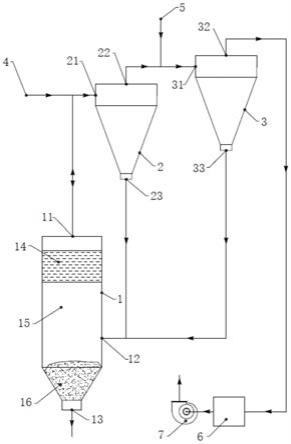
1.本发明属于非金属矿烧结技术领域,具体涉及一种节能闪速悬浮窑系统。
背景技术:2.轻烧氧化镁被广泛用于建材、化工、冶金、医药等多个领域,是生产防火板、轻质隔墙板、硫酸镁、造纸、除硫工艺、钢厂护炉溅渣等的理想材料。轻烧氧化镁的品质很大程度上依赖于所使用的轻烧装置,而轻烧装置的选用综合了矿石原料的化学组分、粒度、炸裂性,以及燃料条件、产品质量要求等因素,目前使用的轻烧装置主要有反射炉、悬浮炉和多层炉。
3.反射炉是一种简单、粗放型的轻烧装置,炉体连续作业,加料及卸料为间歇操作,是一种常见的用于轻烧菱镁矿石的轻烧装置。反射炉的入炉镁石粒度通常在100
‑
200mm之间,其不能焙烧粉料和碎料,所得产品质量不稳定,而且粉尘排放量大、不易控制,易造成污染,同时其单位产品热耗7300
‑
8300kj
·
kg
‑1,生产能耗高,自动化水平低,劳动强度大。
4.悬浮炉的结构非常适合粉料的焙烧,常用以焙烧菱镁矿浮选精矿粉,但悬浮炉的结构特点也导致了其具有原料适应性差、生产参数不易调整等缺点。一旦装置投入运行,难以对其设计参数进行调整,需要长时间的调试和改造。而且悬浮炉的入炉原料的粒度、组分发生波动,悬浮焙烧炉的产量和质量都会受影响,同时还易出现堵料、收料困难等问题。
5.多层炉又名多膛炉或耙式炉,多层炉的炉膛大小和层数多少根据产能要求和热效率确定,其煅烧物料粒度范围一般在0
‑
40mm,既可煅烧小块、又适合粉料煅烧。多层炉采用多层多点加热方式,可以严格控制焙烧温度及加热时间,保证焙烧均匀,产品质量好、活性高。但多层炉的结构复杂、建设周期长、维护专业性高、造价昂贵,限制了多层炉轻烧菱镁矿石的推广。
6.轻烧氧化镁生产过程中还需要对尾气进行脱硫和除尘处理,而烟气进入脱硫塔内的温度最佳温度在90
‑
120℃,烟气允许进入脱硫塔内的承受温度不超过180℃。一旦高出这个温度值,需要开启预喷淋,对烟气输送管道内的烟气进行降温,在烟气温度降至90
‑
120℃区间时,方能进入脱硫塔。同时,对于目前广泛使用的袋式除尘器,必须将高温气体冷却至滤料能承受的温度以下,一般应控制在120℃以下,若采用耐高温滤材则需要考虑成本与寿命。高温烟气进行降温的过程中,被喷淋的烟气热量会浪费掉,并且会消耗大量水资源。可见尾气温度过高不仅会造成能源浪费,同时也会阻碍脱硫除尘设备的运行。
技术实现要素:7.本发明针对以上问题的提出,而研究设计一种节能闪速悬浮窑系统,来解决现有氧化镁轻烧装置适用的原料粒径范围小、能耗高、污染高等问题。本发明采用的技术手段如下:
8.一种节能闪速悬浮窑系统,包括第一投料点、窑炉和第一气固分离器,所述窑炉包括第一进料口、第二进料口、阻尼段、烧成段、反射段和熟料出口,所述阻尼段、烧成段和反
射段沿所述第一进料口至所述熟料出口依次设置,所述阻尼段包括阻尼单元和流道,原料从流道穿过阻尼段,所述烧成段与所述第二进料口相通,所述第一投料点与所述第一进料口相连,所述第一气固分离器包括第一进气口、第一出气口和第一出料口,所述第一进气口与所述第一进料口相连,所述第一出料口与所述第二进料口相连。
9.优选地,所述第一投料点、第一进料口和第一气固分离器之间通过三通管道连接。
