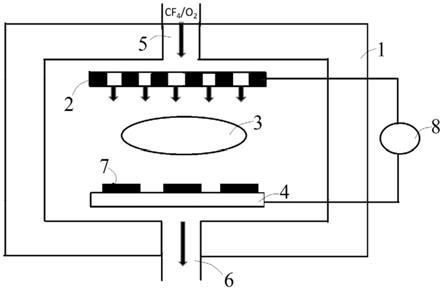
一种去除lpcvd多晶硅绕镀的装置及方法
技术领域
1.本发明涉及晶硅太阳能电池技术领域,更具体地说,涉及一种去除lpcvd多晶硅绕镀的装置及方法。
背景技术:2.近年来,在补贴退潮的倒逼下,我国光伏发电技术处于飞速发展中,其中最为基础的光伏电池技术更是百花齐放。不同类型的高效电池层出不穷。效率的不断提升,让人看到了光伏发电的活力,也看到了光伏发电未来的巨大潜力。
3.perc电池目前量产效率为22.3%~22.8%,perc电池实验室最高效率为24%,量产效率已经越来越接近这个数值,perc电池的效率瓶颈已经到来。而且perc电池已经面临着越来越多的难题:电阻率窗口很窄,el良率下降,双面pid现象,letid现象。
4.近几年,topcon电池横空出世,受到了行业的焦点关注。晶科能源创造了n型单晶硅topcon双面电池24.87%(全面积)和24.90%(孔径面积)的中国最高效率纪录,fraunhofer
‑
ise研究的n型topcon太阳能电池效率则达到了25.8%。根据理论计算,topcon太阳能电池的潜在效率(28.7%)最接近晶体硅太阳单结电池理论极限效率(29.43%)。
5.topcon技术只需要增加薄膜沉积设备,就能很好地与目前量产工艺兼容,topcon电池以较小的成本获得了较大的效率上升。拥有以上的优势,topcon电池毫无疑问拥有广阔的发展前景。n型topcon是继p型perc之后大规模量产的新一代电池之一,topcon技术是在n型电池背面制备一层超薄的隧穿氧化层和一层高掺杂的多晶硅薄层,二者共同形成了钝化接触结构。该结构可以阻挡少子空穴复合,提升电池开路电压及短路电流。
6.topcon电池已经引起多家光伏企业的布局,中来股份、天合光能都宣布topcon实现量产。但是topcon电池良率一直是个大难题,造成生产成本居高不下,严重影响了topcon电池进一步发展的势头,良率偏低的主要原因lpcvd设备沉积多晶硅时造成正面绕镀现象,而目前行业湿法刻蚀的方式去除绕镀会带来各种各样的问题,造成良率和效率达不到预期效果。
7.正面多晶硅绕镀的去除行业目前主流的方法是湿法刻蚀方案。其中湿法刻蚀有酸碱去绕镀两种方案,但是酸碱去绕镀的方法均存在一定的问题。其中,用酸去绕镀,混酸去除电池正面多晶硅的同时也会刻蚀多晶硅下层的硅衬底,造成电池部分区域金字塔被损坏,严重影响电池的外观,造成电池良率偏低,生产成本高。用碱去除的方式则无法将有些电池片正面绕镀的多晶硅完全去除,特别是硅片四个角的区域,与碱反应速率很慢,长时间的刻蚀会影响电池正面其他区域和电池背面,造成器件失效。
8.经检索,中国专利号:zl201380024888.6,授权公告日为:2017年3月1日,发明名称为:蚀刻方法和等离子体处理装置,该申请案的方法包括:(a)准备被处理基体的工序,该被处理基体具有被蚀刻层和设在该被蚀刻层上的掩模;(b)使用该掩模蚀刻被蚀刻层的工序。掩模具有:第1掩模部,其由多晶硅构成;第2掩模部,其由氧化硅构成,且介于该第1掩模部与所述被蚀刻层之间。在蚀刻被蚀刻层的工序中,向收纳有被处理基体的处理容器内供给
用于蚀刻被蚀刻层的第1气体、用于除去已附着于掩模的沉积物的第2气体和用于保护第1掩模部的第3气体,在处理容器内生成等离子体。但该申请案在进行刻蚀时,等离子气体对掩膜部刻蚀速度较快,容易在停止刻蚀时不及时,从而对电池造成损坏。
