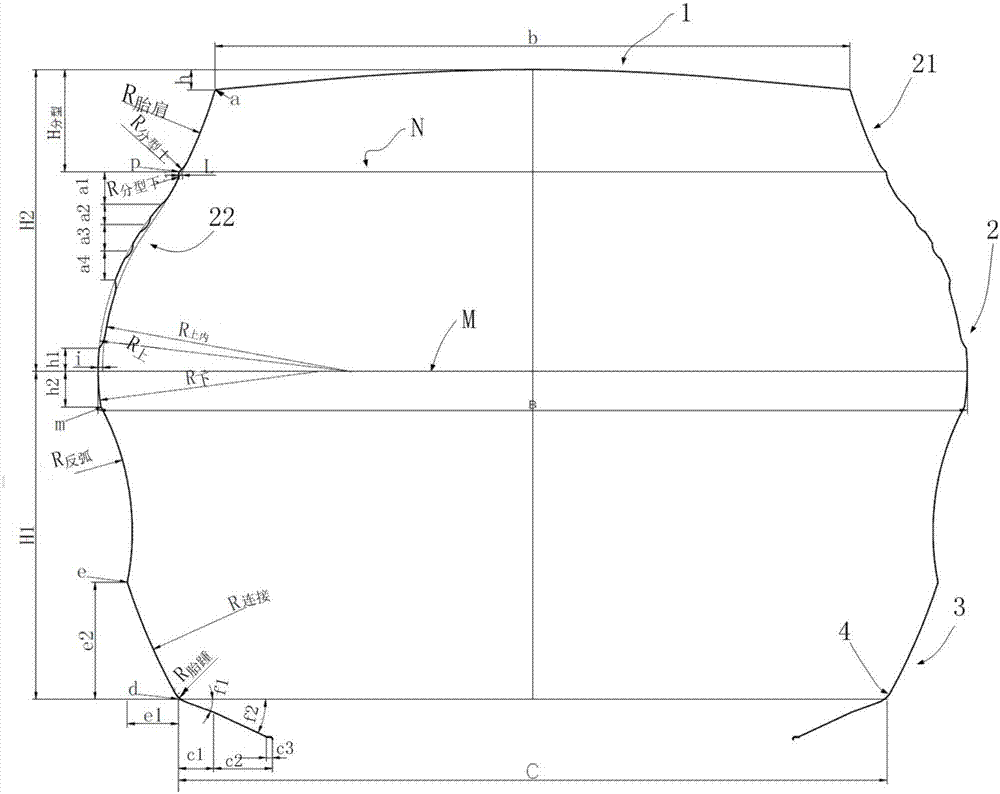
本发明涉及一种tbr轮胎异形轮廓结构及具有该轮廓的轮胎,属于轮胎生产制造
技术领域:
。
背景技术:
:为保证全钢子午线轮胎在使用时的承载性能,普通全钢载重子午线轮胎(tbr)在胎侧轮廓设计多数仍采用胎冠至胎圈均匀过度的圆弧设计,参考图1,为现有轮胎轮廓的设计方案图,胎侧轮廓设计在轮胎水平轴上下主要由两段圆弧设计,该常规轮廓设计技术已使用多年。目前伴随车辆运输的规范、道路路况的优化,车辆在行驶时司机的驾驶体验也越来越受到重视,同时轮胎的单胎重量、油耗等也越来越受到司机的重视。轮胎轻量化也是轮胎行业发展的一个趋势,不仅可以降低生产成本,同时可以节油并减少对环境的污染,但是现有的轮胎轮廓设计显然很难满足上述需求,亟待提出一种新的轮胎轮廓,降低轮胎重量及滚阻,提高拆装及搬运便捷性。技术实现要素:本发明所要解决的技术问题在于针对现有技术中存在的不足,提供一种tbr轮胎异形轮廓结构及具有该轮廓的轮胎,在改变轮胎胎侧轮廓的基础上,降低轮胎的滚阻及重量,提升产品的节油、驾驶舒适性能,便于轮胎装拆。本发明是采用以下的技术方案实现的:一种tbr轮胎异形轮廓结构,包括胎冠部、胎侧部、胎圈部及胎踵部,轮胎的轮廓设计整体异于现有常规设计,体现在轮胎胎侧部的设计弧段数和方向上,所述胎侧部包括位于轮胎水平轴上方的胎肩段和上胎侧圆弧,以及位于轮胎水平轴下方的下胎侧圆弧;所述胎肩段位于胎冠部的下部两侧,且与上胎侧圆弧相切;所述上胎侧圆弧包括上圆弧和上内圆弧,且所述上圆弧和上内圆弧为圆心位于轮胎水平轴上的同心圆弧,上圆弧和上内圆弧之间由防擦部过渡连接;所述下胎侧圆弧包括第一下圆弧和与第一下圆弧连接的反弧段,所述第一下圆弧的圆心位于轮胎水平轴上,且与所述上圆弧相连接,所述反弧段下方为连接反弧段和胎踵部的连接弧,反弧段的设计完全区别与常规产品要求的均匀过渡设计,对于优化胎侧部位材料效果显著且有利于吸收来自路面的冲击。进一步的,为保证异形轮廓轮胎对圈部支撑性能,增加胎圈部位的厚度,以提高其支撑效果,所述连接弧为中间胎圈部位对轮胎的支撑作用,其半径r连接为200mm-240mm,且有效提升轮胎在使用过程中的舒适性。进一步的,为使轮胎上胎侧过度均匀,且考虑轮胎内轮廓的变化,所述上圆弧的半径r上为70mm至90mm,较同型号常规轮胎轮廓设计半径小40mm—50mm;上内圆弧半径r上内比上圆弧的半径r上小,上圆弧与上内圆弧的半径差决定了胎侧防擦部的厚度,配合防擦部设计在提升轮胎防剐蹭的同时改善轮胎使用过程中对来自地面冲击的缓冲,增加车辆的驾驶舒适性。进一步的,所述上内圆弧半径r上内与上圆弧半径r上的差值为0.6mm-2mm,该值的选取根据轮胎承载及路况的差异可在选值范围内变动,较好路况、长里程行驶选值偏小,较差轮廓、承载较大则选值偏大。