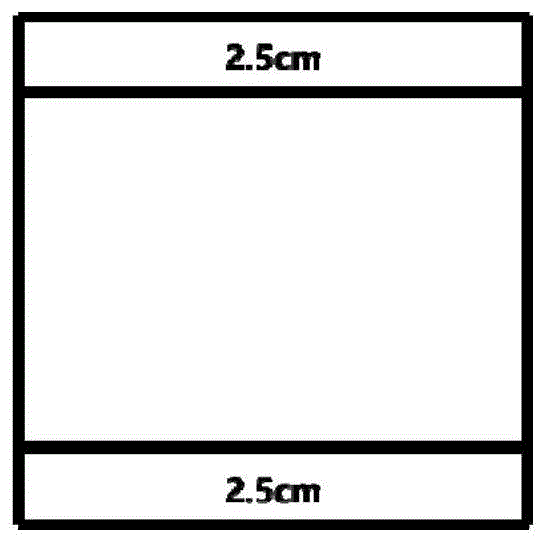
本发明涉及聚氨酯
技术领域:
,具体而言,涉及一种有机硅表面活性剂、软质聚氨酯泡沫及其制备方法。
背景技术:
:软质聚氨酯泡沫广泛应用于沙发、寝具、服装等日常生活用品和工业包装、过滤等工业用品中。透气性作为软泡的重要特性之一,一直被行业所追逐,尤其是在座垫、枕头和床垫等行业。其中,专利cn105530838b报道了一种透气性座椅;cn204207414u报道了一种具有高透气性海绵床垫、枕头;cn106632985b报道了一种聚氨酯泡沫材料及其制备方法和用途,其在高密度泡沫中透气性良好。目前,存在泡沫上下层的透气率差距大的技术难题,特别是在密度相对较低的软质泡沫中,而相关解决方法也鲜有报道。鉴于此,特提出本发明。技术实现要素:本发明的目的在于提供一种有机硅表面活性剂、软质聚氨酯泡沫及其制备方法以解决上述技术问题。本发明是这样实现的:一种软质聚氨酯泡沫用有机硅表面活性剂,其具有如下通式:mdxd'ym;其中,m为(ch3)3sio1/2或(ch3)2rsio1/2;d为(ch3)2sio2/2;d'为(ch3)rsio2/2;x+y为50-120,且y≥5,x与y的比值为10-20:1;r为聚醚。本发明提供了一种软质聚氨酯泡沫用有机硅表面活性剂,采用具有上述结构的有机硅表面活性剂可以形成泡孔更细,更均匀的软质聚氨酯泡沫,有利于提升泡沫的透气率。这样可以使得上下层的聚氨酯泡沫差异性较小,使得发泡过程更稳定,提升了产品上下层品质的一致性。在本发明应用较佳的实施方式中,上述r为聚醚链段,使其具有良好的亲水性,有利于改善产品的相容性,提高乳化性能,其在有机硅表面活性剂中所占的质量分数为50%-70%。在本发明应用较佳的实施方式中,r为如下至少一种聚醚:i.通式为-cnh2n(c2h4o)a(c3h6o)bor'的聚醚;聚醚的数均分子量为2500-5000,式中n为2-4,聚醚中聚氧乙烯基的重量占比为20-60%,r'为1-4个碳原子的烷基或为-c(o)ch3;ii.通式为-cn'h2n'(c2h4o)a'(c3h6o)b'or”的聚醚;聚醚的数均分子量为300-700,式中n'为2-4,聚醚中聚氧乙烯基的重量占比为60-90%,r”为1-4个碳原子的烷基或为-c(o)ch3;iii.通式为-cn”h2n”(c2h4o)a”(c3h6o)b”or”'的聚醚;聚醚的数均分子量为1000-2000,式中n”为2-4,聚醚中聚氧乙烯基的重量占比为20-60%,r”'为h、1-4个碳原子的烷基或为-c(o)ch3。在本发明应用较佳的实施方式中,a为9-59的整数,b为20-72的整数。在本发明应用较佳的实施方式中,a'为3-12的整数,b'为1-5的整数。在本发明应用较佳的实施方式中,a”为4-23的整数,b”为8-28的整数。在本发明应用较佳的实施方式中,x+y为80-100,x与y的比值为13-17:1。在上述通式范围内的聚醚均可用于合成有机硅表面活性剂。聚醚使用过多或过少均会影响产品的性能,这是因为表面活性剂中有亲油和亲水基团,亲油和亲水基团需在一个平衡的状态才能保持表面活性剂的作用。一种有机硅表面活性剂的制备方法,其包括如下步骤:将聚硅氧烷、聚醚、氯铂酸催化剂置于反应器中,在90-95℃反应1-1.5h,得到的产品加入稀释剂即得到有机硅表面活性剂。