10.优选地,还包括第二气固分离器,所述第二气固分离器包括第二进气口、第二出气口和第二出料口,所述第二进气口与所述第一出气口相连,所述第二出料口与所述第二进料口相连。
11.优选地,还包括第二投料点,所述第二投料点与所述第二进气口相连。
12.优选地,还包括引风机,所述第二出气口与所述引风机相连,所述第一气固分离器和第二气固分离器均为旋风分离器。
13.优选地,所述第二气固分离器和引风机之间设有脱硫除尘单元,所述第二出气口与所述脱硫除尘单元相连,所述脱硫除尘单元与所述引风机的进口相连。
14.优选地,所述第一投料点的原料粒度为50mm以下,所述第二投料点的原料粒度为1mm以下。
15.与现有技术比较,本发明所述的一种节能闪速悬浮窑系统的有益效果为:
16.1、本发明中的原料通过窑炉阻尼段时,在阻尼段中阻尼单元的阻挡下延长了预热时间,使得原料预热更充分,能对较大粒度的原料进行彻底预热;该窑炉系统既可煅烧小块原料,又适合粉料煅烧,原料粒度适用范围广。
17.2、本发明中利用尾气余热对原料进行预热,减少窑炉负荷,避免尾气热量的浪费,经换热后的较低温尾气可以直接进入脱硫除尘单元,可去掉尾气强制冷却环节,简化生产工艺;并且窑炉系统完全封闭,尾气可集中收集处理,减轻了环保压力。
18.3、本发明中由于窑炉加料方向与窑炉尾气排出方向相反,阻尼段、烧成段内的细粒状或粉状物料呈悬浮状态,其传热传质速率高,并且有阻尼单元的作用,炉内气体处于激烈的紊流状态,使得物料受热更均匀,原料分解效率高。
19.4、本发明提供的节能闪速悬浮窑系统具有能耗低、污染小、同时适合粉料块料焙烧、产品质量稳定、结构简单占地小、建设快、一次性投入少、经济效益明显的优点。
附图说明
20.图1是本发明的整体流程示意图。
21.图2是本发明中呈条状的阻尼单元的结构示意图。
22.图3是图2中的k向视图。
23.图4是本发明中呈球状的阻尼单元的结构示意图。
24.图5是本发明中呈块状的阻尼单元的结构示意图。
25.图中,1、窑炉;2、第一气固分离器;3、第二气固分离器;4、第一投料点;5、第二投料点;6、脱硫除尘单元;7、引风机;11、第一进料口;12、第二进料口;13、熟料出口;14、阻尼段;15、烧成段;16、反射段;21、第一进气口;22、第一出气口;23、第一出料口;31、第二进气口;32、第二出气口;33、第二出料口;141、阻尼单元;142、流道。
具体实施方式
26.如图1所示,一种节能闪速悬浮窑系统,包括窑炉1、第一气固分离器2和第一投料点4。窑炉1包括位于窑炉1上部的第一进料口11、位于窑炉1侧面的第二进料口12以及位于窑炉1下部的熟料出口13,窑炉1内部沿第一进料口11至熟料出口13依次分为阻尼段14、烧成段15和反射段16。即阻尼段14位于第一进料口11下部,烧成段15位于阻尼段14下部,反射段16位于烧成段15下部,熟料出口13位于反射段16下部。烧成段15与第二进料口12相通,烧成段15上设有燃烧混合气的进口,原料进入烧成段15后与其中的燃烧气体充分接触受热分解,之后落入反射段16进一步分解。如图2
‑
