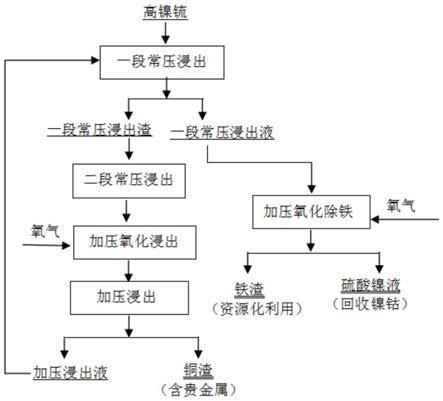
1.本发明涉及高镍锍处理工艺技术领域,更具体的是涉及实现高镍锍中镍、铜、铁分别开路并富集贵金属的方法技术领域。
背景技术:2.在硫化镍铜矿冶炼生产工艺中,硫化原矿选矿得到精矿进入火法冶炼系统得到镍铜富集的高镍锍,此高镍锍中镍含量35%-45%,铜含量20%-30%,铁含量小于4%,硫含量20%-25%。该高镍锍目前采用磨浮分选工艺将其选为镍精矿(含镍60%以上,含铜小于4%)、铜精矿(含铜60%以上,含镍小于4%)和合金分别进入镍、铜、贵金属冶炼系统生产镍、铜及贵金属产品。目前,高镍锍磨浮分选得到镍精矿采用两种工艺处理分别得到镍产品,分别为:镍精矿-高锍-电解镍工艺,镍精矿-加压浸出-电积镍(或硫酸镍)。
3.镍精矿-电解镍工艺中镍精矿中的贵金属最终进入镍阳极泥,镍阳极泥大多数为单质硫,可通过单质硫熔点较低的性质,将大多数单质硫分离,得到富含贵金属的热滤渣,部分(根据生产情况适当搭配处理)含贵金属热滤渣返回火法,最终再次进入高镍锍(衔接磨浮分选工艺),但大多数热滤渣处于堆存状态。整个工艺过程进入镍精炼系统的贵金属存在反复循环的问题且部分贵金属处于堆存状态,降低了贵金属回收率和直收率;镍精矿生产电解镍工艺中镍精矿中的铁最终以黄钠铁钒渣的形式开路。目前,该黄钠铁钒渣少量返回火法冶炼系统搭配处理,大多数也处于堆存状态。
4.镍精矿-加压浸出工艺中的贵金属最终进入加压浸出渣,该渣主要为镍精矿原料中的铁(碱式硫酸铁或三氧化二铁的形式存在)和铜的富集渣,其中铁含量约30%。目前该渣也是搭配少量返回火法冶炼系统处理,但大部分处于堆存状态。
5.所以,现有高镍锍-磨浮分选-生产镍产品、铜产品和贵金属的工艺路线,存在原料中贵金属分散、主要金属回收率低、直收率更低和贵金属原料大量堆存不能变现的问题,且分选产物镍精矿中的铁最终以铁渣固废的形式堆存,占用场地、含有价金属并造成环境污染。
技术实现要素:6.本发明的目的在于:为了解决上述技术问题,本发明提供一种实现高镍锍中镍、铜、铁分别开路并富集贵金属的方法。
7.本发明为了实现上述目的具体采用以下技术方案:
8.一种实现高镍锍中镍、铜、铁分别开路并富集贵金属的方法,包括如下步骤:
9.步骤1、一段常压浸出:将高镍锍原料和加压浸出液混合,鼓空气搅拌反应,反应温度75-85℃,反应时间5-7h,终点ph为4.5-5.0,固液分离得到一段浸出液和一段浸出渣;
10.步骤2、二段常压浸出:将步骤1中得到的一段常压浸出渣加入水和硫酸进行搅拌、鼓空气反应;
11.步骤3、加压氧化浸出:将步骤2中二段常压浸出得到的浸出浆料打入加压釜中,升
温并开启搅拌,通氧气;
12.步骤4、加压浸出:将步骤3得到的加压釜中的物料停止通氧气,然后降温处理、将残留的氧气排出加压釜,继续升温到150-180℃进行反应,反应时间为1-2h,降温、固液分离,得到加压浸出液和铜渣,体系终点ph为2.0-3.0;
13.步骤5、加压氧化除铁:将步骤1中得到的一段常压浸出液泵入加压釜中,升温、搅拌、通氧,控制氧分压0.1-0.3mpa,反应温度150-200℃,反应时间为1-3h,降温、固液分离,得到硫酸镍溶液和铁渣。
14.进一步地,所述高镍锍原料中镍含量35%-45%、铜含量20%-30%、铁含量3.5%-5%、硫含量20%-24%,还含有贵金属。
15.进一步地,步骤3中,加压氧化浸出条件为:控制温度在150-180℃,控制浸出时间1.0-2.0h,控制氧分压0.1-0.3mpa;
16.进一步地,步骤2中,浸出液固比6-8:1,浸出用酸量为理论量的0.85-0.9倍,反应温度75-85℃以上,反应时间5-7h,终点ph为1.5-2.0。
17.本发明的有益效果如下:
18.本发明的本发明的一种实现高镍锍中镍、铜、铁分别开路并富集贵金属的方法,通过控制加压氧化浸出条件,实现铁、镍与铜的分离,产出硫酸镍溶液可直接衔接硫酸镍(电积镍)生产工艺,产出铜渣直接衔接铜熔炼生产电解铜工艺,贵金属富集于铜阳极泥中后进入贵金属回收系统,铁以含铁大于60%的铁渣开路,衔接铁的资源化利用。整个工艺提高各金属直收率,大大减少湿法固废渣的产出,富集并利于贵金属回收。