进一步的,所述防擦部上设置有多个不同形状的凹槽,包括多段防擦弧,且防擦部下端点与轮胎水平轴的垂直距离为8mm-10mm,防擦部上不同形状的凹槽,在优化轮胎重量、提升防擦效果的同时,增加了轮胎的立体感,对轮胎运行过程中的散热也较为有益。进一步的,所述第一下圆弧的上端点为轮胎水平轴端点,其下端点位于轮胎水平轴下方10mm-15mm位置处,为保证轮胎下胎侧圆弧与上胎侧圆弧弧的圆滑过渡,其半径比上圆弧半径r上小10mm-15mm。进一步的,所述反弧段的半径r反弧为上圆弧半径r上的1倍-1.2倍,以保证轮胎在使用过程中的舒适性及生产过程的可操控性,同时考虑轮胎整体质量的控制。进一步的,所述上胎侧圆弧和胎肩段之间设计有分型面,考虑胶料胶边的发生并考虑后期维修的便利,所述胎肩段与分型面相交的点在分型面水平线上向外偏移l距离,所述l的值小于2mm,所达到的点设为p点;所述分型面上下两侧分别为分型面上弧和分型面下弧,其半径分别为r分型上、r分型下,根据胎冠与侧板的配合,考虑胶料胶边的发生并考虑后期维修的便利,所述分型面上弧过p点与胎肩段相切,分型面下弧过p点与上内圆弧相切。本发明另外还提出一种轮胎,具有上述所述的异形轮廓结构,则具有该异形轮廓结构的轮胎,其上胎侧厚度由于采用防擦部凹槽设计较同型号常规轮胎胎侧厚度薄0.5mm-1.0mm,下胎侧采用反弧设计,其厚度较同型号常规轮胎胎侧厚度薄0.7mm-1.0mm,胎圈采用大半径圆弧设计,且为了提升胎圈的刚性及支撑效果,胎圈厚度较同型号常规轮胎厚度厚2mm-2.5mm。与现有技术相比,本发明的优点和积极效果在于:本发明所提出的tbr轮胎异形轮廓结构,突破原有轮胎轮廓设计思路及技术,独特设计了运用上胎侧圆弧、反弧、大圆弧连接胎踵等相互配合的设计思路,配合防擦部设计及常规的胎趾,在轮胎上制造出胎侧轮廓异于常规轮廓的产品。利用该技术方案设计的轮胎在保证承载性能的前提下,具有重量轻、滚阻低、驾驶体验舒适、搬运方便、拆装容易等特点。经验证,使用本方案设计的轮胎产品的重量较常规产品重量降低7%,滚阻降低10%,且该数据均有相关检测报告。附图说明图1现有技术中轮胎侧轮廓结构示意图;图2是本发明实施例1所述的轮胎异形轮廓结构示意图。具体实施方式为了能够更加清楚地理解本发明的上述目的、特征和优点,下面结合附图及实施例对本发明做进一步说明。实施例1,本实施例提出一种tbr轮胎异形轮廓结构,包括胎冠部1、胎侧部2、胎圈部3及胎踵部4,轮胎的轮廓设计整体异于现有常规设计,体现在轮胎胎侧部2的设计弧段数和方向上,具体的,参考图2:所述胎侧部2包括位于轮胎水平轴上方的胎肩段21和上胎侧圆弧,以及位于轮胎水平轴m下方的下胎侧圆弧;所述胎肩段21位于胎冠部1的下部两侧,且与上胎侧圆弧相切;所述上胎侧圆弧包括上圆弧和上内圆弧(其半径分别为r上和r上内),且所述上圆弧和上内圆弧为圆心位于轮胎水平轴上的同心圆弧,且上内圆弧半径r上内与上圆弧半径r上的差值为0.6mm-2mm,该值的选取根据轮胎承载及路况的差异可在选值范围内变动,较好路况、长里程行驶选值偏小,较差轮廓、承载较大