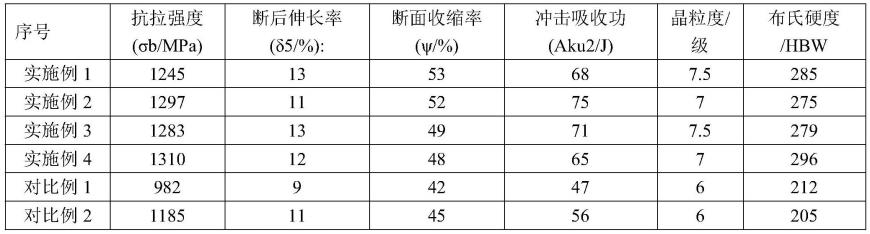
1.本发明属于风电齿轮钢技术领域,具体涉及一种高强韧性风电齿轮钢及其制备方法。
背景技术:2.风力发电机组中的齿轮将风轮在风力作用下所产生的动力传递给发电机并使其得到相应的转速,由于齿面呈高频率的线接触和风电向高速、高载重、低噪声的发展要求,对齿轮钢的耐磨性、韧性、受交变弯曲应力耐疲劳强度和耐齿面接触疲劳损伤要求不断提高。现有采用crmoh钢作齿轮钢由于连铸生产时结晶器内保护渣、水口沉淀物、氧化产物等带入钢液发生卷渣或下夹渣缺陷,钢种成分难以满足钢材力学性能要求,满足炼钢、浇铸过程中产生气孔、夹杂等缺陷使铸态组织均匀致密性下降和轧制敏感,铝、钛含量波动大造成转炉下渣不稳定,使铸坯表面易产生结疱、夹杂和裂纹缺陷,塞棒吹氩结晶液面和结晶器传热壁温度波动较大,导致结晶器出口处坯壳薄且厚度不均匀增加产生裂纹和拉漏。
3.因工艺条件、固液两相区温度较大、杂质元素在固液及边界选分结晶,中等过热的钢液凝固时由较大晶状体并在凝固后期断面柱状晶中心搭接和柱状晶析出溶质元素聚集,产生夹杂物、中心偏析和中心疏松问题,溶质元素在铸坯中心分布不均使钢的力学性能特别是横向性能、延展性、韧性和致密性降低,珠光体带和拉长后的夹杂粗大分散影响对夏比转变温度范围低温处的缺口韧性,不利于后续轧制和改善钢材碳化物网状和抑制马氏体等异常组织;轧制和控冷不当易使铁素体晶粒较粗降低钢材韧性,靠渗氮淬回火调整表面硬度以达到设计齿面的强度和耐磨性,但淬火过程中马氏体亚结构粗大,难以形成稳定的奥氏体岛,降低裂纹扩展阻碍作用,降低韧性,使风电齿轮钢的强度和韧性难以兼顾,造成断齿风险。
技术实现要素:4.本发明旨在至少在一定程度上解决上述技术问题之一,本发明提供一种高强韧性风电齿轮钢及其制备方法。
5.本发明解决其技术问题所采用的技术方案是:
6.一种高强韧性风电齿轮钢,齿轮钢的化学成分按质量百分比计为:c:0.12-0.23%,si:0.17-0.42%,mn:1.7-2.5%,cr:0.4-1.25%,mo:0.5-1.45%,ni:0.35-0.75%,v:0.1~0.35%,b:0.002-0.007%,p≤0.015%,s≤0.015%,cu≤0.01%,al≤0.015%,ti≤0.008%,n≤0.02%,o≤0.002%,余量为fe及不可避免的杂质元素;
7.上述高强韧性风电齿轮钢的制备方法,其制备方法包括依次进行的钢水冶炼、精炼脱氧、连铸、轧制、淬火和回火工序,精炼脱氧工序中软吹氩时间≥30min,连铸工序终控制二冷水量为0.5-0.9l/kg钢,拉矫压下量控制在10~25mm。
8.上述高强韧性风电齿轮钢的制备方法,优选地,其制备方法包括以下步骤:
9.s1、钢水冶炼:将钢铁铁水经kr预处理加入转炉bof吹氧脱碳处理冶炼,在氧化期
向渣层中加造渣料造渣,造渣料选用cao与sio2,控制转炉造渣渣碱度为2.5-3.5,吸收大颗粒夹杂物降低总氧,终点碳含量≥0.12%,出钢全过程吹氩搅拌,控制出钢温度1550℃~1680℃,挡渣出钢获得钢水,满足合金化、化渣量等要求,避免钛含量波动大造成转炉下渣不稳定,从源头上减少了夹杂物的数量,优化出钢成分控制,避免夹杂物的富集造成柱状晶交界面薄弱而易产生裂纹扩展和加工易脆裂现象;
10.s2、精炼脱氧:采用lf+vd炉精炼处理步骤s1的钢水,lf炉的氩气流量为50~100nm3/min,加入铝硅铁脱氧,残al含量控制在≤0.003%,控制[o]≤0.002%,[n]≤0.04%,防止后续过程氧化物夹杂的大量生成,真空脱气后vd炉软吹氩处理,氩气压力为0.3-0.5mpa,软吹氩时间≥30min,出钢温度1530℃~1650℃,保证夹杂物充分上浮,净化钢水,提高钢液纯净度,保证可浇性的同时避免温度过低发生水口堵塞、浇铸中断和连铸表面疱、夹杂和裂纹缺陷,过高对中间包耐火材料的侵蚀而引起铸流失控风险,优化合金和低残余元素控制,得到精炼脱氧钢水;
