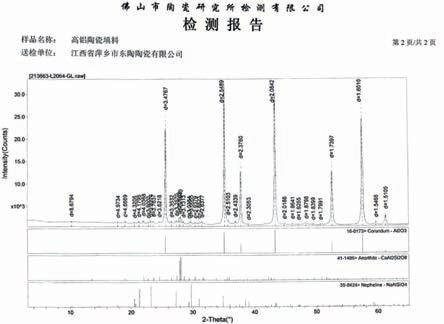
al2o3的转相所致的激烈、快速的相变和很大的收缩,而造成高铝陶瓷填料产品开裂甚至碎片化!即使不开裂,也会造成高铝陶瓷内部很大的残余应力,使高铝陶瓷填料的抗压碎力变差!此外,γ-al2o3的耐腐蚀性、机械强度、耐温性能等不够好,如残存在于高铝瓷球填料之瓷体中,将不利于化工生产的长期、稳定的使用。所以,一直以来所有的高铝陶瓷都必须用煅烧氧化铝为原料。
7.不过,煅烧氧化铝粉都是由工业氧化铝(并添加少量硼酸、nh4f等卤素盐)经1450~1550
°
c长时间煅烧制得的,象热压铸工艺制备电子陶瓷和水阀片的工艺,就需要采用经过1500℃以上、数十小时煅烧的低碱特级氧化铝粉。此煅烧过程需要消耗大量燃料,并产生大量的碳排放!不能适应全球可持续发展的趋势和我国碳达峰的目标要求!同时,这样的煅烧历程,也导致产品价格大幅提升——煅烧氧化铝的吨价是工业氧化铝吨价的1.5~2倍!造成高铝陶瓷填料产业成本高,效益低,竞争力弱。
8.当前,人类社会正面临着可持续发展的客观需要,各国都在拟定2030年前碳达峰行动方案,以履行推动构建人类命运共同体的责任担当和实现可持续发展的庄严承诺,这意味着全球将进行广泛而深刻的经济社会变革,并为此付出艰苦努力和实实在在的行动。陶瓷产业作为一个高耗能、高co2排放的产业,也不能置之度外,自身急需做出重大技术变革和创新,以适应新形势下紧迫、客观的要求。
9.有鉴于上述客观原因,必须适时地对高铝陶瓷填料的生产方式进行技术变革和创新——以工业氧化铝(γ-al2o3)来直接生产高铝陶瓷填料。
技术实现要素:10.鉴于节能减排和碳达峰的迫切、客观的需要,以工业氧化铝(γ-al2o3)来直接生产高铝陶瓷填料成为必然!为此,必须首先解决γ-al2o3→
ɑ-al2o3的转相所致的激烈、快速的相变和很大的收缩,而造成高铝陶瓷填料产品开裂甚至碎片化的问题。
11.针对此问题,本发明的目的是提供一种用γ氧化铝制备的高铝陶瓷填料及其方法。
12.本发明主要采用以下原料并创新配方和工艺,以解决上述问题:(一)主要原料:1、工业γ氧化铝 是一种白色松散的结晶粉末,颗粒由许多粒径小于0.1um的γ-al2o3晶体组成的多孔球形聚集体,其孔隙率约达30%,平均粒径40~70um,其中有的大到100um以上,也有小到几个微米的细颗粒。每个聚集体可含γ-al2o3细晶多达106个。工业γ氧化铝是铝厂最大宗的产品,2020年全球氧化铝产量总计1.34亿吨。工业氧化铝大多用作为电解铝厂的原料,一小部分用作为生产煅烧氧化铝(耐火材料和陶瓷生产用)的原料。本发明以一级工业氧化铝为主要原料,其主要指标要求:氧化铝含量大于98%,氧化钠小于0.5%,灼减小于1%。为了实现资源节约,废物再生利用,发展循环经济,也可以以双氧水企业大量排放的、原用于起吸附作用的氧化铝小球,以及氧化铝质催化剂载体为原料,但必须预先于1200℃以上煅烧,以便氧化分解其中所吸附的有机物和排出水分,且成分同样满足以下要求:氧化铝含量大于98%,氧化钠小于0.5%,灼减小于1%;2、球粘土 是一种含氧化铝和氧化硅的天然纳米矿物,是生产耐火材料最常用的烧结助剂!许多难以烧结的耐火材料,添加少量球粘土后,可以促进耐火材料烧结,提高耐
火材料致密性和机械强度,而又不降低耐火度和荷重软化温度。本发明采用球粘土作为原料,一来可以确保生产工艺性能——提高坯料泥浆的悬浮性,防止高比重的氧化铝因沉降而导致坯料成分不均匀,同时其强有力的粘结性和可塑性,可有效提高坯体的成型性能和干燥强度(实际效果优于著名的苏州高岭土);二来可以促进高铝陶瓷烧结,提高产品的致密度和机械强度。球粘土烧成时可形成莫来石和非晶体活性二氧化硅,后者很容易与氧化铝在1200℃时生成莫来石(参考文献:华南工学院、南京化工学院、武汉建材学院合编《陶瓷工艺学》中国建筑工业出版社1981年第一版,306页);3、硼酸盐矿物或人工合成的含硼物 包括硬硼钙石、硼鎂石(氟硼镁石)、硼钙镁石,以及人工合成的(焦)硼酸钡、硼酸钙、硼酸盐玻璃(熔块粉),它们都含有b2o3;4、活性纳米二氧化硅 包括硅溶胶、白炭黑、铁合金生产的副产物——硅灰,要求纯度大于97%,比表面积大于20m2/g;5、白云石、透辉石、透闪石 为同时含有氧化钙和氧化镁的天然矿物,比单一的、只含氧化镁或氧化钙的矿物(如,滑石、方解石)助熔效果更好!6、煅烧氧化铝为主晶相系刚玉(
