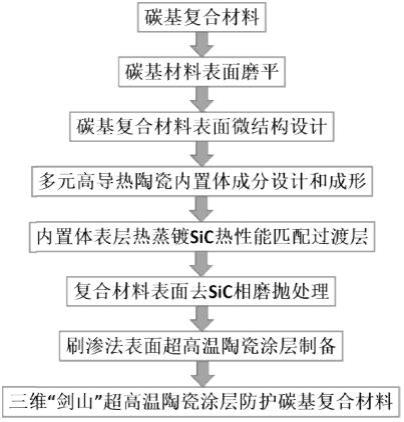
1.本发明涉及一种耐烧蚀三维镶嵌陶瓷涂层及其制备方法;属于陶瓷涂层制备技术领域。
背景技术:2.随着航空航天技术的迅猛发展,高超声速飞行器成为现阶段航空航天领域研究的重点。需经历马赫数5以上飞行速度的高超声速飞行器,由于表面强烈的气动加热和高速粒子冲蚀,导致某些部位表面温度高达2000℃以上。那么对其材料的耐温极限、高温氧化和高速气流冲刷下的强韧化性能要求将更加严苛。同时还要保证其材料质量轻,减少重量带来的飞行速度增加的阻力。而在如此恶劣的氧化对流环境中,极少轻质材料能够保持结构和尺寸的完整性。因此,设计和制备出具有良好的高温抗烧蚀性、抗热震性并能保持良好高温强度的热防护材料,是新型飞行器的关键技术。
3.现有的防热材料主要包括难熔金属、陶瓷材料、c/c复合材料及超高温陶瓷改性c/c复合材料、石墨及其复合材料。每种材料体系都有各自的缺点与不足:难熔金属材料其高温强度与抗热震性存在一定冲突,且其密度较大的缺点严重限制了其使用;陶瓷材料的脆性使其断裂韧性较低,且加工难度大;c/c复合材料在高温下抗氧化性能和抗烧蚀性能较差;单一石墨材料具有和c/c复合材料相同的缺点,即在500℃的高温高氧环境下极易氧化。但由于c/c复合材料具有高强度模量、密度低、热膨胀系数小、耐烧蚀、耐疲劳、化学惰性、尺寸稳定性高、高断裂韧性、高导热率以及低蠕变等一系列优点;在常压下石墨不会出现熔化现象,在高达3700℃的温度下才会出现升华现象,所以石墨的强度随着温度的升高呈现上升趋势,这与大多数材料的强度性质都截然相反,直到温度达到2500℃以上才会出现下降的趋势。其次,石墨材料具有良好的导热性以及抗热震性。石墨的热膨胀系数小,可以承受住温度发生剧烈变化而不损失,且其体积基体保持不变,也不会产生裂纹。同时其导热系数随温度升高而降低,甚至在极高的温度下,石墨成为绝热体。其三,石墨具有超强的耐高温特性。石墨的熔点约为3800~3900℃,沸点为4250℃,在超高温条件下,其质量损失都很小。因此,c/c复合材料和石墨材料是两种非常重要的耐烧蚀热防护材料。为了解决c/c复合材料和石墨材料在500℃以上温度下的抗氧化性能差等问题,国内外研究学者纷纷研究提高c/c复合材料和石墨材料抗氧化性能的超高温陶瓷改性技术。根据c/c复合材料的改性方法的特征可分为两类:一类是基体改性技术;另一种是涂层防护技术。其中,基体改性技术为指通过某种方法向c/c复合材料内部引入抗烧蚀组元,减少基体碳相与外界氧气的接触面积,降低复合材料表面的氧化活性。目前基体改性方法主要有化学气相渗透法(chemical vapor infiltration,cvi)、浆料法(slurry process)、先驱体浸渍-裂解法(precursor infiltration and pyrolysis, pip)、反应熔渗法(reactive melt infiltration,rmi)等。上述方法均存在一些问题,例如制备周期长、孔隙率高、纤维损伤严重等缺陷,均影响了其改性材料的抗氧化烧蚀性能。而涂层防护技术是在c/c复合材料表面制备一定厚度、成分均匀的耐高温抗氧化烧蚀涂层,从而实现阻隔外界氧与c/c复合材料直接接触来达到防氧
化的目的。在c/c复合材料表面制备抗氧化烧蚀涂层的方法主要有浆料刷涂法、包埋法、化学气相沉积法、等离子喷涂法等。与基体改性技术相比,涂层防护是c/c复合材料超高温烧蚀防护最有效的手段。但是涂层防护技术仍然存在一些技术瓶颈,即涂层与基体间的热膨胀系数差异引起热失配,涂层易产生裂纹且与基体结合力差等。涂层在高速气流冲刷作用下难以避免开裂和剥落,最终失去其抗氧化、抗烧蚀能力。目前针对上述问题,国内外研究学者在涂层中引入适量的sic晶须、sic纳米线、hfc纳米线或者组成多层涂层等,能在一定程度上优化涂层与基体间的物理相容性,提高涂层的断裂韧性,从而提高涂层在高速气流冲刷下的抗烧蚀性能。文献“oxidation protection and mechanism of the hfb
2-sic-si/sic coatings modified by in-situ strengthening of sic whiskers for c/c composites, tianying wang,ruiying luo, ceramic international, 44(2018)12370-12380”和“sic nanowire toughened zrb
2-sic ablative coating for sic coated c/c composites, yulei zhang et al. ceramics international, 41(2015)14579-14584.”均报道了采用纳米线或晶须增强超高温陶瓷涂层的抗烧蚀性能并取得了一定的成就。然而对于这种改进成分的涂层,仍然没有摆脱使用超高温不稳定过渡层sic层(2700℃升华)的添加。因此目前的超高温抗烧蚀氧化涂层性能的稳定性,仍需进一步研究和探索。
技术实现要素:4.针对现有技术的不足,本发明目的在于提供一种耐烧蚀三维镶嵌陶瓷涂层及其制备方法。
5.为了实现上述目的,本发明提供如下技术方案:本发明一种耐烧蚀三维镶嵌陶瓷涂层的制备方法,在碳材料中设置内凹结构,然后将梯度高导热陶瓷内嵌体,置于内凹结构内中,获得含梯度高导热陶瓷内嵌体的碳材料,再将含梯度高导热陶瓷内嵌体的碳材料置于含硅粉的模具中,通过热蒸镀于梯度高导热陶瓷内嵌体与碳材料内凹结构的表面形成sic过渡层,最后再于含梯度高导热陶瓷内嵌体的碳材料的表面设置超高温陶瓷涂层,即得耐烧蚀三维镶嵌陶瓷涂层;所述梯度高导热陶瓷内嵌体由上至下,超高温陶瓷含量逐渐降低,高热导率陶瓷逐渐增加,所述超高温陶瓷选自zrc、hfc、vc、zrb2、hfb2、tac中的至少两种,所述高热导率陶瓷选自sic、bn、si3n4中的至少一种。
6.本发明通过在碳材料中设置梯度结构的高导热陶瓷内嵌体,然后依次进行sic过渡层以及超高温陶瓷涂层,形成耐烧蚀三维镶嵌陶瓷涂层,在三者的协同作用下,不仅使涂层与基体结合为一体,而且能大幅提升碳材料的抗烧蚀性能,本发明中,梯度高导热陶瓷内嵌体由超高温陶瓷与高导热陶瓷按梯度复合而成,其中最上层为与超高温陶瓷涂层属于同质材料,通过同质材料梯度递减的方式提高超高温陶瓷涂层与梯度高导热陶瓷内嵌体的界面结合强度,以及涂层与梯度高导热陶瓷内嵌体的力学强度。
