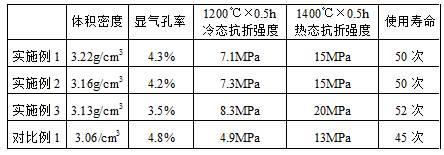
1.本发明涉及耐材领域,尤其是涉及一种提高低碳镁碳砖性能的方法。
背景技术:2.随着炉外精炼和连铸技术的发展,钢包已由单纯的盛装钢水容器逐渐转变为功能复杂的炉外钢水精炼设备。钢水在钢包内停留时间的延长和出钢温度的提高使得钢包的工作环境变得更加苛刻。
3.碳复合耐火材料(如铝镁碳砖、镁碳砖等)具有优异的导热性,较好的抗热震性、抗渣性和高温性能,并已被广泛应用于钢铁工业的各个环节的冶金炉中,如国内钢包普遍采用碳含量在10wt%以上的镁铝碳砖。然而,使用时发现这种耐火材料不仅会导致钢包内衬热导率高、钢水温降快,还会导致钢水增碳,不适应冶炼硅钢、桥梁钢、汽车板钢等低碳、超低碳高端钢的生产,还会导致耐火材料抗氧化性差,降低其使用性能和寿命。因此,镁碳砖的低碳化成为钢包渣线耐火材料的重要发展方向。
4.目前,低碳镁碳砖由于自身导热系数和总碳含量下降、降低对钢水的增碳等优越性而受到各界的高度关注。然而,单纯降低镁碳砖中的碳含量将会导致材料的抗渣性、抗热震性及抗冲刷性均恶化,缩短使用寿命,不能完全满足钢包精炼生产的要求。另外,现有低碳镁碳砖的酚醛树脂结合剂尽管有超过40%的残炭率,但其热解炭的抗氧化性低、脆性大,限制了其在低碳镁碳砖中的应用价值。
技术实现要素:5.有鉴于此,本发明提供了一种提高低碳镁碳砖性能的方法。
6.为实现上述目的,本发明采取下述技术方案:本发明所述的提高低碳镁碳砖性能的方法,向碳含量2wt-6wt%的低碳镁碳砖基体原料中添加复合细粉;其中,所述低碳镁碳砖基体原料中的结合剂为液体树脂,且所述液体树脂中添加有8wt%-15wt%的硼/氧化铜;所述复合细粉的用量为低碳镁碳砖基体原料和复合细粉总和的1wt%-3wt%;复合细粉的制备方法为:第一步,用蒸馏水溶解柠檬酸铜和铜锰合金,加入金属硅粉,搅拌,于110℃干燥2-5h,得到复合硅粉;第二步,将复合硅粉和酚醛树脂粉按1:1的重量比混合均匀,得到复合细粉。
7.优选地,所述第一步中柠檬酸铜和铜锰合金的重量之和是金属硅粉重量的1wt%。
8.优选地,所述金属硅粉中si≥99%,粒度为100-200目;所述酚醛树脂粉的残余碳≥46wt%,粒度《75μm;所述柠檬酸铜的纯度≥99%。
9.优选地,所述铜锰合金含有28.0-31.0%mn、0.9%fe、0.1%sb、0.1%p,余量为cu。
10.优选地,所述液体树脂为液体酚醛树脂,其残余碳≥45wt%,固含量≥75wt%。
11.优选地,所述液体树脂中硼/氧化铜的添加量为10wt%,硼/氧化铜中硼≥8%。
12.与含过渡金属铁钴镍催化剂相比,本发明基于化学气相沉积原理的含铜复合催化原位形成sic/sio2微纳米纤维网络增强低碳镁碳砖的性能。
13.与传统低碳镁碳砖相比,低碳镁碳砖在现场烘烤时的中温区间(1100~1200℃)的强度等综合性能薄弱。而采用本发明方法制备得到的低碳镁碳砖在钢包使用时,利用钢包的烘烤温度(1100~1200℃),可形成sic/sio2纳米线和微纳米纤维的复合网络,有效提高了低碳镁碳砖的性能。具体地:本发明的硼/氧化铜作为催化剂,可加快sic/sio2微纳米纤维网络的形成。