ɑ-al2o3)的氧化铝粉,其中
ɑ-al2o3晶相含量大于90%,氧化铝含量大于99%。
13.(二)本发明的创新点在于:
①
以主晶相为γ
‑ꢀ
al2o3的氧化铝粉为主体原料,该原料无需经过煅烧转变为
ɑ
‑ꢀ
al2o3,而是直接以γ
‑ꢀ
al2o3作为原料来使用,以制备惰性高铝陶瓷填料,其用量达83~94wt%;
②
煅烧氧化铝粉可以完全不用,如使用,则也只需要少量,其用量为≤7wt%;
③
采用硼酸盐矿物或合成的硼酸盐化合物2~5wt%,以促进瓷体中
ɑ
‑ꢀ
al2o3晶相形成,并有效降低烧成温度;
④
添加纳米二氧化硅1~4wt%,减少γ
‑ꢀ
al2o3→
ɑ
‑ꢀ
al2o3转变时的开裂缺陷,提高耐高温性能和化学稳定性;
⑤
在1100℃时施加低温保温程序,为γ-al2o3→
ɑ
‑ꢀ
al2o3转变提供预备期,既提高了
ɑ
‑ꢀ
al2o3相转化率,又降低了开裂缺陷。
14.综合应用上述手段,可以实现直接以γ
‑ꢀ
al2o3为原料制备高铝陶瓷填料。
15.具体生产工艺是:配料——湿法球磨——喷雾干燥——滚动搪粒成球或干粉液压成球——煅烧。其烧成制度是,在升温过程中于1100℃保温1~3小时,最高烧成温度1370~1490℃并保温1~3小时下面结合案例对本发明作进一步说明。其中,实验案例都是从数百个实验例中遴选出的有代表性的实验,其它实验不一一列出。产品测试方法均按照hg/t3683.1-2014《工业瓷球 惰性瓷球》之标准进行),x-ray衍射分析,采用日本岛津的xrd-6100进行定性检测,采用韩国赛可3000ms扫描电镜观测显微结构。
16.基础案例(即:以煅烧氧化铝为原料制备高铝陶瓷填料之传统配方和工艺):山东低碱二级煅烧氧化铝89kg,广西325目煅烧滑石2.5kg,江西萍乡轻质碳酸钙2kg,江西高安325目白云石2.5kg,江苏苏州250目高岭土4kg,加入三聚磷酸钠0.2kg,加水49kg,球磨34小时后补加少许水以利出磨,使用激光粒度测试仪测试坯料颗粒度分布,结果为,5um以下颗
粒占90%以上。料浆经喷雾干燥和陈腐后,以液压或滚动搪粒工艺成型,烘干后入隧道窑内烧成,匀速线性升温,总烧成时间40小时,最高烧成温度1430℃,高火保温时间2.0小时。由此制得的产品,氧化铝含量91.8%,主晶相为
ɑ-al2o3,没有γ-al2o3,另有玻璃相、钙长石,吸水率为2.03%,直径50mm的瓷球抗压碎力≥50kn(因测试用的sgw数显式工程材料强度综合试验仪的最高压力就是50kn,故凡是材料强度超过50kn的样品,都以≥50kn来表示,以下同。另,hg/t3683.1-2014《工业瓷球 惰性瓷球》之标准规定:氧化铝含量大于90%的直径50mm的瓷球,其抗压强度要求为≥21.50kn/颗),耐酸度98.7%,耐碱度96.9%,耐急变温差(320℃
→
20℃空气中)一次以上不裂,最高耐热温度1500℃不软化变形、不开裂。
17.基础案例之实验例1山东工业氧化铝89kg,广西325目煅烧滑石2.5kg,江西萍乡轻质碳酸钙2kg,江西高安325目白云石2.5kg,江苏苏州250目高岭土4kg,加入三聚磷酸钠0.2kg,加水58kg,球磨34小时后补加少许水以利出磨,使用激光粒度仪测试泥浆颗粒分布,结果为,5um以下颗粒占82%以上。料浆经喷雾干燥和陈腐后,以滚动搪粒工艺成型为直径50mm的瓷球,烘干后入隧道窑内烧成,匀速线性升温,总烧成时间40小时,烧成温度1430℃,高火保温时间2.0小时。