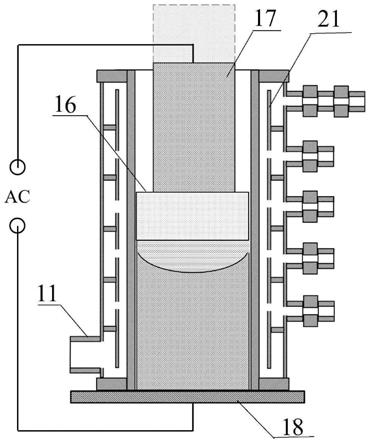
1.本发明属于钢铁冶金技术领域,具体涉及一种单进多出式水冷结晶器的电渣重熔装置和使用方法。
背景技术:2.随着电渣锭直径和合金钢中元素含量的不断提高,改善大尺寸电渣锭的中心偏析、细化晶粒尺寸是生产大尺寸锻件的重要途径。电渣重熔作为生产大尺寸锻件和高合金钢种的装备工艺,虽然一定程度上改善了电渣锭质量,但大尺寸电渣锭的中心仍存在凝固偏析、晶粒粗大等问题。尤其对于大尺寸的不锈钢、镍基合金、工模具钢等电渣锭,其凝固过程中产生的元素偏析及有害析出相等严重影响了电渣锭的大型化生产。因此,降低凝固偏析、细化组织晶粒是生产大尺寸锻件的关键。
3.目前电渣重熔的生产工艺为,电渣重熔初期先将少量的预熔渣置于结晶器底,在金属电极与底板的电弧热下熔渣逐步熔化,随后持续加入剩余熔渣进行熔化;当全部熔渣熔化完后形成液态渣池,将金属电极插入到液态渣池中,在液态渣池焦耳热和水冷结晶器的作用下,金属电极不断熔化成液滴穿过液态渣池,在水冷结晶器的作用下凝固成电渣锭,随着金属电极的不断熔化和电渣锭的不断升高,完成了整支电渣锭的制备。
4.现有技术的电渣重熔相比连铸坯虽然能够提升钢液的凝固速率,但对于高合金钢种的大尺寸电渣锭在凝固过程中仍存在较为严重的凝固偏析、晶粒粗大,尤其对于电渣重熔直径大于60cm的电渣锭,其金属熔池的凝固速率和电渣锭表面质量呈相反的关系。此外,通过优化水冷结晶器的冷却强度,虽然能够在保证电渣锭表面质量的前提下获得较好的内部质量,但其内部质量仍无法满足电渣锭大型化和产品高性能化的要求。
5.综上所述,电渣重熔中同时改善电渣锭内部质量和表面质量对于生产大型锻件具有重要的意义。
技术实现要素:6.本发明要解决的技术问题是同时提升电渣锭表面质量和内部质量,减轻凝固偏析、细化组织晶粒、降低tin、mns、aln等有害析出相,为大型锻件产品提供优质的电渣锭。
7.为了解决上述技术问题,本发明提供了一种单进多出式水冷结晶器的电渣重熔装置和使用方法,具体的,本发明采用如下技术方案:一种单进多出式水冷结晶器的电渣重熔装置,包括单进多出式水冷结晶器,其内部用于金属电极的重新熔化与再凝固,单进多出式水冷结晶器包括一个下进水口、多个出水口;多个出水口沿结晶器高度上下排列。
8.本发明公开了上述单进多出式水冷结晶器的电渣重熔装置在电渣重熔中的应用,该单进多出式水冷结晶器包括一个下进水口、多个出水口;多个出水口沿结晶器高度上下排列。
9.本发明公开了上述单进多出式水冷结晶器的电渣重熔装置在同时改善电渣重熔
铸锭电渣锭表面和内部质量中的应用,该单进多出式水冷结晶器包括一个下进水口、多个出水口;多个出水口沿结晶器高度上下排列。
10.作为常识,本发明单进多出式水冷结晶器的电渣重熔装置具有常规电渣重熔装置的基础部件以及结构,比如电源、水冷电缆、金属电极、底水箱、液态渣池、水冷结晶器以及金属熔池。水冷结晶器的外层和内层构成夹层,用于水流,水冷结晶器设有进水口、出水口,与水冷结晶器夹层连通,循环流动实现结晶器的冷却,本发明中,进水口位于水冷结晶器的下部,多个出水口沿着水冷结晶器的高度方向上下排列。优选的,多个出水口沿着水冷结晶器的高度方向上下竖直排列。进一步优选的,每个出水口设有流量调节阀,结晶器最顶部的出水口装有液体流量计,所有出水口最终全部接入回水总回路,回水总回路带有液体流量计。结晶器各个出水口的冷却水各自调节开闭,从而使得金属熔池v型区变浅、金属熔池凝固速率变快,细化电渣锭组织晶粒,同时改善电渣锭表面质量。
