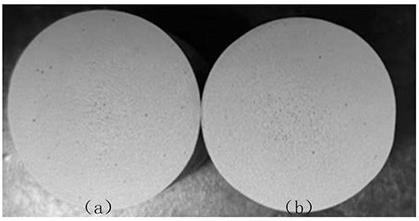
6号轻压下机架对应铸坯中心固相率均控制在0.8-1.0,单辊压下量控制在2.9-3.1mm;轧制的轴承钢圆钢的规格为15-30mm。
10.进一步地,在连铸工序中,末端电磁搅拌参数为400a
×
10hz。
11.进一步地,在连铸工序中,轻压下各机架间距控制在800mm。
12.进一步地,在连铸工序中,2-4号轻压下机架的单辊压下量均为2mm,5-6号轻压下机架的单辊压下量均为3mm。
13.进一步地,还包括的控制工艺是在轧制前铸坯经不低于1200℃的高温扩散加热,加热时间不低于300min,终轧温度控制在820-880℃,轧制后通过超快冷水箱,将表面温度快速降至650-700℃,抑制网状碳化物析出。
14.本发明中提高轴承钢圆钢酸洗低倍质量的机理为:针对较大断面连铸坯,一方面适当增加连铸坯横断面上的柱状晶比例,相较于等轴晶,柱状晶枝晶间溶质均匀,更耐腐蚀,另一方面利用密排的轻压下机架,通过调整拉坯速度,保证在合适的铸坯中心固相率下执行轻压下,补偿凝固过程体积收缩,减少铸坯心部局部溶质的富集,改善柱状晶比例升高对心部偏析带来的不利影响,提高断面均匀性,从而提高轧制后的轴承钢圆钢酸洗低倍质量。
15.相对于现有技术,本发明的有益效果为:生产检验发现酸洗孔洞多出现在轧材的心部区域,且轧材边部区域的耐酸蚀能力优于轧材心部区域的耐酸蚀能力,依据坯材的遗传性,调控连铸坯的凝固组织可从根本上改善轧材的酸洗低倍质量,本发明中的提高轴承钢圆钢酸洗低倍质量的生产控制方法通过对连铸工艺参数的控制,控制连铸坯的凝固组织,有效提高了后续轴承钢圆钢的酸洗低倍质量,从根本上提高了轴承钢的耐酸蚀能力;本发明保证铸坯心部较高过热度,以熔化等轴晶形核质点,进而促进柱状晶生长,随后利用密排的轻压下机架,在铸坯中心固相率0.3-0.8之间执行轻压下,补偿凝固过程体积收缩,减少偏析,随后在铸坯中心固相率0.8-1.0之间继续执行轻压下,减少残留的高溶质钢液在铸坯心部富集,减少中心偏析和疏松,从而达到控制连铸坯的凝固组织的目的,以此来提高轧制后的轴承钢圆钢的酸洗低倍质量;本发明中,还包括的控制工艺是在轧制前铸坯经不低于1200℃的高温扩散加热,加热时间不低于300min,终轧温度控制在820-880℃,轧制后通过超快冷水箱,将表面温度快速降至650-700℃,以抑制网状碳化物析出,高温扩散、控轧控冷工艺能起到继续改善轴承钢圆钢酸洗低倍质量的作用。
附图说明
16.图1为本发明中实施例1和实施例2轧制的20mm规格轴承钢圆钢的酸洗低倍形貌,其中(a)为实施例1轧制的20mm规格轴承钢圆钢的酸洗低倍形貌,(b)为实施例2轧制的20mm规格轴承钢圆钢的酸洗低倍形貌;图2为本发明中对比例1和对比例2轧制的20mm规格轴承钢圆钢的酸洗低倍形貌,其中(a)为对比例1轧制的20mm规格轴承钢圆钢的酸洗低倍形貌,(b)为对比例1轧制的20mm规格轴承钢圆钢的酸洗低倍形貌。
具体实施方式
17.一种提高轴承钢圆钢酸洗低倍质量的生产控制方法,包括连铸工序的控制工艺,连铸工序中采用连铸机进行连铸生产,得到的方形连铸坯断面尺寸为180-240mm,其中浇注温度比钢种液相线温度高40-50℃,即过热度控制在40-50℃,铸坯拉速控制在0.80-0.85m/min,二冷区比水量控制在0.14-0.20l/kg,结晶器电磁搅拌参数为150a
×
2hz,末端电磁搅拌参数为400a
×
10hz,轻压下各机架间距控制在790-810mm,2-4号轻压下机架对应铸坯中心固相率均控制在0.3-0.8,单辊压下量控制在1.9-2.1mm,5-6号轻压下机架对应铸坯中心固相率均控制在0.8-1.0,单辊压下量控制在2.9-3.1mm;还包括的控制工艺是在轧制前铸坯经不低于1200℃的高温扩散加热,加热时间不低于300min,终轧温度控制在820-880℃,轧制后通过超快冷水箱,将表面温度快速降至650-700℃,抑制网状碳化物析出,轧制的轴承钢圆钢的规格为15-30mm。
