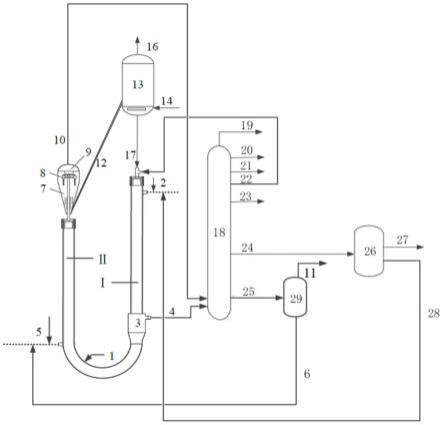
1.本技术涉及石油炼制及石油化工加工过程,具体地,涉及一种制取低碳烯烃的催化转化方法。
背景技术:2.乙烯与丙烯是构成现代石油化工最为重要的两大基础原料,其中,乙烯是世界上最大的化工产品之一,占全球整个石化产品产量的75%以上;丙烯也是重要的有机化工原料,其主要用于制丙烯腈、环氧丙烷、丙酮等。乙烯和丙烯用以生产多种重要有机化工原料、生成合成树脂、合成橡胶及多种精细化学品等。但是,随着油田开采量的不断增加,常规原油可供产量日趋减少,原油品质越来越差,逐渐趋于劣质化、重质化,并不能满足市场对轻质烯烃的需求。
3.采用传统的蒸汽裂解制乙烯、丙烯路线,对轻烃、石脑油等化工轻烃需求量较大,由于原油普遍偏重,化工轻油难以满足乙烯、丙烯原料的需求。研究机构预计从2018年到2026年,全球汽油复合年均增长率预计将低于1%,但丙烯增长约4%。合理利用炼厂流程中的高碳烯烃来裂解制乙烯、丙烯,即满足了石化企业提质增效的目标,又顺应能源转型的时代需求。
4.中国专利cn101092323a中公开了一种采用c4-c8烯烃混合物为原料,在反应温度400-600℃,绝对压力为0.3-1.1kpa的条件下进行反应,经分离装置将c4馏分30-90重量%循环进反应器再次裂解制备乙烯和丙烯的方法。该方法重点通过c4馏分循环,提高了烯烃转化率,得到的乙烯和丙烯不少于原料烯烃总量的62%,但其乙烯/丙烯比较小,无法根据市场需求灵活调节,而且反应选择性低,产物中丁烯含量大,且存在c4分离能耗等问题。
5.中国专利cn101239878a中公开了一种采用碳四及以上烯烃的富烯烃混合物为原料,在反应温度400-680℃,反应压力为-0.09-1.0mpa,重量空速为0.1~50小时-1的条件下进行反应,产物乙烯/丙烯较低,低于0.41,随着温度升高乙烯/丙烯增加,虽然能够在一定程度上提高双烯收率,但是其乙烯选择性较低,无法大量生产乙烯满足市场需求。
6.因此,本领域亟需一种新的方法以生产高产率的乙烯和丙烯。
技术实现要素:7.本公开的目的在于提供一种用于生产低碳烯烃的催化转化方法,提高乙烯和丙烯的产率,实现了石油资源的有效利用。
8.为了实现上述目的,本公开提供了一种用于生产低碳烯烃的催化转化方法,该方法包括:
9.s1、将烯烃含量在50重量%以上的烃油原料与温度在650℃以上的催化转化催化剂在u型管反应器的下行反应区上部接触并进行第一催化转化反应,得到第一料流,将所述第一料流进行油剂分离得到第一催化剂和第一反应物流;
10.s2、将重质原料油与所述第一催化剂在u型管反应器的上行反应区底部接触并进
行第二催化转化反应,得到第二反应物流和待生催化剂;
11.s3、从第一反应物流和第二反应物流中分离出乙烯、丙烯、丁烯、富含烯烃的物流和催化蜡油;将所述富含烯烃的物流引入所述u型管反应器的下行反应区继续反应。
12.可选地,所述富含烯烃的物流为c5以上的烯烃;所述富含烯烃的物流中c5以上烯烃的含量为50重量%-100重量%。
13.可选地,该方法还包括:将所述待生催化剂进行烧焦再生,得到再生催化剂;并且,将所述再生催化剂预热后返回至所述u型管反应器的下行反应区。
14.可选地,该方法还包括:将所述丁烯引入所述u型管反应器的下行反应区中继续反应。
