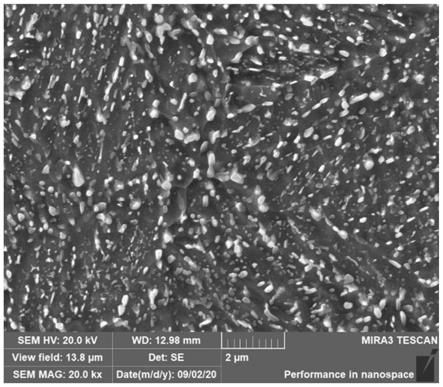
1.本发明涉及石油、天然气开采用管道钢技术领域,具体而言,涉及一种油井管用钢、其制备方法和油井管。
背景技术:2.在石油、天然气生产领域,伴随腐蚀性低的浅井油气资源的枯竭,对腐蚀性高的高压深井的开发一直在增加。油气井的深井化,一方面要求油井钢管具备高强度、高韧性;另一方面,油气井大多含有具有腐蚀性的硫化氢(h2s),因此对钢管的耐腐蚀性要求也提高。
3.低合金钢管暴露在含有h2s的酸性环境中,就会产生源自硫化物应力开裂(ssc)的氢脆性断裂,且越是高强度钢越易发生ssc。
4.以往,用于含有h2s的酸性环境的低合金油气井钢管的最高强度限制在110ksi级别,即屈服强度758mpa以内。如要获得超过110ksi强度级别(如125ksi级别,屈服强度862mpa以上)的油井管钢,需要解决高强度与高韧性、高强度与抗ssc性能的双重矛盾关系。近年来,开始研发的125ksi高强度油井管钢虽然获得了高强度(屈服强度高于862mpa)指标,但抗ssc性能不稳定,而且很少能满足在nace tm 0177标准中method a的条件下,加载最小屈服强度85%的应力保持720小时不断裂的要求。
技术实现要素:5.本发明的主要目的在于提供一种油井管用钢、其制备方法和油井管,以解决现有技术中油井管用钢不能同时满足高强度与高韧性、高强度与抗ssc性能的问题。
6.为了实现上述目的,根据本发明的一个方面,提供了一种油井管用钢,按重量百分比计,油井管用钢的化学成分包括:c 0.4~0.6%,si≤0.3%,mn≤0.5%,cr 0.8~1.2%,mo 0.6~0.9%,v 0.1~0.3%,nb≤0.05%,al≤0.05%,n≤0.03%,s≤0.005%,p≤0.01%,cu 0.7~1.5%,ni和cu的重量百分比满足0.5≤ni/cu≤1,余量为铁和不可避免的杂质。
7.进一步地,油井管用钢在室温的屈服强度》862mpa,抗拉强度》950mpa;0℃条件下,全尺寸v型缺口冲击功》130j。
8.进一步地,油井管用钢的金相组织包括回火索氏体和奥氏体,奥氏体的体积为金相组织总体积的3~5%,回火索氏体的体积为金相组织总体积的95~97%。
9.进一步地,油井管用钢在饱和h2s环境中加载733mpa应力下至少保持720小时不断裂。
10.为了实现上述目的,根据本发明的一个方面,提供了一种上述油井管用钢的制备方法,该制备方法包括:步骤s1,按上述油井管用钢的化学成分进行混料得到原料,将原料进行冶炼和浇注得到钢锭;步骤s2,将钢锭进行保温,然后在奥氏体单相区进行锻造并冷却至室温,得到冷却后的钢锭;步骤s3,将冷却后的钢锭进行热处理,得到油井管用钢。
11.进一步地,步骤s2中,保温的温度为1150~1200℃,保温的时间不少于4h,优选保
温时间为4~12h。
12.进一步地,步骤s2中,锻造包括初锻和终锻,初锻的温度为1100~1150℃,初锻的时间为5min~60min;终锻的温度为950~1000℃,终锻的时间为5min~60min;优选锻造的锻造比大于8,优选锻造的锻造比为8~20;优选冷却为空冷,优选冷却的速度为0.5℃/s~5℃/s。
13.进一步地,步骤s3中,热处理包括:步骤s31,将冷却后的钢锭升温到第一预设温度,并在第一预设温度下进行第一保温,得到第一钢锭;步骤s32,将保温的钢锭加热至第二预设温度,并在第二预设温度下进行第二保温,得到第二钢锭,将第二钢锭冷却至室温,得到第三钢锭;步骤s33,将第三钢锭进行回火处理,得到第四钢锭;步骤s34,将第四钢锭冷却至室温,得到油井管用钢。
14.进一步地,第一预设温度为600~700℃,优选第一保温的时间系数为2.0~4.0;第二预设温度为810~860℃,优选第二保温的时间为60~90分钟;优选步骤s32中冷却为油冷,冷却的速度为5℃/s~20℃/s。
15.进一步地,回火处理的回火温度为680~730℃,回火处理的回火时间系数为3.0~9.0。
16.根据本发明的另一方面,提供了一种油井管,该油井管采用上述油井管用钢制备而成。
17.应用本发明的技术方案,本发明通过增加碳含量,能够提高油井管用钢的强度;其中,碳含量增加,不仅可以起到固溶强化作用提高强度,而且通过增加析出相的种类(碳化物-cr的碳化物、钒的碳化物和钼的碳化物、氮化物-钒的氮化物和富cu相)和数量,一方面析出相起到析出强化的作用,另一方面析出相还可以充当“氢陷阱”,增加“氢陷阱”密度,从而捕获进入材料的氢,使氢均匀弥散分布在材料基体中,抑制氢扩散和聚集的作用,提高了抗ssc性能;同时通过增加钼含量,有效提高油井管用钢的韧性。综合上述作用,提高了油井管用钢抗ssc性能。通过平衡本发明油井管用钢的各化学成分,解决了高强度与高韧性、高强度与抗ssc性能的双重矛盾关系。
附图说明
18.构成本技术的一部分的说明书附图用来提供对本发明的进一步理解,本发明的示意性实施例及其说明用于解释本发明,并不构成对本发明的不当限定。在附图中:
19.图1示出了本发明实施例1的金相组织的sem图;
20.图2示出了本发明实施例1的金相组织的xrd图;
21.图3示出了本发明实施例22的贝氏体组织的om图;
22.图4示出了本发明实施例22的纳米尺寸析出相的tem图;
23.图5示出了本发明实施例22的材料表面形成cu的硫化物的sem图;
24.图6示出了本发明实施例22的材料表面形成cu的硫化物的eds图。
具体实施方式
25.需要说明的是,在不冲突的情况下,本技术中的实施例及实施例中的特征可以相互组合。下面将参考附图并结合实施例来详细说明本发明。
