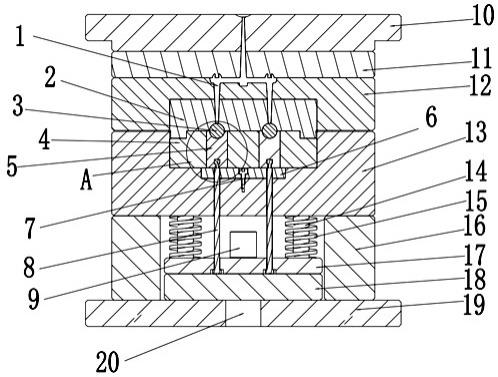
1.本实用新型涉及金属粉末注塑成型技术领域,具体涉及种金属注射成型模具顶出结构。
背景技术:2.金属注射成形,(简称mim)是一种从塑料注射成形行业中引伸出来的新型粉末冶金近净成形技术,其基本工艺过程为:首先是选择符合mim要求的金属粉末和粘结剂,然后在一定温度下采用适当的方法将粉末和粘结剂混合成均匀的注射成形喂料,经制粒后在注射成形机上注射成形,获得的成形坯经过脱脂处理后烧结致密化成为最终成品。金属注射成形技术在制备具有复杂几何形状、均匀组织结构和高性能的高精度近净形产品方面具有独特的优势。凡可以制成粉末的任何金属或合金均可用此方法制造零件。此外,该技术可以完全实现自动化连续作业,生产效率高。
3.原先金属注射成型模具使用的是常规的注塑模具顶针方案:顶针长度延长直接作用在产品面上,不过目前金属注射成型工艺生产的过程中,由于注射喂料的流动性较差,导致了注射压力偏大,模具的顶出系统在大注射压力下会变的非常不稳定,顶针头部相对于型腔面高度有很大变化,注射后的产品因为是树脂和金属粉末的混合材料,所以偏软。顶针与产品的接触面过小,使接触顶针的产品表面塌陷,导致注射成型后的产品顶针印高低明显,非常影响产品的外观、尺寸与性能。如果产品对顶针印要求高,生产的时候需要频繁的上下生产机床调整,非常的影响工作效率,而且在生产过程中,顶针印随着喂料或机器等外在因素的变化而变化,为生产带来了极大的品质隐患。
4.顶针高度影响产品的几个主要因素有:1.顶针与产品接触面较少,产品比较软,顶针顶出时会陷入产品表面。2.在极高的压力下,顶针的承托面在下顶针板上,距离较远,容易发生变动,从而影响顶针头部表面与产品胶位面的高度差。3.顶针较长,加工误差较大,模具组装的误差会导致顶针表面与产品胶位面相对尺寸出现偏差。
技术实现要素:5.本实用新型的目的在于针对粉末注射成型现有模具技术的缺陷和不足,特别是针对产品顶针印缺陷,如:顶针印高低不平,有台阶、凹陷,生产的过程中顶针印高低波动大。针对这样的情况,提供一种金属注射成型模具顶出结构。
6.为达到上述目的,本实用新型采用的技术方案是:一种金属注射成型模具顶出结构,其特征是它包括在动模仁固定板上设置有容纳动模仁的凹槽,在凹槽底部设置有容纳动模仁垫板的凹陷部,在动模仁固定板和动模仁垫板上对应顶针的安装位置设置有圆形通孔;动模仁上设置有产品成型胶位和供成型顶块通过的通孔;成型顶块顶部设置有与动模仁上一致的产品成型胶位,成型顶块尾部设置有容纳并连接顶针的内孔;成型顶块顶部与动模仁顶部齐平;动模仁垫板同时接触动模仁和成型顶块的底部。
7.本方案的具体特点还有,凹槽为方形凹槽且位置度要求在0.01mm以内,大小公差
要求在
±
0.005mm,动模仁镶嵌在动模仁固定板的方形凹槽中。
8.凹陷部是在动模仁固定板上位于动模仁的安装位置下方设置的矩形凹槽,动模仁垫板通过螺丝镶嵌在矩形凹槽里。动模仁垫板材质硬度为hrc60
‑
64。
9.成型顶块外形是四棱柱,成型顶块活动设置在动模仁的方形通孔内。成型顶块尾部的内孔为内凹的t形孔。
10.动模部分包括底板,在底板上面设置模脚,模脚上设置动模仁固定板。在模脚内侧,位于底板与动模固定板之间设置有下顶针板和上顶针板,顶针依次穿过设置于上顶针板上的上下贯通的圆形台阶通孔,动模仁垫板的圆形通孔插入到成型顶块的内孔中并与成型顶块连接固定。在动模仁固定板和上顶针板之间设置有回位导杆,弹簧和限位块,弹簧套装在回位导杆上。
11.回位导杆的尾部设有一个台阶,上顶针板的对应安装位置有一个圆形通孔和一个圆形沉台,回位导杆穿过弹簧,通过上顶针板的圆形通孔,通过动模固定板的圆孔,头部露出动模固定板上平面,回位导杆的尾部台阶沉入上顶针板的圆形沉台里。
12.顶针的头部是一个t形台阶,中部是一个圆柱体,尾部是一个台阶的圆柱体,在顶针与上顶针板的对应安装位置有一个圆形通孔和一个圆形台阶,动模仁固定板对应安装位置有一个圆形通孔,动模仁垫板对应位置有一个圆形通孔。顶针头部和中部穿过上顶针板的圆形过孔,穿过动模仁固定板的圆形过孔,穿过动模仁垫板的圆形过孔,插入到成型顶块的t形孔中连接固定;顶针尾部沉入上顶针板的圆形沉台里。