15.可选地,所述丁烯先于所述富含烯烃的物流与所述催化转化催化剂接触。
16.可选地,所述丁烯继续反应的反应条件包括:反应温度为650-800℃,反应压力为0.05-1mpa,反应时间为0.01-10秒,所述催化转化催化剂与所述丁烯的重量比为(20-200):1;优选地,反应温度为680-780℃,反应压力为0.1-0.8mpa,反应时间为0.05-8秒,所述催化转化催化剂与所述丁烯的重量比为(30-180):1。
17.可选地,该方法还包括:将所述催化蜡油经过加氢处理后得到加氢催化蜡油,将所述加氢催化蜡油引入所述u型管反应器的上行反应区底部继续反应。
18.可选地,所述加氢处理的条件包括:氢分压为3.0-20.0兆帕,反应温度为300-450℃,氢油体积比为300-2000,体积空速为0.1-3.0小时-1
。
19.可选地,所述第一催化转化反应的条件包括:反应温度为600-800℃,反应压力为0.05-1mpa,反应时间为0.01-100秒,所述催化转化催化剂与所述烃油原料的重量比为(1-200):1;所述第二催化转化反应的条件包括:反应温度为400-650℃,反应压力为0.05-1mpa,反应时间为0.01-100秒,所述催化转化催化剂与所述重质原料油的重量比为(1-100):1。
20.优选地,所述第一催化转化反应的条件包括:反应温度为630-780℃,反应压力为0.1-0.8mpa,反应时间为0.1-80秒,所述催化转化催化剂与所述烃油原料的重量比为(3-180):1;所述第二催化转化反应的条件包括:反应温度为450-600℃,反应压力为0.1-0.8mpa,反应时间为0.1-80秒,所述催化转化催化剂与所述重质原料油的重量比为(3-70):1。
21.可选地,所述烃油原料中的烯烃含量为80重量%以上;优选地,所述烃油原料中的烯烃含量为90重量%以上;更优选地,所述烃油原料为纯烯烃原料。
22.可选地,所述重质原料油选自石油烃和/或矿物油;所述石油烃选自减压瓦斯油、常压瓦斯油、焦化瓦斯油、脱沥青油、减压渣油、常压渣油和重芳烃抽余油中的至少一种;所述矿物油选自煤液化油、油砂油和页岩油中的至少一种。
23.可选地,所述烃油原料中的烯烃来自烷烃原料脱氢产生的c4以上馏分、炼油厂催化裂解装置产生的c4以上馏分、乙烯厂中蒸汽裂解装置产生的c4以上馏分、mto副产的c4以上的富烯烃馏分、mtp副产的c4以上的富烯烃馏分;所述烷烃原料选自石脑油、芳烃抽余油和轻质烃中的至少一种。
24.可选地,以所述催化转化催化剂的重量为基准,所述催化转化催化剂包括1-50重量%的分子筛、5-99重量%的无机氧化物和0-70重量%的粘土;所述分子筛包括大孔分子
筛、中孔分子筛和小孔分子筛中的一种或几种。所述催化转化催化剂的重量为基准,所述催化转化催化剂还包含0.1-3重量%的活性金属;所述活性金属选自viii族金属、iva族金属和稀土金属中的一种或几种。
25.通过上述技术方案,本公开的方法通过将油气分离过程中所生产的大分子烯烃以特定的路线进行回炼,可以取代传统的高耗能的蒸汽裂解产乙烯和丙烯的方案,有效提高了乙烯和丙烯产率以及选择性,同时能有效抑制甲烷等副产品的生成,从而达到石油资源高效利用的目的。
26.本公开的其他特征和优点将在随后的具体实施方式部分予以详细说明。
附图说明