附图说明
19.图1是本发明的工艺流程图;
具体实施方式
20.为使本发明实施例的目的、技术方案和优点更加清楚,下面将对本发明实施例中的技术方案进行清楚、完整地描述,显然,所描述的实施例是本发明一部分实施例,而不是全部的实施例。
21.一种实现高镍锍中镍、铜、铁分别开路并富集贵金属的方法,包括如下步骤:
22.步骤1、一段常压浸出:将高镍锍原料和加压浸出液混合,鼓空气搅拌反应,反应温度75-85℃,反应时间5-7h,终点ph为4.5-5.0,固液分离得到一段浸出液和一段浸出渣;
23.步骤2、二段常压浸出:将步骤1中得到的一段常压浸出渣加入水和硫酸进行搅拌、鼓空气反应;
24.步骤3、加压氧化浸出:将步骤2中二段常压浸出得到的浸出浆料打入加压釜中,升温并开启搅拌,通氧气;
25.步骤4、加压浸出:将步骤3得到的加压釜中的物料停止通氧气,然后降温处理、将残留的氧气排出加压釜,继续升温到150-180℃进行反应,反应时间为1-2h,降温、固液分离,得到加压浸出液和铜渣,体系终点ph为2.0-3.0;
26.步骤5、加压氧化除铁:将步骤1中得到的一段常压浸出液泵入加压釜中,升温、搅拌、通氧,控制氧分压0.1-0.3mpa,反应温度150-200℃,反应时间为1-3h,降温、固液分离,
得到硫酸镍溶液和铁渣。
27.进一步地,所述高镍锍原料中镍含量35%-45%、铜含量20%-30%、铁含量3.5%-5%、硫含量20%-24%,还含有贵金属。
28.进一步地,步骤3中,加压氧化浸出条件为:控制温度在150-180℃,控制浸出时间1.0-2.0h,控制氧分压0.1-0.3mpa;
29.进一步地,步骤2中,浸出液固比6-8:1,浸出用酸量为理论量的0.85-0.9倍,反应温度75-85℃以上,反应时间5-7h,终点ph为1.5-2.0。
30.用以下非限定性实施例子对本发明的工艺做进一步的说明,有助于理解本发明及其优点,但不作为对本发明保护范围的限定,本发明的保护范围由权利要求书决定。
31.实施例1
32.表1实施例1所用高镍锍主要成份(%)及贵金属含量(g/t)
33.nicucofesagauptpd39.5026.120.634.9222.7503.308.532.58。
34.具体实施过程:将高镍锍和加压浸出液混合鼓空气搅拌反应,温度75℃,反应5h后,测ph为4.5,固液分离,得到一段常压浸出液;一段常压浸出渣加入水和理论量0.85倍的硫酸进行二段常压浸出,控制液固比为6∶1,鼓空气搅拌反应5h,温度75℃,测ph为2.42;二段常压浸出浆料直接进入加压釜,控制加压温度150℃,氧分压0.3mpa,反应时间1.5h后,停止通氧,并适当降温排气,将加压釜中残留的氧气排出;继续升温到150℃,保温反应2h后降温泄压,出加压釜,物料进行固液分离,得到加压浸出渣(外付铜渣),加压浸出液返回一段常压浸出工序;一段常压浸出液继续进加压釜进行加压氧化除铁,控制加压除铁温度150℃,氧分压0.3mpa,反应时间3.0h,反应结束后降温、泄压,出釜进行固液分离,得到铁渣和除铁后液(外付硫酸镍钴溶液)。硫酸镍钴溶液、铁渣成份及铜渣成份如表2。
35.表2实施例1中硫酸镍钴溶液、铁渣成份及铜渣成份检测分析结果
36.名称nicucofesagauptpd硫酸镍溶液g/l54.710.0510.910.25
ꢀꢀꢀꢀ
铁渣%0.790.010.01658.692.22
ꢀꢀꢀꢀ
铜渣%1.0264.690.162.7020.861208.2521.326.45。
37.实施例2
38.表3实施例2所用高镍锍主要成份(%)及贵金属含量(g/t)
39.nicucofesagauptpd44.2520.320.513.5124.12553.357.532.12。
40.具体实施过程:将高镍锍和加压浸出液混合鼓空气搅拌反应,温度80℃,反应6h后,测ph为4.85,固液分离,得到一段常压浸出液;一段常压浸出渣加入水和理论量0.85倍的硫酸进行二段常压浸出,控制液固比为8∶1,鼓空气搅拌反应7h,温度85℃,测ph为2.35;二段常压浸出浆料直接进入加压釜,控制加压温度180℃,氧分压0.1mpa,反应时间1.0h后,