13.本实用新型的有益效果是: 1、成型顶块不受圆形顶针的限制,可以做各种形状和各种大小,完全与产品相匹配,所以成型顶块头部与产品相接触的胶位面可以设置的更大,是顶针的5
‑
20倍面积。2、成型顶块的尾部承托面在动模仁下方的动模仁垫板上,动模仁垫板的硬度为hrc60
‑
64加强了模具注射过程中动模仁和成型顶块的结构强度,因为把成型顶块底部的承受面缩短至动模仁底面位置,把顶出零件高度较长,影响顶针高低的风险降到了最低,使顶出零件的胶位面与动模仁上的胶位面更佳稳定一致。3、由于成型顶块的底面与动模仁的底面一致在同一平面。所以模具零件加工的的时候,便于把成型顶块装入动模仁中一起加工。以此保证加工完成后成型顶块产品胶位的高度与动模仁产品胶位高度完全一致,动模仁和成型顶块组装在一起,完成产品胶位的加工,确保动模仁上的胶位与成型顶块上的胶位高度、大小差异在0002mm以内。合模注射状态下,动模仁和成型顶块上下端面分别被定模仁和动模仁垫板压紧,成型顶块不会在动模仁方形贯穿孔内上下窜动。通过这种金属注射成型模具顶出结构的注射成型的产品顶针印高度与动模仁胶位的高度一致,外观顶出印不明显。没有凹陷台阶等不良特征。解决了金属注射成型模具顶出印明显,注射过程中生产品质不稳定,从而影响产品外观与性能的问题。
附图说明
14.图1是本实用新型基本结构示意图。图2是图1中的a部放大图。图3是本实用新型动模仁和成型顶块组装后的3d图。图4是图5动模部分3d视图。图5是本实用新型定模部分和动模部分分开示意图。图6是图5动模部分顶出动作后的示意图。图7是图4的b部放大图。
15.图中:1
‑
注射流道;2
‑
定模仁;3
‑
产品;4
‑
动模仁;5
‑
成型顶块;6
‑
动模仁垫板;7
‑
螺丝;8
‑
顶针;9
‑
限位块;10
‑
面板;11
‑
脱料板;12
‑
定模仁固定板;13
‑
动模仁固定板;14
‑
回位
导杆;15
‑
弹簧;16
‑
模脚;17
‑
上顶针板;18
‑
下顶针板;19
‑
底板;20
‑
顶杆过孔;21
‑
机台顶杆;22
‑
成型胶位面;23
‑
动模仁分型面;24
‑
止位面。
具体实施方式
16.如图1至图6所示,一种金属注射成型模具顶出结构,它包括定模部分(图5的上半部分)和动模部分(图5的下半部分)。
17.如图5所示,定模部分包括面板10,在面板10的底部设置有脱料板11、定模仁固定板12,在定模仁固定板12上设有方形凹槽,方形凹槽位置度要求在0.01mm,大小公差要求
±
0.01mm,定模仁2镶嵌在定模仁固定板12的方形凹槽中。
18.如图1所示,面板10和脱料板11上面设置有贯穿的圆锥孔道。定模仁固定板12设置长条状的槽道和圆锥孔道,定模仁2背面设置有圆锥孔道,当面板10,脱料板11、定模仁固定板12、定模仁2,在生产注射机合模状态下几块模板合并在一起,圆锥孔道和槽道就形成注射流道1。
19.如图5、图4所示,动模部分包括底板19,在底板19上面设置模脚16,模脚16上设置动模仁固定板13。在模脚16内侧,位于底板19与动模固定板13之间设置有下顶针板18和上顶针板17,顶针8依次穿过设置于上顶针板17上的上下贯通的圆形台阶通孔,动模仁垫板6的圆形通孔插入到成型顶块5的内孔中并与成型顶块5连接固定。在动模仁固定板13和上顶针板17之间设置有回位导杆14,弹簧15和限位块9,弹簧15套装在回位导杆14上。
20.回位导杆14的尾部是一个台阶的圆柱体,在上顶针板17的对应安装位置有一个圆形通孔和一个圆形沉台,回位导杆14通过弹簧中间的圆孔,通过上顶针板17的圆形通孔,通过动模固定板13的通孔,头部露出动模固定板上平面,尾部台阶沉入上顶针板17的圆形沉台里。上顶针板17上设置回位导杆14,回位导杆14所在位置的上顶针板17和动模仁固定板6都有通孔,通孔直径比回位导杆14双边尺寸大0.05mm以内。回位导杆14的尾部台阶位置被上顶针板17和下顶针板18合并固定。下顶针板18受机台顶杆21推力带动上顶针板17、回位导杆14、限位块9、弹簧15、顶针8向上运动。回位导杆14与动模仁固定板6中的回位导杆过孔做顺滑的配合滑动,为上述向上运动的部件提供了运动轨迹,起到了导柱的作用。