[0011]
s3、连铸:将步骤s2的精炼脱氧钢水吊至连铸钢包回转台,钢水通过钢包水口进入中间包至面升达开浇位,控制中间包内过热度为5-15℃,采用低过热度浇注,有效改善和降低连铸坯的成分偏析,使钢水浇入结晶器至液面超过浸入式水口下端后加入保护渣,保护渣用量为0.4-0.5kg/t钢,保护渣的组成成分按质量百分数计为:cao:30-45%,al2o3:13~35%,sio2:5-22%,li2o:4-8%,caf2:3-8%,na2o:1-6%,c:10-16%,具有适宜碱度和铺展性,提高保护渣在结晶器中的保温性和吸收钢液中夹杂物,同时防止钢水二次氧化、避免劣化传热和润滑性;
[0012]
结晶器振动并开启结晶器电磁搅拌进行浇铸和拉矫机拉坯,避免结晶器壁沾坯、减小拉矫机的拉坯阻力,搅拌电流50~150a,搅拌频率0.5~1.0hz,采用电磁搅拌细化碳化物尺寸,改善连铸坯的中心质量,控制搅拌强度避免产生负偏析现象,浇注速度控制在0.2~0.4m/min,有利于钢水的顺利浇注,控制结晶;
[0013]
结晶器一冷通水水量控制在350~450m3/h,进出水温差小于等于10℃,水压为0.4-0.6mpa,使钢水在结晶器内形成适宜的坯壳厚度、确保结晶器的安全运行,铸坯拉出结晶器后在足辊区至铸坯导向段水冷确保铸坯出结晶器时能承受钢水的静压力而不破裂,控制二冷水量为0.5-0.9l/kg钢,水压为0.2-0.5mpa,迅速增加坯壳厚度并随着铸坯移动对带有液芯的铸坯冷却使其,避免热裂纹;
[0014]
铸坯经引锭杆牵引穿过拉校机被连续矫直后,送入火焰切割区切下坯头、按定尺切割铸坯得到定尺铸坯,采用多点矫直技术,拉矫机压下量控制在10~25mm,矫直温度控制在850~950℃,采用轻压下技术控制铸坯凝固末端的的凝固过程,防止铸坯中心冷凝收缩产生负压,减轻溶质元素在中心的富集,从而减轻钢水在凝固过程中的成分偏析、中心疏松、中心裂纹和缩孔,在600℃以上的定尺铸坯吊至辊道堆垛,控制缓冷速度2-5℃/min缓冷后,送至精整工段对铸坯进行检查精整,得到连铸坯,连铸坯碳偏析指数在1.05以内,避免降低齿轮强度;
[0015]
s4、轧制:采用控轧控冷工艺,将步骤s3的连铸坯经步进式加热炉加热1050-1250℃并在温度区间保温2-3h,使钢奥氏体化,控制水压≥13mpa高压水除磷后控制初轧温度为980-1050℃进入6道次粗轧,经8道次中轧、6道次预精轧和4道次精轧工序,控制终轧温度为790-880℃,轧制过程中每道次变形率控制在10-18%,提高组织均匀性,轧制为圆钢,轧后
风冷快速冷却,控制冷却速度为6-10℃/min,使钢材表面和中心保持一定温度差,并在600℃下入缓冷坑加保温罩缓冷,控制缓冷速度为1-3℃/min,实现对钢材热轧状态带状组织的控制,奥氏体晶粒度均达7级,带状组织为1.0级,组织均匀、净度高、致密性好,提高淬透性和强韧性,提高表面质量,降低内部缺陷,从而影响淬火回火处理的组织性能和变形;
[0016]
s5、淬火:将步骤s4的圆钢以加热速度170-200℃/h升温至预热区680-800℃,升温至透烧区温度为820-850℃,使钢材各部分温度均匀,保温45-65min,升温至渗碳区温度为860-910℃保温1-2h,降温至扩散区温度为830-860℃保温1-2h,降温至淬火区温度为660-750℃保温1-2h,使奥氏体均匀化,获得珠光体类组织,避免发生贝氏体或马氏体转变,出炉风冷,控制冷却速度为20-35℃/min,控制珠光体转变产物细度,避免大块铁素体产生,提高应力和硬度;