由此制得的产品,氧化铝含量91.1%,位于最底层和中间部位的产品有严重开裂情况(有的球直接裂成两半),最上面的产品有部分开裂;基础案例之实验例2山东工业氧化铝89kg,广西325目煅烧滑石2.5kg,江西萍乡轻质碳酸钙2kg,江西高安325目白云石2.5kg,江苏苏州250目高岭土4kg,加入三聚磷酸钠0.2kg,加水58kg,球磨46小时后补加少许水以利出磨,使用激光粒度测试仪测试泥浆颗粒分布,结果为,5um以下颗粒占91%以上。料浆经喷雾干燥和陈腐后,以滚动搪粒工艺成型为直径50mm的瓷球,烘干后入隧道窑内烧成,匀速线性升温,总烧成时间40小时,烧成温度1430℃,高火保温时间2.0小时。由此制得的产品,氧化铝含量91.5%,位于最底层和中间部位的产品均有开裂情况,最上面的产品有部分产品开裂;基础案例之实验例3山东工业氧化铝89kg,广西325目煅烧滑石2.5kg,江西萍乡轻质碳酸钙2kg,江西高安325目白云石2.5kg,江苏苏州250目高岭土4kg,加入六偏磷酸钠0.2kg,加水58kg,球磨34小时后补加少许水以利出磨,使用激光粒度仪测试泥浆颗粒分布,结果为,5um以下颗粒占85%以上。料浆经喷雾干燥和陈腐后,以滚动搪粒工艺成型为直径50mm的瓷球,烘干后入隧道窑内烧成,匀速线性升温,总烧成时间40小时,烧成温度1430℃,高火保温时间2.0小时。由此制得的产品,氧化铝含量91.2%,位于最底层和中间部位的产品有严重开裂情况,最上面的产品有部分开裂;基础案例之实验例4工业氧化铝89kg,广西325目煅烧滑石2.5kg,江西萍乡轻质碳酸钙2kg,江西高安325目白云石2.5kg,江苏苏州250目高岭土4kg,加入柠檬酸钠0.2kg,加水56kg,球磨34小时后补加少许水以利出磨,使用激光粒度测试仪测试泥浆颗粒分布,结果为,5um以下颗粒占89%以上。料浆经喷雾干燥和陈腐后,以滚动搪粒工艺成型为直径50mm的瓷球,烘干后入隧道窑内烧成,匀速线性升温,总烧成时间40小时,烧成温度1430℃,高火保温时间2.0小时。由此制得的产品,氧化铝含量91.3%,位于最底层和中间部位的产品均有开裂情况,最上面的产品有部分开裂现象;基础案例之实验例5工业氧化铝89kg,广西325目煅烧滑石2.5kg,江西萍乡轻质碳酸钙2kg,江西高安325目白云石2.5kg,江苏苏州250目高岭土4kg,加入聚丙烯酸铵0.2kg,加水55kg,球磨34小时后补加少许水以利出磨,使用激光粒度测试仪测试泥浆颗粒分布,结
果为,5um以下颗粒占90%以上。料浆经喷雾干燥和陈腐后,以滚动搪粒工艺成型为直径50mm的瓷球,烘干后入隧道窑内烧成,匀速线性升温,总烧成时间40小时,烧成温度1430℃,高火保温时间2.0小时。由此制得的产品,氧化铝含量91.2%,位于最底层和中间部位的产品有开裂情况,最上面的产品仍有极少数开裂现象;基础案例之实验例6工业氧化铝89kg,广西325目煅烧滑石2.5kg,江西萍乡轻质碳酸钙2kg,江西高安325目白云石2.5kg,江苏苏州250目高岭土4kg,加入聚丙烯酸铵0.2kg,加水55kg,球磨40小时后补加少许水以利出磨,使用激光粒度测试仪测试泥浆颗粒分布,结果为,5um以下颗粒占93%。以上料浆经喷雾干燥和陈腐后,以滚动搪粒工艺成型为直径50mm的瓷球,烘干后入隧道窑内烧成,匀速线性升温,总烧成时间40小时,烧成温度1430℃,高火保温时间2.0小时。由此制得的产品,氧化铝含量91.4%,位于最底层和中间部位的产品有开裂情况,最上面的产品有个别开裂现象。
18.由上述实验可见,如采用基础案例之配方和工艺,只以工业氧化铝等额取代煅烧氧化铝,则无论使用什么分散剂,兼有助磨剂、减水剂功效,并且使球磨时间由34小时增加至48小时,以达到坯料更细的程度,仍避免不了产品开裂等缺陷。鉴此,必须同时变更配方及烧成工艺!同时,使用不同的分散剂,同时又是助磨剂、减水剂,球磨工业氧化铝的效率不同,加水量也不同,以聚丙烯酸铵助磨效果和减水效果最好,其次为柠檬酸钠,三聚磷酸钠对煅烧氧化铝的助磨和减水效果很好,但对工业氧化铝的助磨和减水效果最差。实验发现,工业氧化铝分散度越高,颗粒粒径越细,有助于减少开裂现象(虽然细度不是确保产品合格率的关键因素)。