技术实现要素:9.1.发明要解决的技术问题
10.鉴于目前对多晶硅绕度去除多采用湿法刻蚀,而湿法刻蚀去除绕镀会带来各种各样的问题,造成良率和效率达不到预期效果的问题,本发明提供了一种去除lpcvd多晶硅绕镀的装置及方法,利用等离子气体去除多晶硅绕度,使多晶硅绕度得以完全去除,同时不损坏电池,良率和效率均能满足需要。
11.2.技术方案
12.为达到上述目的,本发明提供的技术方案为:
13.本发明的一种去除lpcvd多晶硅绕镀的装置,包括腔体、第一电极、第二电极和微波发生器;所述的第一电极和第二电极设置在腔体内部,分别靠近腔体入口和腔体出口;所述的微波发生器电连接第一电极和第二电极;所述的第一电极和第二电极之间放置硅片。
14.更进一步地,所述的硅片一面紧贴靠近腔体出口的电极,第一电极和第二电极之间产生的等离子体接触硅片未紧贴电极一侧。
15.更进一步地,所述的等离子体由两电极电解cf4/o2气体产生;所述的cf4/o2气体由腔体入口通入腔体,刻蚀后产生的气体由腔体出口排出。
16.本发明的一种去除lpcvd多晶硅绕镀的方法,其步骤为:
17.步骤一、制备topcon双面电池的pn结,并利用湿法单面刻蚀,去除电池背结;
18.步骤二、对获得的pn结进行氧化,使其表面获得氧化层;
19.步骤三、利用单面刻蚀设备单面去除正面绕镀多晶硅表面的psg;
20.步骤四、利用等离子体对电池正面的多晶硅绕镀进行刻蚀;
21.步骤五、清洗氧化层并利用ald技术和pecvd技术制备topcon双面电池。
22.更进一步地,所述的步骤一中,使用槽式制绒设备,对单晶硅片进行制绒处理,形成金字塔绒面;并采用管式高温扩散技术,对硅基体掺硼制备pn结。
23.更进一步地,所述的步骤二中,在对pn结进行氧化时,氧气流量为15slm/min,氧化温度为980℃,获得的氧化硅厚度根据式(1)进行计算,
24.t=0.5t+22.4
ꢀꢀꢀꢀꢀꢀꢀꢀꢀꢀꢀꢀꢀꢀꢀꢀꢀꢀꢀꢀꢀꢀꢀꢀꢀꢀꢀꢀꢀꢀꢀ
(1)
25.其中,t为氧化硅厚度,t为氧化时间。
26.更进一步地,所述的步骤三中,单面刻蚀设备中配置10
‑
40%体积浓度的hf。
27.更进一步地,所述的步骤四中,选取cf4‑
o2作为等离子气体,cf4气体流量为20
‑
120sccm,o2流量为10
‑
60sccm,其中,o2浓度占cf4‑
o2的35%,等离子气体刻蚀多晶硅和氧化硅的选择比为2。
28.更进一步地,所述的步骤二的氧化过程中,背面沉积的晶硅厚度为d,正面绕镀最边缘区域多晶硅厚度为110%d;步骤四中,等离子气体刻蚀多晶硅和氧化硅的选择比为2,则控制氧化硅临界厚度为110%d/2,并设定工艺窗口为10%,计算得出氧化硅最小厚度为60.5%d,结合公式(1),得出氧化时间为1.21d
‑
44.8。
29.3.有益效果
30.采用本发明提供的技术方案,与已有的公知技术相比,具有如下显著效果:
31.(1)鉴于现有的湿法刻蚀去除绕镀会带来各种各样的问题,造成良率和效率达不到预期效果的问题,本发明提供的一种去除lpcvd多晶硅绕镀的装置,利用等离子气体对绕度进行刻蚀,并将多晶硅一面紧贴电极,使等离子气体只刻蚀多晶硅的一面,而不对另一面造成损害,刻蚀速度快的同时,保证lpcvd多晶硅的完整,使去除绕镀的良率和效率满足要求。
32.(2)本发明提供的一种去除lpcvd多晶硅绕镀的方法,在进行蚀刻前,根据多晶硅堆积厚度,增加电池氧化时间,以增加氧化硅厚度,防止刻蚀过度,对pn结造成损坏。同时使用等离子气体对绕度进行蚀刻,速度较快。等离子气体选用cf4‑
