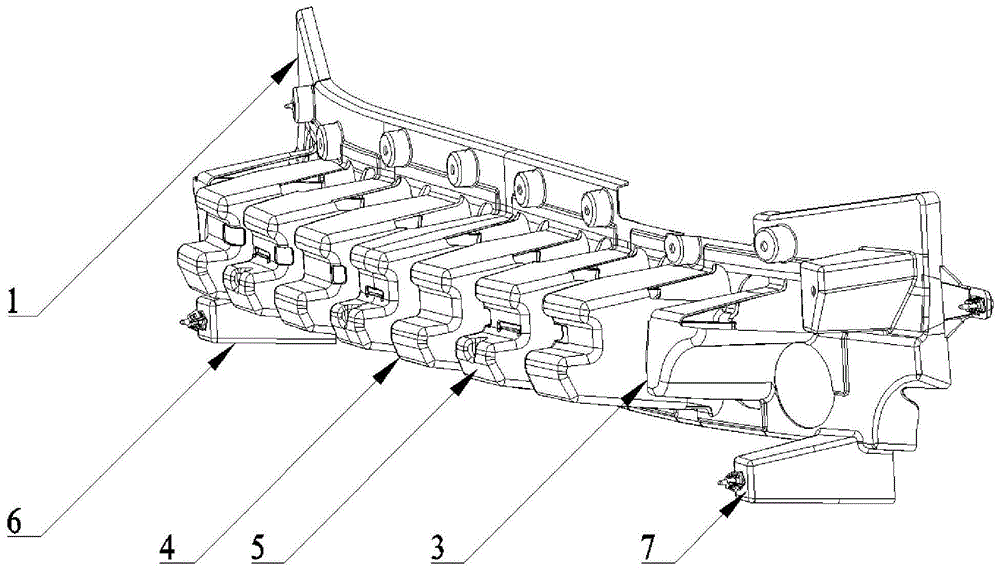
本发明涉及汽车安全附件设备
技术领域:
,具体涉及一种缓冲汽车撞击的吸能件及其制造方法。
背景技术:
:汽车已经成为人类出行的代步工具,大大提升了人类的工作和生活效率,与此同时汽车碰撞安全也越来越收到重视,汽车车身的吸能能力对汽车内乘客的保护作用也越来越重要。在目前的汽车设计中,通常是采用安装在汽车前部和尾部的保险系统来保证车厢结构框架低速碰撞下不受破坏,从而保证车内人员以及汽车主体结构本身的安全,为了尽可能吸收撞击的动力,现在的保险杠设计中,往往会加入一个变形元件,即所谓的碰撞吸能件,但现有使用的吸能件结构简单,吸能效果不能明显,发生碰撞后,车体受冲击较大。而目前的变形元件大多采用吸能抗冲材料制得,但是现有吸能抗冲材料比较单一而且针对汽车碰撞安全的较少,现有吸能材料大多使用发泡金属,因其多孔泡沫金属具有良好的可压缩性、拥有一个较为稳定的压缩平台应力、可以吸收与冲击方向无关的冲击能量。在压缩承载条件下所表现出来的独特的力学性能表明泡沫金属是一种极具潜力的冲击缓冲材料,具有很高的冲击吸能本领,在航空航天、汽车船舶、汽车安全附件和包装运输等防护减振领域得到了广泛的应用,特别在汽车工业的防撞性设计以及在特种车辆上作为爆炸缓冲及防护材料具有重要的应用价值。但在实际应用中泡沫材料强度低、表面粗糙,不能单独作为结构材料使用。将泡沫材料和其他板材结合起来组成复合材料,即以泡沫材料作为芯体组成夹层板,将发挥泡沫材料和板材优点,为泡沫材料的发展提供了广阔的应用前景。技术实现要素:为了克服现有技术中存在的缺点和不足,本发明的目的在于提供一种缓冲汽车撞击的吸能件,该吸能件通过采用特制的发泡金属材料复合设计制得的原料压铸而成,使制得的吸能件具有很好的吸收撞击能量,降低车体的损伤,进一步提升对车内乘客的保护作用。本发明的另一目的在于提供一种缓冲汽车撞击的吸能件的制造方法,通过该方法制得的吸能件具有良好的抗冲击、吸能、阻尼减振性能,能进一步提升对车内乘客的保护作用,另外该制造工艺简单、一体成型,大大提升了生产效率。本发明的目的通过下述技术方案实现:一种缓冲汽车撞击的吸能件,包括格兰板、第一中空吸能块、第二中空吸能块、若干第三中空吸能块、若干第四中空吸能块、第五中空吸能块和第六中空吸能块,所述第一中空吸能块设置于所述格兰板的左端,所述第二中空吸能块设置于所述格兰板的右端,所述第三中空吸能块设置于所述格兰板并位于所述第一中空吸能块的右侧,所述第四中空吸能块设置于所述格兰板并位于所述第三中空吸能块的右侧,所述第三中空吸能块和第四中空吸能块为间隔设置,所述第五中空吸能块设置于所述格兰板并位于所述第一中空吸能块的左下方,所述第六中空吸能块设置于所述格兰板并位于所述第二中空吸能块的右下方;所述第三中空吸能块的顶端设置为呈阶梯状的第一凸台和第二凸台,所述第一凸台和第二凸台中间凹设为第一凹槽;所述第四中空吸能块的顶端设置为呈阶梯状的第三凸台和第四凸台,所述第三凸台和第四凸台中间凹设为第二凹槽,所述第四凸台的上端面凹设有半球体。更为优选的,所述格兰板、第一中空吸能块、第二中空吸能块、第三中空吸能块、第四中空吸能块、第五中空吸能块和第六中空吸能块均由吸能缓冲材料制得,所述缓冲材料由外到内包括金属面板、硅橡胶层和泡沫金属层。本发明中吸能件通过在格兰板上设置的第一中空吸能块、第二中空吸能块、若干第三中空吸能块、若干第四中空吸能块、第五中空吸能块和第六中空吸能块来缓冲大部分的撞击能力,尤其是第三中空吸能块和第四中空吸能块的顶部凸设出的第一凸台、第二凸台、第三凸台和第四凸台以及第一凹槽和第二凹槽来降低吸能件的刚度,在受撞击时第一凸台和第四凸台起到第一级吸能缓冲作用,当第一凸台和第四凸台被压垮后第二凸台和第三凸台起到第二级吸能缓冲作用,阻碍冲击向车体的传递,保护车体。另外第一凹槽和第二凹槽处的第二通孔可以降低吸能块的刚度,在一定的撞击力下吸能块底端直接断裂开减少撞击力对车身的直接冲击。优选的,所述泡沫金属层由发泡金属制得,所述发泡金属包括如下重量份的原料:本发明中所述泡沫金属层所用原料中的石墨烯是由一层碳原子组成的平面碳纳米材料,石墨烯中的碳原子之间由σ键连接,赋予了石墨烯极其优异的力学性质和结构刚性,在本发明中石墨烯改善了制得泡沫金属复合界面结合性能,在泡沫铝内部由于泡沫空隙尺寸影响内部强化效果,本发明通过发泡剂与石墨烯和纳米粒子研磨分散均匀,然后混于铝粉,通过高温烧结,使发泡剂发泡,并使石墨烯分散于泡沫的界面,冷却后得到的发泡金属进一步提升了稳定性、均匀性,同时使发泡金属具有低密度高强度;膨胀玻化微珠经过气炉高温膨胀等特种技术处理和生产工艺加工形成内部多孔,弥补了用聚苯颗粒和普通膨胀珍珠岩作轻质吸能材料的添加剂的诸多缺陷和不足,可辅助铝粉与发泡剂相互共熔,使材料内部呈现密集的闭孔气孔,可获得多孔性、轻质的泡沫铝材料结构。