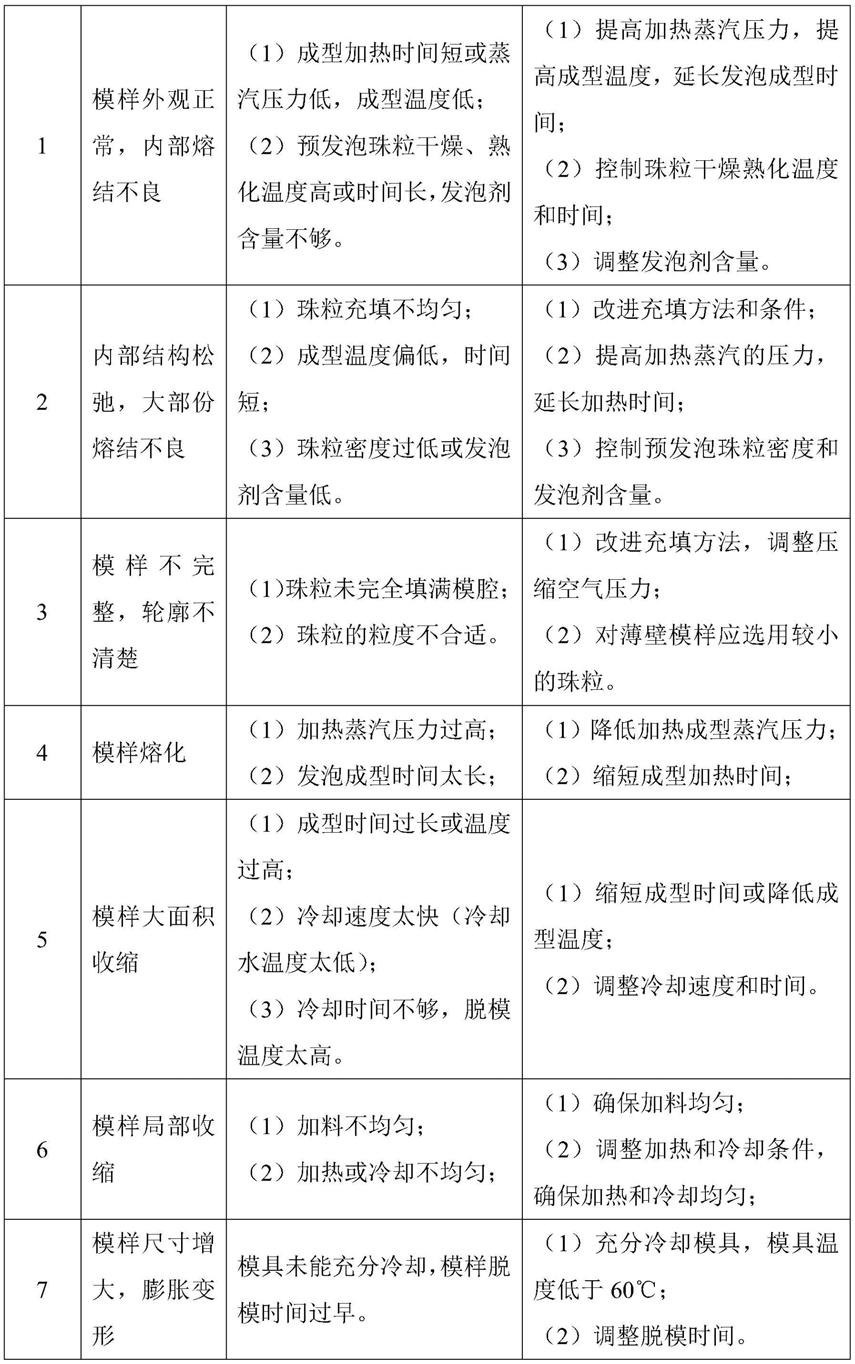
1.本技术涉及消失模铸造的技术领域,特别涉及一种消失模铸造板材的生产工艺。
背景技术:2.消失模铸造(又称实型铸造)是将与铸件尺寸形状相似的泡沫模型粘结组合成模型簇,刷涂耐火涂料并烘干后,埋在干石英砂中振动造型,在负压下浇注,使模型气化,液体金属占据模型位置,凝固冷却后形成铸件的新型铸造方法。
3.与传统的铸造技术相比,消失模铸造由于采用在高温下极易气化的eps、epmma、stmma或stmma-fd泡沫珠粒作模样,由于其具有使得到的铸件表面光洁度高、尺寸形状精确等众多优点,被认为是铸造工业的绿色革命。
4.而消失模的质量与其发泡后所形成板材的密度、密度均匀度、熔结性等性能息息相关。
技术实现要素:5.为了提高消失模铸造板材的质量,本技术提供一种消失模铸造板材的生产工艺。
6.本技术提供的一种消失模铸造板材的生产工艺,采用如下的技术方案:一种消失模铸造板材的生产工艺,包括以下步骤:s1、选样,根据铸件要求选择对应直径范围的模样珠粒;s2、预发泡,使用蒸汽对模样珠粒加热,并对模样珠粒搅拌处理,使模样珠粒膨胀完成发泡;s3、熟化,对预发泡后的模样珠粒进行通风熟化;s4、成型,将模具预热后,再将熟化后的模样珠粒加入模具进行填充;抽真空后通入蒸汽进行加热,其中,共进行四次蒸汽加热,且四次蒸汽加热分别从四个不同的加热面进行加热,加热面分别为板材的四个大面;s5、定型,当成型过程中蒸汽的穿透压力产生的膨胀点达到设定的值,开始启动真空,通过真空负压来冷却定型;直至模具内部达到稳压,然后关闭真空,开模将板材顶出;s6、陈化,将成型后的板材静置进行挥发处理。
7.通过采用上述技术方案,根据铸件选择合适直径的珠粒,然后在经过预发泡和熟化后进行成型,成型时先预热来缩短成型时间,同时,可以高成型的质量以及成型时模具腔室中的冷凝水。
8.然后分别对四个不同的加热面进行四次加热,可以有效保障加热的均匀性,有效提高发泡后所形成板材的密度、密度均匀度、熔结性等性能。之后通过真空负压来进行定型,在冷却时,由于模样泡体是热的不良导体,常常出现表层已被冷却固化定型,芯部的温度还很高的现象。这时如冷却定型不够,虽然皮层已固化定型,但是芯部的大量热量会继续向外传,使皮层温度回升,再加上模样芯部泡体的膨胀力,就可能出现三次发泡现象,使已定型的模样形状变形或破坏,而采用真空负压条件下冷却,能够有效避免该现象的出现。
9.最后进行陈化,使水、戊烷等挥发掉。
10.可选的:s2步骤中,在进料前,先用蒸汽对预发泡机预热至达到发泡所需的温度条件,其中,在预发泡过程中管道蒸汽压力控制在0.1~0.3mpa,预发泡机的膨胀室压力控制在0.03~0.06mpa,预发泡温度为90~100℃,发泡时间为38~60秒。
11.通过采用上述技术方案,上述调节设置,使珠粒的发泡效果较好,一方面不会消耗过多的发泡剂,另一方面可以使珠粒的表面光泽、圆润、有良好的回弹力。
