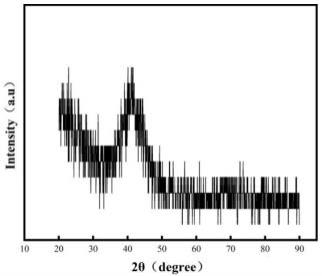
1.本发明涉及高熵合金材料技术领域,特别涉及一种alcrfetimosi六元高熵合金薄膜及其制备方法。
背景技术:2.yeh等在2006年首次提出高熵合金的四个核心效应:热力学上的高熵效应、结晶学上的晶格畸变效应、动力学上的迟滞扩散效应和性能上的鸡尾酒效应,这些效应使得大部分高熵合金在性能上要优于传统合金。高熵合金块体主要通过电弧熔炼方法制备。但制备时样品尺寸有限、工艺成本较高。此外,也有学者采用机械合金法或粉末冶金技术制备高熵合金,但这两种方法工序较为复杂。高熵合金涂层/ 薄膜以高熵合金理论为基础,在降低成本的基础上可获得与高熵合金块体相似的性能。
3.磁控溅射工作温度可控,可在薄壁零件镀nm、μm级薄膜,有利于抑制金属间化合物形成,形成单一固溶体或非晶相,有望应用于复杂薄壁零件表面,提高其硬度、耐磨性和腐蚀性能。
技术实现要素:4.本发明旨在提供一种非等原子比alcrfetimosi高熵合金薄膜材料及制备方法。主要包括靶材的制备、基体的准备以及磁控溅射沉积薄膜。
5.本发明提供的技术方案如下:
6.一种高硬度六元高熵合金薄膜,其特征在于,所述薄膜成分由al、cr、fe、 ti、mo、si六种元素组成,原子比为al 23%~25%、cr 23%~25%、fe 10%~12%、 ti 23%~25%、mo 13%~15%、si 1%~2%。
7.进一步地,所述的高熵合金薄膜,薄膜组织结构为非晶态,硬度为11.21gpa~ 12.99gpa,弹性模量为162.1gpa~177.03gpa。
8.如上所述的高熵合金薄膜的制备方法,其特征在于包括以下步骤:步骤1、靶材粉体制备1a将纯度≥99.9%,粒度~200目的纯金属粉末按照原子比al 23%~25%、cr 23%~ 25%、fe 10%~12%、ti 23%~25%、mo 13%~15%、si1%~2%称量;1b通过行星式球磨机球磨混粉;球磨球料比10∶1;保护气为氩气;转速75r/min;球磨时间18h,每隔3h检查粉体是否粘连;步骤2、合金靶材制备2a通过真空热压烧结炉进行三段式保温热压烧结;炉冷后机械加工至合适靶材尺寸;步骤3、基体的准备3a将单面抛光《100》si和t91钢切成相同尺寸的片状试样;3b切割后用丙酮六面擦净试样,再用去离子水冲洗;然后在无水乙醇中进行超声振动,振动时间15-25min;用吹风机从侧面将基片吹干备用;
步骤4、磁控溅射沉积薄膜;4a将靶材固定在靶材座,si和t91基片放入样品座中,用高温胶固定; 4b打开机械泵、分子泵将本底真空度调为4.3
×
10-4
帕,冲入99.99%氩气作为工作气体;4c在1.8pa工作气压、氩气流量60sccm,溅射功率50w下对靶材和基片进行13-17 min离子清洗,除去表面氧化物;4d将基体加热至300℃,氩气流速30sccm,气压0.5pa,溅射功率200w,持续溅射4-5小时,随后高真空炉冷得到alcrfetimosi高熵合金薄膜。
8.进一步地,步骤1b中球磨球料比10∶1;保护气为氩气;转速75r/min;球磨时间16-20h,每隔3h检查粉体是否粘连。
9.进一步地,步骤2a中烧结环境为真空环境;三段式升温温度分别为470℃、 960℃、1380℃;保温时间分别为90min、30min、2h,制备靶材尺寸为1380℃;保温时间分别为90min、30min、2h,制备靶材尺寸为
10.进一步地,步骤3a中si片为单面抛光,其晶向为《100》;t91钢片为热轧钢板,状态为正火+回火,单面抛光。
11.进一步地,步骤4b中本底真空度4.3
×
10-4
帕,冲入99.99%氩气作为工作气体。
12.进一步地,步骤4c中的工作气压为1.8pa、氩气流量60sccm,溅射功率50w,对靶材和基片的预溅射时间为13-17min。
13.步骤4d中基体温度300℃,氩气流速30sccm,气压0.5pa,溅射功率200w,溅射时间4-5h,高真空炉冷,随后高真空炉冷得到alcrfetimosi高熵合金薄膜。
14.上述的一种高熵合金薄膜厚度约2μm,组织结构呈非晶态,本发明具有以下有益效果:
15.1、薄膜元素分布均匀,表面粗糙度小(1.15nm);由于其结构处于无序状态,且具有al、cr、ti等耐蚀元素,具有优异的耐腐蚀性能;同时,由于元素原子尺寸差异较大,且非晶薄膜没有位错、晶界缺陷,大大提高了薄膜的硬度(11.21gpa~ 12.99gpa)和弹性模量(162.1gpa~177.03gpa)。
16.2、本发明的制备方法可靠,可行性强,可重复性高,成本低,可在复杂构件、薄壁件表面制备高硬度、耐腐蚀的高熵合金薄膜,易于实现工业应用和推广。
附图说明