优选的,所述纳米粒子是由纳米水玻璃、纳米碳酸钙、纳米二氧化硅、纳米二氧化钛、纳米沸石中的至少两种组成的混合物。所述发泡剂是由氢化钛和氢化钙按照重量比为0.8-1.2:1.0组成的混合物。更为优选的,所述氢化钛经过化学镀铁、氧化铝双层包覆处理。本发明中所述纳米粒子纳米沸石与分散剂混合均匀,将得到的混合物与硼酸盐进行混合交联反应得到剪切增稠凝胶,剪切增稠凝胶可以辅助铝液和发泡剂,使制备得发泡金属具有超强的减震吸能作用;而氢化钛在制造泡沫金属时可以作为高纯氢的供源,经特殊处理后的减少了氢化钛粉末的表面张力,使团聚化氢向明减弱,提高了氢化钛开始释放氢的温度,释放氢的开始温度达到600℃以上,避免了氢化钛在分散于铝液时发生分解的问题,并使石墨烯分散于泡沫的界面,冷却得到复含石墨烯的泡沫金属复合金属材料,进一步有助于获得具有低密度高强度的特性的泡沫金属材料。优选的,所述分散剂是由聚乙烯蜡、邻苯二甲酸酯、聚苯乙烯、硬脂酸钙按照重量比为1.0:0.8-1.2:0.8:0.8-1.0组成的混合物。所述增粘剂是由松香树脂、萜烯树脂、石油树脂按照重量比为1.0:0.8-1.2:0.8-1.0组成的混合物。本发明中所采用的聚乙烯蜡具有增强纳米粒子的扩散的作用,同时在压铸件时提高挤压成型速率,增大模具流量,脱模便利,提高产品脱膜后的表面光亮度及光滑度;而邻苯二甲酸酯可以使聚苯乙烯由硬塑胶变为有弹性的塑胶,起到增塑剂的作用;硬脂酸钙可以辅助纳米粒子扩散融入铝液中,同时还可提高凝胶化速度和压铸过程的脱模剂效果;而松香树脂具有高软化点、高粘性,和更好的抗氧化性,融铝时可以防止铝的氧化,并且在液体状态下或在溶液里具有完全抗结晶作用;石油树脂可以配合松香树脂提升制得发泡金属的热稳定性。优选的,所述泡沫金属由如下步骤制得:1)将铝粉熔化并在温度为650-700℃保温,再将增粘剂加入铝熔体中搅拌均匀,反应5-15min使得熔体黏度稳定,得到混合物a,备用;2)将石墨烯、膨胀玻化微珠和纳米粒子混合加入高速搅拌器中,以1000-2000r/min速率搅拌分散均匀得到混合物b,备用;3)将分散剂和步骤2)中得到的混合物b和硼酸盐加入步骤1)中得到的混合物a搅拌分散均匀,得到混合物c,并在500-550℃条件下恒温保温,备用;4)将步骤3)中的混合物c降温至温度为450-500℃,加入发泡剂并搅拌10-20min,将搅拌后的熔体在300-400℃进行恒温发泡,发泡结束后水冷却凝固即得到泡沫金属。本发明中所述泡沫金属采用上述方法制得,由此方法制得的发泡金属解决tih2作为发泡剂存在价格昂贵、操作条件苛刻的问题,另外本发明的发泡剂和纳米粒子可通过改变原料配比来调节泡沫金属的孔隙率和孔径分布。发泡剂中氢化钛和氢化钙的混合物,在高温下与铝粉融液相互共熔,使材料内部呈现密集的闭孔气孔,可获得多孔性、轻质的泡沫铝材料结构,利用制得的泡沫金属用压铸吸能件时,可以使吸能件具有良好的抗冲击、吸能、阻尼减振性能。一种缓冲汽车撞击的吸能件通过如下步骤制得:s1、根据设计尺寸要求准备金属面板和泡沫金属层;s2、将金属面板和泡沫金属层的粘结面分别采用硅橡胶用热硫化胶粘剂进行涂覆处理;s3、将压铸模具预热至150-190℃能够使硅橡胶进行硫化;s4、将步骤s2中处理后的金属面板和泡沫金属层以及硅橡胶层按照设计结构依次放置在模具中,合模施加压力为200-300mpa,并保压时间为1-5min,使硅橡胶硫化成型,退模后取出的产品即为该吸能件。本发明中所述吸能件采用上述方法制得,利用此方法制得的吸能件具有良好的抗冲击、吸能、阻尼减振性能,能进一步提升对车内乘客的保护作用,另外该制造工艺简单、一体成型,大大提升了生产效率,另外在合模时要严格控制施加的压力200-300mpa,若压力过低则会达不到所需压合效果,若压力过高则会导致发泡颗粒被压爆,反而达不到更优异的效果。本发明的有益效果在于:本发明吸能件通过在格兰板上的第一中空吸能块、第二中空吸能块、第三中空吸能块、第四中空吸能块、第五中空吸能块和第六中空吸能块来缓冲大部分的撞击能力,尤其是第三中空吸能块和第四中空吸能块的顶部凸设出的第一凸台、第二凸台、第三凸台和第四凸台以及第一凹槽和第二凹槽来降低吸能件的刚度,在受撞击时第一凸台和第四凸台起到第一级吸能缓冲作用,第二凸台和第三凸台起到第二级吸能缓冲作用,阻碍冲击向车体的传递,保护行人或车内驾驶人员,另外本发明所用发泡金属多孔性、轻质,利用制得的泡沫金属用压铸吸能件时,可以使吸能件具有更好的抗冲击、吸能、阻尼减振性能。