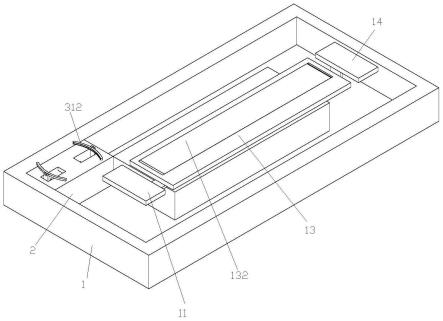
1.本发明属于坩埚制造技术领域,尤其是涉及一种电炉坩埚制备工艺及其加工设备。
背景技术:2.电炉是指引利用电热效应供热的工业电炉和家用电炉。工业电炉又分为电阻炉、感应炉两种,随着现代工业技术的发展感应炉成为电炉中最为节能的电转换加热方式,广泛应用家庭、医药、化工、冶金、等多个领域。电炉具有快速加热、容易控制温度、热效率高等特点,电炉内一般利用坩埚当做容器进行加热。
3.目前,行业里面普遍采用多种方法以实现底部初始形核时形成均匀的小晶粒。虽然行业里各大公司都有自己的方法以实现均匀的小晶粒,但思路基本是一致的,主要是使用底部具有粗糙石英砂颗粒的石英坩埚,并在长晶初级使用冷冲击增大形核量,从而得到均匀的具有一定尺寸大小的小晶粒。
4.但是目前市场上的生产的坩埚及各晶体铸造厂家将注意力集中于解决底部小多晶成核问题,忽略了坩埚侧部由于比较平滑喷涂的氮化硅粉相对致密,在铸锭过程中侧部同样也会成核,由于没有创造类似底部的优良成核条件,初始的形核是随机的、自由的,并不是优化的晶粒和晶向,而且晶粒尺寸不一,局部缺陷密度高,而且侧部生成的大枝晶会挤压底部优良的柱状晶,要么改变原始柱状晶的生长方向,使其斜着生长,增加位错繁殖,要么“吞噬”底部柱状晶,导致底部优良晶粒在竞争生长中失败,弱化底部高效层的作用。而且在喷涂时若将侧部氮化硅涂层喷涂相对疏松不平,虽然为侧部小晶粒成核创造了条件,但是由于坩埚本体中金属杂质远超过氮化硅和硅料中的杂质,通过疏松的氮化硅涂层会源源不断的像晶体中扩散,导致硅片侧部红区较宽。
技术实现要素:5.本发明为了克服现有技术的不足,提供一种电炉坩埚制备工艺及其加工设备。
6.为了实现上述目的,本发明采用以下技术方案:一种电炉坩埚制备工艺,包括以下步骤:
7.a、制备坩埚本体;
8.b、在所述坩埚本体的底壁和侧壁上涂覆石英砂浆,使形成第一涂层;
9.c、在位于所述侧壁上的第一涂层外涂覆氮化硅硅浆液,使形成第二涂层;
10.d、在位于所述底壁上的第一涂层外涂覆氮化硅硅浆液,使形成第三涂层;
11.e、烘干步骤4中的所述坩埚本体;
12.其中,所述氮化硅硅浆液均由混合氮化硅粉、硅溶胶和水混合而成的形成,所述第二涂层与第三涂层中混合氮化硅粉的粒径不同。
13.通过设置第一涂层使得坩埚本体利于多晶铸锭,且可有效降低坩埚本体中的金属杂质向位于坩埚本体内的多晶晶体中扩散;通过设置第二涂层使得为多晶铸锭时侧部小晶
粒成核提供条件,使侧部小晶粒缺陷密度低,对底部柱状晶挤压作用力较小,为底部柱状晶提供更好的垂直生长条件。
14.一种应用于如上述的电炉坩埚制备工艺的加工设备,包括底座和设于所述底座上的载料块,所述底座上设有第一活动槽,所述第一活动槽为回型结构,所述载料块设于所述第一活动槽内;所述载料块上设有第一活动腔,所述第一活动腔顶部设有第一活动槽,所述第一活动腔底部设有设备腔,所述设备腔内设有气缸,所述第一活动腔内设有第一连接板,所述第一连接板上设有第二活动槽,所述第二活动槽内设有夹爪组件;所述底座上方设有第一置料台、第二置料台及第三置料台。
15.所述第二置料台上设有第三活动槽,所述第三活动槽内壁上设有两组第一转辊,所述两组第一转辊上绕设有第一传动带;所述夹爪组件包括设于所述第二活动槽内的活动杆和设于所述活动杆顶部的固定爪,所述活动杆顶部设有第四活动槽,所述第四活动槽内设有第一连接轴,所述固定爪设于所述第一连接轴一端,所述固定爪内壁上设有第五活动槽,所述第五活动槽内设有两组第二转辊,所述两组第二转辊上绕设有第二传动带。
