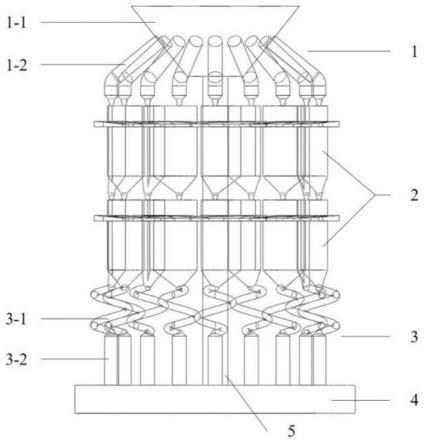
1.本发明涉及航空发动机叶片精密铸造技术领域,具体涉及一种多层模组叠加蜡模结构及其高效制备单晶叶片的方法。
背景技术:2.单晶叶片是航空发动机的重要零件,航空发动机用单晶叶片一般采用熔模铸造法制备。首先进行模组的结构设计,压制蜡模并组合,蜡模模组经脱油脂处理后再经涂挂、撒砂、脱蜡、焙烧等步骤制备模壳,最后将熔融合金液浇入固定于高真空度定向凝固炉的模壳中,抽拉铸型至冷却区域,凝固完成后破真空取样。
3.其中,模组的结构设计作为单晶叶片生产的起始步骤,会直接影响单晶叶片的质量。目前,行业内大批量生产单晶叶片的模组结构普遍为单层模组,即叶片单层排布;在保证单晶叶片生产能力不变的条件下,单层模组的直径大,一方面要求激冷板和定向凝固炉型腔尺寸大,另一方面导致定向凝固过程中横向温度场分布不均匀,等温线发生弯曲,固液界面前沿温度梯度小,易出现过渡段及平台杂晶等凝固缺陷,制约了单晶叶片生产合格率。
4.中国专利cn107931523a和cn210730902u所公开的蜡模组树均为当前工业上普遍应用的单层模组结构,即叶片围绕模组中心单层排布;当面临大批量单晶叶片生产任务时,该种结构为提高生产能力而增加模组中叶片数量时,势必导致模组直径的增加,进而提高了对激冷板和定向凝固炉型腔尺寸的要求。
5.xu等2014年在metallurgical and materials transactions b发表的“multiscale modeling and simulation of directional solidification process of turbine blade casting with mca method”中指出,模组中叶片数量较多时,定向凝固过程中叶片内部的温度场将会倾斜并弯曲。
6.李亚峰的博士学位论文“镍基单晶高温合金涡轮叶片平台杂晶缺陷研究”指出,弯曲的等温线会导致平台边角处优先过冷,达到过冷度后杂晶便形核,杂晶形成倾向随着等温线弯曲程度增大而增大。
7.综上,现有技术大批量制备单晶叶片时普遍使用的是单层模组,此种单层模组的直径较大,一方面要求激冷板和定向凝固炉型腔具有大的尺寸;另一方面造成定向凝固过程中的温度场分布的恶化,包括横向温度场不均匀、等温线弯曲与固液界面前沿温度梯度小,从而导致杂晶形成倾向的增加,严重降低了单晶叶片大批量生产的合格率。
技术实现要素:8.本发明的目的在于提供一种多层模组叠加蜡模结构及其高效制备单晶叶片的方法,采用本发明提供的多层模组叠加蜡模结构,可在保证叶片生产能力不变的条件下,有效缩小模组直径,缩小激冷板和定向凝固炉型腔尺寸,改善定向凝固过程温度场分布,减少凝固缺陷的产生,实现单晶叶片的高效制备。
9.为了实现上述发明目的,本发明提供以下技术方案:
10.本发明提供了一种用于制备单晶叶片的多层模组叠加蜡模结构,包括自上而下依次连接的浇注系统蜡模、叶片蜡模、选晶器蜡模和激冷板蜡模;
11.所述叶片蜡模包括自上而下依次连接的多层叶片蜡模。
12.优选地,所述浇注系统蜡模由浇口杯蜡模和绕所述浇口杯蜡模一圈分布的若干斜浇道蜡模构成;所述斜浇道蜡模的底端与顶层叶片蜡模的顶端相连,所述顶层叶片蜡模的底端与下一层叶片蜡模的顶端相连,以此类推,多层叶片蜡模在垂直方向上首尾相连。