11.本发明中,多个出水口为2~15个,优选5~12个;出水口位于进水口上方,呈垂直排列在结晶器的不同高度上。多个出水口中,最下方的出水口与结晶器底面的距离大于20厘米,优选大于20厘米小于40厘米;多个出水口中,最上方的出水口、与最上方出水口相邻的出水口之间的距离大于25厘米,优选大于25厘米小于55厘米,即最顶部出水口位于结晶器最上端,次顶部出水口距离最顶部出水口的距离大于25厘米;多个出水口中,最下方的出水口、与最上方出水口相邻的出水口之间的出水口均匀分布,即其余出水口按高度平均分布在最下方出水口和次顶部出水口之间,保持间距一致。
12.优选的,单进多出式水冷结晶器的夹层内设有中间层,所述中间层通过隔板安装于夹层内壁,具体安装于外层内壁;隔板数量与单进多出式水冷结晶器的出水口数量一致,出水口与隔板间隔排列;中间层设有环形通水口,环形通水口数量与单进多出式水冷结晶器的出水口数量一致,环形通水口与隔板间隔排列。中间层的设置使得水冷效果更好。
13.本发明公开了使用上述单进多出式水冷结晶器的电渣重熔装置进行电渣重熔的方法,包括以下步骤:本发明公开了使用上述单进多出式水冷结晶器的电渣重熔装置进行电渣重熔的方法,包括以下步骤,电渣重熔装置的底水箱开启水冷,开启结晶器进水口与最上方的出水口,开始电渣重熔,且底水箱的水冷、结晶器进水口与最上方的出水口持续开启直至电渣重熔结束;当结晶器中液态渣池-金属熔池界面到达出水口上方4~6cm时,该出水口开启,其余出水口关闭,直至电渣重熔完成。
14.具体的:(1)采用上述由一个下进水口、一个最顶部出水口、多个沿结晶器高度方向上竖直排列的出水口组成的水冷结晶器,电渣重熔时,各个出水口的开闭根据结晶器内的液态渣池-金属熔池界面高度进行调节;(2)电渣重熔过程中,底水箱的循环冷却水始终呈开启模式、水冷结晶器最顶部的出水口始终呈开启冷却模式,其余出水口根据液态渣池-金属熔池界面高度依次开启和关闭;(3)电渣重熔开始,底水箱的循环冷却水呈开启模式、水冷结晶器采用下进水口进水、最顶部出水口出水、其余出水口关闭的单进单出的冷却模式;(4)随着电渣锭的不断升高,当液态渣池-金属熔池界面到达结晶器最下方的出水
口上方4~6cm时,该出水口(结晶器下端第一个出水口)和最顶部出水口呈开启模式,其余出水口呈关闭模式;(5)当液态渣池-金属熔池界面到达从结晶器下方数第二个出水口上方4~6cm时,该结晶器第二个出水口和最顶部出水口呈开启模式,其余出水口呈关闭模式;(6)当液态渣池-金属熔池界面到达从结晶器下方数第三个出水口上方4~6cm时,该结晶器第三个出水口和最顶部出水口呈开启模式,其余出水口呈关闭模式;(7)当液态渣池-金属熔池界面到达从结晶器下方数第四、五等出水口上方4~6cm时,以此类推、依次循环开启第四、五出水口和闭合其余出水口,保持结晶器的当前出水口和顶部出水口呈开启模式,其余出水口呈关闭模式。
15.本发明中,水冷结晶器侧壁设有夹层,夹层内设有中间层,中间层上设有环形通水口,用于循环水冷,底部设有底水箱,用于底部水冷。采用本发明由一个下进水口、多个沿结晶器高度方向上竖直排列的出水口组成的水冷结晶器,每个出水口的开闭能够调节,优选所有出水口水流量一样。
16.结晶器顶部的出水口一直开启使得液态渣池和上部分金属熔池圆柱区始终处于合理的冷却模式、电渣锭表面渣壳变薄;作为优选示例,当液态渣池-金属熔池界面到达当前出水口上方5cm时打开当前出水口,使得低于当前出水口高度的结晶器中水流量增加,对应高度的下部分金属熔池v型区和成型电渣锭的冷却强度显著增加,有利于金属熔池v型区变浅、金属熔池的凝固速率变快,降低了电渣锭中心偏析、细化组织晶粒,实现同时改善电渣锭表面和内部质量的目标。