18.实施例1连铸工序中采用连铸机进行连铸生产,得到的方形连铸坯断面尺寸为240
×
240mm,其中浇注温度比钢种液相线温度高40℃,即过热度为40℃,铸坯拉速为0.80m/min,二冷区比水量为0.14l/kg,结晶器电磁搅拌参数为150a
×
2hz,末端电磁搅拌参数为400a
×
10hz,轻压下各机架间距为800mm,2-4号轻压下机架对应铸坯中心固相率分别为0.32、0.46、0.68,单辊压下量为2mm,5-6号轻压下机架对应铸坯中心固相率分别为0.93、1.0,单辊压下量为3mm;轧制前铸坯经1220
±
10℃左右的高温扩散加热,加热时间为360
±
10min,终轧温度为840
±
10℃,轧制后通过超快冷水箱,将表面温度快速降至680
±
10℃,抑制网状碳化物析出,最终轧制20mm规格的轴承钢圆钢。
19.实施例2连铸工序中采用连铸机进行连铸生产,得到的方形连铸坯断面尺寸为180
×
180mm,其中浇注温度比钢种液相线温度高50℃,即过热度为4550℃,铸坯拉速为0.85m/min,二冷区比水量为0.20l/kg,结晶器电磁搅拌参数为150a
×
2hz,末端电磁搅拌参数为400a
×
10hz,轻压下各机架间距为800mm,2-4号轻压下机架对应铸坯中心固相率分别为0.30、0.54、0.79,单辊压下量为2mm,5号轻压下机架对应铸坯中心固相率为0.99,单辊压下量为3mm;轧制前铸坯经1220
±
10℃左右的高温扩散加热,加热时间为320
±
10min,终轧温度为840
±
10℃,轧制后通过超快冷水箱,将表面温度快速降至680
±
10℃,抑制网状碳化物析出,最终轧制20mm规格的轴承钢圆钢。
20.对比例1连铸工序中采用连铸机进行连铸生产,得到的方形连铸坯断面尺寸为240
×
240mm,其中浇注温度比钢种液相线温度高20℃,即过热度为20℃,铸坯拉速为0.75m/min,二冷区比水量为0.23l/kg,结晶器电磁搅拌参数为450a
×
2hz,末端电磁搅拌参数为400a
×
10hz,轻压下各机架间距为1200mm,2-3号轻压下机架对应铸坯中心固相率分别为0.60、1.0,单辊压下量2-4mm;轧制前铸坯经1220
±
10℃左右的高温扩散加热,加热时间为360
±
10min,终轧温度为840
±
10℃,轧制后通过超快冷水箱,将表面温度快速降至680
±
10℃,抑制网状碳化物析出,最终轧制20mm规格的轴承钢圆钢。
21.对比例2连铸工序中采用连铸机进行连铸生产,得到的方形连铸坯断面尺寸为180
×
180mm,其中浇注温度比钢种液相线温度高20℃,即过热度为20℃,铸坯拉速为0.80m/min,二冷区比水量为0.28l/kg,结晶器电磁搅拌参数为450a
×
2hz,末端电磁搅拌参数为400a
×
10hz,轻压下各机架间距为1200mm,2-3号轻压下机架对应铸坯中心固相率分别为0.68、1.0,单辊压下量2-4mm;轧制前铸坯经1220
±
10℃左右的高温扩散加热,加热时间为320
±
10min,终轧温度为840
±
10℃,轧制后通过超快冷水箱,将表面温度快速降至680
±
10℃,抑制网状碳化物析出,最终轧制20mm规格的轴承钢圆钢。
22.如图1和图2所示,实施例1和实施例2中通过连铸工序的控制工艺,轧制的20mm规格轴承钢圆钢的酸蚀孔洞数量明显比对比例1和对比例2中轧制的20mm规格轴承钢圆钢的酸蚀孔洞数量少,因而相较于对比例,实施例1和实施例2轧制的20mm规格轴承钢圆钢的酸洗低倍质量明显得到提高,其耐酸蚀能力明显得到提高。综上,本发明中的提高轴承钢圆钢酸洗低倍质量的生产控制方法通过对连铸工艺参数的控制,控制连铸坯的凝固组织,有效提高了后续轴承钢圆钢的酸洗低倍质量,从根本上提高了轴承钢的耐酸蚀能力。