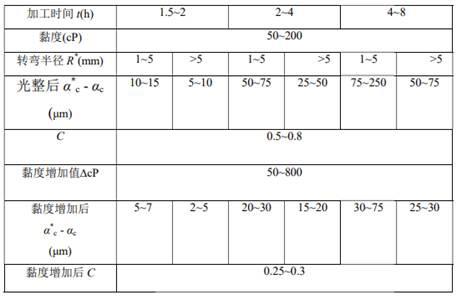
1.本发明涉及内流道的精密加工领域,尤其涉及具有转弯结构的微细内流道的表面光整方法、微细内流道工件以及光整介质。
背景技术:2.具有微细复杂内流道结构的零件在航空航天、船舶、核、汽车、模具等工业领域有着极其广泛的应用,特别是与流体动力系统相关的零部件常常具有微细流道、深小孔及微细流道与深小孔联通等复杂内腔结构,起到对流体的输运、交换或施加液压力等功能,如航空/航天/船舶/汽车各类发动机燃油喷嘴、热交换器、液压组件、油路控制节流器等。
3.可加工微细复杂内流道的工艺技术包括精密机加工、飞秒/水导/长脉冲激光加工、电火花加工及增材制造(3d打印)等。除增材制造技术外,其他单一工艺加工的微细复杂内流道结构相对简单,且长径比较小,需结合焊接等其他组合工艺才可加工微细复杂内流道。精密机加工的微细复杂内流道会产生毛刺、拐点尖角或接刀台阶等问题;飞秒激光加工的内流道表面会产生粘附的残渣颗粒和表面“台阶”效应;水导/长脉冲激光及电火花加工的内流道表面会产生重熔层;增材制造(3d打印)是一种将复杂三维结构零件模型离散为二维结构进行逐层叠加成形的技术,它使复杂微细复杂内流道零件一体化成型成为可能,因而在航空航天、汽车、模具等工业领域的应用日趋增多。然而,增材制造技术在成型零件过程中因存在温度梯度和逐层成型等自身工艺特点,导致零件内流道表面存在半烧结或粘结的粉末颗粒以及表面“台阶”效应。
4.机加工毛刺、飞秒激光加工内流道粘附烧结颗粒、增材制造内流道表面粘结粉末等都会影响零件的使用性能和安全性:当内流道中通入的流体与表层高速摩擦造成毛刺、粘附残渣颗粒或粘结粉末脱落时会成为多余物而随流体到处扩散,或堵塞油路或引起机械磨损故障,从而造成重大安全事故;粗糙度大的内表面在长期使用过程中易成为疲劳裂纹源,若是高温油路系统还易导致积碳现象发生;机加工流道表面的刀纹、拐点尖角或接刀台阶,飞秒激光及增材制造加工内流道表面的“台阶”现象等都会导致流体运动过程产生湍流、涡流和流体沿程阻力急剧增加,甚至造成流体失控,产生振动而降低零件使用寿命。粗糙表面也会使流体中产生大量空化气泡影响燃烧和液力,甚至产生空化腐蚀;对于一些特定材质的零件(如空心叶片)内流道及联通小孔,因重熔层表面易出现微裂纹而导致零件过早失效,因而要求减少重熔层厚度或不允许出现重熔层。
5.因此,通过精密机加工、飞秒/水导/长脉冲激光加工、电火花加工、增材制造(3d打印)等技术加工流体动力零部件内流道表面时,会带来毛刺、粘结粉末和烧结颗粒等残留物、表面粗糙及重熔层等不利问题,需要采用合适的表面光整技术消除这些不利影响后才能满足产品的性能要求。
6.但目前可以有效地对微细复杂内流道表面光整的技术尚未出现,以至于目前对于增材制造的微细复杂内流道工件,其内表面的粗糙度一般都只具有增材制造后的原始平均粗糙度ra≥6.3μm,没有出现内流道的表面最优粗糙度ra小于或等于1.6 μm的产品,对于激
光加工、电火花加工的微细复杂内流道工件没有出现内流道的表面最优粗糙度ra小于或等于0.8 μm的产品;以及对于机加工的微细复杂内流道工件没有出现内流道的表面最优粗糙度ra小于或等于0.4μm的产品,而目前微细复杂内流道若具有s型弯、l型弯、u型弯、o型弯等复杂异形流道,无法采用只能进行直线进给的机加工实现,而只能通过增材制造等方式实现,因此目前也没有出现对于增材制造的微细异形复杂内流道表面最优粗糙度ra小于或等于1.6 μm的产品。
技术实现要素:7.本技术的目的在于提供一种用于具有转弯结构的微细内流道的表面光整方法、具有转弯结构的微细内流道工件以及光整介质。
8.第一方面,本技术提供用于具有转弯结构的内流道的表面光整方法,所述微细内流道的口径小于或等于3mm以及长径比大于或等于50:1,所述微细内流道具有转弯段以及直线段,所述转弯段的转弯角大于90
°
以及转弯半径小于或等于5mm,所述光整方法包括:采用液体固体两相流光整介质,所述光整介质的液体相黏度《1000cp,所述光整介质的固体相为磨粒;对所述光整介质施加预定压力,使得所述光整介质在微细内流道内以》5m/s的流速流动,并且所述光整介质在所述微细内流道的一端流入其内部的流量达到所述微细内流道的口径所能容纳流量的饱和值,使内流道内部的液压力处于憋压状态;所述光整介质在标准时间段光整所述内流道,使得在所述标准时间段所述内流道的表面最优粗糙度满足目标值,且所述光整介质的液体相的黏度至少为第一阈值,使得微细内流道的所述转弯段与所述直线段光整后的单边减薄量的差异值在公差范围之内。
9.本技术实施例的技术方案中,通过采用光整介质的液体相的黏度为小于1000cp的液体,两相流的光整介质在微细内流道内的流速》5m/s,以及在微细内流道的一端流入其内部的流量,达到所述微细内流道的口径所能容纳流量的饱和值,内流道内部的液压力处于憋压状态,形成液体载动磨粒对微细内流道高效磨抛的手段,即通过低黏度的液体相、流体流速以及饱和流量这三者的协同作用,解决了微细内流道光整加工的难题。其原理在于,首先,由于低黏度的液体相、光整介质的流动流速以及饱和流量这三者的协同作用,使得光整介质可以流畅地进入微细内流道并且在微细内流道内形成类似于非牛顿流体的状态,流体边界层平行内流道表面,如“刀具般”坚硬的非牛顿流体中磨粒剪切摩擦实现粗糙表面凸点靶向加工,另外,由以上三者的协同作用,还使得光整介质中磨粒与微细内流道表面产生摩擦微切削力,因此可以不受微细内流道的材料限制而能够获得表面最优粗糙度与磨粒平均刃尖接触长度范围一致的超镜面质量。另外,发明人发现,对于所述转弯段的转弯角大于90
°
以及转弯半径小于或等于5mm的转弯结构,即使达到表面最优粗糙度满足目标值,然而面临转弯段与直线段的单边减薄量的尺寸差异超过公差范围的问题,采用液体相的黏度至少为第一阈值的方案,使得转弯结构的表面最优粗糙度既可以满足目标值的要求,也可以避免转弯段与直线段的尺寸差异超过公差范围的发生。
10.在一些实施例中,所述光整介质的液体相为水基液体。
11.在一些实施例中,所述磨粒具有表面尖角结构,磨粒刃尖平均切削深度为1.4nm ~ 14nm,磨粒刃尖平均接触长度为50nm ~ 1000nm。
12.在一些实施例中,所述标准时间段t0满足以下公式:
其中,α
*c
ꢀ‑ꢀ
αc为微细内流道的转弯段和直线段加工后单边减薄量差异值, c为工程常数,b为磨粒刃尖平均接触长度,l为磨粒刃尖平均切削深度,σw为工件材料屈服极限,r
*
为转弯段的转弯半径。
13.在一些实施例中,所述光整介质在标准时间段光整所述微细内流道,至所述微细内流道的表面最优粗糙度达到目标值,所述标准时间段通过以下步骤得到:所述光整介质在初始时间段光整所述微细内流道,检测微细内流道的表面最优粗糙度,若表面最优粗糙度符合所述目标值则该初始时间段为所述标准时间段;若表面最优粗糙度未达到所述目标值,则逐次增加步进时间段,直至表面最优粗糙度达到目标值,对应的总时间段即为所述标准时间段;其中,所述初始时间段以及步进时间段根据所述磨粒对应的单边减薄速率以及微细内流道的初始平均表面粗糙度得到;所述黏度的第一阈值通过以下步骤得到:若表面最优粗糙度达到目标值,微细内流道转弯段与直线段的单边减薄量尺寸差异超过公差范围和/或转弯结构出现过磨抛变粗、变形甚至破损,在所述液体相的原有的黏度的基础上,步进地增加增粘剂添加量1g/l~2g/l及对应黏度增量10cp~20cp,并相应增加预定压力,使得原有的液体相速度不变,不断步进地增加黏度直至在到达原有的标准时间段及表面最优粗糙度满足目标值,以及微细内流道转弯段与直线段的单边减薄量尺寸差异在公差范围之内,此时的黏度即为液体相的黏度的第一阈值。
