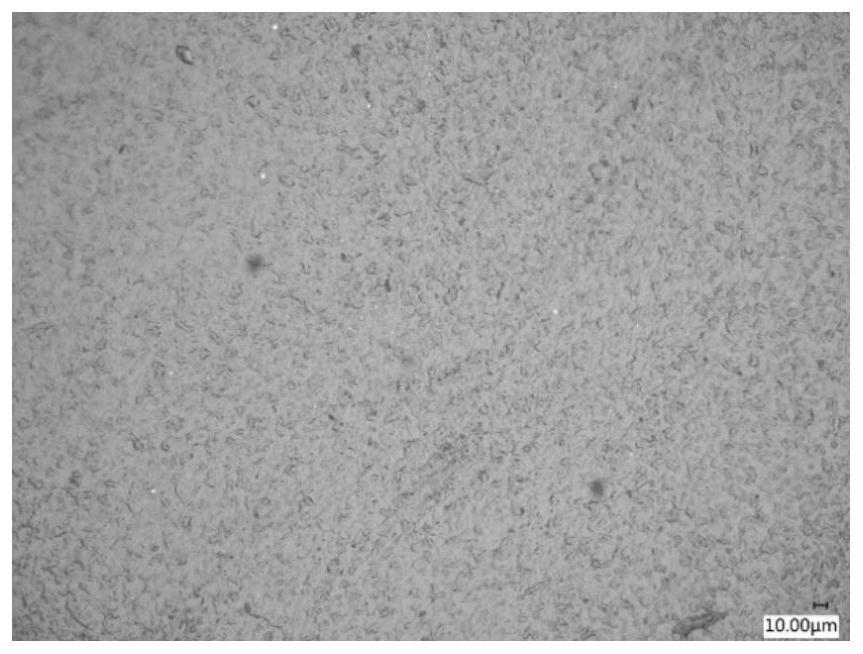
1.本发明属于抗空蚀涂层技术领域。
背景技术:2.空蚀是一种特殊的磨损和腐蚀形式,通常发生在船舶部件的表面,如泵、船用螺旋桨和涡轮叶片。由空化引起的气泡坍塌产生的最大压力可以达到1500mpa,其频率高达10万赫兹,这种周期性高压通常会导致瞬间高温(300℃)和较大的冲击力,材料的局部表面会迅速疲劳。产生的瞬间高温如果不能及时释放到海水中,对将会导致涂层熔化,同时涂层表面会受到气泡和微射流的反复冲击时,无力抵挡,导致点蚀和空隙的产生,使涂层强度急剧下降,从而影响其使用寿命,严重威胁组件的正常和安全运行。
3.另外船舶入水后,船体表面受到海水浸泡发生电化学腐蚀,造成基底服役寿命锐减、然而迄今为止,目前几乎所有的研究只关注与涂层对防腐、防空蚀单方面影响,而不考虑其综合影响,目前还没有报道专门针对抗空蚀和防腐相结合的涂层。
技术实现要素:4.针对上述现象,本发明提出了抗空蚀、防腐多功能涂料及涂层,所述涂料的组分为:聚氨酯预聚体溶液、扩链剂、溶剂和碳化硅粉末;所述的碳化硅粉末占涂料总质量的百分比为1wt%-3wt%,其中最优为3wt%;
5.聚氨酯预聚体溶液的单体为甲苯-2,4-二异氰酸酯(tdi)和聚四氢呋喃醚二醇(ptmg);tdi与ptmg质量比为(0.35~0.5):1;
6.溶剂为乙酸乙酯、乙酸丁酯、dmf、甲苯、异丙醇和丙酮中的一种或几种;溶剂与聚氨酯预聚体溶液的质量比为(7:3)~(1:2);
7.扩链剂为3,3'-二氯-4,4'-二氨基二苯基甲烷(moca)和1,4-丁二醇(bdo)的混合溶液;bdo与moca的质量比为0.67:1;扩链剂与聚氨酯预聚体溶液的质量比为(0.13~0.19):1;
8.所述的碳化硅粉末粒径优选5000-8000目。
9.聚四氢呋喃醚二醇(ptmg)的优选的分子量为1000。
10.所述涂料及涂层的制备方法如下:
11.1)按照tdi与ptmg质量比为(0.35~0.5):1的比例称取tdi与ptmg;
12.2)将ptmg和tdi分别倒入旋转蒸发仪的旋转瓶中,在120℃、0.093mpa真空度下减压蒸馏2h,冷却至60
°
之后装瓶密封保存。
13.3)将tdi倒入四口烧瓶中,并将油浴锅加热至50℃并通入氮气,之后将ptmg倒入至恒压滴液漏斗并以1-20滴/s的速度滴加到四口烧瓶中,ptmg滴加完成之后保证50℃温度继续反应30min,获得聚氨酯预聚体溶液;
14.4)按照bdo与moca的质量比为0.67:1称取bdo与moca混合溶液作为扩链剂,在真空干燥箱中抽真空并加热至110℃使得moca融化。
15.5)取熔化后的扩链剂加入到四口烧瓶,同时也需要加入溶剂,使得溶剂与溶液的质量比值为20~40%;将油浴锅的温度升温以保证溶液的温度可以达到60℃,之后恒温反应6h,冷却至常温之后装瓶密封保存;
16.6)将一定量的碳化硅粉末倒入溶剂中,并在连续超声4小时,使得碳化硅在溶剂中分散,所得碳化硅分散液中碳化硅的浓度为0.5~1ml/mg;
17.7)按照碳化硅粉末占涂料总质量的百分比为1wt%-3wt%称取聚氨酯预聚体溶液和碳化硅分散液,将二者混合超声4小时,之后继续搅拌4小时;