表面活性剂中含有稀释剂。稀释剂可降低产品粘度,有利于实际中的使用;稀释剂还有一定的抗冻作用,使产品凝固点升高。在本发明应用较佳的实施方式中,上述稀释剂为二丙二醇,二乙二醇,碳酸丙烯酯,二乙二醇乙醚,二乙二醇丙醚和环三羟甲基丙烷甲缩醛中的至少一种。采用上述稀释剂在泡沫形成反应中能提高泡沫的成核能力,使发泡反应更有利的进行。一种制备软质聚氨酯泡沫的方法,其包括在合成聚氨酯泡沫的过程中加入上述有机硅表面活性剂。在本发明应用较佳的实施方式中,上述方法还包括在泡沫形成反应混合物中加入多元醇,聚异氰酸酯和聚氨酯泡沫反应催化剂。通过加入多元醇,聚异氰酸酯和聚氨酯泡沫反应催化剂以反应获得软质聚氨酯泡沫。在本发明应用较佳的实施方式中,上述方法还包括在泡沫形成反应混合物中加入填料、发泡剂、着色剂、阻燃剂和抗氧化剂中的至少一种。填料、发泡剂、着色剂、阻燃剂和抗氧化剂可以根据需要选择常规的组分进行添加。一种由上述方法制备得到的软质聚氨酯泡沫,软质聚氨酯泡沫的上下层透气率相差小于或等于10%。采用本发明提供的制备方法,在合成聚氨酯泡沫的过程中加入聚醚改性有机硅表面活性剂,制备的泡沫的透气率更为均匀,发泡过程更稳定,产品的品质上下层透气率更为一致。在本发明应用较佳的实施方式中,上述软质聚氨酯泡沫的密度为17-25kg/m3。本发明具有以下有益效果:本发明提供了一种有机硅表面活性剂、软质聚氨酯泡沫及其制备方法,采用本发明提供的有机硅表面活性剂可以形成泡孔更细,更均匀的软质聚氨酯泡沫。这样有利于缩小上下层聚氨酯泡沫的差异,提升泡沫的透气率,使得发泡过程更稳定,提升了产品上下层品质的一致性。本发明提供的软质聚氨酯泡沫的制备方法简单易行,且制备得到的软质聚氨酯泡沫的上下层透气率差异小,且透气性良好。附图说明为了更清楚地说明本发明实施例的技术方案,下面将对实施例中所需要使用的附图作简单地介绍,应当理解,以下附图仅示出了本发明的某些实施例,因此不应被看作是对范围的限定,对于本领域普通技术人员来讲,在不付出创造性劳动的前提下,还可以根据这些附图获得其他相关的附图。图1为实验例1中泡沫裁剪侧面示意图;图2为实施例1-b的切片泡沫下层的泡孔图;图3为实施例1-b的切片泡沫上层的泡孔图;图4为对比例6的切片泡沫下层的泡孔图;图5为对比例6的切片泡沫上层的泡孔图。具体实施方式为使本发明实施例的目的、技术方案和优点更加清楚,下面将对本发明实施例中的技术方案进行清楚、完整地描述。实施例中未注明具体条件者,按照常规条件或制造商建议的条件进行。所用试剂或仪器未注明生产厂商者,均为可以通过市售购买获得的常规产品。以下结合实施例对本发明的特征和性能作进一步的详细描述。实施例1本实施例提供了表面活性剂的制备方法。其包括如下步骤:向配有机械搅拌器和干燥氮气管线的1000ml四口烧瓶中加入225g的聚硅氧烷(md88d’5.8m),375g的聚醚a和100g的聚醚b。其中,聚醚a是以烯丙基起始的、酯基封端的聚氧化烯烃,其平均分子量为4000,含有重量百分比40%的环氧乙烷基。聚醚b是以烯丙基起始的、酯基封端的聚氧化烯烃,其平均分子量为550,含有重量百分比70%的环氧乙烷基。聚醚a的结构式如下:ch2=ch-ch2(c2h4o)a(c3h6o)boc(o)ch3;eo%=40%;mn=4000g/mol。