[0017]
s6、回火:控制回火温度为450~570℃保温2-3h处理经步骤s5的圆钢后,喷雾冷却,控制冷却速度为30-45℃/min,控制马氏体针的大小,得到齿轮钢,齿轮钢组织中残余奥氏体≤3级、碳化物≤2级,残余奥氏体和马氏体形状均匀细小,表面和心部硬度、组织稳定,从而提高整体硬度、抗拉强度、屈服强度和冲击韧性。
[0018]
钢的组成成分设计原因为:
[0019]
(1)c:碳通过增加马氏体转变能力提高硬度和强度,进而提高风电齿轮的耐磨性,固化物强化和碳化物析出强化,避免结晶器热流较低和结晶器壁面温度波动大、进而引起坯表面粗糙和结晶器出口处坯壳薄,以但碳再高会增加裂纹敏感性、降低韧性,在两相区的凝固界面处钢的延伸率较低和不均匀增加产生裂纹和拉漏,容易在浇注过程中出现严重鼓肚成带液芯矫直时产生内裂、拉漏或角裂,因此碳含量为0.12-0.23%。
[0020]
(2)mn、si、al:锰和硅都是炼钢脱氧剂、影响钢的机械性能、对铝镇静,锰可提高钢的淬透性,起固溶强化作用以弥补钢中因碳含量降低而引起的强度损失,但锰再高会降低钢的韧性,硅可提高钢的硬度、强度、弹性极限和屈强极限,但硅含量再高会降低韧性、过热敏感性、裂纹和脱碳倾向增大、影响残余奥氏体量,锰和硅控制在较窄范围内,提高mn/si比使脱氧产物是液态硅酸盐,改善可浇性,因此锰含量控制在1.7-2.5%,硅含量控制在0.17~0.42%,al是终脱氧剂可防止坯壳出现针孔和气泡,al与n相结合进可细化晶粒,但al易产生二次氧化和al2o3夹杂物而劣化钢水可浇性、影响铸坯表面和内部质量,因此al含量控制在≤0.015%。
[0021]
(3)cr、ni、mo:铬能够提高钢的淬透性、耐磨性和耐腐蚀性能,可细化珠光体的片层间距,但铬再高会造成δ铁素体含量过高、降低热加工塑性、强度和硬度,钼能强化铁素体、细化晶粒提高淬透性、抗蠕变性能,阻止析出相沿奥氏体晶界析出而避免晶断裂,改善断裂韧性,增加回火稳定性,但再高会降低钢水的液相线温度、增加铸坯敏感性而影响后续加工,降低钢材的接触疲劳寿命,镍能提高冲击性能但再高会造成马氏体转变不完全、残留奥氏体量增多而降低强度和硬度,因此控制cr:0.4-1.25%,mo:0.5-1.45%,ni:0.35-0.75%。
[0022]
(3)v、b:矾能细化钢的晶粒组织、提高钢的强度、韧性和耐磨性,高温熔入奥氏体可增加钢的淬透性、适当提高韧性、提高m体的回火稳定性,降低回火脆性,但矾再高会引起时效脆性,硼可提高钢的淬透性、在淬火+低温回火后能得到良好的冲击值,但硼再高容易引起脆性、降低晶粒粗化温度,因此控制v:0.1~0.35%,b:0.002-0.007%。
[0023]
(4)cu、p、s、ti:铜易导致晶界弱化和热裂倾向,磷和硫是钢中的有害元素,磷在结晶过程中易造成偏析和热裂倾向增大,使钢晶界催化,硫易使两相区凝固界面的延伸率下降、热裂敏感性和热裂指数升高,提高mn/s比提高两相区凝固界面的延伸率,钛的时效析出能力强、具有强韧话效果,但再高会造成析出相沿界面扩展而引发裂纹源,因此控制cu≤0.01%,p≤0.015%,s≤0.015%,ti≤0.008%。
[0024]
(5)n、o:氮过高容易在铸坯内产生针孔,氧易增加钢水中的非金属夹杂物含量导致水口堵塞、浇铸中断或铸坯蜂窝气泡,氮影响钢材的时效性,因此控制n≤0.02%,o≤0.002%。
[0025]
与现有技术相比,本发明的有益效果是:
[0026]
