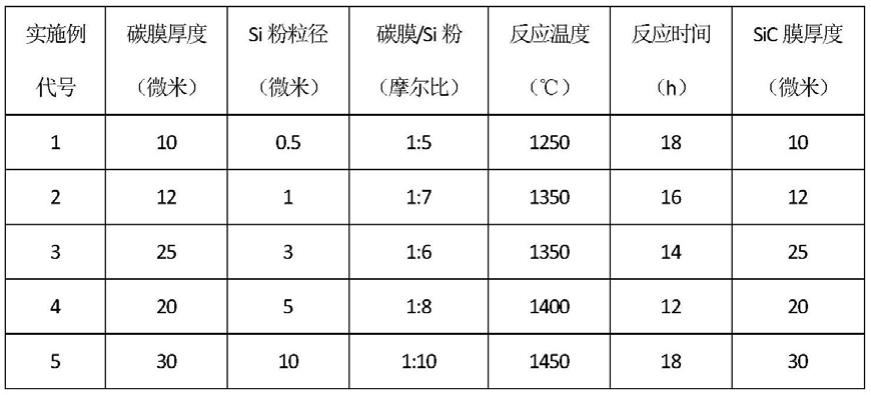
一种sic/zrc层状块体复合材料及其制备方法
技术领域
1.本发明属于超高温陶瓷材料领域,具体涉及一种sic/zrc层状块体复合材料及其制备方法。
背景技术:2.碳化锆陶瓷具有熔点高、硬度大、化学稳定性好、导热性能好、高弹性模量、适中的热膨胀系数、良好的抗热震性及抗烧蚀性能等优点,其作为一种超高温结构材料,已被广泛用于超高温环境下的防热材料和耐磨材料的表面涂层等,但脆性大这一致命弱点使其应用受到一定限制。
3.为克服碳化锆陶瓷材料脆性大的弱点,就必须对其进行增韧。一种有效的途径是利用层状复合材料的强界面残余应力增韧方式。即将碳化锆与其他陶瓷材料(如碳化硅)复合制备成层状块体材料,利用两者之间物理性能的差异,在界面处引入残余应力,当裂纹扩展至界面处时,裂纹会发生偏转,从而延长了裂纹扩展路径,因此提高了该材料的韧性。目前,研究者主要采用流延成型工艺来制备层状碳化硅/碳化锆陶瓷复合材料,如申请号为201410666300.3的中国专利“一种层状碳化硅/碳化锆超高温陶瓷的制备方法”、文献“fabrication and crack propagation behaviour of laminated zrc
‑
sic composites”(materials science&engineering a,2015,647:1
‑
6)等。
4.然而,流延成型工艺不仅需要复杂的成型设备或繁杂的料浆配置过程,而且当层厚较小时,单层陶瓷素坯的微观均匀度很难控制。此外,单层陶瓷素坯通常涉及排胶过程,这不仅需要较长的时间,从而无法实现层状块体复合材料的快速烧结,而且陶瓷素坯中的有机物等挥发后会产生气孔,使得致密度降低,从而限制性能的提高。因此开发工艺简单、成本低、层厚均匀且无需排胶过程的陶瓷基层状复合材料的快速烧结制备技术具有非常重要的意义。
技术实现要素:5.针对现有制备技术存在的不足,本发明的目的在于提供一种工艺简单,成本低廉、不仅能够解决薄层陶瓷素坯存在的均匀性差等问题,而且无需后续冗长排胶工艺的sic/zrc层状复合陶瓷材料及其制备方法,该方法可实现sic/zrc层状复合陶瓷材料的快速烧结,且所制备的材料有高的致密度及优异的性能。
6.为达到上述目的,本发明的制备方法如下:
7.s100,将碳膜浸入硝酸溶液中超声振荡后冲洗干净,然后烘干,得到预处理的碳膜;
8.s200,通过熔盐反应将预处理的碳膜转变为sic膜;
9.s300,通过熔盐反应将预处理的碳膜转变为zrc膜;
10.s400,将sic膜与zrc膜按一定顺序交替堆叠后放入石墨模具内,并预压成型;
11.s500,将装有预压成型试样的石墨模具放入放电等离子烧结装置中,首先抽真空
至0.1pa以下,随后利用脉冲电流对预压成型试样进行60s的激发活化,并在烧结温度为1800~2000℃、轴向压力为40~60mpa的条件下,进行快速烧结并保温5min,随炉冷却后获得sic/zrc层状块体复合材料。
12.所述碳膜为石墨膜或石墨纸。
13.所述碳膜的厚度为10~30微米。
14.所述的s200具体包括以下步骤:
15.s201,按碳膜:si粉=1:(5~10)的摩尔比取si粉;
16.s202,按氯化钠:氟化钠=4:1的质量比,取氯化钠和氟化钠然后将其混合均匀得混合粉;