停止通氧,并适当降温排气,将加压釜中残留的氧气排出;继续升温到180℃,保温反应1.5h后降温泄压,出加压釜,物料进行固液分离,得到加压浸出渣(外付铜渣),加压浸出液返回一段常压浸出工序;一段常压浸出液继续进加压釜进行加压氧化除铁,控制加压除铁温度180℃,氧分压0.2mpa,反应时间1.5h,反应结束后降温、泄压,出釜进行固液分离,得到铁渣和除铁后液(外付硫酸镍钴溶液)。硫酸镍钴溶液、铁渣成份及铜渣成份如表4。
41.表4实施例2硫酸镍钴溶液、铁渣成份及铜渣成份检测分析结果
42.名称nicucofesagauptpd硫酸镍溶液g/l60.280.0010.890.23
ꢀꢀꢀꢀꢀ
铁渣%0.680.0140.0962.561.72
ꢀꢀꢀꢀ
铜渣%1.1365.690.112.3623.351067.2520.515.89。
43.实施例3
44.表5实施例3所用高镍锍主要成份(%)及贵金属含量(g/t)
45.nicucofesagauptpd40.8525.450.604.8623.82502.898.422.85。
46.具体实施过程:将高镍锍和加压浸出液混合鼓空气搅拌反应,温度85℃,反应7h后,测ph为5.0,固液分离,得到一段常压浸出液;一段常压浸出渣加入水和理论量0.9倍的硫酸进行二段常压浸出,控制液固比为7:1,鼓空气搅拌反应7h,温度85℃,测ph为2.52;二段常压浸出浆料直接进入加压釜,控制加压温度170℃,氧分压0.2mpa,反应时间1.0h后,停止通氧,并适当降温排气,将加压釜中残留的氧气排出;继续升温到170℃,保温反应1.5h后降温泄压,出加压釜,物料进行固液分离,得到加压浸出渣(外付铜渣),加压浸出液返回一段常压浸出工序;一段常压浸出液继续进加压釜进行加压氧化除铁,控制加压除铁温度160℃,氧分压0.2mpa,反应时间2.0h,反应结束后降温、泄压,出釜进行固液分离,得到铁渣和除铁后液(外付硫酸镍钴溶液)。硫酸镍钴溶液、铁渣成份及铜渣成份如表6。
47.表6实施例3硫酸镍钴溶液、铁渣成份及铜渣成份检测分析结果
48.名称nicucofesagauptpd硫酸镍溶液g/l66.220.0010.830.25
ꢀꢀꢀꢀꢀ
铁渣%0.560.0120.01160.141.83
ꢀꢀꢀꢀ
铜渣%0.8568.690.101.3622.861127.8621.236.75。
49.实施例4
50.表7实施例4所用高镍锍主要成份(%)及贵金属含量(g/t)
51.nicucofesagauptpd35.8629.370.584.2522.98552.567.983.01。
52.具体实施过程:将高镍锍和加压浸出液混合鼓空气搅拌反应,温度85℃,反应6h后,测ph为4.95,固液分离,得到一段常压浸出液;一段常压浸出渣加入水和理论量0.85倍
的硫酸进行二段常压浸出,控制液固比为7∶1,鼓空气搅拌反应6h,温度85℃,测ph为2.98;二段常压浸出浆料直接进入加压釜,控制加压温度170℃,氧分压0.2mpa,反应时间1.5h后,停止通氧,并适当降温排气,将加压釜中残留的氧气排出;继续升温到180℃,保温反应2.0h后降温泄压,出加压釜,物料进行固液分离,得到加压浸出渣(外付铜渣),加压浸出液返回一段常压浸出工序;一段常压浸出液继续进加压釜进行加压氧化除铁,控制加压除铁温度200℃,氧分压0.1mpa,反应时间1.0h,反应结束后降温、泄压,出釜进行固液分离,得到铁渣和除铁后液(外付硫酸镍钴溶液)。硫酸镍钴溶液、铁渣成份及铜渣成份如表8。
53.表8实施例4硫酸镍钴溶液、铁渣成份及铜渣成份检测分析结果
54.名称nicucofesagauptpd硫酸镍溶液g/l58.220.0110.820.31
ꢀꢀꢀꢀꢀ
铁渣%0.460.0100.00962.141.76
ꢀꢀꢀꢀ
铜渣%1.066.690.122.3623.861216.8620.357.76。