o2气体,对多晶硅和氧化硅刻蚀速率差别大,能够节省氧化层,进而减少氧化时间,节约了资源。
33.(3)本发明提供的一种去除lpcvd多晶硅绕镀的方法,设定较好的氧气流量和氧化温度,保证氧化层较快形成。同时在氧化硅临界厚度基础上增加10%的工艺窗口,防止刻蚀速度过快,停止时导致氧化层厚度不够而影响到pn结,从而提高了刻蚀之后电池的合格率。
附图说明
34.图1为本发明太阳能电池硅片的结构示意图;
35.图2为本发明设备的结构示意图;
36.图3为本发明氧化时间与氧化层厚度关系折线图;
37.图4为o2在cf4‑
o2中占比与对硅和氧化硅刻蚀速率关系图。
38.图中标号说明:
39.1、腔体;2、第一电极;3、等离子体;4、第二电极;5、腔体入口;6、腔体出口;7、硅片;8、微波发生器。
具体实施方式
40.为进一步了解本发明的内容,结合附图和实施例对本发明作详细描述。
41.实施例1
42.本实施例中需要刻蚀的硅片7机构如图1所示,需要将氧化硅上层的多晶硅层完全去除。pn结上层覆盖一层氧化硅(bsg),氧化硅上部是局部存在的多晶硅。多晶硅从边缘到中心绕镀层厚度逐渐降低,至中心处厚度为零。进行刻蚀时,需将上层局部存在的多晶硅去除,且不能刻蚀掉过多下层的氧化硅,以免损伤到氧化硅掩膜下面的硅衬底。
43.结合图2,本实施采用的一种去除lpcvd多晶硅绕镀的装置,包括腔体1、第一电极2、第二电极4和微波发生器8;所述的第一电极2和第二电极4设置在腔体1内部,分别靠近腔体入口5和腔体出口6;所述的微波发生器8电连接第一电极2和第二电极4;所述的第一电极2和第二电极4之间放置硅片7。所述的硅片7一面紧贴靠近腔体出口6的电极,第一电极2和第二电极4之间产生的等离子体3接触硅片7未紧贴电极一侧。所述的等离子体3由两电极电解cf4‑
o2气体产生。cf4‑
o2气体由腔体入口5通入腔体1,刻蚀后产生的sif4气体由腔体出口6排出。其中,微波发生器8射频功率范围为100
‑
5000w,腔体1内压力为10
‑
500pa,温度为200
‑
500℃。本实施例中,微波发生器8射频功率选取5000w,,腔体1内压力为500pa,温度为500
℃。
44.本实施例的装置利用等离子气体对绕度进行刻蚀,并将硅片7一面紧贴电极,使等离子气体只刻蚀硅片7的一面,而不对另一面造成损害,刻蚀速度快的同时,保证lpcvd硅片7的完整,使去除绕镀的良率和效率满足要求。
45.本实施例的一种去除lpcvd多晶硅绕镀的方法,其步骤为:
46.步骤一、制备topcon双面电池的pn结,并利用湿法单面刻蚀,去除电池背结:
47.使用槽式制绒设备,对单晶硅片进行制绒处理,形成金字塔绒面;并采用管式高温扩散技术,对硅基体掺硼制备pn结。并利用湿法单面刻蚀,去除电池背结。
48.步骤二、对获得的pn结进行氧化,使其表面获得氧化层:
49.结合图3,上层氧化硅厚度主要和推结后高温氧化步骤的时间、温度以及氧气流量关系密切。在对pn结进行氧化时,设定氧气流量为15slm/min,氧化温度为980℃,获得的氧化硅厚度根据式(1)进行计算,
50.t=0.5t+22.4
ꢀꢀꢀꢀꢀꢀꢀꢀꢀꢀꢀꢀꢀꢀꢀꢀꢀꢀꢀꢀꢀꢀꢀꢀꢀꢀꢀꢀꢀꢀꢀ
(1)
51.其中,t为氧化硅厚度,t为氧化时间。
52.步骤三、利用单面刻蚀设备单面去除正面绕镀多晶硅表面的psg:
53.单面刻蚀设备中配置10
