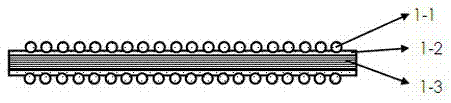
本发明涉及高分子材料
技术领域:
,具体涉及一种非热压罐预浸料的制造工艺。
背景技术:
:随着时代的发展,复合材料的需求量与日俱增,越来越多的复合材料用于包括航天航空、轨道交通在内的一些领域。随之而来的就是复合材料的成本越来越引人关注,如何减少复合材料的成本是很大的实际使用问题,不管是材料还是成型工艺。非热压罐固化(ooa)预浸料是一种只需使用烘箱固化就能达到使用热压罐固化相当性能的新型预浸料,这样大大减少了热压罐固化的成本。目前市场已经有很多成熟的预浸料,如cytec的mtm44-1和mtm45-1等。但对于这种材料,主要的问题在于如何减少固化中的孔隙率。一般来说,固化中孔隙率的产生主要分为树脂反应挥发的气体和铺贴过程中引入在层间的空气。目前,主流的研究方向是在预浸料中引入干纱气道以方便排出树脂反应挥发的气体。而对于铺贴过程中引入再层间的气体研究很少。同时,高韧性树脂,特别是高温固化树脂,由于添加了大量的增韧剂而有高树脂粘度的特点,树脂流动性,涂膜和预浸料工艺难度较大,更甚的可能需要对常规设备进行重大改造或重新采购新设备,成本大。因此,高韧性预浸料的制造成本会相比常规预浸料制造成本大很多,更不用说高韧性ooa预浸料的制造成本。因此很有必要研究一种低成本的适合高韧性ooa预浸料的制造工艺。技术实现要素:本发明的目的是提供一种高韧性非热压罐固化预浸料的生产工艺,其降低高韧性ooa预浸料批量制造和使用过程中的难度,适用于中温和高温固化树脂。为了达到以上目的,本发明的技术解决方案如下:一种高韧性非热压罐固化预浸料的生产工艺,使用添加了功能颗粒的树脂来制造树脂膜或者直接将功能颗粒添加到树脂膜表面,然后再在常规含浸设备上制造预浸料,具体生产工艺步骤根据树脂配方分为两种方法:a.包括添加功能颗粒的树脂b:使用所述树脂b直接涂膜制成树脂膜,然后与纤维在设备上含浸制成预浸料;b.包括未添加功能颗粒的树脂c:使用所述树脂c边涂膜边添加功能颗粒在树脂膜表面,然后将生产好的树脂膜e与纤维在设备上含浸制成预浸料。本发明的进一步改进在于:所述功能颗粒a为聚砜、聚醚砜、聚醚酮、聚醚醚酮、聚醚酰亚胺、聚苯醚、改性聚芳醚砜、核壳橡胶粒子中的一种或多种按一定比例组合的颗粒混合物。本发明的进一步改进在于:所述功能颗粒在所述树脂b中和在所述树脂c中均可以对原树脂进行增韧,其中所述功能颗粒的平均粒径为20~100μm,优选30~50μm。在环境温度低于固化温度的条件下,所述功能颗粒不会与树脂b或树脂c反应或互溶。而在固化温度下所述功能颗粒可直接原位增韧,或者溶解进树脂b或树脂c然后再析出,对原树脂进行增韧。其中树脂b和树脂c可在中温(120℃左右)或高温(180℃左右)下固化。本发明的进一步改进在于:所述树脂b或所述树脂c为环氧树脂、双马来酰亚胺树脂、氰酸酯树脂中的一种。本发明的进一步改进在于:所述树脂b中含有至少一种功能颗粒,所有功能颗粒占整个树脂质量比为3%~15%,优选5~10%。本发明的进一步改进在于:所述树脂b和所述树脂c中,其增韧剂占整个树脂质量比为0%~30%。本发明的进一步改进在于:所述b方法中,所述功能颗粒采用喷射、振动撒粉或粉末涂覆的方式添加到树脂c的树脂膜表面,添加量占树脂膜总克重的3%~15%,优选5~10%,该树脂膜为单面膜或双面膜形式。本发明的进一步改进在于:所述树脂膜浸润纤维的程度通过液体浸润法进行测试,单向预浸料的树脂浸润程度为95%以上,以保证预浸料中尽可能少的空气;织物预浸料的树脂浸润程度为10~40%,尽可能增加固化过程中排气的气道。