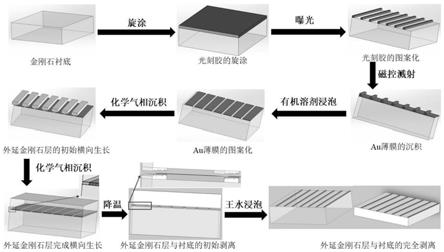
1.本发明属于晶体生长技术领域,具体涉及一种单晶金刚石膜剥离方法,特别涉及一种大尺寸高质量单晶金刚石膜的剥离方法。
背景技术:2.金刚石在室温下的禁带间隙为5.47ev,被称为宽禁带半导体,具有极高的介电强度、电子迁移率、空穴迁移率、饱和电子速度,可进行高压操作,适用于各类高速设备。此外,金刚石具有已知材料中最高的热导率,热辐射性能良好。与si和gan等半导体相比,金刚石的品质因数最高,被认为是未来高功率器件的最有前途的候选材料之一,因此被誉为“终极半导体”。
3.制备金刚石基半导体器件,就需要具有晶圆级的单晶金刚石膜。化学气相沉积法被认为是制备大尺寸、高质量单晶金刚石最有前途的技术,并衍生出同质外延(马赛克拼接)和异质外延两种生长方法。对于同质外延,日本学者h.yamada等通过晶种克隆和马赛克拼接生长,已经获得了2英寸大小的样品(appl.phys.lett.104(2014)102)。对于异质外延,德国学者m.schrecka等通过离子轰击诱导掩埋横向生长的方法在si/ysz/ir(001)和srtio3/ir(001)衬底上获得了直径达92mm的单晶金刚石样品(scie.repo.7(2017)44462)。
4.目前面临着一个重要的难题,即大尺寸外延单晶金刚石膜与衬底间的剥离问题。目前,脉冲激光切割法是剥离外延单晶金刚石膜与衬底的最常用的方法,然而脉冲激光切割法存在着其固有的缺陷,随着金刚石尺寸的扩大,切割深度增加,切割缝会逐渐变宽,材料损耗大幅度增加。基于水射流引导的激光切割技术可以有效减少切割缝宽度的同时增加切割深度,但是这项技术的极限切割尺寸仍然有限,无法成为2英寸级以上单晶金刚石晶圆的有效剥离方法。在另一种方法中,通过离子注入在单晶金刚石亚表面制造牺牲层,以此达到外延金刚石膜与衬底完整剥离的目的。但离子注入设备昂贵、工艺复杂,且外延生长的金刚石膜容易遗传因离子注入导致的辐射缺陷,降低金刚石质量。因此,寻求一种低损耗的高质量单晶金刚石膜的剥离方法十分关键。
技术实现要素:5.本发明的主要目的在于提供一种大尺寸高质量单晶金刚石膜的剥离方法,以解决现有剥离技术中金刚石损耗大、质量降低的问题。
6.为达到上述目的,本发明采用的技术方案如下:
7.一种大尺寸单晶金刚石膜生长和剥离方法,包括以下步骤:
8.步骤1,选取1片(100)取向的单晶金刚石作为衬底,抛光、清洗后用旋涂的方法在衬底表面添加一层1~10μm厚的光刻胶,然后在光刻机中将设计的掩膜图形曝光转移到金刚石衬底上;设计的掩膜图形为开放窗口与保留的光刻胶组成的周期性图形,所述的开放窗口是曝光时去除光刻胶的区域;
9.步骤2,在经过步骤1处理后的金刚石衬底上沉积一层掩膜材料,然后使用有机溶
剂去除金刚石衬底上的光刻胶,沉积在光刻胶上的掩膜材料也将被一起除去,获得具有图形化掩模的金刚石衬底;所述的掩膜材料是金刚石成核密度较低或者无法成核的材料;
10.步骤3,将经过步骤2处理后的金刚石衬底进一步清洗后转移到cvd设备中进行金刚石的沉积生长,生长后降至室温,由于金刚石在掩膜材料表面成核密度较低或者无法成核,在无掩膜材料区域的金刚石同质外延生长过程中横向生长的金刚石将会跨过掩膜材料生长在一起,形成完整的单晶金刚石膜,由于金刚石和掩膜材料的热膨胀系数具有显著差异,在生长结束后的降温过程中,掩模区和开放窗口区将会产生巨大的压应力和拉应力,在室温下,这些高应力区域很容易裂开,从而实现外延金刚石膜的轻松剥离。
11.步骤4,将生长后的样品浸泡到能够溶解步骤2中所沉积的掩膜材料但不损伤光刻胶的溶液中1~10h,实现同质外延单晶金刚石膜和原始的单晶金刚石衬底的剥离。
12.进一步地,步骤1中,所述掩膜图形为网格状图案,每个开放窗口是边长1μm-80μm的正方形,开放窗口的填充因子控制在20%~90%范围内,所述的填充因子为开放窗口的面积与衬底生长面的总面积比值。
13.进一步地,步骤2中,沉积掩膜材料时使用磁控溅射、电子束蒸发、等离子体增强化学气相沉积等方法,所述的有机溶剂优选丙酮,所述的掩膜材料优选au、sio2、mo、al2o3,掩膜材料的厚度优选50nm~800nm。
14.进一步地,步骤3中,所述金刚石的沉积生长,生长过程分为两个阶段,第一个阶段采用高微波功率、低生长气压以促进外延金刚石膜的横向生长,所述微波功率为3~6kw,生长气压为80~160torr,氢气流量为300~800sccm,甲烷浓度在2~8%之间,生长温度为800-1000℃;第二个阶段采用高微波功率、高生长气压以促进外延金刚石膜的高速高质量生长,所述微波功率为3~6kw,生长气压为160~300torr,氢气流量为300~800sccm,甲烷浓度在2~8%之间,生长温度为850-1100℃。