16.所述第二活动槽底部设有第一通槽,所述活动杆侧壁上铰接有第三连接板,所述第三连接板一端铰接有第二连接板,所述第二连接板一端铰接于所述第一通槽内壁上;所述活动杆侧壁上设有第一连接弹簧,所述第一连接弹簧一端固连于所述第二活动槽内壁上,所述第二活动槽内壁上设有第六活动槽,所述第六活动槽内设有第一固定块,所述第六活动槽内壁上设有第七活动槽,所述第七活动槽内设有棘齿板。
17.所述第六活动槽一端设有第三活动腔,所述第一固定块侧壁上设有第二连接弹簧,所述第一固定块上设有第八活动槽,所述第八活动槽内壁上设有第三连接弹簧,所述第三连接弹簧一端设有第二固定块;所述第一连接板顶部设有第一连接块,所述第一连接板底部设有第九活动槽,所述气缸的活塞杆穿设于所述第九活动槽内,所述第九活动槽内设有第一活动块,所述第一活动块底部设有第十活动槽,所述第十活动槽内壁上设有第十一活动槽,所述第十一活动槽内设有第一推板,所述第一推板上设有第一复位弹簧,所述第一推板上设有第一连接绳,所述第一连接绳一端固连于所述第一固定块上;所述第一活动块往上运动时推动所述棘齿板往上运动。
18.所述第七活动槽一端设有第二活动腔,所述棘齿板侧壁上设有第四连接板,所述第一活动块侧壁上设有第二推板,所述第二推板穿设于所述第二活动腔内,所述第四连接板设于所述第二推板上方;所述气缸的活塞杆上设有第一限位块;所述第六活动槽内壁上设有第十二活动槽,所述第一固定块上设有与所述第十二活动槽相对应的第十三活动槽,所述第十二活动槽内设有第五连接板,所述第二固定块上设有第一滑块,所述第五连接板上设有与所述第一滑块相配合的第一滑槽,所述第一连接板侧壁上设有第十四活动槽,所述第十四活动槽内设有活动板,所述活动板上设有第二连接绳,所述第二连接绳一端固连于所述第五连接板上,所述第一活动腔内壁上设有第三推板。
19.所述第一活动腔内壁上设有第十五活动槽,所述第十五活动槽侧壁上设有第十六活动槽,所述第十六活动槽侧壁上设有第十七活动槽,所述第十六活动槽宽度小于所述第十五活动槽宽度,所述第十六活动槽底部设有开口;所述第十七活动槽内设有第二活动块,所述第二活动块上设有第四连接弹簧,所述第四连接弹簧一端设有第一连接杆,所述第一连接杆设于所述第十五活动槽内,所述第一连接杆一端设有第十八活动槽,所述第三推板
可转动连接于所述第十八活动槽内壁上,所述第十八活动槽底部设有支撑板,所述第十五活动槽顶部设有与所述第三推板相配合的凹槽;所述第一连接杆一端设有导杆,所述第二活动块上设有与所述导杆相对应的通孔;所述第十七活动槽侧壁上设有设有第十九活动槽,所述第十九活动槽侧壁上设有第二十活动槽,所述第二十活动槽内设有第二连接杆,所述第二连接杆一端设有第四推板,所述第二连接杆另一端设有第五连接弹簧;所述第一活动腔底部设有与所述第二十活动槽相通的第二十一活动槽,所述第二十一活动槽底部设有第六连接弹簧,所述第六连接弹簧一端设有第一推块。
20.所述第一连接板侧壁上设有第二通槽,所述第二通槽内壁上设有第二十二活动槽,所述第二十二活动槽内设有第八连接弹簧,所述第八连接弹簧一端设有挡板,所述第一活动腔内壁上设有第二十三活动槽,所述第二十三活动槽内壁上设有第七连接弹簧,所述第七连接弹簧一端设有与所述第二通槽相对应的挡块;所述第二十二活动槽上方设有第二十四活动槽,所述第二十四活动槽内设有第三连接杆,所述第三连接杆一端设有第五推板,所述第二十四活动槽侧壁上设有第四活动腔,所述第四活动腔侧壁上设有与所述第六活动槽相通的第二十五活动槽,第二十五活动槽内穿设有第一推杆,所述第四活动腔内设有第一传动杆,所述第一传动杆中部可转动连接于所述第四活动腔内壁上。