27.附图是用来提供对本公开的进一步理解,并且构成说明书的一部分,与下面的具体实施方式一起用于解释本公开,但并不构成对本公开的限制。在附图中:
28.图1是本公开的第一种具体实施方式的流程示意图;
29.图2是本公开的第二种具体实施方式的流程示意图。
30.附图标记说明
[0031]ⅰ下行反应区
ꢀꢀꢀꢀꢀꢀꢀꢀꢀꢀⅱ
上行反应区
[0032]
1u型管反应器
ꢀꢀꢀꢀꢀꢀꢀꢀꢀ
2管线
ꢀꢀꢀꢀꢀꢀꢀꢀꢀꢀꢀꢀꢀꢀꢀꢀꢀ
3旋风分离器
[0033]
4管线
ꢀꢀꢀꢀꢀꢀꢀꢀꢀꢀꢀꢀꢀꢀꢀꢀꢀ
5管线
ꢀꢀꢀꢀꢀꢀꢀꢀꢀꢀꢀꢀꢀꢀꢀꢀꢀ
6管线
[0034]
7出口段
ꢀꢀꢀꢀꢀꢀꢀꢀꢀꢀꢀꢀꢀꢀꢀ
8沉降器
ꢀꢀꢀꢀꢀꢀꢀꢀꢀꢀꢀꢀꢀꢀꢀ
9集气室
[0035]
10管线
ꢀꢀꢀꢀꢀꢀꢀꢀꢀꢀꢀꢀꢀꢀꢀꢀ
11管线
ꢀꢀꢀꢀꢀꢀꢀꢀꢀꢀꢀꢀꢀꢀꢀꢀ
12斜管
[0036]
13再生器
ꢀꢀꢀꢀꢀꢀꢀꢀꢀꢀꢀꢀꢀꢀ
14管线
ꢀꢀꢀꢀꢀꢀꢀꢀꢀꢀꢀꢀꢀꢀꢀꢀ
15管线
[0037]
16管线
ꢀꢀꢀꢀꢀꢀꢀꢀꢀꢀꢀꢀꢀꢀꢀꢀ
17管线
ꢀꢀꢀꢀꢀꢀꢀꢀꢀꢀꢀꢀꢀꢀꢀꢀ
18产物分离装置
[0038]
19管线
ꢀꢀꢀꢀꢀꢀꢀꢀꢀꢀꢀꢀꢀꢀꢀꢀ
20管线
ꢀꢀꢀꢀꢀꢀꢀꢀꢀꢀꢀꢀꢀꢀꢀꢀ
21管线
[0039]
22管线
ꢀꢀꢀꢀꢀꢀꢀꢀꢀꢀꢀꢀꢀꢀꢀꢀ
23管线
ꢀꢀꢀꢀꢀꢀꢀꢀꢀꢀꢀꢀꢀꢀꢀꢀ
24管线
[0040]
25管线
ꢀꢀꢀꢀꢀꢀꢀꢀꢀꢀꢀꢀꢀꢀꢀꢀ
26烯烃分离装置
ꢀꢀꢀꢀꢀꢀꢀꢀ
27管线
[0041]
28管线
ꢀꢀꢀꢀꢀꢀꢀꢀꢀꢀꢀꢀꢀꢀꢀꢀ
29加氢处理反应器
具体实施方式
[0042]
以下对本公开的具体实施方式进行详细说明。应当理解的是,此处所描述的具体实施方式仅用于说明和解释本公开,并不用于限制本公开。
[0043]
本公开提供了一种制取低碳烯烃的催化转化方法,该方法包括:
[0044]
s1、将烯烃含量在50重量%以上的烃油原料与温度在650℃以上的催化转化催化剂在u型管反应器的下行反应区上部接触并进行第一催化转化反应,得到第一料流,将所述第一料流进行油剂分离得到第一催化剂和第一反应物流;
[0045]
s2、将重质原料油与所述第一催化剂在u型管反应器的上行反应区底部接触并进行第二催化转化反应,得到第二反应物流和待生催化剂;
[0046]
s3、从所述第一反应物流和所述第二反应物流中分离出乙烯、丙烯、丁烯、富含烯烃的物流和催化蜡油;将所述富含烯烃的物流引入所述u型管反应器的下行反应区继续反应。
650℃,反应压力为0.05-1mpa,反应时间为0.01-100秒所述催化转化催化剂与所述重质原料油的重量比为(1-100):1;优选地,反应温度为450-600℃,反应压力为0.1-0.8mpa,反应时间为0.1-80秒所述催化转化催化剂与所述重质原料油的重量比为(3-70):1;进一步优选地,反应温度为480-580℃,反应压力为0.2-0.5mpa,反应时间为0.2-70秒所述催化转化催化剂与所述重质原料油的重量比为(4-30):1。
[0057]
本公开中的u型管反应器的下行反应区还可以设置有分离器,用于将步骤s1中的反应产物进行初步分离,将初步分离得到的油气进行进一步分离,将初步分离得到的催化剂送至u型管反应器的上行反应区与重质原料油进行催化裂化反应。
