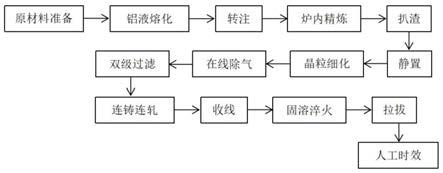
1.本发明涉及架空导线技术领域,具体而言,涉及一种抗拉强度≥380mpa、导电率≥54%iacs的新型高强高导铝合金单丝及其制备方法。
背景技术:2.我国已建成世界最长的架空导线输电线路,成为促进国民经济发展的能源主动脉,但是现有长距离、大跨越架空输电线路主要是由普通钢芯铝绞线组成,电能损耗较大。近期我国已提出实现碳达峰、碳中和的时间表,使用节能导线代替普通钢芯铝绞线大幅降低输电线路的电能损耗,成为架空输电领域重要的发展趋势。
3.我国国标高强度铝合金导线强度315~325mpa、导电率52.5%iacs,节能降耗效果不突出,如果将铝合金线的导电率和强度同时显著提高,绞合后得到高导电高强度铝合金导线,相对于常规钢芯铝绞线的性能优势会十分明显,因此,继续开发更高强度和导电率的合金材料具有重大经济和社会效益。
4.铝镁硅合金导线的强度和导电率是相互制约的,当提高强度后往往会使导电率明显下降,反之亦然。国内生产铝镁硅合金的工艺路线一般为熔炼
→
连铸连轧
→
拉拔
→
时效处理,合金强度或者导电率的改进主要是通过成分调整和工艺参数优化实现,基本工艺路线没有根本性的变化,一个指标的提升往往是以另一个指标的降低为代价,因此难以实现综合性能的大幅改善,如何较好的兼顾两者的指标成为了当前导电铝合金发展的关键。
5.尽管国内技术人员通过经验改进已实现合金强度和导电率的改善,例如专利公开号为cn104538116b、cn107841658b、cn106623478b的专利文献,但仍存在进一步提升空间。
技术实现要素:6.本发明的目的在于提供了一种新型高强高导铝合金单丝及其制备方法,能够提高铝合金单丝的综合性能,铝合金单丝的抗拉强度≥380mpa、导电率≥54%iacs。
7.本发明首先提供一种新型高强高导铝合金单丝,由按质量百分比计的下述成分组成:mg 0.5-0.6wt%,si 0.4-0.55wt%,sc 0.01-0.2wt%,fe0.1-0.15wt%,cu 0.01-0.08wt%,re 0.01-0.03wt%,b 0.001-0.005wt%,cr+mn+v+ti≤0.02wt%,其余为al和不可避免的其它杂质元素,不可避免的杂质元素中每种元素的含量均≤0.005wt%,不可避免的其它杂质元素的总量≤0.02wt%;
8.所述re为镧铈混合稀土元素,以al-re中间合金的形式加入。
9.所述的新型高强高导铝合金单丝抗拉强度≥380mpa、导电率≥54%iacs。
10.本发明还提供上述新型高强高导铝合金单丝的制备方法,包括如下步骤:
11.(1)铝液熔炼:向熔炼炉中加入纯度大于99.7%铝锭,熔炼铝液,加入铝硅合金、铝钪合金、铝稀土合金,加热熔化后搅拌扒渣,将金属镁锭压入铝液内部进行搅拌熔化,对熔化后的铝液充分搅拌均匀,取样进行光谱分析,控制铝液熔体成分在要求的范围内。
12.(2)炉内精炼:将熔炼炉中的铝液转注至保温炉,加入微量铝硼合金进行硼化处
理,进行充分搅拌,调整炉内铝液温度至740~750℃;对炉内铝液进行除气处理,控制铝液中氢含量≤0.3ml/100g。
13.(3)在线精炼:通过流槽从保温炉对铝液进行放流,浇铸开始后,熔体要经过在线精炼进一步提高纯净度,在线精炼包括对流槽内的铝液进行在线除气和在线过滤,控制铝液中氢含量≤0.12ml/100g,有效去除铝液中直径5~10μm的夹杂颗粒。
14.(4)连续铸造:经在线精炼后的铝液浇入轮式结晶器内进行连续铸造,形成铸坯。
15.(5)连续轧制:铸坯进入连轧机组中进行连续轧制,得到铝合金杆材,采用全自动收线装置进行收卷。