12.可选的:加入预发泡机内的模样珠粒要求水份检测达到≤1%;且模样珠粒的挥发份的数据值检测≤9.5%时,发泡时间控制在55~65秒,挥发份的数据值检测≥9.5%时,发泡时间控制在36~45秒。
13.通过采用上述技术方案,可以对预发后的比重进行很好的控制,减少由于不稳定而造成的产品浪费与质量偏差,同时,进一步保障珠粒的表面光泽、圆润、有良好的回弹力。
14.可选的:s2步骤中,进料时预发泡机的搅拌轴工作频率小于发泡时预发泡机的搅拌轴工作频率,发泡时预发泡机的搅拌轴工作频率小于出料时预发泡机的搅拌轴工作频率。
15.通过采用上述技术方案,进料时搅拌来平铺原料,此时不需要很快的搅拌频率;而在进蒸汽后,需要让珠粒具有更均匀的受热,所以需要加快搅拌频率;最后在出料时,加快搅拌频率是为了达到快速排料的效果,原因在于此时虽然蒸汽停止了,但发泡桶内还有较高的温度,需要尽快排料,否则会导致珠粒继续发泡,造成发泡不均匀。
16.可选的:s3步骤中,模样珠粒的挥发份控制为7~8%。
17.通过采用上述技术方案,控制挥发份,以减少珠粒成型后三次发泡的可能性。
18.可选的:s4步骤中,模具预热过程中保持模具整体温度上升均匀。
19.通过采用上述技术方案,避免加热过快造成模具温度上升不均衡,从而造成模样表面珠粒熔融合不一致的现象。
20.可选的:s4步骤中,四个加热面依次加热一次,且两相对面依次进行加热;或,每次加热两个加热面,两加热面为相对面或相邻面,相邻两次加热不对同一加热面加热,且同时对两相对面的加热方式最多只能加热两次。
21.通过采用上述技术方案,可以更好的对芯部进行加热,同时,可以提高加热的均匀性,避免局部温度过高,从而使密度均匀度、熔结性等性能更好。
22.可选的:s4步骤中,四次加热的同时,可以同时分别从板材的两个小面通蒸汽加热,对两小面的加热蒸汽呈交错设置;小面的蒸汽压力小于四个大面的加热蒸汽压力。
23.通过采用上述技术方案,一方面可以提高两个小面所在端的熔结性,其次,可以进一步提高对芯部的加热效果。而交错进汽的设置,使一个小面同时有进汽和出汽端,进汽温度高、出汽温度高,如此可以形成一定的相互交错传递,使得板材在长度方向上整体的受热能够更加均匀。
24.而由于小面加热是一直保持的,经过第一次加热后就已经产生了熔接,所以需要采用更小的蒸汽压力,避免后续加热时出现小面被彻底熔接的情况出现,而导致蒸汽无法穿过。
25.可选的:s4步骤中,两相对的端面的两次加热的蒸汽压力和/或时间呈递减设置。
26.通过采用上述技术方案,板材已经会有蒸汽穿透产生的熔接,后续的穿透压力就
可以减小,如果蒸汽压力过大,表面彻底熔接了,蒸汽就穿不过去,会导致板材的内部熔接不良。
27.可选的:在s4和s5步骤中,均保持抽真空在-0.07~-0.08mpa的真空条件下,且两个步骤共保持真空状态380~430s。
28.通过采用上述技术方案,真空冷却定型,使板材不再膨胀,达到临界值,此时即可停止真空,而达到临界值的时间基本在380~430秒。
