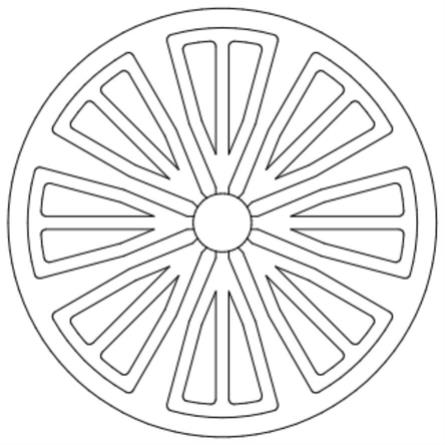
1.本发明属于水处理技术领域,具体涉及圆盘式陶瓷膜。
背景技术:2.陶瓷微滤膜具有化学稳定性高、耐酸、耐碱、耐腐蚀、耐高温、结构坚固、机械强度大、耐压耐磨、分离效率高、使用可靠、可反向冲洗,抗微生物能力强、不与微生物发生反应等优势,在处理油水分离、过滤生物医药中的微生物、分离提纯食品发酵液中的有效成分等方面有着广泛的应用。
3.困扰陶瓷膜微滤技术应用和发展的最关键问题是因浓差极化和膜污染而造成的膜过滤通量下降,要推动膜微滤技术发展就必须解决这两个难题。微滤中膜面除有浓差极化作用外,极易形成颗粒沉积滤饼层,而膜与颗粒之间的电性力和分子力都不及流体流动中的水动力学作用力对过滤的影响大,因而可采用一些措施使流动不稳定来降低膜污染。从流体力学边界层理论可知,由于静止壁面的存在,就不可避免地产生浓差极化现象和在膜表面生成滤饼层。因此,要想最大限度地消除或减缓膜污染,就必须改变边界层的状态,旋转动态膜结构就是以此为基础而提出的。
4.圆盘式陶瓷膜在自身旋转时与过滤液会在膜面上形成一个平行于膜面的剪切应力,使膜面不易形成截留物隔离层,有效减缓膜表面的浓差极化或滤饼层等污染物,降低了过滤阻力和膜污染。圆盘式陶瓷膜在过滤过程中不容易堵塞,使用寿命长、过滤效果高,非常适用于动态错流过滤。
5.陶瓷采用干压成型工艺,具有坯体密度大、尺寸精确、收缩小、机械强度高、成型周期短,成型效率高、便于实现自动化生产等优势。在圆盘式陶瓷膜膜饼的内部开设直线型或曲线形的流道,可降低膜的渗透阻力以及有利于膜渗透液的流通。然而,这种在膜饼内部开设流道的设计大大增加了陶瓷膜制造工艺的难度、复杂性和成本,并且导致陶瓷膜产品合格率极低。现有的干压成型技术中,是利用带有导流槽的模具分别成型两块带有流道的素坯,然后再将两块素坯拼合粘接,形成内部有流道的陶瓷膜。然而该工艺需要两种模具,尤其是带有导流槽的模具在脱模时的难度很高,并且需要将两块不同厚度的素坯扣合成一个完整的圆饼,扣合处还需要高温结合剂粘合,很容易产生不规则品,或存在泄漏风险。
技术实现要素:6.本发明的目的是针对带有导流槽的模具在脱模时的难度高,以及两块素坯扣合工艺复杂、合格率低、存在漏料风险等问题,提供了一种圆盘式多通道陶瓷膜的制备方法,为干压成型工艺,不需要采用导流槽模具且借助压型机压制成一体,降低陶瓷膜制备的工艺难度、且保证坯体的完整性。
7.本发明解决其技术问题所采用的技术方案是:
8.一种圆盘式多通道陶瓷膜的制备方法,其特征在于:包括:
9.1)支撑体的制备:所述支撑体的原料按质量份数计,包括:平均粒径为20~60μm的
氧化铝粉i 100份、烧结助剂5~10份、造孔剂10~15份、第一粘结剂5~8份、和脱模剂3~5份;其中,所述烧结助剂包括质量比为30~50:15~35:10~35:10~30的铝溶胶、钛溶胶、碳酸镁和高岭土;所述氧化铝粉i、烧结助剂和造孔剂干混后,添加第一粘结剂的水溶液和脱模剂进行造粒,烘干,过筛为20~80目的泥料,将泥料装入模具腔内并铺平;将与通道形状一致的至少一个热塑性塑料胶块放置在铺平的泥料上;再加入泥料覆盖所述至少一个热塑性塑料胶块,铺平;随后在双向压力下压制成型,压力为5~15mpa,得到内部有热塑性塑料胶块的素坯;素坯进行烧结:先升温至300~400℃保温1~3小时,然后升温至800~1000℃保温1~3小时,继续升温至1600~1700℃保温1~3小时,升温速率为2~5℃/min,烧结过程中除去所述热塑性塑料胶块,制得内部有通道的支撑体;
