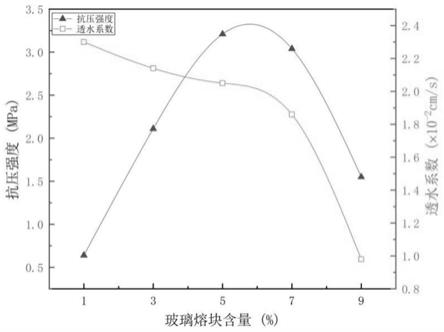
1.本发明涉及煤矸石透水砖制备领域,具体涉及一种煤矸石陶粒制备孔梯度自洁净透水砖的方法。
背景技术:2.煤炭开采、加工级使用过程中会产大量的固态废弃物——煤矸石,是我国目前年排放量和累计堆积量最大的工业固体废料之一,其主要成分是al2o3、sio2,另外还含有一定数量的fe2o3、cao、mgo、na2o、k2o、p2o5、so3和微量的稀有元素(镓、钒、钛、钴等),这些组分决定了它在建材行业的应用具有广阔的应用前景。市场上对于煤矸石的利用主要有:
①
回收煤炭和黄铁矿、
②
用于发电、
③
制造建筑材料、
④
生物肥料。
3.目前,煤矸石在建材行业主要被应用于泡沫混凝土和透水砖的生产。其中,免烧结煤矸石透水砖的制备通常是以透水砖为主要原料,以水泥为粘结剂,再应用合适的工艺参数即可得到性能良好的免烧结煤矸石透水砖。赵亚兵等人研究了煤矸石粒径,原料配比,以及成型压力等工艺条件对多孔透水砖吸水率、透水系数、抗压强度和抗折强度的影响。研究发现随着煤矸石粒径增大,样品吸水率增大,透水系数减小,抗压强度和抗折强度增大;随着水泥含量增加,样品吸水率和透水系数减小,抗压强度和抗折强度增大;随着成型压力增大,样品吸水率和透水系数减小,抗压强度和抗折强度增大。李学军等人研究发现免烧结煤矸石透水砖的性能受煤矸石粒径影响最大,受原料配比、成型压力影响次之。同时李学军还研究了喷涂纳米二氧化钛的透水砖自洁净能力的好坏与光照时间、喷涂剂的用量、透水砖的堵塞程度之间的关系。通过正交试验探究了光照时间、喷涂剂的用量和透水砖的堵塞程度对透水砖恢复率的影响。得出影响喷涂纳米二氧化钛的透水砖自洁净能力的次序为喷涂剂的用量>堵塞程度>光照时间。
4.烧结型煤矸石透水砖是采用煤矸石、黏土为主要原料,再加入造孔剂或发泡剂,经过烧结而得到的陶瓷透水砖。太原理工大学的刘家乐通过以膨胀珍珠岩造孔剂法、发泡剂法的方法来制备透水砖的研究,创新性地提出一种全新的造孔发泡结合的实验方法来制备透水砖。并研究了工艺参数对透水砖制品的性能的影响,得出结论影响较小的是成型压力和保温时间。之后李珠等人继续研究了原料的配比、烧成制度及膨胀珍珠岩掺量对煤矸石烧结透水砖性能的影响。试验表明,当煤矸石与黏土的质量比为7∶3,烧结温度为1050℃,膨胀珍珠岩掺量为80%,保温时间为30min时,所制得的透水砖性能最优,其劈裂抗拉强度为3.75mpa,透水系数为0.355
×
10-2
cm/s。武晓宇等人则制备了一种低温高强粘结剂,并研究了各氧化物对粘结剂性能的影响及釉料配方的熔融温度、抗折强度、维氏硬度、物相组成及晶体结构。结果表明:熔块中casio3晶体的生成对熔块的性能有积极影响,抗折强度最高可达76.03mpa,釉面维氏硬度可达72.08mpa。
5.尽管现在我国相关市场上生产透水砖的厂家较多,但大多局限于生产黏土型透水砖。对于生产煤矸石型透水砖的厂家相对而言较少,且技术还不够完善。
技术实现要素:6.为解决上述问题,本发明提供了一种煤矸石陶粒制备孔梯度自洁净透水砖的方法。
7.为实现上述目的,本发明采取的技术方案为:
8.一种煤矸石陶粒制备孔梯度自洁净透水砖的方法,以煤矸石作为主要原料、低温玻璃熔块粉作为粘结剂、氧化锌等氧化物作为光催化剂、0.2%浓度的羧甲基纤维素钠作为团球助剂制备煤矸石陶粒透水砖。其中,所述低温玻璃熔块粉的添加量为5%、烧结温度为1250℃、保温时间为30min本发明所述的一种煤矸石陶粒制备孔梯度自洁净透水砖的方法具体包括如下步骤:
9.s1、利用电子天平称取一定量的煤矸石粉体,按质量百分比为5%的比例加入适量低温玻璃熔块粉,并按质量百分比为0.5-3%的比例加入适量光催化剂,进行混料;