17.为了控制结晶器不同高度上的各个出水口的开合时间,本发明还公开了一种根据金属电极下降高度计算液态渣池-金属熔池界面高度的方法,用于根据金属电极下降高度控制结晶器各个出水口的开合,其中结晶器的上圆口直径小于下圆口的直径,具有一定的锥度,其为常识。根据金属电极形状的不同,金属电极下降高度和液态渣池-金属熔池界面高度的关系可分为以下三种计算方法:(1)当金属电极为圆柱体时,以金属电极下端触碰到结晶器底部为零点。金属电极下降高度与液态渣池-金属熔池界面高度的变化关系为式(1):(1)其中金属电极半径为a,结晶器上圆口半径为r,结晶器下圆口半径为r,结晶器高度为l,液态渣池-金属熔池界面处的高度为h,金属电极下降高度为h,液态渣池的厚度为p。
18.(2)当金属电极为上圆直径大于下圆直径、带有一定锥度的圆棒时,大头朝上、小头朝下,以金属电极下端触碰到结晶器底部为零点。金属电极下降高度与液态渣池-金属熔池界面高度的变化关系如式(2):(2)其中金属电极小圆半径为a、大圆半径为a,金属电极长度为n,结晶器上圆口半径为r,结晶器下圆口半径为r,结晶器高度为l,液态渣池-金属熔池界面处的高度为h,金属电极下降高度为h,液态渣池的厚度为p。
19.(3)当金属电极为上圆直径小于下圆直径、带有一定锥度的圆棒时,大头朝下、小头朝上,以金属电极下端触碰到结晶器底部为零点。金属电极下降高度与液态渣池-金属熔池界面高度的变化关系如式(3):(3)其中金属电极小圆半径为a、大圆半径为a,金属电极长度为n,结晶器上圆口半径为r,结晶器下圆口半径为r,结晶器高度为l,液态渣池-金属熔池界面处的高度为h,金属电极下降高度为h,液态渣池的厚度为p。
20.液态渣池的厚度p=(加入渣的重量/渣熔体的密度)/(π
×
r2)。
21.现有技术不需要液态渣池-金属熔池界面处的高度参数,也不涉及根据该高度调节冷却的方法,本发明以为三种常规金属电极的形状,根据测试的金属电极的下降高度,首次公开了液态渣池-金属熔池界面处的高度,结合本发明单进多出式水冷结晶器,实现同时提高电渣锭内部质量和表面质量的目标;有效解决了现有技术无法使得电渣锭内部质量和表面质量同时改善的电渣重熔产品的问题。
22.本发明相较于现有技术的优点和技术效果如下:其一、采用单进多出式水冷结晶器及其使用方法,使得下部金属熔池v型区及成型电渣锭的冷却强度显著增加,下部金属熔池v型区的深度变浅、金属熔池凝固速率加快,改善电渣锭偏析、细化组织晶粒等。
23.其二、采用单进多出式水冷结晶器及其使用方法,在保证下部金属熔池v型区及成型电渣锭冷却强度显著增加的情况下,上部金属熔池圆柱区和液态渣池处于合理的水冷强度,有利于金属熔池圆柱区的表面渣壳变薄,即电渣锭表面渣壳变薄,改善电渣锭表面质量。
24.其三、本发明首次公开了金属电极下降高度和液态渣池-金属熔池界面高度的计算方法,根据电渣炉操控台上的电极下降高度示数就能够自动控制结晶器各个出水口的开启和关闭。
25.与现有技术相比,本发明的创造性在于:1)本发明首次公开了单进多出式水冷结晶器及其使用方法,其各个出水口的冷却水可以各自调节开闭,使得结晶器轴向上的水流量呈当前开启出水口的下部结晶器水流量快、当前开启出水口的上部结晶器的水流量慢,实现同时提高电渣锭内部质量和表面质量的目标。
附图说明
26.图1为带有夹层、中间层的单进多出式水冷结晶器结构示意图;图2为单进多出式水冷结晶器的电渣重熔装置结构示意图(浅v型金属熔池特征);图3为现有单进单出式水冷结晶器的电渣重熔装置结构示意图;图4为应用实施例一单进多出式水冷结晶器的电渣重熔装置结构示意图,带有尺寸参数标记;其中:1-1#出水口,2-2#出水口,3-3#出水口,4-4#出水口,5-5#出水口,6-1#出水口的电动调节阀,7-2#出水口的电动调节阀,8-3#出水口的电动调节阀,9-4#出水口的电动
