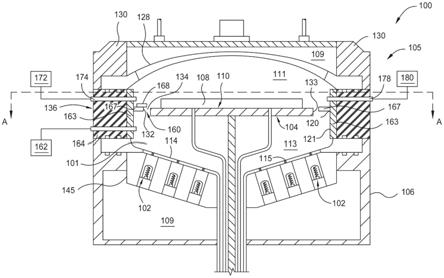
1.本公开内容的实例一般涉及用于半导体处理的设备。更具体言之,本文所述的实例涉及一种用于外延腔室的隔热组件。
背景技术:2.外延是一种常用于半导体处理中的工艺,以制造用于半导体器件的具有极均匀电学特性的高质量材料。随着半导体器件变得越来越小以及制造单元变得越来越大,单个制造基板上的均匀性变得越来越重要。
3.在外延腔室中,基板上的处理气体从腔室的一侧流到去除气体的另一侧。基板可经配置在处理期间旋转以最小化不均匀的影响,但是仍然可能因持续的不均匀性而出现径向变化。外延腔室可以包括绕基座移动(circumnavigate)的隔热组件。隔热组件可以吸收来自基座下方的加热组件的热,并在隔热组件上方再辐射(re-radiate)这些热。
4.在外延腔室内处理基板期间,残留材料(如气态前驱物及其反应副产物)可能会不必要地将材料沉积在外延腔室内的一个或多个内表面上。沉积物的厚度会随着每处理一个基板而增加。随着残留材料沉积物的厚度增加,沉积物最终从外延处理腔室表面剥落,而导致处理空间中不必要的微粒污染。微粒污染可能对沉积在基板上的材料层的质量有负面影响。因此,必须定期清洁外延腔室,以从中去除残留的材料。外延处理腔室清洁包括基板处理操作之间的周期性清洁循环中的一个或两个(both),以及为清洁和定期维护打开腔室。这样的清洁和维护导致较低的基板产量和增加腔室停机时间。因此,这种清洁和维护可能导致处理腔室的生产率流失。
5.因此,在本领域中需要减少外延处理腔室中的腔室污染和停机时间。
技术实现要素:6.本文公开的是一种用于处理腔室的隔热组件。处理腔室包括腔室主体,该腔室主体具有侧壁、底部和盖件,该侧壁、底部和盖件限定腔室主体的内部空间。隔热组件设置在内部空间中。隔热组件包括隔热构件和环形预热构件。环形预热构件包括内圆周。环形预热构件定位于环形隔热件下方。基座设置在内部空间中,并经配置支撑基板。基座定位于环形预热构件的内圆周内。环形开口定位于基座和环形预热构件之间。环形开口的第一部分靠近气体入口。第一部分被隔热构件覆盖。环形开口的第二部分靠近气体出口。环形开口的第二部分没有被隔热构件覆盖。
7.处理腔室的另一实例包括腔室主体,该腔室主体具有侧壁、底部和盖件,该侧壁、底部和盖件限定腔室主体的内部空间。隔热组件设置在内部空间中。隔热组件包括隔热构件。隔热组件还包括具有内圆周的环形预热构件。环形预热构件定位于环形隔热件下方。基座设置在内部空间中,并经配置支撑基板。基座定位于环形预热构件的内圆周内。环形开口定位于基座和环形预热构件之间。环形开口的第一部分靠近气体入口。第一部分被隔热构件覆盖。环形开口的弧形孔靠近气体出口。弧形孔没有被隔热构件覆盖。该处理腔室内的该
弧形孔的位置影响该基座的底侧或该处理腔室的侧壁上的涂层。
8.在又一实例中,处理腔室包括腔室主体,该腔室主体具有侧壁、底部和盖件,该侧壁、底部和盖件限定腔室主体的内部空间。隔热组件设置在内部空间中。隔热组件包括隔热构件和环形预热构件。环形预热构件包括内圆周。环形预热构件定位于环形隔热件下方。基座设置在内部空间中,并经配置支撑基板。基座定位于环形预热构件的内圆周内。环形开口定位于基座和环形预热构件之间。环形开口的第一部分靠近气体入口。第一部分被隔热构件覆盖。环形开口的第二部分靠近气体出口。第二部分没有被隔热构件覆盖。环形开口相对于该气体出口的位置影响该处理腔室的上圆顶或下圆顶上的涂层。
附图说明
9.本公开内容的特征已简要概述于前,并在以下有更详尽的讨论,可通过参考实例以作了解,部分的实例绘示于所附附图中。然而,值得注意的是,所附附图仅绘示了实例,且因此不应视为限制其范围,且可允许其他等效的实例。
