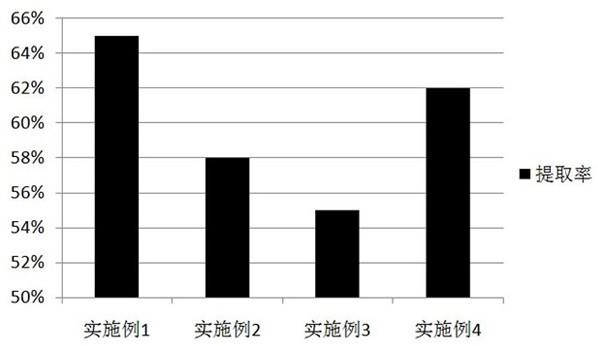
1.本发明涉及γ-聚谷氨酸生产技术领域,具体涉及一种可降解材料的提取工艺。
背景技术:2.γ-聚谷氨酸(γ-pga)最早发现于1937年,研究人员在炭疽芽孢杆菌(bacillus anthracis) 的细胞荚膜中以及于糖化菌(bacillus mesentericus)的细胞荚膜中发现γ-pga,之后在枯草芽孢杆菌(bacillus.subtilis)以及纳豆杆菌(bacillus natto)中也发现了γ-聚谷氨酸。γ-聚谷氨酸是由d-谷氨酸(d-glu)和l-谷氨酸(l-glu)单体以γ-羧基与α-氨基以肽键的形式缩合而成的一种多肽分子,分子链上具有大量活性较高的侧链羧基,具有极高保湿性和吸水性,易于和一些大分子物质结合生成稳定的复合物,是一类理想的可生物降解高分子材料。γ
‑ꢀ
聚谷氨酸对环境无污染,为绿色生物产品,具有极佳的生物可降解性、成膜性、保湿性等许多独特的理化和生物学特性,在注重环保、强调可持续发展的今天,这种生物合成的可降解型功能材料受到人们的青睐,逐渐地被应用于医药制造、食品加工及蔬菜、水果、海产品的防冻等许多领域,是一种具有极大开发价值和广阔前景的多功能新型生物制品。
3.γ-聚谷氨酸的生产过程中,由于液体发酵法所得到的发酵液具有很大的粘度,给下游的分离纯化带来较大困难,通常的分离提取方法都得不到理想效果,因此,提高γ-聚谷氨酸的分离效率是发酵生产该材料的另一技术关键。
技术实现要素:4.针对现有技术中的缺陷,本发明提供一种可降解材料的提取工艺,以提高γ-聚谷氨酸的分离效率。
5.本发明是通过以下技术方案实现的:一种可降解材料的提取工艺,包括以下步骤:步骤1:发酵液的预处理;将发酵液进行稀释,吸收后的发酵液进行超声处理,将发酵液离心,取上清液;步骤2:发酵液的萃取和分离;将上清液分别利用无水乙醇和甘露糖醇进行二次萃取;步骤3:沉淀物洗涤:将步骤2中得到二次萃取的沉淀物用80%的乙醇进行洗涤,洗涤次数2-3次;步骤4:将步骤3得到的沉淀物中按照体积比例为1:1添加4%的氯化钠溶液,ph控制在8-9.5,搅拌30分钟,转速为400r/min,静置沉淀过夜;步骤5:将步骤4中的沉淀物进行离心分离,收集沉淀物,然后透析除盐,沉淀物进行真空冷冻干燥,得到γ-聚谷氨酸纯品。
6.优选地,所述步骤1具体包括以下操作:首先用生理盐水对15ml的发酵液进行稀释,发酵液和生理盐水的体积比为1:1,然后将发酵液进行40-70w功率下进行超声处理,超
声温度为50-70℃,超声时间为50-120分钟,将超声稀释后的发酵液离心,取上清液。
7.优选的,所述步骤2具体包括以下操作:(1)一次萃取:将步骤1的发酵液中加入2倍体积的80%的无水乙醇,然后进行搅拌,搅拌时间为30分钟,搅拌转速为400r/min,离心分离,取沉淀物;(2)二次萃取:将一次萃取得到的沉淀物中加入45ml的甘露糖醇,进行搅拌,搅拌时间为30分钟,搅拌转速为400r/min,离心分离,取沉淀物。
8.优选的,所述步骤5中的透析除盐的包括以下操作,将沉淀物加入3倍体积的超纯水溶解,超声溶解完全,离心取上清液,加入到透析袋中,透析48小时,然后将透析袋的样品进行真空冷冻干燥,得到γ-聚谷氨酸纯品。
9.优选的,将透析袋的样品置于-80℃超低温冰箱中进行预冷12 h,将预冻好的冻干瓶放进物料盘内,盖上有机玻璃罩开启真空泵进行真空冷冻干燥,保持气压1pa至冻干结束,冻干时间为12h。
10.本发明的有益效果体现在:(1)本发明首先通过超声和生理盐水稀释的办法降低了发酵液的粘度,利用生理盐水进行稀释引入了大量的na
+
,高浓度的盐离子抑制了羧基基团间的排斥力,因此,γ-pga发酵液的粘度会大幅度下降,因此可以大幅度提高聚谷氨酸的提取率。
11.(2)本发明中首次采用了乙醇和甘露糖醇二次萃取的方法,采用乙醇可以大幅度的萃取一部分的杂质分子,而甘露糖醇的二次提纯,保证了聚谷氨酸的产品的纯度。