13.优选地,还包括中柱蜡模;所述浇口杯蜡模、中柱蜡模和激冷板蜡模由上到下依次同轴心连接。
14.优选地,所述选晶器蜡模包括上部的螺旋段蜡模和下部的引晶段蜡模。
15.优选地,所述叶片蜡模的层数为两层。
16.本发明提供了一种单晶叶片的制备方法,包括以下步骤:
17.提供上述技术方案所述的多层模组叠加蜡模结构;
18.将所述多层模组叠加蜡模结构依次进行涂挂、撒砂、脱蜡和焙烧,得到模壳;
19.将熔融合金液浇注至所述模壳内,使熔融合金液自下而上定向凝固,脱壳后得到单晶叶片。
20.优选地,所述浇注和凝固均在定向凝固炉中进行;所述使熔融合金液自下而上定向凝固包括:在凝固过程中,将模壳向下抽拉至冷却区域。
21.优选地,所述抽拉的速率为50~150μm/s。
22.优选地,所述脱蜡为蒸汽法脱蜡。
23.优选地,在所述模壳内浇注熔融合金液前,还包括对所述模壳进行预热。
24.本发明提供了一种用于制备单晶叶片的多层模组叠加蜡模结构,包括自上而下依次连接的浇注系统蜡模、叶片蜡模、选晶器蜡模和激冷板蜡模;所述叶片蜡模包括自上而下依次连接的多层叶片蜡模。本发明提供的多层模组叠加蜡模结构在保证叶片生产能力相同的条件下,以叶片蜡模上下叠加的方式构建多层模组叠加蜡模结构,以两层模组叠加蜡模结构为例,可以将模组直径降低到单层模组的一半,有效缩小了模组直径,降低了对激冷板和定向凝固炉型腔的尺寸要求;模组直径的缩小明显改善了定向凝固过程中温度场分布,改善了横向温度场均匀性,降低了等温线弯曲程度,提高了固液界面前沿温度梯度;显著减少了单晶叶片缺陷的产生,能够降低过渡段及平台处杂晶产生倾向,有效提高单晶叶片大批生产的合格率。
附图说明
25.图1为实施例1的多层模组叠加蜡模结构示意图;图1中,1为浇注系统蜡模;1-1为浇口杯蜡模;1-2为斜浇道蜡模;2为叶片蜡模;3为选晶器蜡模;3-1为螺旋段蜡模;3-2为引晶段蜡模;4为激冷板蜡模;5为中柱蜡模;
26.图2为图1的俯视图;
27.图3为图1多层模组叠加蜡模结构中双层叠加叶片的细节展示图;
28.图4为熔融高温合金凝固至叶身处时,单层模组叶片(a)与双层模组叠加叶片下层叶片(b)与上层叶片(c)的温度场模拟结果对比图,标尺上、下限温度分别为合金的液、固相线温度;
29.图5为熔融高温合金凝固至叶片平台处时,单层模组叶片(a)与双层模组叠加叶片下层叶片(b)与上层叶片(c)的温度场模拟结果对比图,标尺上、下限温度分别为合金的液、固相线温度;
30.图6为单层模组叶片(a)和双层模组叠加叶片(b)的凝固晶粒模拟结果对比图。
具体实施方式
31.本发明提供了一种用于制备单晶叶片的多层模组叠加蜡模结构,包括自上而下依次连接的浇注系统蜡模、叶片蜡模、选晶器蜡模和激冷板蜡模;
32.所述叶片蜡模包括自上而下依次连接的多层叶片蜡模。
33.本发明提供的多层模组叠加蜡模结构包括浇注系统蜡模和与所述浇注系统蜡模底端相连的叶片蜡模。作为本发明的一个实施例,所述浇注系统蜡模由浇口杯蜡模和绕所述浇口杯蜡模一圈分布的若干斜浇道蜡模构成。作为本发明的一个实施例,所述斜浇道蜡模为沿浇口杯蜡模周向均匀分布的辐射状结构。在本发明中,所述斜浇道的倾斜角度优选为20
°
~70
°
。在本发明中,所述斜浇道蜡模为多根。
34.作为本发明的一个实施例,所述斜浇道蜡模的底端与顶层叶片蜡模的顶端相连,所述顶层叶片蜡模的底端与下一层叶片蜡模的顶端相连,以此类推,多层叶片蜡模在垂直方向上首尾相连。作为本发明的一个实施例,一根斜浇道蜡模的底端与两个垂直方向上相邻的叶片蜡模相连接,如图3所示。