10.图1是根据一个实施方式的具有隔热组件的处理腔室的示意性截面图。
11.图2是根据一个实施方式的沿图1中的截面线a-a所观察的处理腔室的平面图。
12.图3是根据一个实施方式的在气体入口附近的图1所示的处理腔室的示意性截面图。
13.图4是根据一个实施方式的图1的处理腔室中所示的隔热组件的顶视图。
14.图5是根据一个实施方式的图1的处理腔室中使用的隔热组件的隔热构件的示意性顶视图。
15.图6是绘示沉积厚度的曲线图,该沉积厚度的曲线图与根据实施方式的图1的处理腔室中处理的基板的半径有关联性。
16.为便于理解,在可能的情况下,使用相同的附图标记代表图标中相同的元件。可以预期的是,一个实例中的元件与特征可有利地用于其他实例中而无需赘述。
具体实施方式
17.本文公开的是一种用于处理腔室的隔热组件。处理腔室的实例包括腔室主体,该腔室主体具有侧壁、底部和盖件,该侧壁、底部和盖件界定腔室主体的内部空间。基板支撑件和隔热组件设置在内部空间内。隔热组件包括隔热构件和环形预热构件。在基板支撑件和环形预热构件之间形成环形开口。
18.环形开口的一部分不与隔热构件重叠。环形开口的非重叠部分相对于气体入口和气体出口的位置影响内部空间内的表面上的沉积材料的涂层。更具体言之,将隔热构件定位在气体出口的远程(distally)减少沉积材料在基板支撑件上、处理腔室的上圆顶表面和下圆顶表面上的涂层。因为环形开口的位置减少材料在处理腔室的内部空间内的表面上的沉积,所以延长或改善了用于清洁处理腔室的内部空间内的表面的维护周期。上圆顶和下圆顶以及基板支撑件上沉积材料的减少使内部空间的原位(in situ)清洁循环之间的间隔更长。通过减少周期性维护并在原位清洁之间具有更长的循环,实现了更高的产量。本文公开的实例通过减少腔室内的不必要的涂层而另外实现了改良的工艺稳定度。因此,随着维护间隔之间的平均时间延长,处理腔室的拥有成本降低。
19.在本公开内容中,用语“顶部”、“底部”、“侧面”、“上方”、“下方”、“上”、“下”、“向上”、“向下”、“水平”、“垂直”及类似用语并非指绝对方向。相反地,这些用语是指相对于腔室的基本平面(例如平行于处理腔室的基板表面的平面)的方向。
20.图1是具有隔热组件160的处理腔室100的示意性截面图。处理腔室100具有腔室主体105。腔室主体105包括限定腔室主体105的外壳109的侧壁136、底部106和盖件130。上圆顶128、下圆顶114和衬里163设置在外壳109中。衬里163固定于侧壁136。腔室主体105的内部空间101由上圆顶128、下圆顶114和衬里163限定。内部空间101包括处理空间111和净化空间113。
21.穿过处理腔室100的侧壁136形成处理气体入口174。处理气体入口174也穿过衬里163形成,并提供使处理气体流入处理空间111中的路径。处理气体从气体源172流过处理气体入口174并流穿越过(across)设置在处理腔室100的内部空间101内的基板支撑件104。
22.净化气体入口164耦接至净化气体源162。净化气体入口164也穿过衬里163形成,并且提供使净化气体流入净化空间113中的路径。净化气体从净化气体源162流过净化气体入口164。
23.气体出口178穿过侧壁136设置,且衬里163与处理腔室100的内部空间101中的处理气体入口174实质相对。气体出口178使得内部空间101的处理空间111中的处理气体能够从处理腔室100中排出。内部空间101的净化空间113内的净化气体通过气体出口178从处理腔室100排出。真空源180耦接到气体出口178,以将处理气体与净化气体从处理腔室100的内部空间101排出。