21.顶针8的头部是一个t形台阶,中部是一个圆柱体,尾部是一个台阶的圆柱体,在上顶针板17上的对应顶针8安装位置有一个圆形通孔和一个圆形台阶,在动模仁固定板13对应安装位置有一个圆形通孔,动模仁垫板13对应位置有一个圆形通孔。顶针8头部和中部穿过上顶针板17的圆形过孔,穿过动模仁固定板13的圆形过孔,穿过动模仁垫板6的圆形过孔,插入到成型顶块5的t形孔中连接固定;顶针8尾部沉入上顶针板17的圆形沉台里。顶针8头部为扁平的t型台阶结构,扁平方向的厚度小于成型顶块5上t形槽小槽的厚度。顶针8头部t型台阶先伸入成型顶块5上t型槽中,然后旋转90
°
,t型台阶与t形槽相互卡住连接。顶针8的头部t型台阶为扁型特征,模具组装时顶针8头部插入成型顶块5尾部t形槽中,然后旋转90
°
卡住,此时成型顶块5与顶针8固定一体。顶针8的尾部圆柱台阶侧边有一个平位,平位卡在上顶针板17圆形台阶的平位上。以此防止顶针8在生产过程中自由旋转。
22.在动模仁固定板13上设置有容纳动模仁4的方形凹槽,在方形凹槽底部设置有容纳动模仁垫板6的矩形凹槽,在动模仁固定板13和动模仁垫板6上对应顶针的安装位置设置有圆形通孔。如图1所示,动模仁4上设置有产品成型胶位(与产品3特征相仿)和供成型顶块
5通过的通孔。成型顶块5顶部设置有与动模仁4上一致的产品成型胶位,成型顶块5尾部设置有容纳并连接顶针的内孔。成型顶块5顶部与动模仁4顶部齐平。动模仁垫板6同时接触动模仁4和成型顶块5的底部。
23.方形凹槽位置度要求在0.01mm以内,大小公差要求在
±
0.005mm,动模仁4,镶嵌在动模仁固定板13的方形凹槽中。在动模仁固定板13上位于动模仁4的安装位置下方设有矩形凹槽,动模仁垫板6通过螺丝镶嵌在矩形凹槽里。动模仁垫板6材质硬度为hrc60
‑
64。
24.成型顶块5外形是四棱柱,成型顶块5活动设置在动模仁4的方形通孔内。成型顶块5尾部的内孔为内凹的t形孔。成型顶块5根据产品的要求,可以设置在产品的任意位置,成型顶块的数量根据需求可以选择1个、2个等等以此类推。
25.如图3所示动模仁4和成型顶块5组装在一起,完成产品3胶位的加工,确保动模仁4上的胶位与成型顶块5上的胶位高度、大小差异在0.005mm以内。
26.在下顶针板18底部设置有机台顶杆21。
27.如图1所示模具固定在注射机台上,喂料通过注射流道1进入到产品成型胶位3。
28.如图5所示产品经过冷却塑型后开模。定模部分与动模部分分开。
29.如图6所示机台顶杆21推动下顶针板18向上运动,模具的顶出动作开始:固定在下顶针板18上的上顶针板17、顶针8、回位导杆14、限位块9都向上运动。顶针8头部t形台阶与成型顶块5尾部的t形槽相互结合固定。顶针8向上运动的同时,成型顶块5也随之向上运动。模具胶位里的产品3被成型顶块5顶出模具胶位,产品3从模具胶位中分离。当顶出动作运动至限位块9与动模仁固定板13相接触。此时顶出动作结束,机台顶杆21回退,上顶针板17、下顶针板18受弹簧15压缩力的作用回退。顶针8尾部有台阶受上顶针板17沉头的作用力后退,顶针8头部t形台阶与成型顶块5尾部t形槽相连接,受顶针8影响,成型顶块5也随之向下退回原位。模具顶出的循环工作结束。
30.成型顶块5底部设置t型槽通孔,顶针8的头部也设置t型槽台阶形状。顶针的t型台阶装配在成型顶块的t型槽通孔内,利于t型槽的结构卡住双方紧密结合。顶针8拉住成型顶块5在动模仁4的方形通孔里做上下滑配运动。
31.成型顶块5尾部为t形槽结构,尾部端面平整可作为承托面。中部竖直上下同等大小,利于成型顶块5竖直运动。头部分为二部分:一部分为成型胶位面22,一部分为与定模接触的止位面24,止位面24与动模仁分型面23等高。成型顶块5和动模仁4底部基准一致,所以在零件加工的时候,把成型顶块5装入动模仁4内一起加工。加工完成后成型顶块5的产品胶位面与动模仁4的胶位面高度一致,可以做到0.005mm以内。所以具备非常好的产品外观效果。