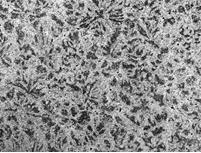
1.本发明涉及铝合金制备技术领域,具体为一种7050合金材料及其铸锭制备方法。
背景技术:2.7075 铝合金结构紧密,耐腐蚀效果强,对于航空、船用板材最佳,随着航空航天业的快速发展,7050 合金的需求量越来越大,但 7050 高强高韧铝合金存在铸造成型难,内部冶金差的问题,按传统工艺生产的产品达不到技术要求。
3.中国专利:一种高性能al-zn-mg-cu系合金,专利授权号:cn 113481416 a,专利授权日:2021年10月8日,提到的合金制备可以制备出比现有铝合金更高综合性能的产品,所述产品具有高强高韧、高淬透性、低方向敏感性、可热处理强度等特性,但是以上制备工艺存在以下缺点:(1)采用al99.95铝锭,铝锭成本高;(2) 该合金合金化程度很高,铸造难度大,铸造时容易产生中心裂纹;(3) 采用单级过滤,由于 7050 合金造渣严重,单级过滤不能完全去除熔体中的杂质;(4)缺少cr、ti和be元素,减弱了细化晶粒的作用,因此需要设计一种低成本大规格7050合金铸锭制备方法来解决上述问题。
技术实现要素:4.本发明所要解决的技术问题是克服7050铸造难度大,大规格扁锭铸造成本高,生产效率低下的问题,提供一种7050合金材料及其铸锭制备方法,该合金属于高强高韧铝合金。
5.本发明涉及一种7050合金铸锭材料,材料的化学元素及其质量百分比如下:si ≤ 0.12%、fe ≤ 0.15%、cu 为 2.0%~2.6%、mn ≤ 0.10%、mg 为 1.9%~ 2.6%、cr ≤ 0.04%、zn 为 5.7%~ 6.7%、ti ≤ 0.06%、zr 为 0.09%~ 0.14%、be为0.0005~ 0.02%,余量为铝和不可避免的杂质。
6.本发明的进一步改进在于:方法步骤如下:步骤一:配料;步骤二:熔炼:首先,在熔炼炉中加入al99.7铝锭和al99.85铝锭、铝铜合金、锌锭、钛剂,待全部熔化后扒渣;其次,加入铝锆合金、金属镁锭和铝铍合金,搅拌均匀,加入al-5ti-1b丝用量,350cm/min/3根锭;再次,取样分析,调整成分使所有成分都达到控制范围;最后,进行炉内精炼并扒渣,控制钠含量≤0.0005%,静置20-40min,然后控制金属温度达到合理的铸造温度;步骤三:铸造:使用普通铸造机,对结晶器底座贴纤维纸,均匀冷却强度,配合杠杆液位控制器和刮水器进行铸造,将熔炼后的物质铸造成铸锭;步骤四:均热:对铸锭进行均匀后处理;
步骤五,锯切:将铸锭底部锯切200mm;步骤六:铣面:对均匀处理后的铸锭进行铣面。
7.本发明的进一步改进在于:在步骤二的熔炼中:炉前控制ti含量≤0.035%,熔炼温度≤780℃,精炼温度740-760℃。
8.本发明的进一步改进在于:在步骤二的熔炼中:取样分析的成分范围即si ≤ 0.12%、fe ≤ 0.15%、cu 为 2.0%~2.6%、mn ≤ 0.10%、mg 为 1.9%~ 2.6%、cr ≤ 0.04%、zn 为 5.7%~ 6.7%、ti ≤ 0.06%、zr 为 0.09%~ 0.14%、be为0.0005~ 0.02%,余量为铝和不可避免的杂质;本发明的进一步改进在于:在步骤二的熔炼中,添加be元素,让使得铸造过程中,凝固壳表面的氧化膜更加致密,减少氧化膜表面裂纹的可能,避免了因氧化膜表面开裂造成的裂纹倾向。
9.本发明的进一步改进在于:在步骤二熔炼中,进行炉内精炼。精炼能够去除铝液中的氢气,并让铝液中的渣随气体上浮,然后扒渣操作将渣去除,避免铸件中气孔和夹渣的产生;炉内精炼采用"t"型精炼器,精炼气体为氩氯混合气,应保持精炼器在熔体下层缓慢移动,使精炼气体遍及熔体; 精炼时间大于等于30min。
10.本发明的进一步改进在于:在步骤三铸造中,对结晶器底座贴纤维纸,相比传统的底部纯铝铺底工艺,能够有效地均匀底部冷却强度,使得内应力均匀,避免底部开裂的可能。