26.如本技术背景技术所分析的,现有技术中存在油井管用钢不能同时满足高强度与高韧性、高强度与抗ssc性能的问题。发明人为了解决上述问题,对影响125ksi级别的高强度钢抗ssc性能的各种因素进行了深入研究。发明人经过研究发现,(1)高强度钢(高于125ksi强度级别)抗ssc性能不佳的主要因素并不是通常认为的引发ssc腐蚀的起点和根源的夹杂物,也不是通常认为的粗大m
23
c6碳化物。但是,碳化物的均匀弥散分布对提高抗ssc性能具有重要作用。(2)高强度钢抗ssc性能的优劣与位错密度具有相关性,位错是氢的传输通道,高的位错密度是导致这种高强度钢(高于125ksi强度级别)抗ssc性能不佳的主要因素。而为了获得钢的高强度,组织中必然存在较高的位错密度,这两者是矛盾关系。
27.因此,基于上述发现,发明人认为提高高强度钢抗ssc性能需要提高高强度钢中碳化物的均匀弥散分布和/或降低高强度钢的位错密度,主要有三条途径:一是阻碍氢进入材料内部;二是进入材料内部的氢避免扩散和聚集;三是通过组织设计提高不发生ssc的临界氢含量。在此基础上,本技术提供了一种油井管用钢、其制备方法和油井管。
28.在本技术的一种典型的实施方式中,提供了一种油井管用钢,按重量百分比计,油井管用钢的化学成分包括:c 0.4~0.6%,si≤0.3%,mn≤0.5%,cr 0.8~1.2%,mo 0.6~0.9%,v 0.1~0.3%,nb≤0.05%,al≤0.05%,n≤0.03%,s≤0.005%,p≤0.01%,cu 0.7~1.5%,ni和cu的重量百分比满足0.5≤ni/cu≤1,余量为铁和不可避免的杂质。
29.本发明通过增加碳含量,能够提高油井管用钢的强度;其中,碳含量增加,不仅可以起到固溶强化作用提高强度,而且通过增加析出相的种类(碳化物-cr的碳化物、钒的碳化物和钼的碳化物、氮化物-钒的氮化物和富cu相)和数量,一方面析出相起到析出强化的作用,另一方面析出相还可以充当“氢陷阱”,增加“氢陷阱”密度,从而捕获进入材料的氢,使氢均匀弥散分布在材料基体中,抑制氢扩散和聚集的作用,提高了抗ssc性能;同时通过增加钼含量,有效提高油井管用钢的韧性。综合上述作用,提高了油井管用钢抗ssc性能。通过平衡本发明油井管用钢的各化学成分,解决了高强度与高韧性、高强度与抗ssc性能的双重矛盾关系。
30.为了进一步说明本技术的有益效果,以下对上述各元素的作用进行说明如下:
31.(1)c的作用
32.c在本发明油井管用钢中具有双重作用:一是固溶强化;二是形成碳氮化物起到析出强化。通过比现有技术中的油井管用钢含有更多的c,有效补偿了高温回火后强度的降低,从而可以保证125ksi(屈服强度高于862mpa)强度级别。为了获得该效果,c含量需要保证0.4%以上;但c含量超过0.6%,由于钢的淬透性增强,容易开裂。因此,c含量的上限为0.6%。例如,c的含量可以为0.4%、0.42%、0.44%、0.46%、0.48%、0.5%、0.52%、0.54%、0.56%、0.58%、0.6%。
33.(2)cr的作用
34.cr为本发明油井管用钢中提高淬透性和形成cr的碳化物的元素。为了获得该效果,需要含有至少0.8%的cr;另一方面cr含量超过1.2%,在该体系钢中cr的作用将达到饱和,因此cr的含量控制在0.8~1.2%,例如cr的含量为0.8%、0.85%、0.9%、0.95%、1.0%、1.05%、1.1%、1.15%、1.2%。
35.(3)mo的作用
36.mo在本发明油井管用钢中具有两方面作用:一是形成mo的碳化物提高回火抗力;
二是mo可以起到改善回火脆性的作用,从而本发明钢具有高的冲击韧性。为了达到这双重效果,mo的含量控制在0.6~0.9%,例如mo的含量为0.6%、0.65%、0.7%、0.75%、0.8%、0.85%、0.9%。
37.(4)v的作用
38.v在本发明油井管用钢中具有双重作用:一方面v与c和n形成碳氮化物起到析出强化作用从而保证强度级别;另一方面v的碳氮化物充当“氢陷阱”,捕获进入材料中的氢,使氢均匀弥散分布在材料基体中,避免局部氢富集造成氢脆断裂。按照本发明钢中c和n的成分范围,本发明钢中v的配比控制在0.1~0.3%最佳,例如可以为0.1%、0.15%、0.2%、0.25%、0.3%。
39.(5)nb的作用
40.nb为根据需要添加的成分,它会与c和n结合形成碳氮化物,起到细化晶粒,提高强韧性的作用,按照本发明钢中c和n的成分范围,本发明油井管用钢中nb的含量不需超过0.05%,例如nb的含量为0、0.01%、0.02%、0.03%、0.04%、0.05%。
41.(6)al的作用
42.al为根据需要添加的成分,如需要脱氧,则可加入不超过0.05%的al;另外加入al后还可与本发明钢中n形成aln,可以起到细化晶粒的作用。例如al的含量为0、0.01%、0.02%、0.03%、0.04%、0.05%。
43.(7)n的作用
44.n为根据需要添加的成分,在本发明中n与c一起与v、al、nb形成碳氮化物,一方面可以细化晶粒,提高强韧性,一方面充当有利“氢陷阱”提高抗ssc性能。为了降低钢的冶炼成本,n的含量≤0.03%最佳。例如n的含量为0、0.01%、0.02%、0.03%。
45.(8)cu的作用
46.cu是关键的合金元素,它在本发明钢中具有多重作用:一是提高钢的抗ssc性能,表现为:(1)cu和h2s形成cu的硫化物附着在材料表面,可有效阻碍氢进入材料内部;(2)回火后组织中形成纳米尺寸富cu相,充当有利“氢陷阱”,捕获进入材料中的氢,使氢均匀弥散分布在材料基体中,避免局部氢富集造成氢脆断裂。二是提高强度,表现为:回火后组织中析出纳米尺寸富cu相,起到析出强化的作用。三是cu是奥氏体形成元素,在高温回火后可以形成一定含量的逆转变奥氏体,均匀分布的奥氏体可容纳更多的氢含量,从而改善抗ssc性能。为了可靠的获得cu在本发明钢中的多重作用,cu的最低含量应高于0.7%,而过多的cu含量容易产出热脆现象,因此cu的最高含量不宜超过1.5%。例如cu的含量为0.7%、0.8%、0.9%、1.0%、1.1%、1.2%、1.3%、1.4%、1.5%。