17.s203,按质量比为1:10,将si粉和混合粉研磨并混合均匀,得到反应粉;
18.s204,将碳膜埋入反应粉内,然后一起放入坩埚中;
19.s205,将坩埚放入真空气氛炉中,在流动氩气保护下于1250~1450℃进行熔盐反应;反应完成后随炉冷却至室温,并用热水煮掉盐,烘干后得到sic膜。
20.所述si粉的粒径≤10微米;s205中,所述熔盐反应时间为12~18小时。
21.所述s300具体包括以下步骤:
22.s301,按碳膜:zr粉=1:(5~10)的摩尔比取zr粉;
23.s302,按氯化钠:氟化钠=10:1的质量比,取氯化钠和氟化钠然后将其混合均匀得到混合粉;
24.s303,按质量比为1:10,将zr粉和混合粉研磨并混合均匀,得到反应粉;
25.s304,将碳膜埋入反应粉内,然后一起放入坩埚中;
26.s305,将坩埚放入真空气氛炉中,在流动氩气保护下于1000~1300℃进行熔盐反应;反应完成后随炉冷却至室温,并用热水煮掉盐,烘干后得到zrc膜。
27.所述zr粉的粒径≤10微米;s305中,所述熔盐反应时间为12~18小时。
28.所述s400中,将单一sic膜与zrc膜裁剪成直径相同的圆片,并按照“m个sic膜圆片—n个zrc膜圆片—m个sic膜圆片—n个zrc膜圆片
……”
的顺序逐层交替堆叠(m和n均≥1)。其中,单一sic和zrc膜的厚度为10~30微米。
29.所述s500中,室温至1000℃的升温速率为150~250℃/min,1000℃至最终烧结温度的升温速率为100~140℃/min。
30.按照以上制备方法制备的sic/zrc层状块体复合材料,sic和zrc在复合材料中逐层交替分布,并呈完美取向排列。
31.与现有技术相比,本发明具有如下优点:
32.本发明利用熔盐反应将碳膜直接转变为sic膜或zrc膜,由于不需要繁杂的浆料配制过程或专用的成型设备等,因此制备工艺简单、成本低。另外,通过控制碳膜的厚度,可方便对单一sic膜或zrc膜的厚度进行调控,因此非常适合制备微观结构均匀的单层陶瓷片,特别是较薄的陶瓷片。此外,本发明无需冗长的排胶工艺,因此可实现层状陶瓷复合材料的快速烧结,且制备出的材料致密度高,性能优异。
33.本发明所制备的复合材料由交替分布且互相平行的sic层和zrc层组成,通过控制单一sic膜或zrc膜的厚度及堆叠过程中单一sic膜或zrc膜的个数,可方便对复合材料中sic或zrc的体积分数进行调控;其制备方法由
①
碳膜的预处理、
②
通过熔盐反应将碳膜转
化为sic膜、
③
通过熔盐反应将碳膜转化为zrc膜、
④
sic膜与zrc膜的逐层堆叠及
⑤
sic/zrc层状块体复合材料的放电等离子烧结五个步骤组成。本发明工艺简单,成本低廉,制备出的材料不仅微观结构均匀,致密度高,且各组元的体积分数可调。另外,本发明也适合其他碳化物膜的制备,因此大大扩展了碳化物系层状复合材料的快速烧结制备方法。
具体实施方式
34.本发明的技术方案是通过下述工艺步骤而得以实现的:
35.s100,将碳膜浸入到体积浓度为30~50%的硝酸溶液中并超声振荡0.5~2h,取出后用酒精冲洗干净,然后放入真空烘箱中,在110~130℃下烘干0.5~2h,得到预处理的碳膜。