聚醚b的结构式如下:ch2=ch-ch2(c2h4o)a'(c3h6o)b'oc(o)ch3;eo%=70%;mn=550g/mol。通过移液枪在烧瓶中加入200μl的二丁氨基乙醇,并进行搅拌。抽真空,并进行n2置换三次,将该混合物加热至90-95℃,并搅拌约10min,添加6ppm的pt(氯铂酸乙醇溶液)。将瓶内的混合物维持在90-95℃,一小时后,测定混合物的si-h的含量小于0.2ml/g,得到淡黄色透明粘性液体。该粘性液体即为实施例1制备得到的产品。实施例2按照实施例1的制备方法,采用表1所示的聚醚组合制备硅氧烷-聚醚表面活性剂。本实施例与实施例1的区别在于聚醚的组合不同,其余步骤相同。本实施例中聚硅氧烷的添加量为210g,聚醚a405g,聚醚b85g。实施例3按照实施例1的制备方法,采用表1所示的聚醚组合制备硅氧烷-聚醚表面活性剂。本实施例与实施例1的区别在于聚醚的组合不同,其余步骤相同。本实施例中聚硅氧烷的添加量为200g,聚醚a360g,聚醚b70g,聚醚c20g。聚醚c的结构式如下:ch2=ch-ch2(c2h4o)a″(c3h6o)b″oc(o)ch3;eo%=40%;mn=1200g/mol。实施例4按照实施例1的制备方法,采用表1所示的聚醚组合制备硅氧烷-聚醚表面活性剂。本实施例与实施例1的区别在于聚醚的组合不同,其余步骤相同。本实施例中聚硅氧烷的添加量为220g,聚醚a390g,聚醚b95g。对比例1按照实施例1的制备方法,采用表1所示的聚醚组合制备硅氧烷-聚醚表面活性剂。本实施例与实施例1的区别在于聚醚的组合不同,其余步骤相同。本实施例中聚硅氧烷的添加量为200g,聚醚a455g,聚醚d40g。聚醚d的结构式如下:ch2=ch-ch2(c2h4o)a'(c3h6o)b'oc(o)ch3;eo%=100%;mn=300g/mol。对比例2按照实施例1的制备方法,采用表1所示的聚醚组合制备硅氧烷-聚醚表面活性剂。本实施例与实施例1的区别在于聚醚的组合不同,其余步骤相同。本实施例中聚硅氧烷的添加量为180g,聚醚a455g,聚醚b60g。对比例3按照实施例1的制备方法,采用表1所示的聚醚组合制备硅氧烷-聚醚表面活性剂。本实施例与实施例1的区别在于聚醚的组合不同,其余步骤相同。本实施例中聚硅氧烷的添加量为190g,聚醚a420g,聚醚b90g。对比例4按照实施例1的制备方法,采用表1所示的聚醚组合制备硅氧烷-聚醚表面活性剂。本实施例与实施例1的区别在于聚醚的组合不同,其余步骤相同。本实施例中聚硅氧烷的添加量为180g,聚醚a290g,聚醚e220g。聚醚e的结构式如下:ch2=ch-ch2(c2h4o)a″(c3h6o)b″och3;eo%=40%;mn=1200g/mol。表1不同聚醚组合表。实验例1将实施例1制备的产品与表2中的不同溶剂按不同的重量比进行分别单独混合,制得有机硅表面活性剂,不同的组合分别标识为实施例1-a、实施例1-b和实施例1-c。表2不同溶剂组合。将混合后的溶液分别用于制备聚氨酯泡沫。