本发明通过适宜的钢成分设计,炼钢成分控制、温度控制、渣料控制,避免夹杂物的富集造成柱状晶交界面薄弱而易产生裂纹扩展和加工易脆裂现象;精炼脱氧控制、吹氩控制、优化合金控制、低残余元素控制,提高钢液纯净度,保证可浇性的同时避免温度过低发生水口堵塞、浇铸中断和连铸表面疱、夹杂和裂纹缺陷;连铸拉速、电磁搅拌和冷却水控制,采用低过热度浇注,避免热裂纹,有效改善和降低连铸坯的成分偏析,减轻钢水在凝固过程中的中心疏松、中心裂纹和缩孔,保证横向性能、延展性、韧性和致密性;采用控轧控冷工艺,组织均匀、净度高、致密性好,提高淬透性和强韧性;淬火使奥氏体均匀化,获得珠光体类组织,控制回火齿轮钢组织中残余奥氏体≤3级、碳化物≤2级,提高整体硬度、抗拉强度、屈服强度和冲击韧性;使风电齿轮钢的强度和韧性得以兼顾,避免断齿风险。
具体实施方式
[0027]
下面详细描述本发明的实施例,下面的实施例是示例性的,旨在用于解释本发明,而不能理解为对本发明的限制。
[0028]
实施例1:
[0029]
发明所述高强韧性风电齿轮钢一种较佳实施方式,所述齿轮钢的化学成分按质量百分比计为:c:0.12%,si:0.35%,mn:1.9%,cr:0.85%,mo:1.23%,ni:0.65%,v:0.13%,b:0.004%,p:0.01%,s:0.005%,cu:0.008%,al:0.008%,ti:0.005%,n:0.008%,o:0.001%,余量为fe及不可避免的杂质元素;其制备方法包括以下步骤:
[0030]
s1、钢水冶炼:将钢铁铁水经kr预处理加入转炉bof吹氧脱碳处理冶炼,在氧化期向渣层中加造渣料造渣,造渣料选用cao与sio2,控制转炉造渣渣碱度为2.8-3,终点碳含量≥0.12%,出钢全过程吹氩搅拌,控制出钢温度1550℃~1680℃,挡渣出钢获得钢水;
[0031]
s2、精炼脱氧:采用lf+vd炉精炼处理步骤s1的钢水,lf炉的氩气流量为50~60nm3/min,加入铝硅铁脱氧,残al含量控制在≤0.003%,控制[o]≤0.002%,[n]≤0.04%,真空脱气后vd炉软吹氩处理,氩气压力为0.35mpa,软吹氩时间≥30min,出钢温度1530℃~1650℃;
[0032]
s3、连铸:将步骤s2的精炼脱氧钢水吊至连铸钢包回转台,钢水通过钢包水口进入中间包至面升达开浇位,控制中间包内过热度为5-15℃,使钢水浇入结晶器至液面超过浸入式水口下端后加入保护渣,保护渣用量为0.45kg/t钢,保护渣的组成成分按质量百分数计为:cao:37%,al2o3:18%,sio2:17%,li2o:6%,caf2:6%,na2o:2%,c:14%;结晶器振动并开启结晶器电磁搅拌进行浇铸和拉矫机拉坯,搅拌电流50~150a,搅拌频率0.5~1.0hz,
浇注速度控制在0.2~0.3m/min;
[0033]
结晶器一冷通水水量控制在380~430m3/h,进出水温差小于等于10℃,水压为0.5mpa,铸坯拉出结晶器后在足辊区至铸坯导向段水冷控制二冷水量为0.6-0.7l/kg钢,水压为0.2mpa;铸坯经引锭杆牵引穿过拉校机被连续矫直后,送入火焰切割区切下坯头、按定尺切割铸坯得到定尺铸坯,拉矫机压下量控制在18~20mm,矫直温度控制在880~900℃,在600℃以上的定尺铸坯吊至辊道堆垛,控制缓冷速度2-4℃/min缓冷后,送至精整工段对铸坯进行检查精整,得到连铸坯,连铸坯碳偏析指数在1.05以内;
[0034]
s4、轧制:采用控轧控冷工艺,将步骤s3的连铸坯经步进式加热炉加热1150-1200℃并在温度区间保温2.5h,控制水压≥13mpa高压水除磷后控制初轧温度为995-1020℃进入6道次粗轧,经8道次中轧、6道次预精轧和4道次精轧工序,控制终轧温度为820-840℃,轧制过程中每道次变形率控制在10-18%,控制冷却速度为6-10℃/min,使钢材表面和中心保持一定温度差,并在600℃下入缓冷坑加保温罩缓冷,控制缓冷速度为1-2℃/min,实现对钢材热轧状态带状组织的控制,奥氏体晶粒度均达7级,带状组织为1.0级;