36.优选地,所述的碳膜采用厚度为10~30微米的石墨膜或石墨纸。
37.s200,通过熔盐反应将预处理的碳膜转变为sic膜。
38.具体地,通过熔盐反应将预处理的碳膜转变为sic膜的工艺,包括以下步骤:
39.s201,按碳膜:si粉=1:(5~10)的摩尔比取粒径≤10微米的si粉;
40.s202,按氯化钠:氟化钠=4:1的质量比,取氯化钠和氟化钠然后将其混合均匀得混合粉;
41.s203,按质量比为1:10,将si粉和混合粉研磨并混合均匀,得到反应粉;
42.s204,将碳膜埋入反应粉内,然后一起放入坩埚中;
43.s205,将坩埚放入真空气氛炉中,在流动氩气保护下于1250~1450℃进行熔盐反应12~18小时;反应完成后随炉冷却至室温,并用热水煮掉盐,烘干后得到sic膜。
44.s300,通过熔盐反应将预处理的碳膜转变为zrc膜。
45.具体地,通过熔盐反应将预处理的碳膜转变为zrc膜的工艺,包括以下步骤:
46.s301,按碳膜:zr粉=1:(5~10)的摩尔比取粒径≤10微米的zr粉;
47.s302,按氯化钠:氟化钠=10:1的质量比,取氯化钠和氟化钠然后将其混合均匀得到混合粉;
48.s303,按质量比为1:10,将zr粉和混合粉研磨并混合均匀,得到反应粉;
49.s304,将碳膜埋入反应粉内,然后一起放入坩埚中;
50.s305,将坩埚放入真空气氛炉中,在流动氩气保护下于1000~1300℃进行熔盐反应12~18小时;反应完成后随炉冷却至室温,并用热水煮掉盐,烘干后得到zrc膜。
51.s400,将单一sic膜与zrc膜裁剪成直径相同的圆片,并按照“m个sic膜圆片—n个zrc膜圆片—m个sic膜圆片—n个zrc膜圆片
……”
(m和n均≥1)的顺序逐层堆叠进石墨模具内,并预压成型。
52.s500,将装有预压成型试样的石墨模具放入放电等离子烧结装置中,首先抽真空至0.1pa以下,随后利用脉冲电流对预压成型试样进行60s的激发活化,并在烧结温度为1800~2000℃、轴向压力为40~60mpa的条件下,进行快速烧结并保温5min,随炉冷却后获得sic/zrc层状块体复合材料。其中,室温至1000℃的升温速率为150~250℃/min,1000℃至最终烧结温度的升温速率为100~140℃/min。
53.本发明所制备的sic/zrc层状块体复合材料,sic和zrc在复合材料中的体积分数可调,且两者逐层交替分布,并呈完美取向排列。其中,单一sic和zrc膜的厚度为10~30微
米。
54.实施例1
55.s100,将表1所示的碳膜浸入到体积浓度为40%的硝酸溶液中并超声振荡1h,取出后用酒精冲洗干净,然后放入真空烘箱中,在120℃下烘干1h,得到预处理的碳膜。
56.s200,通过熔盐反应将一些预处理的碳膜转变为sic膜,具体包括下述步骤:
57.(1)按表1所示的粒径及碳膜与si粉的摩尔比,称取适量的si粉;
58.(2)按氯化钠:氟化钠=4:1的质量比,称取氯化钠和氟化钠的混合粉;
59.(3)按质量比为1:10,将si粉和混合粉倒入研钵中,研磨并混合均匀,得到反应粉;
60.(4)将碳膜埋入反应粉内,然后一起放入石墨坩埚中;
61.(5)将石墨坩埚放入真空气氛炉中,在流动氩气保护下按照表1所示的条件进行熔盐反应。反应完成后随炉冷却至室温,并用热水煮掉盐,烘干后得到sic膜。