附图说明图1是本发明的立体图;图2是本发明的俯视图;图3是本发明第三中空吸能块的局部剖视图;图4是本发明的第四中空吸能块的局部剖视图。附图标记为:1-格兰板、2-第一中空吸能块、3-第二中空吸能块、4-第三中空吸能块、41-第一凸台、42-第二凸台、43-第一凹槽、431-第二通孔、5-第四中空吸能块、51-第三凸台、52-第四凸台、53-第二凹槽、521-第三凹槽、6-第五中空吸能块、7-第六中空吸能块。具体实施方式为了便于本领域技术人员的理解,下面结合实施例及附图1-4对本发明作进一步的说明,实施方式提及的内容并非对本发明的限定。实施例1一种缓冲汽车撞击的吸能件,包括格兰板1、第一中空吸能块2、第二中空吸能块3、若干第三中空吸能块4、若干第四中空吸能块5、第五中空吸能块6和第六中空吸能块7,所述第一中空吸能块2设置于所述格兰板1的左端,所述第二中空吸能块3设置于所述格兰板1的右端,所述第三中空吸能块4设置于所述格兰板1并位于所述第一中空吸能块2的右侧,所述第四中空吸能块5设置于所述格兰板1并位于所述第三中空吸能块4的右侧,所述第三中空吸能块4和第四中空吸能块5为间隔设置,所述第五中空吸能块6设置于所述格兰板1并位于所述第一中空吸能块2的左下方,所述第六中空吸能块7设置于所述格兰板上并位于所述第二中空吸能块3的右下方;所述第三中空吸能块4的顶端设置为呈阶梯状的第一凸台41和第二凸台42,所述第一凸台41和第二凸台42之间凹设有第一凹槽43;所述第四中空吸能块5的顶端设置为呈阶梯状的第三凸台51和第四凸台52,所述第三凸台51和第四凸台52之间凹设有第二凹槽53,所述第四凸台52的上端面凹设有第三凹槽521。进一步的,所述第三凹槽521为内腔呈半球体状的凹槽。所述格兰板1、第一中空吸能块2、第二中空吸能块3、若干第三中空吸能块4、若干第四中空吸能块5、第五中空吸能块6和第六中空吸能块7均由吸能缓冲材料制得,所述缓冲材料由外到内包括金属面板、硅橡胶层和泡沫金属层。所述泡沫金属层由发泡金属制得,所述发泡金属包括如下重量份的原料:所述纳米粒子是由纳米水玻璃和纳米碳酸钙按照重量比为0.8:1.0组成的混合物。所述发泡剂是由氢化钛和氢化钙按照重量比为0.8:1.0组成的混合物。更为优选的,所述氢化钛经过化学镀铁、氧化铝双层包覆处理。所述分散剂是由聚乙烯蜡、邻苯二甲酸酯、聚苯乙烯、硬脂酸钙按照重量比为1.0:0.8:0.8:0.8组成的混合物。所述增粘剂是由松香树脂、萜烯树脂、石油树脂按照重量比为1.0:0.8:0.8组成的混合物。所述泡沫金属由如下步骤制得:1)将铝粉熔化并在温度为650℃保温,再将增粘剂加入铝熔体中搅拌均匀,反应5min使得熔体黏度稳定,得到混合物a,备用;2)将石墨烯、膨胀玻化微珠和纳米粒子混合加入高速搅拌器中,以1000-2000r/min速率搅拌分散均匀得到混合物b,备用;3)将分散剂和步骤2)中得到的混合物b和硼酸盐加入步骤1)中得到的混合物a搅拌分散均匀,得到混合物c,并在500℃条件下恒温保温,备用;4)将步骤3)中的混合物c降温至温度为450℃,加入发泡剂并搅拌10min,将搅拌后的熔体在300℃进行恒温发泡,发泡结束后水冷却凝固即得到泡沫金属。一种缓冲汽车撞击的吸能件通过如下步骤制得:s1、根据设计尺寸要求准备金属面板和泡沫金属层;s2、将金属面板和泡沫金属层的粘结面分别采用硅橡胶用热硫化胶粘剂进行涂覆处理;s3、将压铸模具预热至150℃使硅橡胶进行硫化;s4、将步骤s2中处理后的金属面板和泡沫金属层以及硅橡胶层按照设计结构依次放置在模具中,合模施加压力为200mpa,并保压时间为1min,使硅橡胶硫化成型,退模后取出的产品即为该吸能件。实施例2一种缓冲汽车撞击的吸能件,包括格兰板1、第一中空吸能块2、第二中空吸能块3、若干第三中空吸能块4、若干第四中空吸能块5、第五中空吸能块6和第六中空吸能块7,所述第一中空吸能块2设置于所述格兰板1的左端,所述第二中空吸能块3设置于所述格兰板1的右端,所述第三中空吸能块4设置于所述格兰板1并位于所述第一中空吸能块2的右侧,所述第四中空吸能块5设置于所述格兰板1并位于所述第三中空吸能块4的右侧,所述第三中空吸能块4和第四中空吸能块5为间隔设置,所述第五中空吸能块6设置于所述格兰板1并位于所述第一中空吸能块2的左下方,所述第六中空吸能块7设置于所述格兰板上并位于所述第二中空吸能块3的右下方;所述第三中空吸能块4的顶端设置为呈阶梯状的第一凸台41和第二凸台42,所述第一凸台41和第二凸台42之间凹设有第一凹槽43;所述第四中空吸能块5的顶端设置为呈阶梯状的第三凸台51和第四凸台52,所述第三凸台51和第四凸台52之间凹设有第二凹槽53,所述第四凸台52的上端面凹设有第三凹槽521。