14.在一些实施例中,所述光整方法还包括,内流道光整后,内流道口径扩大值对应的表面最优粗糙度满足以下公式:其中,ra
*
为内流道光整后端口口径扩大后的表面最优粗糙度,ra0为微细内流道的初始平均表面粗糙度,δ为端口口径扩大值, k为凹凸磨削比系数。
15.在一些实施例中,所述预定压力p满足以下公式:其中,ra0为微细内流道的初始平均表面粗糙度,ra为经过光整后微细内流道的表面最优粗糙度的目标值,t为初始时间段。l为磨粒刃尖平均切削深度,b为磨粒刃尖平均接触长度,ρ
l
为水基液体相密度,ρ
p
为磨粒固体相密度、σw为工件材料屈服极限、χ为达到饱和流量的增压比,re为液体相的雷诺数,l为内流道的长度,d为内流道的口径,d为磨粒粒径,k为凹凸磨削比系数。
16.在一些实施例中,所述微细内流道的表面最优粗糙度达到目标值后,以所述预定压力往所述微细内流道中注入清洗介质,所述清洗介质与所述光整介质的液体相互溶,直至从所述微细内流道流出的清洗介质出现丁达尔效应为止。
17.在一些实施例中,所述光整介质在标准时间段光整所述微细内流道,判断所述光整介质在所述微细内流道的流速或流量,若流速或流量达到规定值,则表面最优粗糙度达
到所述目标值。
18.在一些实施例中,所述的微细内流道包括三维空间走向的含s型弯、l型弯、u型弯、o型弯、螺旋弯等转弯结构,所述光整介质的液体相包含有高分子增粘剂。
19.第二方面,本技术提供一种微细内流道工件,该微细内流道工件经过以上第一方面所述的光整方法得到。
20.在一些实施例中,所述微细内流道工件具有口径小于或等于3mm,长径比大于或等于50:1的微细内流道,所述微细内流道具有转弯段以及直线段,所述转弯段的转弯角大于90
°
以及转弯半径小于或等于5mm,通过增材制造、铸造、激光加工、电火花加工等得到所述微细内流道工件,所述微细内流道光整后具有表面最优粗糙度ra小于或等于1.6μm的内表面,且所述微细内流道的所述转弯段与所述直线段的单边减薄量的差异值在0.075mm之内。
21.在一些实施例中,所述微细内流道工件为增材制造的航空发动机燃油喷嘴。
22.第三方面,本技术提供一种光整介质,用于以上第一方面所述的光整方法,所述光整介质包括液体相以及固体相,所述液体相黏度《1000cp,所述固体相包括磨粒,并且所述光整介质的液体相的黏度至少为第一阈值,使得所述光整方法光整后的微细内流道转弯段与直线段的单边减薄量尺寸差异在公差范围之内。
23.在一些实施例中,所述光整介质的液体相加入有高分子增粘剂。
附图说明
24.本发明的上述的以及其他的特征、性质和优势将通过下面结合附图和实施例的描述而变得更加明显,需要注意的是,附图均仅作为示例,其并非是按照等比例的条件绘制的,并且不应该以此作为对本发明实际要求的保护范围构成限制,其中:图1是根据本技术的一些实施例的光整方法的流程示意图。
25.图2是根据本技术的一些实施例的转弯结构的原理示意图。
26.图3是根据本技术的一些实施例的光整方法的微切削力的原理示意图。
27.图4是根据本技术的另一些实施例的光整方法的流程示意图。
28.图5是根据本技术的又一些实施例的光整方法的流程示意图。
29.图6是根据本技术的第一实施例的光整方法的微细内流道的转弯段的结构示意图。
30.图7是根据本技术的第一实施例的光整方法对图6所示的结构进行光整的转弯段的图片。
31.图8是根据第一实施例的对比方案的光整方法对图6所示的结构进行光整的转弯段的图片。
具体实施方式
32.下述公开了多种不同的实施所述的主题技术方案的实施方式或者实施例。为简化公开内容,下面描述了各元件和排列的具体实例,当然,这些仅仅为例子而已,并非是对本发明的保护范围进行限制。“一个实施例”、“一实施例”、和/或“一些实施例”意指与本技术至少一个实施例相关的某一特征、结构或特点。因此,应强调并注意的是,本说明书中在不同位置两次或多次提及的“一实施例”或“一个实施例”或“一替代性实施例”并不一定是指
同一实施例。此外,本技术的一些实施例、又一些实施例、再一些实施例等表述中的某些特征、结构或特点可以进行适当的组合。
33.本技术中使用了流程图用来说明根据本技术的实施例的系统所执行的操作。应当理解的是,前面或下面操作不一定按照顺序来精确地执行。也可以将其他操作添加到这些过程中,或从这些过程移除某一步或数步操作。
34.另外,以下所述的平均粗糙度,即在测量的表面选取多个区域进行测量取平均值,得到该测量表面的平均粗糙度。以下所述的最优粗糙度,即在测量的表面选取多个区域进行测量并取最小值,得到该测量表面的最优粗糙度。例如进行粗糙度测量时,例如粗糙度测量某个区域可以为长度为8mm的管路段,在测量的管路选取多个长度为8mm的管路段测量并去最小值。
35.具有微细复杂内流道结构的零件在航空航天、船舶、核、汽车、模具等工业领域有着极其广泛的应用,然而,目前的加工工艺,例如通过精密机加工、飞秒/水导/长脉冲激光加工、电火花加工、增材制造(3d打印)等技术加工流体动力零部件内流道表面时,会带来毛刺、粘结粉末和烧结颗粒等残留物、粗糙表面及重熔层等不利问题,需要采用合适的表面光整技术消除这些不利影响后才能满足产品的性能要求。
36.目前对于增材制造的微细内流道工件没有出现内流道的表面最优粗糙度ra小于或等于1.6 μm的产品,对于激光加工、电火花加工的微细内流道工件没有出现内流道的表面最优粗糙度ra小于或等于0.8 μm的产品;以及对于机加工的微细内流道工件没有出现内流道的表面最优粗糙度ra小于或等于0.4μm的产品,而微细内流道若具有s型弯、l型弯、u型弯、o型弯等异形流道结构,无法采用直线进给的机加工实现,而只能通过增材制造等方式实现,因此目前也没有出现对于增材制造的微细内流道表面最优粗糙度ra小于或等于1.6 μm的产品。
37.发明人经过深入研究,对多种的内流道表面光整方法进行了尝试以及对比,发现对于零件内流道口径较大(》3mm)、长径比较小(<50:1),且呈近似直线走向时,可采用手工抛磨、化学、电化学、电浆、磁力、磁流变、磨粒流、水射流及超声波等常见方法进行光整,然而,对于内流道口径较小(小于或等于3mm)、长径比较大(大于或等于50:1)的微细内流道而言:(1)采用磨粒流技术,利用刚性较大的半固态软性膏体光整介质对内腔通过挤压衍磨机理光整,发明人发现,这种雷诺数极小状态的蠕变流体很难通过复杂长程微细流道实现均匀加工,易于在拐弯及死角堵塞,强行通过会造成流道变形甚至憋裂流道。即使勉强通过长径比≥50:1内流道时,也会出现随流体行程增加而压力及流速急剧衰减,导致内流道端口“过磨抛”而内部由于压力和流速损失过大而“未磨抛”。此外,不溶于水的胶体磨粒流介质易在内流道拐弯、死角处残留,在完成加工后很难甚至根本无法被彻底清除。
