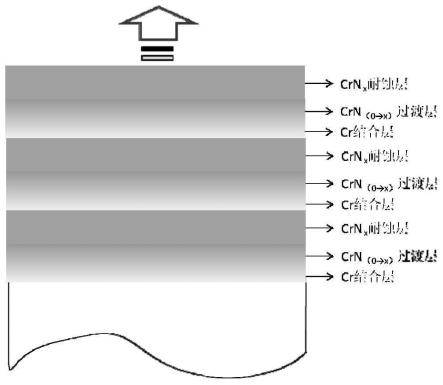
1.本发明涉及高强钢防腐蚀表面处理领域技术领域,特别涉及一种高强度钢表面无氢脆性镀层制品及其制备方法。
背景技术:2.高强钢零件在航天产品领域广泛应用,为避免零部件在制造、流转、运输过程中受结构腐蚀,高强钢及钢制弹性零件常采用电镀锌、镉进行防腐蚀处理。但是电镀工艺特性常带来氢脆问题。由于氢脆具有隐蔽性、延迟性和突发性等特点,一旦发生氢脆现象会导致灾难性后果。集团公司下发了“航天型号产品禁(限)用工艺目录及使用控制要求通知”,把易产生氢脆问题的电镀工艺和高强钢镀锌镀镉列为禁用工艺。为解决氢脆对材料性能的影响,一般选用低氢脆电镀、无氢脆达克罗涂层、无氢脆pvd膜层三种方法,其中,低氢脆电镀仍需除氢处理,无氢脆达克罗涂层存在耐磨性差、结合力不高的缺点,而pvd技术为无氢脆工艺,镀层抗蚀性尚可,耐磨性高。
3.在pvd涂层领域中同样存在着许多不同的技术,基于磁控溅射技术和多弧离子镀技术获得的pvd涂层最适合替代电镀镀层。国内外常见替代电镀镀层的pvd涂层有氮化物硬质层(tin、timen、crn、crmen等),防腐蚀单层(al、cu、ag、au等)及金属化合物层(ti3al、al2o3等)。其中crn涂层被广泛用作抗磨损、耐腐蚀的保护涂层。相对于电镀层,crn涂层的摩擦系数相当,但其内应力特别低,这使得该涂层可以制备得比较厚,比如汽车制造领域常利用厚度超过40μm的crn涂层作为保护涂层。由于属于铬家族,具有较好的耐蚀性,crn涂层也是最优先考虑的电镀层替代产品。
技术实现要素:4.本发明的目的在于提供一种高强度钢表面无氢脆性镀层制品及其制备方法,所制备的镀层为无氢脆性镀层,镀层与金属基底结合力强,可以增强高强钢零件的防腐蚀和耐磨性能,可以大幅提高其暴露在自然环境中的存储性能。
5.为了达到上述技术效果,本发明的技术方案是:提供一种高强度钢表面无氢脆性镀层制品,由基体和在基体表面沉积的镀层构成;所述基体表面沉积的镀层包括cr结合层、crn
(0
→
x)
过渡层、crn
x
功能层;
6.所述cr结合层、crn
(0
→
x)
过渡层和crn
x
功能层依顺序沉积在所述基体表面。
7.进一步的,所述基体的材料为抗拉强度大于1050mpa的高强度钢;
8.所述镀层的厚度为3~20μm,与基体金属结合牢固,不起泡、不脱落,镀层硬度hv为1473~2200,按qj 2027-1990进行中性盐雾试验120h无红锈,按gjb3032-97进行摩擦磨损实验,镀层磨损率小于1.5
×
10-4
mm3/nm。
9.进一步的,所述cr结合层厚度为10~500nm,crn
(0
→
x)
过渡层厚度为100~500nm,crn
x
功能层100~3000nm;
10.所述镀层结构可以为cr/crn
x
单层、cr/crn
x
/cr/crn
x
双层、(cr/crn
x
)3三层或(cr/
crn
x
)n多层中的任意一种,其中cr结合层、crn
(0
→
x)
过渡层、crn
x
功能层厚度可根据要求来调整。
11.进一步的,所述crn
(0
→
x)
过渡层中的x范围为0~1。
12.本发明的另一个技术方案提供一种上述高强度钢表面无氢脆性镀层制品的制备方法,包括如下步骤:
13.s1、基材的选取及预处理:
14.将表面抛光后的高强度钢分别在ht-2、丙酮溶液中超声清洗30min,烘干后,放入真空镀膜设备的工件旋转台上,真空室抽真空至1
×
10-3
pa;
15.s2、溅射清洗:
16.向真空室中通入ar气,启动偏压电源,对样件加-400~600v的偏压,cr靶电流0.3~1a,对靶表面进行预溅射15-25min,除去靶和零件表面的氧化物等杂质;
17.s3、镀cr结合层:
18.调节偏压至-60~100v,调节cr靶电流为0.3~6a,沉积时间5~30min,在基体表面沉积一层cr层;
19.s4、镀crn
(0
→
x)
过渡层:
20.调节偏压至-60~100v,在0~30min内,cr靶电流为0.3~6a,光发射辅助原子层沉积范围为90~30%;
21.s5、镀crn
x
功能层:
22.调节偏压至-60~150v,调节cr靶电流大小为2~5a,保持时间60~180min,光发射辅助原子层沉积范围为60~30%,制备crn功能层;
23.s6、周期结构cr/crn
x
镀层沉积:
24.重复步骤3-5,制备周期结构薄膜;
25.s7、关闭靶材偏压电源,持续通入氩气3h,薄膜制备完成。
26.进一步的,所述工作气体ar气流量为10~30sccm,工作气压为8.0
×
10-2
pa~1.0
×
10-1
pa。
27.进一步的,所述ar气纯度≥99.999%,n2气纯度≥99.999%,cr靶纯度≥99.6%。
28.本发明提供的高强度钢表面无氢脆性镀层制品及其制备方法,采用闭合场非平衡磁控溅射技术制备在高强度钢表面依次沉积cr结合层、crn
(0
→
x)
过渡层、crn
x
功能层耐蚀薄膜。本发明通过控制靶材电流、氩气流量、氮气流量等参数对梯度多层进行耐蚀涂层精确制备。
29.本发明利用闭合场非平衡磁控溅射技术,一方面通过调整膜层组织结构,降低膜层柱状生长,减少膜层内部缺陷。另一方面采用cr镀层与crn镀层交替沉积,缓解应力、消除热膨胀系数不匹配、增强韧性,可以进一步提高镀层抗蚀性,或者说在同样的镀层厚度上获得更高的防护性能,是替代在恶劣环境下使用的防护镀层(如镀镉)的良好途径。此外,本发明的制备方法具有工艺环保、膜层均匀致密性好、可批量化处理等特点,易于实现工业生产,具有良好的应用前景。
附图说明
30.下面结合附图对发明作进一步说明:
31.图1为一种高强度钢表面无氢脆性镀层制品的结构示意图;
32.图2为闭合场非平衡磁控溅射设备示意图
具体实施方式
33.以下结合附图和具体实施例对本发明提出的高强度钢表面无氢脆性镀层制品及其制备方法作进一步详细说明。根据下面说明和权利要求书,本发明的优点和特征将更清楚。需说明的是,附图均采用非常简化的形式且均使用非精准的比率,仅用以方便、明晰地辅助说明本发明实施例的目的。
34.实施例1
35.步骤1、基材的选取及预处理:将表面抛光后的高强度钢分别在ht-2、丙酮溶液中超声清洗30min,烘干后,放入真空镀膜设备的(非平衡磁控溅射设备)工件旋转台上,真空室抽真空至1
×
10-3
pa。
36.步骤2、溅射清洗:向真空室中通入ar气,启动偏压电源,对样件加-400v的偏压,cr靶电流0.3a,对靶表面进行预溅射15min,除去靶和零件表面的氧化物等杂质。
37.步骤3、镀cr结合层:调节偏压至-60v,调节cr靶电流为6a,沉积时间20min,在基体表面沉积一层cr层。
38.步骤4、镀crn
(0
→
x)
过渡层:调节偏压至-60v,在20min内,cr靶电流为6a,光发射辅助原子层沉积(oem)范围为60%。
39.步骤5、镀crn
x
功能层:调节偏压至-60v,调节cr靶电流大小为4a,保持时间180min,光发射辅助原子层沉积(oem)范围为60~30%,制备crn功能层。
40.步骤6、关闭靶材偏压电源,持续通入氩气3h,薄膜制备完成。
41.本实施案例沉积出的镀层,表面为银白色,涂层表面光亮平整。该无氢脆性镀层的厚度为3μm,与基体金属结合牢固,不起泡、不脱落,镀层硬度hv为1473,按qj 2027-1990进行中性盐雾试验120h无红锈,按gjb3032-97进行摩擦磨损实验,镀层磨损率小于1.5
×
10-4
mm3/nm。
42.实施例2
43.步骤1、基材的选取及预处理:将表面抛光后的高强度钢分别在ht-2、丙酮溶液中超声清洗30min,烘干后,放入真空镀膜设备的(非平衡磁控溅射设备)工件旋转台上,真空室抽真空至1
×
10-3
pa。
44.步骤2、溅射清洗:向真空室中通入ar气,启动偏压电源,对样件加-500v的偏压,cr靶电流0.5a,对靶表面进行预溅射20min,除去靶和零件表面的氧化物等杂质。
