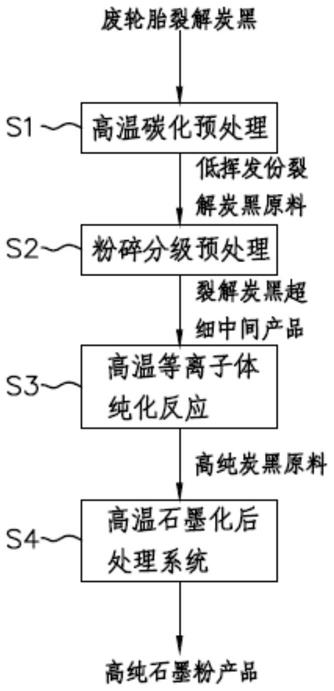
1.本发明涉及炭黑制备技术领域,尤其涉及一种废旧轮胎裂解炭黑高温等离子体纯化处理方法。
背景技术:2.当前,发展循环经济是实现经济社会良性发展的必然选择,推动绿色发展是消除和减少污染物排放的必由之路。我国废旧轮胎及裂解炭黑焚烧率占比接近55%。相对于其他处置技术而言,热解技术已经最大程度的将炭元素固定在裂解炭黑产品中。但裂解炭黑品质低,杂质含量高,无法进行高价值利用,最终也只能作为燃料进行焚烧。废旧轮胎裂解炭黑深度资源化处理系统是对这些“固体废物”进行高价值资源化利用和无害化处置的有效途径,对于发展循环经济、节约炭黑资源、降低能源消耗、保护生态环境、减少并逐步消除“黑色污染”,以及促进橡胶工业绿色可持续发展。
3.裂解炭黑中灰分主要成分为zno、sio2、al2o3、cao等无机氧化物,现有纯化方法一般采用酸洗工艺或酸洗+碱洗联合工艺,这些工艺在生产运行过程中会产生高浓度的酸碱废液,不仅占地面积大,而且严重污染环境,自动化程度较低,工作环境恶劣。本发明针对废轮胎裂解炭黑深度资源化处理过程中的关键环节,重点改善裂解炭黑的品质低和杂质含量高的缺陷,解决其销路难、无法高价值资源回收利用的问题。
技术实现要素:4.本发明所要解决的技术问题是克服现有技术中存在的不足,提供一种废旧轮胎裂解炭黑高温等离子体纯化处理方法,能够使裂解炭黑中的无机灰分反应更快和去除更彻底。
5.本发明是通过以下技术方案予以实现:
6.一种废旧轮胎裂解炭黑高温等离子体纯化处理方法,其特征在于,包括如下步骤:a.将废旧轮胎裂解处理后得到裂解炭黑原料;b.所述裂解炭黑原料进入预处理系统,经预处理产生裂解炭黑中间产品;c.所述裂解炭黑中间产品进入高温等离子体纯化反应器,在等离子体发生器产生的高温、高活性的等离子体炬气体作用下发生纯化反应,得到高纯炭黑原料; d.所述高纯炭黑原料进入后处理改性系统,最终得到高纯炭黑衍生产品。
7.根据上述技术方案,优选地,步骤a中裂解温度为300-800℃。
8.根据上述技术方案,优选地,所述预处理系统包括高温炭化预处理、粉碎分级预处理、筛分预处理和酸洗超声预处理、过滤烘干预处理中的一种或多种。
9.根据上述技术方案,优选地,所述高温炭化预处理温度为800-1500℃。
10.根据上述技术方案,优选地,所述裂解炭黑中间产品的粒径为0.5-200 μm,有机挥发份含量为0-2%,灰分含量为1%-15%。
11.根据上述技术方案,优选地,步骤c中纯化反应温度为1500-3500℃。
12.根据上述技术方案,优选地,所述等离子体炬气体包括氩气、氮气、氦气、四氟化
碳、四氟乙烯、氟利昂、氢气中的一种或多种。
13.根据上述技术方案,优选地,步骤c中所述等离子体发生器产生等离子体炬气体的工作气压力为0.4-1.6mpa,所述等离子体发生器功率为 50-300kw,冷却水流量为10-20m3/h,所述等离子体炬气体平均温度为 5000-10000℃。
14.根据上述技术方案,优选地,所述后处理改性系统包括石墨化后处理、表面包覆改性后处理、药剂活化后处理、洗涤过滤烘干后处理中的一种或多种。
15.本发明的有益效果是:
16.本发明工艺流程简单,运行成本低,能够实现连续化生产,可以充分利用等离子体温度高、能量密度大、气氛可控和活性组分丰富等特点,通过气固相间充分反应,能够使裂解炭黑中的无机灰分反应更快和去除更彻底,获得高纯度的炭黑原料,改善目前废旧轮胎裂解炭黑因灰分含量高、无法高值化利用所造成的环境污染和资源浪费问题。
附图说明
17.图1是本发明实施例1的工艺流程示意图。
18.图2是本发明实施例2的工艺流程示意图。
具体实施方式
19.为了使本技术领域的技术人员更好地理解本发明的技术方案,下面结合附图和最佳实施例对本发明作进一步的详细说明。基于发明中的实施例,本领域普通技术人员在没有做出创造性劳动前提下所获得的所有其他实施例,都属于发明保护的范围。
20.如图所示,本发明包括如下步骤:
21.a.将废旧轮胎经300-800℃裂解处理后得到裂解炭黑原料;
22.b.所述裂解炭黑原料进入预处理系统,在800-1500℃的温度下,经预处理产生裂解炭黑中间产品,其中裂解炭黑中间产品的粒径为0.5-200μ m,有机挥发份含量为0-2%,灰分含量为1%-15%,本例中预处理系统包括但不限于以下方法:高温炭化预处理、粉碎分级预处理、筛分预处理和酸洗超声预处理、过滤烘干预处理等;