62.s300,通过熔盐反应将一些预处理的碳膜转变为zrc膜,具体包括下述步骤:
63.(1)按照表2所示的粒径及碳膜与zr粉的摩尔比,称取适量的zr粉;
64.(2)按氯化钠:氟化钠=10:1的质量比,称取氯化钠和氟化钠的混合粉;
65.(3)按质量比为1:10,将zr粉和混合粉倒入研钵中,研磨并混合均匀,得到反应粉;
66.(4)将碳膜埋入反应粉内,然后一起放入石墨坩埚中;
67.(5)将石墨坩埚放入真空气氛炉中,在流动氩气保护下按照表2所示的条件进行熔盐反应。反应完成后随炉冷却至室温,并用热水煮掉盐,烘干后得到zrc膜。
68.s400,按表3所示,首先将单一sic膜与zrc膜裁剪成直径相同的圆片,然后按照“m个sic膜圆片—n个zrc膜圆片—m个sic膜圆片—n个zrc膜圆片
……”
的顺序逐层堆叠进石墨模具内,并预压成型。
69.s500,将装有预压成型试样的石墨模具放入放电等离子烧结炉中,首先抽真空至0.1pa以下,并利用脉冲电流对预压成型试样进行60s的激发活化,然后按照表3所示的条件进行烧结,保温5min后随炉冷却,获得sic/zrc层状块体复合材料。
70.表1 sic膜的制备工艺
[0071][0072]
表2 zrc膜的制备工艺
[0073][0074]
表3复合材料组成及工艺参数
[0075][0076]
实施例2
[0077]
上述一种sic/zrc层状块体复合材料的制备方法,包括下述步骤:
[0078]
s100,将表1所示的碳膜浸入到体积浓度为30%的硝酸溶液中并超声振荡0.5h,取出后用酒精冲洗干净,然后放入真空烘箱中,在110℃下烘干2h,得到预处理的碳膜。
[0079]
s200,通过熔盐反应将一些预处理的碳膜转变为sic膜,具体包括下述步骤:
[0080]
(1)按表1所示的粒径及碳膜与si粉的摩尔比,称取适量的si粉;
[0081]
(2)按氯化钠:氟化钠=4:1的质量比,称取氯化钠和氟化钠的混合粉;
[0082]
(3)按质量比为1:10,将si粉和混合粉倒入研钵中,研磨并混合均匀,得到反应粉;
[0083]
(4)将碳膜埋入反应粉内,然后一起放入石墨坩埚中;
[0084]
(5)将石墨坩埚放入真空气氛炉中,在流动氩气保护下按照表1所示的条件进行熔盐反应。反应完成后随炉冷却至室温,并用热水煮掉盐,烘干后得到sic膜。
[0085]
s300,通过熔盐反应将一些预处理的碳膜转变为zrc膜,具体包括下述步骤:
[0086]
(1)按照表2所示的粒径及碳膜与zr粉的摩尔比,称取适量的zr粉;
[0087]
(2)按氯化钠:氟化钠=10:1的质量比,称取氯化钠和氟化钠的混合粉;
[0088]
(3)按质量比为1:10,将zr粉和混合粉倒入研钵中,研磨并混合均匀,得到反应粉;
[0089]
(4)将碳膜埋入反应粉内,然后一起放入石墨坩埚中;
[0090]
(5)将石墨坩埚放入真空气氛炉中,在流动氩气保护下按照表2所示的条件进行熔盐反应。反应完成后随炉冷却至室温,并用热水煮掉盐,烘干后得到zrc膜。
[0091]
s400,按表3所示,将单一sic膜与zrc膜裁剪成直径相同的圆片,然后按照“m个sic膜圆片—n个zrc膜圆片—m个sic膜圆片—n个zrc膜圆片
……”
的顺序逐层堆叠进石墨模具内,并预压成型。