[0058]
根据本公开,所述烃油原料中的烯烃含量可以为80重量%以上;优选地,所述烃油原料中的烯烃含量为90重量%以上;更优选地,所述烃油原料为纯烯烃原料。所述重质原料油可以选自石油烃和/或矿物油;所述石油烃可以选自减压瓦斯油、常压瓦斯油、焦化瓦斯油、脱沥青油、减压渣油、常压渣油和重芳烃抽余油中的至少一种;所述矿物油可以选自煤液化油、油砂油和页岩油中的至少一种。
[0059]
本公开的一种实施方式中,所述烃油原料中的烯烃可以来自烷烃原料脱氢产生的c5以上馏分、炼油厂催化裂解装置产生的c5以上馏分、乙烯厂中蒸汽裂解装置产生的c5以上馏分、mto副产的c5以上的富烯烃馏分、mtp副产的c5以上的富烯烃馏分;所述烷烃原料选自石脑油、芳烃抽余油和其他装置的轻质烃中的至少一种。
[0060]
进一步地,在丁烯产物回炼的实施方式中,所述烃油原料中的烯烃来自烷烃原料脱氢产生的c4以上馏分、炼油厂催化裂解装置产生的c4以上馏分、乙烯厂中蒸汽裂解装置产生的c4以上馏分、mto副产的c4以上的富烯烃馏分、mtp副产的c4以上的富烯烃馏分;所述烷烃原料选自石脑油、芳烃抽余油和其他装置的轻质烃中的至少一种。
[0061]
一种实施方式中,烷烃脱氢制烯烃的方法,包括将烷烃与脱氢催化剂进行接触反应,反应器的入口温度为400-700℃,烷烃的体积空速为200-5000h-1
,所述接触反应的压力为0-1.0mpa。所述脱氢催化剂由载体以及负载在载体上的活性组分和助剂组成;以催化剂总重为100%计,所述载体的含量为60-90重量%,所述活性组分的含量为8-35重量%,所述助剂的含量为0.1-5重量%;所述载体为含有改性剂的氧化铝;所述改性剂的含量为催化剂总重的0.1-2重量%,所述改性剂为la或ce;所述活性组分为铂或铬;所述助剂为铋和碱金属组分或者铋和碱土金属组分;铋与所述活性组分的摩尔比为1:(5-50);铋与碱金属组分的摩尔比为1:(0.1-5);铋与碱土金属组分的摩尔比为1:(0.1-5);所述碱金属组分为li、na和k中的一种或多种;所述碱土金属组分为mg、ca和ba中的一种或多种。
[0062]
根据本公开,以所述催化转化催化剂的重量为基准,所述催化转化催化剂可以包括1-50重量%的分子筛、5-99重量%的无机氧化物和0-70重量%的粘土;所述分子筛可以包括大孔分子筛、中孔分子筛和小孔分子筛中的一种或几种。所述催化转化催化剂的重量为基准,所述催化转化催化剂还包含0.1-3重量%的活性金属;所述活性金属选自viii族金属、iva族金属和稀土金属中的一种或几种。本公开中的无机氧化物作为粘接剂,可以选自二氧化硅(sio2)和/或三氧化二铝(al2o3);本公开中的粘土作为基质,可以选自高岭土和/或多水高岭土。在本公开的一种具体的实施方式中,所述催化裂解催化剂还可以负载金属离子,所述金属离子选自非金属元素、过渡金属元素和稀土金属元素中的至少一中,其中,非金属元素可以为磷,过渡金属元素可以选自铁、钴和镍,所述改性元素的重量为催化转化
催化剂重量含量为0.1%-3%。
[0063]