5所示,阻尼段14包括阻尼单元141和多个流道142,阻尼单元141以填料的形式填充在窑炉1内部,原料从流道142穿过阻尼段14。一方面,阻尼单元141能阻止原料过快通过阻尼段14,延缓原料通过阻尼段14的时间,以此延长原料预热时间;另一方面,由于原料需要在流道142中穿过,而流道142的孔径远小于窑炉1直径,相当于缩小了原料与窑炉1炉壁的距离,利于窑炉1传热,提高原料预热效率,便于对较大粒度的原料彻底预热。流道142可以由多个阻尼单元141之间的间隙构成,也可以由阻尼单元141自身提供通道,只要满足能阻挡原料、延长原料预热时间即可。具体的,阻尼单元141可以为如图2、3所示的条形格栅状,其中阻尼单元141错格排列,形成的流道142曲折,也可以为如图4、5所示的玲珑球状、块状,既不妨碍原料通过,又能对原料起到阻挡作用。第一投料点4与第一进料口11相连,通过第一投料点4向窑炉1内投入原料。第一气固分离器2包括第一进气口21、第一出气口22和第一出料口23,第一进气口21与第一进料口11相连,第一出料口23与第二进料口12相连。窑炉1内的尾气通过第一进料口11和第一进气口21进入第一气固分离器2内,由第一气固分离器2进行气固分离,尾气中携带的固体粉末被分离后经第一出料口23和第二进料口12返回窑炉1内回收利用,充分利用资源。
27.第一投料点4、第一进料口11和第一气固分离器2的第一进气口21之间通过三通管道连接。原料从第一投料点4由上而下进入第一进料口11的过程中,同时会被第一进料口11排出的由下而上的高温尾气反吹,此时原料中的较大颗粒料能继续下落至窑炉1内,而原料中的较小颗粒料会随尾气进入第一气固分离器2内。在上述原料与尾气的逆向运动过程中,原料中的较大颗粒料(即块料)会与尾气进行热交换,块料先经尾气进行初始预热,然后进入阻尼段14再次预热,使得原料预热充分,并且回收利用了高温尾气的热量;原料中的较小颗粒料(即粉料)随尾气进入第一气固分离器2中,经气固分离后再返回窑炉1,能充分预热、回收粉料,并且避免了粉料依靠重力下落时容易沉积在阻尼单元141和流道142内的问题。
28.还包括第二气固分离器3,第二气固分离器3包括第二进气口31、第二出气口32和第二出料口33,第二进气口31与第一气固分离器2的第一出气口22相连,第二出料口33与第二进料口12相连。第一气固分离器2内排出的气体中可能含有少量的固体原料,可通过第二气固分离器3进行更充分的回收,保证原料利用率。
29.还包括第二投料点5,第二投料点5与第二气固分离器3的第二进气口31相连,第一出气口22、第二投料点5和第二进气口31之间通过三通管道连接。第二投料点5投入的原料为粉料,原料粉料会随第一出气口22排出的较高温气体进入第二气固分离器3内,粉料经第二气固分离器3分离后,由第二进料口12进入窑炉1受热分解。在上述过程中,粉料会与该较高温气体进行热交换,以此达到预热粉料、回收热量的目的。
30.还包括引风机7,第二出气口32与引风机7的进口相连,由引风机7提供负压风,能
提高窑炉1尾气的排出速度和粉料的分离效率。第一气固分离器2和第二气固分离器3均为旋风分离器,旋风分离器能满足粉料的分离需求,并且其来源广泛、成本较低、管理维修方便,利于实际应用。
31.第二气固分离器2和引风机7之间设有脱硫除尘单元6,脱硫除尘单元6的进口与第二气固分离器3的第二出气口32相连,脱硫除尘单元6的出口与引风机7的进气端相连。设置脱硫除尘单元6,尾气可集中收集处理,减轻了环保压力。