进一步的,所述第三凹槽521为内腔呈半球体状的凹槽。所述格兰板1、第一中空吸能块2、第二中空吸能块3、若干第三中空吸能块4、若干第四中空吸能块5、第五中空吸能块6和第六中空吸能块7均由吸能缓冲材料制得,所述缓冲材料由外到内包括金属面板、硅橡胶层和泡沫金属层。所述泡沫金属层由发泡金属制得,所述发泡金属包括如下重量份的原料:所述纳米粒子是由纳米二氧化硅和纳米碳酸钙按照重量比为0.8:1.0组成的混合物。所述发泡剂是由氢化钛和氢化钙按照重量比为0.9:1.0组成的混合物。更为优选的,所述氢化钛经过化学镀铁、氧化铝双层包覆处理。所述分散剂是由聚乙烯蜡、邻苯二甲酸酯、聚苯乙烯、硬脂酸钙按照重量比为1.0:0.9:0.8:0.85组成的混合物。所述增粘剂是由松香树脂、萜烯树脂、石油树脂按照重量比为1.0:0.9:0.85组成的混合物。所述泡沫金属由如下步骤制得:1)将铝粉熔化并在温度为663℃保温,再将增粘剂加入铝熔体中搅拌均匀,反应7min使得熔体黏度稳定,得到混合物a,备用;2)将石墨烯、膨胀玻化微珠和纳米粒子混合加入高速搅拌器中,以1250r/min速率搅拌分散均匀得到混合物b,备用;3)将分散剂和步骤2)中得到的混合物b和硼酸盐加入步骤1)中得到的混合物a搅拌分散均匀,得到混合物c,并在515℃条件下恒温保温,备用;4)将步骤3)中的混合物c降温至温度为465℃,加入发泡剂并搅拌13min,将搅拌后的熔体在325℃进行恒温发泡,发泡结束后水冷却凝固即得到泡沫金属。一种缓冲汽车撞击的吸能件通过如下步骤制得:s1、根据设计尺寸要求准备金属面板和泡沫金属层;s2、将金属面板和泡沫金属层的粘结面分别采用硅橡胶用热硫化胶粘剂进行涂覆处理;s3、将压铸模具预热至160℃能够使硅橡胶进行硫化;s4、将步骤s2中处理后的金属面板和泡沫金属层以及硅橡胶层按照设计结构依次放置在模具中,合模施加压力为225mpa,并保压时间为2min,使硅橡胶硫化成型,退模后取出的产品即为该吸能件。实施例3一种缓冲汽车撞击的吸能件,包括格兰板1、第一中空吸能块2、第二中空吸能块3、若干第三中空吸能块4、若干第四中空吸能块5、第五中空吸能块6和第六中空吸能块7,所述第一中空吸能块2设置于所述格兰板1的左端,所述第二中空吸能块3设置于所述格兰板1的右端,所述第三中空吸能块4设置于所述格兰板1并位于所述第一中空吸能块2的右侧,所述第四中空吸能块5设置于所述格兰板1并位于所述第三中空吸能块4的右侧,所述第三中空吸能块4和第四中空吸能块5为间隔设置,所述第五中空吸能块6设置于所述格兰板1并位于所述第一中空吸能块2的左下方,所述第六中空吸能块7设置于所述格兰板上并位于所述第二中空吸能块3的右下方;所述第三中空吸能块4的顶端设置为呈阶梯状的第一凸台41和第二凸台42,所述第一凸台41和第二凸台42之间凹设有第一凹槽43;所述第四中空吸能块5的顶端设置为呈阶梯状的第三凸台51和第四凸台52,所述第三凸台51和第四凸台52之间凹设有第二凹槽53,所述第四凸台52的上端面凹设有第三凹槽521。进一步的,所述第三凹槽521为内腔呈半球体状的凹槽。所述格兰板1、第一中空吸能块2、第二中空吸能块3、若干第三中空吸能块4、若干第四中空吸能块5、第五中空吸能块6和第六中空吸能块7均由吸能缓冲材料制得,所述缓冲材料由外到内包括金属面板、硅橡胶层和泡沫金属层。所述泡沫金属层由发泡金属制得,所述发泡金属包括如下重量份的原料:所述纳米粒子是由纳米二氧化硅和纳米二氧化钛按照重量比为0.8:1.0组成的混合物。所述发泡剂是由氢化钛和氢化钙按照重量比为1.0:1.0组成的混合物。更为优选的,所述氢化钛经过化学镀铁、氧化铝双层包覆处理。所述分散剂是由聚乙烯蜡、邻苯二甲酸酯、聚苯乙烯、硬脂酸钙按照重量比为1.0:1.0:0.8:0.9组成的混合物。所述增粘剂是由松香树脂、萜烯树脂、石油树脂按照重量比为1.0:1.0:0.90组成的混合物。