本发明的进一步改进在于:所述碳纤维形式为碳纤维束、单向织物、平纹织物、斜纹织物、缎纹织物、经编织物或碳纤维与其它纤维混编织物中的一种,其纤维面密度为75~900gsm。本发明的进一步改进在于:所述树脂膜在浸润纤维后,因为功能颗粒的粒径足够大,所述功能颗粒会被纤维束过滤而留在预浸料表面,形成表面凸起,当两层预浸料相互铺贴时,功能颗粒形成的表面凸起会阻碍两层预浸料紧密结合,形成一定的空气通道,大大减少了铺贴过程中引入的空气而避免制件高孔隙率。本发明的有益效果是:本发明提供的一种高韧性非热压罐固化预浸料的生产工艺,具有如下优点:1.经本工艺制造的预浸料,不但能满足前期树脂配方设计高韧性的需求,而且可以满足后期使用非热压罐固化工艺达到与热压罐固化性能相当的要求。2.本发明中功能颗粒可以对树脂进行增韧。因此不管是单独添加功能颗粒在树脂膜表面,还是直接添加功能颗粒在树脂中,功能颗粒在后期固化过程中都可以为树脂增韧。而对于一些高粘度的高韧性树脂,单独添加功能颗粒到树脂膜表面,可以大大降低了涂膜工艺难度和随之而来的成本增加。3.功能颗粒添加在预浸料表面形成表面凸起,能够帮助预压实过程中将铺贴引入的空气排出,降低制件孔隙率和固化难度,从而一定程度上有助于提高预浸料的工艺寿命。4.本工艺制造的预浸料表面分布着功能颗粒,可以一定程度上降低预浸料表面的粘性,减小气体引入几率。同时可以通过改变预浸料的浸润程度来调整预浸料粘性,特别是织物预浸料,可以适用于不同结构件的需求。附图说明图1是新型高温固化的高韧性ooa双马预浸料。图1中,1-1为聚醚醚酮颗粒,1-2为双马树脂,1-3为碳纤维斜纹织物。图2是新型高韧性ooa预浸料的涂膜过程。图2中,2-1为涂膜辊,2-2为双马树脂,2-3为初步树脂膜,2-4为冷却板,2-5为测厚仪,2-6为聚醚醚酮颗粒,2-7为粉末涂布辊,2-8为加热板,2-9为橡胶压辊,2-10为带有功能颗粒的树脂膜。图3是ooa预浸料铺贴过程图。图3中,3-1为聚醚醚酮颗粒,3-2为气道,3-3为碳纤维斜纹织物。3-4为双马树脂。图4是新型中温固化的高韧性ooa环氧预浸料。图4中,4-1为核壳橡胶粒子,4-2为环氧树脂,4-3为碳纤维束。图5是ooa预浸料铺贴过程图。图5中,5-1为核壳橡胶粒子,5-2为气道,5-3为碳纤维束,5-4为环氧树脂。具体实施方式为了加深对本发明的理解,下面将结合实施例对本发明做进一步详细描述,该实施例仅用于解释本发明,并不对本发明的保护范围构成限定。本实施例提供一种高韧性非热压罐固化预浸料的生产工艺,关键点在于借鉴了传统的ooa预浸料和增韧树脂制造工艺,创新性的将增韧剂以功能颗粒的形式从树脂中抽离,降低了树脂和后续产品的制造难度,同时通过纤维的过滤作用,将功能颗粒保留在预浸料表面以构造表面凸起,帮助排出铺贴陷入的空气。生产时,先根据性能要求设计树脂的配方,选择是否直接在树脂中添加功能颗粒。对于未含有功能颗粒的树脂,可以在涂膜过程中将功能颗粒添加到树脂膜表面。实施例工艺适用于高韧性ooa预浸料的制造,解决了高韧性树脂制造工艺困难成本高的问题,同时也降低了预浸料ooa成型的工艺难度。实施例1根据高韧性非热压罐固化预浸料示意图,如图1,详细说明具体实例1。根据设计,为了保证预浸料的韧性以及非热压罐固化成型工艺性能,需按照如图1所示的结构进行生产,1-1为聚醚醚酮颗粒,1-2为双马树脂,1-3为碳纤维斜纹织物。其中,聚醚醚酮颗粒1-1的平均粒径为40μm。其中,双马树脂1-2在70℃下的粘度为100000cps,树脂中含有15%质量比的增韧剂。