19.以下案例对配方和工艺进行调整,以从根本上解决产品开裂的问题:改进型实验案例1工业氧化铝89kg,江西高安325目白云石6kg,硅灰2kg,球粘土3kg,加入聚丙烯酸铵0.2kg,加水55kg,球磨36小时后补加少许水以利出磨,使用激光粒度测试仪测试泥浆颗粒分布,结果为5um以下颗粒占91%以上。料浆经喷雾干燥和陈腐后,以滚动搪粒工艺成型为直径50mm的瓷球,烘干后入隧道窑内烧成,匀速线性升温,总烧成时间40小时,烧成温度1430℃,高火保温时间2.0小时。由此制得的产品,氧化铝含量91.3%,吸水率为9.78%,位于最底层和中间部位的产品有少数开裂情况,最上面的产品有个别开裂现象。xrd分析,有较多的
ɑ-al2o3形成,但还含有γ-al2o3,这对于实际应用是不利的;改进型实验案例2工业氧化铝89kg,江西高安325目白云石4kg,硅灰4kg,球粘土3kg,加入聚丙烯酸铵0.2kg,加水55kg,球磨36小时后补加少许水以利出磨,使用激光粒度测试仪测试泥浆颗粒分布,结果为5um以下颗粒占91%以上。料浆经喷雾干燥和陈腐后,以滚动搪粒工艺成型为直径50mm的瓷球,烘干后入隧道窑内烧成,匀速线性升温,总烧成时间40小时,烧成温度1430℃,高火保温时间2.0小时。由此制得的产品,氧化铝含量90.5%,吸水率为10.9%,位于最底层和中间部位的产品有极少数开裂情况,最上面的产品有个别开裂现象。xrd分析,其
ɑ-al2o3含量较高,但仍有γ-al2o3存在;改进型实验案例3工业氧化铝89kg,江西高安325目白云石2kg,硅灰6kg,球粘土3kg,加入聚丙烯酸铵0.2kg,加水55kg,球磨36小时后补加少许水以利出磨,使用激光粒度测试仪测试泥浆颗粒分布,5um以下颗粒占91%以上。料浆经喷雾干燥和陈腐后,以滚动搪粒工艺成型为直径50mm的瓷球,烘干后入隧道窑内烧成,匀速线性升温,总烧成时间40小时,烧成温度1430℃,高火保温时间2.0小时。由此制得的产品,氧化铝含量90.1%,吸水率为
12.2%,位于最底层和中间部位的产品有个别开裂现象,最上面的产品未见开裂。xrd分析,其
ɑ-al2o3含量较高,另有γ-al2o3、莫来石;改进型实验案例4工业氧化铝89kg,江西高安325目白云石6kg,硬硼钙石2kg,球粘土3kg,加入聚丙烯酸铵0.2kg,加水55kg,球磨36小时后补加少许水以利出磨,使用激光粒度测试仪测试泥浆颗粒分布:5um以下颗粒占91%以上。料浆经喷雾干燥和陈腐后,以滚动搪粒工艺成型为直径50mm的瓷球,烘干后入隧道窑内烧成,匀速升温,总烧成时间40小时,烧成温度1430℃,高火保温时间2.0小时。由此制得的产品,氧化铝含量92.1%,吸水率为6.07%,位于最底层和中间部位的产品有开裂现象,最上面的产品仅少数瓷球有开裂。xrd半定量分析,其
ɑ-al2o3含量较高,有γ-al2o3存在;改进型实验案例5工业氧化铝89kg,江西高安325目白云石4kg,硬硼钙石4kg,球粘土3kg,加入聚丙烯酸铵0.2kg,加水55kg,球磨36小时后补加少许水以利出磨,使用激光粒度测试仪测试泥浆颗粒分布:5um以下颗粒占91%以上。料浆经喷雾干燥和陈腐后,以滚动搪粒工艺成型为直径50mm的瓷球,烘干后入隧道窑内烧成,匀速线性升温,总烧成时间40小时,烧成温度1430℃,高火保温时间2.0小时。由此制得的产品,氧化铝含量91.6%,吸水率为4.99%,位于最底层、中间部位有少数开裂,最上面的产品瓷球仅个别开裂。xrd定性分析,其
ɑ-al2o3含量较高,γ-al2o3存在量低于改进型实验案例4;改进型实验案例6工业氧化铝89kg,江西高安325目白云石2kg,硬硼钙石6kg,球粘土3kg,加入聚丙烯酸铵0.2kg,加水55kg,球磨36小时后补加少许水以利出磨,使用激光粒度测试仪测试泥浆颗粒分布:5um以下颗粒占91%以上。料浆经喷雾干燥和陈腐后,以滚动搪粒工艺成型为直径50mm的瓷球,烘干后入隧道窑内烧成,匀速线性升温,总烧成时间40小时,烧成温度1430℃,高火保温时间2.0小时。由此制得的产品,氧化铝含量91.4%,吸水率为3.41%,位于最底层、中间部位有少数开裂,最上面的产品瓷球仅个别开裂。xrd分析,其