所述泡沫金属由如下步骤制得:1)将铝粉熔化并在温度为675℃保温,再将增粘剂加入铝熔体中搅拌均匀,反应10min使得熔体黏度稳定,得到混合物a,备用;2)将石墨烯、膨胀玻化微珠和纳米粒子混合加入高速搅拌器中,以1500r/min速率搅拌分散均匀得到混合物b,备用;3)将分散剂和步骤2)中得到的混合物b和硼酸盐加入步骤1)中得到的混合物a搅拌分散均匀,得到混合物c,并在525℃条件下恒温保温,备用;4)将步骤3)中的混合物c降温至温度为475℃,加入发泡剂并搅拌15min,将搅拌后的熔体在350℃进行恒温发泡,发泡结束后水冷却凝固即得到泡沫金属。一种缓冲汽车撞击的吸能件通过如下步骤制得:s1、根据设计尺寸要求准备金属面板和泡沫金属层;s2、将金属面板和泡沫金属层的粘结面分别采用硅橡胶用热硫化胶粘剂进行涂覆处理;s3、将压铸模具预热至170℃能够使硅橡胶进行硫化;s4、将步骤s2中处理后的金属面板和泡沫金属层以及硅橡胶层按照设计结构依次放置在模具中,合模施加压力为250mpa,并保压时间为3min,使硅橡胶硫化成型,退模后取出的产品即为该吸能件。实施例4一种缓冲汽车撞击的吸能件,包括格兰板1、第一中空吸能块2、第二中空吸能块3、若干第三中空吸能块4、若干第四中空吸能块5、第五中空吸能块6和第六中空吸能块7,所述第一中空吸能块2设置于所述格兰板1的左端,所述第二中空吸能块3设置于所述格兰板1的右端,所述第三中空吸能块4设置于所述格兰板1并位于所述第一中空吸能块2的右侧,所述第四中空吸能块5设置于所述格兰板1并位于所述第三中空吸能块4的右侧,所述第三中空吸能块4和第四中空吸能块5为间隔设置,所述第五中空吸能块6设置于所述格兰板1并位于所述第一中空吸能块2的左下方,所述第六中空吸能块7设置于所述格兰板上并位于所述第二中空吸能块3的右下方;所述第三中空吸能块4的顶端设置为呈阶梯状的第一凸台41和第二凸台42,所述第一凸台41和第二凸台42之间凹设有第一凹槽43;所述第四中空吸能块5的顶端设置为呈阶梯状的第三凸台51和第四凸台52,所述第三凸台51和第四凸台52之间凹设有第二凹槽53,所述第四凸台52的上端面凹设有第三凹槽521。进一步的,所述第三凹槽521为内腔呈半球体状的凹槽。所述格兰板1、第一中空吸能块2、第二中空吸能块3、若干第三中空吸能块4、若干第四中空吸能块5、第五中空吸能块6和第六中空吸能块7均由吸能缓冲材料制得,所述缓冲材料由外到内包括金属面板、硅橡胶层和泡沫金属层。所述泡沫金属层由发泡金属制得,所述发泡金属包括如下重量份的原料:所述纳米粒子是由纳米二氧化钛和纳米沸石按照重量比为0.8:1.0组成的混合物。所述发泡剂是由氢化钛和氢化钙按照重量比为1.1:1.0组成的混合物。更为优选的,所述氢化钛经过化学镀铁、氧化铝双层包覆处理。所述分散剂是由聚乙烯蜡、邻苯二甲酸酯、聚苯乙烯、硬脂酸钙按照重量比为1.0:1.1:0.8:0.95组成的混合物。所述增粘剂是由松香树脂、萜烯树脂、石油树脂按照重量比为1.0:1.1:0.95组成的混合物。所述泡沫金属由如下步骤制得:1)将铝粉熔化并在温度为690℃保温,再将增粘剂加入铝熔体中搅拌均匀,反应13min使得熔体黏度稳定,得到混合物a,备用;2)将石墨烯、膨胀玻化微珠和纳米粒子混合加入高速搅拌器中,以1750r/min速率搅拌分散均匀得到混合物b,备用;3)将分散剂和步骤2)中得到的混合物b和硼酸盐加入步骤1)中得到的混合物a搅拌分散均匀,得到混合物c,并在540℃条件下恒温保温,备用;4)将步骤3)中的混合物c降温至温度为490℃,加入发泡剂并搅拌18min,将搅拌后的熔体在375℃进行恒温发泡,发泡结束后水冷却凝固即得到泡沫金属。一种缓冲汽车撞击的吸能件通过如下步骤制得:s1、根据设计尺寸要求准备金属面板和泡沫金属层;s2、将金属面板和泡沫金属层的粘结面分别采用硅橡胶用热硫化胶粘剂进行涂覆处理;s3、将压铸模具预热至180℃能够使硅橡胶进行硫化;s4、将步骤s2中处理后的金属面板和泡沫金属层以及硅橡胶层按照设计结构依次放置在模具中,合模施加压力为275mpa,并保压时间为4min,使硅橡胶硫化成型,退模后取出的产品即为该吸能件。实施例5一种缓冲汽车撞击的吸能件,包括格兰板1、第一中空吸能块2、第二中空吸能块3、若干第三中空吸能块4、若干第四中空吸能块5、第五中空吸能块6和第六中空吸能块7,所述第一中空吸能块2设置于所述格兰板1的左端,所述第二中空吸能块3设置于所述格兰板1的右端,所述第三中空吸能块4设置于所述格兰板1并位于所述第一中空吸能块2的右侧,所述第四中空吸能块5设置于所述格兰板1并位于所述第三中空吸能块4的右侧,所述第三中空吸能块4和第四中空吸能块5为间隔设置,所述第五中空吸能块6设置于所述格兰板1并位于所述第一中空吸能块2的左下方,所述第六中空吸能块7设置于所述格兰板上并位于所述第二中空吸能块3的右下方;所述第三中空吸能块4的顶端设置为呈阶梯状的第一凸台41和第二凸台42,所述第一凸台41和第二凸台42之间凹设有第一凹槽43;所述第四中空吸能块5的顶端设置为呈阶梯状的第三凸台51和第四凸台52,所述第三凸台51和第四凸台52之间凹设有第二凹槽53,所述第四凸台52的上端面凹设有第三凹槽521。