38.(2)采用磨料水射流技术,也被称为微磨料浆体射流、高速流及高速水粒子光整,通过对水射流喷嘴施加液压力,利用喷嘴喷出带有磨粒的水射流冲击动能冲蚀去除工件表层材料,水射流喷嘴与零件表面保持较短的距离,因此磨料水射流技术很难作用于内流道口径较小(小于或等于3mm)、长径比较大(大于或等于50:1)的微细内流道;(3)采用磁力光整技术,其只能对口径》3mm且呈近直线走向的内流道表面做轻微光亮化加工,而无法对口径小于或等于3mm且呈三维空间走向的含s型弯、l型弯、u型弯、o型
弯、螺旋弯微细复杂内流道进行有效的表面光整,其原因在于,磁力光整是利用较大尺寸磁针磨粒的一种柔性加工,其原理是表面凸点和凹点在外加磁场的作用下会被同时加工,因而这些柔性加工手段只能对表面做轻微光亮化改善,即使材料去除量很大也不能显著改善表面的“台阶”效应、降低表面粗糙度及大尺度剥离表面粘附的粉末、颗粒和毛刺改善;另外,这种方法由于受制磁场运动也无法应对零件上呈三维空间走向的复杂内流道光整;(4)采用化学光整的方法,当内流道口径很小,可容纳的腐蚀溶液较少,化学光整方法的效率会极低甚至局部出现反应气泡塞积而无法光整;(5)采用电化学、电浆光整及超声波方法,因很难在狭小呈三维空间走向的含s型弯、l型弯、u型弯、o型弯、螺旋弯等流道内放置仿形电极,从而无法光整微细复杂内流道;另外,对于(4)、(5),化学、电化学、电浆光整等方法还会对流道基体材料显微组织产生多种腐蚀及变质层缺陷,腐蚀液和反应气体也会对环境和设备有不利影响;同时,(4)、(5)也是一种柔性加工手段,同样会面临(3)类似的缺点,只能对表面做轻微光亮化改善,即使材料去除量很大也不能显著改善表面的“台阶”效应、降低表面粗糙度及大尺度剥离表面粘附的粉末、颗粒和毛刺。
39.综上所述,发明人经过深入研究发现,上述的加工方法,其对于微细内流道的结构而言,都会面临很难深入微细内流道的内部光整和/或光整质量不理想的问题,因此很难适用于微细内流道的光整加工。
40.基于以上,发明人进一步深入研究,发明了一种微细内流道的表面光整方法,通过采用黏度为小于1000cp液体相的两相流光整介质,两相流的光整介质在微细内流道内的流速》5m/s,以及在微细内流道的一端流入其内部的流量,达到所述微细内流道的口径所能容纳流量的饱和值,内流道内部的液压力处于憋压状态,形成液体相对微细内流道的饱和流量的手段,即通过低黏度的液体相、光整介质的流体流速以及饱和流量这三者的协同作用,解决了微细内流道光整加工的难题。其原理在于,首先,由于低黏度的液体相、流体流速以及饱和流量这三者的协同作用,使得光整介质可以流畅地进入微细复杂内流道并且在微细复杂内流道内形成类似于非牛顿流体的状态,流体边界层平行内流道表面,如“刀具般”坚硬的非牛顿流体中的磨粒剪切摩擦实现表面凸点靶向加工。另外,以上三者的协同作用,使得光整介质中磨粒与微细复杂内流道表面产生的摩擦微切削力,因此可以不受微细复杂内流道的材料限制而能够获得表面最优粗糙度与磨粒刃尖平均接触长度范围一致,甚至可以实现表面最优粗糙度ra为0.05μm的超镜面质量,这突破了磨粒流、水射流技术的原理的限制,其原理在于,磨粒流技术切削机制为磨粒挤压表面产生的体积力,因此加工硬度低的金属及高分子柔性材料易出现坑和麻点(ra》0.8μm)。磨料水射流技术中切削力为磨粒冲击表面产生的冲蚀力,加工软质金属易表面粗化(ra》0.8μm)。
41.在长期的实践中,发明人进一步发现,采用以上介绍的通过低黏度的液体相、流体速度以及饱和流量这三者的协同作用的表面光整方法,在一些情况下,对于具有转弯结构的微细内流道工件,存在转弯处过磨抛变粗、变形甚至破损的现象,微细内流道的转弯段与直线段的单边减薄量的尺寸差异在公差范围之外。
42.例如随着光整过程的进行,当微细内流道的内表面虽然达到表面最优粗糙度的目标值,但发生转弯结构过磨抛变粗,甚至弯道壁面被磨穿及光整介质从磨穿的位置喷出。又例检测工件已达到表面最优粗糙度的目标值停止加工后,用线切割的方法剖开工件进行检
查时,发现转弯结构发生过磨抛变粗的现象,弯道结构处的口径明显变宽,导致光整后的工件不符合尺寸要求。
43.发明人经过深入研究发现,发生上述过磨抛变粗、变形甚至破损的现象,微细内流道的转弯段与直线段的单边减薄量尺寸差异在公差范围之外的现象的转弯结构,其具有的结构特点为转弯段的转弯角大于90
°
以及转弯半径小于或等于5mm,而当转弯段的转弯角小于或等于90
°
,或者转弯半径大于5mm时,转弯结构并不会发生上述过磨抛变粗、变形甚至破损,也不会发生微细内流道的转弯段与直线段的尺寸差异在公差范围之外的现象。
44.发生这种情况时,一般采用的解决方案包括,缩短标准加工时间或降低压力继而降低液体相的流速,但这样意味着光整加工的工件的表面最优粗糙度会相应的降低达不到目标值,并且为了满足非牛顿流体的需要,流速也无法降低至5m/s以下。或者采用在转弯结构处增大弯道的口径设置保流区,在转弯大口径内实现流速下降。但在很多工件中,并没有足够的尺寸余量和设计空间增大转弯的口径设置保流区。
45.基于以上,发明人经过深入研究发现,提高两相流的光整介质的液体相的黏度,以及提高预定压力,保证液体相速度不变的情况下,可以避免在转弯结构出现过磨抛的发生,同时满足工件达到表面最优粗糙度的目标值。其原理在于,发明人发现,导致转弯结构发生过磨抛的原因,并非主要是光整介质的高速流动导致对转弯结构的冲刷变形,而是也由于光整介质的磨粒在转弯结构中由于两相流中液体相和固体相密度相差很大,重力和动能对两相流会有很大影响,流体相易改变速度和方向而固体相不易改变速度和方向,离心力作用导致转弯处固液分层,固相磨粒会在离心力的作用下优先集中在内流道转弯处的外侧并对转弯外侧进行过磨抛。因此采用提高黏度使得黏度至少为第一阈值的手段,提高磨粒在水基液体相中的运动阻力,使磨粒在转弯处均散性提高,重力和动能对两相流影响减小,转弯处固液分层变弱,继而转弯处过磨抛程度及对应的过磨抛及变形减弱,从而使得在光整介质的流速为大于5m/s的高速状态下,整体的微细内流道达到表面最优粗糙度的目标值后,其转弯结构也不会出现过磨抛的情况。
46.可以理解到,本技术实施例公开的内流道的表面光整方法,解决了内流道口径较小(小于或等于3mm)、长径比较大(大于或等于50:1)以及具有转弯段以及直线段且转弯段的转弯角大于90
°
以及转弯半径小于或等于5mm的微细内流道光整后出现转弯段出现过磨抛变粗、变形甚至破损、微细内流道的转弯段与直线段的单边减薄量尺寸差异在公差范围之外的问题,从而得到内表面的表面最优粗糙度ra小于或等于1.6 μm的微细内流道工件,工件可具有呈三维空间走向的含s型弯、l型弯、u型弯、o型弯、螺旋弯的微细复杂内流道工件,例如可以是航空/航天/船舶/汽车各类发动机燃油喷嘴、热交换器、液压组件、油路控制节流器。另外,可以理解到,本技术实施例公开的内流道的表面光整方法,并不限于只能用于微细复杂内流道的工件,也可以用于其他尺寸的内流道件的加工。