本发明的柠檬酸铜衍生的铜相和铜锰合金可以溶解硅而生成cu/si合金,从而降低气相氧化硅的形成温度,增加了中温(1100-1200℃)下气相氧化硅的含量。在柠檬酸铜和铜锰合金的作用下,酚醛树脂的键合相由单一碳键转变为c/sic结合碳陶瓷键合相,同时逐步形成sic/sio2纳米线(纳米线的直径约为80-150nm)和微纳米纤维的复合网络。一方面将低碳镁碳砖内部的孔隙堵塞,氧分压将降低,碳键合相和陶瓷键合相的形成阻碍了材料与周围气体之间的氧交换,并保护石墨免受严重氧化;另一方面,sic/sio2纳米线和微纳米纤维的复合网络陶瓷结合相的形成有效地改善材料的力学性能。
14.本发明通过向低碳镁碳砖基体原料中添加复合细粉和硼/氧化铜有效增强了低碳镁碳砖的力学性能。经测试,与现有低碳镁碳砖相比,本发明制备得到的低碳镁碳砖的1200℃
×
2h烧后冷态抗折强度提升20%,1400℃
×
0.5h热态抗折强度提升10%;将本发明的低碳镁碳砖应用于180t以上吨位的精炼钢包,平均使用寿命可提升10%以上,具有重要的推广价值。
具体实施方式
15.下面结合具体实施例对本发明作进一步说明。需要指出的是,以下实施例中的各原料均为现有市售产品。
16.本发明提供了一种提高低碳镁碳砖性能的方法,向碳含量2wt-6wt%的低碳镁碳砖基体原料中添加复合细粉;其中,低碳镁碳砖基体原料中的结合剂为液体树脂,且液体树脂中添加有8wt%-15wt%的硼/氧化铜;复合细粉的用量为低碳镁碳砖基体原料的1wt%-3wt%,其制备方法为:第一步,用蒸馏水溶解柠檬酸铜和铜锰合金,加入金属硅粉,搅拌,于110℃干燥2-5h,得到复合硅粉;其中,复合硅粉中柠檬酸铜、铜锰合金和金属硅粉的重量份配比为:(柠檬酸铜+铜锰合金):金属硅粉=1:100;第二步,将复合硅粉和酚醛树脂粉按1:1的重量比混合均匀,得到复合细粉。
17.本发明复合细粉中柠檬酸铜衍生的铜相和铜锰合金可以溶解硅而生成cu/si合金,从而降低气相氧化硅的形成温度,增加了中温(1100-1200℃)下气相氧化硅的含量。在柠檬酸铜和铜锰合金的作用下,酚醛树脂的键合相由单一碳键转变为c/sic结合碳陶瓷键合相,同时逐步形成sic/sio2纳米线(纳米线的直径约为80-150nm)和微纳米纤维的复合网络,一方面将低碳镁碳砖内部的孔隙堵塞,氧分压将降低,碳键合相和陶瓷键合相的形成阻碍了材料与周围气体之间的氧交换,并保护石墨免受严重氧化;另一方面,sic/sio2纳米线和微纳米纤维的复合网络陶瓷结合相的形成有效地改善材料的力学性能。
18.优选地,金属硅粉中si≥99%,粒度为100-200目;所述酚醛树脂粉的残余碳≥
46wt%,粒度《75μm;所述柠檬酸铜的纯度≥99%。所述铜锰合金含有28.0-31.0%mn、0.9%fe、0.1%sb、0.1%p,余量为cu。
19.优选地,液体树脂为液体酚醛树脂,其残余碳≥45wt%,固含量≥75wt%。更优选地,液体树脂中硼/氧化铜的添加量为10wt%,硼/氧化铜中硼≥8%。
20.与含过渡金属铁钴镍催化剂相比,本发明基于化学气相沉积原理的含铜复合催化原位形成sic/sio2微纳米纤维网络增强低碳镁碳砖的性能。