24.基板支撑件104经配置在处理腔室100中的处理操作期间支撑设置在基板支撑件104的上表面110上的基板108。基板支撑件104可在处理期间旋转基板108以改善沉积在基板108上的材料的均匀性。上圆顶128设置在基板支撑件104上方,并且与基板支撑件104的上表面110和衬里163一起进一步限定处理空间111。净化空间113进一步由下圆顶114、基板支撑件104的底表面(未图示)和衬里163所限定。
25.加热模块145在处理期间向处理腔室100提供热。加热模块145可定位于基板支撑件104上方或下方。在图1所示的处理腔室100中,加热模块145设置在基板支撑件104下方。加热模块145可包括光学元件115,如透镜、光导管或其他反射和折射元件。加热模块145包括多个热源102。多个热源102设置在下圆顶114内。热源102可以是灯、发光二极管(led)和激光器任何组合。可个别地调整反射元件和折射元件的形状以将热源102发出的能量引导向基板支撑件104。来自加热模块145的热加热基板支撑件104,基板支撑件104在基板108与基板支撑件104所接触的情况下通过传导将热传递到基板108。在某些情况下,例如在基板108不接触基板支撑件104的情况下,热也可通过辐射传递。
26.隔热组件160围绕基板支撑件104。隔热组件160是与基板支撑件104同心的环形(annular)或环状(ring-like)结构。隔热组件160的外半径120小于衬里163的内半径121,使得隔热组件160装配在衬里163的内半径内。
27.隔热组件160包括环形预热构件167和隔热构件168。环形预热构件167是环形或环状的(ring shaped)。环形预热构件167的内半径132大于基板支撑件104的外半径133。隔热构件168的形状像环形圈的扇形,即弧形。隔热构件168具有限定扇形的端部的边缘(图2中的236)。环形开口134设置在环形预热构件167和基板支撑件104之间。如下面进一步详细描
述的,隔热构件168与环形开口134的一部分垂直地重叠。
28.图2是沿图1中的截面线a-a观察的处理腔室100的平面图。基板支撑件104具有基座204。在一些实例中,基座204整合于基板支撑件104或为基板支撑件104的部分。或者,基座204可以以使基座204可移动地与基板支撑件104分离(detach)的方式耦接到基板支撑件104。基座204具有由半径212限定的外圆周214。环形预热构件167的内圆周216由其内半径132限定。环形开口134由基座204的外圆周214与环形预热构件167的内圆周216之间的空间限定。环形开口134包括第一部分224和第二部分228。环形开口134的第一部分224被隔热构件168覆盖。处理气体入口174靠近环形开口134的第一部分224。环形开口134的第二部分228没有被隔热构件168覆盖。气体出口178靠近环形开口134的第二部分228。环形开口134的第二部分228是弧形孔232。弧形孔232是由基座204的外圆周、环形预热构件167的内圆周216以及隔热构件168的边缘236所限定的空间。因此,隔热构件168仅通过环形开口134的第一部分224来防止从处理空间111到净化空间113的直接视线(direct line of sight)。
29.从处理气体入口174和净化气体入口164流出的气体以大于通过气体出口178逸出的气体的速度进入处理腔室100。靠近气体出口178的净化空间113中的气体具有较低的速度和质量流率。类似地,靠近气体出口178的处理空间111中的气体具有较低的速度和质量流率。气体出口178处的较低速度和质量流率有助于减小横跨过弧形孔232上的压力变化(以下相对于图3描述)。环形开口134处的较低压力变化有利于在处理空间中的基板108上均匀地沉积材料,因为环形开口134处的压力变化的减小而减少了净化气体进入处理空间111的机会。类似地,横跨过环形开口134上的压力变化的减小而减少了处理气体进入净化空间113的机会。因此,在隔热组件160的弧形孔232处的压力变化影响横跨过基板108上的处理气体的方位角压力分布。以这种方式,弧形孔232的位置减少了在下圆顶114、上圆顶128和衬里163的内表面上不必要的材料沉积。将弧形孔232定位在气体出口178附近使得能够减少处理腔室100的内表面上不必要的沉积材料的量。