则选值偏大,本实施例优选1.5mm,上圆弧和上内圆弧之间由防擦部22过渡连接;所述下胎侧圆弧包括第一下圆弧(其半径为r下)和与第一下圆弧连接的反弧段(其半径为r反弧),所述第一下圆弧的圆心位于轮胎水平轴上,且与所述上圆弧相连接,所述反弧段下方为连接反弧段和胎踵部的连接弧,反弧段的设计完全区别与常规产品要求的均匀过渡设计,对于优化胎侧部位材料效果显著且有利于吸收来自路面的冲击。另外,为保证异形轮廓轮胎对圈部支撑性能,增加胎圈部位的厚度,以提高其支撑效果,所述连接弧的半径r连接为200mm-240mm。该数值的选取过大则造成圈部形状过立,对轮胎重量造成影响;过小则造成圈部过度不均,对轮胎胎圈的支撑作用不足,本实施中优选220mm,所述连接弧的半径明显不同于常规设计的30mm-100mm半径的圆弧设计,连接弧的使用不仅使反弧段与胎踵部得到有效连接,而且增加了胎圈部材料厚度,使圈部支撑性能得到加强,对于增加轮胎的使用寿命、减少因圈部变形导致的圈部损坏有益,同时也有利于轮胎的搬运及装拆。为使轮胎上胎侧过度均匀,且考虑轮胎内轮廓的变化,所述上圆弧的半径r上为70mm至90mm,优选86.5mm,较同型号常规轮胎轮廓设计半径小40mm—50mm;上内圆弧半径r上内比上圆弧的半径r上小1.5mm,即r上内优选85mm,其差值i为防擦部厚度,防擦部22上设置有多个不同形状凹槽,包括多段防擦弧,且防擦部22下端点与轮胎水平轴m的垂直距离h1为8mm-10mm,优选8mm,配合凹槽设计在提升轮胎防剐蹭的同时改善轮胎使用过程中对来自地面冲击的缓冲,增加车辆的驾驶舒适性。本实施例中,所述第一下圆弧的圆心位于轮胎水平轴m上,其上端点为轮胎水平轴端点,其下端点位于轮胎水平轴下方h2为10mm-15mm位置处,优选12mm处,为保证轮胎下胎侧弧与上胎侧弧的圆滑过渡,第一下圆弧的半径r下比上圆弧半径r上小10mm-15mm,优选75mm;且所述反弧段的半径r反弧为上圆弧半径r上的1倍-1.2倍,反弧段的半径r反弧的选取需要严格按照范围取值,取值过小反弧明显,将降低胎侧的支撑性能同时影响胎体在轮胎中的受力,取值过大,反弧作用降低,增加轮胎部位的材料,不利于滚阻、重量的优化,本实施例优选其半径为90mm,以保证轮胎在使用过程中的舒适性及生产过程的可操控性,同时考虑轮胎整体质量的控制。在上胎侧圆弧和胎肩段之间设计有分型面n,考虑胶料胶边的发生并考虑后期维修的便利,所述胎肩段21与分型面n相交的点在分型面水平线上向外偏移l距离,所述l的值小于2mm,所达到的点设为p点;所述分型面上下两侧分别为分型面上弧和分型面下弧,其半径分别为r分型上、r分型下,根据胎冠与侧板的配合,考虑胶料胶边的发生并考虑后期维修的便利,所述分型面上弧过p点与胎肩段相切,分型面下弧过p点与上内圆弧相切,l数值的选择不应超过2mm,优选1.5mm,过大影响模具组装及组装过程中对侧板、花纹块的损伤,过小则影响分型面处轮胎的胶边,易产生胶边杂质。