47.需要解释的是,上下文中的术语“口径”、“长度”意味等效口径以及等效长度,长径比即为等效长度与等效口径的比值。等效口径,内流道截面形状可以为圆形、椭圆形等,截面轮廓由闭合曲线(非折线)构成。内流道截面形状也可以为矩形、三角形等,截面轮廓由闭合折线构成。截面轮廓由任意闭合曲线(非折线)或闭合折线构成,由于截面轮廓为不规则的形状,因此引入等效口径,等效口径定义为对于任意截面形状,取一个和任意截面形状的实际截面积相等的理想圆,此理想圆的直径为等效口径。等效长度指的是内流道中的流体
在内流道两个端口之间实际流动所走过的全路程。
48.根据本技术的一些实施例,参照图1,本技术提供了一种用于具有转弯结构的内流道的表面光整方法,小于或等于3mm以及长径比大于或等于50:1,所述微细内流道具有转弯段以及直线段,转弯段的转弯角大于90
°
以及转弯半径小于或等于5mm,该光整方法包括:采用液体固体两相流光整介质,所述光整介质的液体相黏度《1000cp,固体相为磨粒。
49.对所述光整介质施加预定压力,使得所述光整介质在所述微细内流道内以》5m/s的流速流动,并且所述光整介质在微细内流道的一端流入其内部的流量,达到所述微细内流道的口径所能容纳流量的饱和值,内流道内部的液压力处于憋压状态。
50.此处的转弯结构的定义,如图2所示的,转弯点为沿轴线(直线)初始发生偏转的点,转弯角为相邻两个转弯点之间弧长所对应的圆心角,转弯半径定义为相邻两个转弯点之间弧长所对应的曲率半径。如图2所示的,第一转弯结构11的转弯点为111、112,转弯半径为r1,转弯角a1为锐角,第二转弯结构12的转弯点为121、122,转弯半径为r2,转弯角a2为直角,第三转弯结构13的转弯点为131、132,转弯半径为r3,转弯角a3为钝角。转弯段的转弯角大于90
°
以及转弯半径小于或等于5mm即图2所示的第三转弯结构13,且转弯半径r3小于或等于5mm。
51.此处的液体,其具有黏度《1000cp的性质,本技术中关于黏度的数值的描述,均是指常温下(25摄氏度左右)的乌氏黏度。不同材料、尺寸以及初始平均粗糙度的微细内流道对应的光整方法对应的液体相的黏度的最佳值可以通过在一个下限值的基础上不断增加黏度得到。目前实施例的黏度下限值为50cp左右,发明人经过大量试验数据得到,对于常见的材料例如钛合金、高温合金、钢铁、陶瓷、铝合金、高分子材料等的微细内流道,液体相的黏度至少需要在50cp,光整后才达到粗糙度的目标值。具体得到黏度的最佳值的方法将在后文的实施例中记载,而此处的临界值1000cp也一般并非为最佳值,而是光整介质持续、流畅、稳定地在微细内流道中流动的极限值。
52.实施例中描述的液体相,以水基液体相为例,在去离子水的基础上加入一定增粘剂使得水基液体具备一定的黏度。采用水基液体的有益效果在于,其成本低易于获得,并且较为环保,且在光整结束后光整介质也容易被清洗。但可以理解到,此处的液体相也不限于水基液体,只要是满足黏度μ《1000cp的液体即可。
53.固体相磨粒的材料,可以是常见的磨粒材料,例如碳化物陶瓷:包括碳化硅、碳化钨等;氧化物陶瓷:包括氧化铝、氧化锆、氧化铈等;氮化物陶瓷:包括氮化硼、氮化铬等;天然矿物:包括金刚石/砂、云母、石英、橄榄石等。优选的,可以是金刚石/砂、氧化物陶瓷的一种或者多种组合。
54.在选择磨粒的粒径和质量浓度时,一般在一个下限值的基础上逐步增加得到最佳值的范围。若磨粒的粒径、质量浓度低于下限值,则无法达到预期的光整效果,即微细内流道无法达到表面粗糙度的目标值,其原理在于,若粒径过小导致磨粒自身质量过低,无法产生足够的动能实现有效磨抛,若质量浓度过小,则磨削表面加工点位的概率降低导致无法实现有效磨抛,下限值的选取一般较为保守,例如可以是,在不超过粒径上限值的前提下保守的选择任意一个下限值,内流道口径与磨粒的粒径的比值下限通常为20,即内流道口径要保证至少20个磨粒并行通过时不堵塞,即磨粒的粒径的上限通常为内流道口径的1/20,
而磨粒的下限值一般为上限值的1/5。磨粒的质量浓度的下限值一般为10g/l,下限值的选择,一般是较为保守的,因为系统的压力较大,若发生磨粒堵塞,会导致工件和系统的报废、甚至出现憋裂和爆炸。因此在规定的下限的基础上,逐步增加磨粒的粒径、磨粒的质量浓度直至发生因磨粒粒径过大或者质量浓度过高产生显著的流阻而引发流速流量的下降、以及磨粒颗粒间的相互碰撞影响流速继而降低流速流量和磨削效果,即最佳值可以在下限值的基础上通过试验得到,具体方法将在后文的实施例中记载。
55.对所述光整介质施加预定压力,使得所述光整介质在微细内流道内以》5m/s的流速流动。此处的预定压力,指的是在光整过程的初始状态下使用该压力下使得光整介质在微细内流道的内部就以》5m/s的流速流动,随着光整的进行,内流道表面粗糙度的降低,同样的压力条件下,光整介质在在微细内流道内的流速会越来越快。可以理解到,由于达到的流速是一个范围,此处的预定压力是一个范围的概念,而不是对光整介质只能施加一个特定值。测量光整介质在微细内流道的内部的流动流速,无法采用浸入式测量,否则磨粒会损坏任何传感器探头。可以采用超声测速的方法,也可以利用黏性流体的哈根-泊阿苏依定律:进行间接的测量;在公式中,其中d是内流道口径,l为微细内流道的长度,p为作用在微细内流道两端的压强差,即液压压力p,re为雷诺数 ,um为水基两相流中液体相流速,ρ
l
为液体相的密度,液体相的流速大致等同于光整介质的流速。
56.光整介质的流速大于5m/s,根据理论上形成非牛顿流体的临界条件以及发明人长期实践得到的临界值。工程流体力学资料表明(例如图书资料:杨树人, 汪志明, 何光渝,等. 工程流体力学[m]. 石油工业出版社, 2006.),纯水黏度1cp达到非牛顿流体的临界运动流速》16.6m/s,而本实施例的液体相的黏度的下限值为50cp,大于1cp,因此非牛顿流体的临界流速是小于16.6m/s的。同时结合实践结果,发明人发现小于5m/s时无法得到理想的加工效果,因此临界值为5m/s。
[0057]
所述光整介质在微细内流道的一端流入其内部流量,达到所述微细内流道的口径所能容纳流量的饱和值,内流道内部的液压力处于憋压状态,即本领域所称的饱和流量的状态。
[0058]
此处的容纳流量的饱和值以及饱和流量的状态的含义,为流体流入管道时充满管道截面,管道截面并行容纳流体分子的最大数量。
[0059]
所述光整介质在标准时间段光整所述内流道,使得在所述标准时间段实现内流道的表面最优粗糙度满足目标值,且所述光整介质的液体相的黏度至少为第一阈值,使得微细内流道的所述转弯段与所述直线段的尺寸差异在公差范围之内。
[0060]
光整介质在微细内流道的加工时间,可以是光整介质在标准时间段光整所述微细内流道,至所述微细内流道的表面最优粗糙度为目标值。此处的标准时间段,可以是预定的连续的一段时间,也可以是间断的多段时间,也可以是开始后非预定的连续的一段时间后,检测到光整介质的流速流量达到微细内流道的表面最优粗糙度为目标值对应的流速流量后,光整过程自动停止,例如承上所述的,在一些实施例中,开始加工后,通过测量光整介质在微细内流道内的流动流速或流量,间接地表征得到表面最优粗糙度,当流速或流量值达到规定值,则对应的表面最优粗糙度对应即达到目标值,此时手动或者自动地停止光整加工。此处的表面最优粗糙度为目标值的含义,并非限定需要直接测量表面最优粗糙度,而也