[0035]
s5、淬火:将步骤s4的圆钢以加热速度178-200℃/h升温至预热区790-800℃,20min升温至透烧区温度为820-830℃保温50min,20min升温至渗碳区温度为860-880℃保温1.5h,20min降温至扩散区温度为830-840℃保温1h,40min降温至淬火区温度为660-680℃保温1h,出炉风冷,控制冷却速度为25-35℃/min;
[0036]
s6、回火:控制回火温度为480~500℃保温2h处理经步骤s5的圆钢后,喷雾冷却,控制冷却速度为30-45℃/min,控制马氏体针的大小,得到齿轮钢,齿轮钢组织中残余奥氏体≤3级、碳化物≤2级,残余奥氏体和马氏体形状均匀细小,表面和心部硬度、组织稳定。
[0037]
实施例2:
[0038]
发明所述高强韧性风电齿轮钢的一种较佳实施方式,所述齿轮钢的化学成分按质量百分比计为:c:0.19%,si:0.24%,mn:2%,cr:0.64%,mo:0.89%,ni:0.45%,v:0.18%,b:0.003%,p:0.015%,s:0.015%,cu:0.005%,al:0.003%,ti:0.007%,n:0.008%,o:0.001%,余量为fe及不可避免的杂质元素;其制备方法包括以下步骤:
[0039]
s1、钢水冶炼:将钢铁铁水经kr预处理加入转炉bof吹氧脱碳处理冶炼,在氧化期向渣层中加造渣料造渣,造渣料选用cao与sio2,控制转炉造渣渣碱度为2.6-3,终点碳含量≥0.12%,出钢全过程吹氩搅拌,控制出钢温度1570℃~1610℃,挡渣出钢获得钢水;
[0040]
s2、精炼脱氧:采用lf+vd炉精炼处理步骤s1的钢水,lf炉的氩气流量为50~80nm3/min,加入铝硅铁脱氧,残al含量控制在≤0.003%,控制[o]≤0.002%,[n]≤0.04%,真空脱气后vd炉软吹氩处理,氩气压力为0.35mpa,软吹氩时间≥30min,出钢温度1530℃~1580℃;
[0041]
s3、连铸:将步骤s2的精炼脱氧钢水吊至连铸钢包回转台,钢水通过钢包水口进入中间包至面升达开浇位,控制中间包内过热度为5-15℃,使钢水浇入结晶器至液面超过浸入式水口下端后加入保护渣,保护渣用量为0.42kg/t钢,保护渣的组成成分按质量百分数计为:cao:39%,al2o3:21%,sio2:12%,li2o:7%,caf2:4%,na2o:2%,c:15%;结晶器振动并开启结晶器电磁搅拌进行浇铸和拉矫机拉坯,搅拌电流50~150a,搅拌频率0.5~1.0hz,浇注速度控制在0.3~0.4m/min;
[0042]
结晶器一冷通水水量控制在380~450m3/h,进出水温差小于等于10℃,水压为
0.45mpa,铸坯拉出结晶器后在足辊区至铸坯导向段水冷控制二冷水量为0.5-0.6l/kg钢,水压为0.35mpa;铸坯经引锭杆牵引穿过拉校机被连续矫直后,送入火焰切割区切下坯头、按定尺切割铸坯得到定尺铸坯,拉矫机压下量控制在12~17mm,矫直温度控制在870~885℃,在600℃以上的定尺铸坯吊至辊道堆垛,控制缓冷速度3-5℃/min缓冷后,送至精整工段对铸坯进行检查精整,得到连铸坯,连铸坯碳偏析指数在1.05以内;
[0043]