35.在本发明中,所述叶片蜡模的层数优选为两层。
36.本发明提供的多层模组叠加蜡模结构包括与所述叶片蜡模底端相连的选晶器蜡模。作为本发明的一个实施例,所述选晶器蜡模包括上部的螺旋段蜡模和下部的引晶段蜡模。在本发明中,所述螺旋段蜡模和最底层叶片蜡模的底端相连接。
37.本发明提供的多层模组叠加蜡模结构包括与所述选晶器蜡模底端相连的激冷板蜡模。
38.作为本发明的一个实施例,所述多层模组叠加蜡模结构还包括中柱蜡模;所述浇口杯蜡模、中柱蜡模和激冷板蜡模由上到下依次同轴心连接。
39.作为本发明的一个实施例,当所述叶片蜡模的层数为两层时,所述多层模组叠加蜡模结构为:浇注系统蜡模由浇口杯蜡模和绕所述浇口杯蜡模一圈分布的若干斜浇道蜡模构成;所述斜浇道蜡模的底端与上层叶片蜡模的顶端连接,所述上层叶片蜡模的底端与下层叶片蜡模的顶端连接;所述下层叶片蜡模的底端与螺旋段蜡模的顶端连接,所述螺旋段蜡模的底端与引晶段蜡模的顶端相连接;所述引晶段蜡模的底端与激冷板蜡模连接;所述浇注系统蜡模的浇口杯蜡模、中柱蜡模和激冷板蜡模由上到下依次同轴心连接。
40.本发明还提供了一种单晶叶片的制备方法,包括以下步骤:
41.提供上述技术方案所述的多层模组叠加蜡模结构;
42.将所述多层模组叠加蜡模结构依次进行涂挂、撒砂、脱蜡和焙烧,得到模壳;
43.将熔融合金液浇注至所述模壳内,使熔融合金液自下而上定向凝固,脱壳后得到单晶叶片。
44.本发明提供上述技术方案所述的多层模组叠加蜡模结构。本发明优选采用气动压蜡机压制得到上述技术方案所述的多层模组叠加蜡模结构。在本发明中,所述压制时蜡缸
的温度优选为70~75℃,射嘴温度优选为60~65℃,注射压力优选为0.1~0.6mpa。
45.得到多层模组叠加蜡模结构后,本发明将所述多层模组叠加蜡模结构依次进行涂挂、撒砂、脱蜡和焙烧,得到模壳。在本发明中,所述多层模组叠加蜡模结构在进行涂挂撒砂前优选还包括除油和脱脂处理。本发明采用除油和脱脂处理能够去除模组表面的油脂,提高涂料润湿蜡模表面的能力。
46.本发明优选采用浸涂法对所述多层模组叠加蜡模结构进行涂挂。在具体的涂挂过程中,保持多层模组叠加蜡模结构表面均匀的挂上涂料,避免空白和局部堆积;棱角、凹槽、连接处使用毛笔或特制工具刷涂均匀以避免产生气泡。本发明优选在涂挂每层涂料前清理前一层上的浮砂:涂挂过程中定时搅拌以掌握和调整涂料的粘度。在本发明中,所述撒砂优选为流态化撒砂或雨淋式撒砂。本发明优选将所述多层模组叠加蜡模结构从涂料槽中取出后,待其上剩余的涂料流动均匀而不再连续下滴时即可撒砂;所述撒砂的粒度按涂料层次选择,并与涂料的粘度相适应,面层砂粒度较细,加固层砂粒度较粗。在本发明中,每涂挂和撒砂一层之后,进行干燥和硬化。在本发明的具体实施例中,将所述多层模组叠加蜡模结构进行7层涂挂撒砂,第1层为面层,将70#ec95粉、硅溶胶和料浆混合后进行涂挂,自干8h以上;第2~4层,将35#ec95粉、硅溶胶和料浆混合后进行2层涂挂,自干6h以上;第5~6层,将22#ec95粉、硅溶胶和料浆混合后进行涂挂,自干6h以上;第7层为封严层,仅料浆涂挂,涂挂完成后自干;1~3层干燥后,下层涂挂前用硅溶胶强化且要求良好通风,保证适宜的温度(21
±
1.5℃)与湿度(40