调节阀,10-5#出水口的电动调节阀,11-结晶器主进水口,12-水冷结晶器钢制外层,13-水冷结晶器铜制内层,14-电渣锭,15-上部金属熔池圆柱区,20-下部金属熔池v型区,16-液态渣池,17-金属电极,18-底水箱,19-液体流量计,21-水冷结晶器钢制中间层,22-水冷结晶器中间层隔断,23-水冷结晶器中间层的环形通水口。
27.图5为应用实施例一制备的电渣锭,表面光滑、质量好;图6为应用实施例一的电渣重熔过程中的金属熔池形貌;图7为应用实施例一制备的电渣锭中心部位微观组织,珠光体的片层间距小;图8为对比实施例一制备的电渣锭,表面平整、质量较好;图9为对比实施例一的电渣重熔过程中的金属熔池形貌;图10为对比实施例一制备的电渣锭中心部位微观组织,珠光体的片层间距大;图11为对比实施例二制备的电渣锭,表面呈波纹状、质量差;图12为对比实施例二的电渣重熔过程中的金属熔池形貌;图13为对比实施例二制备的电渣锭中心部位微观组织,珠光体的片层间距较大;图14为单进单出式水冷结晶器的电渣重熔装置增加同平面出水口结构示意图;图15为不设置钢制中间层的单进多出式水冷结晶器结构示意图。
具体实施方式
28.下面结合附图和具体实施例对本发明作进一步说明,以使本领域的技术人员可以更好地理解本发明并能予以实施,但所举实施例不作为对本发明的限定。本发明涉及的具体部件以及部件的具体连接方法为现有常规方法,比如出水口阀门的安装与控制等。本发明具体实验以及测试方法为现有技术,间距为平均值。
29.本发明公开了一种单进多出式水冷结晶器的电渣重熔装置及使用方法,可以达到同时细化电渣锭内部组织晶粒、改善电渣锭表面质量的目的。为此,本发明开发了单进多出式水冷结晶器,其由一个下进水口、一个结晶器最顶部的出水口、多个沿结晶器高度方向上竖直排列的出水口组成。电渣重熔时,各个出水口的开闭根据结晶器内的电渣锭高度进行动态调节;电渣重熔过程中,水冷结晶器最顶部的出水口始终呈开启模式,其余出水口根据电渣锭高度依次开启和关闭。随着电渣锭的不断升高,当液态渣池-金属熔池界面到达第一个出水口上方4~6cm时,第一个出水口和顶部出水口呈开启模式,其余出水口呈关闭模式;当液态渣池-金属熔池界面到达第二个出水口上方4~6cm时,第二个出水口和顶部出水口呈开启模式,其余出水口呈关闭模式;到达第三、四等出水口上方4~6cm时以此类推、依次循环开启和闭合各个出水口,保持当前出水口和顶部出水口呈开启模式,其余出水口呈关闭模式,优选的,所有出水口流量一样。本装置和工艺使得液态渣池和上部分金属熔池圆柱区始终处于合理的冷却模式、电渣锭表面渣壳变薄;同时下部分金属熔池v型区和成型电渣锭对应高度的结晶器的冷却强度显著增加,使得金属熔池v型区变浅、凝固速率变快、电渣锭组织晶粒细化、减轻电渣锭中心偏析,达到了同时改善电渣锭表面和内部质量的目的。现有技术采用单进单出水冷结晶器,无论如何改变结晶器的水冷制度,始终存在电渣锭内部质量差或表面质量差二者不能同时改善的问题。本发明开发的单进多出式水冷结晶器,同时获得了最优的电渣锭表面和内部质量。
30.实施例一
如图1所示,一种单进多出式水冷结晶器的电渣重熔装置,包括水冷结晶器及其他常规部件,其中水冷结晶器根据循环水的方式为单进多出式水冷结晶器,具有1#出水口1、2#出水口2、3#出水口3、4#出水口4、5#出水口5、1#出水口的电动调节阀6、2#出水口的电动调节阀7、3#出水口的电动调节阀8、4#出水口的电动调节阀9、5#出水口的电动调节阀10、结晶器进水口11,都与结晶器自带的夹层连通,该水冷结晶器铜制内层13、钢制外层12之间设置钢制中间层21,钢制中间层21通过隔板22安装于外层12的内壁,隔板数量与单进多出式水冷结晶器的出水口数量一致,出水口与隔板间隔排列;中间层设有环形通水口23,环形通水口数量与单进多出式水冷结晶器的出水口数量一致,环形通水口与隔板间隔排列,内层与中间层的上下表面都有空隙,内层与中间层下表面的空隙为了进水,最上方的环形通水口为内层与中间层上表面的空隙。冷却水从进水口11进入内层与中间层之间,通过中间层上的环形通水口23出水,其设置使得铜制内层的水冷效果更好。五个出水口竖直上下排列。