10.s2、将称好的混合料倒入球磨罐中,球料比为1∶3,60r/min球磨1小时后,倒入恒温箱中干燥30min;
11.s3、配置0.2%浓度的羧甲基纤维素钠溶液;
12.s4、先用羧甲基纤维素钠溶液润湿抛光机内部,再将少量干燥好的混料撒入抛光机内部,将转速调至50转,进行造粒,当粘附在抛光机内部的粉料过多时,需用手刮蹭干净,再向抛光机内持续喷入羧甲基纤维素钠溶液,以达到大量成球的目的,之后将团成的球和废料用铲子捞出,并通过不同直径的筛网筛分,所得的大小球和废料分别装在不同烧杯中,放入恒温箱中进行干燥;
13.s5、将干燥好的球和废料分开装并贴好标签,利用氧化铝坩埚进行烧结,在坩埚的底部铺上一层氧化铝粉末,坩埚内壁则贴上一层石棉,再将不同粒径的煤矸石球粒按照小-大-小的结构进行铺展,使烧成的透水砖在横截面上达到一定的梯度孔结构,从而提高砖在实际应用的使用寿命;
14.s6、将铺装好煤矸石球粒的坩埚放入箱式高温炉中,1250℃烧结30min;
15.进一步地,所述步骤s2中,中球∶小球=1∶4;
16.进一步地,当需要大量大球时,将cmc溶液少量的喷在球的表面,并在其表面撒上粉料,从而达到增加大球产量的目的。
17.本发明具有以下有益效果:
18.所得的透水砖性能较佳,其吸水率为8.79%,抗压强度为4.22mpa,气孔率12.38%、透水系数2.33
×
10-2
。
附图说明
19.图1煤矸石xrd分析。
20.图2煤矸石粉体sem图。
21.图3矸石的差热、热重分析。
22.图4透水系数装置示;
23.图中:1-测试筒、2、6-溢流管、3-储水槽、4-试样、5-透水孔、7-量筒、8-固定箍、9-支撑杆、10-装样模块、11-装样模块底端通孔、12-底座通孔、13-底座、14-固定圆环。
24.图5玻璃熔块含量对透水砖吸水率、气孔率的影响。
25.图6不同熔块含量样品截面形貌
26.图中:a-1%;b-3%;c-5%;d-7%;e-9%。
27.图7玻璃熔块含量对透水系数、抗压强度的影响。
28.图8不同熔块含量试样外观形貌
29.图中:a-1%;b-3%;c-5%;d-7%;e-9%。
30.图9烧结温度对气孔率、吸水率的影响。
31.图10不同烧结温度样品截面形貌;
32.图中:a-1050℃;b-1200℃;c-1250℃;d-1300℃。
33.图11烧结温度对透水系数、抗压强度的影响。
34.图12不同烧结温度试样外观形貌
35.图中:a-1150℃;b-1200℃;c-1250℃;d-1300℃。
36.图13保温时间对吸水率、气孔率的影响。
37.图14不同保温时间样品截面形貌;
38.图中:a-30min;b-60min;c-90min;d-90min;e-120min。
39.图15保温时间对透水系数、抗压强度的影响。
40.图16不同保温时间样品外观形貌;
41.图中:a-30min;b-60min;c-90min;d-90min;e-120min。
具体实施方式
42.为了使本发明的目的及优点更加清楚明白,以下结合实施例对本发明进行进一步详细说明。应当理解,此处所描述的具体实施例仅仅用以解释本发明,并不用于限定本发明。
43.试验资料
44.1.试验材料
45.表1为本试验所用的原料,煤矸石为江西博鸿新材料科技有限公司获得,其成分由表2所示,并通过xrd检验其物相,如图1所示。
46.表1主要实验药品
[0047][0048]
表2煤矸石成分表
[0049][0050]
由图1可知,煤矸石的主要成分以sio2、al2o3为主。从这些原料的特征及应用可知,煤矸石在一定程度上可对配料的可塑型起到调节作用,构成坯体的轻质骨架,同时可以制