10.2)过渡层的制备:所述过渡层的原料按质量份数计,包括:平均粒径为1~10μm的氧化铝粉ii 100份、第一分散剂3~5份、和第二粘结剂15~25份;所述氧化铝粉ii、第一分散剂、第二粘结剂与水混合研磨得到第一涂膜液;将所述第一涂膜液均匀喷涂到所述支撑体外表面,干燥后进行烧结:以2~5℃/min的升温速率升温至1400~1600℃保温1~3小时,在所述支撑体上得到过渡层;
11.3)膜层的制备:所述膜层的原料按质量份数计,包括:平均粒径为0.1~1μm的氧化铝粉iii 100份、第二分散剂5~10份、第二粘结剂10~20份;所述氧化铝粉iii、第二分散剂、第三粘结剂与水混合研磨得到第二涂膜液;将所述第二涂膜液均匀喷涂到所述过渡层外表面,干燥后进行烧结:以2~5℃/min的升温速率升温至1100~1300℃保温1~3小时,得到所述圆盘式多通道陶瓷膜。
12.一实施例中,所述烧结助剂包括铝溶胶30~50%、钛溶胶15~35%、碳酸镁10~35%、高岭土10~30%,且烧结助剂各组分之和为100%。
13.一实施例中,所述造孔剂为平均粒径0.1~10μm的炭黑。
14.一实施例中,所述脱模剂包括油酸、桐油、硬脂酸铝或石墨中的至少一种。
15.优选地,氧化铝粉i的纯度》99%;氧化铝粉ii的纯度》99%;氧化铝粉iii的纯度》99%。
16.一实施例中,所述第一涂膜液的固含量30~50%。
17.一实施例中,所述第二涂膜液的固含量20~40%。
18.一实施例中,所述第一粘结剂、第二粘结剂、第三粘结剂各自独立地选自甲基纤维素、羟丙基甲基纤维素、聚乙二醇或聚乙烯醇中的至少一种。
19.进一步地,所述甲基纤维素的取代度为1.7~2.2;所述羟丙基甲基纤维素的粘度为100~50000cps;所述聚乙二醇的分子量为200~600;所述聚乙烯醇的分子量为1800~2200。
20.一实施例中,所述第一分散剂为聚乙烯醇,分子量为1800~2200,纯度大于99%。
21.一实施例中,所述第二分散剂为聚乙烯醇,分子量为1800~2200,纯度大于99%。
22.一实施例中,所述热塑性塑料胶粒包括pp(聚丙烯)、pe(聚乙烯)、hdpe(高密度聚乙烯)、ps(聚苯乙烯)、abs、pa塑料(尼龙)、聚碳酸酯或聚甲基丙烯酸甲酯中的至少一种。
23.一实施例中,所述涂膜液的研磨以氧化铝球为研磨介质,高速研磨2~5小时。所述“高速”指的是300~500rpm。
24.本发明制得的氧化铝支撑体外径为150~350mm,内径为40~100mm,内孔道数目为
8、12或16,氧化铝膜层的厚度为20~50μm。
25.在本发明支撑体的制备中,氧化铝粉i为支撑体的骨架,为整个材料提供强度,同时堆积形成气孔,为整个材料提供较高的孔隙率;烧结助剂在高温下形成液相,液相扩散促进氧化铝粉粘结在一起,降低支撑体烧结温度的同时赋予其较高的强度;造孔剂用于提高支撑体的孔隙率;粘结剂水解后具有一定的粘性,主要作用是常温下将氧化铝粉和烧结助剂等瘠性料赋予一定的可塑性,从而能通过压机压制成型;注塑成型塑料胶块的作用是先支撑圆盘陶瓷膜支撑体内部的通道,然后在高温烧结过程中分解排去,形成支撑体的内部通道;脱模剂的作用是润滑,方便成型的圆饼与模具凹槽分离,保证完整无缺陷的圆饼形素坯成型。
26.在本发明中,支撑体由粗颗粒组成,孔径较大,而膜层由较细的颗粒组成,孔径较小,因此直接在支撑体上喷涂膜层涂膜液时,两者的结合强度较低,通过在支撑体与膜层间制备过渡层作为大孔与小孔的过渡,提高支撑体与膜层的结合强度。