7.优选的方案,所述碳材料选自c/c复合材料或石墨,所述c/c复合材料的密度为1.6-1.85g/cm3,石墨的密度为1.5-1.9g/cm3。
8.在本发明技术方案中,所选基体材料为高密度热解碳增密c/c复合材料或高纯、高密度石墨的一种。
9.优选的方案,所述内凹结构为圆形盲孔,所述圆形盲孔的直径为5-10 mm,圆形盲
孔的深度为碳材料厚度的30-50%,任意相邻的圆形盲孔的间距为圆形盲孔孔径的1.5-2倍。
10.进一步的优选,所述圆形盲孔为变径圆形盲孔,其中变径圆形盲孔的上部直径为8-10mm;下部直径为5-7mm,变径圆形盲孔的上部与变径圆形盲孔的下部的高度比为1:2~3。
11.发明人发现,通过设置规则分布的变径圆形盲孔作为内凹结构,盲孔上部分的直径较大,盲孔下部分的直径较小,通过盲孔自身的尺寸的梯度性来促进盲孔内部内嵌体热导率的梯度性;可以进一步提高梯度高导热陶瓷内嵌体的导热效果,此外,通过这种上下尺寸不同的类似螺钉结构的盲孔,能增强梯度高导热陶瓷内嵌体的剪切强度,确保梯度高导热陶瓷内嵌体在服役过程中力学强度,避免其与基体脱落,最终导致涂层开裂。
12.优选的方案,所述内凹结构呈等距点阵分布。
13.优选的方案,所述梯度高导热陶瓷内嵌体的水平尺寸比内凹结构小0.1-0.5mm,厚度尺寸一致。
14.优选的方案,所述梯度高导热陶瓷内嵌体的孔隙率≦10%。在本发明中,梯度高导热陶瓷内嵌体需要保证其力学强度,因此梯度高导热陶瓷内嵌体需较为致密,其孔隙率控制在10%以内。
15.优选的方案,所述梯度高导热陶瓷内嵌体均分为5层,其中最底层均为高热导率陶瓷,次底层中高热导率陶瓷的质量分数为65%~75%,超高温陶瓷的质量分数为25%~35%;中间层中高热导率陶瓷的质量分数为40%~50%,超高温陶瓷的质量分数为50%~60%;次顶层中高热导率陶瓷的质量分数为15%~25%,超高温陶瓷的质量分数为75%~85%;最顶层均为超高温陶瓷。
16.本发明中所提供的梯度高导热陶瓷内嵌体由上至下由含量逐渐降低的超高温陶瓷,以及含量逐渐增加的高热导率陶瓷复合而成,其中,高热导率陶瓷的作用是通过自身较高的热导率将样品表面的热量迅速传输到基体内部,以此来降低表面的烧蚀温度,同时减少样品从烧蚀表面到内部的温度差导致的应力集中,避免表面涂层与基体热梯度导致的热应力开裂,提高表面超高温陶瓷涂层与基体的结合强度和使用寿命。在表面超高温陶瓷的抵抗高温的作用,内嵌体快速导热的作用,以及基体多孔结构保证对内部的隔热效果,这三重作用的相互协同下,促使这种三维内嵌陶瓷涂层能实现长久的耐高温烧蚀、耐高温氧化、并不出现涂层剥落的问题。
17.在本发明中,由于高热导率陶瓷相的热膨胀系数与超高温陶瓷之间存在较大热膨胀系数的差异,因此优选为采用上述梯度组成,若不采用上述梯度组分设计的方式,内嵌体与涂层之间将会因为热膨胀系数不匹配而开裂,整体强度较差;同时此外超高温涂层和内嵌体均与基体c/c复合材料或石墨存在较大的热膨胀系数的差异,本发明通过上述的方式设置梯度高导热陶瓷内嵌体可有效提高涂层与基体材料的界面结合强度,实现涂层与梯度高导热陶瓷内嵌体的浑然一体,最终形成高强度的三维内嵌结构,也能有效提高涂层与基体界面结合强度。
18.进一步的优选,所述梯度高导热陶瓷内嵌体的制备过程为:按设计成份,将高热导率陶瓷、超高温陶瓷铺设在模具中,然后于保护气氛下进行无压烧结或放电等离子烧结即得梯度高导热陶瓷内嵌体,所述无压烧结的温度为1600-2000℃,无压烧结的时间为1-3h,放电等离子烧结的温度为1500-1800℃,放电等离子烧结的时间为0.5-1.5h。
19.更进一步的优选,所述保护气氛为ar气氛。
20.烧结后的高热导率超高温陶瓷内嵌体嵌入预加工的内凹结构,随后将复合材料放入铺有硅粉的石墨罐内,并于高频加热炉中采用热蒸镀法进行梯度高导热陶瓷内嵌体和碳基复合材料基体界面处热匹配sic过渡层的制备。
21.优选的方案,所述模具中,si粉质量为碳材料质量的0.8-1倍,所述热蒸镀的温度为1850-2000℃,热蒸镀的时间为0.5-1h。
22.通过热蒸镀于梯度高导热陶瓷内嵌体与碳材料内凹结构的表面形成sic过渡层,可以提高内嵌体与基体c/c或石墨之间的界面结合强度,且sic陶瓷与c/c复合材料、石墨材料有着类似的热膨胀系数,因此在制备超高温陶瓷涂层之前先通过热蒸镀的方法在梯度高导热陶瓷内嵌体与盲孔壁面进行原位生成sic界面层的方式进行化学连接,从而提升界面结合性能。
23.优选的方案,设置超高温陶瓷涂层前,先使用400目的sic砂纸将含梯度高导热陶瓷内嵌体的碳材料表面的sic过渡层磨掉,然后用酒精超声清洗10-20min,最后在100-200℃下干燥6-8h。
24.在热蒸镀方法制备sic过渡层时,碳材料的表层也无法避免的形成sic陶瓷层,为了后续超高温陶瓷涂层在使用过程中,避免sic层过厚影响陶瓷涂层与内嵌体的结合强度,需要将基体表面形成的sic涂层磨掉,裸露出原有基体材料。
25.优选的方案,设置超高温陶瓷涂层的过程为:按设计比例配取难熔金属粉a,与聚乙烯醇混合获得浆料,将浆料涂刷于含梯度高导热陶瓷内嵌体的碳材料的表面,固化处理,反复涂刷-固化处理2~3次,然后再将含固化层的碳材料与蒸镀母料共同置于石墨模具中,在保护气氛下进行热蒸镀处理,即获得超高温陶瓷涂层,所述难熔金属粉a选自zr粉、hf粉、ta粉、nb粉、v粉中的两种或三种,优选为两种,所述蒸镀母料由难熔金属粉b与si粉混合获得,所述难熔金属粉b与si粉的原子比为1:2~3,所述难熔金属粉b选自zr粉、hf粉、ta粉、nb粉、v粉中的至少两种。
26.本发明中,通过先刷渗法形成不致密的超高温陶瓷涂层底层,再使用热蒸镀-原位反应法制备内部sic连接层,并且填补刷涂法的孔洞缺陷,最终促使刷渗法制备出不致密的超高温陶瓷涂层被热蒸镀气氛所填充并形成超高温陶瓷和sic陶瓷填充物,促使所制备的涂层为非常致密度陶瓷涂层。最终,一种强界面、抗烧蚀和耐冲刷的三维内嵌超高温陶瓷涂层于c/c或石墨基体表层成形。
