了描述具体实施例的目的,并不是旨在限制本发明的保护范围。例如,室温可以是指10~35℃区间内的温度。
29.除非另有特别说明,本发明中用到的各种原材料、试剂、仪器和设备等,均可通过市场购买得到或者可通过现有方法制备得到。
30.本技术实施例的技术方案为解决上述技术问题,总体思路如下:
31.根据本发明一种典型的实施方式,提供了一种870mpa级高塑韧性中锰钢宽厚钢板,所述钢板的化学成分以质量分数计包括:
32.c:0.05%-0.10%,si:0.20%-0.50%,mn:4.0%-8.0%,p:≤0.03%,s:≤0.04%,al:0.010%-0.020%,nb:0.035%-0.055%,ti:0.010%-0.020%,n:0.020%-0.050%,其余为fe和不可避免的杂质。
33.上述主要合金元素作用和限定范围详细说明如下:
34.c:c元素是扩大奥氏体相区元素,也是具有强烈固溶强化作用的元素,同时c元素可与nb、ti元素形成析出物而进行第二相,形成沉淀强化作用而改善钢板强度,但c含量过高,产品韧性和焊接性能较差。综合考虑,本钢种需要钢具备优良的强韧性,因而本发明控制碳含量范围为0.05~0.10%。
35.si:不与c形成碳化物,以固溶方式存在于钢中,通过与可动位错的应力场交互作用,阻碍位错运动,提高钢板的强度。但si含量较高时,对钢的焊接性能不利,本发明中的si含量控制为0.20~0.50%。
36.mn:mn通过固溶强化提高组织的强度,适当的mn含量也能大幅提升奥氏体稳定性,提高mn含量能增加钢的淬透性,从而使得钢在很宽的冷速范围内获得马氏体甚至全马氏体,进而在两相区回火中形成少量逆转变奥氏体,回火马氏体组织能增加钢的强度,逆转变奥氏体组织能提高钢的韧塑性能,从而使钢具有优异的综合力学性能,本发明中的mn含量控制为4.0~8.0%。
37.p:p在钢中固溶强化作用强,作为合金元素加入低合金结构钢中,能提高其强度和钢的耐大气腐蚀性能,但p最大的害处是,偏析严重,增加回火脆性,显著增加钢的塑性和韧性,致使钢在冷加工时容易脆裂也即所谓“冷脆”现象。p对焊接性也有不利影响,p是有害元素,应严加控制,本发明中的p含量控制为≤0.03%。
38.s:s在钢中偏析严重,恶化钢的质量,在高温下,降低钢的塑性,是一种有害元素,它以熔点较低的fes形式存在。单独存在的fes的熔点只有1190℃,而在钢中与铁形成共晶体的共晶温度更低,只有988℃,当钢凝固时,硫化铁析集在原生晶界处。钢1100~1200℃进行轧制时,晶界上的fes就将熔化,大大的削弱了晶粒之间的结合力,导致钢的热脆现象,因此对硫应严加控制,本发明中的s含量控制为≤0.04%。
39.al:al增加相变驱动力,al在钢中与n相互作用,形成细小而弥散的aln析出,可抑制晶粒长大,达到细化晶粒、提高钢在低温下的韧性的目的。本发明中的al含量控制为0.010~0.020%。
40.nb、ti:nb和ti微合金化元素对钢板起细化强化作用,进一步保证钢板的低温韧性,本发明中nb元素含量限定为0.035~0.055%且ti元素含量限定为0.010~0.020%。
41.n:n在钢中可形成间隙固溶体,提高钢板强度;同时n也可以同nb、ti、al结合形成弥散的析出物第二相,抑制高温与轧制时的晶粒长大,提高韧性。本发明中的n含量控制为0.020~0.050%。
42.所述的870mpa级高塑韧性中锰钢板,其特征在于:屈服强度≥870mpa,延伸率≥20%,-60℃冲击功≥120j。
43.采用以上设计,在不添加ni、cr、v、mo等合金下,既能保证屈服强度在870mpa以上,还使延伸率≥20%,同时-60℃冲击功≥120j,钢板厚度≤30mm,以能满足高强度高塑韧钢板性能要求。
44.本方法在不添加大量合金的情况下就能实现高强度高塑性高韧性的原理在于:通过合理的微合金成分设计,结合轧制与热处理精准控制钢中的析出物与逆相变奥氏体,采用nb和微合金化细化原始奥氏体晶粒来获得细晶强化和析出强化从而提高强度,采用合理的轧制与热处理工艺获得薄膜状逆相变奥氏体来提高塑性和韧性。