27.本发明中,支撑体中的流道形状及大小可以根据需要设置,例如为涡形叶片状,但并不以此为限。
28.本发明所涉及的设备、试剂、工艺、参数等,除有特别说明外,均为常规设备、试剂、工艺、参数等,不再作实施例。
29.本发明所列举的所有范围包括该范围内的所有点值。
30.本发明所述“大约”、“约”或“左右”等指的是所述范围或数值的
±
10%范围内。
31.本发明中,除有特别说明外,%均为质量百分比,比例均为质量比。所述质量的单位例如为克、千克或吨。
32.本发明中,所述“常温”“室温”即常规环境温度,可以为10~30℃。
33.本技术方案与背景技术相比,它具有如下优点:
34.本发明仅采用一种圆环形模具即可压制成型圆盘膜的支撑体素坯,且模具不带有导流槽,对模具开发和制备的要求低。先在模具腔内装入适量的造粒粉并铺平,然后注塑多个跟通道形状一样的塑料胶块,在铺平后的粉面上均匀放置各个塑料胶块,往里再装入适量的造粒粉并铺平,采用压型机压制成型,脱模、烧结得内有通道的支撑体。本发明无需采用有导流槽的模具,大大降低了成型难度,降低了模具成本。本发明采用压型机一体成型素坯,并借助填充塑料胶块在高温烧结过程中分解排去,形成支撑体的内部通道,省去了两片素坯的贴合工艺,保证了支撑体的完整性和强度可靠性。
附图说明
35.图1为本发明实施例中圆盘式多通道陶瓷膜的结构示意图。
具体实施方式
36.下面通过实施例具体说明本发明的内容:
37.实施例1
38.1)圆盘式多通道陶瓷膜支撑体的制备
39.称取平均粒径为50μm的氧化铝粉i 100份、烧结助剂5份(铝溶胶占35%、钛溶胶占20%、碳酸镁占20%、高岭土占25%)、平均粒径为5μm的炭黑10份、分子量2000且纯度大于
99%的聚乙烯醇6份,将聚乙烯醇搅拌溶于热水中待用,将氧化铝粉i、烧结助剂和炭黑用强力混合机干混5min后,在造粒机上缓慢添加聚乙烯醇水溶液和4份油酸,直至大部分泥料成微球;
40.将造粒后的泥料烘干、过筛,取粒径在20~80目间的泥料微球,装入模具腔内并铺平;
41.将型号为dmda-8916的hdpe胶粒,采用cj150nc型注射机注塑成跟待成型的通道形状一样的胶块,例如图1中的通道形状;注射机的参数设定如下:料筒前段、中段、后段的温度依次为175℃、170℃、168℃,喷嘴温度172℃,塑化压力46mpa,注射压力40mpa,模具冷却水温度16℃,螺杆转速58rpm/min,注射时间2s,保压时间25s,冷却时间14s;注塑8个通道形状的胶块。
42.在铺平后的泥料粉面上均匀放置8个hdpe塑料胶块,往里再填入适量过筛后的泥料,在大吨位压力机上经干压成型得内部有hdpe塑料胶块的素坯,干压成型的压力为双向压力,压力为8mpa;
43.将内部有hdpe塑料胶块的素坯进行烧结:先以3℃/min的速率升温至400℃保温2小时,然后以5℃/min的速率升温至900℃保温2小时,再以4℃/min的速率升温至1680℃保温2小时,得到圆盘式多通道陶瓷膜支撑体。测得支撑体边沿的起泡点泡压为0.0375mpa。通道的结构示意图如图1。
44.2)圆盘式多通道陶瓷膜过渡层的制备
45.称取平均粒径为6μm的氧化铝粉ii 100份、分子量2000的聚乙烯醇3份、粘度为4000cps的羟丙基甲基纤维素20份,然后加入去离子水,并放入行星式球磨机中,以氧化铝球为研磨介质,高速研磨2小时得第一涂膜液,第一涂膜液的固含量为40%;
46.用喷枪将第一涂膜液均匀喷涂到支撑体外表面,室温放置2h后烧结:以3℃/min的速率升温至1500℃保温2小时,得圆盘式多通道陶瓷膜过渡层。