‑
40%体积浓度的hf。由于bsg厚度远大于psg,可以较为轻易的控制反应时间,去除psg。本实施例中选取40%体积浓度的hf。
54.步骤四、利用等离子体对电池正面的多晶硅绕镀进行刻蚀:
55.选取cf4‑
o2作为等离子气体,cf4气体流量为20
‑
120sccm,o2流量为10
‑
60sccm,其中,o2浓度占cf4‑
o2的35%,等离子气体刻蚀多晶硅和氧化硅的选择比为2。结合图4,cf4‑
o2混合气体中o2浓度比例对整个刻蚀反应速率影响很大,经发明人研究发现,当o2浓度比例低于40%时,多晶硅和氧化硅的刻蚀速率与o2浓度比例呈正相关关系,刻蚀速率与o2浓度比例公式如下:
56.s1=133.8q1+33
ꢀꢀꢀꢀꢀꢀꢀꢀꢀꢀꢀꢀꢀꢀꢀꢀꢀꢀꢀꢀꢀꢀꢀ
(2)
57.s2=32.6q2+30
ꢀꢀꢀꢀꢀꢀꢀꢀꢀꢀꢀꢀꢀꢀꢀꢀꢀꢀꢀꢀꢀꢀꢀꢀ
(3)
58.其中,s1为硅刻蚀速率与o2浓度比例关系,s2为氧化硅刻蚀速率与o2浓度比例关系。
59.而当o2浓度比例进一步提升,则刻蚀速率快速下降。因此结合两公式得出当o2浓度比例在35%左右时,刻蚀速率选择比维持在2上下达到峰值。因此在通入cf4‑
o2混合气体时,控制o2浓度占总气体比例的35%。本实施例中,为达到较快的刻蚀速率,选取cf4气体流量为100sccm,o2流量为54sccm。
60.步骤五、清洗氧化层并利用ald技术和pecvd技术制备topcon双面电池。
61.其中,步骤二氧化过程中,背面沉积的多晶硅厚度较为固定,设定其厚度为d,而正面绕镀最边缘区域多晶硅厚度为110%d。而在步骤四中,等离子气体刻蚀多晶硅和氧化硅的选择比为2,则控制氧化硅临界厚度为110%d/2,并设定工艺窗口为10%,计算得出氧化硅最小厚度为60.5%d,结合公式(1),得出氧化时间为1.21d
‑
44.8。
62.本实施例的方法,在进行蚀刻前,根据多晶硅堆积厚度,增加电池氧化时间,以增加氧化硅厚度,防止刻蚀过度,对pn结造成损坏。同时使用等离子气体对绕度进行蚀刻,速度较快。等离子气体选用cf4‑
o2气体,对多晶硅和氧化硅刻蚀速率差别大,能够节省氧化层,
进而减少氧化时间,节约了资源。同时设定较好的氧气流量和氧化温度,保证氧化层较快形成。在氧化硅临界厚度基础上增加10%的工艺窗口,防止刻蚀速度过快,停止时导致氧化层厚度不够而影响到pn结,从而提高了刻蚀之后电池的合格率。
63.实施例2
64.本实施例的装置与实施例1装置结构相同,不同之处在于,微波发生器8射频功率选取100w,,腔体1内压力为10pa,温度为200℃。本实施例的方法与实施例1的方法步骤相同,不同之处在于,步骤三中选择10%体积浓度的hf,步骤四中cf4气体流量为19sccm,o2流量为10sccm。
65.实施例3
66.本实施例的装置与实施例1装置结构相同,不同之处在于,微波发生器8射频功率选取3000w,腔体1内压力为200pa,温度为400℃。本实施例的方法与实施例1的方法步骤相同,不同之处在于,步骤三中选择20%体积浓度的hf,步骤四中cf4气体流量为50sccm,o2流量为27sccm。
67.以上示意性的对本发明及其实施方式进行了描述,该描述没有限制性,附图中所示的也只是本发明的实施方式之一,实际的结构并不局限于此。所以,如果本领域的普通技术人员受其启示,在不脱离本发明创造宗旨的情况下,不经创造性的设计出与该技术方案相似的结构方式及实施例,均应属于本发明的保护范围。