进一步的,所述第三凹槽521为内腔呈半球体状的凹槽。所述格兰板1、第一中空吸能块2、第二中空吸能块3、若干第三中空吸能块4、若干第四中空吸能块5、第五中空吸能块6和第六中空吸能块7均由吸能缓冲材料制得,所述缓冲材料由外到内包括金属面板、硅橡胶层和泡沫金属层。所述泡沫金属层由发泡金属制得,所述发泡金属包括如下重量份的原料:所述纳米粒子是由纳米水玻璃和纳米沸石按照重量比为0.8:1.0组成的混合物。所述发泡剂是由氢化钛和氢化钙按照重量比为1.2:1.0组成的混合物。更为优选的,所述氢化钛经过化学镀铁、氧化铝双层包覆处理。所述分散剂是由聚乙烯蜡、邻苯二甲酸酯、聚苯乙烯、硬脂酸钙按照重量比为1.0:01.2:0.8:1.0组成的混合物。所述增粘剂是由松香树脂、萜烯树脂、石油树脂按照重量比为1.0:1.2:1.0组成的混合物。所述泡沫金属由如下步骤制得:1)将铝粉熔化并在温度为700℃保温,再将增粘剂加入铝熔体中搅拌均匀,反应15min使得熔体黏度稳定,得到混合物a,备用;2)将石墨烯、膨胀玻化微珠和纳米粒子混合加入高速搅拌器中,以2000r/min速率搅拌分散均匀得到混合物b,备用;3)将分散剂和步骤2)中得到的混合物b和硼酸盐加入步骤1)中得到的混合物a搅拌分散均匀,得到混合物c,并在550℃条件下恒温保温,备用;4)将步骤3)中的混合物c降温至温度为500℃,加入发泡剂并搅拌20min,将搅拌后的熔体在400℃进行恒温发泡,发泡结束后水冷却凝固即得到泡沫金属。一种缓冲汽车撞击的吸能件通过如下步骤制得:s1、根据设计尺寸要求准备金属面板和泡沫金属层;s2、将金属面板和泡沫金属层的粘结面分别采用硅橡胶用热硫化胶粘剂进行涂覆处理;s3、将压铸模具预热至190℃能够使硅橡胶进行硫化;s4、将步骤s2中处理后的金属面板和泡沫金属层以及硅橡胶层按照设计结构依次放置在模具中,合模施加压力为300mpa,并保压时间为5min,使硅橡胶硫化成型,退模后取出的产品即为该吸能件。对比例1一种缓冲汽车撞击的吸能件,包括格兰板1、第一中空吸能块2、第二中空吸能块3、若干第三中空吸能块4、若干第四中空吸能块5、第五中空吸能块6和第六中空吸能块7,所述第一中空吸能块2设置于所述格兰板1的左端,所述第二中空吸能块3设置于所述格兰板1的右端,所述第三中空吸能块4设置于所述格兰板1并位于所述第一中空吸能块2的右侧,所述第四中空吸能块5设置于所述格兰板1并位于所述第三中空吸能块4的右侧,所述第三中空吸能块4和第四中空吸能块5为间隔设置,所述第五中空吸能块6设置于所述格兰板1并位于所述第一中空吸能块2的左下方,所述第六中空吸能块7设置于所述格兰板1并位于所述第二中空吸能块3的右下方。所述格兰板1、第一中空吸能块2、第二中空吸能块3、若干第三中空吸能块4、若干第四中空吸能块5、第五中空吸能块6和第六中空吸能块7均由吸能缓冲材料制得,所述缓冲材料由外到内包括金属面板、硅橡胶层和泡沫金属层。所述泡沫金属层由发泡金属制得,所述发泡金属包括如下重量份的原料:所述纳米粒子是由纳米水玻璃和纳米碳酸钙按照重量比为0.8:1.0组成的混合物。所述发泡剂是由氢化钛和氢化钙按照重量比为0.8:1.0组成的混合物。更为优选的,所述氢化钛经过化学镀铁、氧化铝双层包覆处理。所述分散剂是由聚乙烯蜡、邻苯二甲酸酯、聚苯乙烯、硬脂酸钙按照重量比为1.0:0.8:0.8:0.8组成的混合物。所述增粘剂是由松香树脂、萜烯树脂、石油树脂按照重量比为1.0:0.8:0.8组成的混合物。所述泡沫金属由如下步骤制得:1)将铝粉熔化并在温度为650℃保温,再将增粘剂加入铝熔体中搅拌均匀,反应5min使得熔体黏度稳定,得到混合物a,备用;2)将石墨烯、膨胀玻化微珠和纳米粒子混合加入高速搅拌器中,以1000-2000r/min速率搅拌分散均匀得到混合物b,备用;3)将分散剂和步骤2)中得到的混合物b和硼酸盐加入步骤1)中得到的混合物a搅拌分散均匀,得到混合物c,并在500℃条件下恒温保温,备用;4)将步骤3)中的混合物c降温至温度为450℃,加入发泡剂并搅拌10min,将搅拌后的熔体在300℃进行恒温发泡,发泡结束后水冷却凝固即得到泡沫金属。