[0092]
s500,将装有预压成型试样的石墨模具放入放电等离子烧结炉中,首先抽真空至0.1pa以下,并利用脉冲电流对预压成型试样进行60s的激发活化,然后按照表3所示的条件
进行烧结,保温5min后随炉冷却,获得sic/zrc层状块体复合材料。
[0093]
实施例3
[0094]
上述一种sic/zrc层状块体复合材料的制备方法,包括下述步骤:
[0095]
s100,将表1所示的碳膜浸入到体积浓度为50%的硝酸溶液中并超声振荡2h,取出后用酒精冲洗干净,然后放入真空烘箱中,在130℃下烘干0.5h,得到预处理的碳膜。
[0096]
s200,通过熔盐反应将一些预处理的碳膜转变为sic膜,具体包括下述步骤:
[0097]
(1)按表1所示的粒径及碳膜与si粉的摩尔比,称取适量的si粉;
[0098]
(2)按氯化钠:氟化钠=4:1的质量比,称取氯化钠和氟化钠的混合粉;
[0099]
(3)按质量比为1:10,将si粉和混合粉倒入研钵中,研磨并混合均匀,得到反应粉;
[0100]
(4)将碳膜埋入反应粉内,然后一起放入石墨坩埚中;
[0101]
(5)将石墨坩埚放入真空气氛炉中,在流动氩气保护下按照表1所示的条件进行熔盐反应。反应完成后随炉冷却至室温,并用热水煮掉盐,烘干后得到sic膜。
[0102]
s300,通过熔盐反应将一些预处理的碳膜转变为zrc膜,具体包括下述步骤:
[0103]
(1)按照表2所示的粒径及碳膜与zr粉的摩尔比,称取适量的zr粉;
[0104]
(2)按氯化钠:氟化钠=10:1的质量比,称取氯化钠和氟化钠的混合粉;
[0105]
(3)按质量比为1:10,将zr粉和混合粉倒入研钵中,研磨并混合均匀,得到反应粉;
[0106]
(4)将碳膜埋入反应粉内,然后一起放入石墨坩埚中;
[0107]
(5)将石墨坩埚放入真空气氛炉中,在流动氩气保护下按照表2所示的条件进行熔盐反应。反应完成后随炉冷却至室温,并用热水煮掉盐,烘干后得到zrc膜。
[0108]
s400,按表3所示,将单一sic膜与zrc膜裁剪成直径相同的圆片,然后按照“m个sic膜圆片—n个zrc膜圆片—m个sic膜圆片—n个zrc膜圆片
……”
的顺序逐层堆叠进石墨模具内,并预压成型。
[0109]
s500,将装有预压成型试样的石墨模具放入放电等离子烧结炉中,首先抽真空至0.1pa以下,并利用脉冲电流对预压成型试样进行60s的激发活化,然后按照表3所示的条件进行烧结,保温5min后随炉冷却,获得sic/zrc层状块体复合材料。
[0110]
实施例4
[0111]
实施例4中的按表1所示的粒径及碳膜与si粉的摩尔比,按照表2所示的粒径及碳膜与zr粉的摩尔比,称取适量的zr粉;按表3所示,将sic膜与zrc膜裁剪成直径相同的圆片,其他工艺参数和实施例相同。
[0112]
实施例5
[0113]
实施例5中的按表1所示的粒径及碳膜与si粉的摩尔比,按照表2所示的粒径及碳膜与zr粉的摩尔比,称取适量的zr粉;按表3所示,将sic膜与zrc膜裁剪成直径相同的圆片,其他工艺参数和实施例相同。
[0114]
综上所述,本发明制备的sic/zrc层状块体复合材料由交替分布且互相平行的sic层和zrc层组成,作为一种高性能超高温结构材料,将可以广泛用于能源、机械、电子、航空航天等领域。