ɑ-al2o3含量很高,仅有少量γ-al2o3存在;改进型实验案例7工业氧化铝89kg,硬硼钙石8kg,球粘土3kg,加入聚丙烯酸铵0.2kg,加水55kg,球磨36小时后补加少许水以利出磨,使用激光粒度测试仪测试泥浆颗粒分布,5um以下颗粒占91%以上。料浆经喷雾干燥和陈腐后,以滚动搪粒工艺成型为直径50mm的瓷球,烘干后入隧道窑内烧成,匀速线性升温,总烧成时间40小时,烧成温度1430℃,高火保温时间2.0小时,得到的产品表层完全玻化但内层却不致密,存在明显的不均匀分布的情况!出现这样的反常,系硼酸盐有一定的水溶性特性所致:氧化铝粉体在搪粒成球过程中,喷入的水使其中的硼酸盐矿物部分溶解,在瓷球坯体烘干和烧成过程中,溶解在水中的硼酸盐会随水分子一同向瓷球表面移动,导致瓷球坯体的表层和内层的助熔剂存在浓度差,表层的助熔剂多,而内层的助熔剂少,结果在烧成过程中,表层由于助熔剂更多而烧结充分,变得更致密甚至完全玻化,而内层由于助熔剂更少而烧结不充分,变得更疏松甚至完全生烧,形成内、外层成分和结构不均一的缺陷,严重影响产品机械强度、耐腐蚀性能、耐高温(1500℃)性能和抵抗急冷急热温度激变而不破坏的性能;改进型实验案例8工业氧化铝89kg,江西高安325目白云石4kg,硅灰4kg,球粘土3kg,加入聚丙烯酸铵0.2kg,加水55kg,球磨36小时后补加少许水以利出磨,使用激光粒度测试仪测试泥浆颗粒分布,5um以下颗粒占91%以上。料浆经喷雾干燥和陈腐后,以滚动搪粒工艺成型为直径50mm的瓷球,烘干后入隧道窑内烧成,匀速升温,在1100℃保温2小时,总烧
成时间45小时,烧成温度1430℃,高火保温时间2.0小时。由此制得的产品,氧化铝含量90.5%,吸水率为7.79%,位于最底层、中间和上面部位的产品没有开裂情况。xrd分析,其
ɑ-al2o3含量高于同样配方的改进型实验案例2,而γ-al2o3含量低于同样配方的改进型实验案例2;改进型实验案例9工业氧化铝89kg,江西高安325目白云石4kg,硬硼钙石4kg,球粘土3kg,加入聚丙烯酸铵0.2kg,加水55kg,球磨36小时后补加少许水以利出磨,使用激光粒度测试仪测试泥浆颗粒分布,5um以下颗粒占91%以上。料浆经喷雾干燥和陈腐后,以滚动搪粒工艺成型为直径50mm的瓷球,烘干后入隧道窑内烧成,匀速升温,在1100℃保温2小时,总烧成时间45小时,烧成温度1430℃,高火保温时间2.0小时。由此制得的产品,氧化铝含量91.7%,吸水率为4.01%,位于最底层、中间部位的瓷球有个别开裂,最上面的瓷球无开裂现象。xrd分析,其
ɑ-al2o3含量多于同样配方的改进型实验案例5,γ-al2o3基本看不到衍射峰。
20.从改进型实验案例分析,硅灰即活性二氧化硅的加入,可以有效缓解工业氧化铝制高铝陶瓷产品的烧成开裂问题,且因为形成莫来石或熔解于熔体中可提高玻璃性能,有助于提高产品的耐急冷急热性能、耐温性能、机械强度和耐腐蚀性能,但
ɑ-al2o3转化率不够高,且仍有γ-al2o3存在,而最大的缺陷是产品烧结不够致密,吸水率偏高;加入硼酸盐矿物后,不仅减少了产品开裂情况,而且
ɑ-al2o3转化率很高,γ-al2o3存在量明显下降!但硼酸盐矿物过多,易造成产品径向成分和结构不均匀的缺陷,对使用性能有不利影响。还有一个重要发现是,1100℃保温对于促进氧化铝转相有良好作用,在1200℃、1300℃的保温均不如1100℃保温更有效。
具体实施例
21.以下为本发明的实施例;实施例1:按工业氧化铝89kg,土耳其硬硼钙石3.5kg,硅灰2.5kg,白云石2.5kg,球粘土2.5kg配料,加水55kg,聚丙烯酸铵分散剂0.2kg,球磨36小时后出磨,喷雾干燥造粒,滚动搪粒成球,烘干后入窑烧成,匀速线性升温,1100℃保温1小时,烧成温度1410℃,高火保温时间2.5小时,总烧成时间44小时。产品的氧化铝含量91.05%,xrd分析,瓷件中