27.其中,通过刷渗法制备超高温陶瓷涂层时,由于刷渗料与基体为低强度物理结合,再通过加热过程中的基体碳扩散和刷渗料金属扩散的方式于基体表面形成超高温陶瓷涂层,此时刷渗层本身属于多孔结构,因此在热处理后表面依然形成的是属于多孔的超高温陶瓷涂层。但是这些孔洞是本发明所特定设计的,其目的在于形成这些孔洞,为后续热蒸镀法优先形成sic相预留的。后续步骤中,通过si粉和难熔金属粉混合后进行高温热蒸镀工艺,si首先于预留的孔洞内和刷渗涂层底层与基体的间隙处形成sic相,促使超高温陶瓷层与基体的界面层形成的是sic封孔超高温陶瓷层,且这两类物相属于一种三维互穿结构,其次在si蒸汽的辅助作用下,难熔金属也将形成蒸汽,并于sic封孔超高温陶瓷涂层表面形成致密的超高温陶瓷涂层。通过先刷渗后热蒸镀的方法能有效避免单一热蒸镀法只能在表面形成完整sic界面层后形成超高温陶瓷层,界面层大量的sic相的存在不利于界面处抵抗超高温环境,导致sic界面层升华软化,最终导致最外层超高温陶瓷涂层的脱落。然而,通过先
刷渗后热蒸镀法时,超高温陶瓷层与基体间的界面层为sic封孔超高温陶瓷层,该界面层仅出现了一部分sic相,其耐高温性能更加优良,将不存在高温软化的风险,且有sic相的存在也能有效缓解超高温陶瓷涂层与基体因热膨胀系数不匹配而开裂,因此本发明先采用刷渗法后采用热蒸镀法能实现更好的涂层制备效果。
28.进一步的优选,所述难熔金属粉a选自zr粉、hf粉,或所述难熔金属粉a选自ta粉、hf粉,或所述难熔金属粉a选自ta粉、hf粉;当难熔金属粉a选自zr粉、hf粉时,zr粉与hf粉的原子比为0.9~1:1,当难熔金属粉a选自ta粉、hf粉时,ta粉与hf粉的原子比为3.8~4:1,当难熔金属粉a选自ta粉、zr粉时,ta粉与zr粉的原子比为3.8~4:1。
29.当然难熔金属粉a也可以选自除上述优选方案的其他任意两种或三种成份,按等原子比混合,不过发明人发现,由于三元配比的各向异性更大因此优选二元配比,且上述优选方案中的超高温组元配比能碳化或硼化成更高熔点的共晶组织,因此优选上述二元配比下制备超高温陶瓷层。随后使用刷涂法把浆料均匀的涂覆在带有梯度高导热陶瓷内嵌陶瓷体的c/c复合材料表层,然后在250℃烘箱中固化处理,反复2~3遍得到zr、hf、ta、nb、v等二元或多元层。
30.进一步的优选,按设计比例配取难熔金属粉a,与聚乙烯醇于搅拌下混合30-60min获得浆料,所述难熔金属粉a与聚乙烯醇的质量体积比为15-20g:1ml。
31.进一步的优选,所述难熔金属粉b选自zr粉、hf粉,或所述难熔金属粉a选自ta粉、hf粉,或所述难熔金属粉b选自ta粉、hf粉;当难熔金属粉b选自zr粉、hf粉时,zr粉与hf粉的原子比为0.9~1:1,当难熔金属粉b选自ta粉、hf粉时,ta粉与hf粉的原子比为3.8~4:1,当难熔金属粉b选自ta粉、zr粉时,ta粉与zr粉的原子比为3.8~4:1。
32.进一步的优选,所述蒸镀母料置于石墨模具的底部,含固化层的碳材料置于蒸镀母料的上方,使含固化层的碳材料与蒸镀母料的距离为60-150mm。
33.在实际操作过程中,通过工装将含固化层的碳材料架高。
34.进一步的优选,在ar气氛下进行热蒸镀处理,热蒸镀处理的温度为2300-2400℃,热蒸镀处理的时间为2-4h。保温2-4h然后使石墨化炉自然冷却到室温。
35.本发明还提供上述制备方法所制备的耐烧蚀三维镶嵌陶瓷涂层。
36.本发明的原理:本发明技术方案在碳碳复合材料或石墨材料的纵向预先制备出规则分布的内凹结构(内凹结构的尺寸和分布灵活可变),并通过充填不同种类高热导率陶瓷混合粉末、烧结成致密的梯度高导热陶瓷内嵌体,且该内嵌体结构的陶瓷相成分自盲孔上部分到底部呈梯度结构。随后,通过热蒸镀法在内嵌体与盲孔之间的界面处形成促进界面结合强度提升的sic过渡层。最后在带有梯度高导热陶瓷内嵌体的c/c复合材料或石墨材料表面制备一层致密、组分均质的超高温陶瓷涂层。
37.在提高烧蚀性能方面,梯度高导热陶瓷内嵌体结构发挥着两项重要作用,其一是通过自身的高热导率本征特性有效传导复合材料表层的热量,减少材料表层热聚集,降低表面烧蚀温度,以及缓解由于材料内外较大的温度差而导致的热应力开裂;其二为复合材料表层超高温陶瓷涂层提供低热膨胀差异界面点,从而有效解决复合材料表层热防护涂层的热失配问题,提高其抗机械剥蚀性能。超高温陶瓷涂层在提高c/c复合材料或石墨基体的抗烧蚀性能的作用有两点:第一,超高温陶瓷涂层的主要成分为具有超高熔点(3000℃及以
上)的陶瓷相,因此可以通过高熔点陶瓷相来抵抗超高温度烧蚀环境,避免c基材料的升华,保证材料尺寸和结构的稳定性;其二,超高温陶瓷涂层中vc陶瓷能形成高熔点、高沸点氧化物熔体作为愈合基体表层裂纹和孔洞的自愈合剂,而zr系、hf系、ta系等超高温陶瓷则氧化形成高熔点和高沸点的氧化物骨架层。在氧化物熔体和多孔骨架层氧化物的柔性组配下,复合材料表层能形成一层致密、低缺陷、低氧透过率抗氧化保护层有效提高复合材料的高温抗氧化性能。
38.优点和技术效果本发明与现有技术相比,具有以下优点及突破性效果:第一,在传统材料制备工艺的基础上进行结构改造,成本低廉,避免了材料设计、生产制备工艺过程的浪费;第二,较为灵活的变更欲填材料的种类、添加量以及梯度存在的方式,通过内凹增强体的高热导率有效降低基体材料表层的烧蚀温度,从而获得优良的梯度式防隔热一体化效果;第三,超高温陶瓷涂层与内嵌体优异的界面结合性能,有利于提高超高温陶瓷涂层与基体的界面结合强度;第四,超高温陶瓷相分布均匀性高,含量可控性强,从而增强超高温陶瓷涂层防护碳基材料的高温抗热化学烧蚀和机械剥蚀性能,最终提高材料结构的高温服役时间及高温服役性能;第五,采用刷渗涂层成型方法提高超高温陶瓷涂层陶瓷相的均匀性和完整性;第六,充分展现了其近净成形的优点,避免了pip法、化学气相沉积法、等离子喷涂法等手段获取改性基体的材料浪费和制备周期;第七,设备简单,制备周期短,成本低。
附图说明
39.图1为本发明提供的一种耐烧蚀三维镶嵌陶瓷涂层的制备方法的工艺流程图。
40.图2为本发明提供的一种含耐烧蚀三维镶嵌陶瓷涂层的碳材料的三维结构简图。
具体实施方式
41.下面通过实施例具体地对本发明做进一步描述,本发明专利的权利保护范围包括但不局限于此。