29.可选的:在关闭真空35~50秒后再开模。
30.通过采用上述技术方案,在关闭真空后,稳定35~50秒再开模取出,让板材在达到临界值后有个稳定的时间。
31.可选的:模具的侧壁呈可调节尺寸设置,在s4步骤中,模具腔室尺寸大于成品板材尺寸;在s5步骤中,通过模具侧壁对板材进行挤压至板材尺寸。
32.通过采用上述技术方案,可以填充更多的珠粒,而在成型进行小幅的挤压,可以形成更好的密度,且板材的外观质量也能够更好,可以减少外观质量缺陷的出现。
33.可选的:在s2步骤中完成发泡后,抽料5~20l进行密度测试,再根据测试结果调整下批次的投料量。
34.通过采用上述技术方案,根据前一批次珠粒的发泡结果,来调节后一批次珠粒的投料量,对珠粒的发泡密度进行管控,从而对发泡效果进行管控,保障板材的质量。
附图说明
35.图1是实施例一中珠粒预发泡后合格产品在显微镜观察下的结构图;图2是实施例一中珠粒预发泡后不合格产品在显微镜观察下的结构图;图3是实施例一的成型步骤中第一次蒸汽加热时的结构图;图4是实施例一的成型步骤中第二次蒸汽加热时的结构图;图5是实施例一的成型步骤中第三次蒸汽加热时的结构图;图6是实施例二的成型步骤中第四次蒸汽加热时的结构图;图7是实施例二的成型步骤中第一次蒸汽加热时的结构图;图8是实施例二的成型步骤中第二次蒸汽加热时的结构图;图9是实施例二的成型步骤中第三次蒸汽加热时的结构图;图10是实施例二的成型步骤中第四次蒸汽加热时的结构图。
具体实施方式
36.以下结合附图对本技术作进一步详细说明。
37.实施例1:一种消失模铸造板材的生产工艺,包括以下步骤:s1、选样,根据铸件最薄壁厚的十分之一为标准选择对应直径范围的模样珠粒,本实施例中将珠粒的直径范围可以分为0.25-0.35mm、0.25-0.35mm、0.40-0.55mm、0.45-0.60mm、0.60-0.90mm五个规格。
38.在选择时,看最薄壁厚的十分之一位于哪个规格的范围内即选择哪个规格的珠粒,原因在于选择的珠粒直径过大时,密度相应的会降低,而珠粒过小时,生产成本和难度会加大,所以选择适当的就行,如果对表面要求较高时,可以在上述基础上适当降低珠粒的
直径。而如果铸件表面要求较高时,则选择再细一个规格即可。
39.其中,规格数量也可以根据需要分成四个或五个以上,但常规而言,本实施例中分的五个规格已经适用大部分情况,分的太细会增加生产成本,而太粗则会影响成品质量。
40.s2、预发泡,本实施例采用间歇式蒸汽预发泡机,预发泡在进料前,先用蒸汽对预发泡机进行多次预热,通常需要进行5-8次,至达到发泡所需的温度条件,然后开始进料。
41.其中,模样珠粒在加入预发泡机前需要检测挥发份和水份含量,要求水份检测达到≤1%。并且,当模样珠粒的挥发份的数据值检测≤9.5%时,发泡时间控制在55~65秒;而挥发份的数据值检测≥9.5%时,发泡时间控制在36~45秒。