47.(9)ni的作用
48.ni是随cu一同加入的元素,一方面ni可以有效抑制单独加入cu带来的热脆问题,一方面ni可以提高钢的韧性,ni的含量不能过少,过少的ni不能有效抑制热脆危害,但过量的ni会形成较多的奥氏体,强度级别无法保证,因此本发明钢中ni的含量控制原则为:ni/cu重量百分比满足0.5≤ni/cu≤1。例如ni/cu为0.5、0.6、0.7、0.8、0.9、1。
49.根据上述化学成分得到的油井管用钢具有高强度和高韧性,高于125ksi级别,在室温的屈服强度》862mpa,抗拉强度》950mpa;0℃条件下,全尺寸v型缺口冲击功》130j。
50.在一些实施例中,油井管用钢的金相组织包括回火索氏体和奥氏体,回火索氏体
能够降低位错密度,面心立方结构(fcc)的奥氏体组织相比体心立方结构(bcc)的马氏体组织具有更强的容氢能力。即,组织设计中引入适量弥散分布的奥氏体可以提高不发生ssc的临界氢含量,从而改善抗ssc性能,因此控制奥氏体的体积为金相组织总体积的3~5%,回火索氏体的体积为金相组织总体积的95~97%。避免奥氏体含量过多会导致强度降低以及奥氏体过少会导致抗ssc性能下降。在一些实施例中,油井管用钢的金相组织可以认为由回火索氏体和奥氏体组成,仅含有极微量的杂相。
51.根据上述化学成分得到的油井管用钢具有优异的抗ssc性能,参照nace tm0177标准中的method a,油井管用钢浸泡在a溶液饱和h2s环境中加载733mpa应力下至少保持720小时不断裂。
52.在本技术另一种典型的实施方式中,提供了一种上述油井管用钢的制备方法,该制备方法包括:步骤s1,按上述油井管用钢的化学成分进行混料得到原料,将原料进行冶炼和浇注得到钢锭;步骤s2,将钢锭进行保温,然后在奥氏体单相区进行锻造并冷却至室温,得到冷却后的钢锭;步骤s3,将冷却后的钢锭进行热处理,得到油井管用钢。
53.根据上述油井管用钢的化学成分,在制备方法中采用相应的工艺,从而得到高强度和高韧性并具有抗ssc性能的油井管用钢;同时,通过在热处理过程实施冷却工艺,控制金相组织的组成,从而降低位错密度,提高抗ssc性能。采用本技术制备方法制备得到的油井管用钢通过增加碳含量,能够提高油井管用钢的强度;其中,碳含量增加,不仅可以起到固溶强化作用提高强度,而且通过增加析出相的种类(碳化物-cr的碳化物、钒的碳化物和钼的碳化物、氮化物-钒的氮化物和富cu相)和数量,一方面析出相起到析出强化的作用,另一方面析出相还可以充当“氢陷阱”,增加“氢陷阱”密度,从而捕获进入材料的氢,使氢均匀弥散分布在材料基体中,抑制氢扩散和聚集的作用,提高了抗ssc性能;同时通过增加钼含量,有效提高油井管用钢的韧性。综合上述作用,提高了油井管用钢抗ssc性能。通过平衡本发明油井管用钢的各化学成分,解决了高强度与高韧性、高强度与抗ssc性能的双重矛盾关系。
54.对上述冶炼的方式没有特别的限制,本领域常用的冶炼方法都可以用于本发明。优选上述冶炼的方式为真空感应冶炼、电弧炉冶炼、转炉冶炼中的一种。
55.本领域技术人员可以参考本领域常用的温度和时间用于本发明。在一些实施例中,步骤s2中,保温的温度为1150~1200℃,保温的时间不少于4h,优选保温时间为4~12h。
56.本发明的锻造工艺可以参考本领域常用的锻造工艺。在一些实施例中,步骤s2中,锻造包括初锻和终锻,为了使油井管用钢获得良好的机械性能,控制初锻的温度为1100~1150℃,初锻的时间为5min~60min;终锻的温度为950~1000℃,终锻的时间为5min~60min;为了使金相组织均匀致密,优选锻造的锻造比大于8,优选锻造的锻造比为8~20;优选冷却为空冷,优选冷却的速度为0.5℃/s~5℃/s。
57.在一些实施例中,步骤s3中,热处理包括:步骤s31,将冷却后的钢锭升温到第一预设温度,并在第一预设温度下进行第一保温,得到第一钢锭;步骤s32,将保温的钢锭加热至第二预设温度,并在第二预设温度下进行第二保温,得到第二钢锭,将第二钢锭冷却至室温,得到第三钢锭;步骤s33,将第三钢锭进行回火处理,得到第四钢锭;步骤s34,将第四钢锭冷却至室温,得到油井管用钢。通过上述两次分段保温,使组织更加均匀,未溶碳化物全部溶进基体;然后再进行回火使碳化物和富cu相完全析出。
58.根据本发明油井管用钢的化学成分控制热处理工艺的温度和时间,在一些实施例中,第一预设温度为600~700℃,优选第一保温的时间系数为2.0~4.0;保温时间=试样最大厚度
×
保温时间系数,其中,保温时间的单位为分钟,试样最大厚度的单位为mm;为了获得完全奥氏体化和晶粒最佳尺寸,控制第二预设温度为810~860℃,优选第二保温的时间为60~90分钟。
59.通过控制冷却工艺来控制本发明油井管用钢的金相组织,为了进一步平衡回火索氏体和残留奥氏体的相对比例,优选步骤s32中的冷却为油冷,冷却的速度为5℃/s~20℃/s。
60.根据原料的化学成分不同,尤其是碳含量的改变,会导致在热处理的回火过程中,不同的温度条件影响碳化物析出相的生成量,为了进一步提高高碳含量前提下钢的抗ssc性能,对热处理的回火温度也相应进行调整。在一些实施例中,控制回火温度在680~730℃,回火处理的回火时间系数为3.0~9.0;回火时间=试样最大厚度
×
回火时间系数,回火时间的单位为分钟,试样最大厚度的单位为mm。本发明中油井管用钢的碳含量较高,为使强度和韧性达到125ksi级别并具有优异的抗ssc性能,回火温度应该尽可能高。由于其中碳含量较高,在上述680~730℃进行回火,可以使碳与v、nb等充分反应形成相应的碳化物起到充分的析出强化作用。通过高温回火,降低高碳含量下的位错密度,进而控制了因为位错密度高对抗ssc性能的影响,保证了本技术的油井管用钢具有与低碳含量的油井管用钢相当的抗ssc性能,即保证了本技术的高碳含量的油井管用钢的高强度、高韧性、高抗ssc性能。