可以间接地表征,例如以上介绍的,可以表征光整介质在微细内流道的内部的流速、流量等等方法。以上目标值指的是设定的表面最优粗糙度值,一般指的就是对微细内流道最终的表面最优粗糙度的要求,但也不排除在以上光整步骤之后继续进一步的光整,此时设定的便不是最终的表面最优粗糙度的要求。
[0061]
发明人发现,对于具有转弯结构的微细内流道而言,例如通过测量光整介质在微细内流道内的流动流速或流量,当流速或流量值达到规定值对应的表面最优粗糙度达到目标值停止加工后,发现存在转弯处过磨抛变粗、变形甚至破损,微细内流道的转弯段与直线段的尺寸差异在公差范围之外的现象。
[0062]
发明人经过深入研究发现,发生上述过磨抛变粗、变形甚至破损的现象,微细内流道的转弯段与直线段的尺寸差异在公差范围之外的现象的转弯结构,其具有的结构特点为转弯段的转弯角大于90
°
以及转弯半径小于或等于5mm,而当转弯段的转弯角小于或等于90
°
,或者转弯半径大于5mm时,转弯结构并不会发生上述过磨抛变粗、变形甚至破损,也不会发生微细内流道的转弯段与直线段的尺寸差异在公差范围之外的现象。即图2所示的转弯结构示意中,第一转弯结构11、第二转弯结构12基本不会发生上述过磨抛变粗、变形甚至破损、尺寸差异在公差范围之外的现象,而仅有第三转弯结构13,且r3为小于5mm出现上述现象。
[0063]
因此,在表面最优粗糙度达到目标值需要停止光整后,若发现转弯结构的过磨抛变粗、变形甚至破损的情况,重新设置相关的参数条件进行光整加工。发明人经过深入研究,发现采用增加光整介质的液体相的黏度的手段,例如原有黏度的基础上,步进地增加增粘剂添加量1g/l~2g/l及对应黏度增量10cp~20cp,并相应增加预定压力,使得原有液体相的速度不变,不断步进地增加黏度直至达微细内流道转弯段与直线段的尺寸在公差范围之内,此时的黏度即为液体相的黏度的第一阈值。
[0064]
可以理解到,以上描述是对于新工艺的试验步骤,在试验之后,对于转弯段的转弯角大于90
°
以及转弯半径小于或等于5mm的转弯结构的微细内流道的表面光整,液体相的黏度直接配置为根据试验步骤得到的黏度的第一阈值。
[0065]
可以理解到,采用以上实施例的光整方法的有益效果在于:通过采用光整介质的液体相的黏度为小于1000cp的液体,两相流的光整介质在微细内流道内的流速》5m/s,以及在微细内流道的一端流入其内部的流量,达到所述微细内流道的口径所能容纳流量的饱和值,内流道内部的液压力处于憋压状态,形成液体相对微细内流道的饱和流量的手段,即通过低黏度的液体相、流体流速以及饱和流量这三者的协同作用,解决了微细内流道光整加工的难题。其原理在于,首先,由于低黏度的液体相、流体流速以及饱和流量这三者的协同作用,使得光整介质为低黏度高流速的状态从而可以流畅地进入微细内流道并且在微细内流道内形成非牛顿流体的状态,流体边界层平行内流道表面,如“刀具般”坚硬的液体相中磨粒剪切摩擦实现表面凸点靶向加工,从原理上克服了柔性加工中表面凸点和凹点被同时加工只能轻微光亮化的问题,同时因为光整介质的磨粒与微细内流道表面摩擦产生的微切削力,因此可以不受微细内流道的材料限制,而能够获得与磨粒刃尖平均接触长度范围一致的表面最优粗糙度,这突破了磨粒流、水射流技术的原理的限制,其原理在于,磨粒流技术切削机制为磨粒挤压表面产生的体积力,因此加工硬度低的金属及高分子柔性材料易出现坑和麻点(ra》0.8μm)。磨料水射流技术中切削力为磨粒
冲击表面产生的冲蚀力,加工软质金属易表面粗化(ra》0.8μm)。另外,低黏度高流速的流体动力学随形加工方式使内流道表面台阶、尖角、几何轮廓曲率等不符合流体工程学的位置被磨抛的更重,拐点、尖边、内流道轮廓曲率及孔型将实现几何学流线型整形,进一步提高内流道的流体运动性能。另外,以上实施例提出了利用光整介质的流速实现类似如刀具般的坚硬的非牛顿流体及磨粒剪切摩擦实现表面凸点靶向加工的临界流速为5m/s。
[0066]
针对转弯段的转弯角大于90
°
以及转弯半径小于或等于5mm易于发生存在转弯处过磨抛变粗、变形甚至破损,微细内流道的转弯段与直线段的尺寸差异在公差范围之外的问题,采用液体相的黏度至少为第一阈值的方案,使得转弯结构的表面最优粗糙度既可以满足目标值的要求,又可以保证具有转弯结构的微细内流道结构中的光整过程达到预定的表面最优粗糙度,同时避免转弯结构过磨抛变粗、甚至变形和破损。其原理在于,发明人发现的,导致转弯结构发生过磨抛的原因,并非主要是光整介质的高速流动导致对转弯结构的冲刷变形,而是也由于光整介质的磨粒在转弯结构中由于两相流中液体相和固体相密度相差很大,重力和动能对两相流会有很大影响,流体相易改变速度和方向而固体相不易改变速度和方向,离心力作用导致转弯处固液分层,固相磨粒会在离心力的作用下优先集中在内流道转弯处的外侧并对转弯外侧进行过磨抛。因此采用提高黏度使得黏度至少为第一阈值的手段,提高磨粒在水基液体相中的运动阻力,使磨粒在转弯处均散性提高,重力和动能对两相流影响减小,转弯处固液分层变弱,继而转弯处过磨抛程度及对应的过磨抛及变形减弱,从而使得在光整介质的流速为大于5m/s的高速状态下,整体的微细内流道达到表面最优粗糙度的目标值后,其转弯结构也不会出现过磨抛的情况。
[0067]
在一些实施例中,参考图3所示的,两相流光整介质的磨粒1的结构可以是具有表面尖角结构2,以起到微切削的作用,磨粒的结构参数可以是,磨粒刃尖平均切削深度l为1.4nm ~14nm,磨粒刃尖平均接触长度b为50nm~1000nm。可以理解到,由于单个磨粒的粒径一般较小,因此实际情况下磨粒一般会发生局部团聚,图3所示的磨粒结构模型,并非物理意义上的单个磨粒的原子或者分子,而是发生局部团聚的等效磨粒群。即上述的磨粒刃尖平均切削深度为等效磨粒群的刃尖平均切削深度,磨粒刃尖平均接触长度为等效磨粒群的刃尖平均接触长度,另外,为了清楚的示意磨粒刃尖平均切削深度l以及磨粒刃尖平均接触长度b,图3并非是等比例绘制的。另外,磨粒刃尖平均切削深度l为1.4nm~14nm,磨粒刃尖平均接触长度b为50nm~ 1000nm并非通过电镜直接观测得到,而是根据发明人长期实践得到的数据经过统计计算得到的。发明人发现,对于采用以上实施例的光整方法,对内流道的口径的单边减薄速率为5μm/h ~50μm/h,对应的每秒单边减薄速率即为1.4nm/s ~14nm/s,即等效磨粒群每秒钟接触微细内流道表面的磨粒刃尖平均切削深度为1.4nm/s ~14nm/s,即对应磨粒刃尖平均切削深度l为1.4nm ~14nm。如此既保证了光整效果,也不至于微切削速度过快而发生过磨抛,满足光整加工的尺寸精度要求,避免超差。发明人还发现,采用以上实施例的光整方法,可以实现的表面最优粗糙度ra为0.05μm ~ 1μm,磨粒刃尖平均接触长度决定了最终的最优粗糙度,故对应磨粒刃尖平均接触长度为50nm ~ 1000nm。通过大量实践得到等效磨粒群的结构参数,可以对计算预定压力等参数起到重要作用。每秒钟接触微细内流道表面的磨粒刃尖平均切削深度在1.4nm ~14nm之间的具体值、磨粒刃尖平均接触长度在50nm~ 1000nm的具体值,可以根据磨粒的具体粒径近似对应得到,若磨粒的粒径大,那么每秒钟接触微细内流道表面的磨粒刃尖平均切削深度和刃尖接触平均长度对应更大,