21.所述第十活动槽侧壁上设有第三通槽,所述第九活动槽内壁上设有第二十八活动槽,所述第二十八活动槽内设有第二限位块,所述第二限位块底部设有斜槽,所述第二十八活动槽底部设有第五活动腔,所述第二限位块上设有第六连接板,所述第六连接板上设有多个第二复位弹簧;所述挡板底部设有第二连接块,所述第二连接块底部设有第二十六活动槽,所述挡板上设有与所述第二十六活动槽相通的第二十七活动槽,所述第二十七活动槽内设有第二推杆,所述第二十六活动槽内穿设有第三推杆,所述第三推杆上设有第三复位弹簧,所述第三推杆顶端还铰接有第四连接杆,所述第四连接杆另一端铰接于所述第二推杆上,所述第二推杆从所述第二十七活动槽内伸出时,所述第二限位块往所述第二十八活动槽内移动。
22.所述第二十二活动槽内壁上设有第二十九活动槽,所述第二十九活动槽一端设有第五活动腔,所述第五活动腔一端设有第六活动腔,所述第二十九活动槽内设有第六推板,所述第六推板上铰接有第五连接杆,所述第五连接杆一端铰接有第四推杆,所述第四推杆穿设于所述第五活动腔内,所述第六连接板底部设有第六连接杆,所述第六连接杆穿设于所述第六活动腔内,所述第六连接杆一端设有第七连接杆,所述第六活动腔内设有第二传动杆,所述第二传动杆中部可转动连接于所述第六活动腔内壁上;所述第一连接板侧壁上设有空腔,所述空腔侧壁上设有橡胶膜,所述空腔内壁上设有第三十活动槽,所述空腔内设有第七推板,所述第七推板侧壁上设有与所述第三十活动槽相配合的第七连接板,所述第九活动槽底部设有与所述第三十活动槽相通的第三十一活动槽,所述第三十一活动槽底部设有第九连接弹簧,所述第九连接弹簧顶端设有第二推块,所述第七推板上设有第三连接绳,所述第三连接绳一端固连于所述挡板上。
23.本发明具有以下优点:通过设置第一涂层使得坩埚本体利于多晶铸锭,且可有效降低坩埚本体中的金属杂质向位于坩埚本体内的多晶晶体中扩散;通过设置第二涂层使得为多晶铸锭时侧部小晶粒成核提供条件,使侧部小晶粒缺陷密度低,对底部柱状晶挤压作用力较小,为底部柱状晶提供更好的垂直生长条件。
附图说明
24.图1为本发明一种电炉坩埚的加工设备的结构示意图。
25.图2为本发明一种电炉坩埚的加工设备的正视图。
26.图3为图2中沿a-a处的剖视图。
27.图4为图3中的a处放大图。
28.图5为图4中的b处放大图。
29.图6为图2中沿b-b处的剖视图。
30.图7为图6中的c处放大图。
31.图8为图7中的d处放大图。
32.图9为图2中沿c-c处的剖视图。
33.图10为图2中沿n-n处的剖视图。
34.图11为图10中的e处放大图。
35.图12为本发明一种电炉坩埚的加工设备的右视图。
36.图13为图12中沿d-d处的剖视图。
37.图14为图13中的f处放大图。
38.图15为图12中沿e-e处的剖视图。
39.图16为图15中的g处放大图。
40.图17为图16中的h处放大图。
41.图18为图16中的i处放大图。
42.图19为图12中沿f-f处的剖视图。
43.图20为图19中的j处放大图。
44.图21为图12中沿m-m处的剖视图。
45.图22为图21中的k处放大图。
46.图23为图22中的l处放大图。
47.图24为图12中沿g-g处的剖视图。
48.图25为图24中的m处放大图。