61.在本技术又一种典型的实施方式中,提供了一种油井管,该油井管采用上述油井管用钢制备而成。具有上述油井管用钢的油井管具有高强度高韧性的同时还具有优异的抗ssc性能。
62.在本技术一种典型的实施方式中,提供了一种耐酸腐蚀钢,按重量百分比计,该耐酸腐蚀钢的化学成分包括:c 0.05~0.15%,si≤0.3%,mn≤0.6%,cr 0.8~1.2%,mo 0.6~0.9%,v≤0.3%,nb 0.01~0.05%,al≤0.05%,s≤0.005%,p≤0.01%,cu 0.7~2%,ni和cu的重量百分比满足0.5≤ni/cu≤1,余量为铁和不可避免的杂质。
63.基于低碳含量的特点,赋予耐酸腐蚀钢较高的抗ssc性能;并通过增加析出相的种类(碳化物-cr的碳化物、钒的碳化物和钼的碳化物、氮化物-钒的氮化物和富cu相),一方面析出相起到析出强化的作用;同时,通过在化学成分中添加cu元素,可以在材料表面形成阻碍氢进入的“膜”屏障,从而进一步提高本发明耐酸腐蚀钢抗ssc性能。通过nb元素与c形成碳化物,可以细化晶粒,提高耐酸腐蚀钢的强韧性。通过平衡本发明耐酸腐蚀钢的各化学成分,解决了高强度与高韧性、高强度与抗ssc性能的双重矛盾关系。
64.各元素的作用如下:
65.(1)c的作用
66.c是本发明耐酸腐蚀钢中最有效的增强淬透性的元素,高的c含量容易获得马氏体组织,为了获得贝氏体组织,钢中c含量不宜超过0.15%。同时,c又起到固溶强化的作用,c的含量不应低于0.05%。因此,本发明钢中c含量为0.05~0.15%。例如,c的含量可以为0.05%、0.07%、0.09%、0.1%、0.12%、0.15%。
67.(2)cr的作用
68.cr为本发明耐酸腐蚀钢中具有抗一般腐蚀及固溶强化的作用,同时它还可以与c
形成少量cr的碳化物,起到析出强化的作用。为了获得该效果,需要含有至少0.8%的cr,另一方面cr含量超过1.2%,在该体系耐酸腐蚀钢中cr的作用将达到饱和,因此cr的含量控制在0.8~1.2%,例如cr的含量为0.8%、0.85%、0.9%、0.95%、1.0%、1.05%、1.1%、1.15%、1.2%。
69.(3)mo的作用
70.mo在本发明耐酸腐蚀钢中具有两方面作用:一是形成mo的碳化物提高回火抗力;二是mo可以起到改善回火脆性的作用,从而提高本发明耐酸腐蚀钢的韧性。为了达到mo的双重效果,mo的含量控制在0.6~0.9%,例如mo的含量为0.6%、0.65%、0.7%、0.75%、0.8%、0.85%、0.9%。
71.(4)v的作用
72.v为本发明耐酸腐蚀钢根据需要添加的成分。v与c形成碳化物起到析出强化作用从而提高强度。另一方面提高抗ssc性能:v的碳化物充当“氢陷阱”,捕获进入材料中的氢,使氢均匀弥散分布在材料基体中,避免局部氢富集造成氢脆断裂。但v的碳化物要在高于500℃回火时才容易析出,因此,在当前的常规回火温度下,为了保证v的作用充分发挥,优选耐酸腐蚀钢中含有不高于0.3%的v,例如可以为0.1%、0.15%、0.2%、0.25%、0.3%。比如耐酸腐蚀钢中含有不高于0.3%的v,当回火温度在500℃以下时,即使v的碳化物没有析出,但是v也不会对耐酸腐蚀钢产生负面影响。
73.(5)nb的作用
74.nb会与c结合形成碳化物,一方面起到细化晶粒的作用,提高钢的强韧性;另一方面提高抗ssc性能:nb的碳化物充当“氢陷阱”,捕获进入材料中的氢,使氢均匀弥散分布在材料基体中,避免局部氢富集造成氢脆断裂。按照本发明钢中c的成分范围,本发明钢中nb的含量控制在0.01~0.05%。例如nb的含量为0.01%、0.02%、0.03%、0.04%、0.05%。
75.(6)al的作用
76.al为根据需要添加的成分,如需要脱氧,则可加入不超过0.05%的al。例如al的含量为0、0.01%、0.02%、0.03%、0.04%、0.05%。
77.(7)cu的作用
78.cu是关键的合金元素,它在本发明耐酸腐蚀钢中具有多重作用:一是提高钢的抗ssc性能,表现为:(1)cu和h2s形成cu的硫化物“膜屏障”附着在材料表面,可有效阻碍氢进入材料内部;(2)回火后组织中形成纳米尺寸富cu相,充当有利“氢陷阱”,捕获进入材料中的氢,使氢均匀弥散分布在材料基体中,避免局部氢富集造成氢脆断裂。二是提高强度,表现为:回火后组织中析出纳米尺寸富cu相,起到析出强化的作用。为了可靠的获得cu在本发明钢中的多重作用,cu的最低含量应高于0.7%,而过多的cu含量容易发生热脆现象,因此cu的最高含量不宜超过2.0%。例如cu的含量为0.7%、0.8%、0.9%、1.0%、1.1%、1.2%、1.3%、1.4%、1.5%、1.6%、1.7%、1.8%、1.9%、2%。
79.(8)ni的作用
80.ni可以有效抑制单独加入cu带来的热脆问题,一方面ni可以提高钢的韧性,ni的含量不能过少,过少的ni不能抑制热脆危害,但过量的ni会增加淬透性,容易生成马氏体。因此本发明钢中ni的含量控制原则为:ni/cu重量百分比满足0.5≤ni/cu≤1。例如ni/cu为0.5、0.6、0.7、0.8、0.9、1。
81.根据上述化学成分得到的耐酸腐蚀钢具有高强度和高韧性,高于125ksi级别,该耐酸腐蚀钢在室温的屈服强度》862mpa,抗拉强度》980mpa;0℃条件下,全尺寸v型缺口冲击功》130j。
82.马氏体由于位错密度高,其抗ssc敏感性高于贝氏体组织和铁素体组织,即金相组织中马氏体越多,位错密度越高,抗ssc性能越差,因此为了获得高强度抗ssc性能优异的耐酸腐蚀钢,本发明通过降低c含量,控制耐酸腐蚀钢的组织为完全贝氏体,以避免位错密度过高对抗scc性能带来过多的负面影响。