16.(6)固溶处理:对收卷后的铝合金杆材即铝镁硅合金杆材进行固溶处理,固溶处理加热温度为500~540℃,保温2~10h,然后将铝合金杆材送入水槽中淬火冷却。
17.(7)拉拔:对固溶处理后的铝合金杆材进行拉拔,得到直径为2.0~4.5mm的铝合金单丝。
18.(8)单丝时效:对拉拔后的铝合金单丝进行时效处理,时效工艺为150~180℃、保温时间8~15小时,得到新型高强高导铝合金单丝。
19.具体地,所述步骤(2)中,所述保温炉为倾动式保温炉,在加入铝硼合金,开启炉底电磁搅拌装置对铝液进行充分搅拌,控制铝液温度在740~750℃,利用高纯氮气和颗粒精炼剂对炉内铝液进行处理,时间为10~15分钟,随后将表面浮渣彻底扒净,调整铝液温度至710~730℃,静置处理30~60分钟。
20.具体地,所述步骤(3)中,采用旋转喷吹式除气箱对铝液进行在线除气,以高纯氮气为除气介质,转子转速为400~500r/min,经过在线除气处理后铝液中氢含量≤0.12ml/100g;采用双级泡沫陶瓷过滤板对铝液进行在线过滤,所述双级泡沫陶瓷过滤板的孔隙率为30/50ppi,有效去除5~10μm夹杂颗粒,在线过滤步骤也可以采用其他过滤装置,只要达到上述过滤效果或更优效果即可。
21.具体地,所述制备方法还包括在对铝液进行晶粒细化处理,具体在线除气之前,向流槽中在线添加细化剂对铝液进行晶粒细化,所述细化剂为铝钛硼杆,所述细化剂添加量为铝液质量的0.05%~0.15%。
22.具体地,所述步骤(4)中,铸坯截面积为2400mm2,铸造温度700~720℃、铸造速度8~12m/min、冷却水温度15~40℃、冷却水压0.35~0.5mpa。
23.具体地,所述步骤(5)中,控制入轧温度在500~520℃,所述连轧机组采用三辊轧机或二辊轧机,轧制后得到直径为9~12mm的铝合金杆材;通过在线冷却水对铝合金杆材进行冷却,采用自动收线装置进行收卷。
24.具体地,所述步骤(7)中,在滑动式拉丝机上对铝合金杆材进行拉拔,拉拔后软铝单丝直径控制范围为2.0~4.5mm,拉拔模具采用钨钢模,拉拔速度为8~10m/s。
25.优选地,所述步骤(8)中,时效处理时铝合金单丝线盘按节拍依次从时效炉入口端移动至出口端出料,从而确保所有单丝受热均匀。
26.本发明的有益效果:
27.针对目前工厂杆材在线淬火温度低导致合金元素固溶量少、单丝时效后强度偏低的问题,本发明通过杆材固溶淬火处理和单丝时效工艺优化,使mg、si等元素更多的以亚稳强化相析出,充分发挥合金元素的强化效应;同时在铝镁硅合金中引入sc元素,借助杆材的
固溶处理过程以al3sc相形式析出,产生弥散强化效应,这样在保证良好导电率的基础上大幅提高合金强度,实现铝合金单丝抗拉强度≥380mpa、导电率≥54%iacs。
附图说明
28.为了更清楚地说明本发明实施例的技术方案,下面将对实施例中所需要使用的附图作简单地介绍,应当理解,以下附图仅示出了本发明的某些实施例,因此不应被看作是对范围的限定,对于本领域普通技术人员来讲,在不付出创造性劳动的前提下,还可以根据这些附图获得其他相关的附图。
29.图1为本发明高导电率软铝单丝的制备方法的流程示意图。
具体实施方式
30.为使本发明实施例的目的、技术方案和优点更加清楚,下面将对本发明实施例中的技术方案进行清楚、完整地描述。实施例中未注明具体条件者,按照常规条件或制造商建议的条件进行。所用试剂或仪器未注明生产厂商者,均为可以通过市售购买获得的常规产品。