18.8)将步骤7)的混合液在60
°
环境中挥发溶剂,使得溶质与溶液的质量比为2:3后,得到涂料
19.9)将所得涂料使用刷涂、刮涂或者喷涂的方式涂覆于基底处,110℃下硫化12h使得涂层固化。
20.本发明的有益效果:
21.本发明采用聚氨酯为涂层主体,可有效抵挡空泡破裂带来的持续不断的冲击,此外该涂层添加碳化硅纳米颗粒具有良好的散热功能,可保证所吸收空化的能量通过热能瞬间散发出去,同时该涂层的碳化硅纳米颗粒能够阻挡水分子的进入,因此也具有高效的防腐能力。
22.另外添加碳化硅粉末也可以有效提高聚氨酯涂层的力学性能,进而提高其抗空蚀能力。
附图说明
23.图1实施例1空蚀结果光学显微镜图
24.图2实施例2空蚀结果光学显微镜图
25.图3对比例空蚀结果光学显微镜图
26.图4电化学腐蚀测试实验图
27.图5为对比例和实施例应力应变图
具体实施方式
28.下面以具体实施例的形式对本发明技术方案做进一步解释和说明。
29.实施例1:
30.(1)将ptmg 1000倒入旋转蒸发仪的旋转瓶中,在120℃、0.093mpa真空度下减压蒸馏2h,冷却至60℃之后装瓶密封保存。
31.(2)40g tdi100溶液倒入四口烧瓶中,并将油浴锅加热至50℃并通入氮气,之后将80g的ptmg倒入至恒压滴液漏斗并以1-20滴/s的速度滴加到四口烧瓶中,ptmg滴加完成之后保证50℃温度继续反应30min,
32.(3)称取一定量的8.978g bdo与13.4g moca混合溶液作为扩链剂,在真空干燥箱中抽真空并加热至110℃使得moca融化。
33.(4)取上述熔化后的扩链剂加入到四口烧瓶,同时也需要加入332g的溶剂。
34.(5)将油浴锅的温度升温以保证溶液的温度可以达到60℃,之后恒温反应6h,冷却至常温之后装瓶密封保存。
35.(6)将1.43g的碳化硅倒入1.43升的溶剂中,并在连续超声4小时,使得碳化硅在溶剂中分散,得到浓度为1mg/ml的碳化硅分散液;
36.(7)称取上述步骤(4)中的预聚体溶液与步骤(6)中的碳化硅分散液混合超声4小时,之后继续搅拌4小时。
37.(8)将步骤(7)的混合液在60
°
环境中挥发溶剂,使得溶质与溶液比为2:3后,后将溶液使用刷涂、刮涂或者喷涂的方式涂覆于基底处,110℃下硫化12h使得涂层固化。
38.实施例2:
39.(1)将ptmg1000倒入旋转蒸发仪的旋转瓶中,在120℃、0.093mpa真空度下减压蒸馏2h,冷却至60℃之后装瓶密封保存。
40.(2)40g tdi100溶液倒入四口烧瓶中,并将油浴锅加热至50℃并通入氮气,之后将80g的ptmg倒入至恒压滴液漏斗并以1-20滴/s的速度滴加到四口烧瓶中,ptmg滴加完成之后保证50℃温度继续反应30min,
41.(3)称取一定量的8.978g bdo与13.4g moca混合溶液作为扩链剂,在真空干燥箱中抽真空并加热至110℃使得moca融化。
42.(4)取上述熔化后的扩链剂加入到四口烧瓶,同时也需要加入332g的溶剂。
43.(5)将油浴锅的温度升温以保证溶液的温度可以达到60℃,之后恒温反应6h,冷却至常温之后装瓶密封保存