49.图26为图12中沿h-h处的剖视图。
50.图27为图26中的n处放大图。
51.图28为图26中的o处放大图。
52.图29为图12中沿j-j处的剖视图。
53.图30为图29中的p处放大图。
54.图31为图29中的q处放大图。
具体实施方式
55.一种电炉坩埚制备工艺,包括以下步骤:
56.a、制备坩埚本体;
57.b、在所述坩埚本体的底壁和侧壁上涂覆石英砂浆,使形成第一涂层;
58.c、在位于所述侧壁上的第一涂层外涂覆氮化硅硅浆液,使形成第二涂层;
59.d、在位于所述底壁上的第一涂层外涂覆氮化硅硅浆液,使形成第三涂层;
60.e、烘干步骤4中的所述坩埚本体;
61.其中,所述氮化硅硅浆液均由混合氮化硅粉、硅溶胶和水混合而成的形成,所述第二涂层与第三涂层中混合氮化硅粉的粒径不同。
62.所述步骤c中的氮化硅硅浆液的制备方法为:将粒径为1μm-3μm的α相氮化硅粉和粒径为13μm-15μm的β相氮化硅粉以1:1-1:1.5的质量比混合形成混合氮化硅粉;将所述混合氮化硅粉、硅溶胶及水按照质量比为2:1:6的比例混合形成混合浆液;将所述混合浆液在25℃-30℃的温度下搅拌0.5h-1h。
63.所述步骤d中的氮化硅硅浆液的制备方法为:将粒径为1.5μm-2μm的α相氮化硅粉和粒径为2.5μm-3μm的β相氮化硅粉以1:1-1:1.5的质量比混合形成混合氮化硅粉;将所述混合氮化硅粉与硅溶胶及水按照质量比为2:1:6的比例混合形成混合浆液;将所述混合浆液在25℃-30℃的温度下搅拌0.5h-1h。
64.在所述第一涂层与第三涂层之间还涂覆第四涂层,所述第四涂层用于避免所述第一涂层中的氧原子向晶体中扩散;所述第四涂层的制备方法为:将硅溶胶与直径为50目-70目的氮化硅颗粒按照2:1的质量比混合后并在25℃-30℃下搅拌0.5h-1h形成混合砂浆,将所述混合砂浆涂覆在位于所述底壁外的第一涂层上后,于100℃-600℃下烧结1h-2h形成所述第四涂层;所述第二涂层和第三涂层均采用十字交叉法进行涂覆。
65.所述坩埚本体在低压浇铸过程中保持坩埚内充型压力和坩埚外炉膛中压力相等,提升坩埚整体品质。
66.如图1-31所示,一种应用于上述的电炉坩埚制备工艺的加工设备,包括底座1和设于所述底座1上的载料块2,所述底座1上设有第一活动槽,所述第一活动槽为回型结构,所述载料块2设于所述第一活动槽内;所述载料块2上设有第一活动腔,所述第一活动腔顶部设有第一活动槽,所述第一活动腔底部设有设备腔,所述设备腔内设有气缸21,所述第一活动腔内设有第一连接板3,所述第一连接板3上设有第二活动槽,所述第二活动槽内设有夹爪组件;所述底座1上方设有第一置料台11、第二置料台13及第三置料台14;第一置料台、第二置料台及第三置料台分别通过安装架安装在底座上,在加工坩埚时,将坩埚放置在载料块上,气缸推动第一连接板往上运动,第一连接板带动夹爪组件往上运动,夹爪组件贴合在坩埚侧壁上固定坩埚,气缸继续驱动第一连接板往上运动,夹爪组件带动坩埚一同往上运动,坩埚从载料块上升起处于悬空状态,载料块带动坩埚往第一置料台方向移动,第第一置料台一端抵在坩埚底部侧壁上,坩埚在第一置料台作用下翻转至水平状态,此时坩埚处于第一置料台上,载料块继续在第一活动槽内移动,坩埚从第一置料台上移动至第二置料台上,操作人员在坩埚内壁上涂覆石英砂浆,在坩埚内壁上形成第一涂层,随后在坩埚内壁和底壁涂覆第二涂层和第三涂层,完成坩埚的制备;涂覆好涂层的坩埚随载料块继续移动,坩埚从第二置料台上移动至第三置料台上,载料块带动坩埚从第三置料台上移下时,坩埚底端先失去支撑力,坩埚底端往下翻转,坩埚从第三置料台上移下后翻转至竖直状态上,气缸驱动第一连接板往下运动,坩埚下降至载料块上后置于载料块上,将坩埚从载料块上取下,完成坩埚的制备;将第一活动槽设置成回型结构,使载料块在将加工完成后的坩埚取下时重新移动至初始位置上,便于载料块的复位。