21.与传统低碳镁碳砖相比,低碳镁碳砖在现场烘烤时的中温区间(1100~1200℃)的强度等综合性能薄弱。而采用本发明方法制备得到的低碳镁碳砖在钢包使用时,利用钢包的烘烤温度(1100~1200℃),可形成sic/sio2纳米线和微纳米纤维的复合网络,有效提高了低碳镁碳砖的性能。经测试,与现有低碳镁碳砖相比,本发明制备得到的低碳镁碳砖的1200℃
×
2h烧后冷态抗折强度提升20%,1400℃
×
0.5h热态抗折强度提升10%;将本发明的低碳镁碳砖应用于180t以上吨位的精炼钢包,平均使用寿命可提升10%以上,具有重要的推广价值。
22.实施例1本实施例通过向碳含量为2wt%的低碳镁碳砖基体原料中添加2wt%的复合细粉和硼/氧化铜提高低碳镁碳砖的性能,且低碳镁碳砖的基体原料和复合细粉的总和为100wt%。具体包括以下内容:碳含量为2wt%的低碳镁碳砖的基体原料的配方为:97电熔镁砂:5-3mm 28wt%、3-1mm 28wt%、1-0mm 18wt%和200目17wt%;金属铝1wt%;金属硅1wt%;石墨1.5wt%;炭黑0.5wt%;液体树脂(含硼/氧化铜)3wt%;上述液体树脂(优选液体酚醛树脂,型号:圣泉pf5323)中残余碳≥45wt%,固含量≥75wt%;液体树脂中添加有10wt%的硼/氧化铜(硼≥8%);在制砖时,向碳含量为2wt%的低碳镁碳砖的基体原料添加2wt%的复合细粉(复合细粉和低碳镁碳砖基体原料之和为100%),复合细粉的制备方法为:第一步,用蒸馏水溶解柠檬酸铜(柠檬酸铜的纯度≥99%),加入铜锰合金(铜锰合金含有28.0-31.0%mn、0.9%fe、0.1%sb、0.1%p,余量为cu)和金属硅粉(金属硅粉中si≥99%,粒度为100-200目),搅拌,于110℃干燥3h,得复合硅粉;其中,柠檬酸铜:铜锰合金:金属硅粉(重量比)=0.7:0.3:100;第二步,将复合硅粉和酚醛树脂粉(酚醛树脂粉的残余碳≥46wt%,粒度《75μm,型号:圣泉pf4112)按1:1的重量比混合均匀即得复合细粉。
23.本实施例低碳镁碳砖的制备方法是:将2wt%的复合细粉添加到碳含量为2wt%的低碳镁碳砖基体原料中,机压成型,200℃下烘烤8h,制得低碳镁碳砖。
24.经测试,本实施例制得的低碳镁碳砖的体积密度3.22g/cm3、显气孔率4.3%、1200℃
×
2h烧后冷态抗折强度7.1mpa、1400℃
×
0.5h热态抗折强度15mpa;将本实施例的低碳镁碳砖应用于180t精炼钢包的工作衬砖,平均使用寿命可达50次。
25.实施例2本实施例通过向碳含量为3.5wt%的低碳镁碳砖基体原料中添加1.5wt%的复合细粉和硼/氧化铜提高低碳镁碳砖的性能,且低碳镁碳砖的基体原料和复合细粉的总和为100wt%。具体包括以下内容:
低碳镁碳砖(碳含量为3.5wt%)的基体原料的配方如下:97电熔镁砂:5-3mm 28wt%、3-1mm 28wt%、1-0mm 18wt%、200目15.5wt%;金属铝1.5wt%;金属硅1wt%;石墨2.5wt%;炭黑1wt%;液体树脂(含硼/氧化铜)3wt%;本实施例中低碳镁碳砖基体原料中的液体树脂同实施例1;在制砖时,向低碳镁碳砖的基体原料中添加1.5wt%的复合细粉(复合细粉和低碳镁碳砖基体原料之和为100%)。
26.本实施例复合细粉与实施例1中复合细粉的唯一不同之处在于柠檬酸铜、铜锰合金和金属硅粉的重量比不同。具体地,本实施例中柠檬酸铜、铜锰合金和金属硅粉的重量比为0.5:0.5:100。