±
10%)。
47.在本发明中,所述脱蜡优选为蒸汽法脱蜡。在本发明中,所述蒸汽脱蜡时,外胆蒸汽压力优选为0.7~0.75mpa,脱蜡时间优选为12~14min,脱蜡温度优选为160~170min。本发明优选在所述脱蜡后,进行通风干燥。
48.在本发明中,所述焙烧优选在加热炉中进行;所述焙烧的温度优选为850℃;保温时间优选为1.5h。本发明在所述焙烧后,优选随炉冷却至500℃后取出,空冷至室温,得到模壳。
49.得到模壳后,本发明将熔融合金液浇注至所述模壳内,使熔融合金液自下而上定向凝固,脱壳后得到单晶叶片。本发明在所述模壳内浇注熔融合金液前,优选还包括对所述模壳进行预热。在本发明中,所述预热的温度优选为1530~1560℃。在本发明中,所述浇注的时间优选低于5s;所述浇注的温度优选为1520~1540℃。
50.在本发明中,所述浇注和凝固优选均在定向凝固炉中进行;所述使熔融合金液自下而上定向凝固优选包括:在凝固过程中,将模壳向下抽拉至冷却区域。在本发明中,所述抽拉的速率优选为50~150μm/s,更优选为100μm/s。
51.在本发明中,所述浇注和凝固优选在真空条件下进行。
52.下面将结合本发明中的实施例,对本发明中的技术方案进行清楚、完整地描述。显然,所描述的实施例仅仅是本发明一部分实施例,而不是全部的实施例。基于本发明中的实施例,本领域普通技术人员在没有做出创造性劳动前提下所获得的所有其他实施例,都属于本发明保护的范围。
53.实施例1
54.第一步,蜡模的结构设计与制备:
55.本实施例采用的双层模组叠加蜡模结构如图1~2所示。
56.a.双层模组叠加蜡模结构的设计与蜡模压制:所述双层模组叠加蜡模结构由浇注系统蜡模1、叶片蜡模2、选晶器蜡模3、激冷板蜡模4及中柱蜡模5五个部分组成;所述浇注系统蜡模1由浇口杯蜡模1-1和绕其一圈均匀分布的若干斜浇道蜡模1-2构成,所述选晶器蜡模3由上部的螺旋段蜡模3-1和下部的引晶段蜡模3-2构成;使用气动压蜡机将以上结构的蜡模压制出;蜡模压制时蜡缸温度为75℃,射嘴温度65℃,注射压力0.5mpa,对所压制的蜡模进行去除毛刺修型操作;
57.b.双层模组叠加蜡模结构的组合:将上述蜡模按照如下顺序进行组合:斜浇道蜡模1-2底端与上层叶片蜡模顶端连接,上层叶片蜡模底端与下层叶片蜡模顶端连接;下层叶片蜡模底端与选晶器蜡模3顶端连接;选晶器蜡模3底端与激冷板蜡模4连接;浇注系统蜡模的浇口杯蜡模1-2、中柱蜡模5、激冷板蜡模4由上到下依次同轴心连接;
58.c.除油和脱脂:去除双层模组叠加蜡模结构表面的油脂。
59.第二步,模壳的制备:
60.a.涂挂和撒砂:采用浸涂法对脱油脂处理后的双层模组叠加蜡模进行涂挂,保持蜡模表面均匀的挂上涂料,避免空白和局部堆积;棱角、凹槽、连接处使用毛笔或特制工具刷涂均匀以避免气泡;涂挂每层涂料前清理前一层上的浮砂:涂挂过程中定时搅拌以掌握和调整涂料的粘度。撒砂采用雨淋式撒砂;将双层模组叠加蜡模从涂料槽中取出后,待其上剩余的涂料流动均匀而不再连续下滴时进行撒砂;撒砂的粒度按涂料层次选择,并与涂料的粘度相适应,面层砂粒度较细,加固层砂粒度较粗;每涂挂和撒砂一层之后,进行充分干燥和硬化;双层模组叠加模壳进行7层涂挂撒砂,(1)面层,70#ec95粉+硅溶胶+料浆按1:2:2的质量比混合后进行涂挂,自干8h以上;(2)2~4层,35#ec95粉+硅溶胶+料浆按1:2:2的质量比混合后进行2层涂挂,自干6h以上;(3)5~6层,22#ec95粉+硅溶胶+料浆按1:2:2的质量比混合后进行涂挂,自干6h以上;(4)封严层,仅料浆涂挂,涂挂完成后自干;1~3层干燥后,下层涂挂前用硅溶胶强化且要求良好通风,保证适宜的温度(21℃