在本公开的一种实施方式中,所述中孔分子筛可以为zsm分子筛,进一步地,zsm分子筛可以选自zsm-5、zsm-11、zsm-12、zsm-23、zsm-35、zsm-38、zsm-48中的一种或几种。所述小孔分子筛可以为sapo分子筛,进一步地,sapo分子筛可以选自sapo-34、sapo-11、sapo-47中的一种或几种。所述大孔分子筛可以选自稀土y分子筛、稀土氢y分子筛、超稳y分子筛、高硅y分子筛、beta分子筛和其它类似结构的分子筛之中的一种或一种以上的混合物。
[0064]
本公开的一种具体的实施方式,如图1所示,烯烃含量在50重量%以上的烃油原料经管线2进入u型管反应器1的下行反应区ⅰ上部,与来自管线17的热催化转化催化剂接触并反应,反应产物在下行反应区ⅰ底部经旋风分离器3分离后,分离出的油气经管线4引入分离系统,分离出的催化剂随u型管反应器1下行继续参与反应,重质原料油经管线5进入u型管反应器1的上行反应区ⅱ底部,与u型管反应器1内已有料流接触并反应。生成的反应物流和失活的待生催化剂经出口段7进入沉降器8中的旋风分离器,实现待生催化剂与反应物流的分离,反应物流进入集气室9,待生催化剂细粉由料腿返回沉降器,从待生催化剂中汽提出的油气经旋风分离器后进入集气室9。汽提后的待生催化剂经斜管12进入再生器13,主风经管线14进入再生器,烧去待生催化剂上的焦炭,使失活的待生催化剂再生。烟气经管线16进入烟机。预热后的再生催化剂经管线17进入下行反应区ⅰ。反应物流经过大油气管线10进入后续的产物分离装置18,分离得到的氢气、甲烷和乙烷经管线19引出,乙烯经管线20引出,丙烯经管线21引出,丁烯经管线22引入u型管反应器1的下行反应区ⅰ顶部继续反应,丙烷和丁烷经管线23引出,含烯粗物流经管线24引入到烯烃分离装置26,分离得到的富含烯烃的物流由管线27引出,富含烯烃的物流经管线28引入u型管反应器1的下行反应区ⅰ上部继续反应,催化蜡油经管线25引入加氢处理反应器29,加氢处理后的轻组分由管线11引出,加氢催化蜡油由管线6引入u型管反应器1的上行反应区ⅱ底部继续反应。
[0065]
本公开的第二种具体的实施方式,如图2所示,烯烃含量在50重量%以上的烃油原料经管线2进入u型管反应器1的下行反应区ⅰ上部,与来自管线17的热催化转化催化剂接触并反应,反应得到的料流在下行反应区ⅰ底部经旋风分离器3分离后,分离出的物流经管线4引入分离系统,分离出的催化剂随u型管反应器1下行反应区继续参与反应。重质原料油经管线5进入u型管反应器1的上行反应区ⅱ底部,与已有的含有催化剂的物流接触并反应。生成的反应物流和失活的待生催化剂经出口段7进入沉降器8中的旋风分离器,实现待生催化剂与反应物流的分离,反应物流进入集气室9,待生催化剂细粉由料腿返回沉降器,从待生催化剂中汽提出的油气经旋风分离器后进入集气室9。汽提后的待生催化剂经斜管12进入再生器13,主风经管线14进入再生器,烧去待生催化剂上的焦炭,使失活的待生催化剂再生。烟气经管线16进入烟机。预热后的再生催化剂经管线17进入u型管反应器1的下行反应区ⅰ。反应物流经过大油气管线10进入后续的产物分离装置18,分离得到的氢气、甲烷和乙烷经管线19引出,乙烯经管线20引出,丙烯经管线21引出,丁烯经管线22引出,丙烷和丁烷经管线23引出,含烯烃粗物流经管线24引入到烯烃分离装置26,分离得到的烃流由管线27引出,富含烯烃的物流经管线28引入u型管反应器1的下行反应区ⅰ上部继续反应,催化蜡油经管线25引入加氢处理反应器29,加氢处理后的轻组分由管线11引出,加氢催化蜡油由管线6引入u型反应管器1的上行反应区ⅱ底部继续反应。