s4、轧制:采用控轧控冷工艺,将步骤s3的连铸坯经步进式加热炉加热1090-1230℃并在温度区间保温2.5h,控制水压≥13mpa高压水除磷后控制初轧温度为980-1020℃进入6道次粗轧,经8道次中轧、6道次预精轧和4道次精轧工序,控制终轧温度为835-850℃,轧制过程中每道次变形率控制在10-15%,控制冷却速度为8-10℃/min,使钢材表面和中心保持一定温度差,并在600℃下入缓冷坑加保温罩缓冷,控制缓冷速度为1-3℃/min,实现对钢材热轧状态带状组织的控制,奥氏体晶粒度均达7级,带状组织为1.0级;
[0044]
s5、淬火:将步骤s4的圆钢以加热速度178-190℃/h升温至预热区680-750℃,30min升温至透烧区温度为825-835℃保温60min,30min升温至渗碳区温度为870-895℃保温1h,20min降温至扩散区温度为855-860℃保温1h,40min降温至淬火区温度为680-715℃保温2h,出炉风冷,控制冷却速度为22-35℃/min;
[0045]
s6、回火:控制回火温度为475~480℃保温2h处理经步骤s5的圆钢后,喷雾冷却,控制冷却速度为30-43℃/min,控制马氏体针的大小,得到齿轮钢,齿轮钢组织中残余奥氏体≤3级、碳化物≤2级,残余奥氏体和马氏体形状均匀细小,表面和心部硬度、组织稳定。
[0046]
实施例3:
[0047]
发明所述高强韧性风电齿轮钢的一种较佳实施方式,所述齿轮钢的化学成分按质量百分比计为:c:0.15%,si:0.28%,mn:2.3%,cr:0.96%,mo:0.63%,ni:0.7%,v:0.16%,b:0.005%,p:0.002%,s:0.004%,cu:0.006%,al:0.008%,ti:0.006%,n:0.004%,o:0.001%,余量为fe及不可避免的杂质元素;其制备方法包括以下步骤:
[0048]
s1、钢水冶炼:将钢铁铁水经kr预处理加入转炉bof吹氧脱碳处理冶炼,在氧化期向渣层中加造渣料造渣,造渣料选用cao与sio2,控制转炉造渣渣碱度为2.6-3.5,终点碳含量≥0.12%,出钢全过程吹氩搅拌,控制出钢温度1650℃~1680℃,挡渣出钢获得钢水;
[0049]
s2、精炼脱氧:采用lf+vd炉精炼处理步骤s1的钢水,lf炉的氩气流量为50~100nm3/min,加入铝硅铁脱氧,残al含量控制在≤0.003%,控制[o]≤0.002%,[n]≤0.04%,真空脱气后vd炉软吹氩处理,氩气压力为0.4mpa,软吹氩时间≥30min,出钢温度1550℃~1580℃;
[0050]
s3、连铸:将步骤s2的精炼脱氧钢水吊至连铸钢包回转台,钢水通过钢包水口进入中间包至面升达开浇位,控制中间包内过热度为5-15℃,使钢水浇入结晶器至液面超过浸入式水口下端后加入保护渣,保护渣用量为0.48kg/t钢,保护渣的组成成分按质量百分数计为:cao:32%,al2o3:33%,sio2:6%,li2o:5%,caf2:7%,na2o:1%,c:16%;结晶器振动并开启结晶器电磁搅拌进行浇铸和拉矫机拉坯,搅拌电流50~150a,搅拌频率0.5~1.0hz,浇注速度控制在0.3~0.4m/min;
[0051]
结晶器一冷通水水量控制在365~440m3/h,进出水温差小于等于10℃,水压为0.55mpa,铸坯拉出结晶器后在足辊区至铸坯导向段水冷控制二冷水量为0.8-0.9l/kg钢,水压为0.45mpa;铸坯经引锭杆牵引穿过拉校机被连续矫直后,送入火焰切割区切下坯头、
按定尺切割铸坯得到定尺铸坯,拉矫机压下量控制在18~25mm,矫直温度控制在870~910℃,在600℃以上的定尺铸坯吊至辊道堆垛,控制缓冷速度2-5℃/min缓冷后,送至精整工段对铸坯进行检查精整,得到连铸坯,连铸坯碳偏析指数在1.05以内;
[0052]