±
1.5℃)与湿度(40%
±
10%);
61.b.脱蜡:打开浇口杯端面模壳以便于排蜡排气,采用蒸汽法脱蜡,外胆蒸汽压力0.7mpa,脱蜡时间13min,脱蜡温度165min;脱蜡完成后在通风条件下充分干燥12h;
62.c.焙烧:双层模组叠加模壳降温至300℃后,放入加热炉中以850℃焙烧1.5h,随炉冷却至500℃后取出,空冷至室温;
63.d.检查与补壳:检查模壳是否存在变形、裂纹、破损等缺陷;修补裂纹、破损等缺陷,去除浇口多余的模壳边沿。
64.第三步,在定向凝固炉中进行叶片的制备:
65.a.检查设备:检查设备的各个阀门是否可以正常运作,供水、供电、供气装置是否正常,根据合金料的多少合理调整测温装置和坩埚底部的相对位置,清理炉腔内部粉尘并擦拭各观察窗口;
66.b.装母合金:将切割好的合金料打掉较大尺寸的缩孔,经砂纸打磨并用酒精清洗后置入坩埚;
67.c.固定模壳:将双层模组叠加模壳的激冷板模壳用特制卡子或铁丝固定于定向凝固炉的激冷板上,并使模壳浇口中心位置与导液漏斗中心位置同轴,确保合金液顺利浇入模壳,关好炉门;
68.d.抽真空:先打开机械泵粗抽真空至1000pa以内,打开罗茨泵继续抽真空至20pa以内,预热扩散泵,待扩散泵油温升至300℃后,打开扩散泵阀门抽高真空,直至6.67
×
10-3
pa;
69.e.升温与加热:按照设定温度曲线升温加热体,加热双层模组叠加模壳;
70.f.合金熔炼:对单晶高温合金进行熔化并精炼:缓慢加电至合金熔化后,对合金熔体进行过热,直至合金液自由表面仅有少量浮渣存在于边缘区域;之后进行摇炉操作,对坩埚边缘进行预热,防止浇注过程中出现喷溅;过热至设定温度后恒温2min;
71.g.浇注与抽拉:将过热后的熔体迅速降温至略高于浇注温度后,升起测温热电偶,将合金液浇入双层模组叠加模壳后,按照100μm/s的抽拉速率将铸型拉入冷却区域;
72.h.取样:凝固完成后,待整个炉体温度降温至100℃以下破真空取样,脱壳并进行修整工作,得到大批量单晶叶片。
73.以使用相同工艺大批量制备单晶叶片的单层模组为对比例,图4为熔融高温合金凝固至叶身底部时,单层模组叶片与双层模组叠加叶片的温度场模拟结果对比图。由图4可以看出,双层模组叠加叶片内等温线弯曲程度低,叶身底部边角部位过冷程度小,难以达到合金的临界形核过冷度,单晶叶片杂晶缺陷形成倾向小。
74.图5为熔融高温合金凝固至叶片平台处时,单层模组叶片与双层模组叠加叶片的温度场模拟结果对比图。由图5可以看出,双层模组叠加叶片等温线弯曲程度低,平台边角处过冷程度小,难以达到合金的临界形核过冷度,单晶叶片杂晶缺陷形成倾向小。
75.图6为单层模组叶片和双层模组叠加叶片的凝固晶粒模拟结果对比图。由图6可以看出,单层模组叶片中有杂晶形成而难以产出合格单晶叶片,双层模组叠加叶片无杂晶形成,成功制备出单晶叶片。
76.以上所述仅是本发明的优选实施方式,应当指出,对于本技术领域的普通技术人员来说,在不脱离本发明原理的前提下,还可以做出若干改进和润饰,这些改进和润饰也应视为本发明的保护范围。