67.所述第二置料台13上设有第三活动槽,所述第三活动槽内壁上设有两组第一转辊131,所述两组第一转辊131上绕设有第一传动带132;所述夹爪组件包括设于所述第二活动
槽内的活动杆31和设于所述活动杆31顶部的固定爪312,所述活动杆31顶部设有第四活动槽,所述第四活动槽内设有第一连接轴311,所述固定爪312设于所述第一连接轴311一端,所述固定爪312内壁上设有第五活动槽,所述第五活动槽内设有两组第二转辊317,所述两组第二转辊317上绕设有第二传动带313;气缸驱动第一连接板往上运动时,活动杆随第一连接板上升往坩埚方向移动,当第一连接板上升至指定高度后,固定爪夹持在坩埚侧壁上,固定爪固定坩埚后,第一连接板继续上升,坩埚随第一连接板一同上升,将固定位置设置在坩埚中部位置,使坩埚在移动过程中抵在第一置料台上后发生翻转,将坩埚翻转至水平状态上;坩埚从第一置料台上移动至第二置料台上后,第一转辊带动第一传动带转动,第一传动带与坩埚侧壁相接触,第一传动带带动坩埚转动,降低对坩埚内壁的涂覆难度,提升坩埚加工效率;通过将坩埚翻转至水平状态后使坩埚处于转动状态,使坩埚每个侧壁受力均匀,避免涂料产生流挂现象,增加涂层表面的光滑度,提升坩埚成品质量;固定爪通过第一连接轴与活动杆相连,使坩埚在与第一传动带接触时正常转动,同时对坩埚起定位作用,避免坩埚从第二置料台上掉落。
68.所述第二活动槽底部设有第一通槽,所述活动杆31侧壁上铰接有第三连接板315,所述第三连接板315一端铰接有第二连接板316,所述第二连接板316一端铰接于所述第一通槽内壁上;所述活动杆31侧壁上设有第一连接弹簧314,所述第一连接弹簧314一端固连于所述第二活动槽内壁上,所述第二活动槽内壁上设有第六活动槽,所述第六活动槽内设有第一固定块39,所述第六活动槽内壁上设有第七活动槽,所述第七活动槽内设有棘齿板320;第一连接板处于第一活动腔底部时,第三连接板和第二连接板抵在第一活动腔底部,第三连接板推动活动杆往第二活动槽一端移动,使固定爪处于分开状态,以便将坩埚放置到载料块上;第一连接板往上运动时,第一连接弹簧拉动活动杆往第二活动槽一端移动,第三连接板和第二连接板从第一通槽内穿出,固定爪往坩埚方向移动,固定爪抵在坩埚上后,第一固定块往活动杆方向移动,棘齿板从第七活动槽内升起与第一固定块相接触,第一固定块抵在活动杆侧壁上,棘齿板抵在第一固定块上,棘齿板将第一固定块固定,第一固定块为活动杆提供支撑效果,将活动杆固定在第二活动槽一端,保证固定爪对坩埚的固定效果。
69.所述第六活动槽一端设有第三活动腔,所述第一固定块39侧壁上设有第二连接弹簧394,所述第一固定块39上设有第八活动槽,所述第八活动槽内壁上设有第三连接弹簧392,所述第三连接弹簧392一端设有第二固定块391;所述第一连接板3顶部设有第一连接块32,所述第一连接板3底部设有第九活动槽,所述气缸21的活塞杆穿设于所述第九活动槽内,所述第九活动槽内设有第一活动块33,所述第一活动块33底部设有第十活动槽,所述第十活动槽内壁上设有第十一活动槽,所述第十一活动槽内设有第一推板332,所述