具体的对应值可以通过长期的实验数据:磨粒粒径对应的单边减薄速率即每秒钟接触微细内流道表面的磨粒刃尖平均切削深度以及磨粒刃尖平均接触长度即光整后的最优粗糙度得到。
[0068]
在一些实施例中,发明人总结得到,转弯段和直线段单边减薄量差异值α
*c
ꢀ‑ꢀ
αc随加工时间t的关系是:其中,α
*c
为转弯段的单边减薄量,αc为直线段的单边减薄量,α
*c
ꢀ‑ꢀ
αc为内流道中转弯段和直线段随加工时间t加工后单边减薄量差异值,r
*
是转弯半径,c为工程常数,称为固液两相流的分离系数,c=1时表示磨粒和水基在转弯时两相完全分离,内流道转弯处外侧近壁面全部是磨粒固体相,其余区域全部为水基液体相。c=0时表示磨粒和水基液体两相完全不分离,即转弯处外侧近壁面和其它区域全部是均一和均匀的水基和磨粒,b为磨粒刃尖平均切削深度,l为磨粒刃尖平均接触长度,σw为工件材料屈服极限,r
*
为转弯结构的转弯半径。当α
*c
ꢀ‑ꢀ
αc为转弯段和直线段加工后减薄量差异公差要求时,对应的加工时间即为标准时间段t0。
[0069]
当液体相的黏度至少为第一阈值时,发明人经过长期实践发现,工程常数c处于0.25 ~ 0.3的范围。一般是在实践过程中对不同微细复杂内流道构型,不同加工时间t下进行剖切检测,发现光整后的转弯结构随时间开始出现变形以及过磨抛变粗,并且测量α
*c
ꢀ‑ꢀ
αc,以此倒推出c,具体的数据表格见下表1:表1转弯结构的过磨抛情况与黏度以及c值的关系根据表1结合磨粒刃尖平均切削深度l为1.4nm~14nm对应的光整过程中的单边减薄速率为5μm/h~50μm/h,及磨粒刃尖平均接触长度b为50nm~1000nm对应的是磨粒磨抛后极限粗糙度可以实现ra为0.05μm~1μm的最优粗糙度。黏度相比原有黏度增加
∆
cp=50~800后可获得c值范围0.25~0.3。通常工程公差标准α
*c
ꢀ‑ꢀ
αc≤0.075mm,通过表1可以看出黏度增加值对应的最大α
*c
ꢀ‑ꢀ
αc=0.075mm,满足工程公差要求,最大α
*c
ꢀ‑ꢀ
αc=0.075mm对应时间为8小时,即标准时间段最大值,基本涵盖微细复杂内流道的光整标准时间段。最大α
*c
ꢀ‑ꢀ
αc=
0.075mm对应的微细复杂内流道转弯结构为转弯半径1~5mm,基本满足微细复杂内流道所有转弯构型。
[0070]
如此可以根据光整介质的成分、磨粒的参数、微细内流道的材料以及结构参数,以及加工参数要求,快速得到标准时间段,在加工过程中,不能超过标准时间段。
[0071]
在另一些实施例中,参考图4所示的,所述光整介质在标准时间段光整所述微细内流道,该标准时间段的具体值,可以是通过前期试验得到的标准时间段,也可以是现场试验得到的标准时间段。得到该标准时间段的步骤如下:所述光整介质在初始时间段光整所述微细内流道,检测微细内流道的表面最优粗糙度;若表面最优粗糙度符合所述目标值则该初始时间段为所述标准时间段;若不符合所述目标值,则逐次增加步进时间段,直至表面最优粗糙度达到目标值,对应的总时间段即为所述标准时间段;其中,所述初始时间段以及步进时间段根据所述磨粒磨削的单边减薄速率以及微细内流道的初始表面平均粗糙度得到。
[0072]
上述的初始时间段,一般是根据微细内流道的初始表面平均粗糙度以及每秒钟接触微细内流道表面的磨粒刃尖平均切削深度计算的。例如零件内流道初始表面平均粗糙度ra=10μm,表面凸点和凹点平均高度差约等于10μm,每秒钟接触微细内流道表面的磨粒刃尖平均切削深度为1.4nm~14nm,即单边减薄速率为5μm/h~50μm/h,按照下限5μm/h进行估算,则标准时间段至少为2h,因此将初始时间段设置为2h。而步进时间段的选择,一般是根据零件尺寸公差要求以及单边减薄速率计算,例如若公差为正负5μm,那么根据单边减薄速率为5μm/h~50μm/h,按照下限5μm/h进行估算,步进时间对应为1h,以避免时间步进过大而导致尺寸超差。
[0073]
可以理解到,以上过程可以是在光整过程中现场试验得到,即若需要确定某种微细内流道对应的初始时间段,则根据以上方法,通过进行初始时间段以及步进时间段的光整得到标准时间段,并且得到该标准时间段的同时,也完成了该种结构的微细内流道加工。在之后光整该种微细内流道时,标准时间段即可直接对应得到加工总时间。无需再进行初始时间段以及步进时间段的试验。
[0074]
若光整介质在标准时间段光整所述微细内流道,表面最优粗糙度符合所述目标值,但微细复杂内流道转弯段与直线段的尺寸超过公差范围,以及转弯结构出现过磨抛变粗、变形甚至破损、转弯段与直线段的单边减薄量的尺寸差异在公差范围之外的现象,则需要调整光整介质黏度达到黏度第一阈值。
[0075]
所述黏度的第一阈值通过以下步骤得到:若达到标准时间段及表面最优粗糙度满足目标值,弯道出现过磨抛变粗,甚至变形和破损,在所述液体相的原有的黏度的基础上,步进地增加增粘剂添加量1g/l~2g/l及对应黏度增量10cp~20cp,并相应增加预定压力,使得原有的液体相速度不变,不断步进地增加黏度直至在到达微细复杂内流道转弯段与直线段的减薄量差异达到公差上限时,此时的黏度即为液体相的黏度的第一阈值。具体而言可以是:首先,在原有光整介质黏度、预定压力p、标准加工时间及对应的标准流速um基础上,在液体相中增加增粘剂添加量1g/l~2g/l及对应黏度增量10cp~20cp,对多个工件进行试验,例如一个工件的黏度增量为20cp,另一个的黏度增量为进一步增加20cp,即为40cp,依次类推,多个工件同时进行试验,也可以是依次进行试验。即增大黏度和预定压力后保证
原有的流速不变,其原因在于,需要保持所述光整介质在微细内流道内以》5m/s的速度流动的条件,保持原有的流速可以保证原有的光整加工的最优粗糙度效果。
[0076]
选用不同黏度的液体相的光整介质进行加工时,将预定压力适应性调整,使得对应不同黏度的预定压力对应的光整介质的速度均为标准流速um。
[0077]
进行试验后,对工件进行逐个剖切,找出微细复杂内流道转弯段与直线段的尺寸差异达到公差上限时对应的黏度,即为液体相的黏度的第一阈值。
[0078]
本质而言,增加黏度可以使得液体相与磨粒更为均一,从而降低公式中的c值,从而降低微细复杂内流道转弯段与直线段的减薄量差异。理论上黏度越高越好。
[0079]
但可以理解到,黏度不能无限增加,因为为了保证标准流速um不变,黏度的增加则需要提高相应的液压力,黏度的增加需要保证压力系统不超过设备安全上限及成本要求可控的情况。另一方面黏度会影响水基液体相在微细复杂内流道中各个区域的流动性和流速,最终微细复杂内流道各个区域磨抛效果差异性不能超过30%。因此黏度受限于上述两方面的制约,对应的光整介质的最高黏度为黏度的第二阈值,即上述的光整介质的液体相黏度《1000cp。即第二阈值一般为1000cp。