42.上述两发泡时间的数据值,具体需要按照预发设备、模样珠粒等不同进行调整。
43.在进料时,预发泡机的搅拌轴通常以28~35hz启动,此处搅拌保证珠粒达到平铺即可。
44.在预发泡过程中管道蒸汽压力控制在0.1~0.3mpa,预发泡机的膨胀室压力控制在0.03~0.06mpa,预发泡温度为90~100℃,发泡时间根据挥发份数据值进行控制。
45.而在进蒸汽发泡过程中,搅拌轴自动加大搅拌频率,通常为进料时的1.2~2倍,正常情况下变频为47~55hz即可。
46.完成发泡后打开预发泡机的料门,使珠粒进入流化床进行稳压,其原因在于珠粒的泡孔内是负压状态,需要流化床的热风定型,然后再进入到料仓熟化。其中,在出料时,预发泡机顶部开始送空气排料,搅拌轴自动加大搅拌频率,通常为发泡时的1.2~1.6倍,正常情况下自动变频为66~75hz即可。
47.并且,在出料过程中,自动系统抽料5~20l进入密度测试,常规抽料10l,系统记录并反馈给dws信息采集管理系统,dws信息采集管理系统核算出下一锅的投料量,再根据核算出的投料量投料来启动下个批次生产。
48.其中,在预发泡完成后,对抽取珠粒切片后在显微镜下40~50倍下观察,图1所示的为合格的产品,图2所示的为破损的不合格产品,上述预发泡正常情况下的观察结果与图1相近,如果观察结果与图1有一定差异时,可以对上述预发泡步骤中的具体参数进行调整。而如果出现图2所述的情况时,则需要停机检测原因。
49.s3、熟化,在料仓中对预发泡后的模样珠粒进行通风熟化,将模样珠粒的挥发份控制在7~8%,以减少珠粒成型后三次发泡的可能性。
50.珠粒的熟化时间一般控制为12~48小时,具体根据熟化设备、熟化的环境以及挥发份情况进行调节。
51.s4、成型,先将模具预热到85~100℃,具体预热温度由成型步骤中珠粒的发泡温度来定,使得预热温度和发泡温度趋于一致即可,通常为90℃,具体可以根据实际情况进行调整。
52.此外,在对模具预热的过程中,需要保持模具整体温度上升均匀。
53.在完成模具预热后,再将熟化后的模样珠粒加入模具进行填充,在填充过程中,需要确保填充均匀且紧实,否则将无法得到合格且高质量的产品。
54.完成填充后,抽真空至-0.07~-0.08mpa,通常取中间值-0.075mpa即可。完成抽真空后通入蒸汽进行加热,其中,共进行四次蒸汽加热,且四次蒸汽加热分别从四个不同的加热面进行加热,加热面分别为板材的四个大面。
55.加热的蒸汽温度不允许设置过高,正常采用85~100℃,而初始时保持在90℃上下,如果过高会导致内部熔结不良,而如果后续需要调整时,可以适当提高或降低温度。
56.如图3-图6所示,四个加热面依次加热一次,且两相对面依次进行加热。
57.并且,在对四个大面进行加热的同时,分别从两个板材的小面通蒸汽加热,一个小面同时分为进汽区和出汽区,使对两小面的加热蒸汽呈交错设置,这里需要注意的是,小面的蒸汽压力小于四个大面的加热蒸汽压力。