第一推板332上设有第一复位弹簧333,所述第一推板332上设有第一连接绳,所述第一连接绳一端固连于所述第一固定块39上;所述第一活动块33往上运动时推动所述棘齿板320往上运动;第一连接板处于第一活动腔底部时,第二固定块处于第八活动槽内,第一固定块处于第三活动腔内,第二固定块抵在第三活动腔内壁上,活动杆可在第二活动槽内正常移动;气缸驱动第一连接板上升时,气缸推动第一活动块往上运动,第一活动块推动棘齿板往上运动,棘齿板从第七活动槽内升起与第一固定块接触,此时第一活动块抵在第九活动槽顶部,气缸的活塞杆继续伸出时推动第一推板往上运动,第一推板相对于第一活动块移动,第一连接绳拉动第一固定块移动,第一固定块从第三活动腔内移出时,第二固定块从第八活动槽内伸
出,第二固定块伸入到第二活动槽内,第一固定块移动至第六活动槽一端时,第二固定块抵在活动杆侧壁上,为活动杆提供固定力,提升坩埚加工过程中的稳定性。
70.所述第七活动槽一端设有第二活动腔,所述棘齿板320侧壁上设有第四连接板,所述第一活动块33侧壁上设有第二推板331,所述第二推板331穿设于所述第二活动腔内,所述第四连接板设于所述第二推板331上方;所述气缸21的活塞杆上设有第一限位块211;所述第六活动槽内壁上设有第十二活动槽,所述第一固定块39上设有与所述第十二活动槽相对应的第十三活动槽,所述第十二活动槽内设有第五连接板310,所述第二固定块391上设有第一滑块393,所述第五连接板310上设有与所述第一滑块393相配合的第一滑槽,所述第一连接板3侧壁上设有第十四活动槽,所述第十四活动槽内设有活动板330,所述活动板330上设有第二连接绳,所述第二连接绳一端固连于所述第五连接板310上,所述第一活动腔内壁上设有第三推板253;气缸活塞杆抵在第一推板底部时,第一推板带动第一活动块往上运动,第二推板推动第四连接板往上运动,第四连接板带动棘齿板往上运动,棘齿板从第七活动槽内伸出,为移动后的第一固定块提供固定效果;第一固定块从第三活动腔内移出后,第二固定块移动带动第五连接板移动,当第一连接板下降时,活动板抵在第三推板上,第三推板为活动板下降提供阻力,第一连接板相对于活动板往下运动,第二连接绳拉动第五连接板移动,第五连接板带动第二固定块移动,使第二固定块重新进入到第八活动槽内,棘齿板往下运动与第一固定块底面脱开接触,使第一固定块在第二连接弹簧作用下复位。
71.所述第一活动腔内壁上设有第十五活动槽,所述第十五活动槽侧壁上设有第十六活动槽,所述第十六活动槽侧壁上设有第十七活动槽,所述第十六活动槽宽度小于所述第十五活动槽宽度,所述第十六活动槽底部设有开口;所述第十七活动槽内设有第二活动块25,所述第二活动块25上设有第四连接弹簧251,所述第四连接弹簧251一端设有第一连接杆252,所述第一连接杆252设于所述第十五活动槽内,所述第一连接杆252一端设有第十八活动槽,所述第三推板253可转动连接于所述第十八活动槽内壁上,所述第十八活动槽底部设有支撑板,所述第十五活动槽顶部设有与所述第三推板253相配合的凹槽;所述第一连接杆252一端设有导杆254,所述第二活动块25上设有与所述导杆254相对应的通孔;所述第十七活动槽侧壁上设有设有第十九活动槽,所述第十九活动槽侧壁上设有第二十活动槽,所述第二十活动槽内设有第二连接杆261,所述第二连接杆261一端设有第四推板26,所述第二连接杆261另一端设有第五连接弹簧262;所述第一活动腔底部设有与所述第二十活动槽相通的第二十一活动槽,所述第