[0066]
以下通过实施例进一步详细说明本公开。实施例中所用到的原材料均可通过商购
途径获得。
[0067]
实施例中所用的原料a、b为重质原料油,原料c为催化裂化汽油轻馏分,其性质如表1所示。
[0068]
实施例中所用的催化转化催化剂a的制备方法简述如下:用4300克脱阳离子水将969克多水高岭土(中国高岭土公司产物,固含量73%)打浆,再加入781克拟薄水铝石(山东淄博铝石厂产物,固含量64%)和144毫升盐酸(浓度30%,比重1.56)搅拌均匀,在60℃静置老化1小时,保持ph为2-4,降至常温,再加入预先准备好的5000克浆液,其中中孔zsm-5分子筛和大孔y型分子筛(中国石化催化剂齐鲁分公司生产)1600g,二者重量比9:1。搅拌均匀,喷雾干燥,洗去游离na
+
,得催化剂。将得到的催化剂在800℃和100%水蒸汽下进行老化,老化后的催化剂称为催化转化催化剂a,催化转化催化剂a的性质见表3。
[0069]
实施例中所用的催化转化催化剂b商品牌号为cep-1,催化转化催化剂c商品牌号为chp-1,二者均为中国石化催化剂齐鲁分公司生产工业产品,催化转化催化剂b和催化转化催化剂c的性质见表3。
[0070]
实施例中所用的加氢处理催化剂d制备方法简述如下:称取偏钨酸铵((nh4)2w4o
13
·
18h2o,化学纯)和硝酸镍(ni(no3)2·
18h2o,化学纯),用水配成200毫升溶液。将溶液加入到氧化铝载体50克中,在室温下浸渍3小时,在浸渍过程中使用超声波处理浸渍液30分钟,冷却,过滤,放到微波炉中干燥约15分钟。该催化剂的组成为:30.0重量%wo3,3.l重量%nio和余量氧化铝,记作催化剂d。
[0071]
实施例中所用的加氢脱硫催化剂e的制备过程如下:称取1000克由中国石化催化剂长岭分公司生产的拟薄水铝石,之后加入含硝酸(化学纯)10毫升的水溶液1000毫升,在双螺杆挤条机上挤条成型,并在120℃干燥4小时,800℃焙烧4小时后得到催化剂载体。用含氟化铵120克的水溶液900毫升浸渍2小时,120℃干燥3小时,600℃焙烧3小时;降至室温后,用含偏钼酸铵133克的水溶液950毫升浸渍3小时,120℃干燥3小时,600℃焙烧3小时,降至室温后,用含硝酸镍180克、偏钨酸铵320克水溶液900毫升浸渍4小时用相对于催化剂载体为0.1重%的偏钼酸铵(化学纯)和相对于催化剂载体为0.1重%的硝酸镍(化学纯)的混合水溶液浸渍含氟氧化铝载体4小时,120℃烘干3小时,在600℃下焙烧4小时,制得催化剂e。
[0072]
表1-1
[0073]
[0074][0075]
表1-2
[0076]
进料性质b密度(20℃)/(千克/米3)901.5康氏残炭,重量%4.9h,重量%12.86s,重量%0.16n,重量%0.26ni,微克/克6.2族组成,重量% 饱和烃54.8芳烃28.4胶质16.0沥青质0.8
[0077]
表2
[0078]
碳数烷烃,重量%烯烃,重量%环烷烃,重量%芳烃,重量%51.804.400.000.0063.9130.200.670.8773.3233.571.812.3982.7910.681.750.5990.400.850.000.00
[0079]
表3
[0080]