一种缓冲汽车撞击的吸能件通过如下步骤制得:s1、根据设计尺寸要求准备金属面板和泡沫金属层;s2、将金属面板和泡沫金属层的粘结面分别采用硅橡胶用热硫化胶粘剂进行涂覆处理;s3、将压铸模具预热至150℃能够使硅橡胶进行硫化;s4、将步骤s2中处理后的金属面板和泡沫金属层以及硅橡胶层按照设计结构依次放置在模具中,合模施加压力为200mpa,并保压时间为1min,使硅橡胶硫化成型,退模后取出的产品即为该吸能件。对比例2一种缓冲汽车撞击的吸能件,包括格兰板1、第一中空吸能块2、第二中空吸能块3、若干第三中空吸能块4、若干第四中空吸能块5、第五中空吸能块6和第六中空吸能块7,所述第一中空吸能块2设置于所述格兰板1的左端,所述第二中空吸能块3设置于所述格兰板1的右端,所述第三中空吸能块4设置于所述格兰板1并位于所述第一中空吸能块2的右侧,所述第四中空吸能块5设置于所述格兰板1并位于所述第三中空吸能块4的右侧,所述第三中空吸能块4和第四中空吸能块5为间隔设置,所述第五中空吸能块6设置于所述格兰板1并位于所述第一中空吸能块2的左下方,所述第六中空吸能块7设置于所述格兰板上并位于所述第二中空吸能块3的右下方;所述第三中空吸能块4的顶端设置为呈阶梯状的第一凸台41和第二凸台42,所述第一凸台41和第二凸台42之间凹设有第一凹槽43;所述第四中空吸能块5的顶端设置为呈阶梯状的第三凸台51和第四凸台52,所述第三凸台51和第四凸台52之间凹设有第二凹槽53,所述第四凸台52的上端面凹设有第三凹槽521。进一步的,所述第三凹槽521为内腔呈半球体状的凹槽。所述格兰板1、第一中空吸能块2、第二中空吸能块3、若干第三中空吸能块4、若干第四中空吸能块5、第五中空吸能块6和第六中空吸能块7均由吸能缓冲材料制得,所述缓冲材料由外到内包括金属面板、硅橡胶层和泡沫金属层。所述泡沫金属层由发泡金属制得,所述发泡金属包括如下重量份的原料:所述纳米粒子是由纳米二氧化硅和纳米二氧化钛按照重量比为0.8:1.0组成的混合物。所述发泡剂为偶氮二甲酰胺。更为优选的,所述氢化钛经过化学镀铁、氧化铝双层包覆处理。所述分散剂是由聚乙烯蜡、邻苯二甲酸酯、聚苯乙烯、硬脂酸钙按照重量比为1.0:1.0:0.8:0.9组成的混合物。所述增粘剂是由松香树脂、萜烯树脂、石油树脂按照重量比为1.0:1.0:0.90组成的混合物。所述泡沫金属由如下步骤制得:1)将铝粉熔化并在温度为675℃保温,再将增粘剂加入铝熔体中搅拌均匀,反应10min使得熔体黏度稳定,得到混合物a,备用;2)将石墨烯、膨胀玻化微珠和纳米粒子混合加入高速搅拌器中,以1500r/min速率搅拌分散均匀得到混合物b,备用;3)将分散剂和步骤2)中得到的混合物b和硼酸盐加入步骤1)中得到的混合物a搅拌分散均匀,得到混合物c,并在525℃条件下恒温保温,备用;4)将步骤3)中的混合物c降温至温度为475℃,加入发泡剂并搅拌15min,将搅拌后的熔体在350℃进行恒温发泡,发泡结束后水冷却凝固即得到泡沫金属。一种缓冲汽车撞击的吸能件通过如下步骤制得:s1、根据设计尺寸要求准备金属面板和泡沫金属层;s2、将金属面板和泡沫金属层的粘结面分别采用硅橡胶用热硫化胶粘剂进行涂覆处理;s3、将压铸模具预热至170℃能够使硅橡胶进行硫化;s4、将步骤s2中处理后的金属面板和泡沫金属层以及硅橡胶层按照设计结构依次放置在模具中,合模施加压力为250mpa,并保压时间为3min,使硅橡胶硫化成型,退模后取出的产品即为该吸能件。对比例3一种缓冲汽车撞击的吸能件,包括格兰板1、第一中空吸能块2、第二中空吸能块3、若干第三中空吸能块4、若干第四中空吸能块5、第五中空吸能块6和第六中空吸能块7,所述第一中空吸能块2设置于所述格兰板1的左端,所述第二中空吸能块3设置于所述格兰板1的右端,所述第三中空吸能块4设置于所述格兰板1并位于所述第一中空吸能块2的右侧,所述第四中空吸能块5设置于所述格兰板1并位于所述第三中空吸能块4的右侧,所述第三中空吸能块4和第四中空吸能块5为间隔设置,所述第五中空吸能块6设置于所述格兰板1并位于所述第一中空吸能块2的左下方,所述第六中空吸能块7设置于所述格兰板上并位于所述第二中空吸能块3的右下方;所述第三中空吸能块4的顶端设置为呈阶梯状的第一凸台41和第二凸台42,所述第一凸台41和第二凸台42之间凹设有第一凹槽43;所述第四中空吸能块5的顶端设置为呈阶梯状的第三凸台51和第四凸台52,所述第三凸台51和第四凸台52之间凹设有第二凹槽53,所述第四凸台52的上端面凹设有第三凹槽521。