二十一活动槽底部设有第六连接弹簧241,所述第六连接弹簧241一端设有第一推块24;第二活动块底部设有支撑弹簧255;第一连接板往上运动时,第二活动块处于第十七活动槽顶部,第一连接杆抵在第十五活动槽内壁上,第三推板从第十五活动槽内伸出,活动板处于第十四活动槽底部,活动板移动至第三推板底部后推动第三推板往上翻转,第三进入到凹槽内,第一连接板从第三推板一侧正常经过;第一连接板往下运动时,活动板抵在第三推板上,支撑弹簧为第二活动块提供支撑力,第三推板抵在支撑板上无法往下翻转,第一连接板相对于活动板往下运动,第二连接绳拉动第五连接板移动使第二固定块进入到第八活动槽内;活动板移动至第十四活动槽顶部后第一连接板继续往下运动,活动板推动第三推板往下运动,导杆和通孔配合使第一连接杆往下运动时带动第二活动块往下运动,第一连接杆移动至第十五活动槽底部后,第四连接弹簧拉动第一连接杆往开口内移动,第三推板进入到第十五活动槽内,活动板从第三推板一侧经过,使第一连接
板正常下降;第一连接板移动至第一活动腔底部后,第一连接板推动第一推块往下运动,第一推块将第二十一活动槽内的空气推入到第二十活动槽内,气压推动第二连接杆移动,第四推板推动导杆往前移动,第一连接杆被推入到第十五活动槽内,支撑弹簧推动第二活动块往上运动,完成第二活动块和第三推板的复位。
72.所述第一连接板3侧壁上设有第二通槽,所述第二通槽内壁上设有第二十二活动槽,所述第二十二活动槽内设有第八连接弹簧344,所述第八连接弹簧344一端设有挡板34,所述第一活动腔内壁上设有第二十三活动槽,所述第二十三活动槽内壁上设有第七连接弹簧231,所述第七连接弹簧231一端设有与所述第二通槽相对应的挡块23;所述第二十二活动槽上方设有第二十四活动槽,所述第二十四活动槽内设有第三连接杆351,所述第三连接杆351一端设有第五推板35,所述第二十四活动槽侧壁上设有第四活动腔,所述第四活动腔侧壁上设有与所述第六活动槽相通的第二十五活动槽,第二十五活动槽内穿设有第一推杆350,所述第四活动腔内设有第一传动杆3501,所述第一传动杆3501中部可转动连接于所述第四活动腔内壁上;气缸驱动第一连接板往上运动时,气缸的活塞杆抵在第一推板上,第一推板带动整个第一活动块往上运动,棘齿板升起,第一活动块抵在第九活动槽顶部后,第一活动块带动第一连接板一同往上运动,此时固定爪未与坩埚侧壁接触;第一连接板移动至挡块下方时,固定爪在第四连接弹簧作用下抵在坩埚侧壁上,第一连接板继续上升时,挡块抵在挡板上,第一连接板无法继续上升,气缸推动第一推板相对于第一活动块往上运动,第一连接绳拉动第一固定块移动,第一固定块移动至第六活动槽一端推动第一推杆移动,此时第一固定块已为活动杆提供固定力;第一推杆推动第一传动杆转动,第一传动杆转动推动第三连接杆移动,第五推板往第二通槽一侧移动将挡块推入到第二十三活动槽内,第一连接板继续上升,此时固定爪已抵在坩埚侧壁上固定坩埚,第一连接板带动坩埚一同往上运动,将坩埚举起,使坩埚移动至第一置料台处时自动翻转。