23.c.所述裂解炭黑中间产品进入高温等离子体纯化反应器,在等离子体发生器产生的高温、高活性的等离子体炬气体作用下发生纯化反应,本例中等离子体发生器产生等离子体炬气体的工作气压力为0.4-1.6mpa,等离子体发生器功率为50-300kw,冷却水流量为10-20m3/h,等离子体炬气体平均温度为5000-10000℃,等离子体炬气体包括氩气、氮气、氦气、四氟化碳、四氟乙烯、氟利昂、氢气中的一种或多种组合,其中纯化反应温度优选为1500-3500℃,通过高温改变裂解炭黑中所含灰分的化学组成和相态,使裂解炭黑中间产品所含灰分变为气态并随高温等离子体尾气排出反应器,最终得到高纯炭黑原料;
24.d.所述高纯炭黑原料进入后处理改性系统,其中后处理改性系统包括石墨化后处理、表面包覆改性后处理、药剂活化后处理、洗涤过滤烘干后处理中的一种或多种,根据不同炭黑应用需求对高纯炭黑原料进行改性处理,最终得到高纯炭黑衍生产品。
25.本发明工艺流程简单,运行成本低,能够实现连续化生产,可以充分利用等离子体温度高、能量密度大、气氛可控和活性组分丰富等特点,通过气固相间充分反应,能够使裂解炭黑中的无机灰分反应更快和去除更彻底,获得高纯度的炭黑原料,改善目前废旧轮胎
裂解炭黑因灰分含量高、无法高值化利用所造成的环境污染和资源浪费问题。
26.基于上述实施方案,本发明可优选如下两种实施例:
27.实施例1
28.s1、将废旧轮胎经300-800℃裂解处理后得到裂解炭黑原料,裂解炭黑原料中灰分含量为15%,有机挥发份含量3%,粒径0.5-10mm;
29.s2、将废旧轮胎经裂解处理后得到的裂解炭黑在氩气保护下进行高温炭化预处理,碳化温度800-1500℃,处理时间为2h,有机挥发份去除率为80%-95%,得到低挥发份裂解炭黑原料;
30.s3、将步骤s2处理后的低挥发份裂解炭黑原料送入粉碎分级预处理系统,经气流超细粉碎机粉碎处理并经分级筛分后,得到粒径为10-50μm 的裂解炭黑中间产品;
31.s4、将裂解炭黑中间产品送入高温等离子体纯化反应器,等离子体工作气体为氩气,强化辅助反应气为四氟化碳,氩气流量为10-20nm3/h,四氟化碳流量为2-5nm3/h,高活性的电离态等离子体炬气体平均温度为 5000-10000℃,纯化反应器平均温度为1800-2500℃,停留时间为20min,得到高纯炭黑原料;
32.s5、将高纯炭黑原料送入高温石墨化后处理系统,石墨化后处理温度 2800-3000℃,高温停留时间2h,最后得到高纯石墨粉产品。
33.经以上工序处理后高纯石墨粉产品纯度为99.9%-99.99%,粒径为 10-50μm,石墨化度为80%-90%,高纯石墨粉产品可替代天然石墨原料,实现了裂解炭黑的高价值资源化回收利用。
34.实施例2
35.s1、将废旧轮胎经300-800℃裂解处理后得到裂解炭黑原料,裂解炭黑原料中灰分含量为15%,有机挥发份含量3%,粒径0.5-10mm;
36.s2、将废旧轮胎经裂解处理后得到的裂解炭黑在氩气保护下进行高温炭化预处理,碳化温度800-1500℃,处理时间为2h,有机挥发份去除率为80%-95%,得到低挥发份裂解炭黑原料;
37.s3、将步骤s2处理后的低挥发份裂解炭黑原料送入粉碎分级预处理系统,经气流超细粉碎机粉碎处理并经分级筛分后,得到粒径为10-50μm 的裂解炭黑中间产品;
38.s4、将裂解炭黑中间产品送入高温等离子体纯化反应器,等离子体工作气体为氩气,强化辅助反应气为四氟化碳,氩气流量为10-20nm3/h,四氟化碳流量为2-5nm3/h,高活性的电离态等离子体炬气体平均温度为 5000-10000℃,纯化反应器平均温度为1800-2500℃,停留时间为20min,得到高纯炭黑原料;
39.s5、将高纯炭黑原料送入表面包覆改性后处理系统,表面改性采用koh 活化处理,炭与koh重量比为1:1-1:5,烧结温度为500℃,停留时间为 2h,得到活化炭黑中间产品;
40.s6、将活化炭黑中间产品送入洗涤过滤烘干后处理系统,炭与水重量比为1:10,洗涤次数为2-3次,过滤掉水分最后得到含水率30%-50%的高纯活化炭黑,在对其在110℃下进行烘干,烘干至含水率0.5%-2%,最后得到高纯炭黑产品。
41.经以上工序处理后高纯炭黑产品纯度为99.9%-99.99%,比表面积为 200m2/g-800m2/g,高纯炭黑产品具有较高的比表面积和吸附活性可替代商品炭黑,实现了裂解炭黑的高价值资源化回收利用。
42.以上所述仅是本发明的优选实施方式,应当指出,对于本技术领域的普通技术人员来说,在不脱离本发明原理的前提下,还可以做出若干改进和润饰,这些改进和润饰也应视为本发明的保护范围。