31.另外,电渣重熔装置还有常规的液态渣池16、金属电极17、底水箱18以及电源,单进多出式水冷结晶器放置于底水箱上,如图2所示,1#出水口外接液体流量计。
32.电渣重熔时,金属电极在液态渣池的焦耳热下进行熔化,并在水冷结晶器的冷却下重新凝固为电渣锭,水冷结晶器的每个出水口能够通过调节阀调节开闭。具体的,电渣重熔时,将预熔渣加入到电渣炉的单进多出式水冷结晶器内,通电后在金属电极下端和底水箱之间形成电弧熔化预熔渣并形成液态渣池,随后金属电极下端插入液态渣池形成供电回路,在液态渣池的电阻焦耳热下熔化呈熔滴、穿过渣池并在水冷结晶器的冷却下形成电渣锭,此为常规技术。电渣重熔过程中,底水箱的循环冷却水始终为开启模式、水冷结晶器最顶部的出水口始终呈开启模式,其余出水口根据液态渣池-金属熔池界面处的高度依次开启和关闭。作为示例,电渣重熔初期,底水箱的循环冷却水始终为开启模式、水冷结晶器采用下进水口进水、顶部出水口出水、其余出水口关闭的单进单出的冷却模式;随着电渣锭的不断升高,当液态渣池-金属熔池界面到达第一个出水口上方5cm时,第一个出水口和最顶部出水口呈开启模式,其余出水口呈关闭模式;当液态渣池-金属熔池界面到达第二个出水口上方5cm时,第二个出水口和最顶部出水口呈开启模式,其余出水口呈关闭模式;以此类推、当液态渣池-金属熔池界面到达第三、四出水口上方5cm时,依次循环开启第三、四出水口和闭合其余出水口。
33.结晶器顶部的出水口使得液态渣池和上部分金属熔池圆柱区始终处于合理的冷却模式、电渣锭表面渣壳变薄;表面渣壳变薄有利于成型电渣锭与水冷结晶器间的传热。当液态渣池-金属熔池界面到达当前出水口上方5cm时打开当前出水口,使得对应高度的下部分金属熔池v型区和成型电渣锭的冷却强度显著增加,有利于金属熔池v型区变浅、金属熔池的局部凝固时间变快,降低了电渣锭内部的二次枝晶间距、细化电渣锭内部组织晶粒,实现同时改善电渣锭表面和内部质量的目标。
34.本发明采用的电渣炉为现有市售产品,只需要将现有的水冷结晶器替换为本发明的单进多出式水冷结晶器、并配备出水口的各个电动调节阀控制开闭即可;具体操作方法以及测试方法都为本领域常规方法,进水为常温水。本发明的方位关系为实际生产时的位置关系。
35.实施例二在实施例一的基础上,将五个出水口调整为竖直上下排列的九个出水口,其余不
变。得到的电渣锭后,检测两相邻出水口之间对应高度的电渣锭的铸态组织,其电渣锭内部的二次枝晶间距、组织晶粒细小。
36.对比例一如图3所示,将五个出水口调整为一个出水口,位于最上方,为现有单进单出水冷,得到的电渣锭的二次枝晶间距、组织晶粒粗大。
37.应用实施例一参见图4,采用单进五出式水冷结晶器,各个出水口距离结晶器底部的高度见表1,结晶器下口内径为64cm、上口内径为56cm、高为190cm。金属电极为两头直径均为45cm的圆柱形40cr钢连铸坯。
38.使用caf2∶cao∶al2o3=60∶20∶20的预熔渣(质量比),用渣量为125kg,加入到电渣炉的单进五出式水冷结晶器内进行金属电极的重熔,电渣重熔过程中的电流、电压分别为12500a、60v,电极熔化速率为400kg/h,液态渣池的厚度为15cm,保护气氛电渣炉的氩气通入流量为30 nl/min。1#出水口的水流量为70 m3/h, 出水口2#、3#、4#、5#打开时的水流量为70 m3/h;金属电极下降高度0≤h≤28cm时,水冷结晶器的进水流量为70 m3/h;金属电极下降高度h>28cm时,水冷结晶器的进水流量为140 m3/h;底水箱的循环冷却水的流量为25 m3/h。液态渣池的厚度p=(125000/2.6)/(π