58.上述加热蒸汽的压力均控制0.07~0.1mpa,每次加热蒸汽的时间控制在6~13秒。其中,小面的蒸汽压力通常设置为0.07~0.8mpa即可,初始时以0.07mpa进行,后续根据产品质量情况进行适当提高。
59.其中,在相邻两次的加热过程中,即分别对两相对的端面加热时,两次加热的蒸汽压力和/或时间呈递减设置。此处需要说明的是,根据情况的不同,在时间递减设置的时候,蒸汽压力可以设置为保持相同或递增;或者在蒸汽压力递减设置的时候,时间可以设置为保持相同或递增。
60.s5、定型,当成型过程中蒸汽的穿透压力产生的膨胀点达到设定的值,开始启动真空,通过真空负压来进行冷却定型,直至模具内部达到稳压。
61.而在整个s4成型和s5定型的过程中,总共伴随真空380~430秒,具体时间根据板材达到临界值不再膨胀的时间为准。
62.在模具内部达到稳压后关闭真空,35~50秒后开模将板材顶出。35~50秒后开模目的是让板材有个稳定的时间,具体时间根据不同的珠粒直径、不同的发泡条件、不同密度要求的板材都会有所差异,通常设置40s左右即可。
63.s6、陈化,将成型后的板材放入养生区静置进行挥发处理,通常情况下在养生区静置1~3天后,再放入50℃的干燥房内,直至达到挥发份的检测值≤2%。
64.其中,在陈化过程中,虽然温度高点,烷的挥发会快一些。但不能采用直接烘干的方式进行,由于泡沫都具有绝缘性,内部的水是无法烘出来的,所以需要先静置。
65.如果不是在干燥房中进行则需要将静置时间延长。
66.其中,在生产过程中,珠粒材料、板材尺寸、模具结构、发泡密度等都对上述工艺中的各个参数有影响,因此,基于不同的情况需要对工艺进行适当的调整。
67.下表1为板材成品在生产过程中可能出现的一些缺陷即相关的解决办法。
表1
68.实施例2:与实施例1的不同之处在于:本实施例中的模具的侧壁成可调节尺寸设置,通常为开模所在侧的侧壁。
69.并且,在s4步骤中,模具腔室尺寸先设置成大于成品板材的尺寸,这样可以填充更多的珠粒。
70.而在s5步骤中,通过模具侧壁对板材进行挤压,通常挤压的幅度为该方向上板材尺寸的1/500~1/200。
71.其中,本实施例中在s4成型步骤中所有蒸汽加热的压力或/和时间可以适当降低0.02~0.06mpa。
72.实施例3:与实施例1的不同之处在于:每次加热两个加热面,每次加热的两加热面为相对面或相邻面,相邻两次加热不对同一加热面加热,且同时对两相对面的加热方式最多只能加热两次。
73.如图7~10所示,本实施例中先采用对两相对面进行同时加热的方式,在两次加热后,完成对四个加热面均进行一次加热后;此时中间区域的加热效果不佳。
74.因此,再采用对两相邻面同时加热的方式,在两次加热,再次完成对四个加热面均进行一次加热,能够对中间区域也起到较好的加热。
75.本具体实施方式的实施例均为本技术的较佳实施例,并非依此限制本技术的保护范围,故:凡依本技术的结构、形状、原理所做的等效变化,均应涵盖于本技术的保护范围之内。