其中,碳纤维斜纹织物1-3的纤维面密度为220gsm,使用t300级别的3k纤维进行编织。具体实现过程如下:将生产好的双马树脂1-2在如图2所示的涂膜机上进行涂膜。经过一对75℃的涂膜辊2-1的相互作用,将树脂2-2涂覆在离型纸上形成初步树脂膜2-3,面密度为72gsm。使用20℃的冷却板2-4对树脂膜进行降温,防止树脂经过粉末涂布辊时粘贴到辊面上。然后经过一对粉末涂布辊2-7,利用挡板和辊表面沟槽将聚醚醚酮颗粒添加到初步树脂膜表面,粉末涂膜量为8gsm。温度为35℃的加热板2-8使树脂膜软化,通过橡胶压辊的压合作用将功能颗粒固定在树脂膜表面。最后覆上pe膜收卷得到带有功能颗粒的树脂膜2-10。将树脂膜2-10与碳纤维斜纹织物1-3在普通含浸设备上含浸,含浸温度最高为70℃,最终得到本专利所述的高韧性非热压罐固化预浸料。经检验,预浸料表面平整面密度均匀,没有缺胶和富胶区域。用液体浸润法进行含浸程度测试,吸水率为70%。将预浸料以[0/45/90/-45]3s方向铺贴24层,如图3所示。在铺层过程中,两张预浸料的表面凸起会分别在接触另一张预浸料后形成空隙,作为气道3-2。然后制袋,再放入烘箱固化。固化后,c扫检验合格,回波率为80%。在6.67kj冲击能量下的cai测试结果如下表所示,非热压罐固化工艺性能与热压罐固化性能相当:固化工艺非热压罐固化(ooa)热压罐固化cai值310mpa313mpac扫合格合格板材孔隙率0.7%0.6%针对本实例,如果采用普通预浸料工艺生产该双马树脂预浸料,想要后期板材cai达到310mpa,则树脂会因为添加增韧剂在70℃的粘度至少为350000cps。由于该双马树脂的特性,涂膜温度必须不大于80℃,因此70℃下350000cps粘度的树脂很可能造成涂膜不均匀或涂膜设备损坏。而采用本专利所述新工艺则不会出现上述问题。实施例2根据高韧性非热压罐固化预浸料示意图,如图4,详细说明具体实例2。根据设计,为了保证预浸料的韧性以及非热压罐固化成型工艺性能,需按照如图1所示的结构进行生产,4-1为核壳橡胶粒子,4-2为环氧树脂,4-3为碳纤维束。其中,核壳橡胶粒子粒4-1的平均粒径为30μm。其中,双马树脂4-2在70℃下的粘度为60000cps,树脂中含有10%质量比的核壳橡胶粒子。其中,碳纤维束4-3为t300级别的3k纤维,纤维面密度为133gsm,。具体实现过程如下:将生产好的环氧树脂4-2在涂膜机上进行涂膜,涂膜温度为75℃。采用单面膜形式,胶膜面密度为66gsm。然后将树脂膜与碳纤维束4-3在普通含浸设备上含浸,含浸温度最高为95℃,最终得到本专利所述的高韧性非热压罐固化预浸料。经检验,预浸料表面平整面密度均匀,没有缺胶和富胶区域。用液体浸润法进行含浸程度测试,吸水率为99%。将预浸料以[0/45/90/-45]3s方向铺贴32层,如图5示。在铺层过程中,两张预浸料的表面凸起会分别在接触另一张预浸料后形成空隙,作为气道5-2。然后制袋,再放入烘箱固化。固化后,c扫检验合格,回波率为88%。在6.67kj冲击能量下的cai测试结果如下表所示,非热压罐固化工艺性能与热压罐固化性能相当:固化工艺非热压罐固化(ooa)热压罐固化cai值278mpa281mpac扫合格合格板材孔隙率0.5%0.5%行业的技术人员应该了解,本发明不受上述实施例的限制,上述实施例和说明书中描述的只是说明本发明的原理,在不脱离本发明精神和范围的前提下,本发明还会有各种变化和改进,这些变化和改进都落入要求保护的本发明范围内。本发明要求保护范围由所附的权利要求书及其等效物界定。当前第1页12