s4、轧制:采用控轧控冷工艺,将步骤s3的连铸坯经步进式加热炉加热1090-1130℃并在温度区间保温2h,控制水压≥13mpa高压水除磷后控制初轧温度为1030-1050℃进入6道次粗轧,经8道次中轧、6道次预精轧和4道次精轧工序,控制终轧温度为790-835℃,轧制过程中每道次变形率控制在12-16%,控制冷却速度为6-8℃/min,使钢材表面和中心保持一定温度差,并在600℃下入缓冷坑加保温罩缓冷,控制缓冷速度为1-3℃/min,实现对钢材热轧状态带状组织的控制,奥氏体晶粒度均达7级,带状组织为1.0级;
[0053]
s5、淬火:将步骤s4的圆钢以加热速度175-195℃/h升温至预热区730-750℃,升温至透烧区温度为825-835℃保温50min,20min升温至渗碳区温度为875-805℃保温1.5h,20min降温至扩散区温度为845-855℃保温2h,40min降温至淬火区温度为730-750℃保温1h,出炉风冷,控制冷却速度为23-33℃/min;
[0054]
s6、回火:控制回火温度为545~570℃保温2.5h处理经步骤s5的圆钢后,喷雾冷却,控制冷却速度为30-43℃/min,控制马氏体针的大小,得到齿轮钢,齿轮钢组织中残余奥氏体≤3级、碳化物≤2级,残余奥氏体和马氏体形状均匀细小,表面和心部硬度、组织稳定。
[0055]
实施例4:
[0056]
发明所述高强韧性风电齿轮钢的一种较佳实施方式,所述齿轮钢的化学成分按质量百分比计为:c:0.23%,si:0.4%,mn:2.4%,cr:1.1%,mo:0.65%,ni:0.5%,v:0.32%,b:0.007%,p:0.009%,s:0.008%,cu:0.009%,al:0.01%,ti:0.008%,n:0.015%,o:0.001%,余量为fe及不可避免的杂质元素;其制备方法包括以下步骤:
[0057]
s1、钢水冶炼:将钢铁铁水经kr预处理加入转炉bof吹氧脱碳处理冶炼,在氧化期向渣层中加造渣料造渣,造渣料选用cao与sio2,控制转炉造渣渣碱度为2.8-3.5,终点碳含量≥0.12%,出钢全过程吹氩搅拌,控制出钢温度1630℃~1660℃,挡渣出钢获得钢水;
[0058]
s2、精炼脱氧:采用lf+vd炉精炼处理步骤s1的钢水,lf炉的氩气流量为50~100nm3/min,加入铝硅铁脱氧,残al含量控制在≤0.003%,控制[o]≤0.002%,[n]≤0.04%,真空脱气后vd炉软吹氩处理,氩气压力为0.45mpa,软吹氩时间≥30min,出钢温度1530℃~1600℃;
[0059]
s3、连铸:将步骤s2的精炼脱氧钢水吊至连铸钢包回转台,钢水通过钢包水口进入中间包至面升达开浇位,控制中间包内过热度为5-15℃,使钢水浇入结晶器至液面超过浸入式水口下端后加入保护渣,保护渣用量为0.48kg/t钢,保护渣的组成成分按质量百分数计为:cao:37%,al2o3:20%,sio2:19%,li2o:4%,caf2:4%,na2o:6%,c:10%;结晶器振动并开启结晶器电磁搅拌进行浇铸和拉矫机拉坯,搅拌电流50~150a,搅拌频率0.5~1.0hz,浇注速度控制在0.2~0.35m/min;
[0060]
结晶器一冷通水水量控制在365~450m3/h,进出水温差小于等于10℃,水压为0.55mpa,铸坯拉出结晶器后在足辊区至铸坯导向段水冷控制二冷水量为0.7-0.8l/kg钢,水压为0.45mpa;铸坯经引锭杆牵引穿过拉校机被连续矫直后,送入火焰切割区切下坯头、按定尺切割铸坯得到定尺铸坯,拉矫机压下量控制在16~24mm,矫直温度控制在910~950℃,在600℃以上的定尺铸坯吊至辊道堆垛,控制缓冷速度2-5℃/min缓冷后,送至精整工段
对铸坯进行检查精整,得到连铸坯,连铸坯碳偏析指数在1.05以内;