45.步骤3、镀cr结合层:调节偏压至-80v,调节cr靶电流为6a,沉积时间20min,在基体表面沉积一层cr层。
46.步骤4、镀crn
(0
→
x)
过渡层:调节偏压至-80v,在10min内,cr靶电流为4a,光发射辅助原子层沉积(oem)范围为60%。
47.步骤5、镀crn
x
功能层:调节偏压至-80v,调节cr靶电流大小为4a,保持时间90min,光发射辅助原子层沉积(oem)范围为60%,制备crn功能层。
48.步骤6、周期结构cr/crn
x
镀层沉积:重复步骤3-5两次,制备周期结构薄膜。
49.步骤7、关闭靶材偏压电源,持续通入氩气3h,薄膜制备完成。
50.本实施案例沉积出的镀层,表面为银白色,涂层表面光亮平整。该无氢脆性镀层的厚度为5.6μm,与基体金属结合牢固,不起泡、不脱落,镀层硬度hv为1856,按qj 2027-1990进行中性盐雾试验120h无红锈,按gjb3032-97进行摩擦磨损实验,镀层磨损率小于1.5
×
10-4
mm3/nm。
51.实施例3
52.步骤1、基材的选取及预处理:将表面抛光后的高强度钢分别在ht-2、丙酮溶液中超声清洗30min,烘干后,放入真空镀膜设备的(非平衡磁控溅射设备)工件旋转台上,真空室抽真空至1
×
10-3
pa。
53.步骤2、溅射清洗:向真空室中通入ar气,启动偏压电源,对样件加-400v的偏压,cr靶电流0.5a,对靶表面进行预溅射20min,除去靶和零件表面的氧化物等杂质。
54.步骤3、镀cr结合层:调节偏压至-80v,调节cr靶电流为6a,沉积时间30min,在基体表面沉积一层cr层。
55.步骤4、镀crn
(0
→
x)
过渡层:调节偏压至-80v,在10min内,cr靶电流为4a,光发射辅助原子层沉积(oem)范围为50%。
56.步骤5、镀crn
x
功能层:调节偏压至-80v,调节cr靶电流大小为4a,保持时间150min,光发射辅助原子层沉积(oem)范围为60%,制备crn功能层。
57.步骤6、镀cr结合层:调节偏压至-80v,调节cr靶电流为6a,沉积时间20min,在基体表面沉积一层cr层。
58.步骤7、镀crn
(0
→
x)
过渡层:调节偏压至-80v,在10min内,cr靶电流为4a,光发射辅助原子层沉积(oem)范围为50%。
59.步骤8、镀crn
x
功能层:调节偏压至-80v,调节cr靶电流大小为4a,保持时间120min,光发射辅助原子层沉积(oem)范围为60%,制备crn功能层。
60.步骤9、镀cr结合层:调节偏压至-80v,调节cr靶电流为6a,沉积时间10min,在基体表面沉积一层cr层。
61.步骤10、镀crn
(0
→
x)
过渡层:调节偏压至-80v,在10min内,cr靶电流为4a,光发射辅助原子层沉积(oem)范围为50%。
62.步骤11、镀crn
x
功能层:调节偏压至-80v,调节cr靶电流大小为4a,保持时间120min,光发射辅助原子层沉积(oem)范围为60%,制备crn功能层。
63.步骤12、关闭靶材偏压电源,持续通入氩气3h,薄膜制备完成。
64.本实施案例沉积出的镀层,表面为银白色,涂层表面光亮平整。该无氢脆性镀层的厚度为5.7μm,与基体金属结合牢固,不起泡、不脱落,镀层硬度hv为1856,按qj 2027-1990进行中性盐雾试验120h无红锈,按gjb3032-97进行摩擦磨损实验,镀层磨损率小于1.5
×
10-4
mm3/nm。
65.本说明书中未作详细描述的内容属于本领域专业技术人员公知的现有技术。对于本领域技术人员而言,显然本发明不限于上述示范性实施例的细节,而且在不背离本发明的精神或基本特征的情况下,能够以其他的具体形式实现本发明。因此,无论从哪一点来看,均应将实施例看作是示范性的,而且是非限制性的,本发明的范围由所附权利要求而不是上述说明限定,因此旨在将落在权利要求的等同要件的含义和范围内的所有变化囊括在本发明内。