32.第一投料点4的原料的许用粒度为50mm以下,包含小块料与粉体料,可以通过第一进料口11向窑炉1内投入块料或者粉料。第二投料点5的原料粒度为1mm以下,适于投入粉料,能保证粉料被有效预热。本窑炉系统可通过第一投料点4和第二投料点5分别投料,适用的原料粒径范围广。
33.本发明的具体工作原理为:窑炉1由引风机7提供负压,其高温尾气通过第一进料口11排出窑炉1,并依次通过第一进气口21、第一出气口22、第二进气口31、第二出气口32、脱硫除尘单元6、引风机7排入大气。原料由第一投料点4投入后,其中的块料从第一进料口11进入窑炉1,通过阻尼段14的流道142时充分预热,并在阻尼段14中阻尼单元141的阻挡下延长预热时间。经过阻尼层14的原料,有部分块料已经开始分解,再进入到烧成区15后,可以迅速地与燃烧气体接触并吸收热量达到煅烧的温度,进而使得原料可以快速且充分的分解。烧成段15中烧结完成的和未烧结完成的原料继续下落进入反射段16,进一步受热分解,使得烧结完全,达到均质效果,分解后的产品料经熟料出口13排出。而由第一投料点4投入的原料中的较小粒径粉体,一部分直接落入窑炉1内分解,另一部分随第一进料口11排出的高温尾气进入第一进气口21,在第一气固分离器2中充分混合换热分离后,经第一出料口23、第二进料口12进入窑炉1的烧成段15、反射段16受热分解。第一出气口22排出的尾气通过第二进气口31进入第二气固分离器3,途中与第二投料点5投入的粉料混合,在第二气固分离器3内充分混合,完成换热后从第二出料口33排出,并通过第二进料口12进入窑炉1的烧成段15、反射段16受热分解。通过上述窑炉系统,在第一加料点加入块料或粉料、在第二加料点加入粉料均可完成焙烧,最后产品料在熟料出口13处排出,经两次换热分离后,尾气温度可降至100℃
‑
120℃。
34.综合现有轻烧氧化镁领域的反射炉、悬浮炉和多层炉存在的结构与经济效益上存在的缺点,本发明提供一种具有阻尼填料层的轻烧氧化镁窑炉及其余热回收系统,具有能耗低、污染小、同时适合粉料块料焙烧、产品质量稳定、结构简单占地小、建设快、一次性投入少、经济效益明显的优点。具体的,现有反射窑入炉原料粒度通常在100
‑
200mm、悬浮炉通常选用原料为≤200μm的浮选精矿粉,对比反射窑、悬浮炉的入料特点,本发明具有原料适应性强、既可煅烧小块、又适合粉料煅烧的优点。在煅烧方式的设计上,通过原料与尾气对流,使得阻尼段14、烧成段15内的细粒状或粉状物料呈悬浮状态,其对流传热传质速率比物料在固定床和沸腾床中大得多。并且在原料和阻尼单元141的干扰下,使得炉内气体处于激烈的紊流状态,物料受热更均匀,充分的利用了悬浮态利于颗粒粉体的煅烧、固定床适合块料煅烧的特点。原料经预热后在烧成段15与燃烧气体充分接触受热分解,并进入反射仓内在吸收热气和炉体辐射热的过程中继续分解,利于快速、稳定、有效的生产轻烧氧化镁产品。另外利用尾气余热对原料进行预热,减少窑炉负荷,避免尾气热量的浪费,经换热后的较低温尾气可以直接进入脱硫除尘单元6,无需尾气强制冷却环节,简化生产工艺;并且窑
炉系统完全封闭,尾气可集中收集处理,减轻了环保压力。
35.以上所述的实施例仅仅是对本发明的优选实施方式进行描述,并非对本发明的范围进行限定,在不脱离本发明设计精神的前提下,本领域普通技术人员对本发明的技术方案做出的各种变形和改进,均应落入本发明权利要求书确定的保护范围内。