83.根据上述化学成分得到的耐酸腐蚀钢具有优异的抗ssc性能,参照nace tm0177标准method a,耐酸腐蚀钢浸泡在a溶液在饱和h2s环境中加载733mpa应力下至少保持720小时不断裂。
84.在本技术另一种典型的实施方式中,提供了一种上述耐酸腐蚀钢的制备方法,该制备方法包括:步骤s1,按上述耐酸腐蚀钢的化学成分进行混料得到原料,将原料进行经过冶炼和浇注得到钢锭;步骤s2,将钢锭进行保温,然后在奥氏体单相区进行锻造并冷却至室温,得到冷却后的钢锭;步骤s3,将冷却后的钢锭进行热处理,得到所述耐酸腐蚀钢。
85.根据上述耐酸腐蚀钢的化学成分,在制备方法中采用相应的工艺,从而得到高强度和高韧性并具有抗ssc性能的耐酸腐蚀钢;同时,通过控制热处理的冷却工艺,控制金相组织的组成,从而降低位错密度,提高抗ssc性能。采用本技术制备方法制备得到的耐酸腐蚀钢基于低碳含量的特点,赋予耐酸腐蚀钢较高的抗ssc性能;并通过增加析出相的种类(碳化物-cr的碳化物、钒的碳化物和钼的碳化物、氮化物-钒的氮化物和富cu相),一方面析出相起到析出强化的作用;同时,通过在化学成分中添加cu元素,可以在材料表面形成阻碍氢进入的“膜”屏障,从而进一步提高本发明耐酸腐蚀钢抗ssc性能。通过nb元素与c形成碳化物,可以细化晶粒,提高耐酸腐蚀钢的强韧性。通过平衡本发明耐酸腐蚀钢的各化学成分,解决了高强度与高韧性、高强度与抗ssc性能的双重矛盾关系。
86.对上述冶炼的方式没有特别的限制,本领域常用的冶炼方法都可以用于本发明。优选上述冶炼的方式为真空感应冶炼、电弧炉冶炼、转炉冶炼中的一种。
87.本领域技术人员可以参考本领域常用的温度和时间用于本发明。在一些实施例中,步骤s2中,保温的温度为1150~1200℃,保温的时间不少于4h,优选保温时间为4~20h。
88.本发明的锻造工艺可以参考本领域常用的锻造工艺。在一些实施例中,步骤s2中,锻造包括初锻和终锻,初锻的温度为1100~1150℃,初锻的时间为5~60min;终锻的温度为950~1000℃,终锻的时间为5~60min;优选锻造的锻造比大于8,优选锻造的锻造比为8~20;优选冷却为空冷,优选冷却的速度为0.5~5℃/s。
89.在一些实施例中,步骤s3中,热处理包括:步骤s31,将冷却后的钢锭升温到第一预设温度,并在第一预设温度下进行第一保温,得到第一钢锭;步骤s32,将保温的钢锭加热至第二预设温度,并在第二预设温度下进行第二保温,得到第二钢锭,将第二钢锭冷却至室温,得到第三钢锭;步骤s33,将第三钢锭进行回火处理,得到第四钢锭;步骤s34,将第四钢锭冷却至室温,得到耐酸腐蚀钢。
90.根据本发明耐酸腐蚀钢的化学成分控制热处理工艺的温度和时间,在一些实施例中,第一预设温度为600~700℃,第一保温的时间系数为2.0~4.0,保温时间=试样最大厚度
×
保温时间系数,保温时间的单位为分钟,试样最大厚度的单位为mm;为了获得完全贝氏
体化和晶粒最佳尺寸,控制第二预设温度为890~930℃,优选第二保温的时间为60~90分钟。
91.根据原料的化学成分不同,尤其是碳含量的改变,热处理的回火温度也相应进行调整。本发明中耐酸腐蚀钢的碳含量较低,为使强度和韧性达到125ksi级别并具有优异的抗ssc性能,回火温度应该相应降低,并增加回火时间。控制回火处理的回火温度为400~600℃,回火处理的回火时间为6~10小时。回火温度升高,可以适当降低回火时间。在上述400~600℃的低温下回火,可以提高位错密度,进而提高强度,同时避免了因为位错密度提高导致的抗ssc性能的过度下降,进而提高了耐酸腐蚀钢的高强和高抗ssc的综合性能。
92.通过控制冷却工艺来控制本发明油井管用钢的金相组织,为了获得完全贝氏体,优选步骤s32中的冷却为保温棉缓冷,冷却的速度为0.2℃/s~5℃/s。
93.在本技术又一种典型的实施方式中,提供了一种油井管,油井管采用上述耐酸腐蚀钢制备而成。具有上述耐酸腐蚀钢的油井管具有高强度高韧性的同时还具有优异的抗ssc性能。
94.以下结合具体实施例对本技术作进一步详细描述,这些实施例不能理解为限制本技术所要求保护的范围。
95.实施例1
96.按重量百分比计,钢的化学成分为:c 0.45%,si 0.21%,mn 0.42%,cr 0.99%,mo 0.76%,v 0.11%,nb 0.01%,al 0.025%,n 0.018%,s 0.001%,p 0.009%,cu 0.99%,ni 0.62%,其中ni/cu=0.62;余量为fe。
97.制备方法如下:
98.(1)按照上述化学组分混合原料,经过真空感应冶炼和浇注获得钢锭;
99.(2)将上述钢锭在1160℃保温,保温时间8小时;
100.(3)将钢锭在奥氏体单相区锻造:初锻温度1100℃,初锻的时间为20min,终锻温度980℃,终锻的时间为15min,锻造比为10,锻造后空冷至室温,冷却速度5℃/s。
101.(4)切割直径为20mm、厚度为20mm的圆柱形钢样进行热处理:首先钢样随炉升温到第一预设温度650℃保温,保温时间系数为2.0,保温时间为40分钟;然后继续加热到第二预设温度820℃,保温60分钟,出炉油冷至室温,冷却速度15℃/s;将钢样进行回火处理,回火温度为680℃,回火时间系数为9.0,回火时间为180分钟;回火后的钢样出炉油冷至室温,冷却速度12℃/s。
102.实施例2
103.与实施例1不同的是,步骤(4)中的回火温度为710℃,回火系数为6.0,回火时间为120分钟。
104.实施例3
105.与实施例1不同的是,步骤(4)中的回火温度为730℃,回火系数为3.0,回火时间为60分钟。
106.实施例4
107.与实施例1不同的是,按重量百分比计,钢的化学成分为:c 0.48%,si 0.19%,mn 0.32%,cr 1.10%,mo 0.81%,v 0.12%,nb 0.01%,n 0.01%,s 0.001%,p 0.009%,cu 1.27%,ni 0.70%,其中ni/cu=0.55,余量为fe。