42.实施例11)选取密度为1.7g/cm3的三维针刺c/c复合材料板材,采用立式加工中心(jasu v-850)将c/c复合材料板材加工成厚度为10mm,直径为φ300mm的圆块样品;随后在c/c圆块样品表层进行打孔处理,打孔设备采用立式加工中心(jasu v-850),圆形盲孔结构孔径为5mm,孔深为基体材料厚度的50%,即5mm,孔间距为盲孔孔径的8mm,孔分布呈等距点阵分布。
43.2)梯度高导热陶瓷内嵌体的成分为自表面向里的梯度陶瓷相组分设计。选取超高温陶瓷zrc和hfc,以及高热导率陶瓷sic作为陶瓷内嵌体的组成成分;采用放电等离子烧结法进去陶瓷内嵌体的制备。制备后的陶瓷体呈现出随着深度的增加超高温陶瓷相成分逐渐降低,而高热导率陶瓷相含量逐渐增加,最表面超高温陶瓷相高达100%,sic相为0,该特征陶瓷体高度为1mm,随后超高温陶瓷相含量降低为75%,sic相为25%,该特征陶瓷体高度为1mm,随后超高温陶瓷含量继续降低至50%,sic相为50%,该特征陶瓷体高度为1mm,随后超高温陶瓷体含量降低为25%,sic相为75%,该特征陶瓷体高度为1mm,最终超高温陶瓷体为0,sic相为100%,该特征陶瓷体高度为1mm。实现上述陶瓷体特征的方法为采用梯度配比上述质量比例的超高温陶瓷和sic陶瓷的混合粉末,随后通过顺序铺粉的方式进行铺制等离子
烧结陶瓷内嵌体的方法。在实施等离子烧结法时,通过层层烧结的方法实现,内嵌体的梯度变化。采用放电等离子烧结温度为1800℃。烧结气氛为惰性气体(ar)。烧结时间为0.5h。所述内嵌体的尺寸与上述内凹结构相似,其水平尺寸均相差0.1mm,厚度尺寸一样。最终制备梯度高导热陶瓷内嵌体的直径为4.8mm,厚度为5mm,孔隙率为10%。
44.3)将烧结后的梯度高导热陶瓷内嵌体嵌入预加工的内凹结构,随后将复合材料放入铺有硅粉的石墨罐内,并于高频加热炉中采用热蒸镀法进行内嵌体和c/c复合材料基体界面处热匹配sic界面层的制备。其中在热蒸镀法制备sic层时,石墨罐内所铺si粉质量为坯体材料质量的0.8倍,热蒸镀温度为1850℃,热蒸镀时间为0.5h。
45.4)将嵌入了梯度高导热陶瓷内嵌体的c/c复合材料表层制备一层超高温陶瓷涂层,该低缺陷、高质密以及高均匀性超高温陶瓷涂层制备方法选用刷渗法工艺。在进行刷涂之前使用400目的sic砂纸手工打磨试样表面,然后用酒精超声清洗20min,最后在100℃下干燥8h。使用浆料刷涂法在样品表面进行zr、hf混合金属粉末层的制备,再使用热蒸镀-原位反应法制备内部sic连接层,并且填补刷涂法的孔洞缺陷。其中刷涂浆料配比为zr:hf原子比为1:1的混合粉末作为超高温组元,将其混合金属粉末与聚乙烯醇粘结剂混合制成浆料,粉料与聚乙烯醇的比例为15g/ml,搅拌时间为30min制得。随后使用刷涂法把浆料均匀的涂覆在带有梯度高导热陶瓷内嵌体的c/c复合材料表层,然后在250℃烘箱中固化处理,反复三遍得到zr、hf二元层。
46.5)使用原子比(zr+hf)/si为1:2比例的粉料作为蒸镀母料,且zr:hf比为1:1,粉料与基体置于石墨坩埚中,基体与粉料之间保持适宜高度(60mm)。将石墨坩埚放入高频石墨化炉中,ar气环境下加热到2400℃,保温3h,然后使石墨化炉自然冷却到室温,得到(zr/hf)c-sic涂层。此外梯度高导热陶瓷内嵌体与c/c复合材料基体表层也形成一层致密的超高温陶瓷和sic的界面层。最终,一种强界面、抗烧蚀和耐冲刷的“剑山”超高温陶瓷涂层于c/c基体表层成形。涂层厚度为400μm,涂层的最外层中超高温组元相比内层的含量高。该方法制备的涂层致密度和均匀性较好,涂层与基体结合紧密.通过以上制备工艺制得的带有一种耐烧蚀三维互穿陶瓷涂层c/c复合材料进行涂层结合强度测试时,采用万能测试仪,对复合材料进行抗拉强度测试,结果表明,涂层与基体结合强度较高,抗拉强度约为100mpa,内嵌体与涂层结合紧密,涂层脱落过程中,出现内嵌体的拔出效果,这证明了在复合材料内层植入了陶瓷内嵌体后,实现了涂层的三维互穿结构设计,提高了涂层与基体的结合表面积,增加了涂层与基体的结合强度;此外,陶瓷内嵌体的拔出作用也提高了涂层与基体的结合强度。
47.通过以上制备工艺制得的带有一种耐烧蚀三维互穿陶瓷涂层c/c复合材料在3000℃下进行60s每次,循环烧蚀3次的氧乙炔焰烧蚀检测,结果表明该复合材料表面无烧蚀坑,涂层保存完好,未出现涂层开裂和剥蚀的现像,内嵌体的热导效果较好,表面温度明显下降了300℃。
48.实施例21)选取密度为1.7g/cm3的三维针刺c/c复合材料板材,采用立式加工中心(jasu v-850)将c/c复合材料板材加工成厚度为10mm,直径为φ300mm的圆块样品;随后在c/c圆块样品表层进行打孔处理,打孔设备采用立式加工中心(jasu v-850),圆形盲孔结构孔径为5mm,孔深为基体材料厚度的50%,即5mm,孔间距为盲孔孔径的8mm,孔分布呈等距点阵分布。
49.2)梯度高导热陶瓷内嵌体的成分为自表面向里的梯度陶瓷相组分设计。选取超高温陶瓷hfc和tac,以及高温陶瓷sic作为陶瓷内嵌体的组成成分;采用放电等离子烧结法进去陶瓷内嵌体的制备。制备后的陶瓷体呈现出随着深度的增加超高温陶瓷相成分逐渐降低,而高热导率陶瓷相含量逐渐增加,最表面超高温陶瓷相高达100%,sic相为0,该特征陶瓷体高度为1mm,随后超高温陶瓷相含量降低为75%,sic相为25%,该特征陶瓷体高度为1mm,随后超高温陶瓷含量继续降低至50%,sic相为50%,该特征陶瓷体高度为1mm,随后超高温陶瓷体含量降低为25%,sic相为75%,该特征陶瓷体高度为1mm,最终超高温陶瓷体为0,sic相为100%,该特征陶瓷体高度为1mm。实现上述陶瓷体特征的方法为采用梯度配比上述质量比例的超高温陶瓷和sic陶瓷的混合粉末,随后通过顺序铺粉的方式进行铺制等离子烧结陶瓷内嵌体的方法。在实施等离子烧结法时,通过层层烧结的方法实现,内嵌体的梯度变化。采用放电等离子烧结温度为1800℃。烧结气氛为惰性气体(ar)。烧结时间为0.5h。所述内嵌体的尺寸与上述内凹结构相似,其水平尺寸均相差0.1mm,厚度尺寸一样。最终制备梯度高导热陶瓷内嵌体的直径为4.8mm,厚度为5mm,孔隙率为7%。