27.本实施例低碳镁碳砖的制备方法是:将本实施例的复合细粉添加到本实施例的低碳镁碳砖基体原料中,机压成型,200℃下烘烤8h,制得低碳镁碳砖。
28.经测试,本实施例的成品低碳镁碳砖的体积密度3.16g/cm3、显气孔率4.2%、1200℃
×
2h烧后冷态抗折强度7.3mpa、1400℃
×
0.5h热态抗折强度15mpa;将成品低碳镁碳砖应用于180t精炼钢包的工作衬砖,平均使用寿命可达50次。
29.实施例3本实施例通过向碳含量为6wt%的低碳镁碳砖基体原料中添加1wt%的复合细粉和硼/氧化铜提高低碳镁碳砖的性能,且低碳镁碳砖的基体原料和复合细粉的总和为100wt%。具体包括以下内容:本实施例的碳含量为6wt%的低碳镁碳砖基体原料的配方如下:97电熔镁砂:5-3mm 28wt%、3-1mm 26wt%、1-0mm 17wt%、200目16wt%;金属铝2wt%;金属硅1wt%;石墨5wt%;炭黑1wt%;液体树脂(含硼/氧化铜)3wt%;本实施例中的液体树脂同实施例1;在制砖时,向碳含量为6wt%的低碳镁碳的基体原料中添加1wt%的复合细粉(复合细粉和低碳镁碳砖基体原料之和为100%)。
30.本实施例中复合细粉与实施例1中复合细粉的唯一不同之处在于柠檬酸铜、铜锰合金和金属硅粉的重量比不同。本实施例中柠檬酸铜、铜锰合金和金属硅粉的重量比为0.4:0.6:100。
31.本实施例低碳镁碳砖的制备方法是:将本实施例的复合细粉添加到本实施例的低碳镁碳砖基体原料中,机压成型,200℃下烘烤8h,制得低碳镁碳砖。
32.经测试,本实施例的低碳镁碳砖的体积密度3.13g/cm3、显气孔率3.5%、1200℃
×
2h烧后冷态抗折强度8.3mpa、1400℃
×
0.5h热态抗折强度20mpa。将本实施例的低碳镁碳砖应用于200t精炼钢包的工作衬砖,平均使用寿命可达52次。
33.对比例1本发明以不添加硼/氧化铜和复合细粉的低碳镁碳砖(碳含量2wt%)作为对比例1。对比文件1中低碳镁碳砖的基体原料配方同实施例1,并且基体原料配方中的液体树脂中不添加硼/氧化铜。
34.低碳镁碳砖的制备方法是:将原料混合后挤压成型,200℃下烘烤8h。
35.经测试,本对比例成品低碳镁碳砖的体积密度3.06 g/cm3、显气孔率4.8%、1200℃
×
2h烧后冷态抗折强度4.9mpa、1400℃
×
0.5h热态抗折强度13 mpa。将其应用于180t精炼
钢包的工作衬砖,平均使用寿命为45次。
36.将上述实施例1-3和对比例1制得的低碳镁碳砖的性能汇总到表1中。
37.表1从表1可以看出,实施例1-3中的低碳镁碳砖的体积密度明显大于对比例1;实施例1-3的显气孔率也明显高于对比例1;实施例1-3的1400℃
×
0.5h热态抗折强度远远大于对比例1,添加有本发明复合细粉的低碳镁碳砖的1400℃
×
0.5h热态抗折强度提升了10%以上;与对比例1相比,添加有本发明复合细粉的低碳镁碳砖的1200℃
×
0.5h冷态抗折强度提升了20%以上。
38.以上仅为本发明的优选实施例,并非因此限制本发明的专利范围,凡是利用本发明说明书内容所作的等效结构或等效流程变换,或直接或间接运用在其他相关的技术领域,均同理包括在本发明的专利保护范围内。