47.3)圆盘式多通道陶瓷膜膜层的制备
48.称取平均粒径为0.3μm的氧化铝粉iii 100份、分子量2000的聚乙烯醇5份、粘度为4000cps的羟丙基甲基纤维素15份,然后加入去离子水,并放入行星式球磨机中,以氧化铝球为研磨介质,高速研磨3小时得第二涂膜液,第二涂膜液的固含量为25%;
49.用喷枪将第二涂膜液均匀喷涂到过渡层外表面,室温放置3h后烧结:以3℃/min的速率升温至1200℃保温2小时,得圆盘式多通道陶瓷膜成品。
50.本实施例所制备的圆盘式多通道陶瓷膜支撑体强度高,外径为300mm,内径为90mm,内孔道数目为8,抗折强度为39mpa。膜层由平均粒径为0.3μm的氧化铝颗粒组成,颗粒均匀性较好,过滤精度约为0.1μm。该实施例制得的圆盘式多通道陶瓷膜的孔隙率为32.5%,膜层起泡点泡压为0.17mpa,过滤通量可达1.22m3/(m2h)。
51.实施例2
52.1)圆盘式多通道陶瓷膜支撑体的制备
53.称取平均粒径为40μm的氧化铝粉i 100份、烧结助剂5份(铝溶胶占35%、钛溶胶占20%、碳酸镁占20%、高岭土占25%)、平均粒径为5μm的炭黑10份、分子量2000且纯度大于99%的聚乙烯醇6份,将聚乙烯醇搅拌溶于热水中待用,将氧化铝粉i、烧结助剂和炭黑用强力混合机干混5min后,在造粒机上缓慢添加聚乙烯醇水溶液和4份油酸,直至大部分泥料成
微球;
54.将造粒后的泥料烘干、过筛,取粒径在20~80目间的泥料微球,装入模具腔内并铺平;
55.将型号为dmda-8916的hdpe胶粒,采用cj150nc型注射机注塑成跟待成型的通道形状一样的胶块,例如图1中的通道形状;注射机的参数设定如下:料筒前段、中段、后段的温度依次为175℃、170℃、168℃,喷嘴温度172℃,塑化压力46mpa,注射压力40mpa,模具冷却水温度16℃,螺杆转速58rpm/min,注射时间2s,保压时间25s,冷却时间14s;注塑8个通道形状的胶块。
56.在铺平后的泥料粉面上均匀放置8个hdpe塑料胶块,往里再填入适量过筛后的泥料,在大吨位压力机上经干压成型得内部有hdpe塑料胶块的素坯,干压成型的压力为双向压力,压力为8mpa;
57.将内部有hdpe塑料胶块的素坯进行烧结:先以3℃/min的速率升温至400℃保温2小时,然后以5℃/min的速率升温至900℃保温2小时,再以4℃/min的速率升温至1650℃保温2小时,得到圆盘式多通道陶瓷膜支撑体。测得支撑体边沿的起泡点泡压为0.042mpa。通道的结构示意图如图1。
58.2)圆盘式多通道陶瓷膜过渡层的制备
59.称取平均粒径为5μm的氧化铝粉ii 100份、分子量2000的聚乙烯醇3份、粘度为4000cps的羟丙基甲基纤维素20份,然后加入去离子水,并放入行星式球磨机中,以氧化铝球为研磨介质,高速研磨2小时得第一涂膜液,第一涂膜液的固含量为40%;
60.用喷枪将第一涂膜液均匀喷涂到支撑体外表面,室温放置2h后烧结:以3℃/min的速率升温至1450℃保温2小时,得圆盘式多通道陶瓷膜过渡层。
61.3)圆盘式多通道陶瓷膜膜层的制备
62.称取平均粒径为0.3μm的氧化铝粉iii 100份、分子量2000的聚乙烯醇5份、粘度为4000cps的羟丙基甲基纤维素15份,然后加入去离子水,并放入行星式球磨机中,以氧化铝球为研磨介质,高速研磨3小时得第二涂膜液,第二涂膜液的固含量为25%;
63.用喷枪将第二涂膜液均匀喷涂到过渡层外表面,室温放置3h后烧结:以3℃/min的速率升温至1200℃保温2小时,得圆盘式多通道陶瓷膜成品。