备出低聚物。同样的取少量原料的粉体做sem分析,观察煤矸石粉料的微观结构。
[0051]
由图2可知,煤矸石粉体颗粒粒度大多数分布在10um左右,最大的颗粒粒度约为50um,颗粒粒度相差不大,颗粒分布较为集中。
[0052]
将少量煤矸石与低温玻璃熔块粉利用罐式球磨机充分球磨混合后,选取空气气氛进行差热分析及热重分析,结果如图3所示。
[0053]
由图3可知,煤矸石-熔块粉的烧失量约为10.52%,且质量损失多数发生在200℃-650℃之间,发生质量损失主要原因为煤矸石中的碳在该温度区域与空气中的氧气发生反应,主要为:c+o2→
co2,使质量不断下降。同时,通过差热分析可知:煤矸石-玻璃粉熔块从室温100℃左右不断放热,随后出现小幅度的吸热,之后又大幅度地放热,在630℃左右开始不断吸热,直到900℃,最后,继续吸热直到烧结温度。
[0054]
2.烧成制度的确定
[0055]
透水砖的烧成制度由原料或混料其自身的特性来决定,根据混料的差热一热重分析可确定其烧成制度可分为四个阶段。第一阶段以3℃/min的升温速率进行烧结,主要目的是利用炉温将坯体中残留的水分除去。同时,在600℃下保温60分钟,其主要原因是由于低温玻璃熔块粉的混入,而且玻璃熔块在600℃左右会熔融生成玻璃相,所以需要在600℃时保温,便于玻璃相发挥出助熔剂的作用。第二阶段,保持烧结速率,继续以3℃/min的烧结速率进行烧结,直到800℃,主要原因是保持玻璃相的增加,同时防止其由于重力而向下流动,导致堵塞透水砖的孔道,使砖体的透水系数受其影响而下降。第三阶段,直接从800℃升到烧结温度,以2.4℃/min的速率烧结,其主要原因是使不同晶相得物质在高温环境下相互反应,从而生成新的物质,从而使坯体的强度得到增加。在烧结温度需保温60min,其目的是增加反应时间,同时防止样品未烧熟。最后,降温阶段采用随炉降温的方式进行降温。
[0056]
2.1实验步骤
[0057]
利用电子天平称取一定量的煤矸石粉体,按质量百分比为2%的比例加入适量光催化剂,再根据配方比例的不同加入不同量低温玻璃熔块粉,进行混料。
[0058]
将称好的混合料倒入球磨罐中,球料比为1∶3。由于粉煤矸石和玻璃熔块粉的粒度较小,故球磨子主要选用小球,为防止粉料之间形成团聚现象,所以应使用一定质量的中等球;经过多次预试验得出其较优质量比:中球∶小球=1∶4。球磨时间为1小时;球磨转数为60r/min。
[0059]
将混合好的料倒出,放置于恒温箱中干燥30min。
[0060]
配置0.2%浓度的将羧甲基纤维素钠溶液:量取0.5g的羧甲基纤维素钠(简称cmc)与烧杯,先加入少量的水,由于cmc属于有机物,难溶于水。所以先加入少量的水,持续搅拌,然后不断加入少量的水,直至变成悬浊液,将玻璃棒上残余cmc溶液洗入烧杯中。再向所得悬浊液中加水直到达到250ml的刻度线。再将所得悬浊液放入集热式恒温加热磁力搅拌器中,加入磁子,加热至60℃。水浴搅拌,直至变为溶液为止。
[0061]
将干燥好的混料,利用抛光机经过尝试得出快速成球的一种方法:先使用cmc溶液润湿抛光机内部,再而将少量粉料撒入抛光机内部,将转速调至50转,进行造粒。当粘附在抛光机内部的粉料过多时,应当用手刮蹭干净,再向里面持续喷入cmc溶液,以达到大量成球的目的。当需要大量大球时,将cmc溶液少量的喷在球的表面,并在其表面撒上粉料,从而达到增加大球产量的目的。将团成的球和废料用铲子捞出,并通过不同直径的筛网,达到筛
分的效果。将大小球和废料分别装在不同烧杯中,放入恒温箱中进行干燥。
[0062]