15.有益效果:
16.现有技术条件下,外延生长的单晶金刚石膜剥离时存在材料损耗大、剥离尺寸有限、外延晶体质量降低的问题;本发明技术方案中外延生长的单晶金刚石膜在冷却过程中由于应力的差异而自然剥离,外延生长的晶体质量高,材料损耗小,且不受材料尺寸限制。
附图说明
17.图1为本发明实施例1剥离单晶金刚石膜的工艺流程图。
具体实施方式
18.结合实施例进一步描述本发明,并不以任何方式限制本发明,在不背离本发明的技术解决方案的前提下,对本发明所作的本领域普通技术人员容易实现的任何改动或改变都将落入本发明的权利要求范围之内。
19.实施例1
20.(1)将经过简单抛光及丙酮、乙醇清洗预处理后的单晶金刚石衬底表面旋涂一层1μm厚的光刻胶;(2)在光刻机中将开放窗口宽度为20μm,填充因子为80%的掩膜图形曝光转移到涂有光刻胶的单晶金刚石衬底上;(3)将具有光刻胶图形的单晶金刚石衬底转移到磁控溅射腔体中加热至150℃,并在其表面沉积一层厚度为400nm的au薄膜。(4)使用丙酮等有
机溶剂去除金刚石衬底上的光刻胶,沉积在光刻胶上的au薄膜也将被一起除去,获得具有图形化au掩模的金刚石衬底。(5)采用微波等离子体化学气相沉积法在具有图形化au掩模的金刚石衬底表面进行单晶金刚石的同质外延生长,控制第一个生长阶段的微波功率为5kw,生长气压为120torr,氢气流量为400sccm,甲烷浓度为5%,生长温度为900℃,生长12h后进入到第二个生长阶段,控制第二个生长阶段的微波功率为4.5kw,生长气压为200torr,氢气流量为400sccm,甲烷浓度为8%,生长温度为950℃,继续生长24h,冷却至室温后取出;(6)将生长后的样品浸泡到王水中2h,实现独立的同质外延单晶金刚石膜和原始的单晶金刚石衬底之间的完全剥离。本实施例的工艺流程如图1所示。
21.实施例2
22.(1)将经过简单抛光及丙酮、乙醇清洗预处理后的单晶金刚石衬底表面旋涂一层1.5μm厚的光刻胶;(2)在光刻机中将开放窗口宽度为20μm,填充因子为50%的掩膜图形曝光转移到涂有光刻胶的单晶金刚石衬底上;(3)将具有光刻胶图形的单晶金刚石衬底转移到磁控溅射腔体中加热至150℃,并在其表面沉积一层厚度为300nm的金属mo薄膜。(4)使用丙酮等有机溶剂去除金刚石衬底上的光刻胶,沉积在光刻胶上的mo薄膜也将被一起除去,获得具有图形化mo掩模的金刚石衬底。(5)采用微波等离子体化学气相沉积法在具有图形化mo掩模的金刚石衬底表面进行单晶金刚石的同质外延生长,控制第一个生长阶段的微波功率为5kw,生长气压为120torr,氢气流量为400sccm,甲烷浓度为5%,生长温度为900℃,生长10h后进入到第二个生长阶段,控制第二个生长阶段的微波功率为4.5kw,生长气压为260torr,氢气流量为400sccm,甲烷浓度为8%,生长温度为950℃,继续生长20h,冷却至室温后取出;(6)将生长后的样品浸泡到hf溶液中8h,实现独立的同质外延单晶金刚石膜和原始的单晶金刚石衬底之间的完全剥离。
23.实施例3
24.(1)将经过简单抛光及丙酮、乙醇清洗预处理后的单晶金刚石衬底表面旋涂一层1.5μm厚的光刻胶;(2)在光刻机中将开放窗口宽度为20μm,填充因子为40%的掩膜图形曝光转移到涂有光刻胶的单晶金刚石衬底上;(3)将具有光刻胶图形的单晶金刚石衬底转移到磁控溅射腔体中加热至150℃,并在其表面沉积一层厚度为200nm的sio2薄膜。(4)使用丙酮等有机溶剂去除金刚石衬底上的光刻胶,沉积在光刻胶上的sio2薄膜也将被一起除去,获得具有图形化sio2掩模的金刚石衬底。(5)采用微波等离子体化学气相沉积法在具有图形化sio2掩模的金刚石衬底表面进行单晶金刚石的同质外延生长,控制第一个生长阶段的微波功率为5kw,生长气压为120torr,氢气流量为400sccm,甲烷浓度为5%,生长温度为900℃,生长10h后进入到第二个生长阶段,控制第二个生长阶段的微波功率为4.5kw,生长气压为200torr,氢气流量为400sccm,甲烷浓度为8%,生长温度为950℃,继续生长20h,冷却至室温后取出;(6)将生长后的样品浸泡到王水中8h,实现独立的同质外延单晶金刚石膜和原始的单晶金刚石衬底之间的完全剥离。