50.3)将烧结后的梯度高导热陶瓷内嵌体嵌入预加工的内凹结构,随后将复合材料放入铺有硅粉的石墨罐内,并于高频加热炉中采用热蒸镀法进行内嵌体和c/c复合材料基体界面处热匹配sic界面层的制备。其中在热蒸镀法制备sic层时,石墨罐内所铺si粉质量为坯体材料质量的0.8倍,热蒸镀温度为1850℃,热蒸镀时间为0.5h。
51.4)将嵌入了梯度高导热陶瓷内嵌体的c/c复合材料表层制备一层超高温陶瓷涂层,该低缺陷、高质密以及高均匀性超高温陶瓷涂层制备方法选用刷渗法工艺。在进行刷涂之前使用400目的sic砂纸手工打磨试样表面,然后用酒精超声清洗20min,最后在100℃下干燥8h。使用浆料刷涂法在样品表面进行ta、hf混合金属粉末层的制备,再使用热蒸镀-原位反应法制备内部sic连接层,并且填补刷涂法的孔洞缺陷。其中刷涂浆料配比为ta、hf原子比为4:1的混合粉末作为超高温组元,将其混合金属粉末与聚乙烯醇粘结剂混合制成浆料,粉料与聚乙烯醇的比例为15g/ml,搅拌时间为30min制得。随后使用刷涂法把浆料均匀的涂覆在带有梯度高导热陶瓷内嵌体的c/c复合材料表层,然后在250℃烘箱中固化处理,反复三遍得到zr、hf二元层。
52.5)使用原子比(ta+hf)/si为1:2比例的粉料作为蒸镀母料,其中ta:hf为4:1,粉料与基体置于石墨坩埚中,基体与粉料之间保持适宜高度(60mm)。将石墨坩埚放入高频石墨化炉中,ar气环境下加热到2400℃,保温3h,然后使石墨化炉自然冷却到室温,得到(ta/hf)c-sic涂层。此外梯度高导热陶瓷内嵌体与c/c复合材料基体表层也形成一层致密的超高温陶瓷和sic的界面层。最终,一种强界面、抗烧蚀和耐冲刷的三维内嵌陶瓷涂层于c/c基体表层成形。涂层厚度为400μm,涂层的最外层中超高温组元相比内层的含量高。通过该方法制备的涂层致密度和均匀性较好,涂层与基体结合紧密。
53.通过以上制备工艺制得的带有一种耐烧蚀三维镶嵌陶瓷涂层c/c复合材料进行涂层结合强度测试时,采用万能测试仪,对复合材料进行抗拉强度测试,结果表明,涂层与基体结合强度较高,抗拉强度约为60mpa,内嵌体与涂层结合紧密,涂层脱落过程中,出现内嵌体的拔出效果,这证明了在复合材料内层植入了陶瓷内嵌体后,实现了涂层的三维互穿结构设计,提高了涂层与基体的结合表面积,增加了涂层与基体的结合强度;此外,陶瓷内嵌体的拔出作用也提高了涂层与基体的结合强度,但由于tac相与基体材料性能差异,其界面
结合强度相比实施例1的提升效果差。
54.通过以上制备工艺制得的带有一种耐烧蚀三维镶嵌陶瓷涂层c/c复合材料在3000℃下进行180s氧乙炔焰烧蚀检测,结果表明该复合材料表面无烧蚀坑,涂层氧化后的氧化物熔体在内凹结构的限制作用下,有效的减缓了高温氧化物熔体的剥蚀消耗,涂层表面的抗烧蚀氧化层致密度和与基体的结合强度较高,其耐高温极限相比实施例1的高,这主要是因为tac与hfc能形成其熔点大于两者的固溶体,最终促使超高温陶瓷涂层具有更优异的耐温性能。
55.实施例 31)选取密度为1.7g/cm3的三维针刺c/c复合材料板材,采用立式加工中心(jasu v-850)将c/c复合材料板材加工成厚度为10mm,直径为φ300mm的圆块样品;随后在c/c圆块样品表层进行打孔处理,打孔设备采用立式加工中心(jasu v-850),圆形盲孔结构为变径盲孔:其中变径盲孔上部分(50%)直径为10mm,下部分(50%)盲孔直径为7mm,孔深为基体材料厚度的50%,即5mm,孔间距为盲孔孔径的8mm,孔分布呈等距点阵分布。
56.2)梯度高导热陶瓷内嵌体的成分为自表面向里的梯度陶瓷相组分设计。选取超高温陶瓷zrc和hfc,以及高温陶瓷sic作为陶瓷内嵌体的组成成分;采用放电等离子烧结法进去陶瓷内嵌体的制备。制备后的陶瓷体呈现出随着深度的增加超高温陶瓷相成分逐渐降低,而高热导率陶瓷相含量逐渐增加,最表面超高温陶瓷相高达100%,sic相为0,该特征陶瓷体高度为1mm,随后超高温陶瓷相含量降低为75%,sic相为25%,该特征陶瓷体高度为1mm,随后超高温陶瓷含量继续降低至50%,sic相为50%,该特征陶瓷体高度为1mm,随后超高温陶瓷体含量降低为25%,sic相为75%,该特征陶瓷体高度为1mm,最终超高温陶瓷体为0,sic相为100%,该特征陶瓷体高度为1mm。实现上述陶瓷体特征的方法为采用梯度配比上述质量比例的超高温陶瓷和sic陶瓷的混合粉末,随后通过顺序铺粉的方式进行铺制等离子烧结陶瓷内嵌体的方法。在实施等离子烧结法时,通过层层烧结的方法实现,内嵌体的梯度变化。采用放电等离子烧结温度为1800℃。烧结气氛为惰性气体(ar)。烧结时间为0.5h。所述内嵌体的尺寸与上述内凹结构相似,其水平尺寸均相差0.1mm,厚度尺寸一样。最终制备梯度高导热陶瓷内嵌体的直径为4.8mm,厚度为5mm,孔隙率为10%。
57.3)将烧结后的梯度高导热陶瓷内嵌体嵌入预加工的内凹结构,随后将复合材料放入铺有硅粉的石墨罐内,并于高频加热炉中采用热蒸镀法进行内嵌体和c/c复合材料基体界面处热匹配sic界面层的制备。其中在热蒸镀法制备sic层时,石墨罐内所铺si粉质量为坯体材料质量的0.8倍,热蒸镀温度为1850℃,热蒸镀时间为0.5h。
58.4)将嵌入了梯度高导热陶瓷内嵌体的c/c复合材料表层制备一层超高温陶瓷涂层,该低缺陷、高质密以及高均匀性超高温陶瓷涂层制备方法选用刷渗法工艺。在进行刷涂之前使用400目的sic砂纸手工打磨试样表面,然后用酒精超声清洗20min,最后在100℃下干燥8h。使用浆料刷涂法在样品表面进行zr、hf混合金属粉末层的制备,再使用热蒸镀-原位反应法制备内部sic连接层,并且填补刷涂法的孔洞缺陷。其中刷涂浆料配比为zr:hf原子比为1:1的混合粉末作为超高温组元,将其混合金属粉末与聚乙烯醇粘结剂混合制成浆料,粉料与聚乙烯醇的比例为15g/ml,搅拌时间为30min制得。随后使用刷涂法把浆料均匀的涂覆在带有梯度高导热陶瓷内嵌体的c/c复合材料表层,然后在250℃烘箱中固化处理,反复三遍得到zr、hf二元层。