将干燥好的球和废料分开装并贴好标签。利用氧化铝坩埚进行烧结,在坩埚的底部铺上一层氧化铝粉末,坩埚内壁则贴上一层石棉。以防止烧成的透水砖粘结内壁,造成坩埚的损坏和浪费。再将不同粒径的煤矸石球粒按照小-大-小的结构进行铺展,使烧成的透水砖在横截面上达到一定的梯度孔结构,从而提高砖在实际应用的使用寿命。
[0063]
将铺装好煤矸石球粒的坩埚放入箱式高温炉中,按照确定好的烧成制度调节高温炉的程序,关好炉门。
[0064]
对烧结成的煤矸石透水砖做性能测试,其中包括测定透水砖的吸水性、测定透水砖的透水性、测定透水砖的抗压强度等因素。
[0065]
2.2试样性能测试及表征
[0066]
吸水率的测定
[0067]
测定已烧结的煤矸石陶粒透水砖的吸水率,它的吸水率越高,那么吸水能力也越强,透水砖的吸水保湿性能则更好。
[0068]
测试吸水率的步骤如下:首先把烧结好的煤矸石透水砖试样放入恒温干燥箱内进行烘干处理,当干燥至到试样的重量不再发生变化的时候,将此时干燥试样的质量记为m1。将干燥后的试样进行冷却处理,直至室温。之后将透水砖放入水杯中,再向水杯中添加蒸馏水,直到试样完全浸没于蒸馏水。将陶粒透水砖试样在浸泡2h后,用饱和的湿纸巾吸走试样表面的水,之后把它放置于电子天平中进行称量,所得质量记为试样吸水后的质量m2。最后按照吸水率的公式a=(m2-m1)
×
100%/m1,式中,m1:干燥试样的质量、m2:试样吸水2h后的质量(单位:g),进行计算(试样测量三次,取其平均值),所得数据即记为煤矸石陶粒透水砖的吸水率。
[0069]
气孔率的测定
[0070]
有关于气孔率检测,则需要用到密度天平但由于本实验所成样品体积过大,故考虑不使用密度天平。具体步骤如下:首先使用电子天平称量已经干燥的试样质量该值记为m0,把试样放入干净的烧杯里,加入适量蒸馏水,使试样被蒸馏水完全浸没。之后,将烧杯放置在可调节电炉上加热直至蒸馏水沸腾,再持续加热直到烧杯中的透水砖试样表面不再产生气泡,停止对烧杯加热,待烧杯中的蒸馏水自然冷却至室温。将烧杯中的水用吸管吸出,直至蒸馏水刚好浸渍煤矸石样品。将处理好的烧杯放置于天平上,质量记为m
x
,将样品从烧杯中拿出,记录质量设为my。记m
x-my=m1其中m1为浸渍时透水砖样品饱和质量。样品拿出烧杯后立即用饱和吸水的湿纸巾吸取透水砖样品表面的水。将处理后的样品放置在电子天平上,所得质量记为m3。最后,通过运用相关公式进行计算从而得出试样的显气孔率pa(%)、体积密度db(g/cm3)和真显气孔率以及闭显气孔率pc(%)。
[0071]
透水系数的测定
[0072]
透水性能是透水砖最重要的性能之一。通常使用常水法测定透水砖的透水系数。首先使用游标卡尺测量煤矸石陶粒试样的上下直径d分别记为d1、d2,并取二者的平均值记为平均直径d3以及厚度l,测量三次取平均值,并计算出试样的表面积s。用水圆筒和皮筋将试样周围密封,防止水从侧面流出,干扰实验结果,且保证水只能从试样上方向试样下方渗透,再者也需要使向下流的水覆盖透水砖表面留下。测量在一定体积v内,水从透水砖上方向透水砖下方渗透的时间t,测量三次,取其平均值,透水装置示意图如4所示。
[0073]
测量圆桶水位与与水槽之间的水位差h。并通过公式1计算:
[0074]
k=va/qth
ꢀꢀꢀ
(1)
[0075]
k-渗透系数(cm/s);q-渗水量(ml);a-试样上表面积(cm2);v-相同体积的水(ml);h-水位差(cm);t-时间(s);
[0076]
扫描电子显微镜分析
[0077]