[0080]
在一些实施例中,所述光整介质在初始时间段光整所述微细内流道后检测微细内流道的表面最优粗糙度的方法,可以采用通过口径扩大值对应的表面最优粗糙度数值间接检测微细内流道的表面最优粗糙度的方法,满足以下公式:;其中,ra
*
是口径扩大后的表面最优粗糙度,ra0为初始的表面平均粗糙度,δ为端口口径扩大值,一般为0.01mm~0.5mm, k为凹凸磨削比系数,一般为0.2~0.4。
[0081]
此处的凹凸磨削比系数k,表示磨粒在谷的位置相比峰的位置分布概率的比例,可通过谷和峰位置磨削减薄量的比例进行量度。对于机加工的刀具,由于刀具为刚体定位只对凸点指向性加工因此k≈0。对于磨粒流,凸点和谷区都会被磨粒挤压后接触磨削,因此k≈ 0.6~0.8。化学/电化学/磁力/超声波+磨粒等柔性方式对凸点和谷区均为各向同性加工,因此k≈ 0.9~1,即加工较长时间即使表面平均减薄量很大但表面粗糙度无法得到显著改善,只能光亮化并留下橘皮状表面形貌。对于以上实施例介绍的两相流光整方法,由于非牛顿流体具有刚体刀具对表面高速剪切运动,因此对凸点具有更高的指向性磨削,k≈0.2~0.4。一般先计算得到表面最优粗糙度目标值对应的目标口径扩大值,对比该初始时间段测量得到实际口径扩大值,若实际口径扩大值为目标口径扩大值的90%以上,则表明该口径扩大值对应的口径扩大后的表面最优粗糙度ra
*
符合所述目标值,则该初始时间段为所述标准时间段;若不符合所述目标值,则逐次增加步进时间段,直至表面最优粗糙度达到预定值。
[0082]
通过口径扩大值对应的表面最优粗糙度间接检测微细内流道的表面最优粗糙度,其检测过程方便,可直接现场检测。
[0083]
在又一些实施例中,参考图5所示的,整方法还包括,在微细内流道的表面最优粗糙度为目标值之后,对光整后的微细内流道进行清洗,具体可以包括:对所述微细内流道从其端口以所述预定压力注入清洗介质,所述清洗介质与所述光整介质的水基液体相互溶,直至从所述微细内流道流出的清洗介质出现丁达尔效应。
[0084]
清洗介质与水基液体相互溶,例如光整介质为水基两相流,那么清洗介质即对应为去离子水,可以使得光整介质的水基液体相被充分地清理,避免如磨粒流技术导致的在内流道拐弯、死角处残留,在完成加工后很难甚至根本无法被彻底清除的缺陷。而清洗介质的压力与预定压力相同,可以使得清洗介质将光整介质的固体相清除,其原理在于,发明人发现,固体相的残留位置,一般与施加的压力相关,因此施加相同的压力,可以使得清洗介质“找到”残留的固体相以进行清除。
[0085]
判断清洗是否完成的方法,可以无需对工件拆开观察表征,而是通过表征清洗后微细内流道流出的清洗介质出现丁达尔现象即可。例如可以将流出的清洗介质进入透明排水容器并从透明排水容器排出。此过程透明排水容器中的去离子水始终被聚光灯照射,观察清洗去离子水中的光线状态,若清洗后的去离子水中的聚光灯光线呈现混浊,没有直线乳光柱即丁达尔效应产生,则表明此时清洗尚未完成,继续在添加去离子水,直到透明排水容器中的去离子水中聚光灯光线呈现直线乳光柱即出现丁达尔效应为止。可以理解到,以上清洗过程之后,还可以进行依次进入超声波清洗和烘干箱烘干。
[0086]
在一些实施例中,得到固体相的磨粒粒径、磨粒质量浓度的最佳值的步骤可以是:在固体相的磨粒粒径、磨粒质量浓度的下限值的基础上逐渐增加固体相的磨粒粒径、磨粒质量浓度进行光整,直至两相流的光整介质的流速或流量相比于下限值对应的流速或流量降低了1%~5%。
[0087]
例如对于固体相的磨粒粒径而言,在不超过上限值的前提下保守的选择任意一个下限值,按照内流道口径与磨粒的粒径的比值的下限值通常为20,即内流道口径要保证至少20个磨粒并行通过时不堵塞,如此得到对应不同的内流道口径的磨粒粒径的下限值,例如对应内流道口径为3mm,则对应磨粒粒径的上限值为3/20mm,即150μm,在此上限值的基础上,为了保证试验的安全性,一般选取上限值的1/5为下限值,即以30μm的下限值为基础增加磨粒粒径,发明人发现,若磨粒的粒径小于下限值,将导致磨粒自身质量过低,无法产生足够的动能实现高效磨抛。选定磨粒粒径下限后进行试加工,读取光整介质对应的初始的流速或流量数据记为标准值,然后在磨粒粒径下限基础上增加粒径增量1μm~10μm,继续进行待加工的内流道测试加工,重复增加步骤,直到初始流速或流量数据低于流量或流速标准值1~5%,此时磨粒的粒径为最佳值。对应微细内流道的不同口径的磨粒粒径范围可以参见表2。
[0088]
表2:微细内流道的不同口径对应的光整介质的磨粒粒径的最佳值范围又例如对于固体相的磨粒质量浓度而言,按照磨粒的质量浓度为10g/l选定质量浓度下限,发明人发现,若低于此质量浓度下限,则由于磨粒表面磨削点位概率降低导致磨削效果不足,选定质量浓度下限后进行试加工,读取光整介质对应的初始的流速或流量数据记为标准值,然后在质量浓度下限基础上增加磨粒质量浓度2g/l~5g/l,继续进行待加工的内流道测试加工,重复增加步骤,直到初始流速或流量数据低于流量或流速标准值1~5%,此时磨粒的质量浓度为最佳值。对应微细内流道的不同口径的质量浓度范围的最佳值可以
参见表3。如表3所示的,发明人发现,对于口径为0.5mm~1mm的较细的微细内流道,磨粒质量浓度最佳值也相应较低,为10g/l~15g/l,而对口径大于1mm的微细内流道,磨粒质量浓度与口径尺寸相关度较低,为10g/l~35g/l。
[0089]
表3:微细内流道的不同口径对应的光整介质的磨粒质量浓度最佳值范围可以理解到,以上的最佳值,可以是现场通过加工试验得到,即若需要确定某种微细内流道对应的光整介质的磨粒粒径、磨粒质量浓度的最佳值,则根据以上方法,通过测试加工得到。在之后光整该种微细内流道时,即可直接应用该最佳值,无需再进行测试加工。
[0090]
在一些实施例中,预定压力p的数值可以通过以下公式计算得到:其中,ra0为内流道初始表面平均粗糙度,ra为加工后内流道表面最优粗糙度的目标值,l为磨粒刃尖平均切削深度,b为磨粒刃尖平均接触长度,ρ
l
为液体相密度,ρ
p
为磨粒固体相密度、σw为工件材料屈服极限、t为前述的初始时间段,一般可以根据内流道初始表面平均粗糙度以及每秒钟接触微细内流道表面的磨粒刃尖平均切削深度计算得到,χ为内流道达到饱和流量时的增压比,re为液体相的雷诺数,l为内流道的长度,d为内流道的口径,d为磨粒的粒径,k为凹凸磨削比系数。
[0091]
采用以上参数的含义以及具体值一般为,初始表面平均粗糙度ra0由于内流道制造后初始各区域表面粗糙度不完全一致,取内流道各区域粗糙度的平均值,通常ra0数据如下,3d打印6.3μm~ 30μm,精密铸造3.2μm~6.4μm,机加工0.8μm~1.6μm,激光加工和线切割1.6μm~3.2μm、光整后表面最优粗糙度的目标值ra(抛光后各区域粗糙度由于初始差异性也不完全一致,取内流道各区域粗糙度的最优值),通常ra数据如下,3d打印和精密铸造≤1.6μm,机加工≤0.4μm,激光加工和线切割≤0.8μm。微细内流道管长l、管路口径d≤3mm、长径比l/d≥50,雷诺数re为20~200,可以通过液体相的黏度和流速计算得到、凹凸磨削比系数k为0.2~0.4、磨粒粒径d为5μm~150μm、磨粒刃尖平均切削深度l:1.4nm~14nm,磨粒刃尖平均切削深度l可用单位时间减薄量量度,水基两相流光整技术中内流道单边减薄速率为5μm/h~50μm/h。磨粒刃尖平均接触长度b为50nm~1000nm,磨粒刃尖平均接触长度b可用最终极限划痕及对应最优粗糙度量度,水基两相流光整技术中磨粒磨抛后最优粗糙度ra为0.05μm~1μm,因此磨粒刃尖接触长度b为50nm~ 1000nm。液体相密度ρ