×
322)=15cm。
39.电渣重熔过程中,随着金属电极的下降、电渣锭的高度逐渐增加。根据公式(1)计算得到电极下降高度与液态渣池-金属熔池界面高度的对应关系,如表1所示。结晶器各个出水口位置到结晶器底部的距离如表1所示。当液态渣池-金属熔池界面高度到达对应出水口上方5cm时,对应的出水口呈开启模式,具体的结晶器各个出水口的开合模式与电极下降高度(液态渣池-金属熔池界面高度)的对应关系如表1所示。
40.电渣重熔中,底水箱和结晶器最顶部出水口1#始终呈开启模式。当液态渣池-金属熔池界面高度低于等于45cm时,出水口1#呈开启模式,出水口2#、3#、4#、5#呈关闭模式;当液态渣池-金属熔池界面高度在45~75cm时,出水口5#和1#呈开启模式,出水口2#、3#、4#呈关闭模式;当液态渣池-金属熔池界面高度在75~105cm时,出水口4#和1#呈开启模式,出水口2#、3#、5#呈关闭模式;当液态渣池-金属熔池界面高度在105~135cm时,出水口3#和1#呈开启模式,出水口2#、4#、5#呈关闭模式;当液态渣池-金属熔池界面高度到达135cm时,出水口2#和1#呈开启模式,出水口3#、4#、5#呈关闭模式;电渣重熔结束后脱模,得到4000kg的表面光滑的40cr钢,电渣锭表面光滑、无缺陷、质量良好,参见图5。
41.为了测定电渣重熔中金属熔池的深度,在冶炼结束前向渣池中均匀地加入4kg的fes粉末,进而采用硫印实验对金属熔池的形状进行标定。对电渣锭上部40cm高的铸锭沿直径进行纵剖、进行硫印实验,硫印实验得到的金属熔池的形貌如图6所示,其金属熔池深度为195mm。
42.对电渣锭140厘米高的中心部位取样,利用金相显微镜观察并测定其二次枝晶间距为196μm。进一步的,利用扫描电镜观察并测定其珠光体的片层间距为0.21μm,如图7所示。表明该电渣锭具有良好的凝固组织。
43.表1 各个出水口随金属电极下降高度(液态渣池-金属熔池界面高度)的开启、关闭操作
对比应用例一在应用实施例一的基础上,将单进五出式水冷结晶器换为图3的单腔体水冷结晶器,进水口、出水口的水流量为70 m3/h,底水箱的循环冷却水的流量为25 m3/h,其余不变。同样的进行电渣重熔40cr钢,得到电渣锭表面质量如图8所示,表面平整,质量较好但较应用实施例一差些。
44.通过硫印实验测定的金属熔池深度为365mm,如图9所示;对电渣锭140厘米高度的中心部位取样,利用金相显微镜观察并测定其二次枝晶间距为245μm;进一步的,利用扫描电镜观察并测定其珠光体的片层间距为0.46μm,如图10所示,表明该电渣锭的凝固组织差。
45.对比应用例二在应用实施例一的基础上,将单进五出式水冷结晶器换为图3的单腔体水冷结晶器,进水口、出水口的水流量为140 m3/h,底水箱的循环冷却水的流量为25 m3/h,其余不变。进行同样的电渣重熔40cr钢,得到电渣锭表面质量如图11所示,表面呈波纹状、质量差。
46.通过硫印实验测定的金属熔池深度为244mm,如图12所示;对电渣锭140厘米高度的中心部位取样,利用金相显微镜观察并测定其二次枝晶间距为214μm;进一步的,利用扫描电镜观察并测定其珠光体的片层间距为0.31μm,如图13所示。