11.本发明的进一步改进在于:在步骤三铸造中,使用刮水器,并对刮水器装置进行改进;普通刮水器的大面为平直的,小面与结晶器小面形状相同,经改进后的刮水器大面适应铸锭大面的收缩形状,小面与结晶器小面形状相同;该改进能够优化冷却水流的流向,均匀冷却强度;增加刮水器会比传统铸造工艺的冷却强度小,冷却效果比传统冷却更加均匀,尽可能的减少铸造过程中的裂纹产生。
12.本发明的进一步改进在于:在步骤三铸造中,铸造的参数中包括:结晶器液位高度5-8cm,铸造温度700-720℃,铸造速度40-50mm/min,水流量80-100m3/h,水温≤30℃。
13.本发明的进一步改进在于:在步骤五铣面中,铸锭正面铣面量为10-15mm/每面,侧面铣面量为10-20mm/每面。
14.本发明的有益效果:1.在熔炼炉中加入al99.7铝锭和al99.85铝锭,铝锭成本降低并且在熔炼炉中进行熔化,在静置炉中进行精炼除气,将精炼好的铝液导入到流槽中,并用al-5ti-1b 丝进行在线细化;2.炉前控制ti含量≤0.035%,对结晶器底座贴纤维纸,均匀冷却强度,进而均匀内应力,减少裂纹倾向;添加be元素,让使得铸造过程中,凝固壳表面的氧化膜更加致密,减少氧化膜表面裂纹的可能,避免了因氧化膜表面开裂造成的裂纹倾向,并提高al-5ti-1b丝用量,350cm/min/3根锭,减少了中心裂纹的不良率;使用刮水器,并对刮水器装置进行改进,由于普通刮水器的大面为平直的,小面与结晶器小面形状相同,经改进后的刮水器大面适应铸锭大面的收缩形状,小面与结晶器小面形状相同。该改进能够优化冷却水流的流向,均匀冷却强度,增加刮水器会比传统铸造工艺的冷却强度小,冷却效果比传统冷却更加均匀,尽可能的减少铸造过程中的裂纹产生;
3.经过在线除气,可以提高铸造成功率,进行炉内精炼,精炼能够去除铝液中的氢气,并让铝液中的渣随气体上浮,然后扒渣操作将渣去除,避免铸件中气孔和夹渣的产生;炉内精炼采用"t"型精炼器,精炼气体为氩氯混合气,应保持精炼器在熔体下层缓慢移动,使精炼气体遍及熔体; 精炼时间大于等于30min,可以完全去除熔体中的杂质并且提高了生产效率;4.在合金材料中增加cr可以形成碳化物,起到提高耐磨性、耐热性和细化晶粒的作用、增加辅助元素ti可以起到细化晶粒的作用,增加适量的be可以起到细化铝合金晶粒的作用,提高综合力学性能,对铝合金而言,进行晶粒细化而获得细小均匀的等轴晶组织有如下作用:提高材料的屈服强度;改变了第二相的形态、尺寸和分布,使组织分布趋于均匀,减少偏析倾向;改善了塑性变形过程中沿晶粒边界的应力分布,并且在各个部位均匀一致,从而提高了加工工艺性能,在轧制和挤压过程中,易于突破挤压提高轧制速度而不引起裂纹,尤其有助于消除dc铸造和水平连铸铝材的裂纹;改善了铝制品表面处理的外观质量,减少形成条纹的倾向,从而提高了使用价值。
附图说明
15.图1为本发明的实施例一中金相图片边部100
×
放大图的示意图;图2为本发明的实施例一中金相图片芯部100
×
放大图的示意图;图3为本发明的实施例二中金相图片边部100
×
放大图的示意图;图4为本发明的实施例二中金相图片芯部100
×
放大图的示意图。
具体实施方式
16.一种7050合金材料,它的化学元素及其质量百分比如下:si ≤ 0.12wt%、fe ≤ 0.15wt%、cu 为 2.0wt%~2.6wt%、mn ≤ 0.10wt%、mg 1.9wt%~ 2.6wt%、cr ≤ 0.04wt%、zn 为 5.7wt%~ 6.7wt%、ti ≤ 0.06wt%、zr 0.09wt%~ 0.14wt%、be为0.0005~ 0.02%,余量为铝和不可避免的杂质,为了得到晶粒细小的铸造组织,加工和成品性能提供条件。
17.在本发明中,合金材料在轧制时容易产生断裂,由于微量元素na对该合金的断裂行为有显著影响,na含量较低时合金热轧塑性提高,热轧过程中几乎不发生断裂。这对后续成品的延伸率有着影响,本发明中na的含量应不高于0.0005wt%;zn、mg在该合金材料中起到强化作用,且强化效果明显;zr、be起到一定的补充强化作用;fe和si元素做为杂质存在,在该合金中,fe/si应予以控制,fe》si+0.05%,这对后续冲压具有影响;通过以上成分及其质量百分比的控制使铝合金性能得到大幅度提升,可在强度高,抗腐蚀性能强的高应力结构体上得到应用。