制备泡沫的步骤如下:将500.0±0.5g的多元醇ppg添加到一个2000ml的塑料杯中,控制多元醇的温度维持在21.5~22.5℃;添加19.00±0.02g的水,10.0-10.2g有机硅表面活性剂和0.70-0.75g胺a-33,将混合物于2000r/m搅拌20s混合;加入0.95-1.00g辛酸亚锡,2000r/m搅拌20s;倒入温度维持在21.5-22.5℃的甲苯二异氰酸酯249.85±0.20g,2000r/m搅拌7s,将混合物倒入28.5cm*28.5cm*28.5cm的正方体模具中,塑料杯保持反转,持续倒料7s。泡沫开始反应,并不断上升,记录泡沫上升的最高高度、跳泡时间、回缩后的高度,静置泡沫。从混合甲苯二异氰酸酯步骤开始总共200s,将泡沫至于80-100℃的烘箱中进行熟化1h;将泡沫从烘箱拿出,冷却至少0.5h。制备软质聚氨酯泡沫:下述软质聚氨酯泡沫的密度为25.0kg/m3,并按照表3配方的制备。表3配方表。原料配比(wt%)ppg100.0水3.8胺a330.15辛酸亚锡0.20tdi80/20(指数110)50有机硅表面活性剂2.0多元醇ppg的羟基数为56。有机硅表面活性剂的添加量占ppg的2%(wt%)。同时采用相同的方法用市售的表面活性剂uf5880和l-595分别制备聚氨酯泡沫以作为对比例5和对比例6。按照如下方法检测其透气率和完全成型高度。检测方法:将制备好的软质聚氨酯泡沫裁剪成底面20×20cm的长方体,参照图1所示,分别裁取最上层和最下层厚度为2.5cm的泡沫片。完全成型高度:在室温下放置12~24小时后的泡沫的最终高度的厘米数。透气率:泡沫每立方米每分钟下的空气流量。检测结果参照表4所示。表面活性剂的添加量占ppg的2%。表4的数据表明,与对比例5和对比例6的有机硅表面活性剂相比,本发明的有机硅表面活性剂实施例1-a~1-c透气率上下差较小,其中实施例1-b的透气率上下差最小。图2为实施例1-b的切片泡沫下层的泡孔图,图3为实施例1-b的切片泡沫上层的泡孔图,图4为对比例6的切片泡沫下层的泡孔图,图5为对比例6的切片泡沫上层的泡孔图。由图可知,对比例提供的表面活性剂制备出的泡沫的泡孔上下差异较大(图4和图5),从而导致上下层透气率差异大,而本申请提供的表面活性剂制备出的泡沫的泡孔,上下层比较一致,透气率上下差异较小(图2和图3),上下层品质更为一致。表4实验例1中的透气率和成型高度检测数据表。实验例2将实施例1-4和对比例1-4采用实验例表2中实施例1-b的溶剂配方进行复配组合。即设置制得产品的质量占比为60%,二丙二醇质量占比为30%,二乙二醇丙醚的质量占比为10%。实施例1-4和对比例1-4采用实验例表2中实施例1-b的溶剂配方进行复配组合制得的表面活性剂分别标记为实施例1-b、实施例2-b、实施例3-b、实施例4-b、对比例1-b、对比例2-b、对比例3-b和对比例4-b。并按照实验例1提供的方法制备软质聚氨酯泡沫。制备出的泡沫采用实验例1的方法检测其透气率和完全成型高度。检测结果参照表5所示。表5证明本发明的表面活性剂实施例能提供一种上下层透气率相差较小的软质泡沫。对比例3-b虽有较高的透气率,但泡沫的上下层透气率相差较大,即上下层泡沫品质不一致。表5实验例2中的透气率和成型高度检测数据表。以上所述仅为本发明的优选实施例而已,并不用于限制本发明,对于本领域的技术人员来说,本发明可以有各种更改和变化。凡在本发明的精神和原则之内,所作的任何修改、等同替换、改进等,均应包含在本发明的保护范围之内。当前第1页12