47.对比应用例三在应用实施例一的基础上,将单进五出式水冷结晶器换为图3的单腔体水冷结晶器,进水口、出水口的水流量为100 m3/h,底水箱的循环冷却水的流量为25 m3/h,其余不变。
进行同样的电渣重熔40cr钢,得到电渣锭表面质量肉眼可见微小波纹。通过硫印实验测定的金属熔池深度为318mm;对电渣锭140厘米高度的中心部位取样,利用金相显微镜观察并测定其二次枝晶间距为231μm;进一步的,利用扫描电镜观察并测定其珠光体的片层间距为0.39μm。表明其凝固组织不如对比应用例二,更不如应用实施例。
48.对比例证明了本发明提出的单进多出式水冷结晶细化电渣锭组织晶粒尺寸的优越性。
49.本发明采用单进多出式水冷结晶,能同时获得表面光滑和内部质量优异的电渣锭。进一步的,本发明采用单进多出式水冷结晶,使得液态渣池和上部分金属熔池部位处于合理冷却模式,下部分金属熔池和成型电渣锭处于强水冷模式,同时细化电渣锭组织晶粒和改善表面质量。这对于生产大型锻件具有重要的实践生产意义。
50.现有的电渣重熔装置如图3所示,当水冷结晶器冷却强度过小时,金属熔池凝固速率变慢,产生了大量的偏析夹杂物、组织晶粒粗大、严重影响了电渣锭内部质量;当水冷结晶器的冷却强度过大时,造成了电渣锭表面渣壳变厚且表面质量很差等问题;因为在液态渣池-结晶器壁间存在凝固的渣壳,在金属熔池上升中存在不能够将上方凝固的渣壳熔化,为电渣锭表面渣壳变厚、波纹状表面的成因之一,同时电渣锭表面渣壳与下部金属熔池v型区及成型电渣锭与结晶器壁间的传热也有关系,从而影响内部质量;即使如图14,在现有水冷结晶器基础上在同水平面开设对称的一个出水口,电渣重熔效果与图3差不多;具体的,进水口的水流量为140 m3/h、出水口的水流量为70 m3/h+70 m3/h,底水箱的循环冷却水的流量为25 m3/h,其余不变,进行同样的电渣重熔40cr钢,得到电渣锭表面质量与对比应用例二差不多,通过硫印实验测定的金属熔池深度为240mm;对电渣锭140厘米高度的中心部位取样,利用金相显微镜观察并测定其二次枝晶间距为213μm;进一步的,利用扫描电镜观察并测定其珠光体的片层间距为0.30μm。
51.电渣重熔的动态过程复杂,涉及传热和电渣锭凝固的动态变化,因此现有技术无法满足电渣锭大型化和产品高性能化的要求。
52.应用实施例二在应用实施例一的基础上,选择液态渣池-金属熔池界面高度到达对应出水口上方4cm时,对应的出水口呈开合模式,其余一样,得到40cr钢的电渣锭。通过硫印实验测定的金属熔池深度为195mm;对电渣锭140厘米高度的中心部位取样,利用金相显微镜观察并测定其二次枝晶间距为197μm;进一步的,利用扫描电镜观察并测定其珠光体的片层间距为0.21μm,其凝固组织与应用实施例一相差不大。但是得到的电渣锭表面光滑度下降、其表面质量较应用实施例一差,但是优于对比应用。
53.应用实施例三在应用实施例一的基础上,选择液态渣池-金属熔池界面高度到达对应出水口上方6cm时,对应的出水口呈开合模式,其余一样,得到表面光滑的40cr钢,电渣锭表面光滑、质量良好;通过硫印实验测定的金属熔池深度为205mm;对电渣锭140厘米高度的中心部位取样,利用金相显微镜观察并测定其二次枝晶间距为203μm;进一步的,利用扫描电镜观察并测定其珠光体的片层间距为0.24μm。凝固组织较应用实施例一差,优于对比应用。
54.应用实施例四在应用实施例一的基础上,选择液态渣池-金属熔池界面高度到达对应出水口上
方2cm时,对应的出水口呈开合模式,其余一样,得到40cr钢的电渣锭。电渣锭表面光滑度下降,其表面质量明显较对比应用例一差,不符合同时细化电渣锭组织晶粒和改善表面质量。