64.本实施例所制备的圆盘式多通道陶瓷膜支撑体强度高,外径为300mm,内径为90mm,内孔道数目为8,抗折强度为36mpa。膜层由平均粒径为0.3μm的氧化铝颗粒组成,颗粒均匀性较好,过滤精度约为0.1μm。该实施例制得的圆盘式多通道陶瓷膜的孔隙率为33.9%,膜层起泡点泡压为0.175mpa,过滤通量可达1.22m3/(m2h)。
65.实施例3
66.1)圆盘式多通道陶瓷膜支撑体的制备
67.称取平均粒径为30μm的氧化铝粉i 100份、烧结助剂5份(铝溶胶占35%、钛溶胶占20%、碳酸镁占20%、高岭土占25%)、平均粒径为5μm的炭黑10份、分子量2000且纯度大于99%的聚乙烯醇6份,将聚乙烯醇搅拌溶于热水中待用,将氧化铝粉i、烧结助剂和炭黑用强力混合机干混5min后,在造粒机上缓慢添加聚乙烯醇水溶液和4份油酸,直至大部分泥料成微球;
68.将造粒后的泥料烘干、过筛,取粒径在20~80目间的泥料微球,装入模具腔内并铺
平;
69.将型号为dmda-8916的hdpe胶粒,采用cj150nc型注射机注塑成跟待成型的通道形状一样的胶块,例如图1中的通道形状;注射机的参数设定如下:料筒前段、中段、后段的温度依次为175℃、170℃、168℃,喷嘴温度172℃,塑化压力46mpa,注射压力40mpa,模具冷却水温度16℃,螺杆转速58rpm/min,注射时间2s,保压时间25s,冷却时间14s;注塑8个通道形状的胶块。
70.在铺平后的泥料粉面上均匀放置8个hdpe塑料胶块,往里再填入适量过筛后的泥料,在大吨位压力机上经干压成型得内部有hdpe塑料胶块的素坯,干压成型的压力为双向压力,压力为8mpa;
71.将内部有hdpe塑料胶块的素坯进行烧结:先以3℃/min的速率升温至400℃保温2小时,然后以5℃/min的速率升温至900℃保温2小时,再以4℃/min的速率升温至1600℃保温2小时,得到圆盘式多通道陶瓷膜支撑体。测得支撑体边沿的起泡点泡压为0.045mpa。通道的结构示意图如图1。
72.2)圆盘式多通道陶瓷膜过渡层的制备
73.称取平均粒径为3μm的氧化铝粉ii 100份、分子量2000的聚乙烯醇3份、粘度为4000cps的羟丙基甲基纤维素20份,然后加入去离子水,并放入行星式球磨机中,以氧化铝球为研磨介质,高速研磨2小时得第一涂膜液,第一涂膜液的固含量为40%;
74.用喷枪将第一涂膜液均匀喷涂到支撑体外表面,室温放置2h后烧结:以3℃/min的速率升温至1400℃保温2小时,得圆盘式多通道陶瓷膜过渡层。
75.3)圆盘式多通道陶瓷膜膜层的制备
76.称取平均粒径为0.3μm的氧化铝粉iii 100份、分子量2000的聚乙烯醇5份、粘度为4000cps的羟丙基甲基纤维素15份,然后加入去离子水,并放入行星式球磨机中,以氧化铝球为研磨介质,高速研磨3小时得第二涂膜液,第二涂膜液的固含量为25%;
77.用喷枪将第二涂膜液均匀喷涂到过渡层外表面,室温放置3h后烧结:以3℃/min的速率升温至1200℃保温2小时,得圆盘式多通道陶瓷膜成品。
78.本实施例所制备的圆盘式多通道陶瓷膜支撑体强度高,外径为300mm,内径为90mm,内孔道数目为8,抗折强度为33mpa。膜层由平均粒径为0.3μm的氧化铝颗粒组成,颗粒均匀性较好,过滤精度约为0.1μm。该实施例制得的圆盘式多通道陶瓷膜的孔隙率为34.9%,膜层起泡点泡压为0.18mpa,过滤通量可达1.26m3/(m2h)。
79.对比例1