45.作为一种可选的实施方式,所述钢板的化学成分以质量分数计包括:
46.c:0.07%-0.09%,si:0.30%-0.40%,mn:5.0%-7.0%,p:≤0.03%,s:≤0.04%,al:0.013%-0.017%,nb:0.040%-0.050%,ti:0.013%-0.017%,n:0.030%-0.040%,其余为fe和不可避免的杂质。
47.作为一种可选的实施方式,中锰钢宽厚钢板厚度≤30mm。
48.作为一种可选的实施方式,金相组织为体积比占90%-96%的回火马氏体和体积比4%-10%的奥氏体,同时在回火马氏体中含有nb/ti析出相,析出相尺寸<60nm。
49.根据本发明另一种典型的实施方式,提供了一种如上提供的870mpa级高塑韧性中锰钢宽厚钢板的制造方法,所述方法包括:
50.s0.利用500kg真空感应炉进行钢坯冶炼,并锻造为厚度120~200mm的钢坯
51.s1.将铸坯进行加热,获得待轧铸坯;
52.作为一种可选的实施方式,加热温度控制在1150~1250℃,加热时间在240~360min。
53.控制加热温度为1150~1250℃,加热时间为240~360min的原因是在该温度区间使铸坯中的nb、ti等合金元素在该温度区间充分固溶并使奥氏体晶粒获得均匀化,该取值过大的不利影响是奥氏体晶粒过度长大,不利于晶粒细化,过小的不利影响是合金元素固溶不充分,未溶的合金形成碳化物对性能不利。
54.s2.将所述待轧铸坯进行两阶段热轧,后进行冷却,获得半成品;
55.作为一种可选的实施方式,控制粗轧结束温度在1050~1100℃,控制精轧终轧温度在830~860℃。
56.控制粗轧结束温度在1050~1100℃,以便在奥氏体晶粒再结晶温度以上完成粗轧,该温度取值过大的不利影响是粗轧温度过高奥氏体再结晶和晶粒尺寸不均匀,过小的不利影响是奥氏体不能充分再结晶。
57.控制精轧终轧温度在830~860℃,以便在奥氏体再结晶温度以下与相变开始温度以上的温度区间完成精轧,该温度取值过大的不利影响是钢板水冷后强度较低,过小的不利影响是易于在水冷后钢板翘曲,板形较差。
58.作为一种可选的实施方式,控制冷却速率≥5℃/s,终止冷却后钢板表面温度50℃
~200℃。
59.控制冷却速率≥5℃/s的原因是使钢板在快速冷却后获得较强的相变强化效果从而达到较高的强度,该速率取值过小的不利影响是钢板相变强化效果差强度较低。
60.控制终止冷却后钢板表面温度为50℃~200℃,以便获得高强度的完全马氏体组织,该温度取值过大的不利影响是钢板相变强化效果差、强度较低,过小的不利影响是水冷过强而板形较差。
61.s3.将所述半成品进行热处理,获得870mpa级高塑韧性中锰钢宽厚钢板。
62.作为一种可选的实施方式,轧后48小时内送往热处理炉进行回火,回火温度550~600℃,加热时间40~100min,回火后钢板空冷至常温。
63.控制回火温度550~600℃,加热时间40~100min的原因是使材料在该过程中形成高稳定性的逆相变奥氏来获得高塑性和高韧性,该取值过大的不利影响是逆相变奥氏体稳定性差从而钢板塑性和韧性较低,过小的不利影响是无法形成逆相变奥氏体。
64.下面将结合实施例、对照例及实验数据对本技术的870mpa级高塑韧性中锰钢宽厚钢板及其制造方法进行详细说明。
65.实施例
66.一种870mpa级高塑韧性中锰钢宽厚钢板,其铸坯的化学成分以质量分数计如下表:
[0067] csimnpsalnbtin实施例10.0580.274.200.0060.0020.0170.0450.0160.030实施例20.0760.326.700.0080.0030.0150.0380.0130.040实施例30.0630.417.500.0070.0030.0190.0520.0180.030
[0068]
制备方法如下:
[0069]
s1.将铸坯进行加热,获得待轧铸坯;
[0070]
s2.将所述待轧铸坯进行两阶段热轧,后进行冷却,获得半成品;
[0071]
两阶段热轧和冷却的工艺参数如下:
[0072][0073]
s3.将所述半成品进行热处理,获得870mpa级高塑韧性中锰钢宽厚钢板。