[0061]
s4、轧制:采用控轧控冷工艺,将步骤s3的连铸坯经步进式加热炉加热1180-1240℃并在温度区间保温2h,控制水压≥13mpa高压水除磷后控制初轧温度为985-1040℃进入6道次粗轧,经8道次中轧、6道次预精轧和4道次精轧工序,控制终轧温度为792-815℃,轧制过程中每道次变形率控制在10-14%,控制冷却速度为6-10℃/min,使钢材表面和中心保持一定温度差,并在600℃下入缓冷坑加保温罩缓冷,控制缓冷速度为1-3℃/min,实现对钢材热轧状态带状组织的控制,奥氏体晶粒度均达7级,带状组织为1.0级;
[0062]
s5、淬火:将步骤s4的圆钢以加热速度190-200℃/h升温至预热区765-800℃,10min升温至透烧区温度为835-845℃保温55min,20min升温至渗碳区温度为875-895℃保温1.5h,20min降温至扩散区温度为845-860℃保温2h,40min降温至淬火区温度为690-710℃保温1.5h,出炉风冷,控制冷却速度为22-35℃/min;
[0063]
s6、回火:控制回火温度为550~570℃保温2h处理经步骤s5的圆钢后,喷雾冷却,控制冷却速度为35-45℃/min,控制马氏体针的大小,得到齿轮钢,齿轮钢组织中残余奥氏体≤3级、碳化物≤2级,残余奥氏体和马氏体形状均匀细小,表面和心部硬度、组织稳定。
[0064]
对比例1:
[0065]
crnimoh齿轮钢的组成成分按质量百分数计为:c:0.25%,si:0.37%,mn:0.6%,cr:0.35%,mo:0.15%,ni:0.75%,p:0.02%,s:0.01%,cu:0.1%,al:0.02%,ti:0.008%,n:0.008%,o:0.002%。
[0066]
对比例2:
[0067]
crmnmoh齿轮钢的组成成分按质量百分数计为:c:0.17%,si:0.37%,mn:0.85%,cr:1.4%,mo:0.2%,p:0.02%,s:0.01%,cu:0.15%,al:0.018%,ti:0.009%,n:0.008%,o:0.002%。
[0068]
按照gb/t228.1进行金属拉伸试验,按照gb/t229进行夏比摆锤冲击试验,按照gb/231.1测试硬度,按照gb/t1979测试结构钢低倍组织缺陷,按照gb/t2975测试钢力学性能,按照gb/t6394测试金属晶粒度,按照gb/t10561测试钢中非金属夹杂物,实施例与对比例的测试结果如下:
[0069]
表1
[0070][0071]
表2
[0072][0073]
由上表1和表2可知,本发明通过适宜的钢成分设计,炼钢成分控制、温度控制、渣料控制,避免夹杂物的富集造成柱状晶交界面薄弱而易产生裂纹扩展和加工易脆裂现象;精炼脱氧控制、吹氩控制、优化合金控制、低残余元素控制,提高钢液纯净度,保证可浇性的同时避免温度过低发生水口堵塞、浇铸中断和连铸表面疱、夹杂和裂纹缺陷;连铸拉速、电磁搅拌和冷却水控制,采用低过热度浇注,避免热裂纹,有效改善和降低连铸坯的成分偏析,减轻钢水在凝固过程中的中心疏松、中心裂纹和缩孔,保证横向性能、延展性、韧性和致密性;采用控轧控冷工艺,组织均匀、净度高、致密性好,提高淬透性和强韧性;淬火使奥氏体均匀化,获得珠光体类组织,控制回火齿轮钢组织中残余奥氏体≤3级、碳化物≤2级,提高整体硬度、抗拉强度、屈服强度和冲击韧性;降低夹杂物,细化晶粒,使风电齿轮钢的强度和韧性得以兼顾,避免断齿风险。
[0074]
上文所列出的一系列的详细说明仅仅是针对本发明的可行性实施例的具体说明,它们并非用以限制本发明的保护范围,凡未脱离本发明技艺精神所作的等效实施例或变更均应包含在本发明的保护范围之内。