59.5)使用原子比(zr+hf)/si为1:2比例的粉料作为蒸镀母料,其中zr:hf为1:1粉料与基体置于石墨坩埚中,基体与粉料之间保持适宜高度(60mm)。将石墨坩埚放入高频石墨化炉中,ar气环境下加热到2400℃,保温3h,然后使石墨化炉自然冷却到室温,得到(zr/hf)c-sic涂层。此外梯度高导热陶瓷内嵌体与c/c复合材料基体表层也形成一层致密的超高温陶瓷和sic的界面层。最终,一种强界面、抗烧蚀和耐冲刷的“剑山”超高温陶瓷涂层于c/c基体表层成形。涂层厚度为400μm,涂层的最外层中超高温组元相比内层的含量高。该方法制备的涂层致密度和均匀性较好,涂层与基体结合紧密.通过以上制备工艺制得的带有一种耐烧蚀三维镶嵌陶瓷涂层c/c复合材料进行涂层结合强度测试时,采用万能测试仪,对复合材料进行抗拉强度测试,结果表明,涂层与基体结合强度较高,抗拉强度约为130mpa,内嵌体与涂层结合紧密,涂层脱落过程中,出现内嵌体的拔出效果,相比实施例1,该变径盲孔相比单一尺寸盲孔的涂层与基体的界面强度提高效果更佳。这证明了在复合材料内层植入了变径陶瓷内嵌体后,实现了涂层的三维镶嵌结构设计,且变径盲孔的台阶也能提高内嵌体的卡扣作用,更加提高了涂层与基体的结合表面积,增加了涂层与基体的结合强度;此外,陶瓷内嵌体的拔出作用也提高了涂层与基体的结合强度。
60.通过以上制备工艺制得的带有一种耐烧蚀三维互穿陶瓷涂层c/c复合材料在3000℃下进行60s每次,循环烧蚀3次的氧乙炔焰烧蚀检测,结果表明该复合材料表面无烧蚀坑,涂层保存完好,未出现涂层开裂和剥蚀的现像,且内嵌体的热导效果更加,表面温度明显下降了500℃。
61.对比例1选取密度为1.7g/cm3的三维针刺c/c复合材料板材,采用立式加工中心(jasu v-850)将c/c复合材料板材加工成厚度为10mm,直径为φ300mm的圆块样品。
62.采用刷渗工艺在c/c复合材料表层制备一层超高温陶瓷涂层。在进行刷涂之前使用400目的sic砂纸手工打磨试样表面,然后用酒精超声清洗20min,最后在100℃下干燥8h。使用浆料刷涂法在样品表面进行zr、hf混合金属粉末层的制备,再使用热蒸镀-原位反应法制备内部sic连接层,并且填补刷涂法的孔洞缺陷。其中刷涂浆料配比为:zr:hf原子比为1:1的混合粉末作为超高温组元,将其混合金属粉末与聚乙烯醇粘结剂混合制成浆料,粉料与聚乙烯醇的比例为15g/ml,搅拌时间为30min制得。随后使用刷涂法把浆料均匀的涂覆在带有高热导率内嵌陶瓷体的c/c复合材料表层,然后在250℃烘箱中固化处理,反复三遍得到zr、hf二元层。
63.使用原子比(zr+hf)/si为1:2比例的粉料作为蒸镀母料,且zr:hf为1:1,粉料与基体置于石墨坩埚中,基体与粉料之间保持适宜高度(60mm)。将石墨坩埚放入高频石墨化炉中,ar气环境下加热到2400℃,保温3h,然后使石墨化炉自然冷却到室温,得到(zr/hf)c-sic涂层。
64.采用万能测试仪,对复合材料与涂层进行抗拉强度测试,涂层与基体结合强度较低,抗拉强度约为20mpa,涂层迅速从基体表面脱落。这证明了单一的涂层与基体的界面结合强度较差。
65.将上述方法制备的复合材料进行60s每次,循环3次的氧乙炔焰烧蚀测试时,涂层发生开裂,部分涂层从基体表层剥落。这充分说明了单一的超高温涂层不具备优良的耐高
温、抗热震性能,涂层对基体的抗烧蚀和抗氧化性能无法保证。
66.对比例21)选取密度为1.7g/cm3的三维针刺c/c复合材料板材,采用立式加工中心(jasu v-850)将c/c复合材料板材加工成厚度为10mm,直径为φ300mm的圆块样品;随后在c/c圆块样品表层进行打孔处理,打孔设备采用立式加工中心(jasu v-850),圆形盲孔结构为变径盲孔:其中变径盲孔上部分(50%)直径为10mm,下部分(50%)盲孔直径为7mm,孔深为基体材料厚度的50%,即5mm,孔间距为盲孔孔径的8mm,孔分布呈等距点阵分布。
67.2)梯度高导热陶瓷内嵌体的成分为自表面向里的梯度陶瓷相组分设计。选取超高温陶瓷zrc和hfc,以及高温陶瓷sic作为陶瓷内嵌体的组成成分;采用放电等离子烧结法进去陶瓷内嵌体的制备。制备后的陶瓷体呈现出随着深度的增加超高温陶瓷相成分逐渐降低,而高热导率陶瓷相含量逐渐增加,最表面超高温陶瓷相高达100%,sic相为0,该特征陶瓷体高度为1mm,随后超高温陶瓷相含量降低为75%,sic相为25%,该特征陶瓷体高度为1mm,随后超高温陶瓷含量继续降低至50%,sic相为50%,该特征陶瓷体高度为1mm,随后超高温陶瓷体含量降低为25%,sic相为75%,该特征陶瓷体高度为1mm,最终超高温陶瓷体为0,sic相为100%,该特征陶瓷体高度为1mm。实现上述陶瓷体特征的方法为采用梯度配比上述质量比例的超高温陶瓷和sic陶瓷的混合粉末,随后通过顺序铺粉的方式进行铺制等离子烧结陶瓷内嵌体的方法。在实施等离子烧结法时,通过层层烧结的方法实现,内嵌体的梯度变化。采用放电等离子烧结温度为1800℃。烧结气氛为惰性气体(ar)。烧结时间为0.5h。所述内嵌体的尺寸与上述内凹结构相似,其水平尺寸均相差0.1mm,厚度尺寸一样。最终制备梯度高导热陶瓷内嵌体的直径为4.8mm,厚度为5mm,孔隙率为10%。
68.3)将烧结后的梯度高导热陶瓷内嵌体嵌入预加工的内凹结构,随后将复合材料放入铺有硅粉的石墨罐内,并于高频加热炉中采用热蒸镀法进行内嵌体和c/c复合材料基体界面处热匹配sic界面层的制备。其中在热蒸镀法制备sic层时,石墨罐内所铺si粉质量为坯体材料质量的0.8倍,热蒸镀温度为1850℃,热蒸镀时间为0.5h。
69.4)将嵌入了梯度高导热陶瓷内嵌体的c/c复合材料表层制备一层超高温陶瓷涂层,在之前使用400目的sic砂纸手工打磨试样表面,然后用酒精超声清洗20min,最后在100℃下干燥8h。
70.5)使用原子比(zr+hf)/si为1:2比例的粉料作为蒸镀母料,且zr:hf为1:1,粉料与基体置于石墨坩埚中,基体与粉料之间保持适宜高度(60mm)。将石墨坩埚放入高频石墨化炉中,ar气环境下加热到2400℃,保温3h,然后使石墨化炉自然冷却到室温,得到(zr/hf)c-sic涂层。此外高热导率内嵌陶瓷体与c/c复合材料基体表层也形成一层致密的超高温陶瓷和sic的界面层。最终,表面形成的是一种底层为sic界面层和最外层为超高温陶瓷涂层相结合的涂层,涂层厚度为300μm,涂层的最外层中超高温组元相比内层的含量高。