55.应用实施例五在应用实施例一的基础上,选择液态渣池-金属熔池界面高度到达对应出水口上方8cm时,对应的出水口呈开合模式,其余一样,得到40cr钢的电渣锭。通过硫印实验测定的金属熔池深度为220mm;对电渣锭140厘米高度的中心部位取样,利用金相显微镜观察并测定其二次枝晶间距为210μm;进一步的,利用扫描电镜观察并测定其珠光体的片层间距为0.28μm,不符合同时细化电渣锭组织晶粒和改善表面质量。
56.应用实施例六金属电极为带有一定锥度的圆棒时,上圆直径47cm,下圆直径43cm,长度330cm,根据公式(2)通过电极下降高度计算液态渣池-金属熔池界面高度,采用应用实施例一一样的出水口控制方法,具体的结晶器各个出水口的开合模式与电极下降高度(液态渣池-金属熔池界面高度)的对应关系如表2所示。得到电渣锭表面光滑、无缺陷、质量良好;通过硫印实验测定的金属熔池深度为195mm;对电渣锭140厘米高度的中心部位取样,利用金相显微镜观察并测定其二次枝晶间距为197μm;进一步的,利用扫描电镜观察并测定其珠光体的片层间距为0.22μm。
57.表2 各个出水口随金属电极下降高度(液态渣池-金属熔池界面高度)的开启、关闭操作
应用实施例七金属电极为带有一定锥度的圆棒时,上圆直径43cm,下圆直径47cm,长度330cm,根据公式(3)通过电极下降高度计算液态渣池-金属熔池界面高度,采用应用实施例一一样的出水口控制方法,具体的结晶器各个出水口的开合模式与电极下降高度(液态渣池-金属熔池界面高度)的对应关系如表3所示。得到电渣锭表面光滑、无缺陷、质量良好;通过硫印实验测定的金属熔池深度为194mm;对电渣锭140厘米高度的中心部位取样,利用金相显微镜观察并测定其二次枝晶间距为196μm;进一步的,利用扫描电镜观察并测定其珠光体的片层间距为0.21μm。
58.表3 各个出水口随金属电极下降高度(液态渣池-金属熔池界面高度)的开启、关闭操作应用实施例八在实施例一的基础上省略隔板即图15所示的不设置钢制中间层,根据应用实施例一的方法,得到电渣锭表面光滑、无缺陷、质量良好;通过硫印实验测定的金属熔池深度为201mm;对电渣锭140厘米高度的中心部位取样,利用金相显微镜观察并测定其二次枝晶间距为203μm;进一步的,利用扫描电镜观察并测定其珠光体的片层间距为0.23μm。
59.根据以上描述,本发明开发了一种新型的单进多出式水冷结晶器的电渣重熔技术。电渣重熔中,随着电渣锭的不断升高,当液态渣池-金属熔池界面到达第一个出水口上方4~6cm时,开启结晶器第一个出水口和最顶部出水口,其余出水口均为关闭模式。这种出
水模式使得高于第一个出水口的上部分结晶器中冷却水的流量呈合理模式,低于第一个出水口的下部分结晶器中冷却水的流量显著增加:即高于第一个出水口的液态渣池和上部金属熔池圆柱区呈合理的冷却模式,低于第一个出水口的下部金属熔池v型区和成型电渣锭的冷却强度显著增加。液态渣池和上部金属熔池圆柱区为电渣锭表面渣壳的形成区,合理冷却模式使得电渣锭表面获得良好的表面质量;下部金属熔池v型区为金属熔池的凝固区,增加金属熔池v型区的冷却强度使得金属熔池凝固速率变快,从而降低了电渣锭中心偏析、细化组织晶粒。
60.综上所述,在保证电渣锭表面渣壳薄而光滑的前提下,提升金属熔池的凝固速度不仅可以改善凝固偏析和细化晶粒,对锻件产品还可以起到细晶强化的作用,提升产品的力学性能。细晶强化是同时提高钢的塑韧性和强度的有效途径。细晶强化,即细化组织晶粒的方法之一就是提升钢液的凝固速率。因此,提升凝固速率不仅能够细化晶粒、还能够降低因凝固偏析产生的tin、mns、aln等大尺寸夹杂物,获得良好的凝固组织。尤其是,本发明首次公开了金属电极下降高度与液态渣池-金属熔池界面高度的变化关系,实际生产验证该方法具有显著的技术进步,为工业生产提供可行性保障。