18.为了使得制备工艺可行、质量稳定,并且使7050铝合金材料能够达到相应的性能,该7050铝合金材料的制备方法,方法的步骤中含有:步骤一,配料;采用99.7%和99.85%的铝锭、锌锭、金属镁锭、铝锆合金、钛剂,按照内控化学成分以及铸锭的规格、数量确定以上投料量。
19.步骤二,熔炼:完成上述计算步骤后,在熔炼炉中加入铝锭和钛剂,待金属全部熔
化,且金属温度达到740-760℃时开始扒渣,然后依次加入锌锭、金属镁锭、铝锆合金、铝铍合金,搅拌均匀,然后取样分析,调整成分使所有成分都达到控制范围,即:si ≤ 0.12wt%、fe ≤ 0.15wt%、cu 为 2.0wt%~2.6wt%、mn ≤ 0.10wt%、mg 1.9wt%~ 2.6wt%、cr ≤ 0.04wt%、zn 为 5.7wt%~ 6.7wt%、ti ≤ 0.06wt%、zr 0.09wt%~ 0.14wt%、be为0.0005~ 0.02%,余量为铝和不可避免的杂质;然后进行炉内精炼并扒渣;步骤三,铸造:提前对结晶器底座贴纤维纸,待金属温度达到合理的铸造温度,开始铸造,铸造过程中金属从炉内流出来,经过流槽输送,进行在线除气、在线晶粒细化、在线过滤后,金属进入铸造模具中成型,使用普通铸造机,配合杠杆液位控制器和刮水器铸造成为需要规格的铸锭;步骤四,均热:到均热炉内进行均匀化处理,出炉后自然冷却到常温;步骤五,锯切:将铸锭底部锯切200mm;步骤六,铣面:通过铣床将表面和侧面进行铣削;在熔炼步骤中:炉前控制ti含量≤0.035%,熔炼温度≤780℃,熔炼温度≤780℃,精炼温度740-760℃。
20.在铸造步骤中铸造的参数中包括:结晶器液位高度5-8cm,铸造温度(分流盘末端温度)700-720℃,铸造速度40-50mm/min,水流量80-100m3/h,水温≤30℃。
21.在铣面步骤中,铸锭正面铣面量为10-15mm/每面,侧面铣面量为10-20mm/每面,需将侧面完全铣净。
22.为了使本发明的内容更容易被清楚地理解,下面根据具体实施例,对本发明作进一步详细的说明。
23.实施例一一种低成本大规格7050合金材料,它的化学元素及其质量百分比如下:si ≤ 0.12wt%、fe ≤ 0.15wt%、cu 为 2.0wt%~2.6wt%、mn ≤ 0.10wt%、mg 1.9wt%~ 2.6wt%、cr ≤ 0.04wt%、zn 为 5.7wt%~ 6.7wt%、ti ≤ 0.06wt%、zr 0.09wt%~ 0.14wt%、be为0.0005~ 0.02%,余量为铝和不可避免的杂质。
24.具体材料制备方法包括如下步骤:步骤一,配料;采用99.7%和99.85%的铝锭、锌锭、金属镁锭、铝锆合金、钛剂,按照内控化学成分以及铸锭的规格、数量确定以上投料量,按0.25kg/吨铝加入铝铝铍合金。
25.步骤二,熔炼:完成上述计算步骤后,在熔炼炉中加入铝锭和钛剂,待金属全部熔化,且金属温度达到740-760℃时开始扒渣,然后依次加入锌锭、金属镁锭、铝锆合金、铝铍合金,搅拌均匀,然后取样分析,调整成分使所有成分都达到控制范围,即:si ≤ 0.12wt%、fe ≤ 0.15wt%、cu 为 2.0wt%~2.6wt%、mn ≤ 0.10wt%、mg 1.9wt%~ 2.6wt%、cr ≤ 0.04wt%、zn 为 5.7wt%~ 6.7wt%、ti ≤ 0.06wt%、zr 0.09wt%~ 0.14wt%、be为0.0005~ 0.02%,余量为铝和不可避免的杂质;然后进行炉内精炼并扒渣;步骤三,铸造:提前对结晶器底座贴纤维纸,待金属温度达到合理的铸造温度,开始铸造,铸造过程中金属从炉内流出来,经过流槽输送,进行在线除气、在线晶粒细化、在线过滤后,金属进入铸造模具中成型,使用普通铸造机,配合杠杆液位控制器和刮水器铸造成为需要规格的铸锭;步骤四,均热:到均热炉内进行均匀化处理,出炉后自然冷却到常温 ;