71.通过以上制备工艺制得的带有一种耐烧蚀三维镶嵌陶瓷涂层c/c复合材料进行涂层结合强度测试时,采用万能测试仪,对复合材料进行抗拉强度测试,结果表明,涂层与基体结合强度较高,抗拉强度约为100mpa,内嵌体与涂层结合紧密,涂层脱落过程中,出现内嵌体的拔出效果,相比实施例3,该涂层与基体的界面结合强度有所降低。这证明了在没有进行先刷渗法后热蒸镀法的工艺时,超高温涂层基体之间的界面层不能形成一层si相和超高温陶瓷三维互穿结构的界面层,以此来提高超高温陶瓷涂层与基体的界面结合强度。
72.通过以上制备工艺制得的带有一种耐烧蚀三维镶嵌陶瓷涂层c/c复合材料在3000℃下进行60s每次,循环烧蚀3次的氧乙炔焰烧蚀检测,结果表明该复合材料表面有少量的烧蚀坑,由于sic界面层在超高温环境下被升华和软化,导致最外层超高温陶瓷涂层在使用过程中开裂,涂层开始脱落。
73.对比例31)选取密度为1.7g/cm3的三维针刺c/c复合材料板材,采用立式加工中心(jasu v-850)将c/c复合材料板材加工成厚度为10mm,直径为φ300mm的圆块样品;随后在c/c圆块样品表层进行打孔处理,打孔设备采用立式加工中心(jasu v-850),圆形盲孔结构为变径盲孔:其中变径盲孔上部分(50%)直径为10mm,下部分(50%)盲孔直径为7mm,孔深为基体材料厚度的50%,即5mm,孔间距为盲孔孔径的8mm,孔分布呈等距点阵分布。
74.2)梯度高导热陶瓷内嵌体的成分为自表面向里的梯度陶瓷相组分设计。选取超高温陶瓷zrc和hfc,以及高温陶瓷sic作为陶瓷内嵌体的组成成分;采用放电等离子烧结法进去陶瓷内嵌体的制备。制备后的陶瓷体呈现出随着深度的增加超高温陶瓷相成分逐渐降低,而高热导率陶瓷相含量逐渐增加,最表面超高温陶瓷相高达100%,sic相为0,该特征陶瓷体高度为1mm,随后超高温陶瓷相含量降低为75%,sic相为25%,该特征陶瓷体高度为1mm,随后超高温陶瓷含量继续降低至50%,sic相为50%,该特征陶瓷体高度为1mm,随后超高温陶瓷体含量降低为25%,sic相为75%,该特征陶瓷体高度为1mm,最终超高温陶瓷体为0,sic相为100%,该特征陶瓷体高度为1mm。实现上述陶瓷体特征的方法为采用梯度配比上述质量比例的超高温陶瓷和sic陶瓷的混合粉末,随后通过顺序铺粉的方式进行铺制等离子烧结陶瓷内嵌体的方法。在实施等离子烧结法时,通过层层烧结的方法实现,内嵌体的梯度变化。采用放电等离子烧结温度为1800℃。烧结气氛为惰性气体(ar)。烧结时间为0.5h。所述内嵌体的尺寸与上述内凹结构相似,其水平尺寸均相差0.1mm,厚度尺寸一样。最终制备梯度高导热陶瓷内嵌体的直径为4.8mm,厚度为5mm,孔隙率为10%。
75.3)将上述方法制备的复合材料进行60s每次,循环3次的氧乙炔焰烧蚀测试时,内嵌体出现脱落,样品表面依然出现烧蚀坑。这充分说明了单一的内嵌体不能有效提高样品的抗烧蚀性能,其表面降温效果也无法满足抗烧蚀性能提升的作用。
76.对比例41)选取密度为1.7g/cm3的三维针刺c/c复合材料板材,采用立式加工中心(jasu v-850)将c/c复合材料板材加工成厚度为10mm,直径为φ300mm的圆块样品;随后在c/c圆块样品表层进行打孔处理,打孔设备采用立式加工中心(jasu v-850),圆形盲孔结构为变径盲孔:其中变径盲孔上部分(50%)直径为10mm,下部分(50%)盲孔直径为7mm,孔深为基体材料厚度的50%,即5mm,孔间距为盲孔孔径的8mm,孔分布呈等距点阵分布。
77.2)梯度高导热陶瓷内嵌体的成分为自表面向里的梯度陶瓷相组分设计。选取超高温陶瓷zrc和hfc,以及高温陶瓷sic作为陶瓷内嵌体的组成成分;采用放电等离子烧结法进去陶瓷内嵌体的制备。制备后的陶瓷体呈现出随着深度的增加超高温陶瓷相成分逐渐降低,而高热导率陶瓷相含量逐渐增加,最表面超高温陶瓷相高达100%,sic相为0,该特征陶瓷体高度为1mm,随后超高温陶瓷相含量降低为75%,sic相为25%,该特征陶瓷体高度为1mm,随后超高温陶瓷含量继续降低至50%,sic相为50%,该特征陶瓷体高度为1mm,随后超高温陶瓷体含量降低为25%,sic相为75%,该特征陶瓷体高度为1mm,最终超高温陶瓷体为0,sic相
为100%,该特征陶瓷体高度为1mm。实现上述陶瓷体特征的方法为采用梯度配比上述质量比例的超高温陶瓷和sic陶瓷的混合粉末,随后通过顺序铺粉的方式进行铺制等离子烧结陶瓷内嵌体的方法。在实施等离子烧结法时,通过层层烧结的方法实现,内嵌体的梯度变化。采用放电等离子烧结温度为1800℃。烧结气氛为惰性气体(ar)。烧结时间为0.5h。所述内嵌体的尺寸与上述内凹结构相似,其水平尺寸均相差0.1mm,厚度尺寸一样。最终制备梯度高导热陶瓷内嵌体的直径为4.8mm,厚度为5mm,孔隙率为10%。
78.3)将烧结后的梯度高导热陶瓷内嵌体嵌入预加工的内凹结构,随后将复合材料放入铺有硅粉的石墨罐内,并于高频加热炉中采用热蒸镀法进行内嵌体和c/c复合材料基体界面处热匹配sic界面层的制备。其中在热蒸镀法制备sic层时,石墨罐内所铺si粉质量为坯体材料质量的0.8倍,热蒸镀温度为1850℃,热蒸镀时间为0.5h。
79.4)将嵌入了梯度高导热陶瓷内嵌体的c/c复合材料表层制备一层超高温陶瓷涂层,该低缺陷、高质密以及高均匀性超高温陶瓷涂层制备方法选用刷渗法工艺。刷渗前,样品表面不进行sic层的打磨处理,直接使用浆料刷涂法在样品表面进行zr、hf混合金属粉末层的制备,再使用热蒸镀-原位反应法制备内部sic连接层,并且填补刷涂法的孔洞缺陷。
80.其中刷涂浆料配比为:zr:hf原子比为1:1的混合粉末作为超高温组元,将其混合金属粉末与聚乙烯醇粘结剂混合制成浆料,粉料与聚乙烯醇的比例为15g/ml,搅拌时间为30min制得。随后使用刷涂法把浆料均匀的涂覆在带有高热导率内嵌陶瓷体的c/c复合材料表层,然后在250℃烘箱中固化处理,反复三遍得到zr、hf二元层。