ɑ-al2o3含量很高,完全没有γ-al2o3存在,产品吸水率为4.94%,直径50mm瓷球抗压碎力大于50kn,耐酸度96.8%,耐碱度94.7%,耐急变温差(320℃
→
20℃空气中)一次以上不裂,最高耐热温度1500℃不软化变形、不开裂;实施例1之对比例a按工业氧化铝89kg,土耳其硬硼钙石3.5kg,硅灰2.5kg,白云石2.5kg,球粘土2.5kg配料,加水55kg,聚丙烯酸铵分散剂0.2kg,球磨36小时后出磨,喷雾干燥造粒,滚动搪粒成球,烘干后入窑烧成,匀速线性升温,1100℃保温1小时,烧成温度1370℃,高火保温时间2.5小时,总烧成时间44小时。产品的氧化铝含量91.04%,xrd分析瓷件中
ɑ-al2o3含量较多,有γ-al2o3存在,产品吸水率为8.64%,直径50mm瓷球抗压碎力31kn,耐酸度93.7%,耐碱度91.2%;实施例1之对比例b按工业氧化铝89kg,土耳其硬硼钙石3.5kg,硅灰2.5kg,白云石2.5kg,球粘土2.5kg配料,加水55kg,聚丙烯酸铵分散剂0.2kg,球磨36小时后出磨,喷雾干燥造粒,滚动搪粒成球,烘干后入窑烧成,匀速线性升温,1100℃保温1小时,烧成温度1390
℃,高火保温时间2.5小时,总烧成时间44小时。产品的氧化铝含量91.03%,xrd分析瓷件中
ɑ-al2o3含量很高,γ-al2o3约有微弱的衍射峰,产品吸水率为5.65%,直径50mm瓷球抗压碎力44kn,耐酸度94.2%,耐碱度92.8%;实施例1之对比例c按工业氧化铝89kg,土耳其硬硼钙石3.5kg,硅灰2.5kg,白云石2.5kg,球粘土2.5kg配料,加水55kg,聚丙烯酸铵分散剂0.2kg,球磨36小时后出磨,喷雾干燥造粒,滚动搪粒成球,烘干后入窑烧成,匀速线性升温,1100℃保温1小时,烧成温度1430℃,高火保温时间2.5小时,总烧成时间44小时。产品的氧化铝含量91.08%,xrd分析瓷件中
ɑ-al2o3含量很高,完全没有γ-al2o3存在,产品吸水率为3.39%,直径50mm瓷球抗压碎力大于50kn,耐酸度97.1%,耐碱度94.8%实施例1之对比例d按工业氧化铝89kg,土耳其硬硼钙石3.5kg,硅灰2.5kg,白云石2.5kg,球粘土2.5kg配料,加水55kg,聚丙烯酸铵分散剂0.2kg,球磨36小时后出磨,喷雾干燥造粒,滚动搪粒成球,烘干后入窑烧成,匀速线性升温,1100℃保温1小时,烧成温度1450℃,高火保温时间2.5小时,总烧成时间44小时。产品的氧化铝含量91.07%,xrd分析瓷件中
ɑ-al2o3含量很高,完全没有γ-al2o3存在,产品吸水率为2.44%,直径50mm瓷球抗压碎力大于50kn,耐酸度98.9%,耐碱度96.1%;实施例2:按工业氧化铝89kg,土耳其硬硼钙石3.5kg,硅灰2.5kg,白云石2.5kg,球粘土2.5kg配料,加水55kg,聚丙烯酸铵分散剂0.2kg,球磨36小时后出磨,喷雾干燥造粒,滚动搪粒成球,烘干后入隧道窑内烧成,匀速升温,总烧成时间45小时,其中在1100℃保温2小时,烧成温度1410℃,高火保温时间2小时。产品的氧化铝含量91.09%,经佛山陶瓷研究所有限公司xrd半定量分析(检测报告单号:l2064/w211024-03),瓷件中
ɑ-al2o3含量约64%,钙长石约4%,霞石1%,非晶相物质31%左右,完全没有γ-al2o3存在(详见附图1),采用赛可sne-3000ms电镜观察瓷件,得到附图2、3、4照片:瓷体结构致密,刚玉晶体呈粒状且连续分布,晶体发育良好,尺寸约5um,为典型的微晶型结构(附图2、3、4)。产品吸水率为3.98%,直径50mm瓷球抗压碎力大于50kn,耐酸度96.9%,耐碱度95.1%,耐急变温差(320℃
→
20℃空气中)一次以上不裂,最高耐热温度1500℃不软化变形、不开裂;实施例3:按工业氧化铝89kg,土耳其硬硼钙石3.5kg,硅灰2.5kg,白云石2.5kg,球粘土2.5kg配料,加水55kg,柠檬酸钠分散剂0.2kg,球磨36小时后出磨,喷雾干燥造粒,滚动搪粒成球,烘干后入隧道窑内烧成,匀速线性升温,总烧成时间45小时,烧成温度1410℃,高火保温时间2.5小时。产品的氧化铝含量91.02%,xrd分析瓷件中