108.实施例5
109.与实施例4不同的是,回火温度为710℃,回火系数为6.0,回火时间为120分钟。
110.实施例6
111.与实施例4不同的是,回火温度为730℃,回火系数为3.0,回火时间为60分钟。
112.实施例7
113.与实施例1不同的是,按重量百分比计,钢的化学成分为:c 0.6%,si 0.3%,mn 0.5%,cr 1.20%,mo 0.9%,v 0.3%,nb 0.05%,n 0.03%,s 0.005%,p 0.01%,cu 1.5%,ni 1.5%,其中ni/cu=1,余量为fe。
114.实施例8
115.与实施例1不同的是,按重量百分比计,钢的化学成分为:c 0.4%,si 0.21%,mn 0.42%,cr 0.8%,mo 0.6%,v 0.1%,nb 0.01%,al 0.025%,n 0.018%,s 0.001%,p 0.009%,cu 0.0.7%,ni 0.35%,其中ni/cu=0.5;余量为fe。
116.实施例9
117.与实施例1不同的是,按重量百分比计,钢的化学成分为:c 0.45%,si 0.21%,mn 0.42%,cr 0.99%,mo 0.76%,v 0.11%,n 0.018%,s 0.001%,cu 0.99%,ni 0.62%,其中ni/cu=0.62;余量为fe。
118.实施例10
119.与实施例1不同的是,回火温度为750℃。
120.实施例11
121.与实施例1不同的是,回火温度为650℃。
122.实施例12
123.与实施例1不同的是,步骤(3)中,初锻的时间为5min,终锻的时间为5min。
124.实施例13
125.与实施例1不同的是,步骤(3)中,初锻的时间为60min,终锻的时间为60min。
126.实施例14
127.与实施例1不同的是,步骤(3)中,锻造比为20。
128.实施例15
129.与实施例1不同的是,步骤(3)中,锻造比为5。
130.实施例16
131.与实施例1不同的是,步骤(3)中,锻造比为25。
132.实施例17
133.与实施例1不同的是,步骤(3)中,冷却速度为0.5℃/s。
134.实施例18
135.与实施例1不同的是,步骤(4)中,第一预设温度为600℃,第二预设温度为810℃。
136.实施例19
137.与实施例1不同的是,步骤(4)中,第一预设温度为700℃,第二预设温度为860℃。
138.实施例20
139.与实施例1不同的是,步骤(4)中,第二预设温度为750℃。
140.实施例21
141.与实施例1不同的是,步骤(4)中,第二预设温度为900℃。
142.对比例1
143.按重量百分比计,钢的化学成分为:c 0.24%,si 0.20%,mn 0.49%,cr 1.0%,mo 0.80%,nb 0.021%,al 0.023,s 0.0023%,p 0.005%,余量为fe。
144.制备方法如下:
145.(1)按照上述化学组分混合原料,经过真空感应冶炼和浇注获得钢锭;
146.(2)将上述钢锭在1160℃保温,保温时间8小时;
147.(3)将钢锭在奥氏体单相区锻造:初锻温度1100℃,初锻的时间为20min,终锻温度980℃,终锻的时间为15min,锻造比为10,锻造后空冷至室温,冷却速度5℃/s。
148.(4)切割直径为20mm的圆柱形钢样进行热处理:首先钢样随炉升温到910℃保温,保温时间为60分钟;水冷至室温,冷却速度15℃/s;将钢样进行回火处理,回火温度为690℃,9回火时间为60分钟;回火后的钢样出炉水冷至室温,冷却速度12℃/s。
149.对比例2
150.与对比例1不同的是,按重量百分比计,钢的化学成分为:c 0.25%,si 0.20%,mn 0.44%,cr 1.0%,mo 0.80%,v 0.10%,nb 0.020%,al 0.025,s 0.0023%,p 0.005%,余量为fe。
151.对比例3
152.与对比例1不同的是,按重量百分比计,钢的化学成分为:c 0.16%,si 0.24%,mn 0.44%,cr 1.03%,mo 0.79%,v 0.11%,al 0.022,s 0.003%,p 0.005%,余量为fe。
153.对比例4
154.与对比例1不同的是,按重量百分比计,钢的化学成分为:c 0.27%,si 0.20%,mn 0.48%,cr 1.02%,mo 0.80%,v 0.10%,nb 0.006%,al 0.025,s 0.0023%,p 0.005%,余量为fe。
155.对比例5
156.与对比例1不同的是,按重量百分比,油井管用钢的化学成分为c 0.49%,si 0.24%,mn 0.41%,cr 1.0%,mo 0.74%,v 0.21%,nb 0.02%,al 0.01%,n 0.012%,s 0.001%,p 0.008%,余量为fe。
157.制备过程与实施例1相同。
158.对比例6
159.与对比例1不同的是,按重量百分比计,油井管用钢的化学成分为:c 0.55%,si 0.20%,mn 0.38%,cr 0.91%,mo 0.86%,v 0.11%,n 0.01%,s 0.001%,p 0.008%,余量为fe。
160.制备过程与实施例1相同。
161.对比例7
162.与对比例1不同的是,按重量百分比计,油井管用钢的化学成分为:c 0.45%,si 0.21%,mn 0.42%,cr 0.99%,mo 0.76%,v 0.11%,nb 0.01%,al 0.025%,n 0.018%,s 0.001%,p 0.009%,cu 2%,ni 1.24%,其中ni/cu=0.62;余量为fe。