进一步的,所述第三凹槽521为内腔呈半球体状的凹槽。所述格兰板1、第一中空吸能块2、第二中空吸能块3、若干第三中空吸能块4、若干第四中空吸能块5、第五中空吸能块6和第六中空吸能块7均由吸能缓冲材料制得,所述缓冲材料由外到内包括金属面板、硅橡胶层和泡沫金属层。所述泡沫金属层由发泡金属制得,所述发泡金属包括如下重量份的原料:所述纳米粒子是由纳米水玻璃和纳米沸石按照重量比为0.8:1.0组成的混合物。所述发泡剂是由氢化钛和氢化钙按照重量比为1.2:1.0组成的混合物。更为优选的,所述氢化钛经过化学镀铁、氧化铝双层包覆处理。所述分散剂是由聚乙烯蜡、邻苯二甲酸酯、聚苯乙烯、硬脂酸钙按照重量比为1.0:01.2:0.8:1.0组成的混合物。所述增粘剂是由松香树脂、萜烯树脂、石油树脂按照重量比为1.0:1.2:1.0组成的混合物。所述泡沫金属由如下步骤制得:1)将铝粉熔化并在温度为700℃保温,再将增粘剂加入铝熔体中搅拌均匀,反应15min使得熔体黏度稳定,得到混合物a,备用;2)将膨胀玻化微珠和纳米粒子混合加入高速搅拌器中,以2000r/min速率搅拌分散均匀得到混合物b,备用;3)将分散剂和步骤2)中得到的混合物b和硼酸盐加入步骤1)中得到的混合物a搅拌分散均匀,得到混合物c,并在550℃条件下恒温保温,备用;4)将步骤3)中的混合物c降温至温度为500℃,加入发泡剂并搅拌20min,将搅拌后的熔体在400℃进行恒温发泡,发泡结束后水冷却凝固即得到泡沫金属。一种缓冲汽车撞击的吸能件通过如下步骤制得:s1、根据设计尺寸要求准备金属面板和泡沫金属层;s2、将金属面板和泡沫金属层的粘结面分别采用硅橡胶用热硫化胶粘剂进行涂覆处理;s3、将压铸模具预热至190℃能够使硅橡胶进行硫化;s4、将步骤s2中处理后的金属面板和泡沫金属层以及硅橡胶层按照设计结构依次放置在模具中,合模施加压力为300mpa,并保压时间为5min,使硅橡胶硫化成型,退模后取出的产品即为该吸能件。对实施了1-5和对比例1-3制得的吸能件的吸能效果、发泡颗粒密度、回弹性、抗压强度进行测试,结果如下表所示:项目吸能率(%)发泡颗粒密度(g/cm3)回弹性(%)抗压强度(mpa)实施例1750.304019实施例2800.333920实施例3830.393622实施例4800.353721实施例5780.363818对比例1400.354512对比例2500.234615对比例3450.254510由上表可知,本发明实施例1-5中制得的吸能件的各物理性能优越,吸能效果、发泡颗粒密度和抗压强度有显著的提升,且回弹性相对下降,使制得的吸能件具有良好的抗冲击、吸能、阻尼减振性能,而且具有使用寿命长、环保性能好的特点。与实施例1相比,对比例1中在制备吸能件时第三中空吸能块的顶端没有设置呈阶梯状的第一凸台、第二凸台和第一凹槽,所述第四中空吸能块的顶端也没有设置呈阶梯状的第三凸台、第四凸台和第二凹槽以所述第四凸台52的上端面凹设有第三凹槽521,进一步的,所述第三凹槽521为内腔呈半球体状的凹槽,对制得的吸能件进行各项物性测试,分析发现此吸能件的吸能效果和抗压强度显著的下降;说明本发明在制备吸能件时在第三中空吸能块的顶端设置呈阶梯状的第一凸台、第二凸台和第一凹槽,所述第四中空吸能块的顶端也设置呈阶梯状的第三凸台、第四凸台和第二凹槽以及所述第四凸台52的上端面凹设有第三凹槽521,进一步的,所述第三凹槽521为内腔呈半球体状的凹槽,能使制得的吸能块具有很好吸能和抗压强度效果,而且具有使用寿命长、环保性能好的特点。与实施例3相比,对比例2中在制备吸能件所用发泡金属时用偶氮二甲酰胺替代了氢化钛和氢化钙按照重量比为0.8:1.0组成的混合物,对制得的吸能件进行各项物性测试,分析发现此吸能件的吸能效果、发泡颗粒密度和抗压强度显著的下降,且回弹性有所提升;说明本发明在制备吸能件所用发泡金属时所用发泡剂氢化钛和氢化钙按照重量比为0.8:1.0组成的混合物,能使制得的吸能块具有很好吸能和抗压强度效果,而且具有使用寿命长、环保性能好的特点。与实施例5相比,对比例3中在制备吸能件所用发泡金属时没有添加石墨烯,对制得的吸能件进行各项物性测试,分析发现此吸能件的吸能效果、发泡颗粒密度和抗压强度显著的下降,且回弹性有所提升;说明本发明在制备吸能件所用发泡金属时添加石墨烯,能使制得的吸能块具有很好吸能和抗压强度效果,而且具有使用寿命长、环保性能好的特点。上述实施例为本发明较佳的实现方案,除此之外,本发明还可以其它方式实现,在不脱离本发明构思的前提下任何显而易见的替换均在本发明的保护范围之内。当前第1页12