81.5)使用原子比(zr+hf)/si为1:2比例的粉料作为蒸镀母料,其中zr:hf为1:1粉料与基体置于石墨坩埚中,基体与粉料之间保持适宜高度(60mm)。将石墨坩埚放入高频石墨化炉中,ar气环境下加热到2400℃,保温3h,然后使石墨化炉自然冷却到室温,得到(zr/hf)c-sic涂层。此外高热导率内嵌陶瓷体与c/c复合材料基体表层也形成一层致密的超高温陶瓷和sic的界面层。
82.由于在进行刷渗涂层之前,未将样品表面多余的sic层打磨掉,最终,在c/c基体表层形成了一种sic界面层较厚的超高温陶瓷涂层和sic涂层。涂层厚度为430μm,涂层的最外层中超高温组元相比内层的含量高。
83.通过以上制备工艺制得的带有一种耐烧蚀三维镶嵌陶瓷涂层c/c复合材料进行涂层结合强度测试时,采用万能测试仪,对复合材料进行抗拉强度测试,结果表明,涂层与基体结合强度较高,抗拉强度约为110mpa,相比实施例2,该涂层与基体结合强度有所降低。这证明了sic界面层过厚时,由于涂层应力分布不均导致涂层力学性能降低。
84.通过以上制备工艺制得的带有一种耐烧蚀三维互穿陶瓷涂层c/c复合材料在3000℃下进行60s每次,循环烧蚀3次的氧乙炔焰烧蚀检测,结果表明该复合材料中心区涂层有少量内陷,这说明涂层界面层过厚时,界面层与梯度层热膨胀系数相差较大,热应力分布不均,导致涂层于界面层出现开裂。这也证明了如果界面层过厚时,涂层与基体的界面过度效果会变差,不利于其增强涂层与基体的结合强度。
85.对比例51)选取密度为1.7g/cm3的三维针刺c/c复合材料板材,采用立式加工中心(jasu v-850)将c/c复合材料板材加工成厚度为10mm,直径为φ300mm的圆块样品;随后在c/c圆块样品表层进行打孔处理,打孔设备采用立式加工中心(jasu v-850),圆形盲孔结构为变径
盲孔:其中变径盲孔上部分(50%)直径为10mm,下部分(50%)盲孔直径为7mm,孔深为基体材料厚度的50%,即5mm,孔间距为盲孔孔径的8mm,孔分布呈等距点阵分布。
86.2)梯度高导热陶瓷内嵌体的成分为自表面向里的梯度陶瓷相组分设计。选取超高温陶瓷zrc和hfc,以及高温陶瓷sic作为陶瓷内嵌体的组成成分;采用放电等离子烧结法进去陶瓷内嵌体的制备。制备后的陶瓷体呈现出随着深度的增加超高温陶瓷相成分逐渐降低,而高热导率陶瓷相含量逐渐增加,最表面超高温陶瓷相高达100%,sic相为0,该特征陶瓷体高度为2mm,随后超高温陶瓷相含量降低为50%,sic相为50%,该特征陶瓷体高度为2mm,随后超高温陶瓷含量继续降低至0,sic相为100%,该特征陶瓷体高度为1mm。实现上述陶瓷体特征的方法为采用梯度配比上述质量比例的超高温陶瓷和sic陶瓷的混合粉末,随后通过顺序铺粉的方式进行铺制等离子烧结陶瓷内嵌体的方法。在实施等离子烧结法时,通过层层烧结的方法实现,内嵌体的梯度变化。采用放电等离子烧结温度为1800℃。烧结气氛为惰性气体(ar)。烧结时间为0.5h。所述内嵌体的尺寸与上述内凹结构相似,其水平尺寸均相差0.1mm,厚度尺寸一样。最终制备梯度高导热陶瓷内嵌体的直径为4.8mm,厚度为5mm,孔隙率为10%。
87.3)将烧结后的梯度高导热陶瓷内嵌体嵌入预加工的内凹结构,随后将复合材料放入铺有硅粉的石墨罐内,并于高频加热炉中采用热蒸镀法进行内嵌体和c/c复合材料基体界面处热匹配sic界面层的制备。其中在热蒸镀法制备sic层时,石墨罐内所铺si粉质量为坯体材料质量的0.8倍,热蒸镀温度为1850℃,热蒸镀时间为0.5h。
88.4)将嵌入了梯度高导热陶瓷内嵌体的c/c复合材料表层制备一层超高温陶瓷涂层,该低缺陷、高质密以及高均匀性超高温陶瓷涂层制备方法选用刷渗法工艺。在进行刷涂之前使用400目的sic砂纸手工打磨试样表面,然后用酒精超声清洗20min,最后在100℃下干燥8h。使用浆料刷涂法在样品表面进行zr、hf混合金属粉末层的制备,再使用热蒸镀-原位反应法制备内部sic连接层,并且填补刷涂法的孔洞缺陷。其中刷涂浆料配比为:zr:hf原子比为1:1的混合粉末作为超高温组元,将其混合金属粉末与聚乙烯醇粘结剂混合制成浆料,粉料与聚乙烯醇的比例为15g/ml,搅拌时间为30min制得。随后使用刷涂法把浆料均匀的涂覆在带有高热导率内嵌陶瓷体的c/c复合材料表层,然后在250℃烘箱中固化处理,反复三遍得到zr、hf二元层。
89.5)使用原子比(zr+hf)/si为1:2比例的粉料作为蒸镀母料,其中zr:hf为1:1粉料与基体置于石墨坩埚中,基体与粉料之间保持适宜高度(60mm)。将石墨坩埚放入高频石墨化炉中,ar气环境下加热到2400℃,保温3h,然后使石墨化炉自然冷却到室温,得到(zr/hf)c-sic涂层。此外高热导率内嵌陶瓷体与c/c复合材料基体表层也形成一层致密的超高温陶瓷和sic的界面层。最终,一种强界面、抗烧蚀和耐冲刷的“剑山”超高温陶瓷涂层于c/c基体表层成形。涂层厚度为400μm,涂层的最外层中超高温组元相比内层的含量高。该方法制备的涂层致密度和均匀性较好,涂层与基体结合紧密.通过以上制备工艺制得的带有一种耐烧蚀三维镶嵌陶瓷涂层c/c复合材料进行涂层结合强度测试时,采用万能测试仪,对复合材料进行抗拉强度测试,结果表明,涂层与基体结合强度较高,抗拉强度约为125mpa,内嵌体与涂层结合紧密,涂层脱落过程中,出现内嵌体的拔出效果,相比实施例1,该变径盲孔相比单一尺寸盲孔的涂层与基体的界面强度提高效果更佳。这证明了在复合材料内层植入了变径陶瓷内嵌体后,实现了涂层的三维镶嵌
结构设计,且变径盲孔的台阶也能提高内嵌体的卡扣作用,更加提高了涂层与基体的结合表面积,增加了涂层与基体的结合强度;此外,陶瓷内嵌体的拔出作用也提高了涂层与基体的结合强度。相比实施例3,内嵌体梯度分为三梯度时,不影响涂层与基体的结合强度。
90.通过以上制备工艺制得的带有一种耐烧蚀三维互穿陶瓷涂层c/c复合材料在3000℃下进行60s每次,循环烧蚀3次的氧乙炔焰烧蚀检测,结果表明该复合材料烧蚀中心区出现涂层开裂,出现鼓泡现象。这主要是因为梯度内嵌体的只分为三等分梯度,梯度性不明显,这将导致大量热量于表层的内嵌体聚集,导致内嵌体膨胀严重,这又将给涂层带来一向上的力,最终导致涂层向上出现开裂现象。因此,本对比例说明,内嵌体的梯度性需要分为五等份梯度,少于五等份梯度,内嵌体热应力,热导率均影响了最终涂层的高温性能。