[0081][0082]
实施例1
[0083]
本实施例按照图1的流程进行,在u型管反应器的中型装置上进行试验。1-戊烯和高温催化转化催化剂a在下行反应区顶部接触,在反应温度700℃,反应压力0.1mpa,反应时间5s,催化剂与原料的重量比45:1下发生催化转化反应,重质原料油a和催化转化催化剂a在上行反应区底部接触,在反应温度530℃,反应压力0.1mpa,反应时间6s,催化剂与原料的重量比5:1下发生催化转化反应,1-戊烯与重质原料之比为1:9。分离反应的反应产物和待生催化剂,将所得待生催化剂一起引入再生器烧焦再生,将所得反应产物一起引入组合分离系统,得到包括乙烯、丙烯、丁烯、富含烯烃的物流(沸点小于250℃)和催化裂化蜡油(沸点大于250℃)等的产品。催化裂化蜡油和加氢催化剂d在350℃,氢分压18mpa,体积空速1.5小时-1
,氢油体积比1500的条件下反应得到加氢催化裂化蜡油。将所得到的丁烯引入下行反应区顶部再裂化,反应温度为740℃,催化剂与原料的重量比为100:1,反应时间为0.2s;富含烯烃的物流引入下行反应区顶部再裂化,反应温度为700℃,反应时间为5s;所述加氢催化裂化蜡油与重质原料油混合,再返回上行反应区底部进行反应。反应条件和产品分布列于表4。
[0084]
对比例1
[0085]
本对比例采用与实施例1类似的工艺流程,在u型管反应器的中型装置上进行试验,不同之处在于富含烯烃的物流不返回u型管反应器中继续反应。重质原料油a和催化转化催化剂a在上行反应区底部接触,在反应温度530℃,反应压力0.1mpa,反应时间6s,催化剂与原料的重量比5:1下发生催化转化反应。分离反应的反应产物和待生催化剂,将所得待生催化剂一起引入再生器烧焦再生,将所得反应产物一起引入组合分离系统,得到包括乙烯、丙烯、丁烯、富含烯烃的物流和催化裂化蜡油等的产品。催化裂化蜡油和加氢催化剂d在350℃,氢分压18mpa,体积空速1.5小时-1
,氢油体积比1500的条件下反应得到加氢催化裂化蜡油。将所得到的丁烯引入下行反应区顶部再裂化,反应温度为740℃,催化剂与原料的重量比为100:1,反应时间为0.2s;所述加氢催化裂化蜡油与重质原料油混合,再返回上行反应区底部进行反应。反应条件和产品分布列于表4。
[0086]
实施例2
[0087]
本实施例按照图1的工艺流程进行,在u型管反应器的中型装置上进行试验。重质原料油a和催化转化催化剂a在上行反应区底部接触,在反应温度530℃,反应压力0.1mpa,反应时间6s,催化剂与原料的重量比5:1下发生催化转化反应,分离反应的反应产物和待生
催化剂,将所得待生催化剂一起引入再生器进行烧焦再生,将所得反应产物一起引入组合分离系统,得到包括乙烯、丙烯、丁烯、富含烯烃物流和催化裂化蜡油等的产品。催化裂化蜡油和加氢催化剂d在350℃,氢分压18mpa,体积空速1.5小时-1
,氢油体积比1500的条件下反应得到加氢蜡油。将所得到的丁烯引入下行反应区顶部再裂化,反应温度为740℃,催化剂与原料的重量比为100:1,反应时间为0.2s;富含烯烃的物流引入下行反应区顶部再裂化,反应温度为700℃,反应时间为5s;所述加氢催化裂化蜡油与重质原料油混合,再返回上行反应区底部进行反应。反应条件和产品分布列于表4。
[0088]
对比例2
[0089]