[0074]
热处理的工艺参数如下:
[0075] 钢板厚度,mm回火温度,℃回火时间,min实施例11556045实施例22058060实施例33060090
[0076]
对比例1
[0077]
一种中锰钢宽厚钢板,其铸坯的化学成分以质量分数计如下表:
[0078] csimnpsalnbtin
对比例10.0670.316.500.0050.0030.0170.0510.0120.025对比例20.0530.277.810.0040.0080.0130.0380.0150.031对比例30.1200.352.010.0050.0060.0350.0450.0180.023
[0079]
制备方法如下:
[0080]
s1.将铸坯进行加热,获得待轧铸坯;
[0081]
s2.将所述待轧铸坯进行两阶段热轧,后进行冷却,获得半成品;
[0082]
两阶段热轧和冷却的工艺参数如下:
[0083][0084]
s3.将所述半成品进行热处理,获得宽厚钢板。
[0085]
热处理的工艺参数如下:
[0086] 钢板厚度,mm回火温度,℃回火时间,min对比例12051060对比例22565075对比例31858055
[0087]
实验例
[0088]
将实施例1-3和对比例1-n制得的钢进行性能检测,检测方法为:根据gb/t228《《金属材料室温拉伸试验方法》》测定钢板拉伸性能,根据gb/t229-2007《《金属材料夏比摆锤冲击试验方法》》测定钢板厚度1/4处的冲击性能,测试结果如下表所示:
[0089] 屈服强度,mpa抗拉强度,mpa延伸率,%-60℃冲击功,j实施例192396623.0138实施例287993126.0157实施例390795224.5162对比例1959102414.037对比例252498028.068对比例369571112.031
[0090]
由上表可得,本发明实施例提供的方法制备的870mpa级中锰钢宽厚钢板力学性能优良,屈服强度≥879mpa,抗拉强度≥931mpa,断后延伸率≥24.5%,-60℃冲击功≥138j,各项力学指标良好;通过对比例和实施例数据的比较可得,当回火温度或化学成分不在本技术实施例提供的范围内时,会出现强度、-60℃冲击功与延伸率较低的情况。
[0091]
附图2-3的详细说明:
[0092]
如图2所示,为实施例1制备的钢板的金相组织图,由图可得,组织回火马氏体和奥氏体的双相组织;
[0093]
如图3所示,为实施例1制备的钢板的投射电镜图,由图可得,钢中含有弥散的nb、ti析出物,析出物尺寸<60nm。
[0094]
本发明实施例中的一个或多个技术方案,至少还具有如下技术效果或优点:
[0095]
(1)本发明实施例提供的钢板的屈服强度>870mpa,断后伸长率≥20.0%,-60℃
冲击功≥120j,填补了屈服强度870mpa级高塑韧性中锰钢板宽厚钢板的空白;
[0096]
(2)本发明实施例提供的方法通过低c添加nb/ti的成分设计,采用轧后水冷+回火处理,通过获得回火马氏体和奥氏体以及nb、ti析出物获得到屈服强度870mpa级的高塑韧性中锰钢宽厚钢板;
[0097]
(3)本发明实施例提供的钢板相比于传统添加mo、v、ni等元素的中锰钢,合金成本可降低10%以上。
[0098]
最后,还需要说明的是,术语“包括”、“包含”或者其任何其他变体意在涵盖非排他性的包含,从而使得包括一系列要素的过程、方法、物品或者设备不仅包括那些要素,而且还包括没有明确列出的其他要素,或者是还包括为这种过程、方法、物品或者设备所固有的要素。
[0099]
尽管已描述了本发明的优选实施例,但本领域内的技术人员一旦得知了基本创造性概念,则可对这些实施例作出另外的变更和修改。所以,所附权利要求意欲解释为包括优选实施例以及落入本发明范围的所有变更和修改。
[0100]
显然,本领域的技术人员可以对本发明进行各种改动和变型而不脱离本发明的精神和范围。这样,倘若本发明的这些修改和变型属于本发明权利要求及其等同技术的范围之内,则本发明也意图包含这些改动和变型在内。