73.所述第十活动槽侧壁上设有第三通槽,所述第九活动槽内壁上设有第二十八活动槽,所述第二十八活动槽内设有第二限位块38,所述第二限位块38底部设有斜槽,所述第二十八活动槽底部设有第五活动腔,所述第二限位块38上设有第六连接板381,所述第六连接板381上设有多个第二复位弹簧382;所述挡板34底部设有第二连接块341,所述第二连接块341底部设有第二十六活动槽,所述挡板34上设有与所述第二十六活动槽相通的第二十七活动槽,所述第二十七活动槽内设有第二推杆345,所述第二十六活动槽内穿设有第三推杆342,所述第三推杆342上设有第三复位弹簧343,所述第三推杆342顶端还铰接有第四连接杆346,所述第四连接杆346另一端铰接于所述第二推杆345上,所述第二推杆345从所述第二十七活动槽内伸出时,所述第二限位块38往所述第二十八活动槽内移动;挡块抵在挡板上时,气缸推动第一推板相对于第一活动块往上运动,气缸的活塞杆移动至第十活动槽顶部,第一限位块抵在第二限位块底部的斜槽上推动第二限位块移动,当第一固定块移动至第六活动槽一端时,第一限位块移动至第二限位块顶部,在第一限位块和第二限位块配合下将气缸的活塞杆固定在第十活动槽内的当前位置上,避免第一固定块在载料块移动时发生移动,保证坩埚加工过程中的安全性;第一连接板往下运动时,第二连接块抵在挡块顶部,挡块推动第三推杆往上运动,第三推杆移动带动第四连接杆转动,第四连接杆推动第二推杆移动,第二推杆移动后第二限位块进入到第二十八活动槽内,气缸的活塞杆失去固定后相对第一活动块往下运动,第一固定块往回移动复位,完成第一固定块的复位。
74.所述第二十二活动槽内壁上设有第二十九活动槽,所述第二十九活动槽一端设有第五活动腔,所述第五活动腔一端设有第六活动腔,所述第二十九活动槽内设有第六推板340,第六推板上设有第四复位弹簧3401,所述第六推板340上铰接有第五连接杆3402,所述第五连接杆3402一端铰接有第四推杆3403,所述第四推杆3403穿设于所述第五活动腔内,所述第六连接板381底部设有第六连接杆383,所述第六连接杆383穿设于所述第六活动腔内,所述第六连接杆383一端设有第七连接杆384,所述第六活动腔内设有第二传动杆385,所述第二传动杆385中部可转动连接于所述第六活动腔内壁上;所述第一连接板3侧壁上设有空腔,所述空腔侧壁上设有橡胶膜36,所述空腔内壁上设有第三十活动槽,所述空腔内设有第七推板37,所述第七推板37侧壁上设有与所述第三十活动槽相配合的第七连接板371,所述第九活动槽底部设有与所述第三十活动槽相通的第三十一活动槽,所述第三十一活动槽底部设有第九连接弹簧221,所述第九连接弹簧221顶端设有第二推块22,所述第七推板37上设有第三连接绳,所述第三连接绳一端固连于所述挡板34上;第一连接板往下运动时,第三推杆抵在挡块顶部,第三推杆移动推动第二推杆移动,第二推杆伸入到第二十九活动槽内推动第六推板移动,第六推板带动第五连接杆转动,第五连接杆推动第四推杆移动,第四推杆推动第二传动杆转动,第二传动杆推动第七连接杆移动,第七连接杆带动第二限位块移动,第二限位块进入到第二十八活动槽内,气缸活塞杆移动至第九活动槽底部,第一固定块往回移动,第一固定块失去对活动杆的固定作用,此时坩埚处于载料块上,减小固定爪对坩埚侧壁的挤压力,使固定爪可相对于坩埚进行移动;第一限位块推动第二推块往下运动,第二推块将第三十一活动槽内的空气推入到的第三十活动槽内,气压推动第七连接板移动,第七推板往橡胶膜方向移动,空腔内空气挤压橡胶膜,橡胶膜膨胀抵在第一活动腔内壁上,第三连接绳拉动挡板往第二十二活动槽内移动,挡板进入到第二十二活动槽内后挡块从第二通槽内经过,此时橡胶膜仍抵在第一活动腔内壁上,第一限位块抵在第九活动槽底部带动第一连接板往下运动,完成第一连接板复位。
75.第三置料台端面上可设置橡胶垫结构,避免翻转后的坩埚撞击在第三置料台端面上损坏。
76.本发明附图仅为示意图,其具体尺寸以实际实施为准。