ɑ-al2o3含量很高,尚有极微量的γ-al2o3存在,产品吸水率为4.36%,直径50mm瓷球抗压碎力大于50kn,耐酸度96.2%,耐碱度94.1%,耐急变温差(320℃
→
20℃空气中)一次以上不裂,最高耐热温度1500℃不软化变形、不开裂;实施例4:按工业氧化铝89kg,西藏硼鎂石4.0kg,硅灰2.5kg,白云石2kg,球粘土2.5kg配料,加水55kg,聚丙烯酸铵分散剂0.2kg,球磨36小时后出磨,喷雾干燥造粒,干粉液压成球,烘干后入隧道窑内烧成,匀速升温,总烧成时间46小时,其中在1100℃保温2小时,烧成温度1410℃,高火保温时间2.5小时。产品的氧化铝含量90.7%,xrd分析瓷件中
ɑ-al2o3含量很高,含有极少量尖晶石,完全没有γ-al2o3存在,产品吸水率为3.23%,直径50mm瓷球抗压碎力大于50kn,耐酸度98.8%,耐碱度96.3%,耐急变温差(320℃
→
20℃空气中)一次以上不裂,最高耐热温度1500℃不软化变形、不开裂;
实施例5:按工业氧化铝89kg,焦硼酸钡3kg,硅灰2kg,白云石3kg,球粘土3kg配料,加水55kg,柠檬酸钠分散剂0.2kg,球磨36小时后出磨,喷雾干燥造粒,滚动搪粒成球,烘干后入隧道窑内烧成,匀速升温,总烧成时间46小时,其中在1100℃保温2小时,烧成温度1420℃,高火保温时间1.5小时。产品的氧化铝含量90.1%,xrd分析瓷件中
ɑ-al2o3含量很高,有微量钡长石,完全没有γ-al2o3存在,吸水率为3.84%,直径50mm瓷球抗压碎力大于50kn,耐酸度98.6%,耐碱度95.9%,耐急变温差(320℃
→
20℃空气中)一次以上不裂,最高耐热温度1500℃不软化变形、不开裂;实施例6:按废氧化铝催化剂的煅烧物(al2o3含量≥98%)85kg,煅烧
ɑ-al2o3粉5kg,人工合成硼酸钙3kg,硅灰2kg,白云石2kg,球粘土3kg配料,加水55kg,聚丙烯酸铵0.2kg,球磨36小时后加水、加溶解后的聚乙烯醇0.2%(干基计),再混磨0.5~1小时后出磨,喷雾干燥造粒,加入脱模剂并混合均匀,陈腐后干粉液压成球,烘干后入隧道窑内烧成,匀速升温,总烧成时间46小时,其中在1100℃保温2小时,烧成温度1400℃,高火保温时间2小时。产品的氧化铝含量91.8%,xrd分析瓷件中
ɑ-al2o3含量很高,完全没有γ-al2o3存在,含少量钙长石,吸水率为3.91%,直径50mm瓷球抗压碎力≥50kn,耐酸度98.5%,耐碱度96.2%,耐急变温差(320℃
→
20℃空气中)一次以上不裂,最高耐热温度1500℃不软化变形、不开裂;实施例7:按工业氧化铝93kg,硼鎂石2kg,硅灰2kg,白云石1kg,球粘土2kg配料,加水53kg,聚丙烯酸铵分散剂0.2kg,球磨38小时后加水、加溶解后的聚乙烯醇0.2%(干基计),再混磨0.5~1小时后出磨,喷雾干燥造粒,加入脱模剂并混合均匀,陈腐后干粉液压成型,烘干后进入隧道窑内烧成,匀速升温,总烧成时间49小时,其中在1100℃保温3小时,烧成温度1470℃,高火保温时间2.5小时。产品的氧化铝含量93.1%,xrd分析瓷件中
ɑ-al2o3含量极高,完全没有γ-al2o3存在,吸水率为6.43%,直径50mm瓷球抗压碎力大于50kn,耐酸度98.4%,耐碱度95.9%,耐急变温差(320℃
→
20℃空气中)一次以上不裂,最高耐热温度1500℃不软化变形、不开裂;实施例7a:按工业氧化铝88kg,煅烧
ɑ-al2o3粉5kg,硼鎂石2kg,硅灰2kg,白云石1kg,球粘土2kg配料,加水53kg,聚丙烯酸铵分散剂0.2kg,球磨38小时后加水、加溶解后的聚乙烯醇0.2%(干基计),再混磨0.5~1小时后出磨,喷雾干燥造粒,加入脱模剂并混合均匀,陈腐后干粉液压成型,烘干后进入隧道窑内烧成,匀速升温,总烧成时间46小时,其中在1100℃保温1小时,烧成温度1470℃,高火保温时间1.5小时。产品的氧化铝含量93.4%,xrd分析瓷件中