胎踵之后的部位等轮廓尺寸与正常轮廓相同,保证了轮胎与轮辋的结合,同时避免了因特殊轮廓需要配备专用轮辋的问题的发生。本实施例提出的轮胎轮廓胎侧形状完全不同于现有市场常见的轮廓设计,胎侧至胎圈呈现不规则形状,异于常见轮胎的均匀过度。下面结合图2说明本实施例所述异形轮胎轮廓大致设计步骤:首先根据tra标准确定断面宽b值,然后确定h1、h2的值以及分型面高度h分型、行驶面宽度b、花纹弧高h;本领域技术人员结合图2以及轮胎相关设计标准与要求,可得到着合宽度c值、r胎肩,结合断面宽b、h2的数值确定r上,然后根据防擦部厚度i,进而确定r上内;考虑胶料胶边的发生并考虑后期维修的便利,确定分型面上弧半径为r分型上和分型面下弧半径为r分型下,根据轮胎使用环境并考虑轮胎整体重量,依次设定防擦部的间距为a1、a2、a3、a4,h1为断面水平轴位置的防擦部距离;根据轮胎所用轮辋形状,考虑轮胎使用过程中的轮辋与胎圈部位的气密性并结合现有子口设计,确定胎趾与着合水平线的夹角f1、f2,相应距离为c1、c2、c3,e1为过d点横向向外偏移的距离,e2为过d点竖向向上偏移的距离,由e1和e2的交点确定e点的位置;连接弧的半径r连接的数值确定,其位置为过e、d点的圆弧;为保证断面宽度符合相关标准要求且保证轮胎在使用过程中胎侧的保护作用,确定下胎侧圆弧的范围为h2,下胎侧圆弧(确定其半径为r下)与距离轮胎水平轴距离为h2的水平直线的交点定为m;然后确定反弧段半径r反弧,其过m、e两点;所有的点及数值及位置确定,进而可根据起点、端点、半径的方法绘制该异形轮廓。实施例2,在实施例1的基础上,本实施例提出一种具有实施例1所述异形轮廓结构的轮胎,由于其侧轮廓的特殊设计,其上胎侧厚度由于采用不同弧段组合及防擦部凹槽设计较同型号常规轮胎胎侧厚度薄0.5mm-1.0mm,下胎侧采用第一下圆弧和反弧设计,其厚度较同型号常规轮胎胎侧厚度薄0.7mm-1.0mm,胎圈部分采用大半径圆弧(连接弧)设计,且为了提升胎圈的刚性及支撑效果,胎圈厚度较正常厚度厚2mm。表1:本实施例异形轮廓轮胎与现有同型号常规轮胎在胎面花纹一致的情况下,其监测数据(滚阻与重量)对比表:异型轮廓产品现有产品(正常轮胎)滚阻(n)4.615.1重量(kg)46.649.9本方案所述的轮胎重量轻、滚阻低、装拆、搬运方便,由于胎侧部位的轮廓变化,利于车辆运转过程中吸收来自路面的冲击,提升驾驶舒适性;经测算,从表1可以看出,本实施例产品的轮胎重量较现有常规产品重量降低7%、滚阻降低10%,本论述数据均有相关检测报告,轮胎滚阻及重量得到明显改善。以上所述,仅是本发明的较佳实施例而已,并非是对本发明作其它形式的限制,任何熟悉本专业的技术人员可能利用上述揭示的技术内容加以变更或改型为等同变化的等效实施例应用于其它领域,但是凡是未脱离本发明技术方案内容,依据本发明的技术实质对以上实施例所作的任何简单修改、等同变化与改型,仍属于本发明技术方案的保护范围。当前第1页12