本次实验使用日本日立公司所生产扫描电子显微镜,其仪器主要由离子泵、真空泵、电子枪、聚光器、物镜、偏转线圈、样品室、监视器等部分组成。扫描电镜主要是利用电子枪激发的电子与试样撞击所产生的二次电子信号成像来观察试样表面形貌。分辨率一般为3-6nm,因为分辨率较高,所以对试样的厚度具有十分严格的要求。
[0078]
抗压强度的测定
[0079]
抗压强度是透水砖的另一个重要性能,一般是使用万能力学试验机来测定煤矸石陶粒透水砖试样在外加压力的作用下,所能承受的最大极限压力。由于本实验所生产的透水砖样品为上大下小的陀螺状试样,故先用游标卡尺分别测量试样的上下直径d1、d2,计算出平均直径d3.并计算其表面积s。随后进行实验测试,使压力传感器匀速下降匀速,均匀的对试样施加载荷,直至试样被破坏,试样形状出现显著变化。记录载荷p
x
。其抗压强度所用的公式(2)所示:
[0080]
r=p/s
ꢀꢀꢀꢀ
(2)
[0081]
式中,r-抗压强度,mpa;p-载荷,n;s-受力面积,mm2。
[0082]
结果
[0083]
熔块含量对煤矸石陶粒透水砖的性能影响
[0084]
不同熔块含量分别制备出煤矸石陶粒透水砖,将玻璃熔块粉-煤矸石所团成的陶粒经过铺垫,以烧结温度1250℃、保温时间90min的烧成制度下进行烧结。同时,控制熔块粉的含量分别为1%、3%、5%、7%、9%,研究玻璃熔块粉含量对陶粒透水砖性能的影响,从而探究玻璃熔块粉含量的较优值,其实验数据如表3所示。
[0085]
表3不同玻璃粉含量制备透水砖的性能
[0086][0087]
由图5可知随着玻璃熔块含量增加,透水砖的吸水率先上升后下降,直到玻璃熔块的含量为5%时出现峰值。这是由于熔块粉含量的增加,烧结产生的玻璃相增加,使陶粒之间的粘结加强,间隙之间产生的孔隙得到增加,从而使透水砖的吸水率、气孔率增加。当玻璃熔块含量大于5%时,由于烧结产生的玻璃相不断增加,堵塞了部分孔隙,使吸水率、气孔率随着熔块粉含量的增加而下降。但在熔块粉含量大于7%时,气孔率反而增加了,主要原因是上层陶粒由于高温玻璃相大量产生时,都向着第二层的陶粒表面依附,由于玻璃相是液态的所以会不断向下流动,在底层陶粒之间形成了蜂窝状的大量孔隙,使气孔率增加,如图6所示。
[0088]
由图7可得出玻璃熔块含量对透水系数、抗压强度的影响。随着熔块含量的增加,其抗压强度也随之增加,直到熔块粉含量为5%时达到最高值。由于熔块含量增加,其他条件相同的情况下玻璃相的含量增加,颗粒之间粘性增强使得强度增加。而5%之后由于下层的陶粒之间未有效粘结,所以抗压强度开始降低。随着熔块含量的增加,透水系数则逐渐下降,到9%时由于熔块含量增加,中间层的陶粒由于玻璃相的运动致使致密度大大加高,致使透水系数大大下降。
[0089]
样品外观形貌如8所示,随着熔块含量的增加,样品表面玻璃相也会不断增加。终上所述,得出5%熔块粉含量制备的透水砖性能相对较优。
[0090]
烧结温度对煤矸石陶粒透水砖的性能影响
[0091]
熔块含量为5%,煅烧温度分别选择1050℃、1150℃、1200℃、1250℃、1300℃,在保温90min条件下进行烧结,研究烧结温度对透水砖性能的影响,以探究较优的烧结温度。由于透水砖在1050℃时未形成有效烧结,故结论中不予讨论,当成一组参考数据。测试其性能可得以下数据,如下表4所示。
[0092]
表4不同烧结温度制备透水砖的性能
[0093][0094]
图9为不同烧结温度对透水砖吸水率、气孔率的影响,由图可知气孔率和吸水率先升高后降低,但在1300℃时吸水率和气孔率出现了大幅下降。主要原因为过高的烧结温度使得玻璃相大量增加,陶粒之间的孔隙被填充的同时液态玻璃相沸腾也会产生孔隙,但与被填充的孔隙相比,沸腾产生的孔隙太少,对气孔率和吸水率的影响更低。所以在1300℃时,总体来说,气孔率和吸水率还是大幅下降的。