31.本发明通过合金组分的优化可确保铝合金单丝的抗拉强度≥380mpa、导电率≥54%iacs,本发明新型高强高导铝合金单丝,由按质量百分比计的下述成分组成:mg 0.5-0.6wt%,si 0.4-0.55wt%,sc 0.01-0.2wt%,fe0.1-0.15wt%,cu 0.01-0.08wt%,re 0.01-0.03wt%,b 0.001-0.005wt%,cr+mn+v+ti≤0.02wt%,其余为al和不可避免的其它杂质元素,不可避免的杂质元素中每种元素的含量均≤0.005wt%,不可避免的其它杂质元素的总量≤0.02wt%;
32.所述re为镧铈混合稀土元素,以al-re中间合金的形式加入。
33.请参阅图1,本发明提供的新型高强高导铝合金单丝的制备方法,包括如下步骤:
34.(1)铝液熔炼:向熔炼炉中加入纯度大于99.7%铝锭,熔炼铝液,加入铝硅合金、铝钪合金、铝稀土合金,加热熔化后搅拌扒渣,将金属镁锭压入铝液内部进行搅拌熔化,对熔化后的铝液充分搅拌均匀,取样进行光谱分析,控制铝液熔体成分在要求的范围内。
35.(2)炉内精炼:将熔炼炉中的铝液转注至10吨容量倾动式保温炉,加入微量铝硼合金进行硼化处理,开启炉底电磁搅拌装置对熔体进行充分搅拌,调整炉内铝液温度至740~750℃;利用高纯氮气和颗粒精炼剂对炉内铝液进行除气处理,时间为10~15分钟,控制铝液熔体中氢含量≤0.3ml/100g。随后调整温度至710~730℃静置处理40分钟。
36.(3)在线精炼:熔体在线精炼包括在线除气和过滤,在线除气以高纯氮气为除气介质,除气箱转子的转速为450r/min,经过处理后的熔体中氢含量≤0.12ml/100g;在线过滤采用双级泡沫陶瓷过滤板,孔隙率为30/50ppi,有效去除5~10μm夹杂颗粒。
37.具体地,具体在线除气之前还需要对铝液进行晶粒细化处理,向流槽中在线添加细化剂对铝液进行晶粒细化,所述细化剂为铝钛硼杆,所述细化剂添加量为铝液质量的0.05%~0.15%。
38.(4)连续铸造:经在线精炼后的铝液浇入轮式结晶器内进行连续铸造,形成铸坯;连续铸造过程采用轮式结晶器,铸坯截面积为2400mm2,铸造温度700~720℃、铸造速度8~12m/min、冷却水温度15~40℃、冷却水压0.35~0.5mpa。
0.15%,cu 0.03%,re 0.03%,b 0.004%,cr+mn+v+ti 0.017%,其余为al和不可避免的其它杂质元素,不可避免的杂质元素中每种元素的含量均≤0.005%,所得单丝强度为382mpa、导电率为54.38%iacs。
56.实施例2
57.步骤一:向熔炼炉中加入纯度大于99.7%铝锭、铝硅合金、铝钪合金、铝稀土合金加热熔化,将定量的金属镁锭压入铝液内部熔化。将熔化后的铝液充分搅拌均匀,取样进行光谱分析,控制熔体成分在要求的范围内。
58.步骤二:将铝液转注至10吨容量倾动式保温炉,加入微量铝硼合金进行硼化处理,开启炉底电磁搅拌装置对熔体充分搅拌。调整熔体温度至740℃,采用高纯氮气和颗粒精炼剂对熔体进行处理,时间为10分钟,控制铝熔体中氢含量≤0.3ml/100g。随后扒去表面浮渣,调整温度至720℃静置处理40分钟。
59.步骤三:浇铸开始后对熔体进行在线除气和过滤处理,在线除气采用旋转喷吹除气箱,以高纯氮气为除气介质。在线过滤采用双级泡沫陶瓷过滤板,孔隙率为30/50ppi。在线添加铝钛硼杆进行晶粒细化处理,细化剂添加量为0.07%。
60.步骤四:连续铸造过程采用轮式结晶器,铸坯截面积为2400mm2,铸造温度710℃、铸造速度10m/min、冷却水温度20℃、冷却水压0.37mpa。
61.步骤五:铸坯从结晶轮出来后剪掉头部10米长度,随后铸坯通过导入装置送入连轧机组,入轧温度为500℃。轧制过程在13机架三辊轧机中进行,轧制后得到直径为12mm的铝合金杆材,在线冷却后自动收杆。