ɑ-al2o3含量极高,完全没有γ-al2o3存在,吸水率为5.21%,直径50mm瓷球抗压碎力大于50kn,耐酸度98.8%,耐碱度96.4%,耐急变温差(320℃
→
20℃空气中)一次以上不裂,最高耐热温度1500℃不软化变形、不开裂;实施例8:按工业氧化铝94kg,硬硼钙石3kg,硅灰1kg,白云石1kg,球粘土1kg配料,加水52kg,聚丙烯酸铵分散剂0.2kg,球磨39小时后加水、加溶解后的聚乙烯醇0.2%(干基计),再混磨0.5~1小时后出磨,喷雾干燥造粒,加入脱模剂并混合均匀,陈腐后干粉液压成型,烘干后入隧道窑内烧成,匀速升温,总烧成时间49小时,其中在1100℃保温3小时,烧成温度1490℃,高火保温时间3小时。产品的氧化铝含量94.1%,xrd分析瓷件中
ɑ-al2o3含量很高,且完全没有γ-al2o3存在,吸水率为7.95%,直径50mm瓷球抗压碎力大于50kn,耐酸度97.9%,耐碱度96.8%,耐急变温差(320℃
→
20℃空气中)一次以上不裂,最高耐热温度1500℃不软化变形、不开裂;
实施例8a:按工业氧化铝87kg,煅烧
ɑ-al2o37kg,硬硼钙石3kg,硅灰1kg,白云石1kg,球粘土1kg配料,加水52kg,聚丙烯酸铵分散剂0.2kg,球磨39小时后加水、加溶解后的聚乙烯醇0.2%(干基计),再混磨0.5~1小时后出磨,喷雾干燥造粒,加入脱模剂并混合均匀,陈腐后干粉液压成型,烘干后入隧道窑内烧成,匀速升温,总烧成时间46小时,其中在1100℃保温1.5小时,烧成温度1490℃,高火保温时间1.5小时。产品的氧化铝含量94.5%,xrd分析瓷件中
ɑ-al2o3含量在所有实施例中最高,且完全没有γ-al2o3存在,吸水率为6.01%,直径50mm瓷球抗压碎力大于50kn,耐酸度98.9%,耐碱度97.1%,耐急变温差(320℃
→
20℃空气中)一次以上不裂,最高耐热温度1500℃不软化变形、不开裂;实施例9按工业氧化铝83kg,硅灰4kg,硬硼钙石5kg,透辉石4kg,球粘土4kg配料,加水53kg,聚丙烯酸铵分散剂0.2kg,球磨39小时后补加水,再混磨0.5小时后出磨,喷雾干燥造粒,陈腐后搪粒成球,烘干后入隧道窑内烧成,匀速升温,总烧成时间46小时,其中在1100℃保温2小时,烧成温度1370℃,高火保温时间1.5小时。产品的氧化铝含量85.05%,xrd分析瓷件中含有
ɑ-al2o3、尖晶石、钙长石,完全没有γ-al2o3存在,吸水率为2.11%,直径50mm瓷球抗压碎力大于50kn,耐酸度96.3%,耐碱度92.5%,耐急变温差(320℃
→
20℃空气中)一次以上不裂,最高耐热温度1500℃不软化变形、不开裂。
22.附图说明:图1为实施例2之产品的xrd图谱图2、3、4为实施例2之产品不同放大倍数的扫描电镜照片本发明的优点:本发明所涉及的产品是石油化工、煤化工、化肥、有色冶炼等化工反应塔(器)广为使用的高铝陶瓷填料。以往高铝陶瓷填料都是以
ɑ-al2o3为原料来制备,而
ɑ
‑ꢀ
al2o3又是由γ
‑ꢀ
al2o3经高温煅烧而制得。本发明简化了生产工艺——直接以γ
‑ꢀ
al2o3投料来制备惰性高铝陶瓷填料(无需使用经过煅烧的
ɑ
‑ꢀ
al2o3),其配方为:主晶相为γ
‑ꢀ
al2o3的氧化铝原料83~94wt%,硼酸盐矿物或合成的硼酸盐化合物2~5wt%,球粘土1~4wt%,纳米二氧化硅1~4wt%,钙镁复合矿物1~4wt%,煅烧氧化铝粉0~7wt%,结合1100℃低温保温工艺手段,实现了由γ
‑ꢀ
al2o3直接投料制备高铝陶瓷填料。本发明由于减少了γ-al2o3→
ɑ
‑ꢀ
al2o3的高温煅烧工序,大大降低了碳排放和能源消耗,所制得的产品各项性能完全满足我国化工行业标准要求,生产的产品合格率高。
23.本发明产品主要用作化工、冶金、环保反应塔(器)的的支撑材料和覆盖材料。