163.制备过程与实施例1相同。
164.对比例8
165.与对比例1不同的是,按重量百分比计,油井管用钢的化学成分为:c 0.45%,si 0.21%,mn 0.42%,cr 0.99%,mo 0.76%,v 0.11%,nb 0.01%,al 0.025%,n 0.018%,s 0.001%,p 0.009%,cu 0.5%,ni 0.31%,其中ni/cu=0.62;余量为fe。
166.制备过程与实施例1相同。
167.对比例9
168.与对比例1不同的是,按重量百分比计,油井管用钢的化学成分为:c 0.45%,si 0.21%,mn 0.42%,cr 0.99%,mo 0.76%,v 0.11%,nb 0.01%,al 0.025%,n 0.018%,s 0.001%,p 0.009%,cu 0.99%,ni 0.396%,其中ni/cu=0.4;余量为fe。
169.制备过程与实施例1相同。
170.对比例10
171.与对比例1不同的是,按重量百分比计,油井管用钢的化学成分为:c 0.45%,si 0.21%,mn 0.42%,cr 0.99%,mo 0.76%,v 0.11%,nb 0.01%,al 0.025%,n 0.018%,s 0.001%,p 0.009%,cu 0.99%,ni 1.089%,其中ni/cu=1.1;余量为fe。
172.制备过程与实施例1相同。
173.将上述各实施例和对比例热处理后的钢样切取力学性能试样,拉伸试样规格为直径5mm,标距25mm,测试温度为室温;冲击试样尺寸为10mm
×
10mm
×
55mm,v型缺口,测试温度为0℃。评价抗ssc性能的试样按照nace tm0177标准,methoda,a溶液,加载应力为733mpa。各实施例和对比例钢的力学性能和抗ssc性能如表1所示。
174.表1
175.176.[0177][0178]
如图1和图2所示,本发明实施例1中的油井管用钢获得的显微组织为回火索氏体和少量奥氏体组织。
[0179]
实施例22
[0180]
按重量百分比计,耐酸腐蚀钢的化学成分为:c 0.091%,si 0.24%,mn 0.51%,cr 1.0%,mo 0.82%,v 0.20%,nb 0.02%,al 0.01%,s 0.001%,p 0.008%,cu 0.92%,ni 0.64%,其中ni/cu=0.7,余量为fe。
[0181]
制备方法如下:
[0182]
(1)按照上述化学成分混合原料,经过真空感应冶炼和浇注获得钢锭;
[0183]
(2)将上述钢锭在1180℃保温,保温时间5小时;
[0184]
(3)将钢锭在奥氏体单相区锻造:初锻温度1120℃,初锻的时间为20min,终锻温度950℃,终锻的时间为20min,锻造比为12,锻造后空冷至室温,冷却速度5℃/s;
[0185]
(4)切割直径为20mm的圆柱形钢样进行热处理:首先将钢样随炉升温到第一预设温度680℃保温,保温时间系数为2.0,保温时间为40分钟;然后继续加热到第二预设温度910℃,保温60分钟,出炉将钢样覆盖保温棉缓冷至室温,冷却速度1.2℃/s;再将钢样进行
回火处理,回火温度为450℃,回火时间为10小时;回火后的钢样出炉空冷至室温,冷却速度5℃/s。
[0186]
实施例23
[0187]
与实施例22不同的是,回火温度为550℃,回火时间为8小时。
[0188]
实施例24
[0189]
与实施例22不同的是,回火温度为600℃,回火时间为6小时。
[0190]
实施例25
[0191]
与实施例22不同的是,按重量百分比计,钢的化学成分为:c 0.14%,si 0.21%,mn 0.50%,cr 1.0%,mo 0.82%,v 0.03%,nb 0.02%,al 0.01%,s 0.001%,p 0.008%,cu 0.93%,ni 0.465%,其中ni/cu=0.5,余量为fe。
[0192]
实施例26
[0193]
与实施例25不同的是,回火温度为550℃,回火时间为8小时。
[0194]
实施例27
[0195]
与实施例25不同的是,回火温度为600℃,回火时间为6小时。
[0196]
实施例28
[0197]
与实施例22不同的是,按重量百分比计,耐酸腐蚀钢的化学成分为:c 0.097%,si 0.21%,mn 0.51%,cr 1.0%,mo 0.82%,v 0.10%,nb 0.015%,al 0.02%,s 0.001%,p 0.008%,cu 1.17%,ni 0.75%,其中ni/cu=0.64,余量为fe。
[0198]
实施例29
[0199]
与实施例28不同的是,回火温度为550℃,回火时间为8小时。
[0200]
实施例30
[0201]
与实施例28不同的是,回火温度为600℃,回火时间为6小时。
[0202]
实施例31
[0203]
与实施例22不同的是,按重量百分比计,钢的化学成分为:c 0.099%,si 0.22%,mn 0.51%,cr 1.03%,mo 0.83%,v 0.01%,nb 0.02%,al 0.03%,s 0.001%,p 0.009%,cu 1.28%,ni 0.72%,其中ni/cu=0.56,余量为fe。
[0204]
实施例32
[0205]
与实施例31不同的是,回火温度为550℃,回火时间为8小时。
[0206]
实施例33
[0207]
与实施例31不同的是,回火温度为600℃,回火时间为6小时。
[0208]
实施例34
[0209]
与实施例22不同的是,按重量百分比计,钢的化学成分为:c 0.05%,si 0.24%,mn 0.51%,cr 0.8%,mo 0.6%,v 0.20%,nb 0.01%,al 0.01%,s 0.001%,p 0.008%,cu 0.7%,ni0.35%,其中ni/cu=0.5,余量为fe。
[0210]