在提升管反应器的中型装置上进行试验,重质原料油a和催化转化催化剂b在提升管底部接触,在反应温度为610℃,催化剂与原料的重量比为16.9:1,反应压力0.1mpa,反应时间6s下发生催化转化反应,产物不进行加氢处理和返回所述装置继续反应。反应条件和产品分布列于表4。
[0090]
实施例3
[0091]
本实施例采用与实施例2类似的工艺流程,不同之处在于采用更重原料b。催化裂化蜡油不进行深度加氢处理,在加氢脱硫反应器内与加氢脱硫催化剂e接触,在反应压力6.0mpa、反应温度350℃、氢油体积比350、体积空速2.0小时-1
下反应,得到低硫加氢馏分油作为轻油组分。反应条件和产品分布列于表4。
[0092]
对比例3
[0093]
在提升管反应器的中型装置上进行试验,重质原料油b和催化转化催化剂c在提升管底部接触,在反应温度为530℃,催化剂与原料的重量比为5:1,反应压力0.1mpa,反应时间6s下发生催化转化反应,加氢处理与实施例3基本相同,产物不返回所述装置继续反应。反应条件和产品分布列于表4。
[0094]
实施例4
[0095]
本实施例采用与实施例1类似的工艺流程,不同之处是第一反应器进料为催化轻汽油馏分c。反应条件和产品分布列于表4。
[0096]
表4
[0097]
[0098][0099]
通过表4可以看出:烯烃高温裂解时乙烯和丙烯有更高产率,得到的反应产物中乙烯和丙烯的含量在56%左右,且原料烯烃含量越多是效果越好。此外,烯烃裂化的苯、甲苯、二甲苯产率明显增加。
[0100]
实施例5
[0101]
本实施例按照图2的流程进行,在u型管反应器的中型装置上进行试验。1-戊烯和高温催化转化催化剂a在下行反应区顶部接触,在反应温度700℃,反应压力0.1mpa,反应时间5s,催化剂与原料的重量比45:1下发生催化转化反应,重质原料油a和催化转化催化剂a在上行反应区底部接触,在反应温度530℃,反应压力0.1mpa,反应时间6s,催化剂与原料的重量比5:1下发生催化转化反应,1-戊烯与重质原料之比为1:9。分离反应的反应产物和待生催化剂,将所得待生催化剂一起引入再生器烧焦再生,将所得反应产物一起引入组合分离系统,得到包括乙烯、丙烯、丁烯、富含烯烃的物流和催化裂化蜡油等的产品。催化裂化蜡油和加氢催化剂d在350℃,氢分压18mpa,体积空速1.5小时-1
,氢油体积比1500的条件下反应得到加氢催化裂化蜡油。将所得到的富含烯烃的物流引入下行反应区顶部再裂化,反应
温度为700℃,反应时间为5s;所述加氢催化裂化蜡油与重质原料油混合,再返回上行反应区底部进行反应。产品中乙烯收率为6.48%,丙烯收率为21.46%,丁烯收率为24.96%,三烯总收率高达52.90%。
[0102]
以上详细描述了本公开的优选实施方式,但是,本公开并不限于上述实施方式中的具体细节,在本公开的技术构思范围内,可以对本公开的技术方案进行多种简单变型,这些简单变型均属于本公开的保护范围。
[0103]
另外需要说明的是,在上述具体实施方式中所描述的各个具体技术特征,在不矛盾的情况下,可以通过任何合适的方式进行组合。为了避免不必要的重复,本公开对各种可能的组合方式不再另行说明。
[0104]
此外,本公开的各种不同的实施方式之间也可以进行任意组合,只要其不违背本公开的思想,其同样应当视为本公开所公开的内容。