l
为1200kg/m3~1500kg/m3,对于水基液体相而言,一般为1500kg/ m3,磨粒固体相密度ρ
p
为2200kg/m3~3300kg/m3,具体的值不同的固体磨粒而不同。工件材料屈服极限σw查表可得,t为初始时间段,即通过初始平均粗糙度以及磨粒刃尖平均切削深度计算,饱和流量下的增压比χ需要大于1,一般在50~400之间,此处的饱和流量的增压比的含义,指的是流体从内流道前端管路输入内流道,内流道前端的管路内腔与内流道的截面积的比,例如对于推动抛光介质的缸体与待加工工件的内
流道截面积而言,缸体为前端,内流道为后端,则缸体与内流道的截面积的比例为50 ~ 400。具体的值根据实际情况而定。
[0092]
采用以上的方法,解决了微细内流道加工参数预先设定的难题,使得光整方法高效以及安全可靠。可以理解到,预定压力p的数值也可以通过尝试的方法得到,只需要满足使得光整介质在微细内流道的内部以》5m/s的流速流动即可,例如根据经验估计一个较小的下限值,之后不断尝试直到满足流速要求,但这种方法效率较低,或者可以根据该公式或者试验数据的基础上计算制作一个数据表格,之后进行光整加工只需要进行查表的动作即可。发明人经过长期试验得到了钛合金/高温合金/钢铁对应的光整方法的工程参数,如下表4所示的。
[0093]
表4:钛合金/高温合金/钢铁对应的光整方法的工程参数而对于陶瓷/铝合金/高分子材料,对应的预定压力比表4中钛合金/高温合金/钢铁材料对应的预定压力p低50%~70%。
[0094]
在一些实施例中,上述介绍的用于提供光整介质的水基液体相具有一定黏度的增粘剂可以包括高分子增粘剂,优选的可以是高分子长链柔性的聚氧化乙烯和聚丙烯酞胺等
的一种或多种组合,发明人发现,采用高分子增粘剂,随着黏度在一定范围的增加,反而使得内流道各个区域基本等流速及均一的磨抛效果。其原理可能在于,高分子的长链提供了湍流减阻效应,降低液体在内流道中沿程阻力,从而实现内流道各个区域基本等流速及均一的磨抛效果,避免端口与内部存在磨抛效果差异。另外发明人还发现,若采用非高分子的增粘剂,虽然可以增加液体相的黏度,但流道端口与内部磨抛效果差异开始增加,流道端口比内部磨抛效果更重。采用高分子增粘剂尤其适用于微细内流道包括三维空间走向的含s型弯、l型弯、u型弯、o型弯、螺旋弯的结构,采用高分子增粘剂的湍流减阻效果,可以保证三维空间走向的含s型弯、l型弯、u型弯、o型弯、螺旋弯的结构的光整过程中,使液体不会因在内流道中随着沿程阻力的增加而显著降低自身流速,保证各个区域最劣粗糙度与最优粗糙度差异在30%以内,实现较好的均一光整效果。
[0095]
承上所述的,通过以上实施例介绍的光整方法可以得到一种具有转弯结构的微细内流道工件,其具有的微细内流道口径小于或等于3mm,以及长径比大等于50:1,且微细内流道具有转弯段以及直线段,所述转弯段的转弯角大于90
°
以及转弯半径小于或等于5mm,通过增材制造、铸造、激光加工、电火花加工等得到所述微细内流道工件,所述微细内流道光整后具有表面最优粗糙度ra小于或等于1.6μm的内表面,且所述微细内流道的所述转弯段与所述直线段的单边减薄量的尺寸差异在0.075mm之内。
[0096]
例如在一些实施例中,通过以上实施例介绍的光整方法得到微细内流道工件为增材制造的发动机燃油喷嘴,其油路为微细内流道,表面粗糙度ra小于或等于1.6μm,另外,由于光整后达到如此低的表面最优粗糙度,表明光整过程中已经将零件内流道表面存在半烧结或粘结的粉末颗粒去除。与未经光整的增材制造的燃油喷嘴相比,可以避免当内流道中通入的燃油与表层高速摩擦造成毛刺、粘附残渣颗粒或粘结粉末脱落时成为多余物而随流体到处扩散,或堵塞油路或引起机械磨损故障,从而造成重大安全事故;也避免了粗糙度大的内表面在长期使用过程中易成为疲劳裂纹源,若是高温油路系统还易导致积碳现象发生;也避免了内流道表面的“台阶”现象导致流体运动过程产生湍流、涡流和流体沿程阻力急剧增加,甚至造成流体失控,产生振动而降低零件使用寿命。也避免了粗糙表面也会使流体中产生大量空化气泡影响燃烧和液力,甚至产生空化腐蚀。
[0097]
为了更加清楚地说明本技术的效果,以下列出一个具体的微细内流道工件采用以上实施例介绍的光整方法的例子。
[0098]
第一实施例本实施例的目标产品为某型航空发动机燃油喷嘴,待进行光整加工的内流道采用激光增材制造技术,微细内流道的口径d=1.3mm~1.4mm,流道总长度为130mm~140mm,长径比为100,包含直线以及转弯结构。材料为高温合金,如图6所示的,具有的转弯段100的转弯半径r*=5mm且转弯角a*为120
°
,转弯段100和直线段200加工后单边减薄量差异公差要求α
*c
ꢀ‑ꢀ
αc≤0.075mm。具体光整方法如下:第一步:光整介质的制备,先依次将防冻剂、消泡剂、除锈剂、分散剂和润滑剂添加到去离子水中;通过乌式黏度计测试,缓慢增加增粘剂将水基黏度调节为50cp,然后对待加工零件内流道进行测试加工,读取流速或流量数据记为标准值,继续增加增粘剂1g/l及对应黏度增量约10cp,继续进行待加工零件内流道测试加工,直到初始流速或流量数据低于标准值1%~5%,此时增粘剂浓度为最佳,相应光整介质黏度最佳,经试验燃油喷嘴最佳增粘
0.096mm及满足最终最优粗糙度ra小于或等于 1.6μm要求,且如图7所示的,转弯结构并未出现过磨抛变粗、变形甚至破损的情况,经检测转弯段和直线段最终单边减薄量差异α
*c
ꢀ‑ꢀ
αc≤0.075mm,满足产品及转弯段和直线段加工后单边减薄量差异公差要求α
*c
ꢀ‑ꢀ
αc≤0.075mm。
[0104]
第七步:抛光介质黏度确定后,在设备中输入标准时间8小时和预定压力p= 71mpa进行正式加工,当加工达到标准加工时间时设备自动停机加工结束。
[0105]
第八步:加工结束后,吸出料缸中的抛光介质并将料缸清洁,重新将0.1μs/cm
ꢀ‑
10μs/cm净洁度的去离子水添加到料缸中。将预定压力设定为p= 71mpa,开启设备进行去离子水加工清洁,经过内流道排出的去离子水直到聚光灯光线照射出现直线乳光柱(丁达尔效应)时,清洗结束。
[0106]
第九步:将零件超声波清洗10分钟,气枪吹干,最后烘干箱烘干,完成最终清洗。
[0107]
本发明虽然以上述实施例公开如上,但其并不是用来限定本发明,任何本领域技术人员在不脱离本发明的精神和范围内,都可以做出可能的变动和修改。因此,凡是未脱离本发明技术方案的内容,依据本发明的技术实质对以上实施例所作的任何修改、等同变化及修饰,均落入本发明权利要求所界定的保护范围之内。