[0095]
图10则反映烧结温度对了透水系数和抗压强度的影响。其中抗压强度随烧结温度的升高而升高,到1250℃达到峰值,之后下降。其原因是烧结温度高于1250℃时,透水砖内部会由于过烧产生许多孔隙,从而导致抗压强度下降。透水砖的截面形貌,如图11所示。而透水系数在1150℃-1200℃的温度阶段快速下降,这主要是因为在1150℃时,透水砖没有形成完全烧结,当温度继续上升时,由于温度升高玻璃相增加,然后向陶粒表面聚集从而堵塞了透水砖内部的孔隙。再继续升高温度时,玻璃相继续向陶粒表面聚集,当陶粒之间孔隙被填满后,新的陶粒表面之间会产生新的孔隙,所以当烧结温度为1250℃时透水系数会增加。当温度高于1250℃时,由于烧结过度,液态的玻璃相沸腾产生气泡使得透水砖的透水系数略为上升。
[0096]
图12是不同烧结温度下所得样品的图片,由外观可得出随着烧结温度的上升,透水砖的外表上玻璃相逐渐增加,外表反光程度逐渐加深。
[0097]
综上可得:煤矸石陶粒透水砖的较优烧结温度为1250℃,透水砖的综合性能达到相对较优值。
[0098]
保温时间对煤矸石陶粒透水砖的性能影响
[0099]
在熔块含量为5%、烧结温度为1250℃的条件下,分别研究保温时间在30min、60min、90min、120min和150min等条件下陶粒透水砖的性能,继而得出保温时间对煤矸石陶粒透水砖的性能数据如表5所示
[0100]
表5保温时间对透水砖的影响
[0101][0102]
图13表示在不同保温时间的状态下,陶粒透水砖的吸水率、气孔率的变化。由图可知,陶粒透水砖的吸水率随着保温时间的增加先增加后减少,在保温时间为90min时达到最高值。气孔率随着保温时间的增加,先下降后上升再下降的趋势。在保温时间为30min时,透水砖的气孔多,但是比较均匀。当提高保温时间,样品的液态玻璃相由于沸腾使得陶粒之间的气孔减少,而且不均匀,致使透水砖的气孔率下降。但是在保温时间为90min时,气孔率出现短暂的上升。这是由于玻璃相运动到陶粒表面后,结构之间产生了新的孔隙,同时颗粒表面也会产生小孔。而当保温时间大于90min时,产生的新孔隙,又被玻璃相堵住,故而气孔率又开始下降。透水砖下层的截面形貌图如图14所示,从图中也可证明孔结构变化情况。
[0103]
图15表示的是在不同保温时间影响下,陶粒透水砖的透水系数、抗压强度的变化。由图可知透水系数和抗压强度随着保温时间的增加,总的来说呈现下降的趋势。造成这种现象的原因主要是随着保温时间的增加,液态玻璃相向下流动和向颗粒表面依附的性质,使得颗粒堆积所产生的的孔隙被堵塞,从而导致透水系数下降。抗压强度的下降则是由于保温时间的增加使得陶粒内部产生的气孔越来越多,虽然由于玻璃相流动使得孔隙被填充。但总体而言与前者相比较,其对强度的影响更小。在30min-60min的时间段透水系数与抗压强度略有上升,这是由于保温时间的增加使玻璃相沸腾的时间增加了,致使被填充的孔隙由于沸腾产生的气泡,形成了许多不规则的孔道,且在陶粒之间形成了许多由玻璃相行成的连桥使得透水系数和抗压强度得到增强增加,样品的截面形貌图如图14所示,从图中也可证明玻璃相的孔连桥现象。不同保温时间的样品外表如图16所示,由图可知,保温时间对样品外观形貌影响不大。
[0104]
综上结论,当煤矸石透水砖的熔块含量为5%,烧结温度为1250℃时,保温时间为30min所得样品的各项性能综合而言达到相对最优值。
[0105]
以上所述仅是本发明的优选实施方式,应当指出,对于本技术领域的普通技术人员来说,在不脱离本发明原理的前提下,还可以作出若干改进和润饰,这些改进和润饰也应视为本发明的保护范围。