30.图3是图1中所示的气体入口附近的处理腔室100的示意性截面图。在一些实例中,基座204可以由基板支撑件104支撑。基座204可以具有凹陷部分312,凹陷部分312具有通孔320。凹陷部分312经配置在垂直方向上支撑基板108。基座204还可具有凸起部分316,该凸起部分316具有多个开口324。基板支撑件104的凸起部分316在横向方向上固持基板108,从而防止基板在水平或径向方向上滑动。每个开口324的直径大于每个通孔320的直径。凸起部分316围绕基板108。
31.在给定压力下,处理气体304从处理气体入口174进入处理空间111。通常将处理气体304在基板108上方朝向气体出口178抽出。净化气体328被加压并且通过净化气体入口164进入净化空间113。因为处理气体304气体和净化气体328在压力下进入处理腔室100,所以压力差可在环形开口134的区域中产生压力变化332。此外,因为在处理气体入口174和净化气体入口164附近,净化气体328和处理气体304的速度较高,所以在处理气体入口174和净化气体入口164附近的区域中,质量流率也增加。
32.隔热构件168垂直地定位于环形开口134上方,以减少环形开口134区域中的压力变化332。压力变化332的减小减少了净化气体328进入处理空间111的机会。因此,较低的压力变化332有助于在处理空间111中的基板108上均匀地材料沉积。
33.图4是在图1的处理腔室中使用的隔热组件160的顶视图。隔热构件168放置在环形
预热构件167上。隔热构件168的内圆周216向内延伸以覆盖环形开口134。因此,环形预热构件167的内圆周216大于隔热构件168的内半径412。环形预热构件167的外半径416也大于隔热构件168的外半径424。
34.隔热构件168具有间隙420,该间隙420暴露出环形预热构件167的一部分422。即,间隙420表示除了隔热构件168之外将用以完成圆环形形状的扇形。然而,应当理解的是,间隙420不是分段或其他形状,而仅仅是隔热构件168中的开口,因此可以等同地描述为可以通过隔热构件168中的开口而接受的任何形状。通过将暴露部分422放置在气体出口178附近,暴露部分422为从处理气体入口174流向气体出口178的气体提供了更直接的热暴露,所述气体横跨过环形预热构件167到达基板支撑件104。从处理气体入口174朝向气体出口178流动的处理气体304直接暴露于从净化气体入口164朝向气体出口178流动的净化气体328。隔热构件168的内圆周216可大于150mm,以容纳标称直径为300mm的基板。例如,对于直径为300mm的基板,内圆周216可以为约151mm至约155mm。在一些实例中,基板可以是6英寸或8英寸。因此,基板的直径可为约150mm至约300mm。间隙420可具有经选择的尺寸,该尺寸经选择以向在气体出口178处离开处理室100的气体提供所需的热暴露。
35.转到图5,图5是在图1的处理腔室100中使用的隔热组件160的隔热构件168的示意性顶视图。所示的间隙420具有尺寸502。尺寸502可具有约50mm至约180mm的宽度。间隙420的尺寸502对应于图2中所示的弧形孔232。因此,间隙420与基板半径240的比率620也对应于图6中观察到的并且在下面讨论的沉积厚度的均匀性。