实施例35
[0211]
与实施例22不同的是,按重量百分比计,钢的化学成分为:c 0.15%,si 0.3%,mn 0.6%,cr 1.2%,mo 0.9%,v 0.30%,nb 0.05%,al 0.05%,s 0.005%,p 0.01%,cu 2%,ni 2%,其中ni/cu=1,余量为fe。
[0212]
实施例36
0.005%,余量为fe。
[0247]
对比例13
[0248]
与对比例11不同的是,按重量百分比计,钢的化学成分为:c 0.16%,si 0.24%,mn 0.44%,cr 1.03%,mo 0.79%,v 0.11%,al 0.022,s 0.003%,p 0.005%,余量为fe。
[0249]
对比例14
[0250]
与对比例11不同的是,按重量百分比计,钢的化学成分为:c 0.27%,si 0.20%,mn 0.48%,cr 1.02%,mo 0.80%,v 0.10%,nb 0.006%,al 0.025,s 0.0023%,p 0.005%,余量为fe。
[0251]
对比例15
[0252]
与对比例11不同的是,按重量百分比计,钢的化学成分为:c 0.097%,si 0.21%,mn 0.51%,cr 1.0%,mo 0.82%,v 0.10%,nb 0.015%,al 0.02%,s 0.001%,p 0.008%,cu 0.4%,ni 0.256%,其中ni/cu=0.64,余量为fe。
[0253]
制备方法与实施例22相同。
[0254]
对比例16
[0255]
与对比例11不同的是,按重量百分比计,钢的化学成分为:c 0.097%,si 0.21%,mn 0.51%,cr 1.0%,mo 0.82%,v 0.10%,nb 0.015%,al 0.02%,s 0.001%,p 0.008%,cu 2.5%,ni 1.6%,其中ni/cu=0.64,余量为fe。
[0256]
制备方法与实施例22相同。
[0257]
对比例17
[0258]
与对比例11不同的是,按重量百分比计,钢的化学成分为:c 0.097%,si 0.21%,mn 0.51%,cr 1.0%,mo 0.82%,v 0.10%,nb 0.015%,al 0.02%,s 0.001%,p 0.008%,cu 1.17%,ni 0.468%,其中ni/cu=0.4,余量为fe。
[0259]
制备方法与实施例22相同。
[0260]
对比例18
[0261]
与对比例11不同的是,按重量百分比计,钢的化学成分为:c 0.097%,si 0.21%,mn 0.51%,cr 1.0%,mo 0.82%,v 0.10%,nb 0.015%,al 0.02%,s 0.001%,p 0.008%,cu 1.17%,ni 1.287%,其中ni/cu=1.1,余量为fe。
[0262]
制备方法与实施例22相同。
[0263]
对比例19
[0264]
与对比例11不同的是,按重量百分比计,钢的化学成分为:c 0.091%,si 0.24%,mn 0.51%,cr 1.0%,mo 0.82%,v 0.20%,nb 0.02%,al 0.01%,s 0.001%,p 0.008%,cu 0.92%,余量为fe。
[0265]
制备方法与实施例22相同。
[0266]
热处理后的钢样切取力学性能试样,拉伸试样规格为直径5mm,标距25mm,测试温度为室温;冲击试样尺寸为10mm
×
10mm
×
55mm,v型缺口,测试温度为0℃。
[0267]
评价抗ssc性能的试样按照nace tm0177标准,methoda,a溶液,在饱和h2s环境中加载733mpa应力。各实施例和对比例钢的回火温度、回火时间与之对应的相关性能见表2。
[0268]
表2
[0269]
[0270]
[0271]
[0272][0273]
实施例结果表明,本发明钢获得的显微组织为贝氏体组织,见附图3。
[0274]
本发明钢解决了高强度与高韧性、高强度与抗ssc性能的双重矛盾关系。这主要归因于较低位错密度的贝氏体组织(图3)和高密度的纳米尺寸析出相(图4)起到有利氢陷阱的作用以及在材料表面形成cu的硫化物阻碍氢的进入共同的作用(图5、图6)。
[0275]
从以上的描述中,可以看出,本发明上述的实施例实现了如下技术效果:本发明通过增加碳含量,能够提高油井管用钢的强度;其中,碳含量增加,不仅可以起到固溶强化作用提高强度,而且通过增加析出相的种类(碳化物-cr的碳化物、钒的碳化物和钼的碳化物、氮化物-钒的氮化物和富cu相)和数量,一方面析出相起到析出强化的作用,另一方面析出相还可以充当“氢陷阱”,增加“氢陷阱”密度,从而捕获进入材料的氢,使氢均匀弥散分布在材料基体中,抑制氢扩散和聚集的作用,提高了抗ssc性能;同时通过增加钼含量,有效提高油井管用钢的韧性。综合上述作用,提高了油井管用钢抗ssc性能。通过平衡本发明油井管用钢的各化学成分,解决了高强度与高韧性、高强度与抗ssc性能的双重矛盾关系。
[0276]
本发明基于低碳含量的特点,赋予耐酸腐蚀钢较高的抗ssc性能;并通过增加析出相的种类(碳化物-cr的碳化物、钒的碳化物和钼的碳化物、氮化物-钒的氮化物和富cu相),一方面析出相起到析出强化的作用;同时,通过在化学成分中添加cu元素,可以在材料表面形成阻碍氢进入的“膜”屏障,从而进一步提高本发明耐酸腐蚀钢抗ssc性能。通过nb元素与
c形成碳化物,可以细化晶粒,提高耐酸腐蚀钢的强韧性。通过平衡本发明耐酸腐蚀钢的各化学成分,解决了高强度与高韧性、高强度与抗ssc性能的双重矛盾关系。
[0277]
以上所述仅为本发明的优选实施例而已,并不用于限制本发明,对于本领域的技术人员来说,本发明可以有各种更改和变化。凡在本发明的精神和原则之内,所作的任何修改、等同替换、改进等,均应包含在本发明的保护范围之内。