12.(3)本发明中的干燥方式首先将透析袋样品首先进行预冷,以使得样品冻结完全和形成小的冰晶,降低冷冻干燥所需时间,相比于真空干燥,采用该方式的γ-pga收率更高,且最终所获成品性状和品质更佳更优。
附图说明
13.图1为各个实施例的γ-pga的提取率实现结果对比图。
具体实施方式
14.为更进一步阐述本发明所采取的技术手段及其效果,以下结合本发明的优选实施例来进一步的说明本发明的技术方案,但本发明并非局限在实施例范围内。
15.实施例1一种可降解材料的提取工艺,包括以下步骤:步骤1:发酵液的预处理;首先用生理盐水对15ml的发酵液进行稀释,发酵液和生理盐水的体积比为1:1,然后将发酵液进行40-70w功率下进行超声处理,超声温度为50-70℃,超声时间为50-120分钟,将超声稀释后的发酵液离心,取上清液。
16.步骤2:发酵液的萃取和分离;(1)一次萃取:将步骤1的发酵液中加入2倍体积的80%的无水乙醇,然后进行搅拌,搅拌时间为30分钟,搅拌转速为400r/min,离心分离,取沉淀物;(2)二次萃取:将一次萃取得到的沉淀物中加入45ml的甘露糖醇,进行搅拌,搅拌时间为30分钟,搅拌转速为400r/min,离心分离,取沉淀物;步骤3:沉淀物洗涤:将步骤2中得到二次萃取的沉淀物用80%的乙醇进行洗涤,洗
涤次数2-3次。
17.步骤4:将步骤3得到的沉淀物中按照体积比例为1:1添加4%的氯化钠溶液,ph控制在8-9.5,搅拌30分钟,转速为400r/min,静置沉淀过夜;步骤5:将步骤4中的沉淀物进行离心分离,收集沉淀物,然后透析除盐,沉淀物进行真空冷冻干燥,得到γ-聚谷氨酸纯品。
18.所述步骤5中的透析除盐的包括以下操作,将沉淀物加入3倍体积的超纯水溶解,超声溶解完全,离心取上清液,加入到透析袋中,透析48小时,然后将透析袋的样品进行真空冷冻干燥,得到γ-聚谷氨酸纯品。
19.真空冷冻干燥的操作如下:将透析袋的样品置于-80℃超低温冰箱中进行预冷12 h,将预冻好的冻干瓶放进物料盘内,盖上有机玻璃罩开启真空泵进行真空冷冻干燥,保持气压1pa至冻干结束,冻干时间为12h。
20.实施例2一种可降解材料的提取工艺,包括以下步骤:步骤1:发酵液的预处理;首先用蒸馏水对15ml的发酵液进行稀释,发酵液和蒸馏水的体积比为1:1,然后将发酵液进行40-70w功率下进行超声处理,超声温度为50-70℃,超声时间为50-120分钟,将超声稀释后的发酵液离心,取上清液。
21.步骤2:发酵液的萃取和分离;(1)一次萃取:将步骤1的发酵液中加入2倍体积的80%的无水乙醇,然后进行搅拌,搅拌时间为30分钟,搅拌转速为400r/min,离心分离,取沉淀物;(2)二次萃取:将一次萃取得到的沉淀物中加入45ml的甘露糖醇,进行搅拌,搅拌时间为30分钟,搅拌转速为400r/min,离心分离,取沉淀物;步骤3:沉淀物洗涤:将步骤2中得到二次萃取的沉淀物用80%的乙醇进行洗涤,洗涤次数2-3次。
22.步骤4:将步骤3得到的沉淀物中按照体积比例为1:1添加4%的氯化钠溶液,ph控制在8-9.5,搅拌30分钟,转速为400r/min,静置沉淀过夜;步骤5:将步骤4中的沉淀物进行离心分离,收集沉淀物,然后透析除盐,沉淀物进行真空冷冻干燥,得到γ-聚谷氨酸纯品。
23.所述步骤5中的透析除盐的包括以下操作,将沉淀物加入3倍体积的超纯水溶解,超声溶解完全,离心取上清液,加入到透析袋中,透析48小时,然后将透析袋的样品进行真空冷冻干燥,得到γ-聚谷氨酸纯品。
24.真空冷冻干燥的操作如下:将透析袋的样品置于-80℃超低温冰箱中进行预冷12 h,将预冻好的冻干瓶放进物料盘内,盖上有机玻璃罩开启真空泵进行真空冷冻干燥,保持气压1pa至冻干结束,冻干时间为12h。
25.实施例1与实施例2的不同之处在于使用了蒸馏水进行稀释。