36.间隙420具有第一边缘504和第二边缘506。间隙420的第一边缘504和第二边缘506对应于隔热构件168的边缘236。第一边缘504和第二边缘506大致平行于径向线508,该径向线508将间隙420对上的角度510平分(bisect)。间隙420促进处理气体304和净化气体328的均匀层流。在其他实例中,边缘504和506可具有任何期望的方向性。例如,每个边缘504或506可平行于与相应边缘504或506相交的径向线508。第一边缘504或第二边缘506可具有特征512,以防止在处理腔室100的操作期间隔热构件168的运动。在另一个实例中,在间隙420的任一侧上的边缘504和506的两个外角具有圆头(rounded)形状,即特征512。特征512的圆角是圆形的,但是可将任何期望的形状添加到边缘504或506中的任一者的角上。例如,特征512可以是任何合适角度的倒角。特征512的圆角具有约0.01mm至约1.5mm之间的曲率半径,如约0.1mm至约1.0mm之间的曲率半径,例如约0.3mm、0.4mm或0.5mm。
37.图6是表示沉积厚度的曲线图600,沉积厚度与处理腔室中处理的基板的半径有关联性。曲线图600具有表示基板半径的x轴604和表示沉积厚度的y轴608。曲线图600是从具有隔热组件160的处理腔室100中获得的,其中弧形孔232定位于气体出口178附近。整个基板108上的沉积均匀性对应于弧形孔232的位置。如前所述,减小弧形孔232处的压力变化332会增加横跨基板108上的处理气体的方位角压力分布。如图2所示,基板108具有给定的基板半径240。
38.曲线图600的横坐标(即x轴604)表示的变量x是曲线图中工艺运行数的乘数,且变量x可以大于或等于6且小于12。例如,对于x=10,x轴604上的标识符将为20、40、60等。当半径小于或等于4x时,在给定范围内观察到整个基板108上的沉积均匀性。然而,当半径大于4x时,观察到整个基板108的沉积均匀性降低。
39.当基板半径240小于或等于阈值612时,隔热组件160减少下圆顶114、上圆顶128和
衬里163的内表面上不必要的材料沉积。在一个实例中,间隙420的宽度与基板半径240的比率620为约1比约3(即1/3或0.33)。比率620也可以是6比5,或约1.2。比率620还可包括0.33至1.2之间的值,每个值都增加了沉积在基板108上的沉积材料的均匀性。然而,随着基板半径增加超过阈值612,在那些内表面上的材料沉积开始增加。
40.如以上关于图2和图3所述,在处理空间111和净化空间113之间的环形开口134处的压力变化332对应于处理腔室100内弧形孔232的位置。
41.在处理腔室100中多个工艺运行中,基板108上的沉积材料的均匀性增加。在此实例中,变量x是曲线图中工艺运行数的乘数。变量x可以大于或等于2且小于10。例如,对于x=2,标识符将读为2、4、6、8等。在x下的初始工艺运行与在5x下的工艺运行之间的平均沉积厚度差为约0.05μm。在x下的初始工艺运行与在7x下的最终工艺运行之间观察到相同的0.05μm的平均差(average difference)。从在x下的初始工艺运行到在7x下的最终工艺运行平均沉积厚度差约为0.0408。在此实例中,在x下的初始工艺运行和在7x下的最终工艺运行之间存在约0.08%的平均差。换句话说,具有弧形孔232的隔热组件160对于至少7x工艺运行能够实现高达0.08%的沉积均匀性。
42.本公开内容涉及一种用于处理腔室的隔热组件。虽然前面所述涉及特定实例,但在不背离本公开内容的基本范围下,可设计本公开内容的其他实例,且本公开内容的范围由随附权利要求书所确定。