17.图1为所述a1crfetimosi高熵合金薄膜xrd,表明薄膜为非晶结构。
18.图2为实施例1所述高熵合金薄膜形貌。
19.图3为所述实施例1所述高熵合金薄膜粗糙度。
20.图4为所述实施例1所述高熵合金薄膜纳米压痕。
21.图5为所述实施例2所述高熵合金薄膜形貌。
22.图6为所述实施例2所述高熵合金薄膜纳米压痕。图7为所述实施例2所述合金薄膜位移-弹性模量曲线。
具体实施方式
23.下面结合附图和实施例进一步说明本发明,旨在便于本发明的理解,不起任何限定作用。
24.实施例1
25.本实施例制备的alcrfetimosi高熵合金薄膜,具体制备方法如下:
26.1、靶材粉体制备
27.(1)将纯度≥99.9%,粒度~200目的纯金属粉末按照原子比al 23%~25%、 cr 23%~25%、fe 10%~12%、ti 23%~25%、mo 13%~15%、si 1%~2%进行称量;
28.(2)通过行星式球磨机球磨混粉;球磨球料比10∶1;保护气为氩气;转速75 r/min;球磨时间18h,每隔3h检查粉体是否粘连;
29.2、合金靶材制备
30.将制备好的粉体放入模具中,一起放入真空热压烧结炉中,在真空环境下升温至470℃保温90min,升温至960℃,保温30min,升温至1380℃,保温2h,炉冷;并机械加工靶材尺寸为
31.3、基体的准备
32.将单面抛光《100》si切成相同尺寸的片状试样,试样用丙酮六面擦净,再用去离子水冲洗;然后在无水乙醇中超声振动20min,用吹风机从侧面将基片吹干备用;
33.4、磁控溅射沉积薄膜
34.(1)将靶材固定在靶材座,si基片放入样品座中,用高温胶固定住;
35.(2)打开机械泵、分子泵将本底真空度抽至4.3
×
10-4
pa,并冲入99.99%氩气作为工作气体;
36.(3)在1.8pa工作气压、氩气流量60sccm,溅射功率50w对靶材和基片进行15min离子清洗,除去表面氧化物、杂质等污染物;
37.(4)将基座加热至300℃,氩气流速30sccm,气压0.5pa,溅射功率200w,持续溅射4.5小时,随后高真空炉冷得到alcrfetimosi高熵合金薄膜。
38.按照上述实施例得到的合金薄膜成分均匀,保持了靶材的成分。
39.图2是按照上述实施例得到的合金薄膜表面形貌。
40.图3是按照上述实施例得到的合金薄膜表面粗糙度。
41.图4为所述实施例1所述高熵合金薄膜纳米压痕载荷-位移曲线。
42.表1是按照上述实施例得到的合金薄膜成分。表1
43.实施例2
44.本实施例制备的alcrfetimosi高熵合金薄膜,具体制备方法如下:
45.1、靶材粉体制备
46.(1)将纯度≥99.9%,粒度~200目的纯金属粉末按照原子比al 23%~25%、 cr 23%~25%、fe 10%~12%、ti 23%~25%、mo 13%~15%、si 1%~2%进行称量;
47.(2)通过行星式球磨机球磨混粉;球磨球料比10∶1;保护气为氩气;转速75 r/min;球磨时间18h,每隔3h检查粉体是否粘连;
48.2、合金靶材制备
49.将制备好的粉体放入模具中,一起放入真空热压烧结炉中,在真空环境下升温至470℃保温90min,升温至960℃,保温30min,升温至1380℃,保温2h,炉冷;并机械加工靶材尺寸为
50.3、基体的准备
51.将热轧t91钢板切成相同尺寸的片状试样,六面机械磨光,在丙酮、去离子水、乙醇中分别超声振动20min,单面抛光后,用乙醇擦拭抛光面,并用吹风机从侧面将基片吹干备用;
52.4、磁控溅射沉积薄膜
53.(1)将靶材固定在靶材座,钢基片放入样品座中,利用高温胶固定;
54.(2)打开机械泵、分子泵将本底真空度抽至4.3
×
10-4
pa,并冲入99.99%氩气作为工作气体;
55.(3)在1.8pa工作气压、氩气流量60sccm,溅射功率50w对靶材和基片进行15min离子清洗,除去表面氧化物、杂质等污染物;
56.(4)将基座加热至300℃,氩气流速30sccm,气压0.5pa,溅射功率200w,持续溅射4.5小时,随后高真空炉冷得到alcrfetimosi高熵合金薄膜。
57.图5是按照上述实施例得到的合金薄膜表面形貌。
58.图6是按照上述实施例得到的合金薄膜位移-硬度曲线。
59.图7是按照上述实施例得到的合金薄膜位移-弹性模量曲线。
60.表2是按照上述实施例得到的合金薄膜成分。表2本发明通过熔炼-退火-锻造-热轧-退火的工艺,在显著细化显微组织的同时,有效控制fcc相中析出有序相,释放晶格畸变,有效阻碍位错运动,形成高密度位错,最终形成细小孪晶,有效提升合金的高温性能。与目前广泛研究的cocrfeni(al,mo) 体系中可拉伸且具耐热潜质的高熵合金对比,700℃高温性能优势明显。表3