26.实施例3一种可降解材料的提取工艺,包括以下步骤:步骤1:发酵液的预处理;首先用生理盐水对15ml的发酵液进行稀释,发酵液和生理盐水的体积比为1:1,然后将发酵液进行40-70w功率下进行超声处理,超声温度为50-70℃,超声时间为50-120分钟,将超声稀释后的发酵液离心,取上清液。
27.步骤2:发酵液的萃取和分离;将步骤1的发酵液中加入2倍体积的80%的无水乙醇,然后进行搅拌,搅拌时间为30分钟,搅拌转速为400r/min,离心分离,取沉淀物;步骤3:沉淀物洗涤:将步骤2中得到萃取的沉淀物用80%的乙醇进行洗涤,洗涤次数2-3次。
28.步骤4:将步骤3得到的沉淀物中按照体积比例为1:1添加4%的氯化钠溶液,ph控制在8-9.5,搅拌30分钟,转速为400r/min,静置沉淀过夜;步骤5:将步骤4中的沉淀物进行离心分离,收集沉淀物,然后透析除盐,沉淀物进行真空冷冻干燥,得到γ-聚谷氨酸纯品。
29.所述步骤5中的透析除盐的包括以下操作,将沉淀物加入3倍体积的超纯水溶解,超声溶解完全,离心取上清液,加入到透析袋中,透析48小时,然后将透析袋的样品进行真空冷冻干燥,得到γ-聚谷氨酸纯品。
30.真空冷冻干燥的操作如下:将透析袋的样品置于-80℃超低温冰箱中进行预冷12 h,将预冻好的冻干瓶放进物料盘内,盖上有机玻璃罩开启真空泵进行真空冷冻干燥,保持气压1pa至冻干结束,冻干时间为12h。
31.实施例1和实施例3的区别在于仅使用乙醇进行一次提取。
32.实施例4一种可降解材料的提取工艺,包括以下步骤:步骤1:发酵液的预处理;首先用生理盐水对15ml的发酵液进行稀释,发酵液和生理盐水的体积比为1:1,然后将发酵液进行40-70w功率下进行超声处理,超声温度为50-70℃,超声时间为50-120分钟,将超声稀释后的发酵液离心,取上清液。
33.步骤2:发酵液的萃取和分离;(1)一次萃取:将步骤1的发酵液中加入2倍体积的80%的无水乙醇,然后进行搅拌,搅拌时间为30分钟,搅拌转速为400r/min,离心分离,取沉淀物;(2)二次萃取:将一次萃取得到的沉淀物中加入45ml的甘露糖醇,进行搅拌,搅拌时间为30分钟,搅拌转速为400r/min,离心分离,取沉淀物;步骤3:沉淀物洗涤:将步骤2中得到二次萃取的沉淀物用80%的乙醇进行洗涤,洗涤次数2-3次。
34.步骤4:将步骤3得到的沉淀物中按照体积比例为1:1添加4%的氯化钠溶液,ph控制在8-9.5,搅拌30分钟,转速为400r/min,静置沉淀过夜;步骤5:将步骤4中的沉淀物进行离心分离,收集沉淀物,然后透析除盐,沉淀物进行真空干燥,得到γ-聚谷氨酸纯品。
35.所述步骤5中的透析除盐的包括以下操作,将沉淀物加入3倍体积的超纯水溶解,超声溶解完全,离心取上清液,加入到透析袋中,透析48小时,然后将透析袋的样品进行真空冷冻干燥,得到γ-聚谷氨酸纯品。
36.实施例4和实施例1的区别在于实施例4采用了真空干燥的方式进行干燥。
37.各个实施例实验结束后计算得到的γ-pga的提取率,计算方法如下:由于十六烷基三甲基溴化铵(ctab)溶液与γ-pga反应产生浑浊的特性,通过反应体系的吸光度来反映其浊度,进而通过浊度与γ-pga浓度的线性关系计算γ-pga的提取率,计算结果如下图1所
示:实施例1和实施例2结果表明,超声和生理盐水稀释的办法可以提高聚谷氨酸的提取率,其机理为利用超声处理可以降低发酵液的粘度,利用生理盐水进行稀释引入了大量的na+,高浓度的盐离子抑制了羧基基团间的排斥力,因此,γ-pga发酵液的粘度也因此大幅度下降,导致聚谷氨酸的提取率的升高。
38.实施例1和实施3相比,采用了乙醇和甘露糖醇二次萃取的方法,采用乙醇可以大幅度的萃取一部分的杂质分子,而甘露糖醇的二次提纯,保证了聚谷氨酸的产品的纯度。
39.实施例1采用真空冷冻干燥的方式,实施例4采用真空干燥的方式,本发明中的干燥方式首先将透析袋样品首先进行预冷,以使得样品冻结完全和形成小的冰晶,降低冷冻干燥所需时间,相比于真空干燥,采用该方式的γ-pga提取率更高,且最终所获成品性状和品质更佳更优。