62.步骤六:对合金杆进行固溶处理,固溶加热温度为500℃、保温时间为3h,随后用冷却水对杆材进行淬火冷却。
63.步骤七:在滑动式拉丝机上对杆材进行拉拔,拉拔后铝镁硅合金单丝直径为3.5mm。拉拔模具采用钨钢模,拉拔速度为9m/s。
64.步骤八:对拉拔后的铝合金单丝进行时效处理,时效工艺为155℃/9h。
65.经分析检测,本实施例中合金成分为:mg 0.56%,si 0.53%,sc 0.1%,fe 0.14%,cu 0.02%,re 0.025%,b 0.003%,cr+mn+v+ti 0.018%,其余为al和不可避免的其它杂质元素,不可避免的杂质元素中每种元素的含量均≤0.005%,所得单丝强度为387mpa、导电率为54%iacs。
66.对比例1
67.步骤一:向熔炼炉中加入纯度大于99.7%铝锭、铝硅合金、铝稀土合金加热熔化,将定量的金属镁锭压入铝液内部熔化。将熔化后的铝液充分搅拌均匀,取样进行光谱分析,控制熔体成分在要求的范围内。
68.步骤二:将铝液转注至10吨容量倾动式保温炉,加入微量铝硼合金进行硼化处理,开启炉底电磁搅拌装置对熔体充分搅拌。调整熔体温度至740℃,对熔体进行喷粉处理,时间为10分钟。随后扒去表面浮渣,调整温度至720℃静置处理40分钟。
69.步骤三:浇铸开始后对熔体进行在线除气和过滤处理,在线除气采用旋转喷吹除气箱,以高纯氮气为除气介质。在线过滤采用双级泡沫陶瓷过滤板,孔隙率为30/50ppi。在线添加铝钛硼杆进行晶粒细化处理,细化剂添加量为0.07%。
70.步骤四:连续铸造过程采用轮式结晶器,铸坯截面积为2400mm2,铸造温度710℃、
铸造速度10m/min、冷却水温度25℃、冷却水压0.38mpa。
71.步骤五:铸坯从结晶轮出来后剪掉头部10米长度,随后铸坯通过导入装置送入连轧机组,入轧温度为500℃。轧制过程在15机架三辊轧机中进行,轧制后得到直径为9.5mm的铝合金杆材,在线冷却水淬火后自动收杆。
72.步骤六:在滑动式拉丝机上对杆材进行拉拔,拉拔后铝镁硅合金单丝直径为3.8mm。拉拔模具采用钨钢模,拉拔速度为9m/s。
73.步骤七:对拉拔后的合金单丝进行时效处理,时效工艺为150℃/7h。
74.经分析检测,对比例中合金成分为:mg 0.61%,si 0.55%,fe 0.15%,cu 0.01%,re 0.033%,b 0.004%,cr+mn+v+ti 0.021%,其余为al和不可避免的其他杂质元素,不可避免的杂质元素中每种元素的含量均≤0.005%,所得单丝强度338mpa、导电率54.76%iacs。
75.通过上述实施例及对比例数据表明,本发明通过合金组分的优化,在铝镁硅合金中引入弥散强化效应更好的al3sc相,并通过杆材固溶淬火和单丝的长时间时效处理析出更多的亚稳强化相,在保证良好导电率的基础上实现强度性能的大幅提升,可以确保铝合金单丝的抗拉强度≥380mpa、导电率≥54%iacs。
76.本发明可应用于对强度要求较高的6201导电铝镁硅合金单丝的批量生产,也可用于其他对强度及导电率综合性能要求较高的铝合金单丝的生产制备。
77.以上所述仅为本发明的优选实施例而已,并不用于限制本发明,对于本领域的技术人员来说,本发明可以有各种更改和变化。凡在本发明的精神和原则之内,所作的任何修改、等同替换、改进等,均应包含在本发明的保护范围之内。
78.以上所述,仅为本发明的具体实施方式,但本发明的保护范围并不局限于此,任何熟悉本技术领域的技术人员在本发明揭露的技术范围内,可轻易想到的变化或替换,都应涵盖在本发明的保护范围之内。因此,本发明的保护范围应以所述权利要求的保护范围为准。