80.1)圆盘式多通道陶瓷膜支撑体的制备
81.称取平均粒径为30μm的氧化铝粉i 100份、烧结助剂5份(铝溶胶占35%、钛溶胶占20%、碳酸镁占20%、高岭土占25%)、平均粒径为5μm的炭黑10份、分子量2000且纯度大于99%的聚乙烯醇6份,将聚乙烯醇搅拌溶于热水中待用,将氧化铝粉i、烧结助剂和炭黑用强力混合机干混5min后,在造粒机上缓慢添加聚乙烯醇水溶液和4份油酸,直至大部分泥料成微球;
82.将造粒后的泥料烘干、过筛,取粒径在20~80目间的泥料微球,装入有凹槽的模具中,在大吨位压力机上经干压成型得其中一个外表面有流道的素坯,干压成型的压力为双向压力,压力为8mpa;
83.将造粒后的泥料烘干、过筛,取粒径在20~80目间的泥料微球,装入没有凹槽的模具中,在大吨位压力机上经干压成型得外表面无流道的另一块素坯,干压成型的压力为双向压力,压力为8mpa;
84.称取平均粒径为15μm的氧化铝粉i 100份、烧结助剂5份(铝溶胶占35%、钛溶胶占20%、碳酸镁占20%、高岭土占25%),用强力混合机干混5min得混合粉末。称取分子量2000且纯度大于99%的聚乙烯醇20份,将聚乙烯醇搅拌溶于80份热水中待用。称取60份混合粉末、30份聚乙烯醇胶水、和10份ro水于烧杯或研钵中,搅拌或研磨30min后得浓浆。将浓浆均匀涂覆于两片素坯的表面后将两片素坯贴合在一起,并在两片素坯的边沿均匀涂覆一层浓浆。贴合的素坯在60℃下烘10h。
85.将贴合好的素坯进行烧结:先以3℃/min的速率升温至400℃保温2小时,然后以5℃/min的速率升温至900℃保温2小时,再以4℃/min的速率升温至1600℃保温2小时,得内部有多通道圆盘式陶瓷膜支撑体。测得支撑体边沿的起泡点泡压为0.01mpa。通道的结构示意图如图1。
86.2)圆盘式多通道陶瓷膜过渡层的制备
87.称取平均粒径为3μm的氧化铝粉ii 100份、分子量2000的聚乙烯醇3份、粘度为4000cps的羟丙基甲基纤维素20份,然后加入去离子水,并放入行星式球磨机中,以氧化铝球为研磨介质,高速研磨2小时得涂膜液,涂膜液的固含量为40%;
88.用喷枪将涂膜液均匀喷涂到支撑体外表面,室温放置2h后烧结:以3℃/min的速率升温至1400℃保温2小时,得圆盘式多通道陶瓷膜过渡层。
89.3)圆盘式多通道陶瓷膜膜层的制备
90.称取平均粒径为0.3μm的氧化铝粉iii 100份、分子量2000的聚乙烯醇5份、粘度为4000cps的羟丙基甲基纤维素15份,然后加入去离子水,并放入行星式球磨机中,以氧化铝球为研磨介质,高速研磨3小时得涂膜液,涂膜液的固含量为25%;
91.用喷枪将涂膜液均匀喷涂到过渡层外表面,室温放置3h后烧结:以3℃/min的速率升温至1200℃保温2小时,得圆盘式多通道陶瓷膜成品。
92.本对比例所制备的圆盘式多通道陶瓷膜支撑体强度高,外径为300mm,内径为90mm,内孔道数目为8,抗折强度为34.3mpa。膜层由平均粒径为0.3μm的氧化铝颗粒组成,颗粒均匀性较好,过滤精度约为0.1μm。该对比例制得的圆盘式多通道陶瓷膜的孔隙率为33.7%,边沿膜层先起泡,起泡点泡压为0.09mpa,过滤通量可达1.24m3/(m2h)。
93.这种两片贴合的工艺制备的支撑体,贴合不良处容易产生泡压缺陷。这降低了膜层的泡压,膜片在使用过程中容易漏料,影响过滤效果。
94.以上所述,仅为本发明较佳实施例而已,故不能依此限定本发明实施的范围,即依本发明专利范围及说明书内容所作的等效变化与修饰,皆应仍属本发明涵盖的范围内。