44.(6)将2.8g的碳化硅倒入1.4升的溶剂中,并在连续超声4小时,使得碳化硅在溶剂中分散。
45.(7)称取上述步骤(4)中的预聚体溶液与步骤(6)中的碳化硅分散液混合超声4小时,之后继续搅拌4小时。
46.(8)将步骤(7)的混合液在60
°
环境中挥发溶剂,使得溶质与溶液比为2:3后,后将溶液使用刷涂、刮涂或者喷涂的方式涂覆于基底处,110℃下硫化12h使得涂层固化。
47.对比例:
48.(1)将ptmg1000倒入旋转蒸发仪的旋转瓶中,在120℃、0.093mpa真空度下减压蒸馏2h,冷却至60℃之后装瓶密封保存。
49.(2)40g tdi100溶液倒入四口烧瓶中,并将油浴锅加热至50℃并通入氮气,之后将80g的ptmg倒入至恒压滴液漏斗并以1-20滴/s的速度滴加到四口烧瓶中,ptmg滴加完成之后保证50℃温度继续反应30min,
50.(3)称取一定量的8.978g bdo与13.4g moca混合溶液作为扩链剂,在真空干燥箱中抽真空并加热至110℃使得moca融化。
51.(4)取上述熔化后的扩链剂加入到四口烧瓶,同时也需要加入332g的溶剂。
52.(5)将油浴锅的温度升温以保证溶液的温度可以达到60℃,之后恒温反应6h,冷却至常温之后装瓶密封保存
53.(6)将步骤(5)的混合液在60
°
环境中挥发溶剂,使得溶质与溶液比为2:3后,后将溶液使用刷涂、刮涂或者喷涂的方式涂覆于基底处,110℃下硫化12h使得涂层固化。
54.本发明所述的tdi与ptmg质量比为0.35~0.5:1,以保证其高效的力学性能和抗空蚀能力。因为随着预聚体中nco基含量的增加,体系中硬段含量提高,使聚氨酯中的苯环、氨基甲酸酯基及脲基甲酸酯基含量增加,从而提高了聚氨酯的拉伸强度和硬度,适当提高聚
氨酯的拉伸强度和硬度可有效提高其抗空蚀的能力。
55.本发明所述的bdo与moca的质量比为0.67:1,保证良好的bdo与moca的摩尔比可保证涂层具有一定力学性能且涂层硬度适宜,若moca含量过高则外硬段中含有苯环的结构随之增多,最终使材料的硬度、拉伸强度增大,当涂层的硬度过大时,材料的韧性降低,无法有效的抵抗空蚀。
56.本发明所述的碳化硅其与聚氨酯的质量比为1wt%-3wt%,其中最优为3wt%,碳化硅含量过多,会导致碳化硅在聚氨酯中团聚影响了涂层抗空蚀性能。
57.基于gb/t 6383-2009《振动空蚀试验方法》对上述涂层进行长达12小时的空蚀实验。获得以下结果:
[0058] 质量损失实施例12.3mg实施例21.9mg对比例4.3mg
[0059]
图1~图3为实施例1、实施例2和对比例的空蚀结果光学显微镜图,实施例1和实施例2经过12小时的空蚀,表面基本没有出现空蚀坑,而对比例1经过12小时的空蚀,表面已经出现大量的空蚀坑(圈中部分所示)。
[0060]
图4为电化学腐蚀测试实验图,从图中可以看出本发明所制备的涂层具有高效的防腐能力。
[0061]
图5为对比例和实施例应力应变图,从图5可以看出,实施例1和实施例2就有良好的拉伸性能,且拉伸性能比对比例高,可推测实施例1和实施例2可抵抗空蚀带来的疲劳破坏。