步骤五,锯切:铸锭底部锯切200mm,并取厚度为20mm样片用于检测;步骤六,铣面:通过铣床将表面和侧面进行铣削;在熔炼步骤中:炉前控制ti含量≤0.035%(检测值为0.002),熔炼温度≤760℃,精炼温度745℃。
26.在铸造步骤中铸造的参数中包括:结晶器液位高度6cm,铸造温度(分流盘末端温度)700℃,铸造速度40-50mm/min,水流量80-100m3/h,水温≤30℃。
27.在铣面步骤中,铸锭正面铣面量为10-15mm/每面,侧面铣面量为10-20mm/每面,需将侧面完全铣净。
28.低倍检测数据:实验结果分析:铸锭边部晶粒度1级,铸锭边部晶粒度1级,符合用户要求;铸锭的粗晶区和偏析区可在铣面工序将其铣净;金相检测中未发现组织过烧,和明显的夹渣、孔洞。检测结果符合铸锭检验要求。
29.实施例二一种低成本大规格7050合金材料,它的化学元素及其质量百分比如下:si ≤ 0.12wt%、fe ≤ 0.15wt%、cu 为 2.0wt%~2.6wt%、mn ≤ 0.10wt%、mg 1.9wt%~ 2.6wt%、cr ≤ 0.04wt%、zn 为 5.7wt%~ 6.7wt%、ti ≤ 0.06wt%、zr 0.09wt%~ 0.14wt%、be为0.0005~ 0.02%,余量为铝和不可避免的杂质。
30.配料;采用99.7%和99.85%的铝锭、锌锭、金属镁锭、铝锆合金、钛剂,按照内控化学成分以及铸锭的规格、数量确定以上投料量,按0.25kg/吨铝加入铝铝铍合金。
31.熔炼:完成上述计算步骤后,在熔炼炉中加入铝锭和钛剂,待金属全部熔化,且金属温度达到740-760℃时开始扒渣,然后依次加入锌锭、金属镁锭、铝锆合金、铝铍合金,搅拌均匀,然后取样分析,调整成分使所有成分都达到控制范围,即:si ≤ 0.12wt%、fe ≤ 0.15wt%、cu 为 2.0wt%~2.6wt%、mn ≤ 0.10wt%、mg 1.9wt%~ 2.6wt%、cr ≤ 0.04wt%、zn 为 5.7wt%~ 6.7wt%、ti ≤ 0.06wt%、zr 0.09wt%~ 0.14wt%、be为0.0005~ 0.02%,余量为铝和不可避免的杂质;然后进行炉内精炼并扒渣;铸造:提前对结晶器底座贴纤维纸,待金属温度达到合理的铸造温度,开始铸造,铸造过程中金属从炉内流出来,经过流槽输送,进行在线除气、在线晶粒细化、在线过滤后,金属进入铸造模具中成型,使用普通铸造机,配合杠杆液位控制器和刮水器铸造成为需要规格的铸锭;均热:到均热炉内进行均匀化处理,出炉后自然冷却到常温 ;锯切:铸锭底部锯切200mm,并取厚度为20mm样片用于检测铣面:通过铣床将表面和侧面进行铣削;
在熔炼步骤中:炉前控制ti含量≤0.035%(检测值为0.01%),熔炼温度≤765℃,精炼温度750℃。
32.在铸造步骤中铸造的参数中包括:结晶器液位高度6.2cm,铸造温度(分流盘末端温度)710℃,铸造速度40-50mm/min,水流量80-100m3/h,水温≤30℃。
33.在铣面步骤中,铸锭正面铣面量为10-15mm/每面,侧面铣面量为10-20mm/每面,需将侧面完全铣净。
34.低倍检测数据:实验结果分析:铸锭边部晶粒度1级,铸锭边部晶粒度1级,符合用户要求;铸锭的粗晶区和偏析区可在铣面工序将其铣净;因炉前钛含量控制与实施例一略有差异,铸锭边部和中部的晶粒尺寸在实施例二中更小;金相检测中未发现组织过烧,和明显的夹渣、孔洞。检测结果符合铸锭检验要求。
35.以上所述的具体实施例,对本发明解决的技术问题、技术方案和有益效果进行了进一步详细说明,所应理解的是,以上所述仅为本发明的具体实施例而已,并不用于限制本发明,凡在本发明的精神和原则之内,所做的任何修改、等同替换、改进等,均应包含在本发明的保护范围之内。